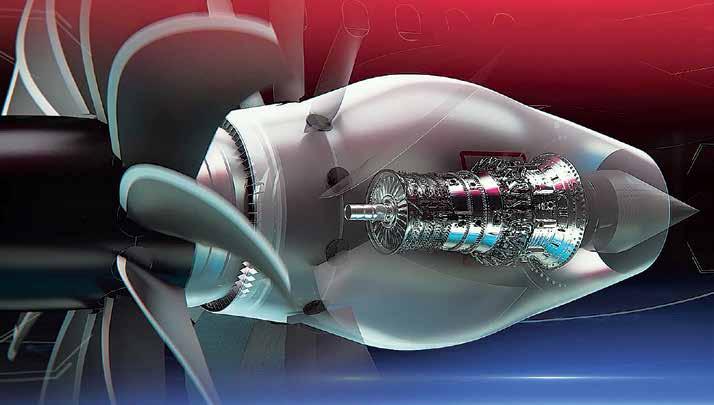
16 minute read
CFM RISES
By JOSEPH NORONHA
The commercial aviation industry is under growing pressure to clean up its act on emissions. Aviation is hardly a major emitter, accounting for just 2.4 per cent of global carbon dioxide (CO2) emissions. However, its relative share of emissions is projected to at least triple by 2050 as air traffic surges and other sectors of the economy successfully decarbonise. Acutely aware of the danger of being branded a climate change “bad boy”, the industry has set its sights on achieving net-zero carbon emissions by 2050. In other words it aims to completely eliminate or at least offset its emissions by then. This ambitious goal (some would call it an impossible dream) rests on two main pillars – sustainable aviation fuels (SAF) and technological innovations, especially more fuel-efficient aircraft. SAFs produced from renewable sources can reduce carbon emissions by up to 80 per cent compared to conventional jet fuel. But they are expensive and their current production is pitifully low – around one per cent of the global jet fuel requirement.
When it comes to fuel efficiency, CFM International, a 50-50 joint venture between two of the world’s leading aerospace companies – General Electric (GE) and Safran Aircraft Engines (SAE) – has been in the forefront of technological advancement for over 40 years. Its first product, the CFM56, was a highbypass turbofan engine that entered service on April 24, 1982, and eventually became one of the most successful engines in history. However, in an effort to further improve efficiency, the LEAP engine, introduced in 2016, was 15 per cent more fuelefficient than the CFM56-5B and -7B engines. LEAP is doing exceedingly well, having logged over 25 million engine flight hours in just six and a half years of revenue service. It has left the competition far behind. Yet CFM feels the need to achieve a step change in efficiency over LEAP.
In the past, revolutionary change has been attempted only in response to rising fuel prices. When fuel prices declined there was a corresponding ebbing of enthusiasm and investment. How- ever this time the incentive to develop more advanced technologies is that of making aviation more sustainable. This motivation can only increase given the global anxiety about impending catastrophic climate change. Enter the CFM RISE programme.
Rise Arises
The CFM International RISE (Revolutionary Innovation for Sustainable Engines) Technology Demonstration Program was launched on June 14, 2021. Its goals include reducing fuel consumption and carbon emissions by more than 20 per cent compared to today’s most efficient engines, as well as ensuring compatibility with alternative energy sources like SAF, electricity and hydrogen. RISE is developing new technologies that can significantly reduce the environmental impact of aviation, including emissions and noise, thus making aviation more sustainable. Although RISE is only a technology demonstrator, technologies matured under its aegis will serve as the foundation for the nextgeneration CFM engine that could be available by the mid-2030s. The RISE engine will produce around 30,000 lb of thrust, which puts it in the LEAP turbofan class. Clearly therefore CFM International’s initial focus will be the single-aisle market. But growth will probably be achievable by scaling up the fan blades and engine core.
An Opening For The Open Fan
Central to the RISE programme is state-of-the-art propulsive efficiency achieved by adopting an open fan architecture. All previous efficiency breakthroughs were achieved by technologies that permitted a larger fan size and a higher bypass ratio. The larger fan required a huge fan case or nacelle to enclose it, greatly adding to the engine weight and overall drag of the aircraft. But RISE is visibly different. At one stroke, its open fan design dispenses with most of the dead weight. The fan is expected to have a diameter of around 13 feet approximating to the outer diameter of the LEAP nacelle.
RISE’s single rotating open fan design has variable pitch carbon fibre composite blades, behind which is a row of static guide vanes. On the other hand, SAE’s 2017 Sage2 demonstrator had a contra-rotating second fan stage. The original open-fan design that GE Aviation flight-tested in 1988 under its Unducted Fan (UDF) project also had a direct-drive (gearless), contra-rotating, pusher fan. But the RISE design is much simpler and lighter because stationary outlet guide vanes replace the contra-rotating fan blades. This permits flight speeds similar to that using conventional turbofan engines. Acoustics, which were a major drawback of the earlier open fan designs, are also significantly improved.
Because of their large diameter, the fan blades of the RISE open fan will need to rotate relatively slowly so that their tips don’t reach supersonic speeds. A reduction gearbox between the low-pressure spool and the fan drive shaft reduces the shaft’s rotation rate compared with that of the low-pressure turbine. Under an agreement signed in February, Airbus and CFM plan to flight-test the RISE demonstrator using an Airbus A380. The A380 will be fitted with a large support pylon and a reinforced inboard wing structure to accommodate the open fan.
Another crucial feature of CFM’s RISE is a compact engine core. In 2021, NASA awarded GE Aviation contracts to test and mature new jet engine core designs, including compressor, combustor and high-pressure turbine technologies to improve thermal efficiency.
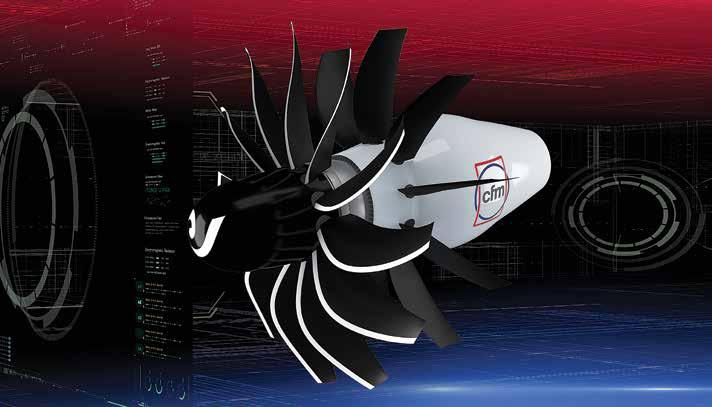
Building Blocks
Apart from its eye-catching open fan the RISE demonstrator will incorporate several advances in engine architecture, aerodynamics, and advanced materials that will help it achieve higher fuel efficiency and lower CO2 emissions than its predecessors. It also features technologies such as carbon fibre composites (CFC), ceramic matrix composites (CMC) and additive manufacturing.
GE Aviation and CFM International are the only engine manufacturers with CFC blades in commercial service. These fan blades are higher strength and lighter weight than the titanium fan blades they have replaced. Similarly CMCs, another advanced composite material containing silicon carbide fibres, are lighter and more heat resistant than traditional metal alloys. Engines built using CMCs can operate at higher temperatures with less cooling air. Exploiting both these technologies is additive manufacturing (also known as 3D printing) using new materials, which makes for lighter engine parts with higher capabilities and more complex designs than parts made by conventional manufacturing techniques.
RISE’s software-driven engine controls will ensure optimal fuel efficiency during each phase of flight – take-off, climb, cruise, etc. They will also monitor real-time engine health, allowing proactive resolution of emerging issues and thus improving the engine’s durability.
CFM’s RISE, from the outset, aims to reduce aviation’s environmental impact by permitting the use of 100 per cent SAF. RISE will also be capable of hybrid-electric operation, in which part of the thrust is provided by electrical power. And, most excitingly, it may be easily adaptable to run on hydrogen. Hydrogen, which is the most abundant element in the universe, produces no CO2 emissions when it burns and is therefore a potent ally in humanity’s ultimate quest to eliminate carbon emissions. Although the use of hydrogen as an aviation fuel presents daunting challenges, CFM engineers are confident that viable solutions can be found. According to GE Aviation’s CEO John Slattery, replacing conven- tional jet fuel completely with SAF would reduce CO2 emissions by 80 per cent. And if hydrogen were the fuel, CO2 emissions would drop to zero.
Only The Beginning
Since the world entered the commercial jet era on May 2, 1952, with the entry into service of the de Havilland DH.106 Comet, there have not been many major advancements in jet engine technology. In fact, when the Rolls-Royce Conway, the world’s first production turbofan, entered service in the late 1950s, it attracted hardly any attention because its bypass ratio was a mere 0.3. Since then technological progress has been evolutionary rather than revolutionary with the fan diameter inching up and the bypass ratio correspondingly increasing.
However, air transport is a crucial factor in deciding whether or not the world can avert climate change. Aviation therefore can no longer count on incremental progress. A sustainable future requires a propulsion system that will dramatically increase fuel efficiency as well as meet anticipated International Civil Aviation Organization (ICAO) noise and emissions standards. The CFM RISE open fan architecture is a radical innovation that seems to offer the best hope of achieving the large reduction in CO2 emissions that aviation urgently needs to become environmentally sustainable. With its larger blades and smaller core than that of other current engines, CFM expects the RISE open fan to have an astounding bypass ratio of 75:1. This is nearly an order of magnitude greater than the 11:1 ratio achieved by the CFM LEAP-1A and the 12.5:1 ratio achieved by the Pratt & Whitney PW1100G GTF engine.
CFM International believes that the RISE technology demonstrator is only the beginning. Although RISE will feature advanced technologies tailor-made for a futuristic single-aisle aircraft propulsion system, the technology suite it develops will probably find its way into commercial aircraft of all sizes and thrust classes for decades to come. SP
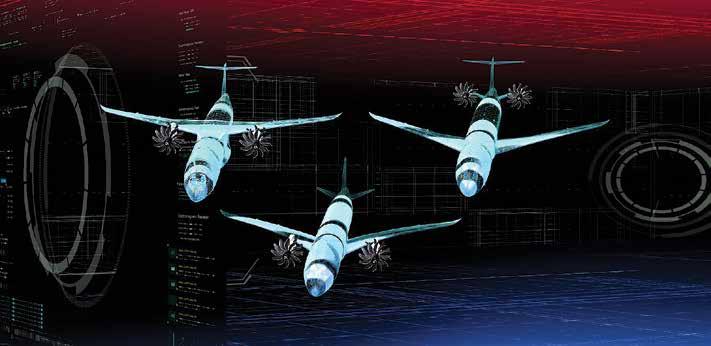
LEONARDO DA VINCI (1452-1519)
In 2020, a University of Maryland engineering team designed and tested the technology underlying da Vinci’s hovering device. The result was Crimson Spin, an unmanned quadcopter drone that actually flew on several brief journeys.
What place can someone born in 1452 have in an aviation Hall of Fame, considering that the first powered flight happened only in 1903? As Dane Cook said, “Every great thing starts with an idea.” And Leonardo da Vinci, world famous for paintings like the “Mona Lisa” and “The Last Supper”, was certainly not lacking in ideas – ideas about aviation that were centuries ahead of his time. Long before the first person could take to the skies, theories about how this might be practically achieved germinated in his fertile mind.
Leonardo da Vinci was born on April 15, 1452, in the hill town of Vinci, Central Italy. Till the nineteenth century, he was generally regarded only as a painter. However, he was also an astronomer, sculptor, geologist, mathematician, botanist, inventor, engineer, architect and musician. All this came to light only after 1800, and not from any surviving works, but from his long-lost notebooks concerning science and technology. Thousands of pages of writings and drawings, today referred to as “Leonardo’s codices”, reveal that he was an intellectual and technical genius as well as an inspired inventor. Among his many pursuits was a quest for the possibility of human flight. It dominated his attention from the late 1480s to the mid-1490s.
When Leonardo da Vinci was employed by the Milanese royal court to work on military technology, he became fascinated by the potential value of reconnaissance from the air. So fascinated, that he produced more than 35,000 words and 500 sketches dealing with the properties of air, bird flight and flying machines. Although these studies are distributed throughout his codices, there is one work devoted almost entirely to the subject. “Codex on the Flight of Birds” c. 1505, now held at the Royal Library of Turin, comprises 18 folios. It has a detailed examination of avian flight, noting for the first time that the centre of gravity of a flying bird does not coincide with its centre of pressure. There are scores of pages analysing the motion of the wings of bats and birds whilst in straight flight, in turns, while gliding etc. He explained the behaviour of birds as they ascend against the wind and arrived at the basic concept of a stall. Long before Newton defined gravity, Leonardo hinted at the action of this mysterious force. His observations of gliding flight by birds led him to the basic principles of how a mechanical device that emulated bird flight would need to be balanced using wings and tail-plane. He noted the crucial importance of lightweight structures, even though the technology of the day had no such possibilities. He actually constructed a number of potential flying devices and attempted to launch some of them from a hill near Florence, but without success.
One design was what is now called an ornithopter – a flying machine operated by flapping mechanical wings like a bird. Leonardo da Vinci’s ornithopter resembled a giant bat, with a wingspan of over 33 feet, and a frame of pine covered with raw silk to create a light but sturdy membrane. The pilot would lie face down and spin cranks connected to a rod-and-pulley system with both hands and feet while using a head piece for steering a small rudder. The contraption was remarkable for how the entire human body would be used to maximise the power generated by the lone pilot. However, as da Vinci himself would probably have realised, while the flying machine may have been capable of flying through the air, no human body could have generated enough power to get it off the ground.
Similarly, da Vinci’s proposed hovering device closely resembles a rudimentary helicopter, 400 years before such craft began to appear. It was to be built of wood, reeds and taffeta. He envisioned a spring, wound by crank turners, building up and storing energy. That stored energy could be released in a quick unwinding burst, spinning the screw rotor: “A small model can be made of paper with a spring like metal shaft that after having been released, after having been twisted, causes the screw to spin up into the air.” While Leonardo’s design was aerodynamically sound, he lacked the modern materials necessary to build a lightweight and durable blade. He described its helical screw as being made of linen, with the pores stopped up by starch – a rather impractical proposition. However, in 2020, a University of Maryland engineering team designed and tested the technology underlying da Vinci’s hovering device. They added a modified screw system to a modern drone. The result was Crimson Spin, an unmanned quadcopter drone that actually flew on several brief journeys.
Leonardo da Vinci died at Clos Lucé, France, on May 2, 1519. All in all, he was perhaps one of the most fascinating people history has ever known. SP

— JOSEPH NORONHA
Military
Rajnath Singh Reviews Progress Of Infrastructure Projects
Appointments
Atr
• Bernard Marquez has been appointed Head of Quality at ATR, effective March 1, 2023. Bernard takes the lead of an integrated and independent Quality function.
• Daniel Cuchet has been appointed SVP Engineering effective from February 1, 2023 and Head of Design Organisation ATR effective January 1, 2023.
Embraer
Embraer announced that Andreza de Souza Alberto will be the new Vice President of People, ESG and Corporate Communications. The change becomes effective on February 1, 2023.
Defence Minister Rajnath Singh chaired a high-level meeting in New Delhi on March 14, 2023 to review the progress in construction of various infrastructure projects on the northern border areas. The Defence Minister called for expediting all pending projects on top priority, stating that ‘whole of nation’ approach should be adopted in matters of national security. To fast-track the pending projects, it has been decided to set up a committee of Secretaries which will meet at frequent intervals.
SUCCESSFUL FLIGHT-TEST OF INDIGENOUS POWER TAKE OFF SHAFT
Cfm
CFM International has appointed Florence Minisclou as Executive Vice President. Florence is responsible for overseeing the CFM56 and LEAP programs and also serves as Vice President of CFM programs for Safran Aircraft Engines.
Safran Landing Systems
Jean-Michel Hillion is appointed Executive Vice-President Wheels & Brakes Division of Safran Landing Systems as of Feburary 1, 2023. Since January 2021, Jean-Michel held the position of Group Vice-President Strategy and Climate.
Box while accommodating misalignments that arise in the drive line.
Aeronautical Development Agency, Centre for Military Airworthiness and Certification, Directorate General of Aeronautical Quality Assurance and Hindustan Aeronautics Limited teamed along with CVRDE to achieve this feat.
CONTRACT FOR PROCUREMENT OF 70 HTT-40 BASIC TRAINER AIRCRAFT
Maiden successful flight-test of Power
Take off (PTO) Shaft was conducted on Light Combat Aircraft (LCA Tejas) Limited Series Production (LSP) - 3 aircraft in Bengaluru on March 14, 2023. The PTO shaft, indigenously designed and developed by Combat Vehicles Research & Development Establishment (CVRDE), Chennai is a critical component in the aircraft, and will support the requirements of future fighter aircraft & their variants and offers competitive cost & reduced time of availability.
The PTO shaft was designed with unique innovative patented ‘Frequency Spanning Technique’ which enables it to negotiate different operating engine speeds. The light weight high speed, lubrication free PTO shaft transmits higher power between aircraft engine gear box and Aircraft Mounted Accessory Gear
Ministry of Defence, on March 7, 2023, signed contract with Hindustan Aeronautics Limited (HAL) for procurement of 70 HTT-40 Basic Trainer Aircraft at a cost of over `6,800 crore. The HTT-40 is a turboprop aircraft possessing good low speed handling qualities and provides better training effectiveness. This fully aerobatic tandem seat turbo trainer has an air-conditioned cockpit, modern avionics, hot re-fueling, running change over and zero-zero ejection seats.
The aircraft will meet the shortage of basic trainer aircraft of Indian Air Force for training of newly-inducted pilots. The procurement will include associated equipment and training aids including simulators. Being an indigenous solution, the aircraft is configurable for upgrades to incorporate the futuristic requirements of the Indian Armed Forces. The aircraft will be supplied over a period of six years. The HTT-40 contains approximately 56 per cent indigenous content which will progressively increase to over 60 per cent through indigenisation of major components and subsystems. The HAL would engage the domestic private industry, including MSMEs, in its supply chain. The procurement has the potential to provide direct and indirect employment to thousands of people spread over more than 100 MSMEs.
MoD SIGNS CONTRACT FOR SIX DORNIER-228
Ministry of Defence, on March 10, 2023, signed a contract for procurement of six Dornier-228 aircraft for the Indian Air Force (IAF) from Hindustan Aeronautics Limited (HAL) at a cost of `667 crore. The aircraft was used by IAF for Route Transport Role and communication duties. Subsequently, it has also been used for training of transport pilots of the IAF. The present lot of six aircraft will be procured with an upgraded fuel-efficient engine coupled with a five bladed composite propeller. The aircraft is ideally suited for short haul opera- tions from semi-prepared/short runways of the North East and island chains of India. The addition of the six aircraft will further bolster the operational capability of the IAF in the remote areas.
Aeronautics Signs Contract With Finnish Defence Forces
egy to deliver the combat proven BARAKMX Air and Missile Defence (AMD) system providing effective defence to the ADF and Australian national assets, rapid initial operational capability (IOC), and a proven path to Australian industrial sovereignty in the AMD realm.
Boeing To Produce 184 Apache
Boeing will build 184 AH-64E Apaches for the US Army and international customers, including the first Apaches for Australia. This $1.9 billion award brings the total current funded value of the contract to $2.1 billion, and has the potential to increase to more than $3.8 billion with future obligations.
for 12 jets and Lockheed Martin has received a contract to begin its long-lead activities. Bulgaria has also signed an LOA for an additional eight jets for its fleet. Once these are finalised, the backlog will increase to 147.
LOCKHEED MARTIN, KOREA AEROSPACE INDUSTRIES ANNOUNCE PARTNERSHIP
Lockheed Martin, Korea Aerospace Industries and Red 6 Aerospace announced a new partnership that will deliver advanced 21st Century Security capabilities across a spectrum of training and combat aircraft.
Aeronautics Ltd, leader in designing, developing and manufacturing Unmanned Aerial Systems (UAS) for the global defence, HLS, and markets announced that it has signed a mid-life upgrade contract with the Finnish Defence Forces (FDF) for its existing Orbiter 2 Mini UAS array. Under the terms of the contract, Aeronautics will provide the FDF with a comprehensive mid-life upgrade package that includes a full suite of sensors, avionics, and data-processing systems to enhance the system’s performance. The contract will also involve a substantial transfer of know-how, increasing the FDF’s level of self-sufficiency, and assuring the customer of Orbiter 2 array maintenance and support capabilities for the next decade.
Iai And Daronmont Tech Sign Mou
The US Army will receive 115 remanufactured Apaches, with an additional 15 Apaches to be procured as options, ensuring significant savings to taxpayers. The additional 54 aircraft will be delivered to partner nations as part of Foreign Military Sales. This award comes on the heels of the US Army’s Apache fleet surpassing five million flight hours, a milestone proving the AH-64 is the most capable, reliable and versatile attack helicopter.
Boeing Global Services will continue to deliver optimal readiness for the warfighter including training devices, spare provisions, support and test equipment kits, depot support, field engineering and technical manuals.
BAHRAIN’S FIRST F-16 BLOCK 70 AIRCRAFT
The partnership will initially bring Red 6’s revolutionary augmented reality platform, the Airborne Tactical Augmented Reality System (ATARS), into the TF-50 and variants. The system gives pilots and ground operators new capabilities to see and interact with synthetic threats in real-time, high-speed environments. The TF-50A is configured as a light attack fighter/trainer with additional enhancements to include radar, electronic warfare system, tactical data link, and other capabilities to meet Air Combat Command requirements. While the ATARS system is initially targeted for the TF-50 and variants, it could eventually be applied to operational Lockheed Martin platforms such as the F-16, F-22 and F-35.
Industry
LOCKHEED MARTIN AND TATA GROUP SIGN MoU
Lockheed Martin and Tata Group have reached an agreement to begin the implementation of fighter wing production at the companies’ joint venture, Tata Lockheed Martin Aerostructures Limited (TLMAL), in Hyderabad, India. The Memorandum of Understanding (MoU) envisions production of 29 fighter wing shipsets, with an option of additional shipsets, and deliveries commencing in 2025.
Israel Aerospace Industries (IAI) has signed an MoU with defence leader Daronmont Technologies, to deliver advanced air and missile defence capabilities for the purchase of defence systems and other ADF programmes. The signing took place as part of the AVALON Australian International Airshow.
IAI will leverage Daronmont’s proven integration, development and manufacturing capabilities as part of its broad Australian Industry Capability (AIC) strat-
Bahraini, American and Lockheed Martin officials celebrated the first F-16 Block 70 for the Royal Bahraini Air Force at Lockheed Martin, South Carolina. This F-16 Block 70 jet is the first of 16 jets for Bahrain, and took its first flight on January 24, 2023. From here, it will begin additional flight tests at Edwards Air Force Base before arriving in Bahrain in 2024.
Six countries have selected Block 70/72 aircraft. In addition to the current official backlog of 127 jets to-date to be built in Greenville, Jordan has signed a Letter of Offer and Acceptance (LOA)
Lockheed Martin formally recognised TLMAL as a potential co-producer of fighter wings in October 2021 following TLMAL’s successful production and qualification of a prototype fighter wing shipset. That achievement further strengthened Lockheed Martin’s partnership with India; and supports its F-21 offering for procurement of 114 new fighter aircraft — exclusively for India and the Indian Air Force — by proving additional indigenous production capability. The India F-21 represents an unprecedented strategic and economic opportunity for the United States-India relationship to future advanced technology cooperation. l