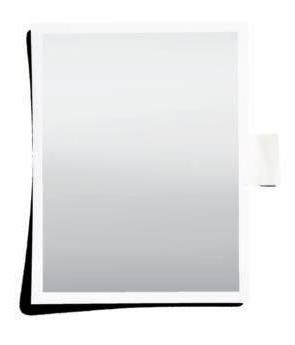
7 minute read
Important Considerations When Testing Springs with Force Systems
By James M. Clinton
Spring testing is one of the most difficult testing processes. A common misconception is that because springs are viewed as relatively simplistic components in terms of design and function, they must be just as easy to test and verify. There are also many deleterious factors and improper techniques that affect the accuracy and methodology used when testing springs.
This article covers critical considerations and basic force testing precautions when testing extension and compression springs.
Testing System Load Capacity Using a load sensor that is suitable for the spring being tested is a major consideration in accurately testing springs for spring rate, spring constant, initial tension, free length, etc. Do not attempt to test a spring with a load rating that is less than 20 percent of the load system’s load cell sensor. For example, if the force system has a 500N (110lbf, 50kgf) load cell, that sensor is acceptable for testing between 100N (22lbf, 10kgf) and 500N.
Load Cell Deflection A load cell sensor must deflect in either compressive or tensile directions in order for the sensor to provide a measured output. Additionally, the entire load string used in the test will have some deflection ‒ for example, the testing fixture, the test frame, the crosshead, etc. Deflection may need to be compensated for when testing springs. Some force testers have a deflection compensation feature within the corrections setting, which is extremely helpful. Grip String Alignment The grip string is the combined load cell sensor and testing fixture (top and bottom) that is used to test the spring. Hooks are often used for testing extension springs. Platens and specialized testing fixtures that ensure spring containment during compression are used for compression springs.
It is absolutely critical that the spring being tested is perfectly aligned to the grip string. The spring should be in the center of the platens to ensure even loading.
Correct Spring Preparation Accurate measurement of spring rate, spring constant, free length and initial tension require that the spring is designed and manufactured correctly. Compression springs should have a perfectly flat surface at both ends (top and bottom). If not, length measurements are compromised, which can lead to inaccurate and inconsistent spring rates. Compression springs with ground ends can often be tested with simple platens. Springs without ground ends can have trouble standing unsupported, and typically require a guide rod that runs through the center of the spring to keep it in place during testing.
Extension springs, with initial tension, should have loops that are perfectly symmetrical to each other. Extension spring loops should have equal distance between the inside of the loop and the first coil. Extension spring loops should have a common seating location within the loop — for example, when the spring is under load, the position where the loops align should be parallel with each other. Most spring loops such as circular or v-shaped ones will automatically guide a hook into the proper position. For some springs such as the modified or custom types, hooks may be preferred. For example, the square shaped loop won’t center a round hook.
Note that if there are inconsistencies in the spring’s physical makeup, measurements will be affected. If a manual system had previously been used, such as a force gauge with manual test stand, it will be difficult to correlate the data. Force gauges cannot compensate for physical inconsistencies on the spring, and do not have any deflection compensation.
Correct Testing Fixtures Compression springs can be tested using platens as long as the platens are not oversized to the spring’s outside diameter. Accurate compression measurement suggests that the platen should be no greater than 25 percent of the spring’s outside diameter. Compression springs should use a testing fixture that will contain the spring should the spring “walk,” or move to the point where the spring can shoot out of the platen.
When testing an extension spring, there is always some movement of the spring as it is pulled apart. The end loops will typically position themselves to a perpendicular location along the grip string. However, if the hooks used to secure the loops have a rough finish, or
Application Advice
One of the most common problems in testing springs is using a load sensor that has too large a measurement capacity for the spring under test. Do not attempt to measure spring forces that are less than 20 percent if the load cell sensor being used. Two-point tests are always preferred for better accuracies versus a one-point test setup. A best practice is to use two points (either load or height) that are at 20 percent and 80 percent of the spring’s full-scale. Deflection compensation may be used. The testing system and its components will deflect during a compression or extension spring test. This deflection may be compensated for or removed for accurate and repeatable testing. The spring being tested must be aligned perpendicular to the centerline of the grip string. The top of the spring must be perfectly parallel to a top test fixture. Correct alignment of the spring is critical for proper measurements of heights, lengths or load rates. Loops on an extension spring should promote selfalignments. Both loops should be identical in size and location with respect to the spring centerline. Initial tension is on any extension spring with closed coils, and it is important to understand what the initial tension specification is for the spring before testing. A compression spring under load represents a projectile. Extreme care should be taken when testing a compression spring. The test fixture should be one that captures the spring, and a safety shield is strongly recommended for any spring test. Use the proper testing fixture based on the spring’s physical design. There are special self-aligning platens that must be used when a spring may not have a perfectly flat surface at its top or bottom. Hooks with a high-polished finish and low-resistance finish should be used when testing extension springs if friction affects the measurements. Friction will affect spring measurements, so consider using a lubricant on the platen surface when testing Belleville washers. A lubricant or grease can be used on extension hooks to minimize frictional effects. Data sampling will affect spring results, so if correlating data to a previous system that uses RS-232 or a handheld force gage, it may be necessary to reduce the sampling rate. It is always best to test springs at the lowest acceptable speed. Testing at too great a speed can cause repeatability errors as well as some measurement errors. Hysteresis is found in most springs. Free length is generally measured when the compression spring is returning from the load target (measured when going back to its home position, rather than measuring from its home position on the compression move).
are too large for the spring, it is common for the loops to exhibit frictional errors that affect accurate measurements of free length and initial tension. Hooks used for extension spring testing should have a low-resistance surface to minimize any frictional effects and should not be oversized compared to the spring loop opening and type.
Friction Effects Belleville washers are difficult to accurately test. Test fixturing is critical since frictional forces caused by the spring flattening during compression and against the platen surface is highly likely.
To eliminate frictional effects, use the proper type of platen, typically a smooth surface with a hardness of HRC60 or higher. Consider using some type of lubricant, such as a fine machine oil on the surface of the platen, to counter frictional loading.
A compression spring will unwind slightly during compression, so a small degree of spring movement can be expected.
For extension springs, use hooks with a smooth surface also. Applying a small amount of grease on the hooks will help to minimize frictional effects.
Correlating Data When changing or upgrading from one force testing system to another, it is important to correlate the data. Examine existing test methods and system components, including the type of load sensor and testing fixture. Make sure the load resolution is identical to the previous system. If the load resolution is different, different results can be expected for spring rates, free length and initial tension.
Testing Speed Testing speed is generally subjective and dependent on the application. In a production environment, testing speed will be greater for better throughput. In a lab environment, testing speed will tend to be lower. It is always best to test at the lowest speed possible. Spring testing using a force gage and manual tester is not recommended, since velocity is unknown and inconsistent.
Hysteresis Effects There is some hysteresis when checking a compression spring that is not fixtured over a pin. The coils unwind when compressed, and the end coils twist and move on the platen. Platens can be put on bearings to eliminate this effect for extremely precise springs.
A solution for hysteresis is to measure the load while compressing the spring and again on the return move. Take the average of these two readings. This averages out the hysteresis. Make sure to check that the amount of over travel does not cause the spring to set. n
James M. Clinton is the product manager, force, material test and special order for The L.S. Starrett Company. Visit www.starrett.com.
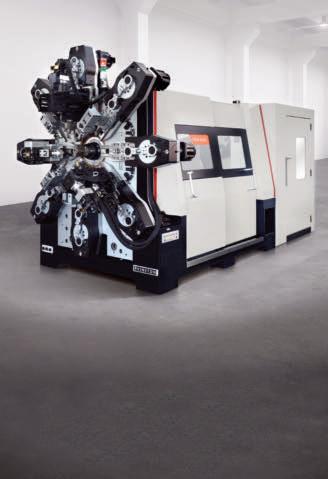