
1 minute read
There is More to Springmaking Than Just Making Springs
(Editor’s note: In this edition, we wind the clock back to October 1989 to reprint part of Edward H. Lanke’s President’s Message. Lanke, who died March 10, 2010, was the founder and longtime president of Wisconsin Coil Spring. Lanke wrote numerous articles for the magazine and was beloved by many in the industry. His message, from nearly 35 years ago, rests squarely on the continued need to develop a skilled workforce. This should sound familiar to those who currently operate spring manufacturing businesses.)
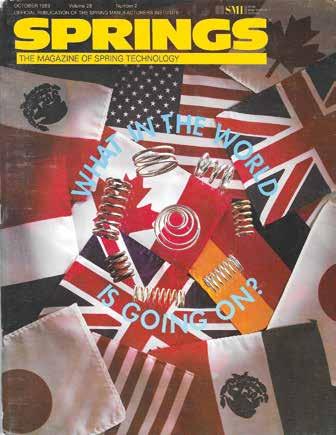
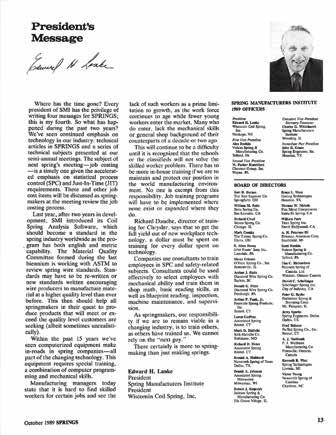
Within the past 15 years we’ve seen computerized equipment make inroads in spring companies—all part of the changing technology. This equipment requires special training, a combination of computer programming and mechanical skills.
Manufacturing managers state that it is hard to find skilled workers for certain jobs and see the lack of such workers as a prime limitation to growth, as the workforce continues to age while fewer young workers enter the market. Many who do enter, lack the mechanical skills or general shop background of their counterparts of a decade or two ago.
This will continue to be a difficulty until it is recognized that the schools or the classifieds will not solve the skilled worker problem. There has to be more in-house training if we are to maintain and protect our position in the world manufacturing environment.
No one is exempt from this responsibility. Job training programs will have to be implemented where none exist or expanded where they do.
Richard Dauche, director of training for Chrysler, says that to get the full yield out of new workplace technology, a dollar must be spent on training for every dollar spent on technology.
Companies use consultants to train employees in SPC and safety-related subjects. Consultants could be used effectively to select employees with mechanical ability and train them in shop math, basic reading skills, as well as blueprint reading, inspection, machine maintenance and supervision.
As springmakers, our responsibility if we are to remain viable in a changing industry, is to train others, as others have trained us. We cannot rely on the “next guy.”
There certainly is more to springmaking than just making springs. n
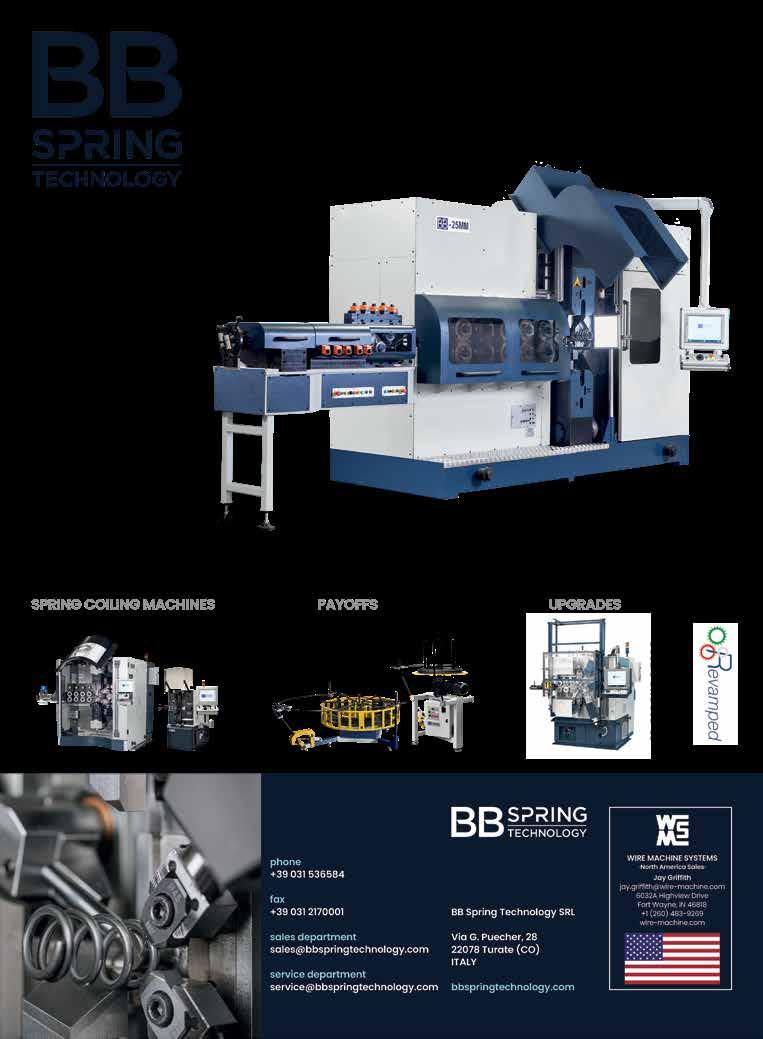