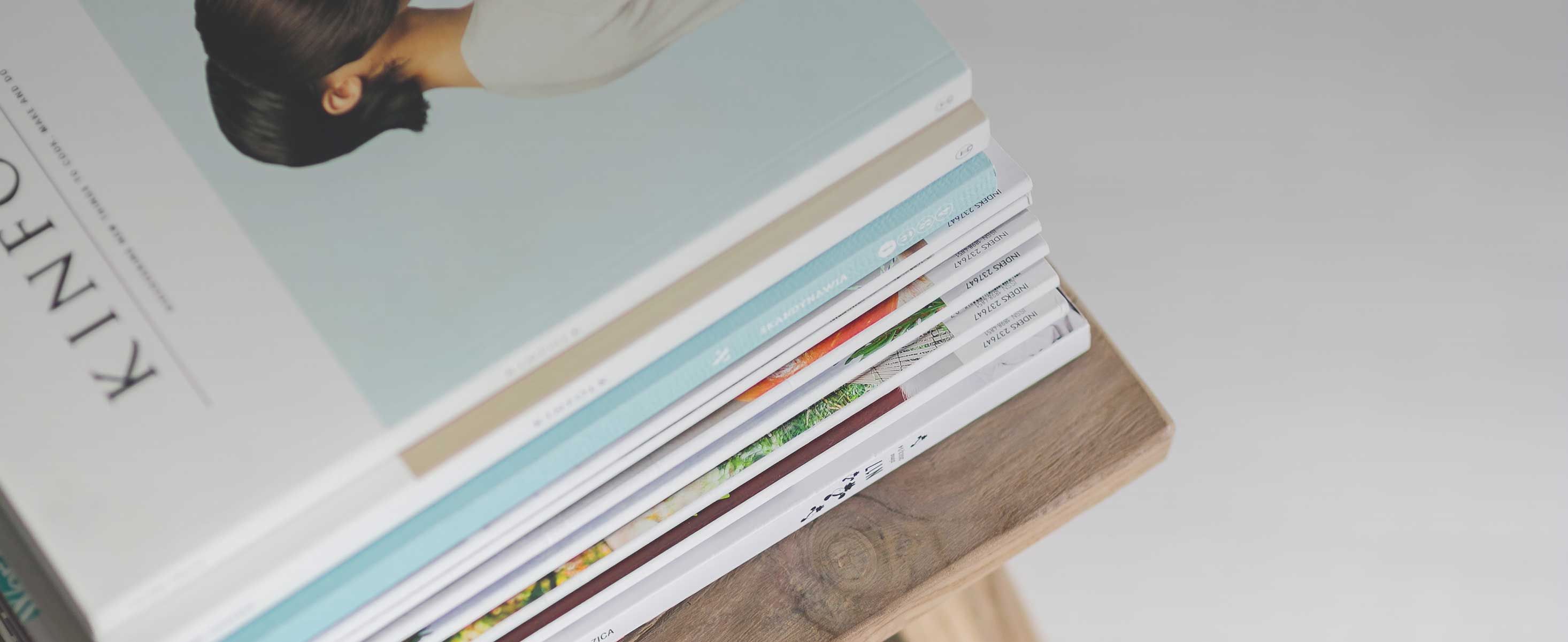
3 minute read
5 Conclusions
Issues and challenges Clamps are a grossly polluting and inefficient brick making technology, but they are widely used since the initial cost of setting up a clamp is very little, as it does not have any fixed structure. It is also difficult to enforce regulations on these kilns, which can literally be moved from one place to another. Different studies and surveys conducted on clamp-type kilns have highlighted the following issues: • Specific energy consumption is highest in clamps compared to other brickmaking technologies employed in the country. • The loss in terms of over- and under-burnt bricks is huge. The number of good quality bricks produced is only about 50 per cent. • Clamps hardly follow any siting guidelines and are usually located in the vicinity of residential area, highways or water bodies in order to have easy access to the market for the finished product and easy availability of the raw material, causing nuisance to nearby inhabitants and adding to the pollution load in environmentally sensitive zones. • Clamps do not use any air pollution control mechanism; the green bricks are simply stacked and set on fire which results in huge emissions. • The heat loss from the surface of a clamp is very high, thereby resulting in higher amount of fuel consumption. • In the absence of proper engineering practices, there is incomplete combustion of fuel, which results in emission of large amounts of black carbon. • Getting clamps under the regulatory radar is very difficult for the agencies as clamps are not housed within any permanent structures.
Brick manufacturing in India has been paid very little attention, despite it being resource- and labour-intensive, as well as having poor environmental performance record. Considering the huge environmental impact of clamp -type kilns in terms of energy inefficiency, contribution to green house gases as well as black carbon emissions, and loss of other natural resources, this so-called informal sector needs to be formalized and given the shape of a proper industry. The formalization of clamps as an industry will not only have to be focused on reduction of emissions but should also take into consideration the loss of invaluable natural resources.
Advertisement
Recommendations Considering these issues and challenges, a roadmap for clamp-type kilns in Maharashtra and elsewhere in the country has become the need of the hour. CSE had classified clamps into two groups on the basis of use and made a separate set of recommendations for environment friendly operation of each group:
1. Non-commercial clamps A unit is considered non-commercial if it manufactures bricks for the personal use of the clamp operator. The typical batch size of these units is generally 10,000 to 25,000. They use agricultural waste as internal fuel, and wood and wood-based charcoal as the main fuel. The SEC of this type of kiln is very high— in the range of 2–3 MJ per kg of fired bricks. Labour is provided by family members and the kiln is usually located at a place where the bricks are needed.
Switching to other brick making technology immediately is not feasible for these clamps and, thus, a period of three years, i.e., till 2020, should be provided to them. Meanwhile, to improve the environmental performance of these kilns, the following measures can be enforced: • Such clamps should make use of some kind of removable enclosures which can be refitted in other clamps to reduce the SEC and increase efficiency. • Flue gases from the enclosed clamp should be channelized through a chimney to reduce the concentration of emissions. Stack height can be decided according to the batch size of the clamp. • There should be internal fuel and waste mixing in the clay preparation while making green bricks. • There should be multi-layer fuel placement while stacking green bricks. • To reduce fugitive emissions, a mobile water sprinkling system should be utilized. The area around the clamp should also be paved to avoid pollution due to dust.
2. Commercial clamps Commercial clamps are those units which have a batch size of 25,000 to 1,000,000 bricks and the annual production is in the range 1.5 lakh to 10 million, depending upon the demand. Bricks are supplied not only to the local area but also cater to the need of bigger construction establishments and builders. The SEC of this type of kilns is also on the higher side, ranging between 1.5–2.8 MJ per kg of fired brick.
Considering the environmental impact of these kilns, it has become necessary for such kilns to switch to a cleaner technology like zigzag. This transition should be enforced strictly.