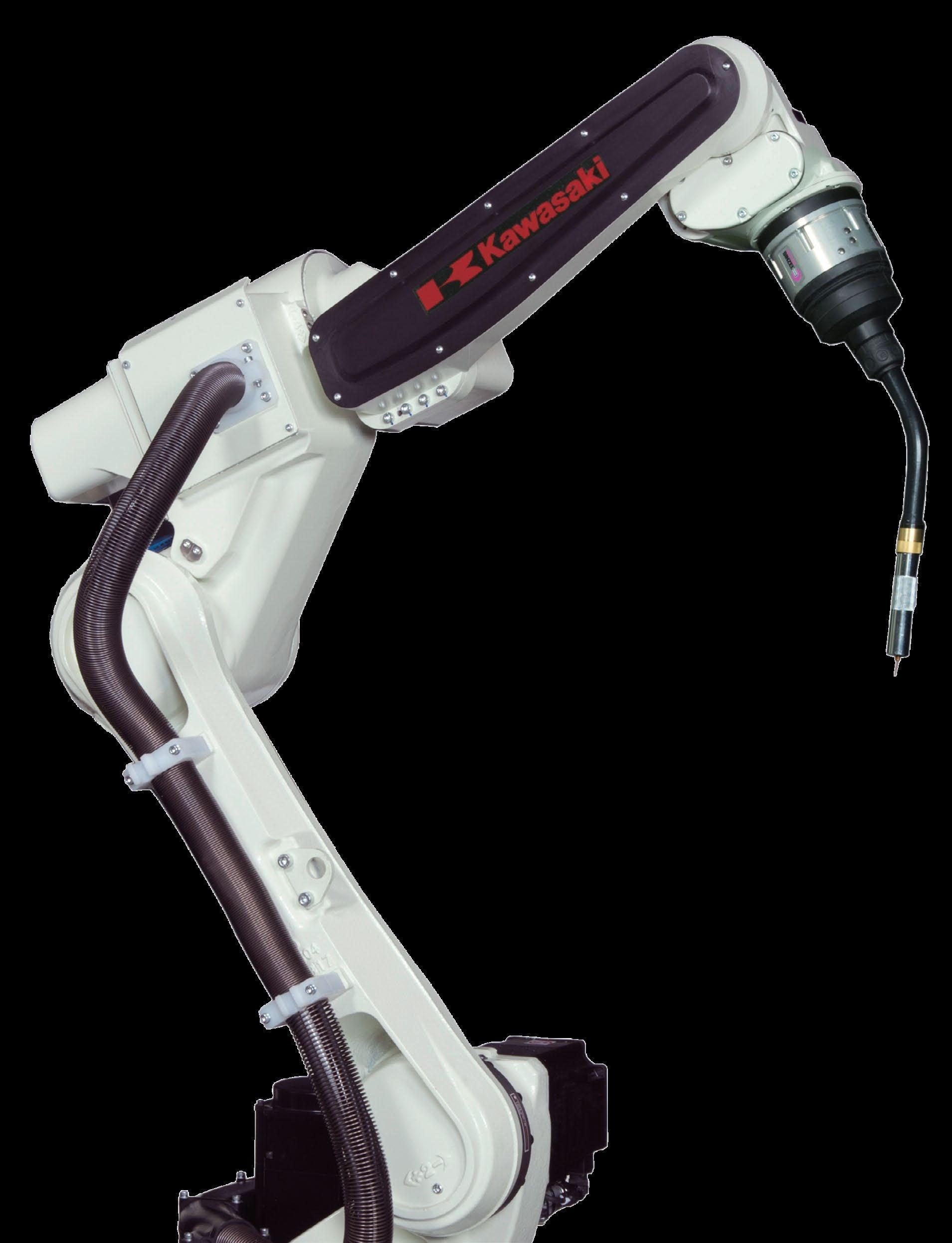
10 minute read
WORKFORCE DEVELOPMENT
Responding to the Demand for Automation
As experienced arc welders become an increasingly scarce resource and mass production amplifies the need for consistent product quality, many companies are at a loss. They need to weld their parts, but it’s difficult to find skilled welders who can produce high quality products, let alone maintain that standard of quality while meeting daily production goals. Advances in robotic arc welding have made it possible for companies to experience the quality and consistency of an expert arc welder on their best day, every single weld.
In the mid-1980s, Kawasaki Motors Manufacturing Corp., USA (KMM) installed their first Kawasaki robots. Growing tired of inconsistent part fit and the constant struggle to find enough welders to keep up with production, KMM’s new robots were put to work arc welding their all-terrain vehicle (ATV) and Mule and Teryx four-wheeler frames. Now, 30 years later, the manufacturer uses 71 Kawasaki arc welding robots, and that number grew to 84 by June of 2019.
“Before robotic welding, there was a lot of frustration on the floor, because you’d get burn didn’t fit well,” explains Scott Gordon, chief engineer, Kawasaki Motors Manufacturing Corp. “We found that the quality of our product was dramatically improving with the implementation of laser tube cutting and the use of robotic welding.”
Challenges
KMM wasn’t looking to robots to increase the amount of vehicles they were producing; they needed Kawasaki robots to maintain their current rate of production while providing a more repeatable frame. Because KMM needed to weld several different vehicles and models – sport utility ATVs and four-wheeler vehicles – they needed a versatile solution that could weld a variety of parts.
A Solution for Labor Shortage
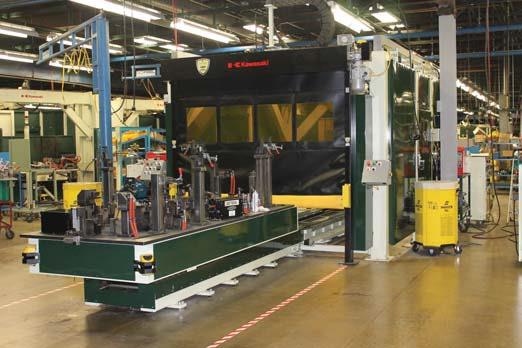
For years, KMM had been fighting an uphill battle against a growing labor shortage in the welding industry. In order to staff enough welders with the necessary level of experience, KMM designed a training course to certify new welders – an exercise that cost the company time and money, and still still couldn’t meet their demand for welders. Their newly trained welders were having to work overtime in order to meet production goals, which was also adding costs. Now, 80 percent of KMM’s arc welding processes are automated using Kawasaki robots, and only 20 percent of the work needs to be done manually. Trained welders can do a bulk of the work, which includes double checking the robots’ work or accessing areas too small for the robot to reach.
Consistency & Reliability
Keeping up with increasing standards for product quality using manual techniques was a challenge.
KMM does mostly pipe-to-pipe welding, so they couldn’t rely on a vision system to keep a robot true to the process path – they needed robots with high levels of repeatability, so they could run programs without having to see the path. Kawasaki RA010L robots have a repeatability of ±0.05 millimeter, which results in the consistency Gordon
has seen firsthand during his 33 years of experience. They are equipped standard with arc welding-specific software to enable quick and easy programming of the process path. “Kawasaki robots are by far the most reliable that we’ve seen on the market,” Gordon said.
Solution

Flexibility was a must. KMM needed a solution that could weld a multitude of parts, and that they could modify to suit their fluctuating production needs and evolving product line. To accomplish this, KMM developed five different types of cells using a combination of Kawasaki R series and F series robots, to weld different components of the ATV and four-wheeler frames. Four of the five cells (called Type 1, Type 2, Type 3 and “Kneeling Easel” cells) weld parts ranging in size. Once complete, these parts are fed into the “Battle Bot” cell, which welds the entire ATV or four-wheeler body.
The Type 1 cell welds small parts like suspension arms, and the Type 2 cell welds mid-size parts such as seats or front guards. It uses a Kawasaki RA010L robot to weld mid-size parts as they rotate on a welding table, attached to a quick-change fixture. The Type 3 cell has a 108 inch long and 52 inch wide cylindrical work envelope, making it ideal for welding long parts. The “Kneeling Easel” cell was developed specifically for welding large 6 ft. by 6 ft. cab frames, whose cumbersome shape posed an ergonomic challenge for human welders.
For welding the entire vehicle frame, Gordon designed the “Battle Bot” cell, which is fed by the other cells. Because this cell was responsible for welding such an integral, and visible, section of the vehicle, KMM utilized a special wave form that combined the strength and penetration of MIG welding, and the clean look of pulse welding. With Kawasaki robots, they were able to do both in the same cell for a high quality product with minimal splatter.
Results
» Four cells specializing in welding different parts feed the “Battle Bot” cell » One “Battle Bot” cell that welds the entire ATV or four-wheeler vehicle frame » 80% of all arc welding is done by Kawasaki R series and F series robots » Manual welds are required for only 20% of work » Human welders double check robots’ work or weld difficult-to-access areas » Product inconsistencies have been eliminated due to flexibility and high levels of repeatability found in Kawasaki arc welding robots
After seeing a drastic decrease in chassis distortion and an increase in consistency over 30 years of use, KMM continues to grow their fleet of Kawasaki arc welding robots. The company’s reliance on manual welding has decreased, so they spend less time hunting for workers in the midst of a labor shortage, and more time on manufacturing. KMM will continue to use Kawasaki arc welding robots to weld thousands of ATV, Mule and Teryx four-wheeler frames.
Kawasaki B Series Arc Welding Robots
Kawasaki’s top-of-the-line arc welding robots match the quality of an expert welder. Each robot is equipped standard with arc welding specific software to enable quick and easy programming of the

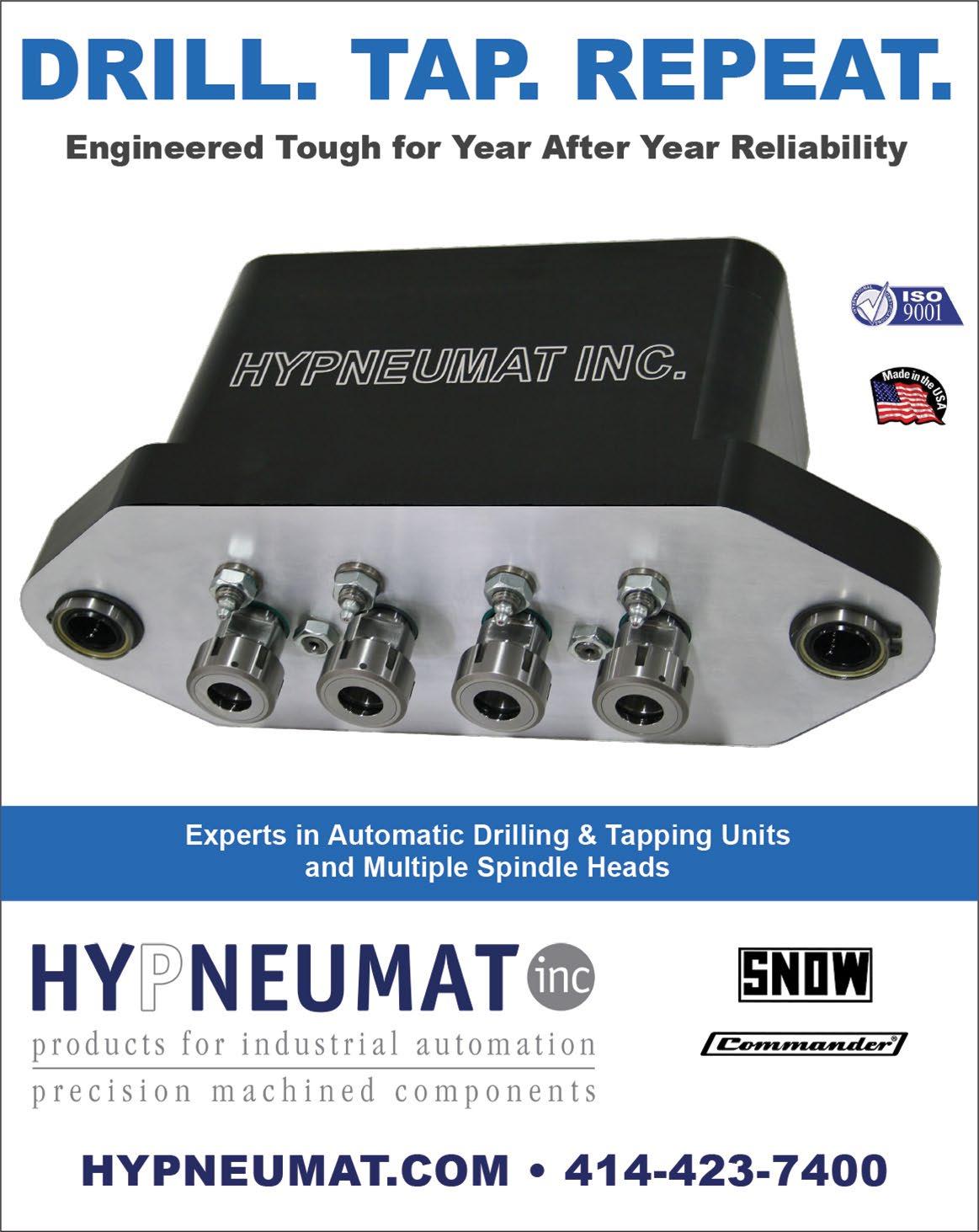
process path. Adaptive welding functionality is available to modify robot position, weave pattern and speed during welding to fill variable joints. Their built-in intelligence, flexibility and high accuracy make Kawasaki's arc welding robots ideal for a wide range of arc welding applications. Kawasaki’s BA006N/L arc welding robots have a hollow wrist structure that allows for easy management of cables and hoses around the torch, providing stable wire feeding and reliable offline teaching.
Reduced Downtime
A standard, dedicated start sequence function improves the arc establishment. Also, for weld process faults, the robot includes a restart sequence function to automatically conduct overlap welding and resume the operation.
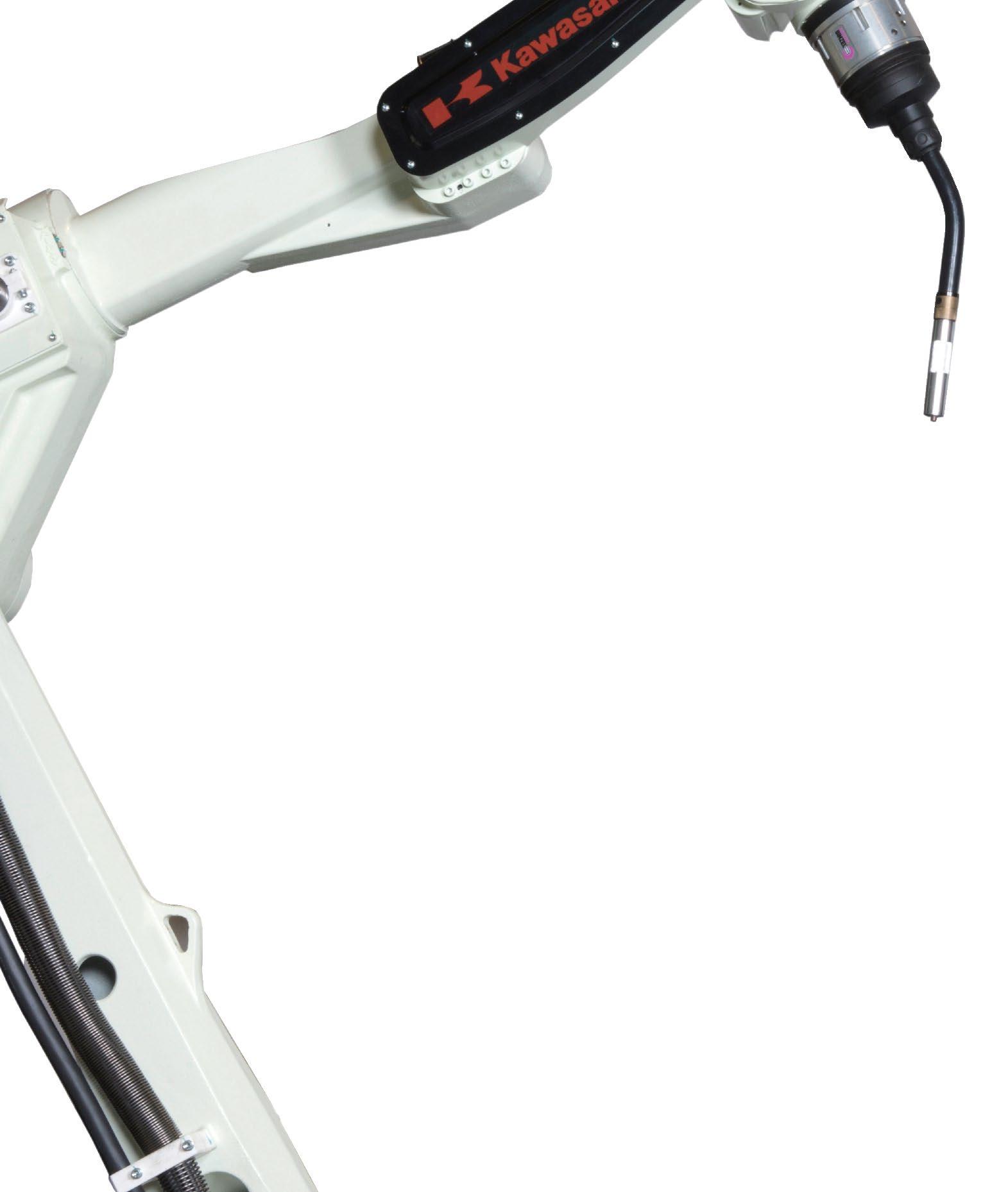
Welding Condition Database
During an automated process, the operator can change the welding conditions on-the-fly, and then store these changes to a built-in database. The saved conditions can then be recalled from the database to be reused in a process.
Advanced Technology
Servo-torch, touch sensing, special weaving pattern, real-time path modification (RTPM) sensor, startpoint sensing, multilayer welding function, and auto voltage control (AVC) sensor are some of the advanced arc welding options available with the Kawasaki welding robots. Kawasaki arc welding robots also feature a one button "arc on / arc off" function to allow operators to easily, and quickly, turn the weld off and on during the automatic weld process. This manual arc control helps operators deal with part anomalies. Kawasaki offers arc welding specific offline programming software to automatically generate robot programs from 3D CAD data. Kawasaki's KCONG software significantly reduces robot teaching time and lowers production costs.
Kawasaki RS007N/L Robots
As a response to the rising demand for fast, flexible and compact industrial robots, Kawasaki developed two 6-axis vertically articulated robots with a maximum payload capacity of 7 kilogram and different reach. The RS007N and RS007L models are some of the newest additions to the company general-purpose R series line of small-to-medium payload (3-80 kg) robots, which offers excellent functional and environmental performance for packaging, assembly, material handling, and other applications.
Superior Speed
Both the Kawasaki RS007N and RS007L robots continue to offer the operational advantages of the R series robots while incorporating a newly redesigned arm structure and main-unit weight reductions. These enhancements result in the fastest operating speeds in these robots' class (12,100 mm/s) along with increased working ranges. By redesigning the arm structure and adjusting the acceleration rates in accordance with load weights and robot positioning, these models also offer consistently optimized performance by significantly reducing cycle times.
Expanded Working Range
The RS007N robot features a 730 mm reach and the RS007L a 930 mm reach for greater flexibility in production facility layouts. By utilizing a cantilever design for the upper arm section, Kawasaki has achieved a longer maximum reach and an expanded range of motion: below, behind and in the immediate vicinity of the robot. Additionally, these floor or ceiling mount models are designed to house vision cables, sensor harnesses, air lines and other components inside the arm structure. This prevents interference with and from peripheral equipment, thus allowing for operation in tight installation spaces.
The RS007N and RS007L robots feature a double-seal construction on all axes and waterproof electrical connections, offering an IP67 classification for the wrist and IP65 for the remaining axes. This first rate environmental protection means the robots are protected against large quantities of dust, water, lubricants, coolants, and can even withstand high surface temperatures and temporary submersion.
Controller
The RS007N and RS007L robots come standard with Kawasaki’s newest F60 robot controller. This state-of-the-art controller helps manufacturers digitally connect their machines and extract value
from the Internet of Things (IoT), and features enhanced data collection and transfer capabilities to support overall equipment efficiency (OEE) calculations and smart manufacturing. The Bluetooth enabled controller allows for the collection and analysis of both robot and production data and provides the ability to link to the cloud, other robots or machines, tablets, vision cameras and various fieldbuses.
Kawasaki’s NEW RS013N Robot – An Evolution of the R Series
Both the Kawasaki RS007N and RS007L robots continue to offer the operational advantages of the R series robots while incorporating a newly redesigned arm structure and main-unit weight reductions. These enhancements result in the fastest operating speeds in these robots' class (12,100 mm/s) along with increased working ranges. By redesigning the arm structure and adjusting the acceleration rates in accordance with load weights and robot positioning, these models also offer consistently optimized performance by significantly reducing cycle times.
Industry Leading Speed & Flexibility
The new robot’s design includes a new arm structure, drive system and lighter main unit, which enables high speeds and a large working area. Its 1,460 mm reach is the largest in its class, allowing for installation flexibility and use in a wider variety of applications. The RS013N robot also leads its class in speed, resulting in reduced cycle times and increased productivity.

Enhanced Versatility
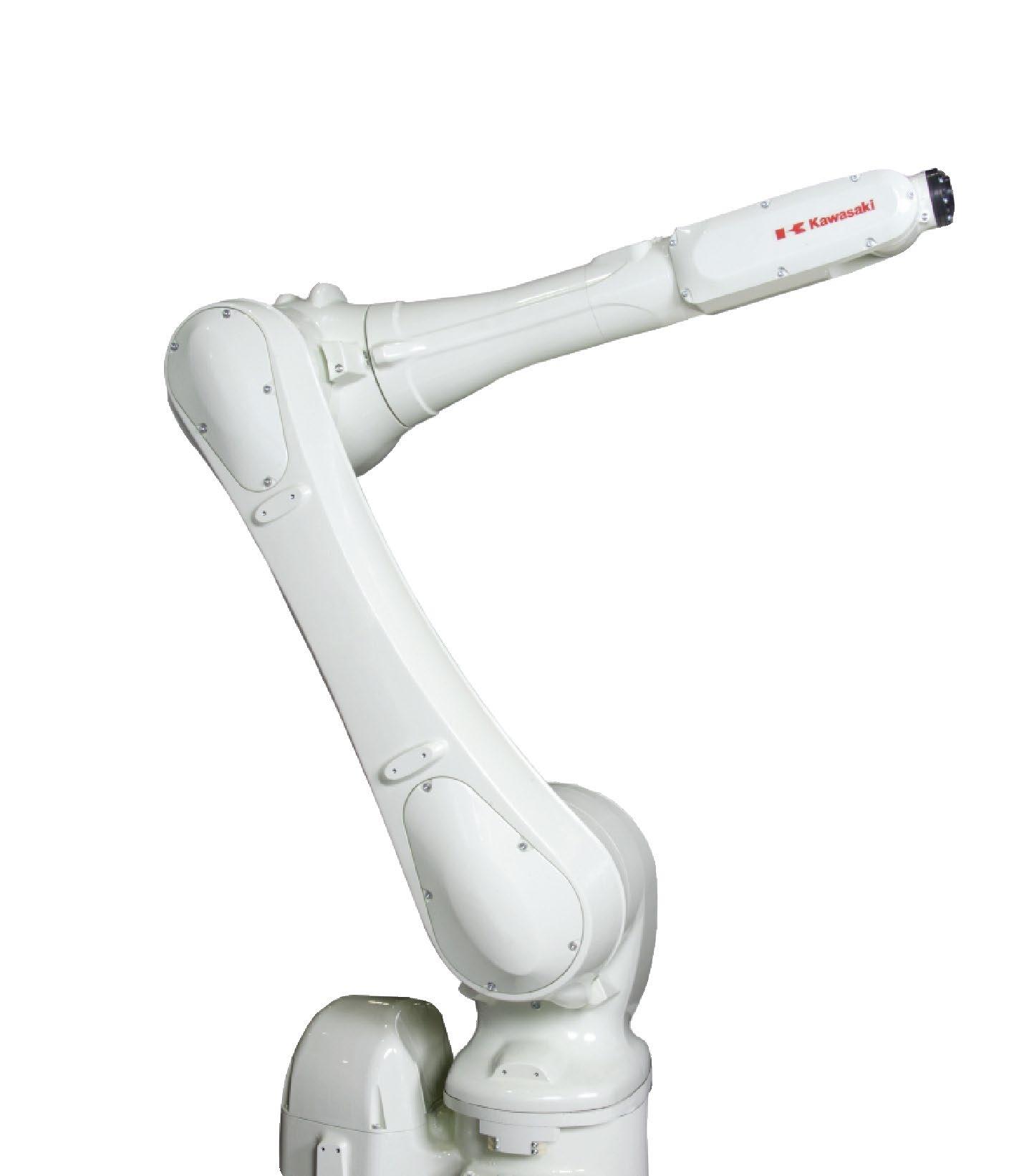
In addition to its expanded work area, the robot’s wiring and installation options contribute to its overall flexibility. The robot’s internal Ethernet wiring enables easy connection to a vision system or other peripheral devices, and its floor, ceiling and wall mount options provide installation flexibility for any layout. The dust-tight RS013N offers a full-body IP67 rating, fully covered motors and waterproof electrical connections allow the robot to Kawasaki’s next generation R series robots (RS007N/L and RS013N) also have reduced interference zones around the robot base, which allows the user to maximize their floor space and working area.
Built for Longevity
Kawasaki’s new R series robots are designed with ease of use and longevity in mind. The motor has been moved and covered to protect it from harsh environments and workplace wear, and the new motor location on the base allows for enhanced protection and easier serviceability.
With more than 210,000 robots shipped worldwide, Kawasaki is a leading supplier of industrial robots and robotic automation systems with a broad product portfolio, able to service a wide range of applications across diverse industries. Kawasaki Robotics (USA), Inc. is a subsidiary company of Kawasaki Heavy Industries, Ltd., Robot Division of Japan, and is headquartered in Wixom, Michigan, with sales and service offices in North and South America. Kawasaki has incorporated over 50 years of experience as a robot industry leader into the development of technically advanced controllers and high quality robots.
For more information, visit www.KawasakiRobotics.com