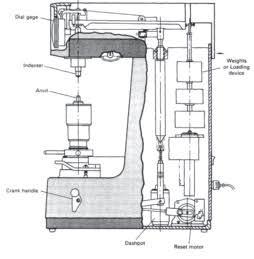
12 minute read
Technically Speaking
By C. Richard Gordon
This is the fourth Springs magazine article in the series regarding mechanical tests for springmaking materials, the hardness test. Previous articles in the series are the tensile test (Winter 20201), the coiling and wrapping tests (Spring 20202), and the torsion test (Summer 20203). This article includes presentation materials from a Testing and Properties class4 that I have taught for a number of years for the Wire Association International as part of their Fundamentals of Wire Manufacturing program.
Overview
In general, the testing of materials represents an important part of all quality work. It can include the control of incoming raw materials, materials in production, and produced materials or components before delivery.
Many different techniques are used, including chemical analysis; microscopy; nondestructive testing; mechanical tests such as tensile strength, hardness and fatigue; and technological tests such as bending, torsion, coiling, wrap and weldability.
In this series of articles, we have focused on mechanical and technological tests used to characterize springmaking materials. In this article, several different types of hardness tests will be discussed.
The uniformity of tensile strength and ductility of the wires used to produce springs are critical to successful spring production and end use. The hardness test can be good indicator of tensile strength.
Hardness Testing
In general, the hardness of a material suggests a resistance to deformation. For metals, hardness is a measure of the resistance to permanent or plastic deformation. For materials testing, hardness can be thought of as a resistance to indentation. Hardness can be correlated with tensile properties of materials. It is an important quality parameter for assessing the suitability for many wire products and springs. It is included as a specification parameter for many sophisticated product standards worldwide. Hardness testing is a key element in many quality control procedures and research and development work.
In this article, several different types of hardness tests will be discussed: Brinell, Rockwell, Vickers, and Knoop.
In all these techniques, an indenter is forced into the sample of interest by the application of a specific load or force, as shown in Figure 1. The depth or width of the impression left is evaluated to establish a measure of hardness.
Force
Indenter
SampleIndentation
Figure 1. Schematic representation of hardness testing.
With the Rockwell hardness test, the depth of indenter penetration is measured. With the Brinell, Vickers and Knoop hardness tests, the size of the impression left by the indenter is measured.
Figure 2 shows typical indentation marks from various hardness tests.
There are essentially two basic types of indentation hardness tests: 1) macro load testing, using loads greater than or equal to 1,000 grams force and 2) micro load testing, using loads less than 1,000 grams force.
Rick Gordon is the technical director for SMI. He is available to help SMI members and non-members with metallurgical challenges such as fatigue life, corrosion, material and process-related problems. He is also available to help manage and oversee processes related to failure analysis. This includes sourcing reputable testing labs throughout North America, forwarding member requests to the appropriate lab and reporting results and recommendations. He can be reached at c.richard.gordon@gmail. com or 574-514-9367.
Figure 2. Indentation marks for 1) Brinell, 2) Rockwell Standard and Superficial, 3) Macro Vickers, 4) Micro Vickers and 5) Knoop tests.
Brinell Hardness Testing (HB or BHN)
The first simple indentation hardness test system was developed by J. A. Brinell of Sweden in 1900. It is considered the first widely accepted and standardized indentation hardness test. The indenter was a 10 mm (0.4 in.) diameter hardened steel ball (now a tungsten carbide cobalt ball). The system uses loads of 500 kg (1,100 lbs.), 1,500 kg (3,300 lbs.), and 3,000 kg (6,600 lbs.) to indent the metal surface. The load is applied for 10 to 30 seconds. After removing the load, the indentation is measured. The Brinell hardness is based on the applied load divided by the surface area of the impression. The load to be used is selected so that the indentation diameter is in the range of 25 to 60 percent of the ball diameter5 . The indentation diameter at a given load is dependent on the material properties.
The Brinell test method is described in detail in “ASTM E10 – 18 Standard Test Method for Brinell Hardness of Metallic Materials.” The test method is specified in “ASTM A125-96(2018) Standard Specification for Steel Springs, Helical, Heat-Treated.”
Advantages and disadvantages of the Brinell hardness test are listed below.
Advantages
• The test is fast. • Minor specimen preparation is required. • There is just one continuous hardness scale. • The indenter shape does not produce a stress riser. • The test is good for annealed and for heterogeneous microstructures. • The test is widely accepted in the U.S.
Disadvantages
• Thick specimens are required. • The test produces a large indentation. • The test gives only bulk hardness data. • High hardness materials cannot be tested.
The Rockwell Hardness Test
Stanley and Hugh Rockwell received their first patent in 1919 for the Rockwell hardness tester while working for a manufacturing company in Bristol, Connecticut. In 1920, Stanley started commercial production of Rockwell testers in collaboration with instrument manufacturer Charles H. Wilson in Hartford, Connecticut. A schematic view of a Rockwell hardness test unit is shown in Figure 3.
The Rockwell tester uses the depth of indent after the preliminary load and before the primary load is removed to calculate the hardness number. Because the indent is not measured, the Rockwell test is faster than the Brinell or Vickers tests. The principle of the test is shown in Figure 4.
The principal criterion for this tester was to provide a quick method for determining the effects of heat treatment on steel bearing races. One of the main strengths of the Rockwell test was the small area of indentation needed. It is also much easier to use as readings are direct, without the need for calculations or secondary measurements.
Because of the wide range of hardness values for various materials, there are 15 regular Rockwell scales which use 10 kg force as the primary minor test load. The superficial Rockwell test was developed in 1932. There are 15 superficial Rockwell hardness scales that use a primary minor test load of 3 kg force. In all, there are five different indenters and six different loads resulting in the 30 different hardness scales.
Since Rockwell hardness is dependent on load and indenter, it is necessary to specify the combination used. For most spring materials, the RB and RC scales are used.
The RB scale is used for softer metals and utilizes a 1.6 mm diameter steel ball and a 100 kg major load. The range of scale is RB0 to RB100.
The RC scale is used for harder metals and utilizes a diamond indenter and a 150 kg major load. The useful range of the scale is RC20 to RC70.
The Rockwell test methods are described in detail in “ASTM E18 – 19 Standard Test Methods for Rockwell Hardness of Metallic Materials1,2.”
Advantages and disadvantages of the Rockwell hardness test are listed below.
Advantages
• The test is fast. • Minimal specimen preparation is required. • The test is free from operator error. • The test covers a wide hardness test range. • High hardness materials can be tested. • Specimen thickness is less restrictive than the Brinell test. • The test is widely accepted in the U.S.

(Left) Figure 3. Schematic view of a Rockwell hardness testing unit5 .
(Above) Figure 4. Principle of the Rockwell hardness test showing a diamond indenter. The same principle applies when using steel ball indenters and other loads5 .
Disadvantages
• The test has less sensitivity. • There are multiple scales, indenters and load combinations, to choose from when testing materials of unknown hardness. • Conversion to other hardness scales is not easy. • The test gives only bulk hardness data.
Vickers Hardness Test (HV)
The macro Vickers hardness test was developed in 1921 by Robert L. Smith and George E. Sandland at Vickers Ltd. as an alternative to the Brinell method, to measure the hardness of materials. The indenter was a square based pyramidal shape made of diamond. The use of a diamond indenter overcame the limitations of the Brinell test for testing harder materials. The Vickers test is often easier to use than other hardness tests since the required calculations are independent of the size of the indenter, and the indenter can be used for all materials irrespective of hardness. The first low-load Vickers (micro) hardness tester was built by Lips and Sacks in 1936.
For both the macro (macro HV) and micro (micro HV) hardness testers, hardness values can be calculated directly using the appropriate constant and knowing the load applied and mean diagonal length.
Advantages and disadvantages of the Vickers hardness test are listed below.
Advantages
• Small specimens can be tested. • Indents can be placed precisely. • Hardness changes can be plotted in relationship to faces, depth or geometries. The test has high sensitivity. One continuous scale is used for testing all materials. The Vickers hardness values correlate well to strength and other properties.
Disadvantages
• Manual operation requires training and skill. • Extensive specimen preparation is required. • Manual operation is time consuming and arduous. • Equipment is delicate and subject to environmental influences.
Knoop Microhardness Testing (HK)
In 1939 Frederick Knoop and his associates at the National Bureau of Standards (now NIST), developed a low load test based on a rhombohedral shaped diamond indenter. The long axis is 7.114 times the short axis. Loads range from 25 to 100 grams. In this test, the Knoop hardness number (HK) can be calculated directly knowing the load applied, the measured long diagonal length and calculation constant. The Knoop indenter is excellent for testing thin coatings and for specimens with a steep hardness gradient.
Figure 5 shows a historic Knoop hardness test unit, a schematic of the geometry of the rhombohedral shaped diamond indenter and a typical indentation mark.
This was the test method used by Dan Sebastian in his SMI White Paper, “Microhardness Residual Stress Study Effect of Stress Relieving Temperature on Tensile Strength, Residual Stress, and Microhardness6.” In this work, microhardness profile data for spring cross sections was compared to residual stress data measured by X-ray diffraction.
Advantages and disadvantages of the Knoop microhardness test are listed below.
Figure 5. A historic Knoop hardness test unit, a schematic of the geometry of the indenter and a typical indentation mark are shown.
Figure 6. Knoop hardness indentations in a case-hardened steel sample7 . Magnification 100X.


Figure 7. Automated Vickers hardness testing unit. (Photograph courtesy of the Leco Corporation9.)
Advantages
• It is easier to test thin coatings in cross-section compared to Vickers. • Indents in a transverse can be spaced closer to each other. • Good results have been observed in materials with a steep hardness gradient.
Disadvantages
• Manual operation requires training and skill. • Extensive specimen preparation is required. • Manual operation is time consuming and arduous. • Equipment is delicate and subject to environmental influences. • Hardness is more variable with test load. • It is more difficult to correlate HK hardness values with strength and other properties.
The Vickers and Knoop test methods are described in detail in “ASTM E92-17 Standard Test Methods for Vickers Hardness and Knoop Hardness of Metallic Materials” and “ASTM E384 – 17 Standard Test Method for Microindentation Hardness of Materials.”
Knoop Hardness Testing Example
Figure 6 contains a photomicrograph of a case-hardened steel part which shows both core (bottom) and carburized outer case (top) regions. The case is harder as attested by the smaller microhardness indentations.
Modern Systems
Today, hardness testing equipment is available which utilizes: • Advanced camera technology for image capture and indent measurement • Programmable computer control for sample positioning (x-y-z), data storage and analysis.
With the introduction of these improvements, speed of testing is better and operator measurement errors have been eliminated. Of course, these equipment improvements come at a cost. Many companies continue to operate hardness test equipment manually. Manually operated and automated hardness test units are available from a number of companies8, 9, 10, 11 . Universal hardness test machines are also available where multiple hardness tests, i.e., Brinell, Rockwell and Vickers tests can be performed on one machine10 .
An example of a modern hardness test unit is shown in Figure 7.
ASTM test methods for hardness testing discussed in this article are shown in Table 1.
Summary
In this article, the Brinell, Rockwell, Vickers and Knoop hardness tests were described. These methods remain the
ASTM E10 – 18 Standard Test Method for Brinell Hardness of Metallic Materials
ASTM E18 – 19 Standard Test Methods for Rockwell Hardness of Metallic Materials1,2
ASTM E92-17 Standard Test Methods for Vickers Hardness and Knoop Hardness of Metallic Materials
ASTM E384 – 17 Standard Test Method for Microindentation Hardness of Materials
ASTM E140 – 12be1 Standard Hardness Conversion Tables for Metals Relationship Among Brinell Hardness, Vickers Hardness, Rockwell Hardness, Superficial Hardness, Knoop Hardness, Scleroscope Hardness and Leeb Hardness
standards for quality control and research and development in the metals industry. Equipment improvements have been made over time to increase the speed of testing and to eliminate operator errors.
Moving Forward
The bend and reverse bend tests are planned for review in a future article. n
References
1. Gordon, C.R., Types of Tests Used to Characterize Springmaking
Materials – Part 1: The Tensile Test, Springs, Winter 2020, p.27 2. Gordon, C.R., Types of Tests Used to Characterize Springmaking
Materials – Part 2: The Coiling and Wrapping Tests, Springs, Spring 2020, p. 27. 3. Gordon, C.R., Types of Tests Used to Characterize Springmaking
Materials – Part 3: The Torsional Ductility Test, Springs, Summer 2020, p.17. 4. Gordon, C.R., Ferrous Testing & Properties, Fundamentals of Wire
Manufacturing, WAI, Fall 2019. 5. Metals Handbook 9th ed, Volume 8, Mechanical Testing, American
Society for Metals, 1985. 6. Sebastian, D.R., “Microhardness Residual Stress Study - Effect of
Stress Relieving Temperature on Tensile Strength, Residual Stress, and Microhardness,” SMI, 2017. 7. R.W. Hertzberg, Deformation and Fracture Mechanics of Engineering Materials, 3rd ed.,1989 John Wiley and Sons, NY. 8. Starrett https://www.starrett.com/ 9. Leco Corporation https://www.leco.com/ 10. Buehler https://www.buehler.com/ 11. Struers Inc. https://www.struers.com/
Untangle Your Springs Problem American Made
Over 25 Years Experience
stop WastIng tImE and man Hours! IdEal For sEparatIng tanglEd:
D-Tangler 2000
• Hooks • Springs • Wire Forms • Rings • Clips • Small Parts
Just type and mark, it’s that easy!

Easy to usE: Just drop your tangled material into the input tube and out they come UNTANGLED!


Dispense Works Inc