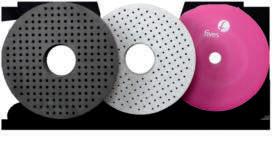
7 minute read
Flashback
The Five Top Causes of Spring Failures and How You Might Prevent Them
By Luke Zubek, PE
(Editor’s note: In this issue of Flashback we reprint a popular “how to” article from a former SMI staff member that originally appeared 10 years ago in the Fall 2010 issue of Springs.)
Examining spring failures over the past years has inevitably led to me to recognize many trends in the causes, alloys affected, and commonalities encountered. I have prepared this article in an effort to summarize my observations on the top five causes and, more importantly, to address preventative actions.
The causes and preventions reflect my own experience and observations and are in no particular order of frequency or importance. When submitting any defective material for failure analysis it is important to provide the consulting engineer with accurate fabricating details, service conditions and operating details. Failure to supply the correct background information can lead to non-conclusive or inaccurate conclusions.
Number One: Hydrogen Embrittlement (HE) HE occurs when three factors are present: 1. A tensile stress of sufficient magnitude either applied or residual. 2. A susceptible material is being used; the most susceptible spring materials are martensitic steels with high hardness (> 35 HRC), containing specific alloys and residual elements. The “poster child” of susceptibility is ASTM
A401 or chrome silicon (CrSi). 3. Hydrogen content above a threshold level (depending on the above two factors only a few parts-permillion are necessary). The source of the hydrogen can be external to the spring like an acid wash. More commonly, the source of hydrogen is already present in the steel; the amount of residual hydrogen in non-degassed steel can be as high as 10 ppm.
HE has also been referred to as delayed cracking since the embrittlement process takes time to occur. Hydrogen atoms diffuse to the grain boundaries that are under tension. As time progresses, the pressure in these areas builds up, ultimately causing the steel to fracture intergranular. After the steel fractures, the detrimental hydrogen is locally liberated and ductility returns to the steel. This mechanism is directly reflected in the fracture features; the transformation from brittle to ductile features is one of the main fingerprints of hydrogen embrittlement.
The most common causes of hydrogen embrittlement in springs are a delayed stress relief, skipped bake after plating, and hydrochloric acid cleaning. Knowing these causes can help prevent HE from occurring.
Some suggestions to help prevent HE: • Stress relief immediately after coiling and use an in-line oven. • Document coiling times and stress relief times on CrSi grades. • Bake soon after electro-plating. • No hydrochloric acid cleaning on oil tempered grades. • Cautiously use high tensile CrSi grades and use music wire whenever possible. • Use a degassed steel that has intentionally low residual hydrogen (~1 ppm)
Number Two: Surface Quality Most surface quality issues that I have dealt with occur on stainless steel grades like 17-7PH and 302SS. These seams or folds are usually just within the required specification and reduce the operational life by facilitating fatigue cracks to initiate. Sometimes the surface takes on an appearance that is described as looking like a turtle shell or alligator skin.
Fatigue typically initiates from one of the deeper folds or seams that are oriented between the grains. These areas are essentially the grain boundaries that are etched out during scale removal. It follows that as the grain size is reduced so is the depth of the seams,
therefore the impact that these seams have on performance is reduced with finer grain size.
To mitigate poor surface quality on stainless steel springs, consider the following: • Electro-polishing the surface will remove the high asperities on the surface and essentially reduce the depth of the surface seams. Springs do not need to be passivated after electro-polishing. • Shot peening the surface puts the surface in residual compression. When peened correctly, this process can double the fatigue life on springs. • Use nickel coated wire. • Purchase wire that has a guaranteed finer grain size. • Don’t over-passivate the spring. More is rarely better.
Number 3: Corrosion Problems with corrosion arise when the spring encounters a corrosive contaminant. This can be a one-time or continued exposure. The bottom line is that the choice of material and/ or processing must fit the operating environment.
Some suggestions that might help reduce the effects of corrosion: • Properly identify the source of corrosion. Regrettably this is usually done after the spring has broken. Corrosion deposits can be accurately identified by utilizing the detectors, like energy dispersive spectroscopy, on a scanning electron microscope (SEM). For exposure to chloride pitting, use stainless steels that contain intentional additions of molybdenum (Mo); the more the better. Alloys 302SS and 17-7 PH do not contain any significant Mo additions; consider using alloys like 316 SS (2.5%Mo), 904L (4.5%Mo), AL-6X (6.5%Mo). In environments that contain hydrogen sulfide, use grades like Inconel X-750 that stand up better than chrome silicon.
Number 4: Processing Issues I’ve decided to make this category “processing issues,” defined as some of the more common processing mistakes that can cause performance problems.
Aside from surface quality problems the two main causes of fracturing during cold forming are: • Cold forming AFTER stress relief. For hard drawn steels like music wire, the stress relief increases the tensile strength of the steel (strain aging). But in the metallurgical world you rarely get anything for free; as the tensile strength increases, the ductility drops.
Therefore, as a general rule complete all forming on the spring before the stress relief is applied. • Cold forming too fast. This mainly occurs on wire forms and simple bends. As the strain rate increases, the ductility decreases. Although your new coiler may be able to make 1000 parts an hour, it may be better
FIVES, A LEADER IN SPRING GRINDING ABRASIVE TECHNOLOGY
GARDNER ABRASIVES:
— Custom engineered — Consistent manufacturing process — Higher speeds & stock removal rates — Advanced bond technology — Over 110 years of abrasive expertise
Visit us at the smi metal engineering expo Booth 619
www.fivesgroup.com
— Cutting Tools | Abrasives E: cuttingtools.abrasives@fivesgroup.com - Concord Twp., Ohio - South Beloit, Illinois - USA
to slow down and make only 800 parts per hour and avoid breaking any parts.
Some other frequent processing problems are: • Sharp tooling marks that mechanically deform the wire surface. • Insufficient stress relief from an overloaded furnace.
Number 5: Fatigue from Overstress This is probably the most common cause of spring failures. For many springs types it is not economically desirable or physically possible to design a spring for infinite life. Springs that fail from overstress originate failure at predictable orientations, where the amount of operational stresses are the greatest. For compression springs, the fracture initiates at the spring ID. For torsion springs, the fracture initiates at the spring OD. And for extension springs with hooks, the fracture occurs at the inside bend of the hook. In general, if the cross sectional area contains about 50 percent smooth fatigue features and contains no material or quality issues, I would consider the failure to be “normal.”
The most common example of a “normal” overstress failure occurs on the hooks of an extension spring. The most simple and cost effective solution to lower the operational stresses is to reduce the last few coil diameters along with the hook diameter.
I’ve examined many fractures on springs that were unnecessarily designed right at or just above the recommended maximum stress level. Most of these issues can be resolved quickly with the help of a good spring design software, like ASD 7.0. This software produces efficient designs on nested springs, conical springs and springs in series. This Windows-based software can make fatigue life predictions when two operational loads are entered. When knowing the fatigue life becomes critical, there is no replacement for actual testing of the spring, preferably in the same or similar operational environment and assembly.
This covers most but not all causes of spring failures and some of the more practical solutions that may help prevent these problems from occurring. An experienced springmaker will recognize that most of these solutions will increase the price of the spring. In some applications it may not even be possible. There also may be many other solutions to these issues, so please feel free to send your comments to me at ljzubek@gmail.com. n
Luke Zubek, PE graduated with a masters degree in engineering from Illinois Institute of Technology. Zubek has more than 30 years of experience in the metals industry including 10 years with a major steel producer and six years as SMI’s technical director. He currently works for CNH Industrial as senior materials engineer. He can be contacted at ljzubek@gmail.com. This article was peer reviewed when it originally appeared.
INTRODUCING
Spring Testing REVOLUTIONIZED
The Authority on Accuracy.
NEW
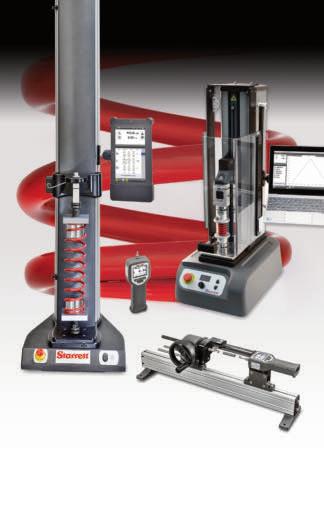
Available with Basic or Advanced Software
Innovative Spring Testing Solutions
MADE IN
Starrett offers a complete line of AMERICA innovative force solutions for spring testing. In addition, a new, affordable For more information visit high volume production testing starrett.com/springs solution is available in basic software (S1) and advanced (S2).
PRECISION TOOLS/GAGES
SPRING TESTING
spring inspection
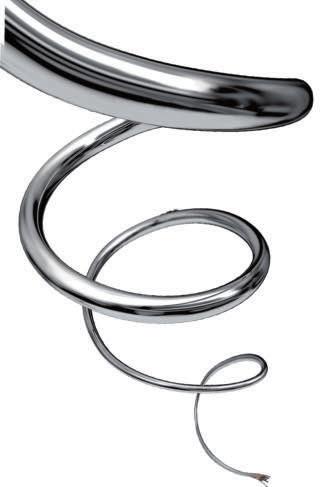
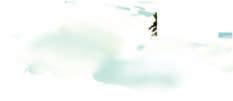