
10 minute read
Be Aware Safety Tips
OSHA’s New Era and An Important Topic for the Spring Industry
By Laura Helmrich-Rhodes, CSP, Ed.D.
As this article is being written, the presidential ballots are being counted. It looks like we will be under the leadership of the Democratic Party, which usually leads to greater regulation, oversight and enforcement of safety, health and environmental laws. As the new era begins, we can anticipate the hiring of more Occupational Safety and Health Administration (OSHA) inspectors and the filling of the assistant secretary of labor for OSHA opening quite quickly. A new agenda will emerge and will likely focus on greater enforcement since that was a frequent criticism of the Republican-run OSHA.
The apparent new administration’s emphasis on limiting the spread of COVID-19 will likely be a part of the OSHA agenda for workforce protection. To date, there have been more than $2 million in citations for COVID-19 related violations, mostly in health-related work sectors and the food industry. This is likely to encompass other work sectors, streamline the employee complaint process and increase inspection priority. It is important that your company follows the Centers for Disease Control and Prevention (CDC) guidelines, OSHA respiratory protection standards and abides by the OSHA recordkeeping rules (see helpful links below for guidance). It is also important to be ready for wall-to-wall inspections should an inspector arrive for whatever reason.
Material Handling Important Regulations — All Spring Companies Can Relate
The efficient movement of materials in a company may be one of the most important decisions made for profitability, quality and employee well-being. Industrial engineering assures the most efficient set up, but it is the department supervisors and shop floor workers who keep safe and efficient products moving.
There are many regulations addressing how materials are transferred into, around and out of your facility. These regulations vary by state, so be sure to look beyond the federal regulations that include, but are not limited to, walking working surfaces, cranes and hoists, forklifts, conveyors and ropes/ chains/slings. This discussion will pinpoint employers’ obligations to prevent injury due to slings as well as help to implement the management of this key operation using 6S methodology. There are regulations also which depend on specific operations. For example, if you are dipping or coating or subjecting hoist and slings to high temperatures, then you would need to consult those obligations too.
The loss of raw materials and finished product are far outweighed by the loss of an employee due to crushed fingers, caught between equipment or even struck by the load. There is not only the downtime associated with the loss, but there is an obvious moral imperative to protect employees. Prevention of loss increases efficiency and employee morale by demonstrating a culture of caring. Loss of profits to citations is another consideration. For the period October 2019 to September 2020, OSHA cited all employers more than $2 million for just the material handling general standard alone (29 CFR 1910.176) More specifically, U.S. manufacturers incurred 32 citations at 27 facilities and carried $127,466 or almost 59 percent of all the penalty cost.
It is important to define what constitutes a “sling” for this discussion. According to OSHA “slings are made from alloy steel chain, wire rope, metal mesh, natural or synthetic fiber rope (conventional three strand construction), and synthetic web (nylon, polyester and polypropylene).”
Examples of slings can be found on page 16 and are taken from the OSHA standards.
It is easy to find information on the care, use and storage of slings. Always start with the manufacturer’s requirements then move to the OSHA standards. Never use any slings or components that are not legibly marked with the manufacturers name and capacities. Remember that repairs can only be made by the manufacturer - no bolts, splices or welds to any material handling equipment!
Finding information on the “how to” of material handling safety management is more elusive. Knowing the regulations is the easy part. The day-to-day implementation of safety can be the real challenge. (I equate this to the doctor telling a patient to lose weight but doesn’t give the “how to be successful” guidance.) A formal written sling or material handling safety program is best and should look like any of your other written
Laura Helmrich-Rhodes, CSP, Ed.D., is an independent regulations compliance consultant to the Spring Manufacturers Institute (SMI). A former member of PA/OSHA Consultation, she is an associate professor in the Safety Sciences Department at Indiana University of Pennsylvania where she teaches graduate and undergraduate classes on topics such as OSHA standards, safety communications, workers’ compensation and human relations. Rhodes is available for safety advice and information. Contact SMI at 630-495-8588 or laurahrhodes@gmail.com.
ISO procedures or SOPs, as long as they include the key elements of responsibility, accountability and authority. Inserting the sling safety steps into your established quality initiatives works well so that everyone is equating personnel loss/ injury to error.
For the sake of connecting safety to the quality product/service efforts, let’s look at where you can insert sling safety into a 6S, Lean or any quality product program. Using the 6S methodology example of OSHA sling requirements will be shared. Let’s look at each of the 6S components:
Sort
In the sort step we eliminate whatever is not needed. It is obvious that what is not used needs to be removed from the work area to assure only the items needed are on hand.
OSHA is very clear that slings that are damaged or defective must not be used.
Leaders In Double Disc Technology
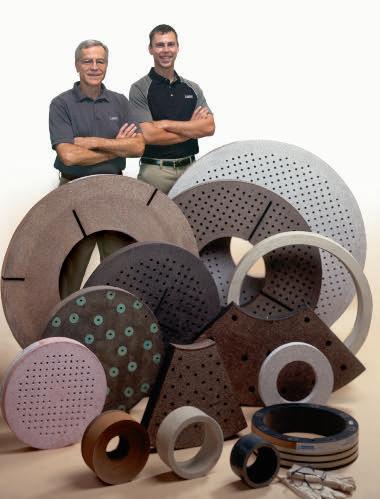
Jack and Jeff Shoemaker, second and third generations continuing the tradition at Anchor Abrasives. Certified to ISO 9001 since 1994.
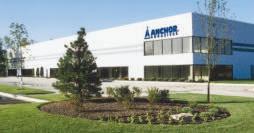
At Anchor Abrasives we specialize in the design and manufacture of resin, epoxy and oxychloride bonded nut inserted discs and cylinders...plus centerless and rollwheels.
Today, in our modern manufacturing facility, we are ready to continue our tradition of innovative quality products and unmatched customer service. For more information contact Anchor Abrasives Company, 7651 West 185th Street, Tinley Park, IL 60477 U.S.A. Phone: 708-444-4300; Fax: 708-444-1300.
www.anchorabrasives.com They actually talk about the removal of damaged slings and attachments more than once in the regulations. Surprisingly, the regulation is very specific on the removal of items. For example, it is worth learning the threshold for discarding both hooks and wire rope:
if hooks are cracked, have been opened more than 15 percent of the normal throat opening measured at the narrowest point or twisted more than 10 degrees from the plane of the unbent hook they must be discarded. 1910.184(e)(9)(ii) and Wire ropes must be discarded if there are 10 randomly distributed broken wires in one rope lay, or five broken wires in one strand in one rope lay. 1910.184(f)(5)(i)
Set in Order
This step gets us to organize what remains to allow for easy access for use. This includes organizing the workspace so that items are in close proximity. OSHA addresses setting things in order in standards for the storage of materials in 29 CFR 1910. 176 by requiring secure storage and housekeeping. They also require that permanent aisles and passageways be permanently marked if mechanical handling equipment is used. See 29 CFR 1910.176 (a).
A manufacturer,s recommendation will indicate if the slings, and especially ropes, should be hung for storage or coiled. Avoiding sharp edges for hanging slings over is important. Building a specific storage jig to properly store ropes, chains, and rigging attachments is a great way to keep these items in order.
Shine
In the quality world,cleaning the work area daily (or at some set frequency) advises using cleaning times as an opportunity for inspection. OSHA addresses this in material handling by specifically requiring that areas be kept clear of accumulations of materials that constitute a hazard and assuring safe clearances. See 29 CFR 1910. 176(c) There are also specific inspections frequencies set forth. It is likely that most employers are out of compliance on this
specific standard, especially the documentation portion which states:
Inspections: Each day before being used, the sling and all fastenings and attachments shall be inspected for damage or defects by a competent person designated by the employer. Additional inspections shall be performed during sling use, where service conditions warrant. Damaged or defective slings shall be immediately removed from service. 29 CFR 1910.184 (d)
Creating accountability for this activity is paramount by determining who will perform the inspections. For alloy chain slings, OSHA has a formal definition of a competent person. The easiest way to remember it is one who has skill, knowledge and authority given by the employer. There are additional inspection requirements for attachments and specific types of slings in the standard that should be reviewed. An example
Standardize
The 5S and 6S protocol instruct us to standardize by scheduling regular cleaning and maintenance, as well as formalizing best practices in the work area. Every process is done in a standard way. This supports the idea of formal written procedures for all aspects of safety, including forklift safety, cranes and hoists, slings, chains and ropes.
Slings have to be padded to protect from sharp edges. This should be a standard practice to not only protect the employee and the load, but it can also increase the life of slings by reducing costs. OSHA also says that the load cannot be pulled from under the load when the load is on the sling. This can be eliminated by great training and consistent supervision.
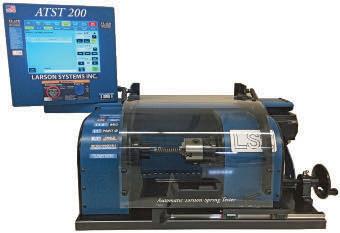
Sustain
Make 6S a way of life. This means training, cleaning and self-discipline. It also means that everyone must follow the process and be open to improvement. Individual workers need to be assured that material handling items are properly stowed when not in use and inspected/disposed of properly. The role of the supervisor in assuring that these items are carried out cannot be overemphasized. It is the supervisor who determines the time pressure under which the work is accomplished and time allotted for the care of equipment. If the workers know that supervisors are counting on them to complete tasks safely then it does become a way of life, or what I call a culture of caring.
Safety
This is integral to each of the elements above and allows focus on any additional safety issues, such as reporting hazardous situations.
Benefits of Implementing Sling Management Practices
One advantage of being an older safety professional is I’ve seen things come and
go. As my career began, Total Quality Management (TQM) was being touted as the solution to all our manufacturing problems. Then came other approaches like the advent of ISO standards, Lean, 5S and so on. I’m not a proponent of any one system, I have taught the precepts of them all in safety sciences classes but I have never seen a one-size-fits-all approach. Customers often say they take parts of each system that work well for them. I have found in my years with the springmakers that there are specific reasons for committing to ISO, and many spring and wire manufacturers participate in those quality mandates. (By the way, I always like to mention that ISO has a standard for safety too.)
The benefits associated with the implementation of 5S to business are easily generalized to the material handling portion of your operations and were used merely as a framework for this discussion. Specifically, implementing 6S reduces potential risks associated with sling misuse, damage to raw materials,
Triangle fitting Length Measured pull to pull when flat
Triangle-choker (Type I) Choker slot
Fitting eye
Choker fitting
Length Measured pull to pull when flat

Triangle-triangle (Type II)
Lap Length
Eye and eye with flat eyes (Type III) Eye product or injury, increases the equipment availability when needed for tasks, lowers defect rates, reduces costs, increases production flexibility, improves employee morale, better asset utilization and enhance enterprise image to customers and management. Use your own quality scheme and take time to insert material handling training, inspections, and other important steps into those already implemented practices. After all, the safe and efficient movement of raw materials and finished products are the key to business operations. n
Helpful Links OSHA one-page summary of OSHA Guidance for COVID Protection in the Workplace
https://www.osha.gov/SLTC/ covid-19/covid-citations-lessons. pdf?fbclid=IwAR2BMfDxzdbb-35Ul4wxbhlSiUVeVIvpoJfIC-RTH49Hdhdsw4hKqwNycUU
Frequently Asked Questions COVID-19
https://www.osha.gov/SLTC/covid-19/covid-19faq.html
Sample Sling Safety Program
https://case.edu/ehs/sites/case.edu.ehs/ files/2018-02/Crane%2C-Hoist-and-SlingSafety-Program.pdf
Lift All Sling Inspection Training Video
https://youtu.be/unvB4acQU9k
Length
Eye and eye with twisted eyes (Type IV)
Length
Important Federal OSHA Regulations
1910. 22 Walking Working Surfaces 1910. 132 Personal Protective Equipment 1910. 176 Material Handling General Requirements 1910. 184 Slings

Endless type (Type V)
Length
Return eye (Type VI)
Taken from https://www.osha.gov/laws-regs/regulations/standardnumber/1910/1910.184