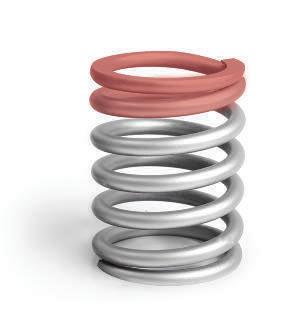
3 minute read
Dean of Springs
When Are the “Dead” End Coils Active?
By Dan Sebastian
In spring design 101 we are taught that the end coils, which have almost no pitch or touch the adjacent coil, should be treated as inactive for calculations. In general this is true, but in certain applications they can become active. This is most common in highly dynamic applications.
High Speeds*
In certain applications, springs are expected to operate at very high rates of speed. If the speed approaches the natural frequency or one of its nodes, serious problems can occur. A node is a fraction of the frequency (i.e. 1/2, 1/8, 1/11, 1/13). This is normally not a factor if you are higher than the 13th node (1/13). If you are in a danger zone, the end coils can become active as a surge wave is generated; the wave will reflect off the stationary end, which can cause it to leave its seat and results in no load on the contact surface.
The spring designer can lessen the effect of these surge waves by building in very “slow closings” or even adding inactive coils. In the case above, as the surge Inactive coils wave traverses down the spring, the inactive coils will become active. This changes the spring rate, which in turn changes the natural frequency and can dampen out the effect of the surge wave. This is something most spring designers can work with as long as they know the speeds (frequencies) that a spring will see. The challenge is how much room the device manufacturer has provided for the spring.
Impact Loading*
Another highly dynamic application that spring designers are asked to design uses a spring to absorb impact loads. The very nature of an impact load (the almost instantaneous stopping of mass) causes surge waves to be generated and then absorbed by the spring. In most cases, the spring will release the energy at a calculable force and return to its pre-loaded position. Over time, and due to the frequency of the impact load, the spring will have a finite life and produce a “normal” spring failure rate.
A number of years ago, one of our plants made springs designed for impact loading but encountered a very unusual failure mode. In spite of the typical failure mode for this kind of application, we saw springs that did not fail in the body but instead only the very end of the springs broke off. It took awhile for us to find the root cause. It turns out the inpact load was applied by a bar that was not larger than the spring’s OD.
When the surge wave returned and the bar was still in place, the forces were so great that the top would bend backward around the bar after a number of repetitions. Then it would break off just like a paper clip breaks after a few cycles of bending.
Conclusions
It turns out that dead or inactive coils can become active in highly dynamic enviroments. This is why a spring designer must understand how and how often (cycle frequency) the spring must respond to the forces. Beyond the calculated loads and contact forces, you will also have to carefully look at the material selection. As in any fatigue application, it is important to understand the effect of strength and fracture toughness in the material selected. n
* The calculations to support the design selection can be found in the SMI “Encyclopedia of Spring Design” in the compression, extension, garter and torsion spring section.
Dan Sebastian is a former SMI president and currently serves as a technical consultant to the association. He holds a degree in metallurgical engineering from Lehigh University and his industry career spans more than four decades in various technical and management roles. He may be reached by contacting SMI at 630-495-8588.