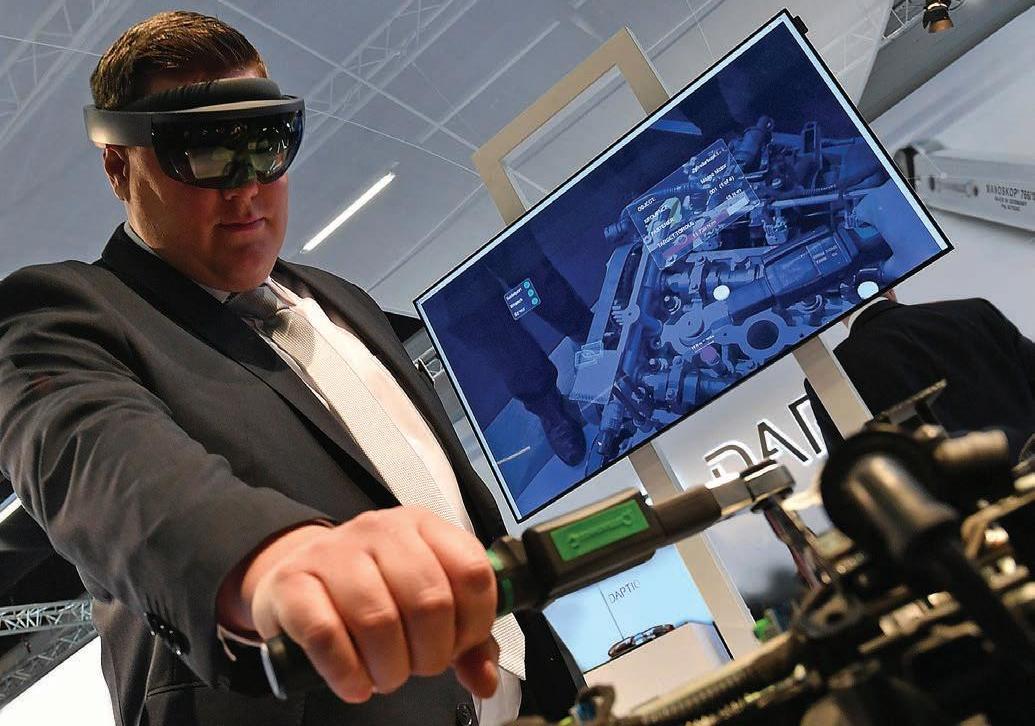
23 minute read
FOCUS SMART & CONNECTED TOOLS
Torque tools are becoming increasingly integrated in the digital working environment
DIGITAL TOOLS Torque tool specialist Stahlwille takes a firm position with Industry 4.0 solutions
Industry 4.0 solutions are playing an increasingly decisive role when it comes to making business processes more efficient. Anything that can be computerised will be computerised. This megatrend is already having a major impact on the development and use of hand tools. Torque tools, measuring and testing units will become increasingly integrated in the digital working environment and will communicate with one another. This does not only apply to large industrial enterprises, but is becoming more and more relevant for medium sized and smaller companies. Stahlwille has already positioned itself now to respond to these developments strategically and in the long term. The result is DAPTIQ, a range of integration-enabled solutions for use in Industry 4.0 environments that is being continuously expanded and developed. The focus is on minimising setup costs, reducing process costs and, in this way, accelerating processes while improving transparency.
Real-time response
Using DAPTIQ solutions enables real-time responses to changes in production processes and in maintenance. Efficiency and process capability can be significantly improved but above all, secure automatic logging is guaranteed. DAPTIQ products can not only communicate with each other, but also with other systems in the specific working environment. The use of these solutions does not require any complex interventions in the IT infrastructure by the customer. Stahlwille has opted for open and flexible programming interfaces. The integration of DAPTIQ solutions in production planning and control systems is possible without any major adaptation efforts, no software from Stahlwille is required. Tailored closely to the needs of the user, the system enables future-orientated applications incorporating intelligent worker guidance and position determination to be set up.
Short training periods and high process capability
Controlled fastener tightening is becoming increasingly important in production processes and maintenance, and the same applies to the requirement to record bolted connections and tightening parameters. Intelligent strategies can be implemented to meet this requirement using integration-capable tool and torque solutions. In connection with superordinate systems, DAPTIQ solutions require only short training periods and provide enhanced process quality. At Stahlwille, the customer is always the focal point. The electromechanical torque wrenches are the only ones on the market that provide the familiar feedback of the mechanical "click", combined with the advantages of a tool that is integration-capable.
MANOSKOP 766 DAPTIQ – full integration in Industry 4.0 environments
The electromechanical angle-controlled torque wrench MANOSKOP 766 DAPTIQ can exchange data bidirectionally and receive and execute instructions. Users are freed from timeconsuming routines and training times are shortened. Human error and, as a result, the error rate are reduced. Last but not least, interaction with the customer's centralised systems means automatic logging of tightening data is a simple matter. This tool is the only one on the market that works electromechanically: it measures digitally and can be networked wirelessly. The wrench signals three times whether the tightening operation has been carried out correctly and the specified target torque has been reached – by means of an LED traffic light system, the digital display and the familiar click. The system also detects whether fasteners have been overlooked or tightened twice. Error messages cannot be ignored. The Manoskop 766 Daptiq can be directly integrated into worker guidance systems. When a fastener-tightening process is initiated, the tool receives its data from the process control system via radio transmission and the required torque is set automatically. The display of the tightening sequence and of the assembly points is possible in a number of ways – using permanently installed monitors, for example, or mobile end devices such as tablets. Completed tightening operations are reported back to the process control system in real time in a traceable and lossproof manner, logged with a time stamp and the exact torque, and the result visualised on the monitor screen, which ensures seamless traceability at all times.
Calibrating and testing in-house
With DAPTIQ perfectControl, Stahlwille offers a calibrating unit which, depending on the version, is able to calibrate both torque and angle-controlled wrenches automatically. The user is guided through the entire testing process by the software. Electronic torque wrenches can be calibrated fully automatically to a large extent. As soon as calibration has been completed, the corresponding data is available to the computer aided quality assurance (CAQ) system for archiving. With the SmartCheck, end users can check torque and angle tightening tools themselves to ensure, before work begins, that the tools are working exactly and reliably within the specified tolerance ranges. With the DAPTIQ version of this solution, Stahlwille provides a model that has a non-proprietary cablelinked interface for direct connection to the CAQ system, for instance. This allows automated workflows to be created in which every tool has to be checked first before the CAQ system releases it for production tasks.
Stahlwille’s Manoskop 766 in action Open to new solutions and business models
Stahlwille is continuing to add to its DAPTIQ range. Products that promise to deliver added value to customers in connection with networked production will, in future, always be available as DAPTIQ versions. Stahlwille is also driving the development of completely new business models. With "Pay per Use", the user no longer pays for the tool, but for the actual use or for the data generated in the process. With a view to life cycle costs for use of the tool, such models provide for capital expenditure that is far more calculable. Customers have the possibility to expand these solutions for their tools step-by-step up to an all-round carefree package. That includes modules such as training, usage analysis, condition monitoring, calibration, repair and maintenance, and an exchange service. In the course of the digital transformation of processes and companies, Stahlwille also supports the development of digital IoT platforms, such as SIEMENS MindSphere. In doing so, the company is applying its expertise as a pioneer in torque technology to implement data-driven business models, which offer customers more flexibility and greater efficiency while reducing costs.
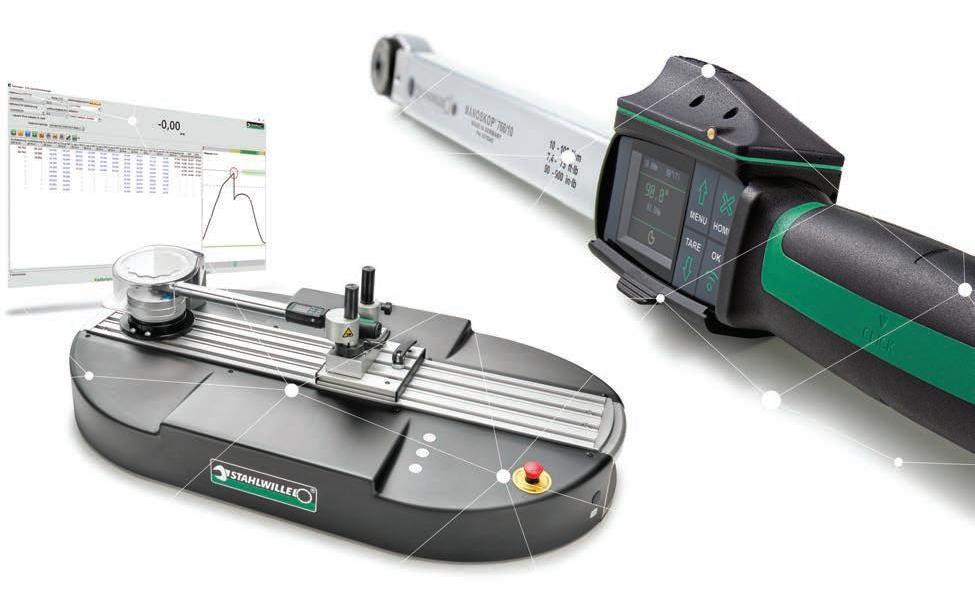
www.stahlwille.de
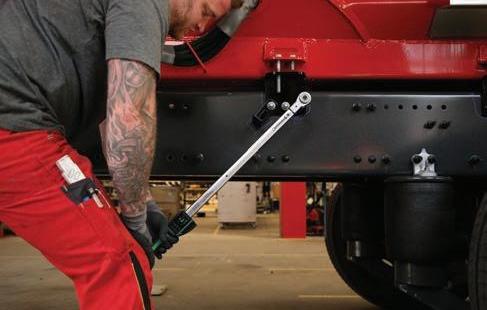
The automatic perfectControl DAPTIQ calibrating unit reduces time and effort required to calibrate and adjust torque wrenches
A £100,000 birthday present
Hague Fasteners celebrated its 50th anniversary by looking to the future, bolstering its manufacturing power with a £100k CNC machine…
“I
t’s the busiest 18 months that I can remember,” Hague Fasteners Managing Director Jon Hague tells Torque Magazine. The family business and Black Country manufacturer is celebrating its half century this year and Hague says 2020 was one of the most successful of his tenure. That’s why the firm has taken the decision to invest, he explains: “Now is the time to renovate and future proof the business.” That project has included a whopping £100,000 investment into a new three-axis CNC lathe to help the business deliver more complex parts and increased capacity. The XYZ CT 65 LTY was commissioned at the start of October and has already been used to deliver contracts for the oil and gas sector, with the company hoping the additional turnover will help it move towards its target of £2 million sales by year end. The big investment can perform complex steps in one operation and as it is easy to set up, smaller runs become ever more worthwhile. Hague adds that future investments will likely also look at machines that are more efficient in this way, rather than in terms of square footage expansion. The road to 50 has not always been straightforward, however. The firm has been subject to the peaks and troughs that have affected UK manufacturing over recent decades and even faced its own ‘make or break’ spell over a decade ago. Suffice to say, Hague Fasteners came out the other side more strongly than ever. In 2017, the firm moved to its current 8,500 ft² on Monmer Close in Willenhall in 2017 and now focuses on small batches of specialised items, often troubleshooting and lending its expertise and sticking to a high spec philosophy. The company produces specialist fasteners, headed bolts, studs, nuts and milled components in high integrity materials and critical nickel alloys. It has built an enviable reputation for supplying products you can’t get off the shelf in small to medium batch quantities and in very fast lead times. Working with high integrity steel and superalloy bar, the company can work to customer drawings to produce parts ranging in size from 2mm to 250mm in diameter. Alongside MD Jon Hague are his wife Claire and sons Jack (Technical Director), Tom (Customer Service) and Max (Finance). The family ethic extends to all of its 16-strong workforce, says MD Jon Hague, while a new crop of apprentices are also proving their worth. “Jaguar Land Rover has done us a favour, by selling the idea of engineering as a career path,” explains Hague. Claire Hague, Company Owner, went on to add: “We also wanted to do something in our 50th year that left a lasting positive legacy, so made the commitment to become Carbon Neutral by 2024. “This has seen us create the ‘Hague Forest’, where we will endeavour to plant and grow 200 trees every year in Haiti, Kenya and Madagascar to offset the 75 tonnes of CO2we create manufacturing specialist fasteners for use across the globe.”
www.haguefasteners.co.uk
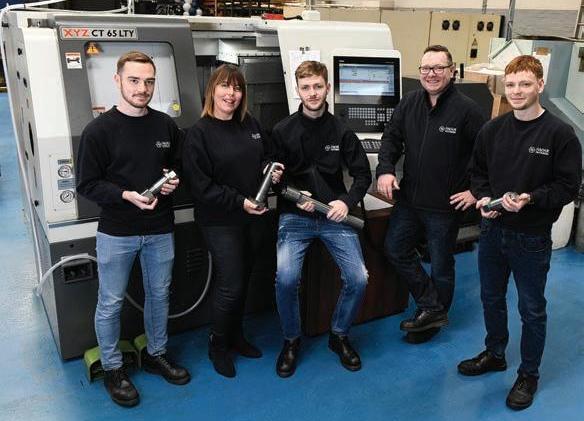
Standard Listed - you know who’s best! But contact us for all the rest...
• Non-preferred Metrics • Intermediate Sizes • Short and Long Lengths • Slotted Grub Screws • A4/80 Bolts & Socket Caps • 6 Lobe (TX) Drive Screws • All Metal Self-Locking Nuts • Studding Connectors And many more...
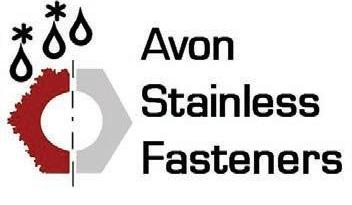
SMART RIVET TOOLS FROM STANLEY
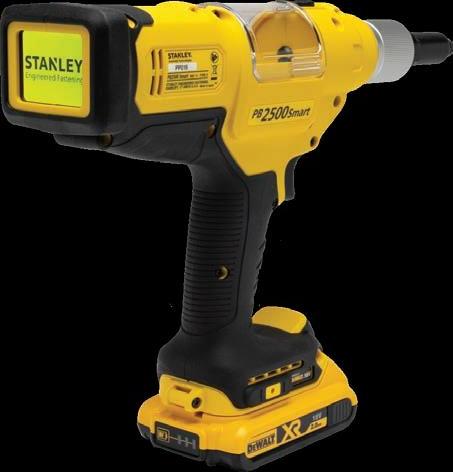
STANLEY’s high performance Smart Rivet Tools allow manufacturers to reduce scrap, optimise the assembly area and provide real-time process data by recording the stem break load and rivet pull distance.
PB2500 Smart Rivet Tool
The PB2500 Smart is an evolution of the original proven and robust PB2500 tool, delivering a leading cordless blind rivet installation and process monitoring system. It maximises productivity: The PB2500 Smart installs 1,100 steel 4.8mm (3/16”) open end fasteners with a single charge, using a 2.0Ah battery. On-board process monitoring ensures that incorrectly fastened joints are detected immediately, preventing entire batches being affected. It’s easy to use too: The PB2500 features a quick release nose housing and jaw guide, quick slide battery installation, LED light to ensure clear line of sight to the application and ergonomic soft grip handle for operator comfort. The built-in touch screen allows the process monitoring system to be easily set up and used. Without having to negotiate the constraints and hazards of a compressed air line, operators can easily move around applications, while the balanced ergonomic design maximises output and reduces operator fatigue. The on-board process monitoring system includes OK / Not OK notifications for each rivet installation, together with a review of the related placing curves. A whopping 500,000 setting results can be stored. Unscheduled downtime is never welcome and the PB2500 avoids it with its long-lasting DEWALT lithium-ion battery with what STANLEYsays is an industry leading charging time. Toolless, quick change, nose housing and jaw guide systems further enhance productivity. The Wi-Fi and Bluetooth-enabled tool delivers permanent and vibration-resistant assembly when used in conjunction with STANLEYEngineering Fastening breakstem rivets.
Avoiding unscheduled downtime: The DEWALT lithium-ion battery is long-lasting with what the firm says is an industry leading charging time BR12PP-8 Smart Rivet System
Also from the STANLEYEngineered Fastenings stable is the BR12PP-8 Smart Rivet Tool with the QBE-Series Controller, which together provide an advanced level of capabilities for rivet setting. The BR12PP-8 is a programmable, full errorproofing and process monitoring cordless blind rivet setting system 8kN covering rivet sizes 1/8”(3.2mm) and 3/16”(4.8mm). The BR12PP-8 delivers advanced error proofing capabilities such as Rivet Count, Job Select, and Connection to the error proofing systems of customers. In terms of process traceability, the BR12PP-8 offers onboard storage of 500 rivet pull results, with two rivet pull traces stored locally, which provide force, distance, speed, current and bus voltage recorded every 1ms during the rivet pull. All the recorded force data is easily exported and it can be integrated with manufacturing execution systems where every rivet and vehicle can be linked together for future reference if needed. Once again, increased productivity is possible because the BR12PP-8 tool can be configured with an optional barcode and can change between 16 different jobs, another great location for this tool is where multiple rivets or application thicknesses are present.

DELIVERING QUICKER, SAFER AND SMARTER MAINTENANCE OF WIND TURBINES

With more demand for smart bolting solutions that can handle bigger and more powerful turbines come on stream, Atlas Copco Tools explains how it is bringing its Smart Connected Assembly philosophy to the field as well as the factory…
The wind energy sector is focused on generating increased wind farm output and reduced operational costs as energy companies are under pressure to reduce wholesale electricity prices through more renewable delivery. From a supply chain perspective, Atlas Copco Tools and Industrial Assembly Solutions is experiencing rising demand for its smart bolting solutions, as bigger and far more powerful turbines capable of generating up to 15MW of electricity come on stream. As turbine size increases, the requirement for tightening larger bolts in challenging off-shore environments, as well ensuring fewer bolted joint failures, improved operational efficiency and faster installation times, is therefore critical. In the context of tower construction and turbine installation and maintenance, Atlas Copco is focused on helping its partners to overcome logistical and operational challenges, as well as delivering competitive advantages in efficiency, whilst reducing risk, time on task and of course, costs. On a mission to apply its Smart Connected Assembly philosophy in the field, as well as in the factory, Atlas Copco has pioneered a number of transducerised tools and data driven systems which, thanks to in-built cloud connectivity, has made it possible for a fully traceable process to be effective at remote installations. The SRB HA Smart and Connected battery nutrunner models, for example, feature an internal Wi-Fi server, allowing the tools to be linked to any mobile device. This enables torque, angle and batch data collection without the need for additional software. For the ultimate in functionality and process control, the SRB HA features an accessory bus for a barcode scanner and can also be integrated into overlying systems for live data feed and analysis. Powered by Lithium-Ion 36V battery technology, the SRB HA is also the only product of its type on the market equipped with a dual trigger, designed to avoid the risk of finger pinch injury. The Tensor Revo HA was designed specifically for use in the construction and maintenance of turbines, requiring high access. Delivering tightening performance of up to 8000Nm, its DC electric motor is the fastest on the market by up to six times, says Atlas Copco, and also features an integrated torque transducer, which measures real torque applied to the joint. To ensure errorproofing, the Tensor Revo HA has a signal light incorporated in the motor housing, indicating green for ‘tightening OK’ and red for ‘fail’. Its high torque, slim gearbox with 360° gear swivel enables access to the trickiest located bolts. Not only does the torque transducer measure the real torque but angle measurement ensures each bolt is tightened correctly by detecting damaged threads or variation in lubrication. All bolt tightening data can be downloaded and linked to bar codes or identifiers. Even graphical traces of the actual tightening can be stored for analysis. Atlas Copco recently introduced the PFXC (Power Focus CrossCountry) power pack. Whilst existing packs available in the market are often big, bulky and not functional for field use, making them prone to damage which causes costly issues, the PFXC is built to withstand extreme weather. Featuring rugged waterproof construction and robust metal framing, the unit can be easily transported to site for the benefit of operators. In order to have a truly connected and efficient system it is critical that all bolting technologies (hydraulic torque, bolt tensioning, continuous rotation) have one common user interface, both for operational process control and data analysis. Users can instantly connect tools to the power pack with any Wi-Fi device via the QR Code and programme in presets, such as target torque, method and speed. Combined with smart technologies, the PFXC provides the functionality for instant tightening data, so that field operatives know that the process is being completed correctly first time out, saving time, money and vastly increasing safety.
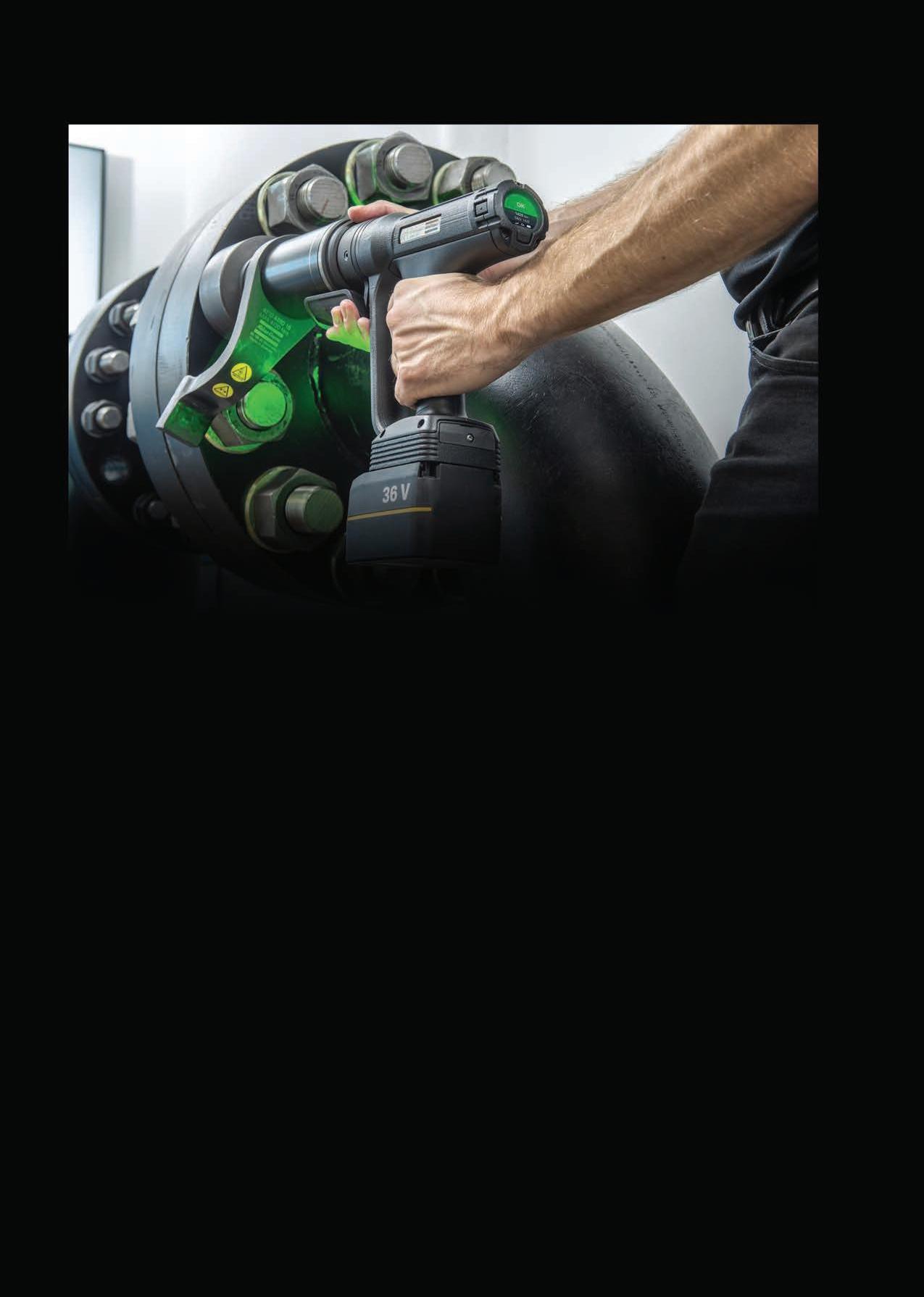
www.atlascopco.com/en-uk/itba/products/ Bolt-tightening-solutions
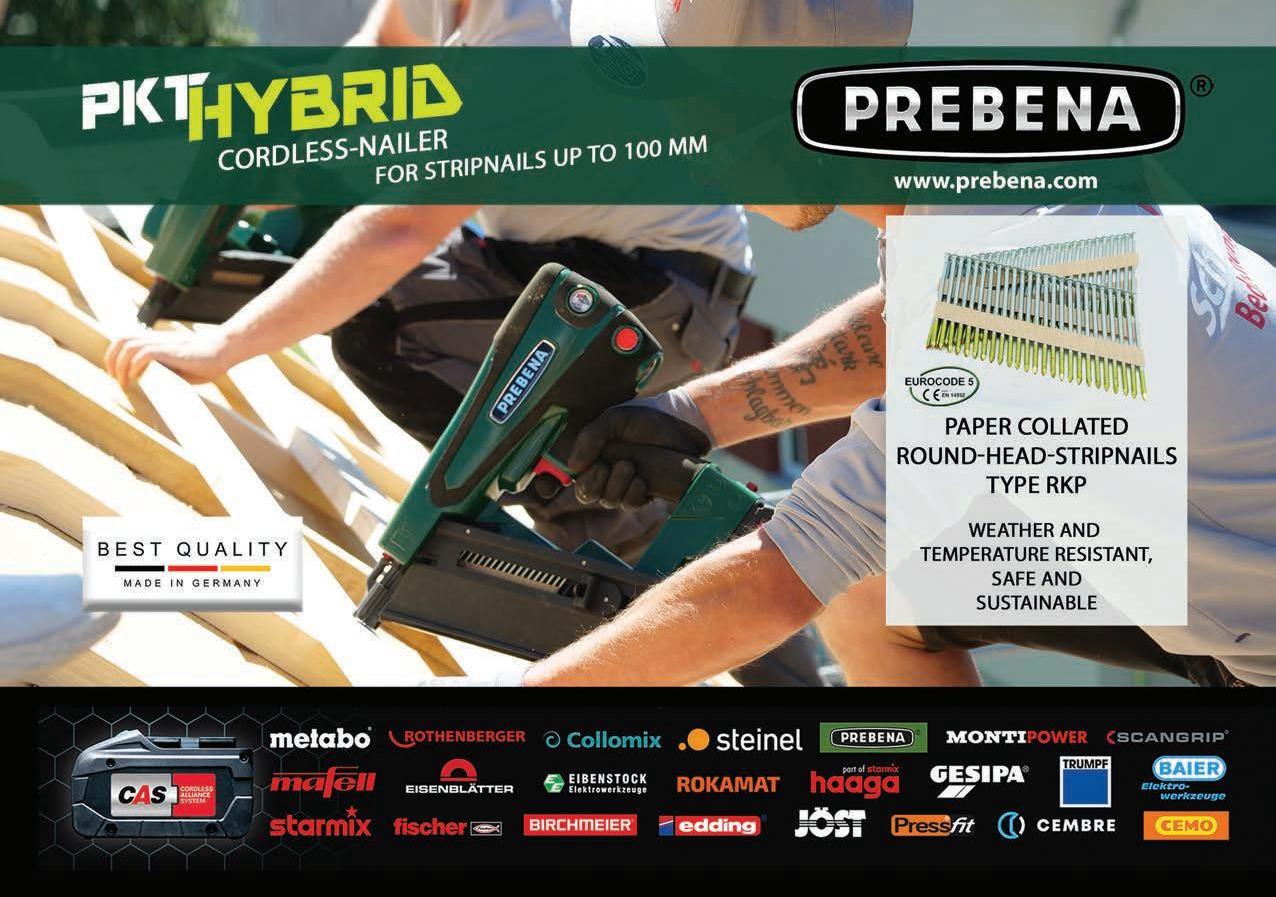
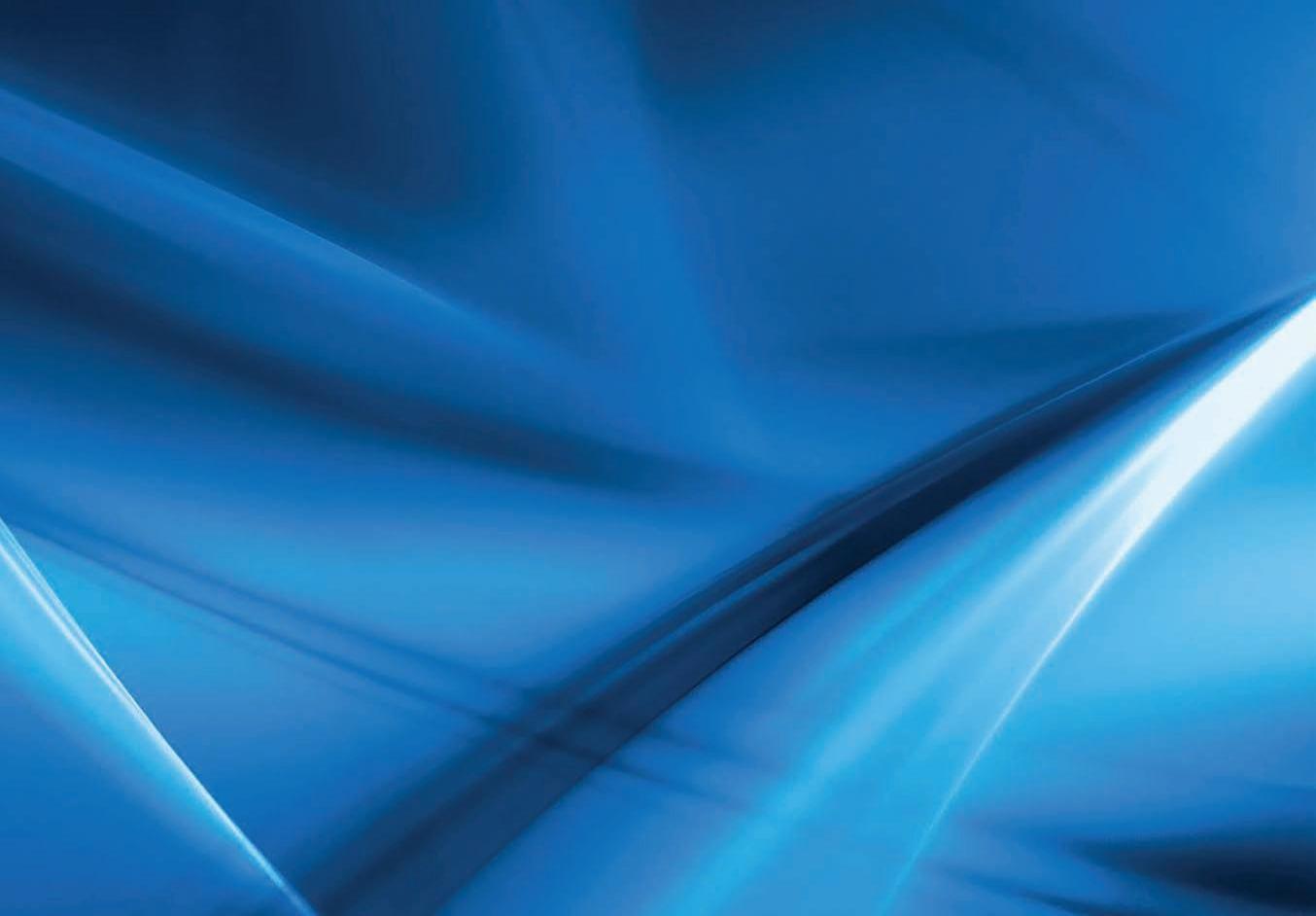

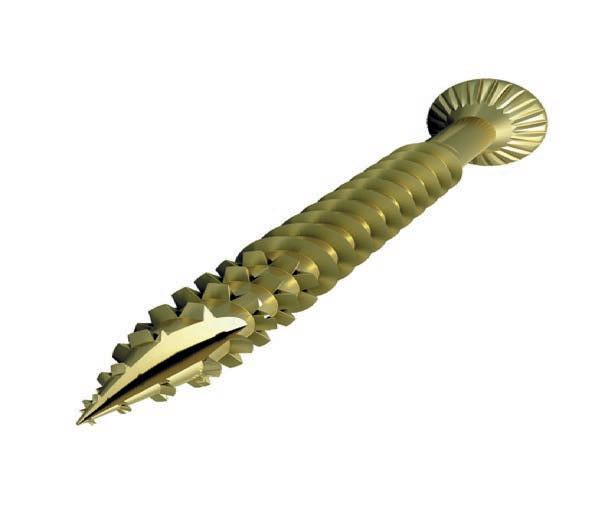
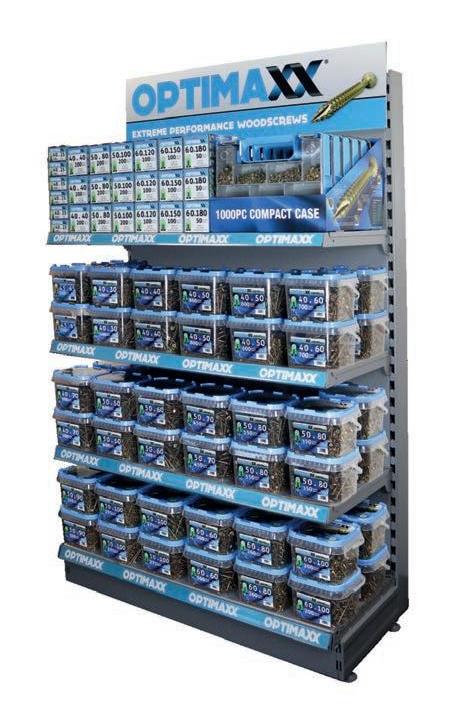

Serenco Nederlands Managing Director Remco Geirnaert
For end users, well-made tools can become much loved items, with operators often forming attachments to brands. Long-term relationships are also important at the B2B level, so says Serenco, forming the basis for sustainable growth. Serenco Nederlands Managing Director Remco Geirnaert speaks with Jonathon Harker and the continued enormous potential of the tools market…
Serenco Nederlands BV is a traditional, family-owned business that firmly believes in a ‘partner for life’ concept. “The way we operate with suppliers and customers is based on long-term relationships,” Managing Director Remco Geirnaert tells Torque Magazine. “You have to invest in partnerships and I believe you need reliable two-way relationships to achieve sustainable growth.” That ethos also brings together tools and end users, Geirnaert explains: “Tools are very emotional products and end users can build a relationship with a good product that is built to last.” Serenco started out in 1986 by seeking out innovative tools and bringing together ingenious products has become a formula for success. The company grew with brands like Metrinch, a tool system with the patented Metrinch Wall Drive profile that drives only on the flats and not on the corners. Able to operate on both metric and inch series fasteners, Metrinch’s success with Serenco initiated the development of special tools for automotive and for general industry. That automotive sector has proved a key market for Serenco, and it’s also one undergoing significant change, says Geirnaert. “We see automotive converging to a wider mobility remit thanks to the growing influence of e-bikes and electric cars. Some have compared this new generation of mobility as electric motors and batteries on wheels,” he adds, emphasising the scale of change in the sector. While Serenco says it is seeing the automotive market slowly take up more cordless tools, it sees even more potential advantages in using battery-power tools in the general industry sectors, thanks to added ease of operation and portability. “Serenco has a great reputation for tools for servicing,” says the Serenco boss, drawing our attention to the cordless torque multiplier (PH-1500-24V). It’s lightweight and silent in use compared to an air impact wrench. It boasts four torque settings for tightening (450 Nm, 650Nm, 800 Nm and 1,500 Nm) and this easy to operate power tool has no load speed. It’s very competitively priced too, says Serenco, at approx. €1,299. It’s just one example of the innovative tools which are available under the Serenco umbrella.
Supply challenges
2021 has been a strong year for the firm, but the increased costs the industry has been experiencing have been difficult. Geirnaert notes the high level of activity in the US market as having an effect on the global supply chain: “Some companies have seen their orders from the US double. Now the USA has recently
passed the $1 trillion infrastructure bill, so that will have a big effect on the order books too.” The industry is contending with shortages, including semiconductors, which Geirnaert confirms are affecting the tool business: “Yes. Like every industry, this is already hurting. In many cases, it’s not a case of being unable to get materials, it’s more the increased costs. If you add the different layers of costs together then it’s quite a significant price increase for customers.”
Factories are extending lead times, he adds: “Honestly I think that it is getting worse, not better. I don’t see any signs of improvements, because all the problems are continuing to get worse. Ordering so far in advance is a challenge and adds complexity to the market. So, what do we do? Order two years in advance? Bike shops are working on 2023 orders at the moment. At some point it will slow down. No industry keeps growing indefinitely, so there will be a readjustment. But which industry will be first and where? “So, on the one hand, business has picked up a lot, but it’s a challenging environment.”
// Some companies have seen their orders from the US double. Now the USA has recently passed the $1 trillion infrastructure bill, so that will have a big effect on the order books too.//

“People underestimate the tool market”
Current market challenges aside, Serenco is highly optimistic and enthusiastic about the potential for growth. Currently the firm has customers in 48 countries: “Growth will largely come in geographical terms. We are very well established in many territories like the UK, and we are building in Southern Europe and Eastern Europe.” The potential is enormous, he adds: “People underestimate the tool market. It’s a huge sector. Its construction, general industry, automotive, DIY, the electrification of mobility… tools are everywhere.” Tools also tap into current sustainability trends, he adds: “Tools enable people to repair instead of replace – cars, dishwashers… selling tools for people to fix the products that they already own, to enable them to enjoy repair and mechanical jobs. That’s my take on it!” To find out more about the Serenco ranges and ambitions for the market, contact the firm at
www.serenco.nl
group
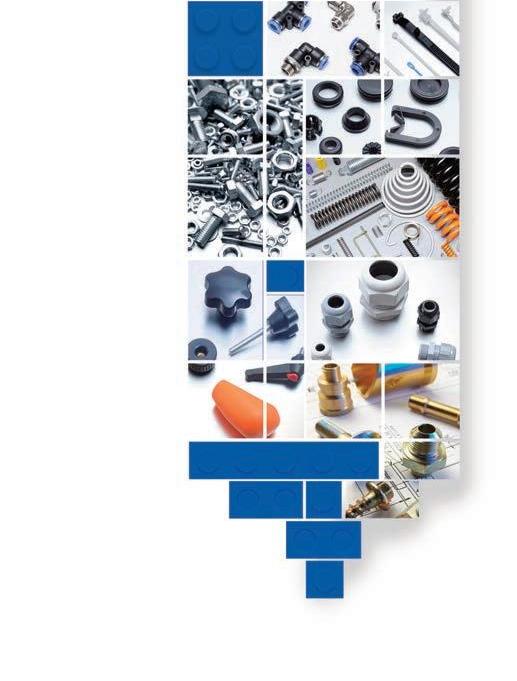
In association with BOLTED Magazine, about bolting technologies. Read and subscribe at www.bolted.com

Accidents involving trucks and vulnerable road users often end tragically, but is this a fact that must be accepted? Not if you ask EDEKA Südbayern, a German food retailer that has made itself known as a pioneer in traffic safety.
Few traffic safety topics are more vigorously discussed in Germany than the need for modern safety systems in trucks. According to the German Federal Statistical Office, 3,100 accidents involving trucks and cyclists occurred in 2017. 76 of these cases led to fatalities – which means more than one death per week. About a third of the accidents leading to personal injury were caused by trucks turning right, meaning the truck driver could not see the cyclist. In recent years, several children have fallen victim to these accidents. Demands to ban trucks completely from cities are being raised, and pressure is growing on governments to take action. An EUwide regulation on extended truck safety systems is already in the works but is not expected to become law before 2024.
TAKING THE INITIATIVE WITH TRUCK SAFETY
One company that isn’t waiting for new legislation is EDEKA Südbayern. Four years ago, the company developed a turning assistant with an integrated camera that eliminates the “blind spot” for the truck driver, who now can see cyclists and pedestrians more easily. “After several fatal road accidents involving trucks in the region, I conducted research and found out that there were no corresponding safety solutions on the market,” explains Anton Klott, the company’s Technical Director. “Our trucks drive through all big cities in this region and turning is always a dangerous manoeuvre. I decided to develop the solution myself, and two months later, we had the first turning assistant on the road.” Today the system is distributed externally by a partner in the truck market. So far – as part of a project that doesn’t generate any profit for EDEKA Südbayern – it has been installed in more than 2,000 vehicles belonging to other companies. “We are a food retailer that loves safety,” says Klott. “These accidents have dramatic consequences, also for the truck drivers. Statistics show that 80% of all drivers involved in a fatal accident are permanently disabled and unable to continue working. Police and other first responders also need psychological support to cope with these incidents.”
PROVIDING THE SAFEST TRUCK FLEET IN EUROPE
EDEKA is one of the largest food retailers in Germany. EDEKA Südbayern is one of its seven regional companies with a fleet of about 300 trucks and 475 truck drivers covering the entire southern part of Germany, driving in shifts, 24 hours a day. Klott is a trained car mechanic, carriage builder and farrier and has been with the company for 40 years, since 2000, as Technical Director. He shares a great vision with the company’s management: to provide the safest truck fleet in Europe. And their turning assistant is only one part of that. “Safety is more important than money,” he says, using the fire extinguisher in the truck’s cockpit as an example. It is a safety feature that is not required by law but is standard equipment in all EDEKA Südbayern trucks. “Our drivers have been able to extinguish fires in accidents on the highway and to save lives quite a few times now. Several colleagues have even been awarded the Bavarian Rescue Medal for their efforts.” The vehicles also have a reversing assistant that can initiate an automatic brake. Ultrasonic sensors at the rear make it impossible to drive over people or objects. Even before the technology was approved, EDEKA Südbayern installed side flashing lights. When the driver changes direction, the entire truck side blinks and warns cyclists who are travelling parallel to the truck.
SECURING WHEELS WITH NORD-LOCK WHEEL NUTS
Furthermore, the wheels of the trucks are secured by NordLock extended wheel nuts. “We used to have big problems with loosening wheel bolts,” says Klott. “Sometimes they were not properly derusted, sometimes the driver forgot to retighten them. Alternative solutions were always complicated. For example, the driver had to check regularly that certain indicators on the wheel nuts pointed in the right direction. That’s all history now. The wheel nut solution from Nord-Lock is a perfect system that increases safety.” “Accidents due to loosening wheel nuts can be tragic and also be an incredible blow to the transport company’s public image,” says Stephan Gruber, a Nord-Lock Group sales engineer. “That’s why more and more companies use Nord-Lock to eliminate these kinds of accidents.” EDEKA Südbayern proves that great visions don’t have to be expensive. “All our security attributes only account for about 1% of the total truck acquisition cost,” says Klott. The company has close contacts and a security partnership with the German Ministry of Transport. Truck safety is high on the public agenda, and Klott is proud that his company has been able to inspire others to increase safety. He says: “Today, all long trucks in Germany must have a turning assistant and side flashing lights by law. Of course, that’s a great feeling.” Watch Nord-Lock Group’s three-part video series with Edeka: How to build the safest truck fleet in Europe –How to build the safest truck fleet in Europe –Part 01 –on YouTube.
Nord-Lock Group produces Bolted, a biannual magazine covering secure bolting, industry insights and engineering challenges. Head to Bolted.com to read the latest issue.