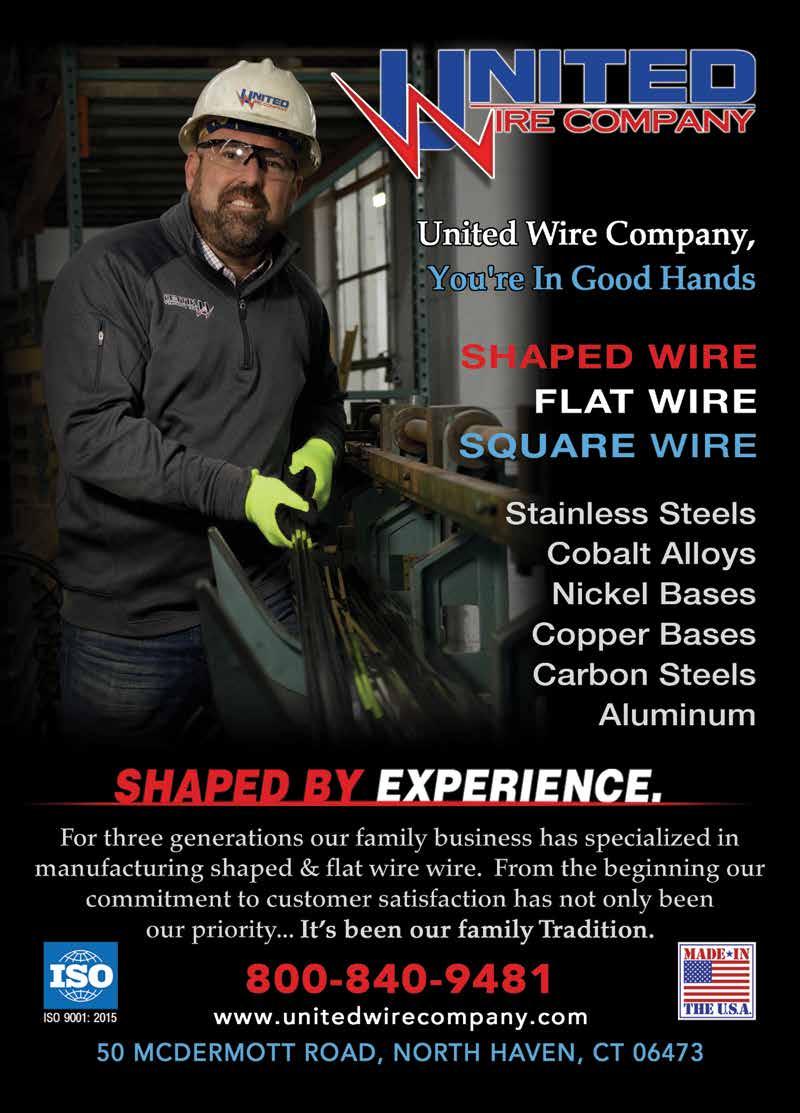
6 minute read
The Impact of Wire Drawing Die Geometry on the Development of Residual Stresses and Potential for Improved Spring Fatigue Life
By C. Richard Gordon
(Editor’s note: This article describes the work presented at the 2019 SMI Metal Engineering eXpo in Pittsburgh, Pennsylvania, on the impact of wire drawing die geometry on the development of residual stresses and potential for improved spring fatigue life.1 The presentation concluded with the proposal to produce test wires for spring manufacture and testing to demonstrate the concept. There was support from SMI members and associate members to conduct this work. Along with many other projects, in March 2020, COVID-19 postponed the experiments. It is hoped this work can be initiated soon.)
Background and Introduction
The presence of residual compressive stresses on the surface of springs is a desirable way to significantly improve spring fatigue life. Shot peening is a common technique used successfully in the spring industry to induce these compressive surface stresses in springs.
In the production of wire drawn through conical converging dies, conventional internal wire drawing die geometry and drawing reduction practices act to produce a nonuniform stress distribution in the wire cross section with tensile stresses present at the wire surface.
Research studies on the impact of changes to the internal wire drawing die geometry have shown that it is possible to change the stress state at the surface of the wire from tensile to compressive.
In this article, changes to wire drawing die geometry will be reviewed and the resultant improvements in stresses and mechanical properties of wire and bar products presented. The results suggest that it may be possible to achieve improved spring fatigue life in some springs using wire produced with an optimum surface stress condition.
A proposed research project is presented to determine how the residual stresses in the wire translate to residual stresses in the spring and the potential impact on spring fatigue life.
Materials Design Philosophy
In the Fall 2019 issue of Springs, 2 I discussed the engineering concept known as the materials design philosophy, which can be used as a tool to better understand composition-property relationships. Briefly, the materials design philosophy shows the relationship between the composition of the material and the final product properties (Figure 1).
A material with a specific composition is processed in a given operation. The combination of the material and the processing results in a particular structure (metallurgical microstructure). The microstructure in turn results in the specific material properties. In reality, the process of design occurs from right to left. Engineers are interested in specific material properties, which in turn are dependent on the structure, which is a function of designed processing of a material with a specific composition.
Material properties such as tensile strength and ductility are determined through mechanical testing, which have been discussed in past Springs articles.3,4,5,6,7,8
Wire Drawing Overview
Wire/rod drawing is a metalworking process which involves pulling the workpiece through a single or series of conical converging die (or shaped wire dies) to reduce the diameter or area and increase its length.
Modern wire drawing can involve single or multi-pass operations. Stresses formed in wire drawing are due to non-uniform deformation and thermal gradients across the wire cross section.
Wire drawing was discussed as part of the Springs magazine series of articles: “Advances in Spring Making Materials — Part 3: Wire Drawing and Heat Treating.”9
C. Richard (Rick) Gordon is the technical director for SMI. He is available to help SMI members and non-members with metallurgical challenges such as fatigue life, corrosion, material and process-related problems. He is also available to help manage and oversee processes related to failure analysis. This includes sourcing reputable testing labs throughout North America, forwarding member requests to the appropriate lab and reporting results and recommendations. He can be reached at c.richard.gordon@gmail.com or 574-514-9367.
For the purpose of this article, Figure 1 was expanded to include the current process of interest, wire drawing. In terms of structure, we are most interested in the stress distribution at the wire surface and how we can modify that stress distribution through a change in the internal wire drawing die geometry.
Lasalle Steel Patent10
LaSalle Steel was issued a patent in 1964 describing the modification of the internal geometry of a wire drawing die resulting in the change in residual stress at the wire surface from tensile to compressive. Implementation of this technology resulted in the production of a new product line of cold drawn bar products. More recent research on wire has shown similar results.
Wire Drawing Die Geometry
Figure 3 shows a typical cross section of a tungsten carbide wire drawing die.9
Wire or rod enters the bell and entrance angle of the die, and these areas are intended to promote wire alignment and lubricant flow and reduce abrasion. Next, the wire enters the approach angle portion of the die, probably the most important feature, which establishes the deformation zone. As a general guideline, wire should make contact halfway to bearing. Next, the wire enters the bearing section of the die. Traditionally surfaces are parallel from entry to exit of the bearing. Bearing length is specified as a percentage of wire diameter. The traditional purpose of this section is to preserve drawn wire size. This is followed by the back relief section which is tapered to minimize scraping of the wire at the die exit.
Traditionally, wire drawing dies are produced with the bearing section with parallel sides. The innovation of the LaSalle Steel patent is to produce the bearing section with a taper as shown in Figure 4.
Methods for Evaluating Residual Stress in Wire
Methods for evaluating residual stress in wire include:
1. metal removal either mechanically or electrochemically
2. metal slitting (cutting)
3. X-ray diffraction and
4. neutron diffraction.
In the LaSalle Steel patent, the simple slitting method was used to demonstrate the concept as shown in Figure 5 with the optimum bearing angle ~ 0°58’ - 1°9’.
Figure 6 shows a) a schematic of the wire splitting geometry and stress calculation and b) a precision diamond saw for cutting small diameter wires.
Proposal for Future Study
In this work, experiments are proposed to determine how the residual stresses in the wire translate to residual stresses in the spring and the potential impact on spring fatigue life.
In part 1, wire coils from the same parent coil will be drawn using 1) conventional wire drawing dies and 2) experimental dies prepared with a tapered die section. Each wire type will be tested to confirm the surface residual stresses produced as a result of wire drawing.
In part 2, if the compressive residual surface stress state is demonstrated using the experimental dies, springs will be produced from each wire type for characterization including spring fatigue testing.
Summary
This article describes the work presented at the 2019 SMI Metal Engineering eXpo in Pittsburgh, Pennsylvania, on the impact of wire drawing die geometry on the development of residual stresses and potential for improved spring fatigue life.1 The potential for modifying the wire drawing die internal geometry to create favorable compressive surface stresses was demonstrated. A proposal for future study was presented and there was support from SMI members and associate members to conduct this work. COVID-19 delayed the start of the project. It is hoped this work can be initiated in the near future. n
References
1. Gordon, C.R., The Impact of Wire Drawing Die Geometry on Development of Residual Stresses and Potential for Improved Spring Fatigue Life, SMI Metal Engineering eXpo 2019, Pittsburgh, Pennsylvania
2. Gordon, C.R., Springmaking Materials/Materials Design Philosophy, Springs, Fall 2019, p.23
3. Gordon, C.R., Types of Tests Used to Characterize Springmaking Materials — Part 1: The Tensile Test, Springs, Winter 2020, p.27
4. Gordon, C.R., Types of Tests Used to Characterize Springmaking Materials — Part 2: The Coiling and Wrapping Tests, Springs, Spring 2020, p. 27.
5. Gordon, C.R., Types of Tests Used to Characterize Springmaking Materials — Part 3: The Torsional Ductility Test, Springs, Summer 2020, p.17.
6. Gordon, C.R., Types of Tests Used to Characterize Springmaking Materials — Part 4: Hardness Testing, Springs, Fall 2020, p.19.
7. Gordon, C.R., Types of Tests Used to Characterize Springmaking Materials — Part 5: The Reverse Bend Testing, Springs, Winter 2021, p.19.
8. Gordon, C.R., Types of Tests Used to Characterize Springmaking Materials — Part 6: Fatigue Testing of Wire, Springs, Summer 2021, p.21.
9. Gordon, C.R., Advances in Springmaking Materials — Part 3: Wire Drawing and Heat Treating, Springs, Winter 2022, p. 21
10. US Patent No. 3,157,274, Method of Controlling Residual Stresses in Materials During Working, by F.A. Kyle et. al., November 17, 1964
11. Yoshida K / Koyama R, Reduction of Residual Stress of Drawn Wires, WAI Journal 2012 45(7):56
SMI has a team of experts, who speak the language of springs, ready to assist you. It could be a metallurgy question about fatigue life or corrosion, or perhaps you need help with a spring design and the use of materials when manufacturing springs. To find out how SMI Technical Services can help you, phone 630-460-8588 or visit www.smihq.org/springsadvice.
Correction:
In the Winter 2023 issue of Springs, Figure 1 in the Technically Speaking article was published in error. A correction was made and can be found in the electronic copy on the SMI website at shorturl.at/mAJUZ.