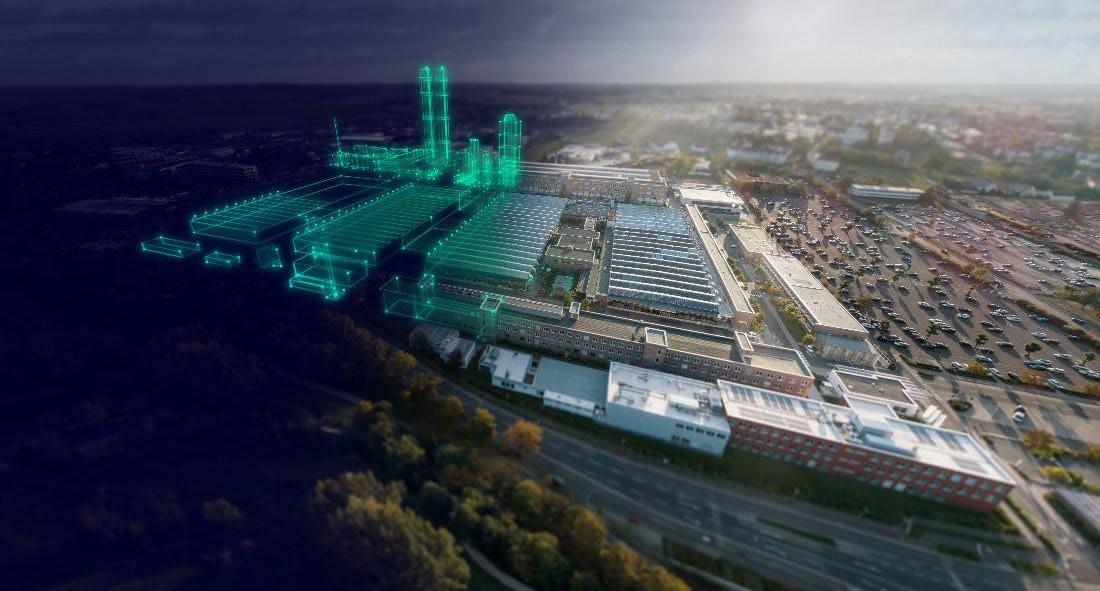
4 minute read
Managing Energy for the Sustainable Factory
By: Rahul Garg, VP of Industrial Machinery, Siemens Digital Industries Software
Sustainability is vital for the manufacturing engines of the world that consume substantial energy. The spiraling price of power is increasing this urgency as it is forcing many regional factories to curtail production or even shut down. Now more than ever, manufacturers globally are determined to address this critical issue, which has put pressure on both the industrial machinery industry and factory operations to aggressively deliver capabilities for a more a sustainable factory to meet these pressing energy directives.
The most effective path to sustainable process, environment, and products is embracing digitalization. With a comprehensive digitalization strategy, it is now feasible to design, develop and deploy smart machines and optimize factory operations to achieve the ultimate zero downtime, zero harm and zero waste.
Digitalization to achieve optimal performance and sustainability
Manufacturers are committing to digitalization to achieve a new level of smart manufacturing. Digitalization delivers more data and better data—key for boosting operational efficiencies to achieve a host of benefits: high availability, maximized factory utilization, and real-time management of supply chains. Equally important, digitalization enables manufacturers to track and lower energy consumption in the short term while leading to greater sustainability overall and the sought-after triple zero of manufacturing.
To improve energy usage and sustainability requires a deep understanding of operations. If you can measure it, you can optimize it. In my role as vice president of industrial machinery at Siemens Digital Industries Software, I am constantly talking with manufacturers and over time have observed that there are 3 steps for effectively implementing digitalization:
1. IT/OT fusion for actionable insights—the initial step is gathering rich, useful data generated by the factory operations technology (OT). The goal is to amass sufficient information to uncover actionable insights. Data is collected across a wide variety of physical sensing technologies, including programmable logic controllers (PLCs), sensors and gauges, IoT devices, etc. Then IT is used to store, retrieve, process, analyze, and recommend action on digital data extracted from OT. It is important to identify key indicators like carbon footprint, performance and profitability early on so that the right data is collected and analyzed.
Extending beyond the factory walls, it is critical to have a clear understanding of the supplier ecosystem. Not only does this provide awareness of cost, timelines and potential disruptions, but also it enables measurement of carbon intensity and resource utilization up and down the value chain. A connected industrial ecosystem, from suppliers and distributors to energy producers, is required to identify new opportunities for partnering and sustainably growing together.
2. Closed-loop manufacturing for continuous improvement—once all the relevant data is available on an ongoing basis, it is possible to create a connected feedback loop. This can be used to continuously hone the cost, time and quality of the manufacturing process while minimizing energy consumption. In short, it tightens the alignment of the as-planned product with the as-built and as-used product in a continuous, iterative process. Engineering teams can receive timely manufacturing feedback to expedite problem resolution and ensure optimal manufacturing that effectively leads to the goal of zero downtime. At the same time, operations can be continuously refined for the most efficient energy usage. This requires linking energy and production data to fine tune the energy consumption of specific machines, as well as the energy productivity of the whole plant to drive sustainable industrial innovation.
3. Closed-loop quality for maximum sustainability with manufacturing being continuously enhanced, it is now possible to pursue optimal product quality that includes long-term sustainability goals—such as zero waste. Closed-loop quality ensures complete visibility of quality-related metrics from planning through delivering on the quality of the completed product. Organizations that establish closed-loop quality processes achieve a median product compliance rate of 99 percent, with a majority performance ranging from 97-100 percent. That means near zero waste without compromising on product performance or sustainability.
Digital twin for energy-aware factory operations
This three-step approach to digitalization, once implemented, supports a comprehensive digital twin of the manufacturing environment. This is a critical game-changer for manufacturers positioning themselves for the future. The digital twin is a virtual, digital replica of the physical objects of an entire machine or the entire manufacturing system or the entire shop floor in a digital environment.
The IT and OT convergence delivers continuous real-time data to increasing the fidelity of the comprehensive digital version of the factory over time. This means that while the factory operates, the digital twin provides a physically accurate simulation that combines the virtual and physical worlds.
The comprehensive digital twin is the basis for improving operations via simulation using the digital model. This includes optimizing operations, predicting maintenance, enabling more efficient commissioning, better changeovers and faster production line changes.
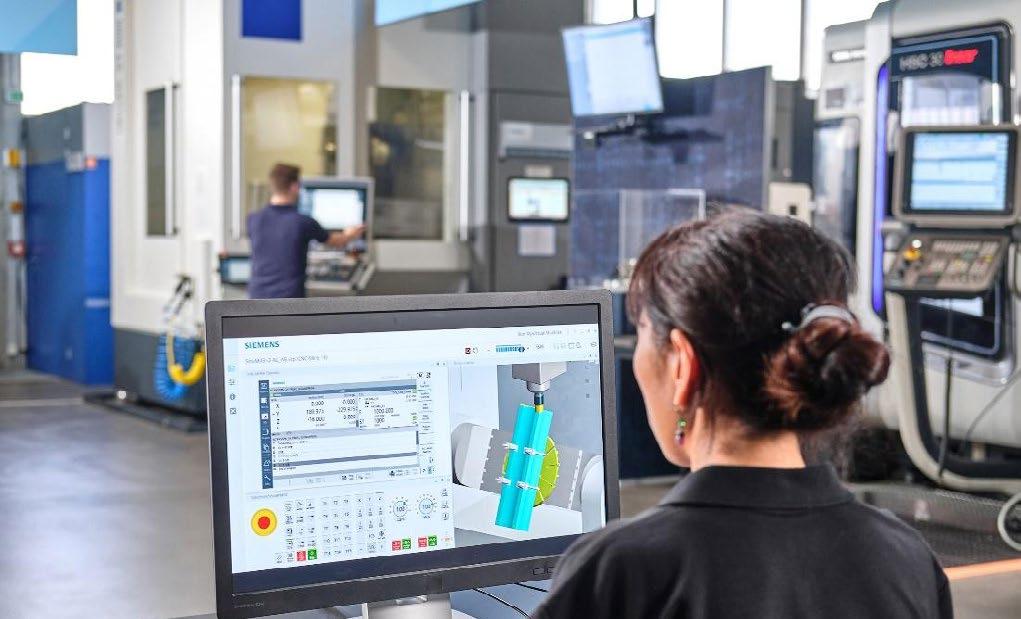
Moreover, the digital twin can be used to simulate and enhance the energy efficiency of the individual machines tool paths, the entire manufacturing line and even the movement of materials in the factory based on real data. The result is lower energy usage without sacrificing on quality or production throughput goals.
Energy efficiency today for a more sustainability future
Digitalization is the best path for lowering manufacturing energy consumption today while pursuing long-term sustainability goals. The immediate result is lower energy usage due to augment machine efficiency and approaching the goal of zero downtime, zero harm, zero waste. Over time, however, is where the real rewards are reaped. The digital twin for optimizing operations and product quality, combined with a robust connected industrial ecosystem, will lead to a lasting, sustainable future.
ABOUT THE AUTHOR:
Rahul Garg is the Vice President for Industrial Machinery at Siemens Digital Industries Software, responsible for defining and delivering key strategic initiatives and solutions, and global business development. He and his team are responsible for identifying key initiatives and developing solutions for the industry while working closely with industry-leading customers and providing thought leadership on new and emerging issues faced by the machinery industry. Rahul’s experience and insight are derived from 25-year career delivering software-based solutions for product engineering and manufacturing innovation for the global manufacturing industry, spanning a career in R&D to program management, sales and P&L management and having focused exclusively on the industrial machinery and heavy equipment industry since 2007.
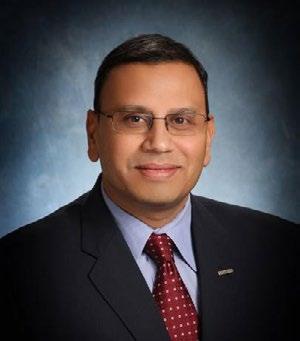