
4 minute read
New Products
©iStockphoto.com/hüseyin harmandaglı, morkeman, PeskyMonkey Alloy Wire International Introduces Inconel Alloy 686

Alloy Wire International, a UK-based leading manufacturer of round, flat and profile wire, recently launched its new Inconel Alloy 686, a single-phase, austenitic alloy that delivers excellent resistance to general and stress corrosion cracking that can occur in aggressive liquids and gases. The company says this wire is expected to be used within components destined for corrosive environments in industries that demand material that performs under the most extreme engineering conditions without premature failure.
Areas of application include springs, wireforms and fasteners throughout the chemical and petrochemical processing, oil and gas extraction, acid processing, waste management and in marine environments.
“Springmakers had a fundamental role in the COVID-19 response, and we continue to support firms who supply products into automotive, aerospace, medical, nuclear and the resurgent oil and gas markets,” said Alloy Wire International’s Stephen Olley. “They require material that can work in all types of demanding applications, from intense heat and sub-zero temperatures to highly corrosive environments. This is why we are so pleased to be launching Inconel alloy 686 after months of trials and testing.”
Alloy Wire International says the new material is available in sizes ranging from .001” (0.025mm) to .197” (5.00mm) and can be made to customer specification within three weeks. For more information, visit www.alloywire.com or follow @alloywire on Twitter.
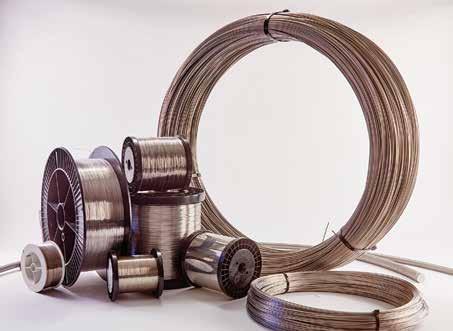
HSI and Forming Systems, Inc. Launches New Conveyor Oven Model HCF85
The miniature HSI Conveyor Oven Model HCF85 is flexible and able to work in-line between springmaking or any other metal hardware machinery. A 3.6 kW heating power and minimized footprint makes the HCF85 a lean and powerful oven. Available with an optional ECB-E, which prevents the springs from bouncing off a conveyor belt.
General specifications of this small oven include: a 11.8” x 1.9” heat zone (L300mm x H50mm); 3.9” wide (100mm) conveyor; and overall size L33.5” x W20.9” x H63.4” (850mm x 533mm x 1610mm).
HSI now offers over 38 standard conveyor oven models and, like all HSI high performance ovens, the HCF85 is available with optional accessories including a digital speed meter, solid state relays, HMI temperature recorder (485H-mini) and a maximum temperature of 500°C (930°F).
For additional information, including option details and pricing, contact Forming Systems, Inc. at info@formingsystemsinc.com or 269-679-3557.
Digital Faceplates and Control Panels Offer Prototyping Solutions
For a rapid, functional prototype to be created to look exactly as the proposed final product, many companies count on printers to create custom faceplates and control panels. Badger Tag & Label has offered digital printing and plotter die cutting for more than 10 years and has seen exponential growth in the requests for short-run pieces used on prototypes. Their wide format digital printing allows for full color plus white to encompass every color imaginable on substrates up to 1.75” thick. The photo quality reproduction and crisp resolution can be combined with lamination for even greater durability.
When the printing is combined with Badger’s Zünd plotter cutter, virtually any intricate cut and quantity are possible. Because no die costs are involved, this is a cost-effective method for a quantity as minimal as one finished piece. Both die and kiss cutting can be completed on the same piece.
“When companies use our services to design faceplates, control panels and other graphics for their prototypes, the development process is quick and costeffective. Those companies get feedback and identify any concerns during the development phase instead of after the final product is launched. We’ve even been able to offer options not considered when we are involved early on,” says Ryan Will, vice president at Badger.
One example of the ideal piece for this process was a self-contained testing kit. Badger’s customer engineered the technology, assembled the components and created the kit. Then they enlisted Badger to design and print the faceplates for both halves of the case as well as the exterior label. The customer shared the prototype with potential clients and was able to validate market interest. They were then able to proceed to full production in a record timeframe.
While these digital control panels and faceplates are an alternative to the traditional metal versions, one area of metal that is exploding for Badger Tag & Label is Metalphoto.® When permanent identification is critical, this process seals the image inside anodized aluminum which makes it resistant to temperatures exceeding 700ºF, corrosion, sunlight, abrasion and chemicals. Metalphoto stands up to the outdoor elements for over 20 years and it meets military specifications.
Contact Badger Tag & Label at 800331-4863, sales@badgertag.com, or www.badgertag.com. n
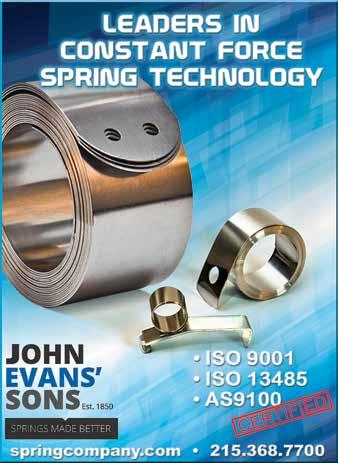
