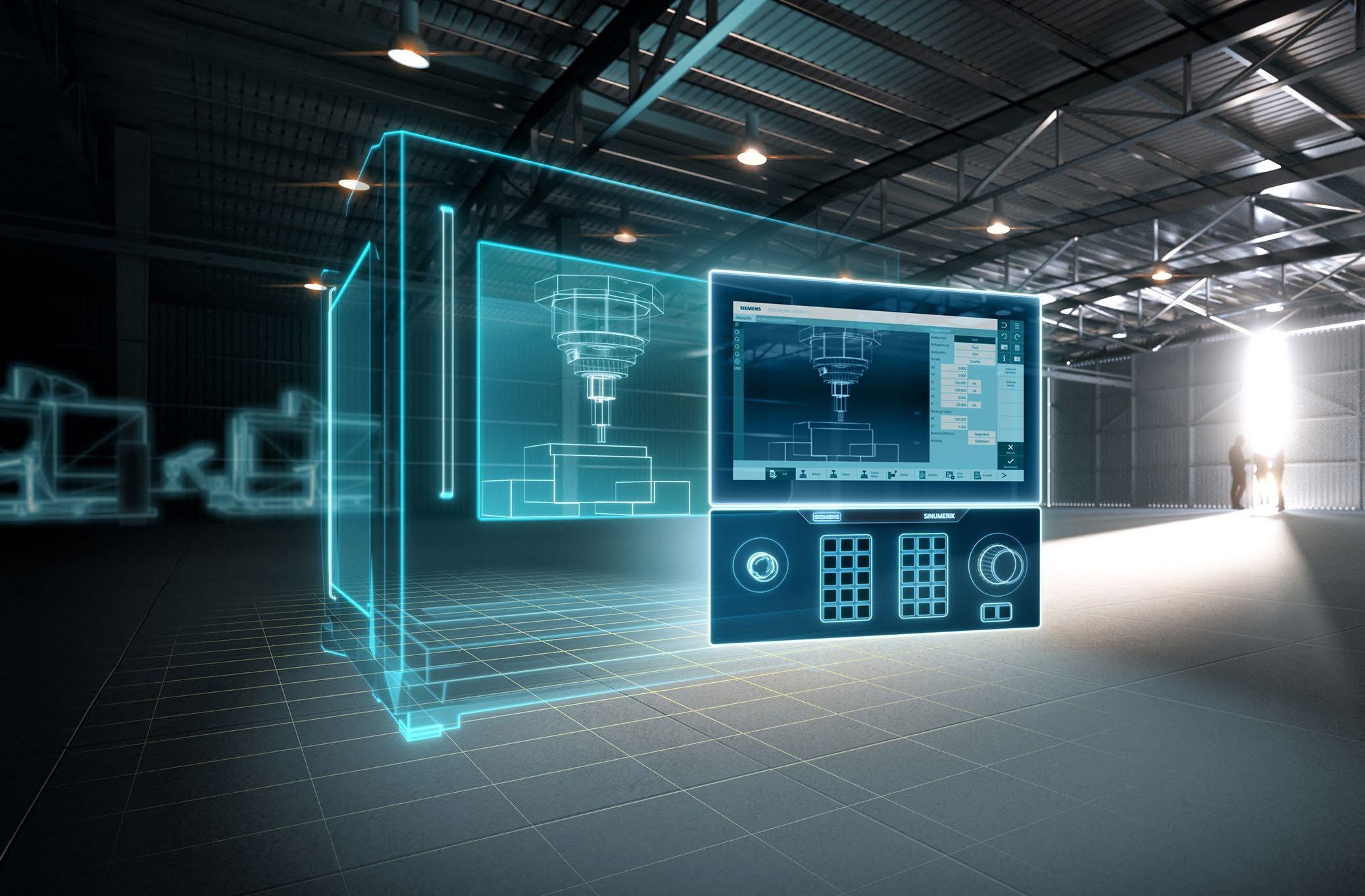
6 minute read
NEW TECHNOLOGY
The new digital-native CNC from Siemens, SINUMERIK ONE, is setting new productivity benchmarks with its digital twins — the new hardware platform and innovative technology functions.
Increasing CNC Machine Users’ Efficiency
SINUMERIK ONE Dynamics — Powerful New Technology Packages for Motion Control and Workpiece Quality
During Siemens Machine Tool Days 2020, Siemens launched three powerful technology packages exclusively for its new SINUMERIK ONE control system. The SINUMERIK ONE Dynamics packages are available in three different variants: ONE Dynamics Operate, ONE Dynamics 3-axis milling and ONE Dynamics 5-axis milling. The software functions contained in each technology package support users from machine-oriented programming in the job shop to high-performance machining of CAD-CAM-programmed workpieces with high surface quality.
The ONE Dynamics Operate package supports the machine tool user in efficient programming in the machine shop with the proven SINUMERIK machining cycles and high-quality CNC simulation for milling and turning applications. In addition, the user is given a wide range of options for accessing NC programs and workpiece documentation. Users have the option of paperless manufacturing and can, for example, visualize 3D CAD data on the shopfloor within a very short time. For the execution of CAM-generated CNC programs for free-form surface machining, ONE Dynamics 3- and 5-axis milling packages offer the Top Surface and Top Speed Plus CNC functions for excellent motion control and perfect workpiece surfaces.
With Top Surface, the geometric data from the CAM system is checked and optimized during processing on the CNC using an intelligent algorithm. This ensures high surface quality when milling complex free-form surfaces. This is particularly advantageous for geometrically complex mold components that place special demands on surface quality, mold accuracy and production
efficiency — for example in tool- and mold-making, aircraft construction or medical technology.
Top Speed Plus ensures with new filter technology that increased dynamics are made possible without activating mechanical vibrations of the machine and that the contour accuracy is reliably maintained. Depending upon the specific application, this can reduce machining times by up to 30 percent. As a result, unit costs for milling with CAM-generated CNC programs can be reduced and production efficiency increased.
With a few exceptions, the functions of SINUMERIK ONE Dynamics do not require any commissioning effort by the machine tool builder. Once activated, they are available to the user for immediate use on the CNC machine. Since they are CNC software functions, no intervention at the machine or in the machine’s mechanics is required. For users who have particularly challenging requirements when it comes to machining quality and speed, the machine tool builder can add additional optional CNC functions of the SINUMERIK control that go beyond the SINUMERIK ONE Dynamics packages. These additional functions must then be activated and parameterized by the machine builder for the user’s individual machine and adapted to the machine statics and dynamics.
Shorten Development and Commissioning Times By Up To 50% The new generation of machine tool control, SINUMERIK ONE, is at the heart of the digital transformation of CNC machines. As a digital native control, SINUMERIK ONE features not only a new hardware platform, but also versatile software for the creation of a digital twin. It closes the gap between the virtual and the real world while helping to reduce development and commissioning times considerably.
The central element for engineering the SINUMERIK ONE is the Totally Integrated Automation (TIA) Portal. Both PLC (Programmable Logic Controller) and Safety are engineered in this framework with modern programming languages and a seamless data flow. The integration of SINUMERIK ONE into the TIA Portal enables a consistent digital development process for CNC machines, which makes all engineering tasks easier.
With its integrated Simatic S7-1500F failsafe PLC, machine tool builders can take full advantage of the benefits the TIA Portal brings. Uniform, centralized data handling enables efficient engineering and considerably reduces the potential for errors caused by inconsistent data. Drag-and-drop is used to network peripherals easily and to establish communication links with other machine components. In addition, machine builders can create software libraries with ready-made hardware configurations and numerous function and software modules in TIA Portal, thus standardizing the development of the CNC machine.
SINUMERIK ONE is based upon Safety Integrated as the Siemens industry standard. The controller also supports safety functions integrated in the drive. In addition, thanks to the integration of the Simatic S7-1500F PLC for implementation of the safety logic, only one failsafe program is required. This simplifies safety engineering and reduces safety commissioning time.
Customized Safety Lifting Devices For Any Application

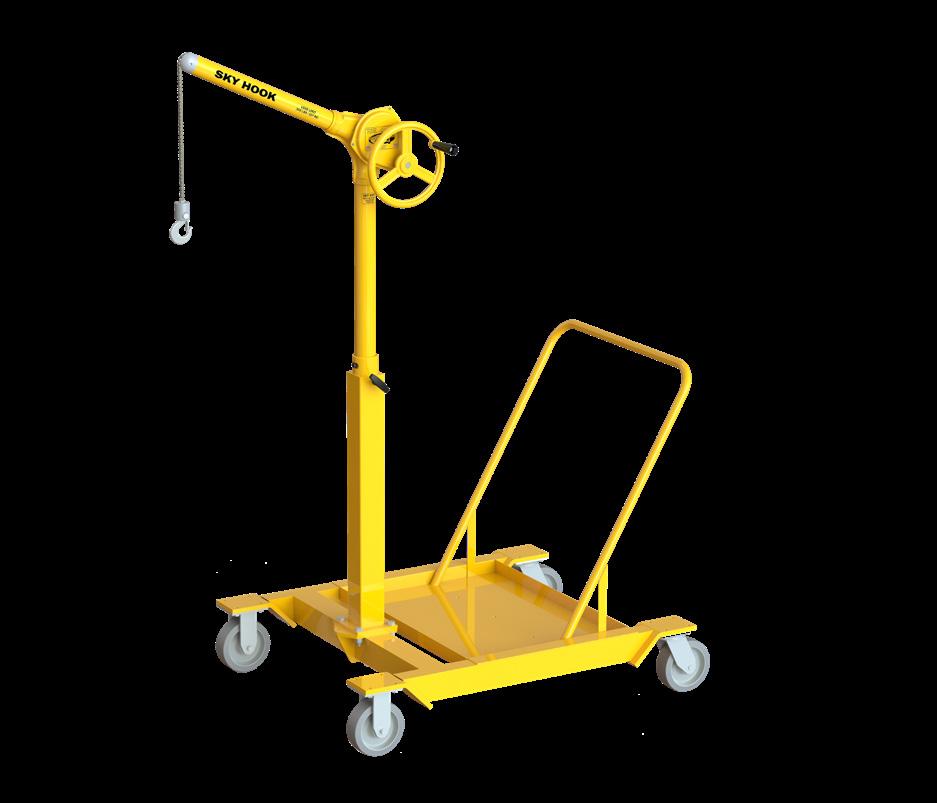
Safely Lifts Up To 500 lbs! Ergonomic Portable Lightweight Meets OSHA & ASME Requirements

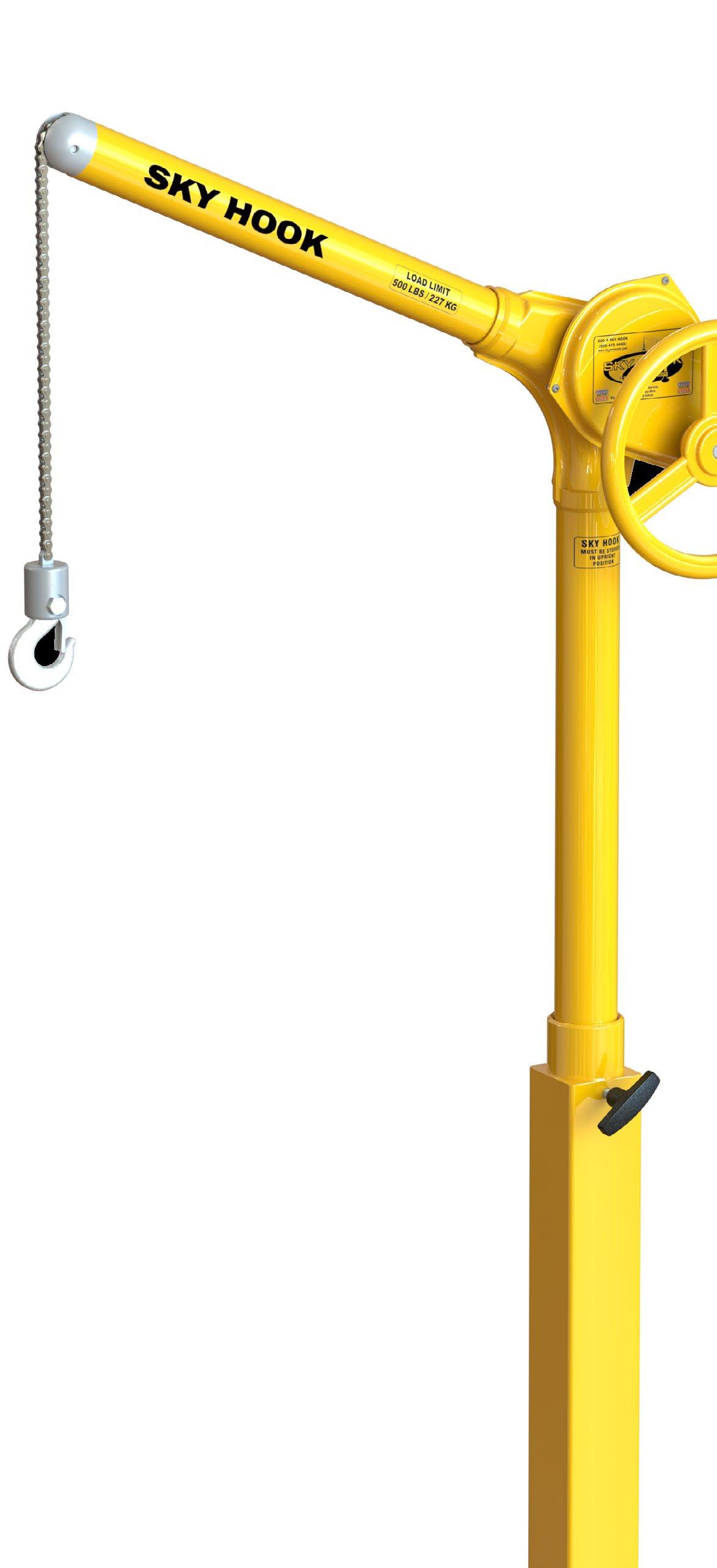
800-4-SKYHOOK
800-475-9466 • 208-365-5770
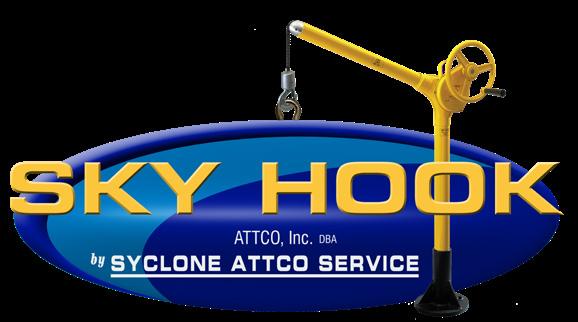
The central element for engineering the SINUMERIK ONE is the TIA Portal. Both PLC (Programmable Logic Controller) and Safety are engineered in this engineering framework.
With Create MyVirtual Machine software, machine tool builders can use a digital twin of the CNC and utilize it as a virtual test rack. In this way, engineering and software modules can be tested comprehensively without the need to use hardware.
Programming tasks, which previously had to be performed successively, can now be completed at the same time. This creates flexibility and reduces dependencies. Using the virtual image of the CNC, logic functions in the safety environment can be virtually tested and commissioned in advance. Virtual commissioning with the digital twin helps to minimize commissioning time in the real world.
Run MyVirtual Machine software allows the CNC user to create the machining environment that will happen before they get to the manufacturing floor. Users can quickly and easily validate the actual machining of the product, evaluate the process that will happen before the first cut, and optimize their CNC part programs to stay up-and-running. New machine tool operators can even be trained without tying up the actual CNC machine.
For more information about SINUMERIK ONE, please visit usa.siemens. com/sinumerik-one
ABOUT SIEMENS DIGITAL INDUSTRIES (DI)
Siemens Digital Industries (DI) is an innovation leader in automation and digitalization. Closely collaborating with partners and customers, DI drives the digital transformation in the process and discrete industries. With its Digital Enterprise portfolio, DI provides companies of all sizes with an end-to-end set of products, solutions and services to integrate and digitalize the entire value chain. Optimized for the specific needs of each industry, DI’s unique portfolio supports customers to achieve greater productivity and flexibility. DI is constantly adding innovations to its portfolio to integrate cutting-edge future technologies. Siemens Digital Industries has its global headquarters in Nuremberg, Germany, and has around 75,000 employees internationally.

ABOUT SIEMENS CORPORATION
Siemens Corporation is a U.S. subsidiary of Siemens AG, a global powerhouse focusing on the areas of power generation and distribution, intelligent infrastructure for buildings and distributed energy systems, and automation and digitalization in the process and manufacturing industries. Through the separately managed company Siemens Mobility, a leading supplier of smart mobility solutions for rail and road transport, Siemens is shaping the world market for passenger and freight services. Due to its majority stakes in the publicly listed companies Siemens Healthineers AG and Siemens Gamesa Renewable Energy, Siemens is also a world-leading supplier of medical technology and digital healthcare services as well as environmentally friendly solutions for onshore and offshore wind power generation. For more than 160 years, the company has innovated and invented technologies to support American industry spanning manufacturing, energy, healthcare and infrastructure. In fiscal 2018, Siemens USA reported revenue of $23.7 billion, including $5.0 billion in exports, and employs approximately 50,000 people throughout all 50 states and Puerto Rico.
For specific product information and inquiries, send an e-mail to: cnc.marketing.us@siemens.com
Follow us on Social Media: www.twitter.com/siemens_cnc_us www.facebook.com/Siemens.CNC.US