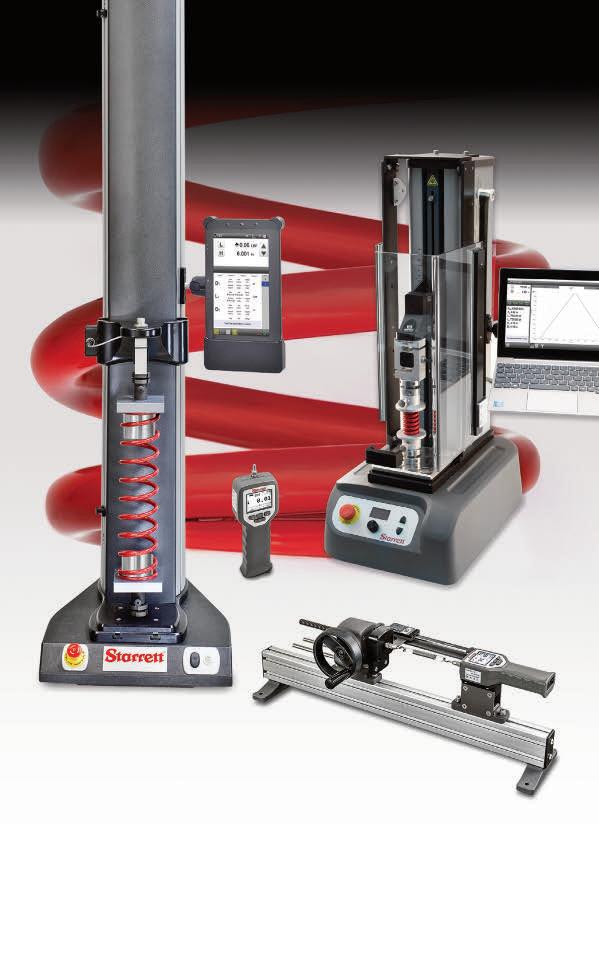
8 minute read
Be Aware Safety Tips
Leading and Lagging Indicators: Safety Performance Measurements That Inspire Culture
By Laura Helmrich-Rhodes, CSP, Ed.D.
Are you measuring safety, health and environmental performance by your OSHA or workers’ compensation experiences? In other words, are only lagging indicators being used to assess your environment health and safety (EHS) program? To determine if you are meeting/exceeding your goals, other metrics need to be considered, along with creating a formalized process for continuous improvement. Let’s first look at what constitutes a safety management system, then begin to identify meaningful metrics that assure a return on investment, and ones that can move the company’s safety culture in a positive direction.
Safety Management Systems
Companies operating in a federal OSHA plan in this industrial sector are not mandated to have a safety management system in place. Some state OSHA plans and certain types of business sectors do have obligations for formalized safety management. For example, California Injury and Illness Prevention Program (IIPP or I2P2) is a state regulation. OSHA did attempt to make formalizing safety programs required; however, those criteria are now called “OSHA Safety and Health Program Guidelines.” The concept of an SMS is simple; a systems approach to manage overall risk, achieve total worker health and measure corporate social responsibility.
During the Reagan/Bush administration, OSHA began to recognize exemplary performance by large organizations by creating the Voluntary Protection Program (VPP). Large organizations were recognized for implementing formal safety efforts using the “Guidelines,” Celebrating hours/days/years without lost time accidents is no longer acceptable practice; however, rewarding positive behaviors that typically reduce accidents is highly encouraged. For example, improved department audit scores for housekeeping, or percent usage of protective equipment over six months would be worth celebrating.
and it freed them from random OSHA inspections. It created a formalized partnership between big companies and OSHA. It also created an opportunity for data sets and measuring if these efforts really work. The National Safety Council reported in their 2014 “Journey of Excellence” that implementing an SMS reduces injuries 15 to 35 percent and has an estimated ROI of $3-$6 invested.
The OSHA Guideline framework includes the following elements: • Management Leadership • Worker Participation • Hazard ID & Assessment • Hazard Prevention & Control • Education & Training • Program Evaluation &
Improvement • Coordination & Communication on Multi-Employer Worksites
According to OSHA, the use of this framework can improve product, process and service quality, improve workplace morale, improve recruitment and retention, and provide a more favorable image and reputation among customers, suppliers and the community.
Since the introduction of this framework, other formalized systems have evolved and are parallel with the evolution of the quality initiatives we have all experienced since the days of Edwards Deming. American National Standards Institute (ANSI) Z10, which began to be formed in 1999 and last updated in 2019, includes provisions for internal safety audits and management review. This consensus standard group worked with the American Society of Safety Professionals to outline a more comprehensive safety management system than what OSHA outlined in the guidelines. Since the publication of ANSI Z10, a more global business perspective has emerged.
Your company may already be ISO 9001 and perhaps ISO 14001 compliant.
Laura Helmrich-Rhodes, CSP, Ed.D., is an independent regulations compliance consultant to the Spring Manufacturers Institute (SMI). A former member of PA/OSHA Consultation, she is an associate professor in the Safety Sciences Department at Indiana University of Pennsylvania where she teaches graduate and undergraduate classes on topics such as OSHA standards, safety communications, workers’ compensation and human relations. Rhodes is available for safety advice and information. Contact SMI at 630-495-8588 or laurahrhodes@gmail.com.
That same organization, ISO, in partnership with the American Society of Safety Professionals, has established its own safety management system, the ISO 45001. Like OSHA guidelines, it includes employer commitment and worker participation, hazard identification and controls, and training. In addition, it also includes provisions for monitoring and measurement for the purpose of improving the system. This standard has the same structure and terminology as the other ISO standards. Another positive difference with this SMS is that it addresses outsourcing and procurement (a topic discussed in a previous Springs column “Not Your Grandfather’s Independent Contractor”).
I would be remiss if I did not mention the use of incentive (reward) programs aimed at reducing accident frequency. These are not a substitute for a safety
INTRODUCING
Spring Testing REVOLUTIONIZED
The Authority on Accuracy.
NEW
Available with Basic or Advanced Software
Innovative Spring Testing Solutions
Starrett offers a complete line of innovative force solutions for spring testing. In addition, a new, affordable high volume production testing solution is available in basic software (S1) and advanced (S2).
MADE IN AMERICA
For more information visit starrett.com/springs
PRECISION TOOLS/GAGES
SPRING TESTING
spring inspection
system, and they are a violation of OSHA if they influence accident reporting. Celebrating hours/days/years without lost time accidents is no longer an acceptable practice; however, rewarding positive behaviors that typically reduce accidents is highly encouraged. For example, improved department audit scores for housekeeping, or percent usage of protective equipment over six months would be worth celebrating. Keeping work fun and engaging workers is more important than ever, so finding creative ways to both retain workers and reward exceptional performance is necessary. Keep in mind that it cannot influence accident reporting.
Meaningful Occupational Safety Metrics?
Most managers know that lagging indicators look back at events that have already occurred. The two best examples for this discussion are the Total Recordable Incident Rate (TRIR) and Days Away Restricted or Transferred (DART) rates. These rates and the reduction of Experience Modification Rates (EMR) have been what safety and HR professionals, along with senior management, have long used as measures of the effectiveness of overall safety efforts. It has been determined that this strategy is not scientific and other measures need to be implemented. Numerous modern studies have shown these data, along with other long held safety beliefs such as the “Safety Pyramids” by Heinrich and Bird, are invalid and should not be used for decision making (see Manuele, Walaski and Hallowell).
Instead, companies should use leading indicators as evidence of improvement in their safety management system. Leading indicators are those that are predictive and preventive. They offer feedback and show positive process movement. According to the Campbell Institute as reported by Pam Walaski (2020), 70 percent of organizations are still using lagging indicators only, while just 26 percent are using leading indicators to measure safety performance.
Much of the literature on safety leading indicators reminds leadership to not just tally events such as safety committee meetings, supervisor safety trainings or
Much of the literature on safety leading indicators reminds leadership to not just tally events such as safety committee meetings, supervisor safety trainings or incident investigations, but to also assess the quality of proactive and preventative events.
incident investigations, but to also assess the quality of proactive and preventative events. For example, it should not be the completion of a safety audit but the quality and improvements arising from the audits that should be measured.
John Doerr, author of “Measure What Matters” advises senior management to have “clear benchmarks” that are “black and white.” That way, everyone is clear as to what is important and how they will be measured. Using leading indicators that underline a commitment to employee safety, with resources allocated to perform them, are the best way to move the safety culture forward. If you are only celebrating no lost time accidents or a reduction in your experience rating, dig deeper to see what is really being celebrated. What happened that allowed that to occur? What system processes were improved that employees acted without error? Have step-by-step procedures been written to avoid error/accidents over that time period? Has training raised safety hazard awareness? Were new safeguards installed?
Conclusion
Large and small companies should consider implementing the new ISO 45001 standard, especially if ISO 9001 and/or ISO 14001 are already in place. Measure and celebrate the things that matter, the activities that display commitment to quality products and environmental health and safety! Use the continuous improvement methodology to move the safety culture forward too. If your company is interested in continuing this discussion and would like to formalize your safety program, be sure to turn to SMI for help. n
Sample Listing of Leading Indicators to Measure (Remember, it is quality not just quantity!)
• Hazard report completion • Safety suggestions • Supervisor trainings attended • Supervisor toolbox talks • Development/revision of job safety analysis (JSA) • Behavior based safety observations completed • Safety committee—percent attended, items completed • Maintenance completion time of safety related items • Employee retention rates • PPE Usage • Employee job trainings/retraining • Welding/hot work permits completed • Arc flash prevention permits completed
What we know about occupational safety:
• Injuries and illnesses have a negative impact on profits • Work stoppages cost money • Replacing injured or ill workers has cost • Damaged property, machinery and product is a measurable loss • Accidents are errors in the process • Efficiency decreases waste and can increase profitability • Worker knowledge and attention to tasks vary by individual • Motivation is personal • Indirect costs of accidents likely are far greater than direct cost
Bibliography and Helpful Websites
Burdick, Guy (April 8, 2021) Safety Management Systems — Which Is Right for You? https://ehsdailyadvisor.blr.com/2021/04/safety-management-systems-which-is-right-foryou/ (Retrieved 5/13/21) Esposito, Paul (March, 2021) Safety Through Accountability & Recognition, Professional Safety EHS Daily Advisor (April 7, 2020) Now’s the Time to Migrate from OHSAS 18001 to ISO 45001 https://ehsdailyadvisor.blr.com/2020/08/nows-the-time-to-migrate-from-ohsas-18001-toiso-45001/ (Retrieved 5/13/21) Hollawell, Mathew et al (April 2021) Statistical Invalidity of TRIR as a Measure of Performance,
Professional Safety (Retrieved 5/13/21) https://aeasseincludes.assp.org/professionalsafety/pastissues/066/04/F2Hallowelletal_0421.pdf?_ga=2.23679091.839002868.1620857329-871067188.1531924963 Manuele, Fred (2008) Advanced Safety Management: Focusing on Z10 and Serious Injury
Prevention, Wiley Jack J. Phillips, Patricia P. Phillips, & Al Pulliam, ROI in EHS (Environmental Health & Safety),
ISBN: 978-1-118-63978-8, Scrivener and Wiley, print. Recommended Practices for Safety & Health Programs: Safety and Health Program Guidelines,
US Dept. of Labor, OSHA https://www.osha.gov/shpguidelines/docs/OSHA_SHP_Recommended_Practices.pdf Walaski, Pam (August 2020) The Role of Leading and Lagging Indicators, Professional Safety Walaski, Pam, (June 2017) Right Sizing Risk Management for Small and Medium Size Business
Professional Safety

