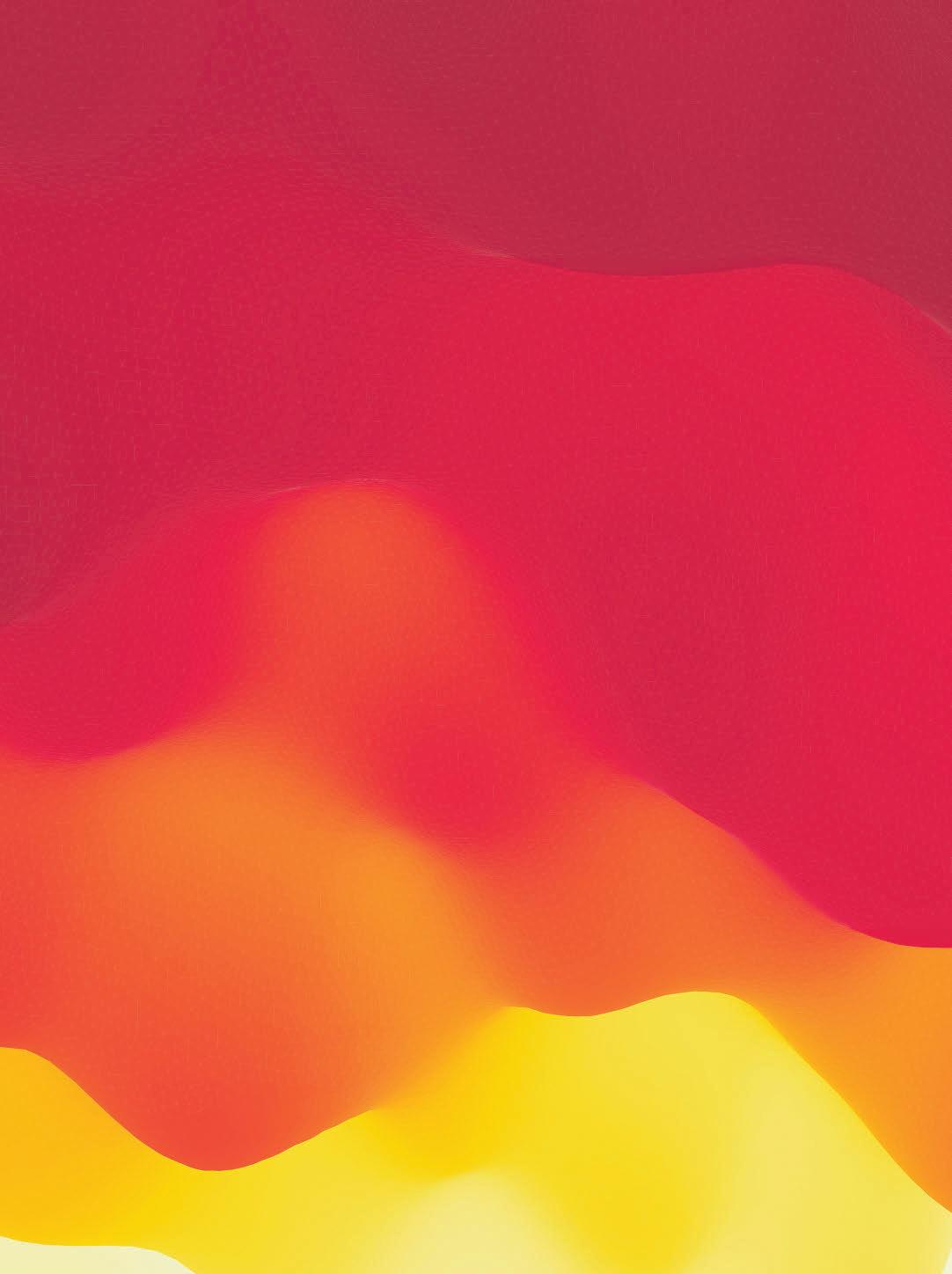
7 minute read
Time-In-Process and Belt Speed Control on a Conveyor Oven
By Daniel Pierre III
When comparing ovens for a new investment, one factor that influences your decision is the range of time you can keep parts in the oven. To a lesser extent, another is whether you can control your speed digitally or through a variable speed potentiometer. If you have a specific application in mind, you may know what speed or Time-In-Process (TIP) you require. If you need an oven for general use, one tends to select ovens with the widest range of speeds to maximize your flexibility.
Unfortunately, most specification sheets do not come with asterisks to further explain that you usually cannot get the entire range of speed indicated. To make things more complicated, there are additional speed ranges available for that oven. This lack of clarity illustrates that you need to utilize your relationship with your oven supplier to fully understand an oven’s capability. It is nearly impossible to compare “apples to apples” by just looking at the specification sheets. From an oven designer’s point of view, let me explain what goes on to develop the optimal drive system for an oven.
First, ovens are designed from the inside out. You have known wattages of heating elements and/or a known capacity of heating forced air. For electric ovens, there are limits to consider so you do not have nearby elements affecting another element’s performance. In the end, you have a heat chamber with the optimal heating power. Next, you determine how much mass can pass through the oven so it will not be overloaded, both physically and thermodynamically. These are the hard facts, and all sorts of formulas can assist in this design stage.
Now comes the “art” of the design. An oven designer must guess the typical loads that will be used in these ovens. This is where relationships with our customers as well as relationships with the makers of spring coiling machines are beneficial. The more oven designers can understand the probable load scenarios, the better we can calculate the stress relief needs of the parts, i.e., TIP. You are left with a range of speeds that are likely to be needed for this oven.
This is only half of the design, though. The harder calculations are understanding the torque needs based on the load range. The smoothness of the conveyor bed, the weight of the conveyor belt plus parts, the size of the drive drum and a customized torque wrench reveal the torque needs of the drive motor. Next comes the calculations based on the gear ratio (or choices of gear ratios) of various drive motors.
All of this information will give you a specific range of speeds possible for a particular motor on an oven. Typically, for digital speed control, the range of speed is limited to about 90 percent of the motor’s range. In analog potentiometers, you can often see that the motor stops before you crank the dial all the way to zero. Digital controllers can cut that dead space out.
Motor size Motor ratio Motor torque Motor TIP range
15 120:1 110 1~10.5 minutes
15 24:1 220 2~21 min utes
18 120:1 279 1~10.5 minutes
18 240:1 477 2~21 minutes
22 300:1 247 2.5~26 minutes
22 750 : 1 617 1.5~65 minutes
This is still not the whole story. Remember the mention of gear ratios on drive motors? Some motor makers offer different gear ratios in the same sized motor. It means one could swap motors to yield a different set of speed ranges. Please note that this comes at a cost of torque. While you might get the optimal speed range, the motor might not be able to handle the load. Some examples of this can be seen in Table 1.
If you wanted to process 17-7 stainless steel, you might think you are golden if you just swap in a size 22 motor with a 750:1 gear ratio. On a larger oven, this might be an option, but on a smaller oven, a larger motor might not physically fit in the space provided. A potential solution is changing the drive system to an indirect drive system and adding in yet another set of gear ratios. Often, the cost to fabricate a new motor mount and to add chain and sprockets is about a wash, adding with the cost of a larger motor with a favorable gear ratio. However, external gearing in this manner increases your torque and expands the overall speed range. [Specifically for 17-7 material, you should desire a 70-minute belt speed so you can have time to get the parts to 900F and hold for a full 60 minutes.]
If the range of parts you will run are similar enough to use the same belt weave, but you need the added flexibility to run the belt very slowly, there is always the option of buying the indirect drive system. It takes perhaps 30 minutes to make a changeover, plus a small change in programming for the digital speed controller. Your oven supplier can assist with that. If you have an analog potentiometer, just be warned that any previous markings you may have made on the dial such as “3 = 7 minutes” will change when you change the drive system, and your markings will have to be recalibrated.
If you look at Table 2, you will notice the new range of speeds and that there
Mapes: quality that’sMapes: quality that’s never out of tune. never out of tune.
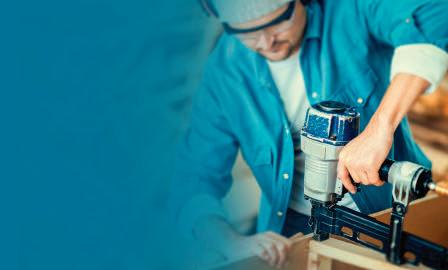
Choose Mapes Fine Music Choose Mapes Fine Music Wire for consistent quality. Wire for consistent quality. The high-performance wire high-performance wire for your demanding spring jobs. demanding spring jobs.
MAPES FINE MUSIC WIRE MAPES FINE MUSIC WIRE
Call for special wire needs and solutions, including restricted tensiles and size tolerances.
Wire diameter .063" – .006" / 1.6 mm – .15 mm
Coatings Phosphate, Tin Zinc, Tin Industry standards ASTM A228-18 ASTM A227-17 EN10270-1 AMS 5112N JISG 3521 SWA, SWB JISG 3522 SWPA, SWPB Military specifications Others, inquire
THE MAPES PIANO STRING COMPANY
P.O. BOX 700, ELIZABETHTON, TENNESSEE 37644 423-543-3195 • FAX 423-543-7738 www.mapeswire.com • info@mapeswire.com
ISO 9001:2015
certified QMS Your Preferred Supplier of Custom Springs from Design to Production
Beyond the Spring™
Helping you bring your industrial application or POP display to life
With innovative machinery, tooling and engineers, Vulcan Spring can deliver a spring solution for even the most challenging applications.
Contact us with questions or about a custom spring need today.
+1-215-721-1721 | VulcanSpring.com
is still a trade-off on the fastest speeds. For this oven, it would be impossible to have a total range of speeds from 2~73.5 minutes. If you will run applications that require 4-5 minutes for some parts and 65-72 minutes for another application, you will likely need to manually change the drive system (or buy two ovens!).
There is no one perfect oven that can handle all production runs, just like you would not use the same coiler to run 0.008” and 0.625” wire. A larger oven would be overkill for small parts, even though it might get you the belt speed range you desire. A larger oven’s belt weave could also be too open for smaller parts. The cost to maintain temperatures in a larger oven when running small parts also adds to inefficiencies. If you are considering an oven for general use, please discuss your potential applications so your oven provider can steer you in the right direction. Sometimes the better investment is buying an option, rather than buying an oven that is too large for the sum of your applications. n

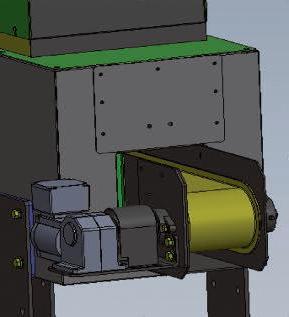
Pictured on the left is an indirect drive furnace option that can increase your belt speed range. Pictured on the right is a direct-drive furnace system that has minimal costs.
Table 2 How Indirect drive systems add torque, but limit speed ranges.
"indirect drive with 3.5 sprocket ratio"
Motor size Gear ratio Torque TIP Range Torque TIP Range
15 240:1 220 2~21 minutes 770 7~73.5 minutes
WIRED FOR PRECISION
Unsurpassed Quality Since 1959
Swift Turnaround Times Award Winning Service Prototypes to Full-Run Production
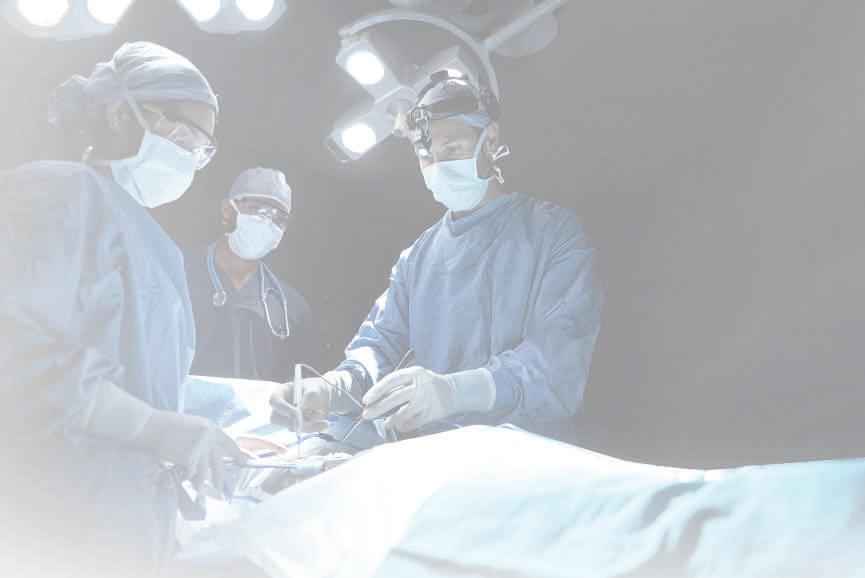
Certified ISO 9001:2015
97 Ronzo Road, Bristol, CT 06010 | (860) 583-1305 | RadcliffWire.com