
52 minute read
SMI Introduces First 300-Level Spring Design Course
SMI Introduces By Gary McCoy First 300-Level Spring Design Course
SMI’s technical director, Rick Gordon, presented the first offering of the association’s first advanced spring design training class, Spring Design 301–Springs Fatigue in January 2022. Thirty-nine students from 25 companies participated in the webinar which was well received with many favorable student comments. The training effort was supported by Todd Piefer, vice president, applications development at Universal Technical Systems, Inc. (UTS), SMI’s software partner. Piefer helped facilitate the class, administering quizzes and addressing student questions about the Advanced Spring Design software (ASD7).
Development of the 301 training module was championed by Jason Sicotte at Associated Spring/Barnes Group and Al Mangels at Lee Spring Company. Piefer at UTS provided important content using the ASD7 software. Additional team members included SMI president Bert Goering, Gary Van Buren and Gordon.
Based on student input, the next training modules selected for development are: 205–Beam, Constant Force, Spiral and Torsion Bar Spring Design and 206–Snap Ring Design. There has also been interest expressed for advanced 201, 202, and 203 classes.
In the 16 course offerings (201, 202, 203, 301) to date, 440 student training sessions have been taught both in person and virtually.
A second new class, 304 Springs–Dimensioning, Tolerancing, and Testing was scheduled to take place March 24, and SMI’s third new class, 206–Snap Ring Design will be offered Sept. 15.
Future class offerings in the popular basic (200 series) and advanced (300 series) include:
2022 Virtual Classes Date
201 Compression Spring Design Thursday, April 14, 2022 202 Extension Spring Design Thursday, May 19, 2022 203 Torsion Spring Design Thursday, June 16, 2022
301 Springs–Fatigue
Thursday, July 21, 2022 206 Snap Ring Design Thursday, Sept. 15, 2022 201 Compression Spring Design Thursday, Oct. 20, 2022 202 Extension Spring Design Thursday, Nov. 17, 2022 203 Torsion Spring Design Thursday, Dec. 15, 2022
SMI will present two in-person classes at the 2022 CASMI SpringWorld event as shown below:
2022 In Person Classes — CASMI SpringWorld Date
301 Springs–Fatigue Wednesday, Oct 12, 2022
304 Springs–Dimensioning, Tolerancing and Testing Thursday, Oct. 13, 2022
Training Overview
SMI’s spring design training program consists of three fundamental, seven basic, and four advanced spring design training classes. Fundamentals courses were developed with new hires and non-technical staff in mind. Basic classes are designed to meet the needs of production and technical staff, including engineers, designers and inspectors. Advanced courses address a higher level of expertise for engineers, designers and other technical staff. The SMI technical committee has been working to develop these programs.
Two fundamentals training modules, “Spring Fundamentals” and “Overview of Spring Making Materials,” are available to the public on the SMI website: www.smihq.org. SMI member feedback for these modules has been very favorable.
Courses are organized as focused, real-world spring design training programs, combining basic spring design content for each spring type with practical hands-on use of SMI’s wellrespected ASD7 software. For each spring type, students will learn: • The seven-step spring design process • Definitions and terminology • Design theory • Design stress analysis • How to input engineering design data into the ASD7 software • Important ASD7 tolerancing criteria
Classes benefit students by increasing their spring design knowledge and benefit their company by having an SMI-trained associate as part of their team.
For more information, visit www.smihq.org or contact Dina Sanchez at dina@smihq.org. n
SMI has a team of experts, who speak the language of springs, ready to assist you. It could be a metallurgy question about fatigue life or corrosion. Or perhaps you need help with a spring design and the use of materials when manufacturing springs. To find out how SMI Technical Services can help you, phone 630-495-8588 or visit www.smihq.org/springsadvice.
Flashback
SMI Annual Market Summary
As Kelley Christy of Diamond Wire Spring and chairman of SMI’s Benchmarking Committee stated in the Committee Connection article on p. 63, there is great value in measuring your company against the rest of the industry.
“Our company has benefited greatly from the SMI Annual Market Summary because it helps us understand our business as compared with others in our industry, but it also provides us with an individualized report,” stated Christy.
In this edition of Flashback, we publish data from the annual market summary reports from 1981 and 1982. Enjoy this look back from the October 1983 issue of Springs and reflect on where we have come as an industry over the past 40 years. n
©iStockphoto.com/tostphoto Five Questions

Gibraltar Corporation
Five Questions provides an opportunity for SMI associate members to tell the spring industry about the products and services they offer. In this edition, we talk with Michael Shapiro, President, Gibraltar Corporation.
1|Can you tell us about the history of Gibraltar Corporation? Gibraltar was started in 2005 as the North American agent of Simco. Since 2005, we’ve expanded our product line offering with Pyromaitre’s high speed stress relieving and tempering furnaces, YSM verstislides, SAS testers, Delta, our own line of cost effective small wire CNC coilers, 2-8mm formers, and single and double table downfeed grinders. We also offer cost effective, high quality carbide spring tooling with suppliers in Korea, Taiwan and Italy.
2|What are the latest trends in springmaking and wireforming equipment? The common denominator in the industry is lack of labor, so all trends are focused on increased use of automation, increasing production speed of the equipment, real-time inspection and ease of usage.
3|Gibraltar represents several different machinery and accessory manufacturers. What advantage does that provide to springmakers? Our slogan is ‘one source, many solutions.’ We offer a variety of options and solutions at different price points to suit the individual needs of our customers, all of which are backed by our responsive service and support.
4|How has the pandemic impacted your business during the past two years? In many ways. We’ve pivoted many of our in-person visits and meetings to video for sales, support and training. We now stock more machines, tooling, and spare parts due to the extended lead-times and logistical delays. We try to be proactive when possible, but we had no plan for the pandemic so we adapted as required.
5|Can you tell us about a recent challenge that you were able to solve for a customer? With every day comes opportunities to assist customers and solve problems. Our business is based on addressing customer challenges, including technical, budgetary, logistical, support and providing responsive responses and solutions. n
Gibraltar Corporation 1945 Techny Road Unit 5 Northbrook, IL 60062 Phone: 847-383-5442 mshapiro@gibraltar8.com www.gibraltar8.com
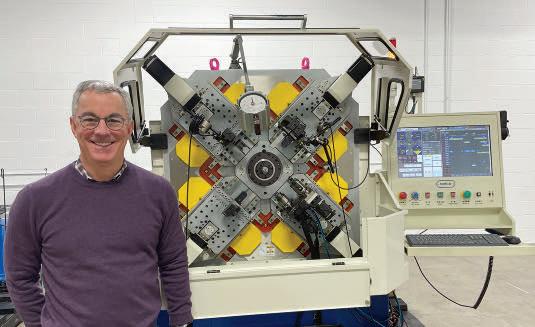
Michael Shapiro
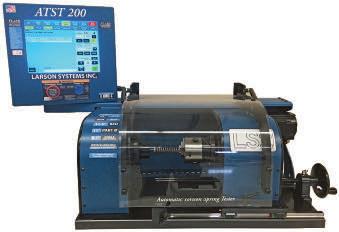
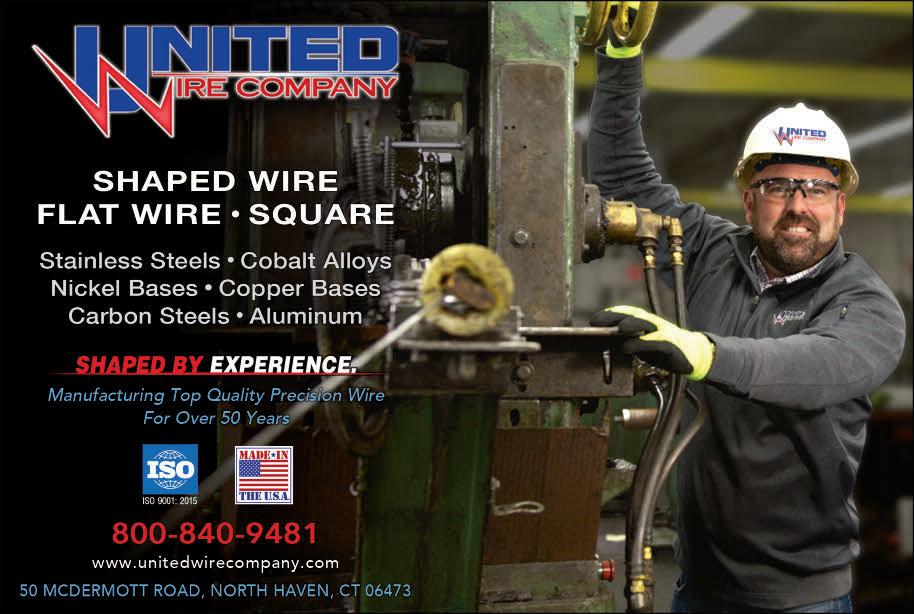

Springmaker Spotlight
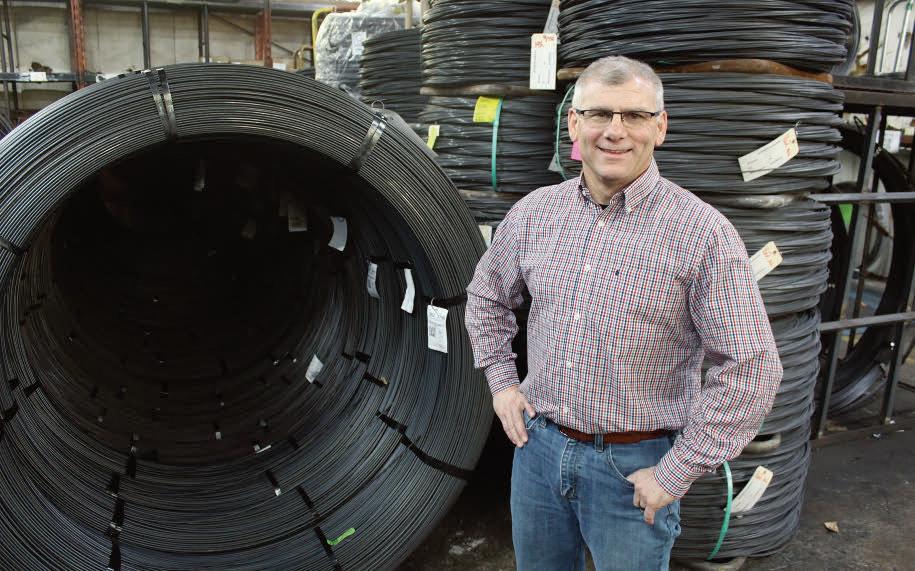
Gene Huber, Jr.
Faith and Family
A Profile of Gene Huber, Jr. and Winamac Coil Spring
By Gary McCoy, Managing Editor Gene Huber, Jr., the incoming president of SMI, has fond memories of growing up in the spring industry at Winamac Coil Spring in Kewanna, Indiana. It’s the company his maternal grandfather, Walter Pesaresi, started back in 1948.
Huber remembers coming to the plant with his grandpa and occasionally on Saturdays when his father, Gene Huber Sr., needed to get some work done. He fondly recalls one Saturday pushing a hand cart with his brother, Chad Huber, through the aisles of the factory.
“We ran into a barrel of springs in the dark and they happened to be shiny gold brass. We hit that barrel and right then the buzzer for the morning break went off. There was not a soul in factory besides us. We thought we had broken into Fort Knox, and we ran like crazy,” recalled Huber with a chuckle.
The two brothers did not destroy the factory and are now part of the thirdgeneration leadership team that runs Winamac Coil Spring. Huber serves as
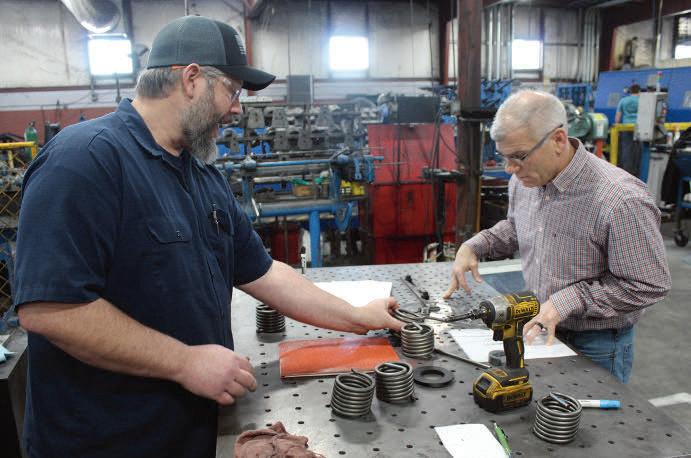
Huber, Jr. (right) working on part development with Phil Fritz.

Sean Rainford displaying his work cell at the company’s plant two. executive vice president and Chad is the vice president of operations over the company’s three manufacturing plants. They work together with their cousins Tony Pesaresi, company president; Andrew Pesaresi, who until recently was the division manager of the company’s wireform division and now works in the purchasing department; and DJ Pesaresi, vice president of purchasing.
In addition, several fourth-generation family members are now part of Winamac Coil Spring, including Huber’s son, Eric, who works in the company’s machine build design and software areas, and son Brock, who works in the maintenance area and will become the department manager when a longtime employee retires in May. Tony Pesaresi’s son, Garrett, heads up the company’s wireform division located in nearby Winamac.
Huber is quick to point out that, in addition to family, there is a strong contingent of outside talent to bolster the company in sales, production, engineering, quality and floor management.
The Path Forward
Huber said the third-generation leadership team has built upon the success of its second-generation predecessors that included the late Joe Pesaresi, president, Dan Pesaresi Sr., chairman, Gene Huber Sr., chief financial officer and Barb Huber, corporate secretary.
In an article on Winamac Coil Spring published in the Winter 2010 issue of Springs, Joe Pesaresi remarked about the third generation that would someday lead the company. Joe said the biggest issue the next generation would face is “finding the right people that will work with them, like Gene, Danny and I did. I hope they’re blessed with that,” he said. “We were just fortunate to have the right people through the years. And they’re hard to find today.”
The challenge for the third generation to uphold their grandfather’s value of hard work and determination was tested early on when they took over the company in 2015.
“At the time when the second generation retired, the third generation had a very minority ownership of the company,” said Huber. “We chuckle that we owned the hubcaps.”
The company had just bought its new plant in Winamac to house its wireform division at about the same time one of Winamac’s biggest product lines in the ag sector took a sharp decline. “It was something that the ag world had not done in a long time,” remarked Huber.
That downturn lasted nearly five years. “We joke that we got handed the keys to the car and we didn’t have a steering wheel,” lamented Huber.
Huber says they made it through, and recently implemented a new ERP system and several different lean protocols.
Other than that early challenge, Huber says the transition between generations went very well except for when it came to changing offices.
“Both dad and uncle Joe went away for the winter, and at that point they still came into the office just about every day,” explained Huber. “Because we were looking to expand the offices, Tony and I had decided we would have different offices at a more convenient location. They both said, ‘No, no, just take over our offices. We’ll find someplace to be.’”
While the second generations leaders were away for the winter, the move took place.
“I wouldn’t suggest it that way,” said Huber with a laugh. “We put ‘executive wing’ over a hallway that led to their offices. And when they came back there were a lot of quiet moments.”
I remember hearing my dad explain his new office to somebody. “They said, ‘Gene, nice new office,’ and he said, ‘It’s just a closet.’”
Growth Opportunities
Winamac Coil Spring continues to be known for manufacturing compression, extension, single and double torsion springs, and wireforms working with wire sizes ranging from .008" to .625". They serve a variety of markets, including agricultural, off-road recreational, lawn and garden, railroad, appliance, construction, recreational vehicles, irrigation, valving, industrial, furniture and general industrial.
In 2020, Winamac Coil Spring was inducted into the Indiana Manufacturers Association’s Hall of Fame. When the company received the award, Tony Pesaresi remarked, “From rural Indiana we supply six of the world’s top agriculture equipment companies, as well as some of the most recognized brands in the offroad power sports industry.”
The company employs 170 workers among its three plants, two in Kewanna and one in Winamac. The company has nearly 250,00 square feet of factory space with room to expand. Huber says they could still use more people if they could just find them. He says the automation of many processes has allowed them to do more with less.
Huber says the company continues to follow the motto: “We like to innovate and fix people’s problems.”
He says they often say to customers: “Let us jump in where you’ve got a problem and let us become the supplier you don’t want to live without.”
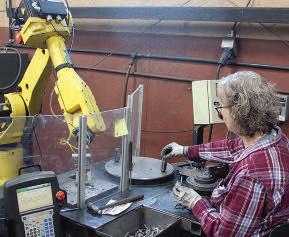
Barbi Baldwin at her work station at the company’s plant one.
Eric Huber works in the company’s machine build design and software areas.
A banner at Winamac Coil Spring that displays the company’s values to its employees.
Extension springs continue to be an important part of the company’s product offerings.
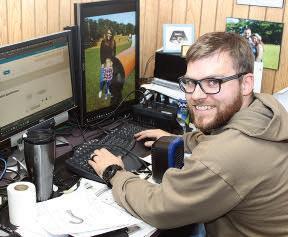
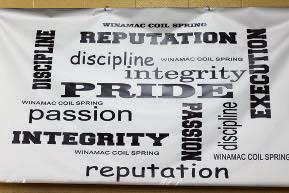

Huber says engineers are typically conservative by nature, but he says there are times when you have to say, “It looks like a risk, but it’s one we’re willing to try.”
It harkens back to company founder Walter Pesaresi, who was often known by the phrase: “We may have to fix it later, but just keep moving.”
He says they are currently looking at a recap of their finishing department (grinding) and to move ahead with new technology.
Huber says they are also looking at mergers and acquisitions (M&A), “meaning, is there something out there we should diversify into?”
Winamac Coil Spring has never been a supplier to the automotive industry, but Huber says they recently helped design a part for a customer that will go inside an engine.
“We’ll see if that goes any further, because that would almost be like an M&A,” explained Huber. “That would perhaps be the start of an LLC that we put on its own, but it would be a single product.”
Overall, Huber says the leadership team at Winamac Coil Spring is excited and positive about the future.
He went on to say, “A normal thing for us to say is that Kewanna, Indiana is not the mecca of the world, nor the corner on education and knowledge, but we love to learn from others in the industry.”
A Technical Start
With an engineering degree from Purdue University, it was only natural that Huber would first get involved with SMI as a member of the technical committee.
He’s always enjoyed what he calls the “pool of camaraderie” that SMI provides, because of the opportunity to bounce ideas off other technical experts like former SMI president Dan Sebastian and Jason Sicotte of Associated Spring.
“We’re all in like-minded businesses, which means we can talk about things we are doing to help each other without
Huber says the company continues to follow the motto: “We like to innovate and fix people’s problems.” He says they often say to customers: “Let us jump in where you’ve got a problem and let us become the supplier you don’t want to live without.”
8
Your source for the best in close tolerance strip and edged products.
strip: cold rolled high carbon/pre-tempered spring steels, coated, low carbon stainless, copper based alloys and aluminum ultra-narrow width, close-tolerance slitting edging: round, square, semi-round, deburred, custom, etc. oscillate (traverse) and ribbon wound coils ISO 9001: 2015 certified 43 years servicing the industry
tel. 847.537.2881 toolkinginc.com Wheeling (Chicago), Illinois 60090 USA
Mapes: quality that’sMapes: quality that’s never out of tune. never out of tune.
Choose Mapes Fine Music Choose Mapes Fine Music Wire for consistent quality. Wire for consistent quality. The high-performance wire high-performance wire for your demanding spring jobs. demanding spring jobs.
MAPES FINE MUSIC WIRE MAPES FINE MUSIC WIRE
Call for special wire needs and solutions, including restricted tensiles and size tolerances.
Wire diameter .063" – .006" / 1.6 mm – .15 mm
Coatings Phosphate, Tin Zinc, Tin Industry standards ASTM A228-18 ASTM A227-17 EN10270-1 AMS 5112N JISG 3521 SWA, SWB JISG 3522 SWPA, SWPB Military specifications Others, inquire
THE MAPES PIANO STRING COMPANY
P.O. BOX 700, ELIZABETHTON, TENNESSEE 37644 423-543-3195 • FAX 423-543-7738 www.mapeswire.com • info@mapeswire.com
ISO 9001:2015
certified QMS
giving away our own secret sauce,” explained Huber.
Huber jokes that he was on the technical committee long enough that he ended up becoming the committee chair.
He was later asked to join the executive committee, which would eventually lead him to become president of SMI. Huber will officially begin his two-year term as president when SMI holds its annual meeting in Scottsdale, Arizona, April 23–26.
While he is more comfortable with the technical committee because of his background, Huber says he enjoys the executive committee and the ability to engage with SMI in a different way.
“I always tell my wife, Sherri, ‘I feel like I got fortunate to sit in a room with a lot of smart people and if I keep my mouth shut, they won’t know what I don’t know,’” said Huber with a smile.
“I have grandparents, parents, aunts and uncles, and cousins who have all been involved in this industry for a long time,” said Huber. “We come from what you might call the ‘sticks,’ so it’s interesting for me to say that I’m the president of SMI. It’s humbling, and I look forward to trying to payback in some area for the many times SMI members have helped me and our company in the past.”
Staying Relevant
As he embarks on being president, Huber believes one of the challenges is keeping
Two Association Presidents, One Company
Gene Huber, Jr. and his cousin, Tony Pesaresi, might be the only individuals from one company in the spring industry to ever serve simultaneously as presidents of SMI and the Chicago Association of Spring Manufacturers (CASMI). Pesaresi has served as CASMI president since 2019 and is currently a member of the SMI board of directors as the CASMI representative. Pesaresi’s two-year term as CASMI president was extended due to COVID19 and will conclude in 2023.
Winamac Coil Spring’s legacy of association service started with Dan Pesaresi, Sr., who served as a CASMI board member and a one-year term as president in 1970. Dan’s son, DJ Pesaresi, also served on the CASMI board and was once in line to become CASMI president before needing to step aside for personal reasons.
“My uncle Joe enjoyed attending the SMI meetings, but he was not a committee guy,” explained Huber. In addition to CASMI, Huber says his uncle Dan served on several SMI committees and his dad was a member of the benchmarking committee.
On the distinction of two cousins being association presidents at the same time, Tony Pesaresi said they are both happy to add to their respective spring manufacturing organizations that each have a different purpose.
“Where SMI has a national, global and far-reaching focus, CASMI is
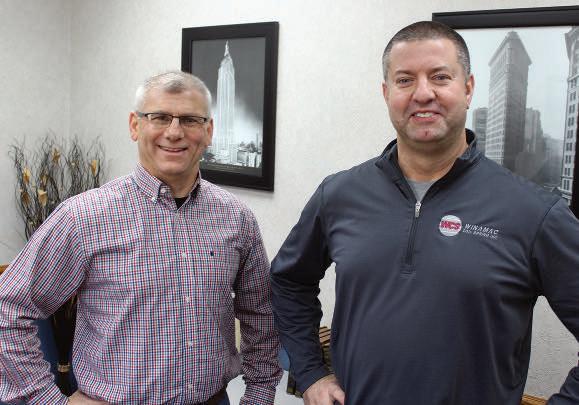
Gene Huber, Jr. and his cousin, Tony Pesaresi.
centered on being a regional group,” explained Pesaresi. “While they both have a different emphasis, it’s just an accomplishment for both of us to give back to our industry.”
Pesaresi said the honor of leading their respective associations exemplifies the roots they both have in the industry and “wanting to see the industry get better and to work together to make that happen.”
Pesaresi said that once Huber made the commitment to become more involved in SMI by joining the executive committee, “I let him know that I personally supported his endeavors with SMI, and that the company would stand by him 110 percent in whatever he needed. When I say ‘our company,’ that does mean a lot because we’re family.”
Pesaresi sends well wishes to his cousin on becoming the next president of SMI.
“Gene has already exemplified the technical aspects of the industry and has shared his knowledge for many years that way,” said Pesaresi. “I wish him the best when it comes to leading the overall organization as well, and I’ve told him that I am always here to help.”
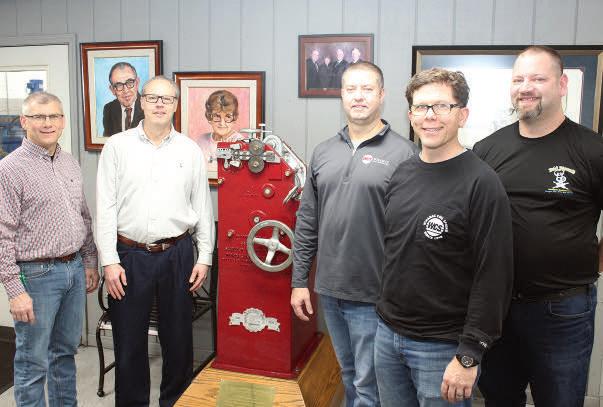
The third-generation leadership team at Winamac Coil Spring: Gene Huber, Jr., DJ Pesaresi, Tony Pesaresi, Chad Huber and Andy Pesaresi.
A great memory of the 2nd through 4th generations of Winamac Coil Spring at the 2016 CASMI SpringWorld trade show. Pictured front row (l-to-r): Gene Huber, Jr., Brock Huber, Gene Huber, Sr., Dan Pesaresi, Jr., Joe Pesaresi and DJ Pesaresi. Back row (l-to-r): Eric Huber, Andy Pesaresi, Garrett Pesaresi, Tony Pesaresi, Chad Huber and Kirk Huber.
A bench donated by
Winamac Coil Spring employees to honor the legacy of former president Joe Pesaresi, who passed away in 2018. SMI relevant to all companies who are members. As mergers and acquisitions have taken place in the industry, Huber asks, “Do these overarching corporations feel the same way about SMI as a private, family business owner does?” Huber believes they should.
He points to one company that has used events like the SMI Metal Engineering eXpo as an opportunity to bring divisional managers together for company meetings, to participate in educational sessions, to see and buy new equipment and to network with other springmakers.
As the new SMI president, Huber sees the priority of continuing some of the successes in industry education that are already in place through the educational symposia at the Metal Engineering eXpo and SMI’s new spring design training classes.
“We need to push forward into education and keep it moving,” explained Huber. “Gathering information and making it readily available to springmakers is very important to our success.”
He also sees the need to continue unifying the industry.
“We must continue to push forward and bring our industry together across the board, across the nation as much as we can through the Americas and also into Europe and beyond to create that synergy,” Huber explained.
“We’re all challenged right now with material issues and COVID-19-related things,” said Huber. “Hopefully by the time the end of my tenure comes, that’s behind us. Right now, we must continue to meet those challenges head on and keep everyone moving.”


All in the Family
Huber says his parents, Barb and Gene Sr. set a strong example of faith, family and hard work for him and his siblings to follow. In the wintertime, his parents spend time in Phoenix, Arizona with Huber’s twin sister Gina and her husband James. The Huber twins are the oldest, followed by Missy, who lives in Indianapolis with her husband, Greg. Chad is the youngest and married to Pam.
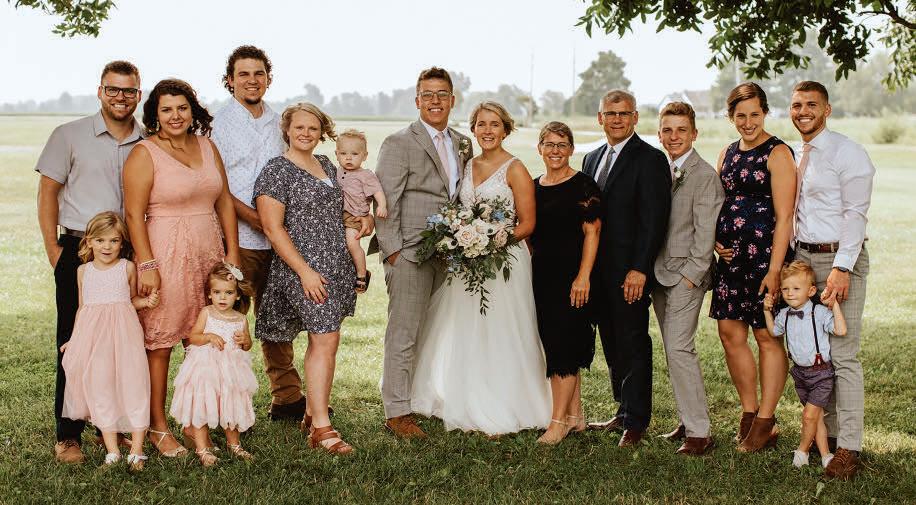
The Huber family pictured (l-to-r): Son Eric, granddaughter Aspen, daughter-in-law Felicia, granddaughter Paisleigh, son Brock, daughter-in-law Taylor, grandson Cole, son Ross, daughter-in-law Emmy, wife Sherri, Gene, son Quinn, daughter-in-law Erica (carrying granddaughter Roma), grandson Zander and son Kirk.

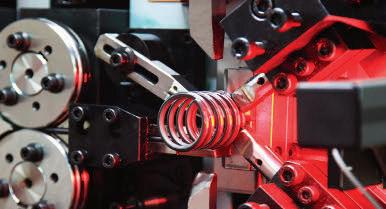
Spring Tooling for All Machines Complete line of carbide and steel tooling for the spring industry.
Machines
• Fenn (TORIN) • Itaya • MEC • Samuel • Sleeper & Hartley • Additional Machines – A.I.M. – ASAHI – Bamatec (Schenker) – Baird – Bobbio – E.N. Machine (Ming) – Simplex – Wafios
Line of carbide and steel tooling include…
• Arbors/Mandrels • Block Guides • Body Tools • Caps • Coiling Tools • Cutting Tools • Feed Rolls • Guides/Liners • Pencil Arbors • Pitch Tools • Quills
naspringtool.com 860-583-1693
169 WHITE OAK DRIVE BERLIN, CT 06037
Huber and his wife, Sherri, have five boys. Eric is the oldest and married to Felicia. They have two daughters, Aspen and Paisleigh. Kirk is married to Erica, and they have a son, Zander and a daughter, Roma. Brock is married to Taylor, and they have a son, Cole. Ross just got married to Emmy and is pursuing studies at Purdue University. Quinn is a junior in high school.
As mentioned earlier, Eric and Brock work at Winamac Coil Spring. Kirk spent some time working at the family business, but recently decided to take a job in the software industry.
The Hubers are active members of the Francesville Apostolic Christian Church. Huber says faith is an important part of his life. “The Great Commission in the Bible is all about spreading the Word of God. Jesus Christ was a relational person, and until we build relationships with people, we can’t show who Jesus Christ is. I believe in the ministry of reconciliation that is found in the Bible.”
The affection Huber has for his own family extends to the family at Winamac Coil Spring. As he said a few years ago when they joined the Indiana Manufacturer Association’s Hall of Fame, “The dedication, innovation and skill of our employees have helped our company become leaders in the large spring and wireform industry.”
Huber says the teamwork among family and employees is what makes the company great. “My job, a lot of times, is to invent and look into new products and how we can make them. Tony’s job is to make sure we are strategically aligned, and he does that very well.”
Huber says each member of the thirdgeneration leadership team brings a unique perspective to help elevate the company. “Within a family business there is talent that somebody brings to the table that you would miss if they were not there.”
Huber says he tries to follow the Golden Rule: to treat others as you would like to be treated. He says it makes sense in his employer/employee relationships and in his dealings with fellow SMI members.
He concludes, “If we treat each other like we’d like to be treated, we’ll probably be OK and not step on each other’s toes.” n
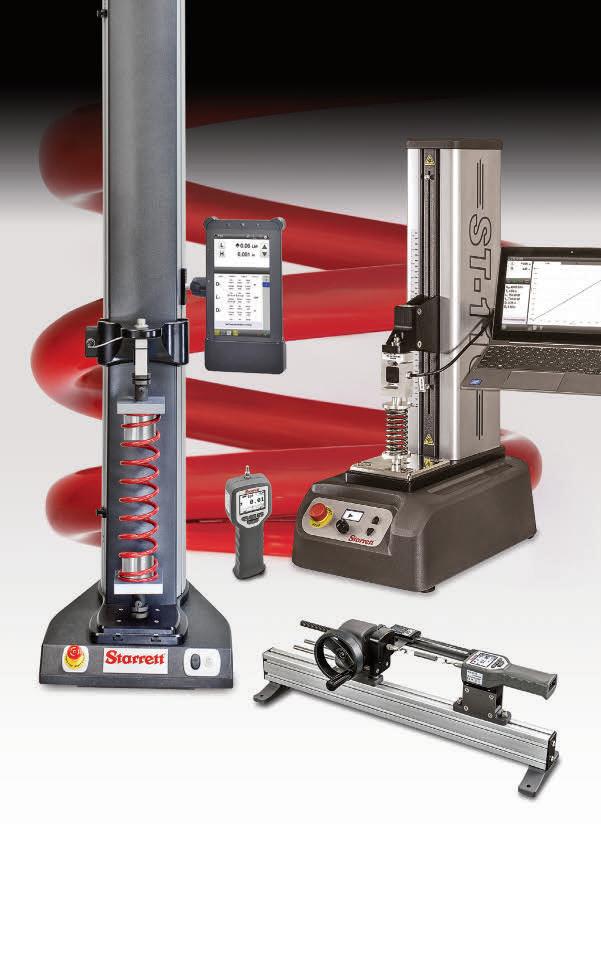
INTRODUCING
Spring Testing REVOLUTIONIZED
The Authority on Accuracy.
NEW
Available with Basic or Advanced Software
Innovative Spring Testing Solutions
Starrett offers a complete line of innovative force solutions for spring testing. High volume production testing solutions are available with both basic (L1) and advanced (L2) software.
MADE IN AMERICA
For more information visit starrettmetrology.com/force
PRECISION TOOLS/GAGES
SPRING TESTING
spring inspection
LSS.18.03.4.force-half-springs-SPRINGS-MAG.indd 1 2/10/22 3:20 PM

Untapped Talent
Reviewed by Gary McCoy
The opening line of the introduction to the book “Untapped Talent: How Second Chance Hiring Works for Your Business and the Community” got my attention because of the unprecedented challenge springmakers and society in general faces: Where to find the next generation of workers. In the book, Jeffrey D. Korzenik lays out the task when he says, “The successful CEO of the future will be the one who can effectively manage through the coming talent shortage.”
Korzenik provides a strategy for business leaders for meeting this challenge, with a particular focus on providing a “second chance” to those with criminal records.
The author first lays out the size of the worker shortage challenge, and goes on to provide a solution that every business should consider. Korzenik says employers who hire second chance workers have access to a labor pool overlooked by competitors and community partners who are willing to help them staff and train employees.
While the author says there is a large pool of job candidates with criminal records to choose from, he focuses on how to choose quality over quantity. The book provides lots of helpful information on the criminal justice system to provide a context in identifying the potential of second chance hiring.
As the publisher, HarperCollins Leadership, explains in a summary of the book, “‘Untapped Talent’ includes dozens of examples of businesses (from factories to restaurants to retail) that have successfully implemented the second chance hiring practices outlined in this book.”
The book includes practical onboarding and coaching strategies that will help ensure a smooth transition and a productive, happy new employee.
I’ve met several springmakers who are willing to give employee candidates a second chance and have had success in doing so. This book will help those who’ve already done it and those who might want to consider it. n
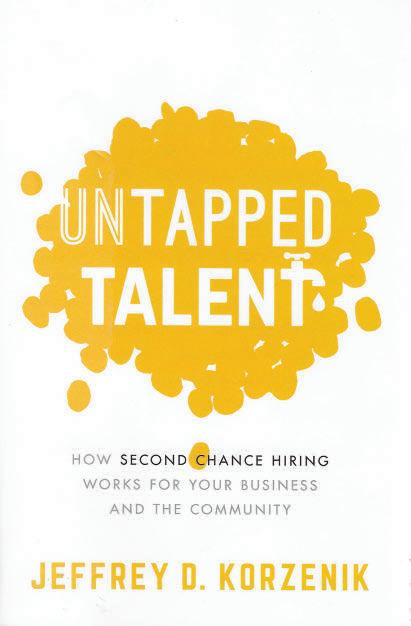
Have a favorite business book you would like to tell us about or review? Send your suggestions to Springs magazine editor Gary McCoy at gmccoy@fairwaycommunications.com.

PTC - Pretension Control INTERNATIONAL PATENT HIGH SPEED CNC COILERS
FX 5 Ø 0.10 - 0.80 FX 10 Ø 0.15 - 1.10 FX 15 Ø 0.25 - 1.50 FX 30 Ø 0.40 - 3.00
MILANO - ITALY NIMSCO LLC North American distributor 5115 B Tremont Ave. Davenport, IA 52807 Ph: 563-391-0400 Fax: 563-391-0403 i in nf fo o@ @n ni im ms sc co o. .c co om m
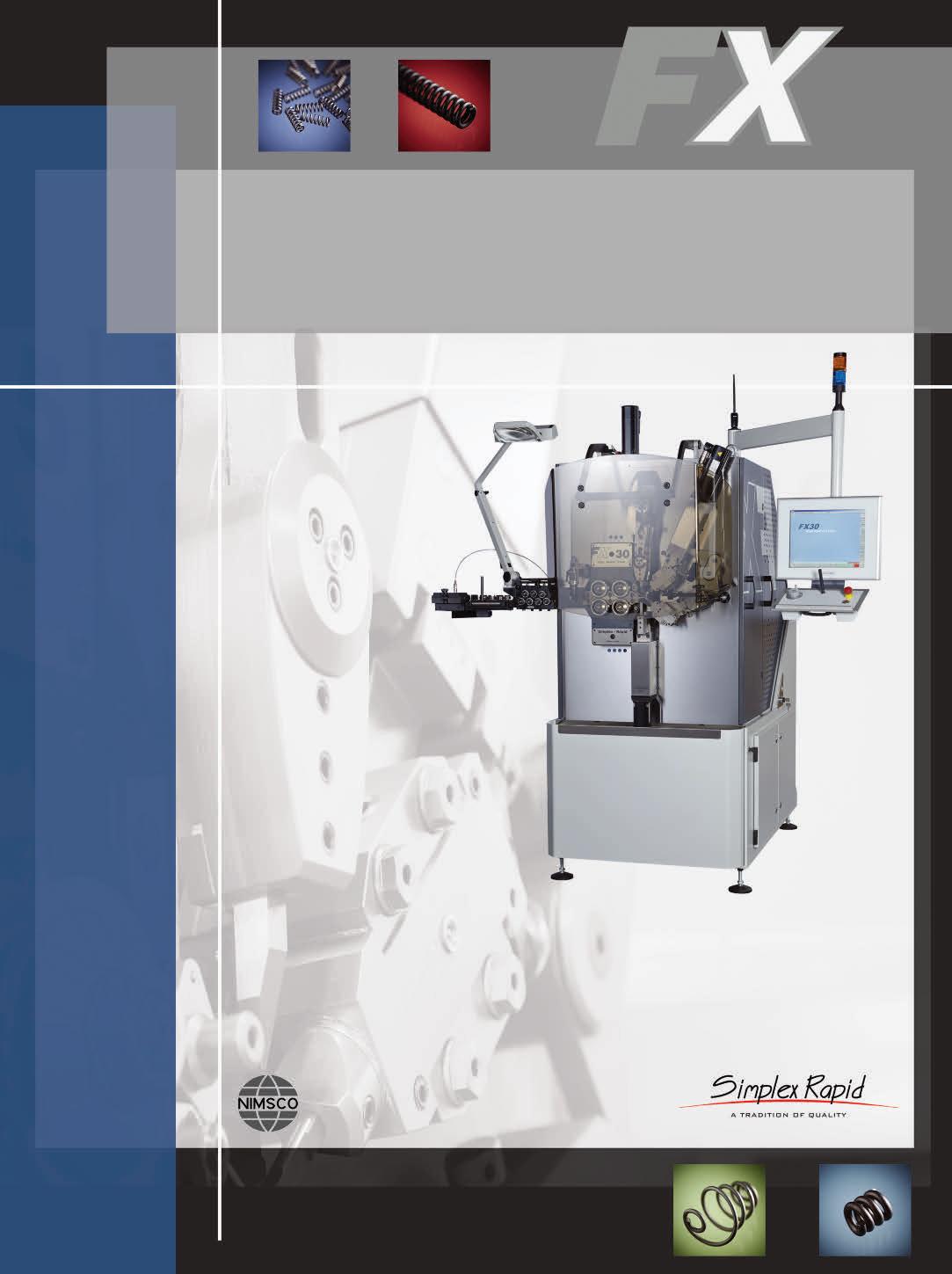
wongwean/Shutterstock.com CTE News

ABB Apprentices Join the Next Generation of Manufacturers
As manufacturers work to fill the skills gap and hire more employees, some are modernizing a tried-and-true approach: taking on apprentices. In Fort Smith, Arkansas, ABB, an industrial electric motor and robotics manufacturer, is leading the way with its innovative program for local high school students.
Apprentices work three hours per day, four days per week during the school year and 40 hours per week during the summer. ABB trains them in a range of roles, to provide them with a strong foundation in manufacturing skills and the ability to work their way into an advanced technician role.
“These students are getting paid, and paid well for a part-time job,” said ABB vice president of operations Johnny McKusker. “They learn a variety of skills that most juniors and seniors in high school aren’t exposed to. And if they decide they like manufacturing and want to stay on, then we’re getting a person who joined us early, has had a lot of training and investment and is able to contribute at a high level early in their career.”
Last year, nearly all of ABB’s apprentices took on permanent roles within the company after graduating. They were also able to continue their education through a local university, with ABB providing tuition reimbursement to help them pay for it.
“Manufacturing as a career has changed significantly in the last 25 years,” said McKusker. “It’s not hot, dirty and dangerous work. Instead, it offers technical skill development and an opportunity to earn a good living.”
According to at least one participant in the program, the apprenticeship has been an excellent way to learn important skills and gain experience in a real work environment.
“My experience has been great,” said Nadia, a current apprentice working on the digital solutions team. “It’s given me the opportunity to learn about manufacturing, but also about bonding and building relationships with my colleagues. I’m getting the experience of what a real job would be like outside of school.”
“I want to continue working for this company,” said Nadia. “I took this apprenticeship because ABB was my dream job from the start, because of how great they are in industrial engineering. Seeing the opportunities here and seeing how they take care of bonding and relationship building — it’s something I really like and appreciate.” (Source: Manufacturing Institute, Dec. 9, 2021, https://bit.ly/3FHVOge)
Safety & Health Cold Stress
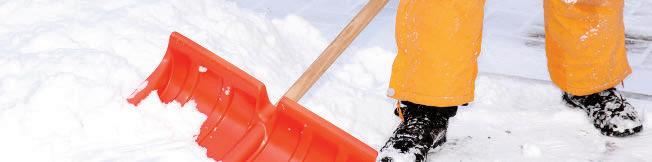
1 The Problem
Cold temperatures are often associated with occupations that take employees outdoors
during the winter months. In addition to the obvious outdoor cold condition jobs, many employees work indoors in refrigerated environments year round. Production facilities involving food and the distribution network required to get refrigerated food products to consumers require exposure to cold conditions. Prolonged exposure can lead to cold stress. Some employers fail to recognize and address cold stress hazards due to lack of monitoring and knowing the related signs and symptoms, which include: •Hypothermia •Frostbite •Cold water immersion •Dehydration
2 Solutions that Work
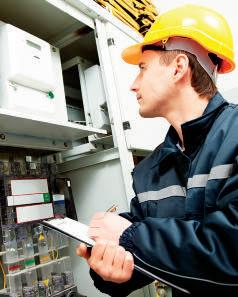
Even the most attentive, proactive worker can’t tackle the dangers of cold stress alone. A cooperative approach is important. OSHA’s guidance for cold stress prevention lists engineering controls, training, safe work practices and personal protective equipment (PPE), such as appropriate cold weather attire, as foundational components for employers to build into their work plans. Employers should: • Provide engineering controls such as thermostats and door flaps to help control exposure • Train workers on how to help prevent and recognize cold stress illnesses and injuries, and how to apply first aid treatment • Give workers frequent breaks in warm areas • Ensure employees are dressed properly in cold temperatures • Reduce exposure time • Allow workers to interrupt work if they feel a cold condition affecting them
3 How Grainger Can Help
Grainger has what you need to help keep your employees safe in extreme cold conditions.
Fast Facts
4
MAIN FACTORS
that contribute1 to cold stress: •High or cold wind •Dampness •Cold temperatures •Cold water
70°F
Hypothermia can occur in any water temperature below this level.2
2x
Twice as many people die of “excessive cold” conditions in a given year than of “excessive heat.”3
Products Services Expertise Resources
•Insulated Clothing •Hand & Foot Warmers •Portable Heaters •Blankets •Ice Melt
• Anti-Slip Footwear
Attachments •Work Shelters • Grainger Online
SafetyManager Suite® • Technical Product Support
Email safetysupport@grainger.com
• Field Safety Specialists
Your Grainger Rep is Standing By
Contact your Grainger representative or login to Grainger.com/smi and view a list of the most common cold stress related products • Safety & Health Solution Center
grainger.com/safety
• Safety & Health Catalog
grainger.com/safetycatalog
• Grainger KnowHowSM site
grainger.com/knowhow
©2019 W.W. Grainger, Inc. W-BMCL570-2 G0029 1 https://ehs.princeton.edu/workplace-construction/occupational-health/heat-cold-stress/cold-stress-facts 2 NIOSH, Cold Water Immersion, June 2018 3 CDC’s National Center for Health Statistics Compressed Mortality Database

Gary Van Buren Retires as SMI Technical Advisor
After four years of service to SMI as the association’s technical advisor, Gary Van Buren announced his retirement effective March 1, 2022. Van Buren plans to continue to participate informally on the SMI technical committee.
Van Buren, a longtime SMI member, joined the SMI staff in 2018. With more
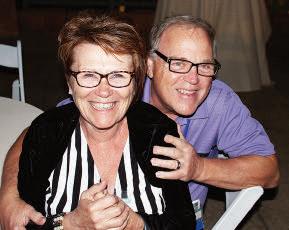
Linda and Gary Van Buren at the 2020 SMI Annual Meeting in the Bahamas. than 25 years in the industry, he was well suited for the position. Most of his experience came at Spring Team, Inc. in Austinburg, Ohio as the company’s engineering manager. While at Spring Team, Van Buren was a member of the SMI technical committee for approximately 15 years.
In his work with SMI, Van Buren was available to assist members with design and problem-solving issues, including spring design and technical consultation. Most recently he was responsible for teaching SMI’s new spring design training classes.
“Gary has been a valuable contributor to SMI’s technical services, assisting with many member questions and helping teach the spring design courses,” said SMI executive director, Lynne Carr. “We wish the best to Gary and his wife, Linda, in retirement. He will be missed.”
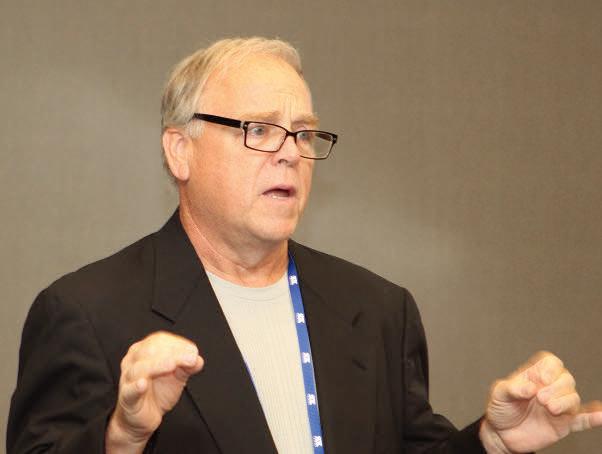
Van Buren taught the first spring design training class at the 2019 SMI Metal Engineering eXpo in Pittsburgh.
SMI’s technical director, C. Richard (Rick) Gordon, said that Van Buren has been a great partner and contributor to the SMI technical effort.
“The knowledge and experience which he developed at Spring Team have been great assets in answering spring design questions. Gary also served as our trainer as we introduced the spring design courses of compression, extension and torsion springs. He taught 15 of our 16 classes, training over 400 students. We all wish Gary and his wife Linda the very best in his retirement.”
Van Buren holds degrees in electrical engineering and mechanical engineering from Kent State University.
To send best wishes to Van Buren, he can be reached at gvanburen2@gmail.com.
©iStockphoto.com/MF3d
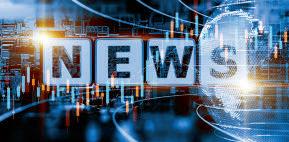
Send Us Your News
SMI members receive priority placement for their product, company, personnel and events announcements in the magazine. Your news releases should be roughly 50 to 100 words and may be accompanied by color photos (highresolution .JPEG photos at 300 dpi preferred). Send to dina@smihq.org.
SMI’s New 401(k) Retirement Plan Launches
A Q&A About the Program with Liz Hickox of Core Financial Partners
Last year SMI introduced a new 401(k) multiple employer program through Core Financial Partners (CFP). The program is designed to provide SMI members with a resource to offer its employees a superior retirement program that lessens the burden of plan administration and can help save money.
Liz Hickox of Core Financial Partners is a retirement plan specialist and the point person for SMI’s new offering. Based in Newport, Rhode Island, Hickox has been traveling throughout the U.S. over the past year to introduce SMI members to the new program. We recently caught up with Hickox to provide an overview and update on the plan.
What is a Multiple Employer Plan 401(k) and what are the advantages to individual SMI members?
A multiple employer plan can refer to a few things. At its core, it’s just that. Multiple employers as part of a common nexus or association that come together to leverage each other for buying power, and strength in numbers. The SMI Plan offers two variations of a multiple employer plan, a traditional closed MEP and an exchange plan.
A closed MEP offers large plans the ability to not only enjoy the benefits of lower fees, but the ability to share the cost of the audit while maintaining their own plan design features.
Smaller, non-audited plans are siloed outside this arrangement to avoid any audit costs, yet enjoy the same cost savings. Each plan is priced on an individual basis so the larger plans will not ever subsidize the costs for the smaller plans, yet both achieve greater buying power as adopting employers through their membership in the SMI program.
What are some of the risks and liabilities that SMI members can face who sponsor their own 401(k) program?
Sponsoring a 401(k) is a tremendous amount of time and risk. You are not only overseeing your money, but business owners (plan sponsors) are also personally responsible for the retirement assets of each employee.
I was very fortunate to attend the retirement of an SMI client/member that oversaw her company’s 401(k). The plan was (is!) my “Marquis Client;” their plan was without a doubt the most well run that I had ever had the pleasure of working with. I was, and am, very proud of it.
As we enjoyed cake and celebrations in the plant cafeteria, I asked her how much time she had dedicated to simply overseeing the plan? “About 20 hours a month,” she replied.
Done right (as it rarely is!), a 401(k) takes a lot of time. Any person involved in plan assets is a fiduciary, and not only must perform their job and act in the best interest of the plan and its participants, but they also need to stay educated and current in their understanding and oversight of qualified plans.
The current 401(k) landscape has drawn the attention of ambulance chasing lawyers hungry for a chance to win. Among the hot topics they look to pursue are excessive fees (“Was there a lower share class available?”), investment quality (“Are you offering an underperforming fund that doesn’t adhere to IPS criteria? Do you have an IPS?”). Any disgruntled employee can call the U.S. Department of Labor (DOL) and make a claim (“I think my former employer’s plan had high fees), and they will open up a case.
Will it go anywhere? Maybe… Maybe not…But it will take time; and should the DOL find a breach that resulted in losses, participants accounts are to be made whole by the plan fiduciaries from personal assets.
From an administrative perspective, it’s a lot to oversee! “Are you tracking eligibility?” “Are you sending disclosures and notices with the appropriate timeline?” “Have you ensured that hardship
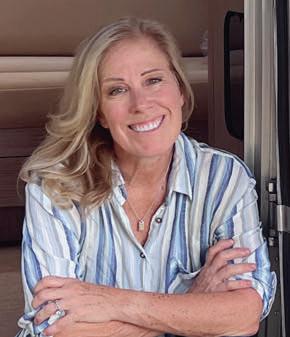
Liz Hickox on the steps of the Core Financial Partners mobile office, a 27-foot Airstream trailer.
claims are legitimate?” “What is your onboarding procedure?” ”Do you have an education program with qualified teachers?”
All these tasks and the associated risk, unless outsourced to a named third party in writing, fall on the shoulders of the plan sponsor and the individuals that handle any plans assets.
How does Core Financial Partners and its program partners Pentegra and Empower America help alleviate these risks?
We’re really proud of this plan.
Outgoing SMI president Bert Goering and the SMI board of directors spent a lot of time researching not only the appropriate strategy (there are numerous iterations of multiple employer plans) to determine which was best for their members, but also the partners supporting it.
Empower is the #1 recordkeeper for plans under $50 million and offered us an extremely competitive fee structure for all members regardless of size; they offer access to investments and provide a robust participant experience and website; they assist in distributing notices, offer structured and custom on-site education from employee education specialists.1
Admittedly, plan advisors are not educators. That’s not our job and at times can promote a conflict of interest if an advisor makes a recommendation to invest in higher fee assets outside the plan.
The SMI plan eliminates the risk to the employee and the plan trustees by employing skilled and experienced educators to offer fiduciary level guidance to participants.
Pentegra acts as a full scope administrative fiduciary and assumes the risk and responsibility for all administrative tasks, in writing. Additionally, (and importantly!) they also sign the 5500, removing the business owners name from the return, and the risk that goes along with it.
The plan trustees are no longer the face of company to the DOL.
The investment piece, from my experience, is where most plan sponsors are unknowingly incorrect in their understanding of who is ultimately responsible for investment selection, replacement and removal decisions.
Many assume the platform recordkeeper is responsible for fund recommendations or that the advisor is. In 99.97 percent of all cases, they are not, and results in a proprietary fund lineup.
Many plans retain an advisor that assumes some of the responsibility (a limited scope 3(21)-level fiduciary), but not ALL.
Unless a plan retains a full scope 3(38) fiduciary level investment advisor in writing, the ultimate responsibility for investment oversight and final decisions of fund oversight and management fall on the plan sponsor’s shoulders.
The SMI retirement program retains a third-party team of professionals comprised of seven chartered financial analysts that not only assume the task of making unbiased, non-proprietary decisions, but the risk associated with it. Your advisor may have a Nobel Prize for their theory on asset allocation from Wharton, but unless they acknowledge full responsibility for all investment decisions that role is still the plan sponsor’s.
In addition, our relationship with RPAG2 (www.rpag.com) offers SMI members with exclusive access to extremely low-cost CITs (collective investment trusts) that are not available outside this relationship.
Our team at CFP works with the 3(38) investment team in a fiduciary capacity and acts as advocate and partner for all members. CFP works alongside the plan sponsor to continually monitor all services and providers, as well as review plan design, structure employee education and repeatedly benchmark all plan fees to ensure reasonableness, including our own.
Can you tell us about some of the meetings you’ve had so far with SMI members?
If you know me, you know I love industrialism. I’ll gladly accept any invite to tour a plant and love to hear how things are made.
Last fall, we held to our promise to Bert and his team and set out on a monthlong trip to the Midwest, the hotbed of spring manufacturers, to introduce the SMI plan.
We visited SMI members in New York, Pennsylvania, Ohio, Illinois, Indiana and Michigan. We toured their factories and learned what their specialty is; how their products are made, and more importantly, who they were as business owners and individuals.
We learned and appreciated how they came to the industry and how they grow their business.
We heard what their strengths are, and what their challenges are. We had lunch; we talked family and football (go Dawgs!) and learned they all have one thing in common. SMI members care deeply about their employees and, although they may be direct competitors to each other, support each other as colleagues.
What are your accommodations when you are on the road to meet with members?
Why do I feel you set this question up? Ha!
Our business, much like the SMI, is family owned. My husband Brian is a Certified Financial Planner (CFP®), and my business partner.
Although he has solid experience in the qualified plan world, he took a different path and works exclusively with business owners on an individual basis (estate and business succession plans, executive compensation).
Calendar of Key Events for the Global Spring Industry
2022
May 19
SMI Spring Design Training 202 Extension Spring Design
Online www.smihq.org June 7–9
WAI WireExpo
Dallas, Texas wirenet.org/events/wire-expo June 16
SMI Spring Design Training 203 Torsion Spring Design
Online www.smihq.org June 20–24
wire & Tube 2022
Düsseldorf, Germany www.wire-tradefair.com July 21
SMI Spring Design Training 301 Springs — Fatigue
Online www.smihq.org Oct. 5–7
wire and Tube Southeast Asia
Bangkok, Thailand www.wire-southeastasia.com
Oct. 12–14
SpringWorld 2022
Donald E. Stephens Convention Center, Rosemont, Illinois www.casmi-springworld.org Oct. 25–27
wire South America
São Paulo, Brazil www.wire-south-america.com Nov. 9–11
ISO/TC227 Meetings
Hangzhou, China Nov. 23–25
wire India
Mumbai www.wire-india.com
2023
Sept. 12–14
SMI Metal Engineering eXpo
South Point Hotel & Casino, Las Vegas www.metalengineeringexpo.org
While we complement each other, we have very different skill sets and defer to each other’s area of expertise with respect and appreciation.
I spent a great deal of time on the road in the early stages of this plan, which left us apart from each other.
Additionally, as a (fairly!) competitive triathlete, it left me falling short of my commitment to my personal goals, and to lead a healthy life. Airport food limits healthy options, and as much as I vow to bring my sneakers and run on the hotel treadmill, it simply never happens.
With a 98-pound rescue “Lab-ish” dog named Salty that is too big to fly, I never saw my family and was alone in a hotel four days a week.
In the spring of 2021, we made the commitment to hit the road and meet as many SMI members as physically possible, and the only way to do that was to take our business and personal life (and our dog) with us.
Core Financial Partners mobile office and home on the road is a 27-foot Airstream trailer!
We travel with all we need to run our business and lead an active life: Professional clothes, training gear, bikes, a paddleboard and a dog.
One of us flies out every two weeks to meet clients, while the other maintains basecamp operations.
It’s been a steep learning curve, but it’s been a fun one, because we absolutely love being able to meet SMI members. Although we’re all perfectly capable of holding a Zoom meeting, you can never replace a handshake.
References
1. Article in PLANSPONSOR magazine,
Dec. 31, 2019. 2. Securities and investment advisory services offered through Royal Alliance
Associates, Inc. member FINRA/SIPC.
Royal Alliance Associates, Inc. is separately owned and other entities and/or marketing names, products or services referenced here are independent of
Royal Alliance Associates, Inc.
Retraction
In the Winter 2022 issue of Springs, ads for Gibbs/Interwire were placed in the wrong position. This was an error by Springs magazine and not an error by Gibbs/Interwire. Springs magazine apologizes for the ad placement error.
The Gibbs/Interwire ad on page 1 (see below) should have been on the inside back cover.
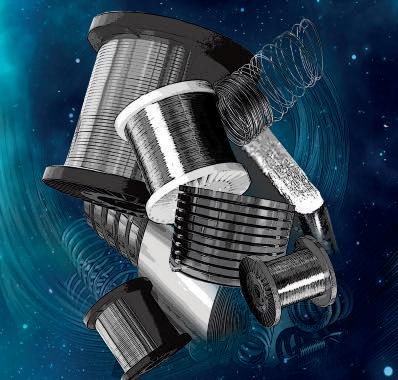
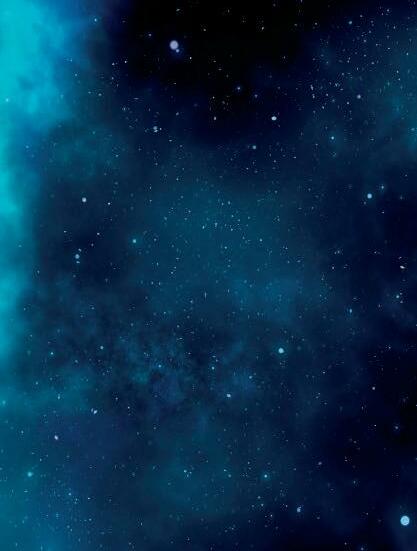
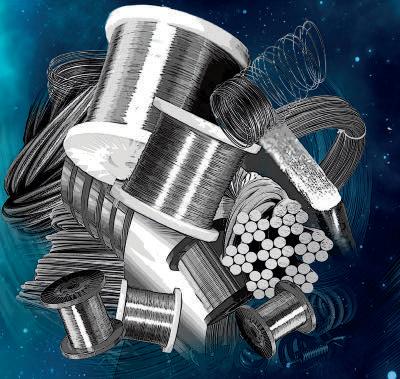

YOUR COMPLETE METALS SOLUTION The Gibbs/Interwire ad on the inside back cover (see below) should have been on page 1
The year is 2022. The world is recovering from a pandemic. Shutdowns and shortages disrupt many companies.
To save the day, two preeminent names in the metals industry have joined forces to create a metals powerhouse. Together, they provide an extensive array of high quality products and exceptional service to help you reach for the stars.
Relationships with the highest quality mills and our expansive distribution network enable this new alliance to be your strategic partner for all wire and strip needs.
Scan to learn more or visit the inside back cover
©iStockphoto.com/Studio-Pro Committee Connection
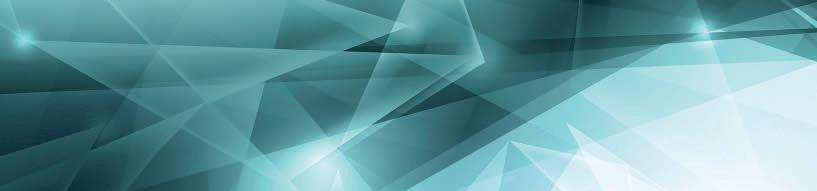
Surveys Help SMI Members Benchmark With the Industry
SMI regularly surveys its members to help them understand how they are doing relative to others in the industry.
The responsibility for distributing these surveys rests with SMI, but an important part of the process is in the input of the SMI Benchmarking committee, which is chaired by Kelley Christy of Diamond Wire Spring.
Christy encourages SMI members to participate in these surveys because of the benefit it accrues to their company.
“Our company has benefited greatly from the SMI Annual Market Summary because it helps us understand our business as compared with others in our industry, but it also provides us with an individualized report,” explained Christy. “We also appreciate the wage and benefit and salary surveys to help our company understand how our compensation program compares to other spring companies.”
Christy notes that the important part of each SMI survey is the confidentiality provided. “No company data is ever shared with SMI members or SMI itself. You can have complete confidence that what you submit is protected.”
By Gary McCoy
Kelley Christy
If you are interested in becoming a member of the SMI Benchmarking committee, contact Lynne Carr, SMI executive director at 630-495-8588 or email: lynne@smihq.org.
Here’s the schedule of surveys for the remainder of 2022 and into 2023.
Key Business Trends (regular and associate members) Survey Sent Responses Due Results Sent
First quarter 2022 Second quarter 2022 Third quarter 2022 Fourth quarter 2022 April 5, 2022 July 11, 2022 Oct. 4, 2022 Jan. 11, 2022 April 13, 2022 April 14, 2022 July 18, 2022 July 19, 2022 Oct. 11, 2022 Oct. 12, 2022 Jan. 18, 2022 Jan. 19, 2022
Wage & Benefits (every other year — regular member contacts) Survey Sent Responses Due Results Sent 2022 Aug. 6, 2022 Sept. 6, 2022 Sept. 20, 2022
Salary
(every other year — regular member contacts) 2023
Survey Sent Responses Due Results Sent
Oct. 1, 2023 Oct. 30, 2023 Nov. 30, 2023
Annual Market Summary (regular member contacts and prospective members) Survey Sent Responses Due Results Sent First mailing by SMI April 4, 2022 Email from SMI May 4, 2022 Email follow up from previous by Mackay Research Group recipients May 25, 2022 Published cutoff date for return May 30, 2022 Industry Report to SMI July 15, 2022 Individualized Reports to SMI Members July 30, 2022

HB-LD Box Ovens
Forming Systems Inc. (FSI) recently introduced the newest oven design fromHSI, the HB-LD series of Lift Door Box Ovens with HMI panel.
These new ovens are designed for batch stress relieving and heating for a variety of components at a maximum temperature of 500°C (930°F). There are a variety of sizes available, from 180 liters to 2200 liters. The doors are pneumatically operated for ease of operation.
Other features include: touch screen panel and PLC controlling system with communication protocols; digital error diagnosis; built-in temperature recording system; estimated power consumption monitoring and recording; remote access via VNC software for monitoring on a PC, tablet device or smartphone; and CQI9-oriented configuration for the automotive industry.
Available options include: two-stage programmable temperature control function (HMI-Ep); AMS2750F capable; TUS3 capable; trolley and SS tray systems.
For additional information, contact FSI at info@formingsystemsinc.com or 269-679-3557. n

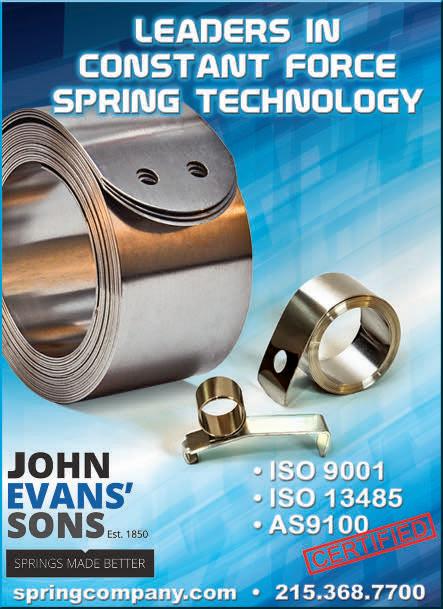

Send Us Your News
SMI members get priority placement of their product news. News releases should be roughly 50 to 100 words and may be accompanied by color photos (HiRes .JPEG at 300 dpi preferred). Send to dina@smihq.org.
©iStockphoto.com/RichVintage
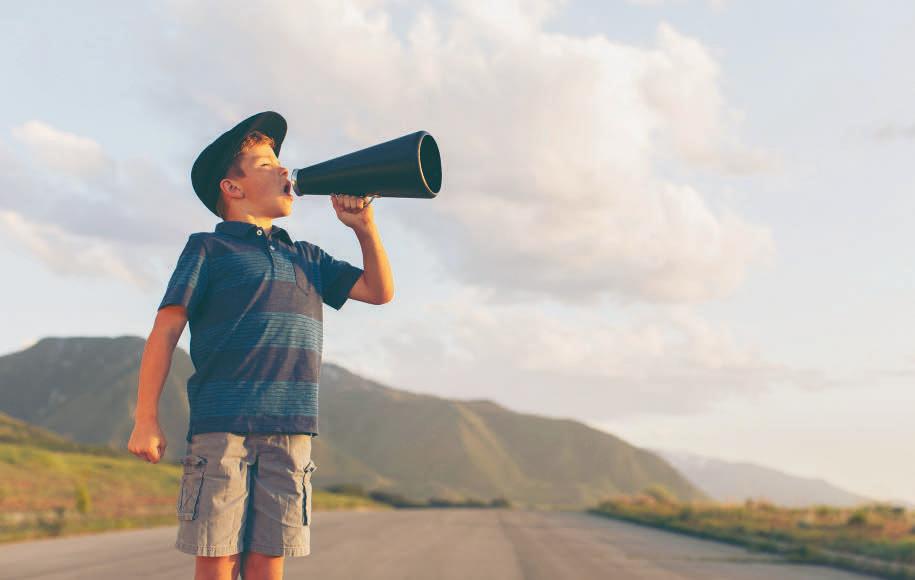
A & D Trading
(440) 563-5227. . . . . . . . . . . . . . . . .22
Admiral Steel
(800) 323-7055 ................40
Alloy Wire International
(866) 482-5569. . . . . . . . . . . . . . . . . .3
Anchor Abrasives
(708) 444-4300 ................ 10
BB Spring Technology
+39 031 536584 ...............64
CASMI
www.casmi-springworld.com .....66
Diamond Wire Spring Co
(800) 424-0500 ................18
Dispense Works
(815) 363-3524 .................37
Elgiloy
(888) 843-2350. . . . . inside back cover
FENN/Torin
(860) 259-6600 ................31
Forming Systems Inc
(877) 594-4300 ......... back cover
Gibbs Interwire
(800) 800-4422 .................1
Gibraltar
(847) 383-5442. . . . . . . . . . . . . . 43-44
Industrial Steel & Wire
(800) 767-0408 ............... 9, 11
JN Machinery
(224) 699-9161 .............. 26-27
John Evans’ Sons
(215) 368-7700 .................65
Larson Systems
(763) 780-2131 .................46
Mapes Piano String Co
(423) 543-3195 .................50
NIMSCO
(563) 391-0400 .................65
North American Spring Tool
(860) 583-1693 .................53
Proto Manufacturing
(800) 965-8378 ................53
Advertisers Index
Radcliff Wire
(860) 583-1305 .................37
RK Trading
(847) 640-9371. . . . . . . . . . . . . . . . . .6
Simplex Rapid
(563) 391-0400 .................56
Spring Manufacturers Institute
(630) 495-8588. . inside front cover, 58
Starrett
starrettmetrology.com ...........54
Tool King
(847) 537-2881 .................50
United Wire
(800) 840-9481 ................46
Vinston
(847) 972-1098 .................16
WAFIOS
(203) 481-5555 ..................5
Zapp Precision Strip
(203) 386-0038 ................20
Markus Arnold WAFIOS Machinery Corporation
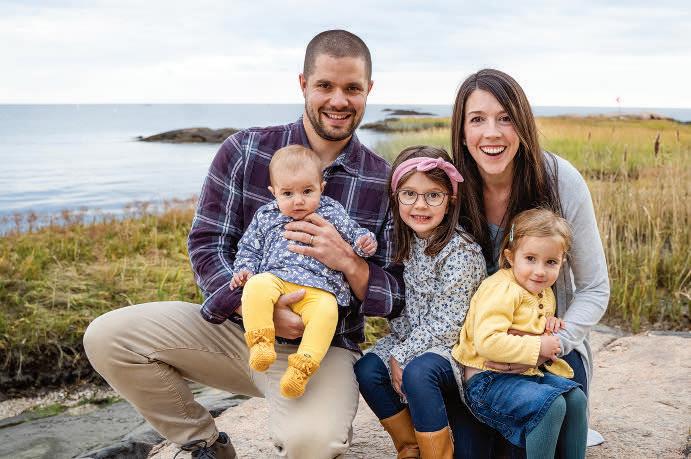
(L-to-r): Markus, Lowenna, Martha, Lucy and Elena Arnold.
Name: Markus Arnold Company name and city: WAFIOS Machinery Corporation, Branford, Connecticut. Brief history of your company: Founded in 1893, WAFIOS is a producer of wire and tube processing machines. For more than 60 years WAFIOS Machinery Corporation has been representing WAFIOS in the United States of America and Canada. Job title: President. Spring industry affiliations: CASMI, SMI and NESMA. Birthplace: Freudenstadt in the Black Forest, Germany. Current home: Guilford, Connecticut. Family (spouse, children, pets, etc.): My wife, Lucy and our three daughters Martha, 5, Elena, 3, and Lowenna, 8 months. What I like most about being a spring machine producer: The vast variety of applications for our machines and the capabilities of consistently evolving technology. Favorite food: Tough question. I’m a huge fan of food and really appreciate a meal made from scratch. I love trying new and exotic things, but if I had to choose I would say I’m a big fan of Indian cuisine. Favorite books/authors: “My Utmost for His Highest” by Oswald Chambers. Favorite song/musician: Currently at top of my playlist is “Twinkle, Twinkle, Little Star” and “Let It Go” thanks to my girls! Hobbies: Hiking, cycling, skiing and being outdoors. Favorite places: Berchtesgadener Land, a beautiful mountain region in the German Alps. Best times of my life: I think that every season in life holds blessings and the potential for great moments and I try to be joyful about each season’s blessings. A really great evening to me is: Family, friends, good food and good wine. The one thing I can’t stand is: Slow walkers! I knew I was an “adult” when: I did my first tax return. If I weren’t working at WAFIOS, I would like to: Sail around the world. The most difficult business decision I ever had to make was: A combined business and family decision to relocate from Germany to the U.S. to start my new position at WAFIOS Machinery Corporation. We are so glad that we did! I would like to be remembered in the spring industry: Along with my colleagues at WAFIOS Machinery Corporation, for enabling customers to achieve great success by providing the right machine and service. But people will probably remember me for: The German who never managed to speak proper English.

ELGILOY® ALLOY 75 1947 MISSION-CRITICAL SINCEELGILOY® ALLOY 75 1947 MISSION-CRITICAL SINCE AN ALLOY SO INFLUENTIAL TO MISSION-CRITICAL PRODUCTS WE NAMED OUR COMPANY AN ALLOY SO INFLUENTIAL TO MISSION-CRITICAL PRODUCTS WE NAMED OUR COMPANY
AFTER IT.AFTER IT.
Elgiloy AlloyElgiloy Alloy Developed in 1947, Elgiloy Alloy, a non-corrodingDeveloped in 1947, Elgiloy Alloy, a non-corroding watch spring material with an infinite life span, waswatch spring material with an infinite life span, was soon recognized for applications in aerospace, thesoon recognized for applications in aerospace, the petrochemical industry and medical devices.petrochemical industry and medical devices.
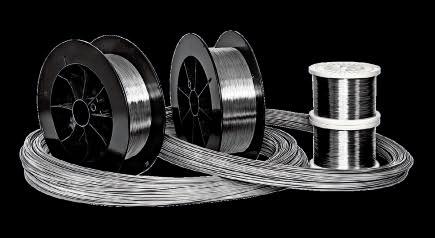
ELGILOY® ALLOY 75 1947 MISSION-CRITICAL SINCEELGILOY® ALLOY 75 1947 MISSION-CRITICAL SINCE ELGILOY® ALLOY 75 1947 MISSION-CRITICAL SINCEELGILOY® ALLOY 75 1947 MISSION-CRITICAL SINCE SAVE NEW AN ALLOY SO INFLUENTIAL TO MISSION-CRITICAL PRODUCTS WE NAMED OUR COMPANY AFTER IT. AN ALLOY SO INFLUENTIAL TO MISSION-CRITICAL PRODUCTS WE NAMED OUR COMPANY AFTER IT. AN ALLOY SO INFLUENTIAL TO MISSION-CRITICAL PRODUCTS WE NAMED OUR COMPANY AFTER IT. AN ALLOY SO INFLUENTIAL TO MISSION-CRITICAL PRODUCTS WE NAMED OUR COMPANY AFTER IT. Developed in 1947, Elgiloy Alloy, a non-corroding watch spring material with an infinite life span, was soon recognized for applications in aerospace, the Elgiloy Alloy Developed in 1947, Elgiloy Alloy, a non-corroding watch spring material with an infinite life span, was soon recognized for applications in aerospace, the Elgiloy AlloyDeveloped in 1947, Elgiloy Alloy, a non-corroding watch spring material with an infinite life span, was soon recognized for applications in aerospace, the petrochemical industry and medical devices. Elgiloy Alloy Developed in 1947, Elgiloy Alloy, a non-corroding watch spring material with an infinite life span, was soon recognized for applications in aerospace, the petrochemical industry and medical devices. Elgiloy Alloy DATE! petrochemical industry and medical devices.petrochemical industry and medical devices.

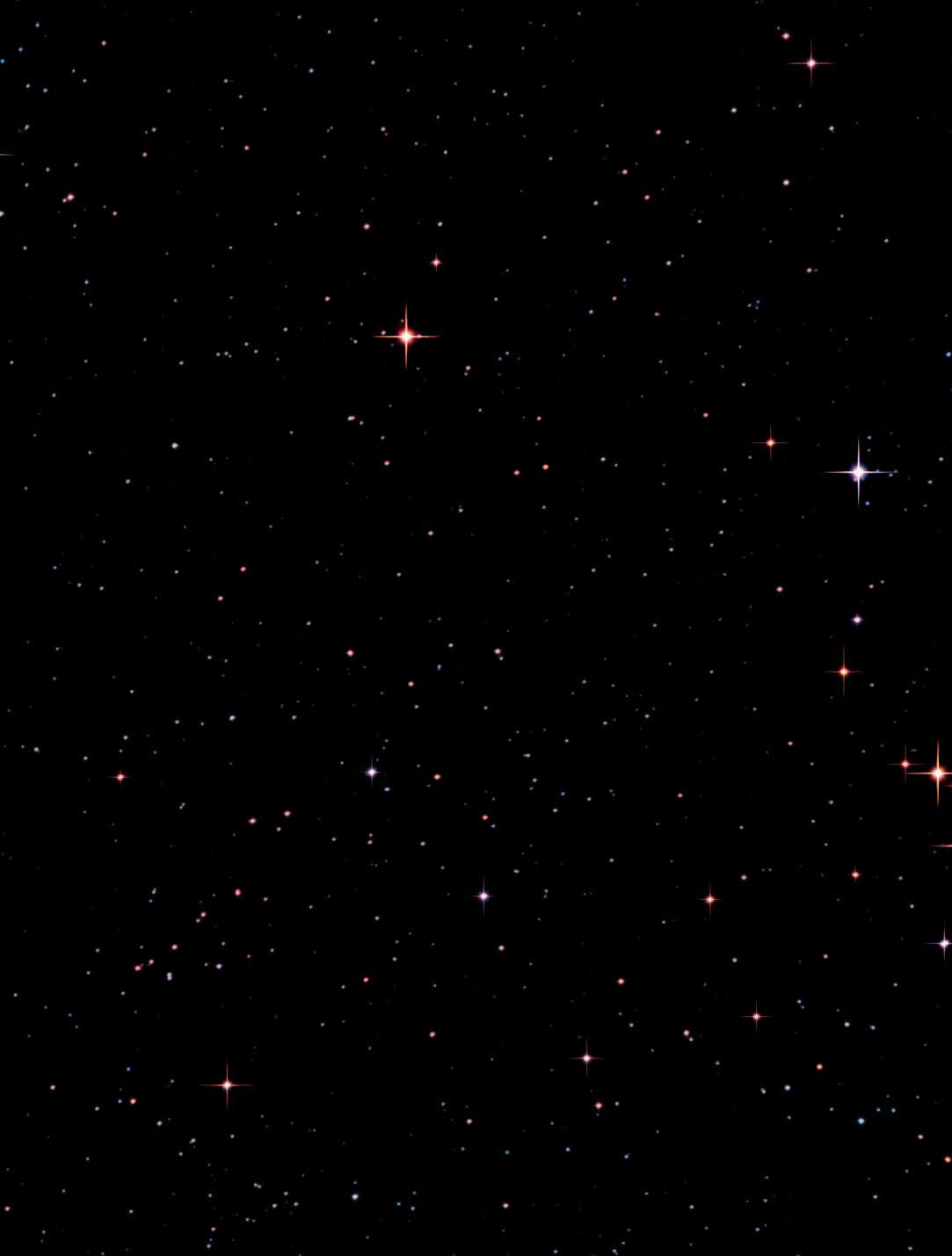
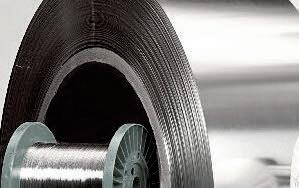


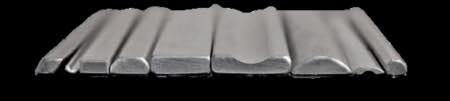
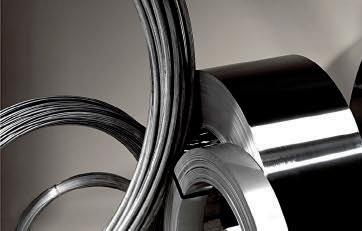



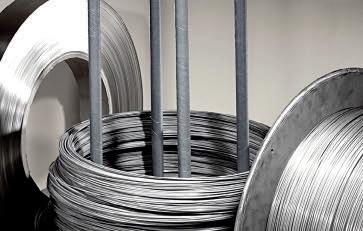

Elgiloy Specialty MetalsElgiloy Specialty MetalsElgiloy Specialty MetalsElgiloy Specialty Metals Today, Elgiloy Specialty Metals produces more than 50 high-performance alloys for strip & wire applications. Today, Elgiloy Specialty Metals produces more than 50 high-performance alloys for strip & wire applications. Today, Elgiloy Specialty Metals produces more than 50 high-performance alloys for strip & Elgiloy Specialty Metals Today, Elgiloy Specialty Metals produces more than 50 high-performance alloys for strip & Elgiloy Specialty MetalsToday, Elgiloy Specialty Metals produces more than 50 high-performance alloys for strip & wire applications. Today, Elgiloy Specialty Metals produces more than 50 high-performance alloys for strip & wire applications. wire applications.wire applications. Precision strip from .0008" up to .100" Round wire from .001" up to .875" Shaped wire from .005" Centerless grinding, shaving, polishing & cut-to-length services We offer: Precision strip from .0008" up to .100" Round wire from .001" up to .875" Shaped wire from .005" Centerless grinding, shaving, polishing & cut-to-length services We offer: Precision strip from .0008" up to .100" Round wire from .001" up to .875" Shaped wire from .005" Centerless grinding, shaving, polishing & We offer: Precision strip from .0008" up to .100" Round wire from .001" up to .875" Shaped wire from .005" Centerless grinding, shaving, polishing & We offer: Precision strip from .0008" up to .100" Round wire from .001" up to .875" Shaped wire from .005" Centerless grinding, shaving, polishing & cut-to-length services We offer: Precision strip from .0008" up to .100" Round wire from .001" up to .875" Shaped wire from .005" Centerless grinding, shaving, polishing & cut-to-length services We offer: cut-to-length servicescut-to-length services
September 12-14, 2023
Las Vegas South Point Hotel & Casino
Elgiloy.com | 888-843-2350 Elgiloy Specialty Metals is a division of Combined Metals & affiliate of Gibbs Interwire Elgiloy.com | 888-843-2350 Elgiloy Specialty Metals is a division of Combined Metals & affiliate of Gibbs Interwire Sign up for updates at metalengineeringexpo.org Elgiloy.com | 888-843-2350Elgiloy.com | 888-843-2350 Elgiloy.com | 888-843-2350 Elgiloy Specialty Metals is a division of Combined Metals & affiliate of Gibbs Interwire Elgiloy.com | 888-843-2350 Elgiloy Specialty Metals is a division of Combined Metals & affiliate of Gibbs Interwire Elgiloy Specialty Metals is a division of Combined Metals & affiliate of Gibbs Interwire Elgiloy Specialty Metals is a division of Combined Metals & affiliate of Gibbs Interwire
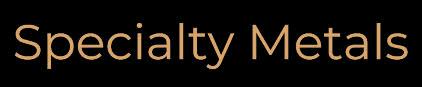
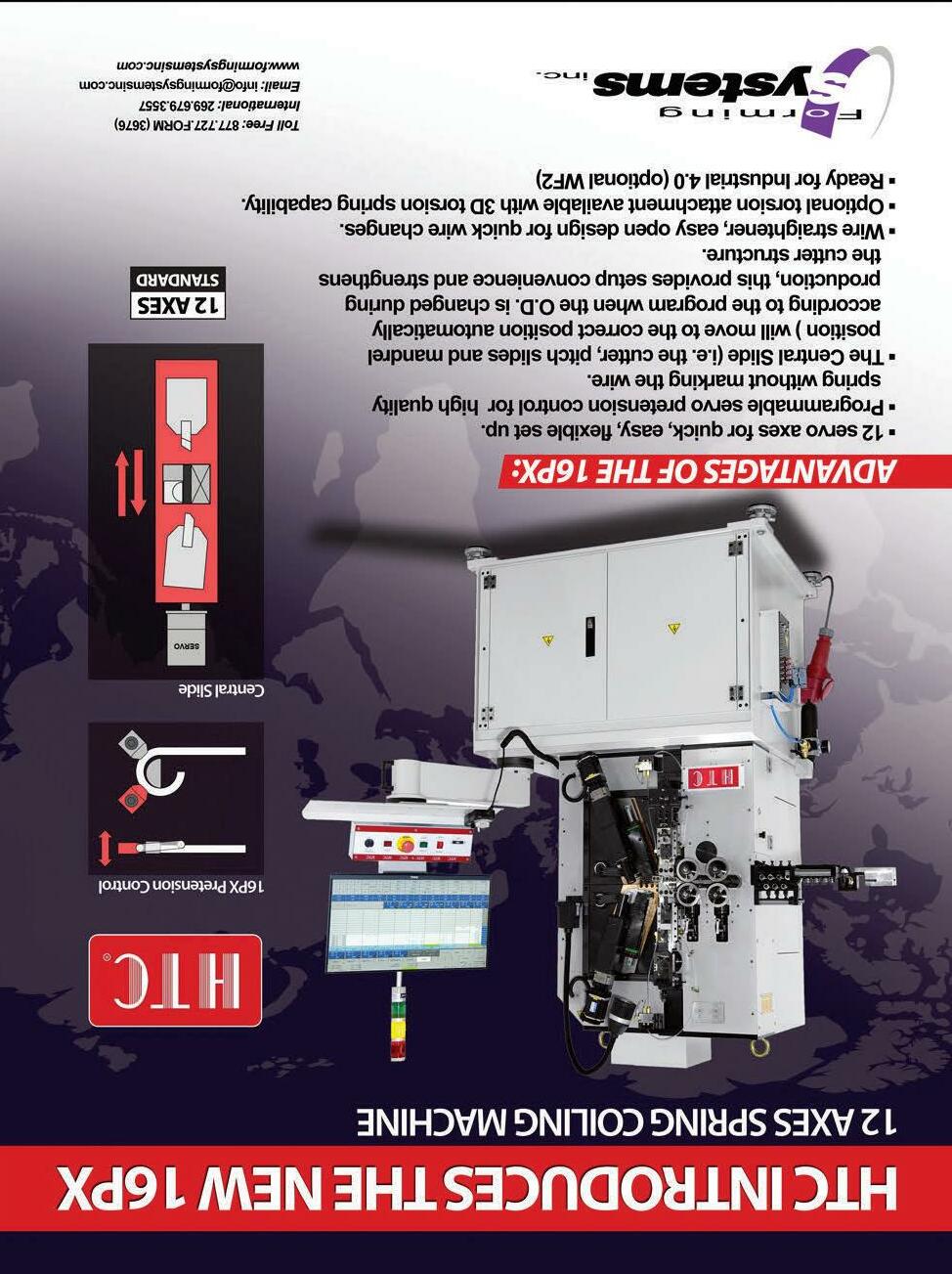