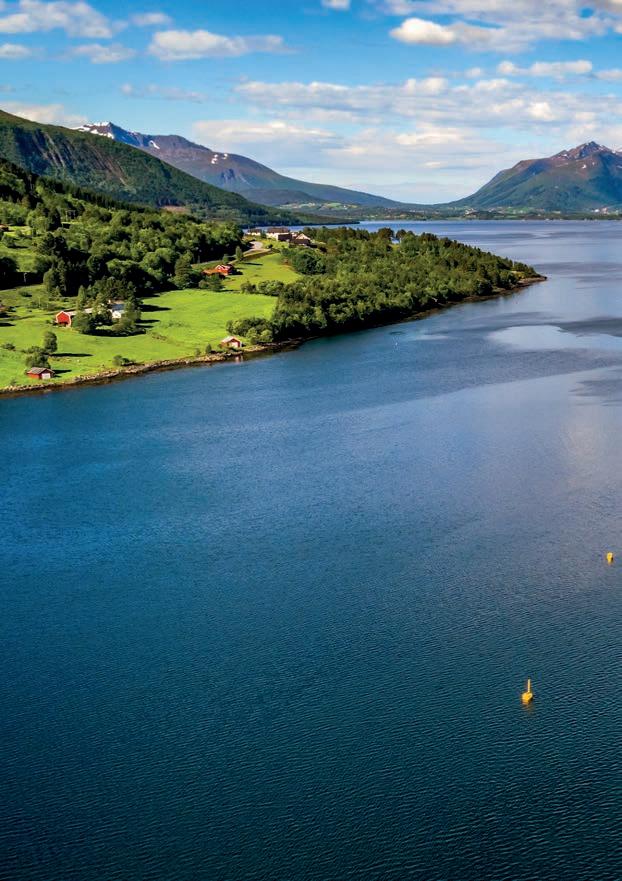
1 minute read
CORROSION RESISTANT CLAMPING
How
Under ordinary conditions, the connections between components are among the most vulnerable elements of any system. But in extreme environments, these vulnerabilities can be dramatically amplified. In the following case study, the application of superior clamping technology makes all the difference between operational continuity and the potential for expensive and timeconsuming disruption.
The challenge
The clean, icy waters of the Norwegian North Sea offer an optimal environment for offshore fish farming. But its attractive conditions also impose considerable operational challenges. Saltwater can compromise the integrity of structures, cables and connections by creating opportunities for pitting, crevice corrosion, and stress corrosion. Worse, the stormy North Sea makes maintenance difficult and expensive. Rough seas and powerful currents create fluctuations along cable lines that can undermine connections, sabotaging entire systems.
For an offshore fish farm 40km from Tromsø, Norway, successful operation means maintaining electricity and fibre optic systems without interruption; its undersea cables must withstand Arctic conditions at a minimal expense of time and labour.
The solution
Uninterrupted electrical and fibre optic service depends on reliable undersea cabling; these are most vulnerable where they bend. To protect the cables, installers deploy bend restrictor systems to prevent cable kinking.
For more than 25 years, NORMA has provided its client – a Norwegian maintenance and operations contractor to the oil and fishing industries – with suitable connectors for harsh undersea environments. Together, the client and NORMA’s DS Nordic sales team developed a bend restrictor system, based on ‘failproof’ clamps, that could withstand Arctic weather conditions without regular maintenance.
The heart of the bend restrictor solution are hose clamps capable of securing the seal and preventing cable kinks. NORMA designed the bend restrictors around its ABA Original SMO hose clamps made of SMO 254 austenitic stainless steel. Manufactured by the industryleading Swedish brand ABA for challenging environments, the ABA Original SMO is a premium hose clamp. Designed to perform where ordinary stainless steel and acidproof materials are insufficient, the clamp’s SMO 254 steel has proven its value in highpressure applications exposed to corrosive materials such as sea salt and chlorine, proving popular in many seawater, chemical, shipbuilding, and foodprocessing applications. As part of the bend restrictor solution, the ABA Original SMO wormdrive hose clamp was a novel innovation for reliable connections under extreme conditions.

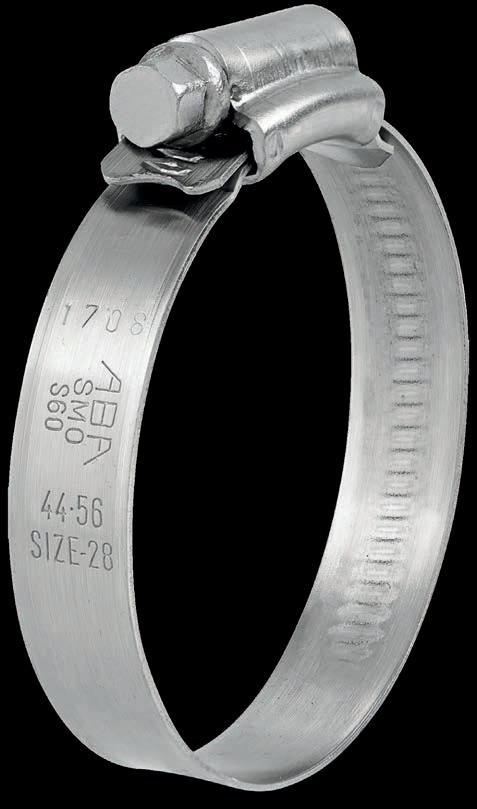
The result www.normagroup.com
40km from land, the Norwegian fish farm could ill afford sudden interruptions. Worse, making repairs deep under water would be exceptionally complicated and expensive. By using ABA Original SMO clamps that resist corrosion in uncompromising conditions, NORMA’s client ensured uninterrupted electrical and fibre optic service for the next 20 years.
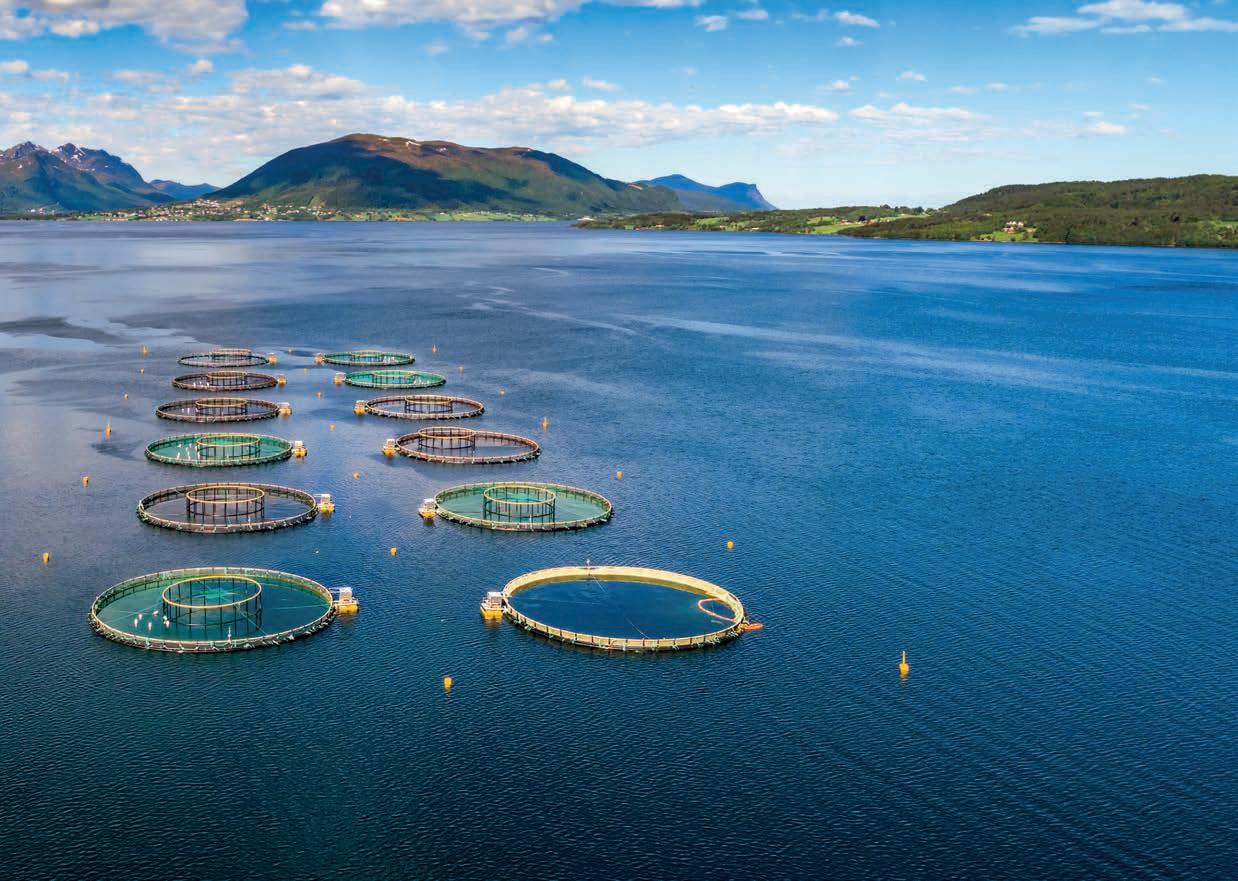
”BY USING ABA ORIGINAL SMO CLAMPS THAT RESIST CORROSION IN UNCOMPROMISING CONDITIONS, NORMA’S CLIENT ENSURED UNINTERRUPTED ELECTRICAL AND FIBRE OPTIC SERVICE FOR THE NEXT 20 YEARS.“
The