
10 minute read
Blechexpo 2019
Blechexpo 2019: Sheet Metal and Joining Technology Highlights
The 14 th Blechexpo, in combination with the 7 th Schweisstec, will be covering all aspects of sheet metal, pipe and profile processing between 5 - 8 November this year. The two complementarity industry events provide expert visitors with comprehensive product and service offerings dealing with all facets of thermal and mechanical processing, as well as welding, joining and fastening technology.
Advertisement
The Blechexpo-Schweisstec trade fair duo takes place once every two years, taking turns with the Euroblech fair in Hanover. Months before the event opens its doors it was already clear that this year will see more exhibitors, require more exhibition floor space and be more international than two years ago. Over the summer, an increase amounting to more than 150 primary exhibitors and a 20% rise in floor space compared to 2017 was confirmed.
A total of roughly 1,500 exhibitors will set the tone in nine exhibition halls at Blechexpo-Schweisstec in Stuttgart. Bookings and reservations from foreign countries have even doubled as compared to 2017. More than a year ago, it was already clear that the 2017 figures for technology companies from Italy, China, Turkey and Spain will be exceeded.
The number of exhibitors from some countries has even been doubled”, said project manager Georg Knauer. The organizers attribute the reason for this surge to the strictly practical-oriented concept of the trade fair duo: Blechexpo-Schweisstec claims to cover all
relevant issues and trends relevant to the digitalised, automated world of sheet metal and metal processing.
Sheet metal as a structural material
As a structural material – along with pipe and profile materials – sheet metal has evolved into a common alternative to conventional cast iron, steel and plastic constructions. Lightweight design and modular component systems characterise the image of modern, material, weight and cost-saving vehicle, machinery and equipment manufacturing – all the more reason to attend the Blechexpo and Schweisstec.

Precision cutting, stamping and forming of high-strength and ultra high-strength sheet metal are just as much on the forefront at Blechexpo as innovative machine building solutions, tooling with a long service life and changing equipment for rapid tool changeovers. Pre-processing and final processing, module assembly and surface finishing of optically sensitive components, as well as lightweight design and construction solutions are also at the centre of attention. The fair also covers associated issues from handling and quality assurance to digitalisation and automation solutions.
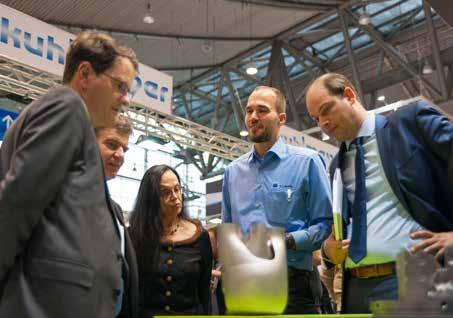
Knowledge Transfer: Stahlnews Expert Meet and Blechexpo Forum
On the evening of the first day, on 5 November 2019, the 4 th Stahlnews Expert Meet will provide a first opportunity for the exchange of ideas and knowledge transfer, with five presentations scheduled. Then, over the following days, some 30 presentations by representatives of renowned companies will be held at the Blechexpo Forum. Both Stahlnews Expert Meet and Blechexpo Forum go by the motto “The Steel Industry in Times of Glo balisation and Industry 4.0”. (see separate box).
All participating companies will profit from the trade fair’s international setting in 2019, because it is only possible to gain truly comprehensive insights into the respective sales markets and their supply chains at a worldclass technical event. “We feel that our concept targeted at strict process orientation is being confirmed by the international influx of leading companies. Demonstrating the practicality and applicability of the exhibited technologies for routine industrial use at a technical trade fair is obviously being very well received throughout Europe, as well as in the USA and in China,” the organisers say.
A new floor plan and exhibitor distribution concepts provide even better orientation. They guide and bundle the flow of visitors in a thematic fashion. Experts are guided to the offerings in which they’re explicitly interested in a targeted manner with minimal legwork.
New space for processors in hall 10
Leading sheet-metal processing companies will unveil their innova tions in halls 1and 3 of the Stuttgart Exhibition Centre. Halls 4 and 5 will have an emphasis on stamping technology. The latest technologies on pressing and forming will be presented in hall 8. Visitors with an interest in cutting and welding or joining will be able to explore offerings in halls 5 and 7, respectively, and may move on to other segments with minimal distances to walk.
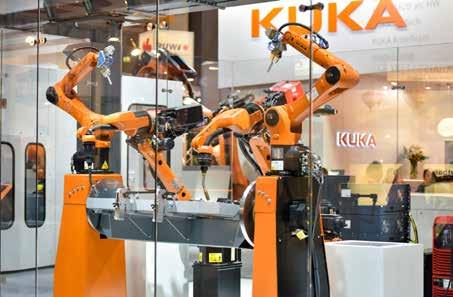
The new, comparatively larger hall 10 now gives adequate space for expanding offerings in the field of steel processing services. Numerous new exhibitors are taking advantage of this opportunity to introduce themselves to global expert visitors, and established, longstanding participants will be able to increase their booth floor space as well.
stahlnews-ExpertMeet – on the evening of the first fair day, November 5
These experts have confirmed that they will be on hand and will hold presentations each lasting roughly 15 minutes:
• Prof. Dr. Matthias Liewald, Director of the Institute for Forming Technology at the University in Stuttgart. Topic: “Brief Overview of Current Research Focal Points on the Forming of Steel and new Approaches to Industry 4.0 Processes”
• Norbert Thumfart, CEO, Weyland and director of the Board at ARGE Stahl- und Metalldistribution. Topic: The Future of the Steel Industry and its Suppliers in Eastern Europe
• Tim Milde, Managing Director and COO, XOM Materials GmbH. Topic: eCommerce and Platforms as an Opportunity for the Metals Market
• Dr. Markus Reifferscheid, Vice President R&D at the SMS Group. Topic: The Learning [Steel] Plant
• Dr. Ir. Menno van der Winden, General Manager Advanced Analytics at TATA Steel Europe. Topic: WEF “Lighthouse 2019”: Distinction for Dramatic Improvement in Production through Advanced Analytics
Blechexpo Forum
In addition, further representatives of renowned companies will hold brief presentations at the Blechexpo Forum on the following days of the fair. Some thirty talks have been scheduled by companies including Tata, Kasto, ArcelorMittal Commercial, and Welser Profile.
Companies at Blechxpo 2019
ARKU Maschinenbau GmbH, Germany
ARKU’s new deburring machine EdgeBreaker 3000 features two sequential processing zones which deburr and round sheet metal parts up to 80 mm thick on both sides in a single pass. The patented brush change click system enables quick and easy replacement of the abrasives, thus rapid and flexible adaptation to the deburring task. The automatic calibration system measures the abrasive consumption and compensates for this.
Exhibition hall 1– Booth 1001
Dee Tee Industries Ltd., India
Dee Tee’s Smart Slit is an industry-oriented slitter line tooling management software. It helps in examining tool life and performance. With Smart Slit one can define the knife’s slitting capability and hence can prevent knife chipping and blunting.
Exhibition hall 10 – Booth 10108
Prima Power GmbH, Germany
Making its world premiere at Blechexpo will be Prima Power’s new bending solution, the eP Genius 1030, consisting in the integration of a servo-electric press brake eP-1030 with an automatic tool change storage. The highly dynamic, accurate, and reliable servo-electric technology, granting constant performance over time thanks to the absence of hydraulic oil, combines with the benefits of a fast and dynamic automatic tool change system. The result is a more versatile, faster and more reliable bending system, which eliminates the manual set-up of the machine.
Exhibition hall 3 – Booth 3504
Lantek GmbH, Germany
Lantek, which claims to be a pioneer in the digital transformation of companies in the metal sector, will be showcasing the “Lantek MetalShop“ – a web interface that enables the quotation, sale, and production planning of metal parts by sending a .DXF file. Subsequently, using the correct import of a geometry, the algorithm can precisely estimate fundamental parameters such as cutting times, cost of material, stock levels, and margins to apply. “
WILA B.V., Netherlands
WILA will show its Smart Tooling Concept: a smartphone app which offers tool management for press brake tools. The Smart Tooling App allows WILA customers to experience the advantages of digitalization and data connectivity: access to tool data anytime, anywhere; major time savings; error-free tool data entry and simplified stock management. The Smart Tooling App is part of the WILA Smart Tooling concept, which adopts a step by step approach to take tool management for press brake tools to Industry 4.0 standard.
Exhibition hall 1 – Booth 1405
Schuler Pressen GmbH, Germany
The completely redesigned MC 125 stamping press now also offers smart functions to medium-sized companies. Thanks to additional integrated sensors, the condition of the MC 125 can be fully monitored at all times. This ensures the productivity and can prevent unplanned shutdowns. Visitors to the Schuler stand at Blechexpo can experience this on their mobile devices themselves. The mechanics have also received an update: Schuler has now implemented the sliding guide via prestressed, play-free roller guides.
Exhibition hall 8 – Booth 8511
Autopulit - Maquinaria para el pulido automático S.A., Spain
Spain’s Autopulit will exhibit the CRHU-150 robotic cell, developed as an automatic system for weld dressing of sheet metal shaped parts, guaranteeing constant finish in spite of the geometric variations from the manufacturing process. A measuring system checks the real dimensions of each part, prior to the weld dressing process. When executed, the reference program adjusts to the specific geometry of each part, modifying the trajectories in real time according to the dimensional differences measured. Automatic recognition of the piece holding tool allows the different parts references to be processed randomly.
Exhibition hall 5 – Booth 5308
Roemheld GmbH, Germany
Roemheld at the Blechexpo will be introducing an element for the fully automatic clamping of dies on the press ram, which can measure real-time data on clamping forces and transmit them to the machine control.
The new series of the rapid clamping system Flexline is therefore suitable for predictive maintenance and use in Industry 4.0 applications. Also, the company provides an overview of components for the efficient, fast and safe transport and change of heavy dies. On display are various transport carts, carrying Exhibition hall 8 – Booth 8507 consoles as well as roller or ball bars for machine tables.
Exhibition hall 8 – Booth 8507
Voortman Steel Machinery B.V., Netherlands
The new Voortman V310 CNC plasma cutting and drilling machine means all known advanced technologies of our current range, plus extra additions. Equipped with a drill spindle, the V310 meets diversity and flexibility in processing where cutting, drilling and marking are carried out in one process list. Holes up to 40mm can be carbide drilled with the SK40 drill spindle.It has the fastest height control in the market combined with the reduced cut-to-cut cycle time of our Instant Cut Technology, you are able to gain a 30% processing time improvement for each product.
Exhibition hall 5 – Booth 5107
EMW/Schäfer: Portfolio and digital services extended
EMW Steel Service Centre and Schäfer Perforated Metal will be among the exhibitors at the 14 th Blechexpo in Stuttgart. At stand 10201 in hall 10, the two business divisions from the Schäfer Werke Group will be presenting a selection of their product and service portfolios.
Since the beginning of the year, the SSC’s new logistics centre at the headquarters in Neunkirchen has been in operation, with notable improvement of order processing and overall capacity. Following the launch of the “Yoursteel“ customer portal at the end of 2018, EMW now has the capability to retrieve all important information on orders and stocks at any time, as well as being able to download various documents such as test reports, delivery notes and much more. “By setting up and launching the “Yoursteel” platform, we can offer our customers an even more efficient service and are ideally equipped to meet the demands of Industry 4.0,” says Michael Mockenhaupt, managing director of the EMW Steel Service Centre.
New location in Saxony, new space at home
The company opened a new location at the beginning of this year. The plant in the Saxony town of Treuen will not only serve customers in the Saxony and Thuringia regions but also international clients in Poland, the Czech Republic, Slovakia and other central European countries.
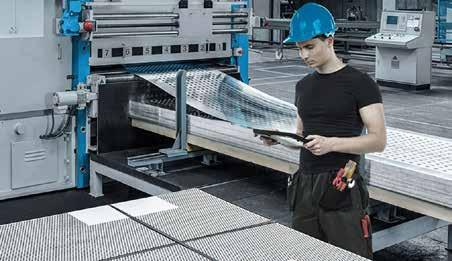
Production line at EMW Service Centre and Schäfer Perforated Metals
Meanwhile at the headquarters in Neunkirchen in the Siegerland area of North Rhine Westphalia, two new halls are closing the gap between service centre halls 3 and 6. Together with SSI Schäfer’s warehouse management software WAMAS, these approx. 12,000 m² facilities will significantly improve internal logistics processes and reduce loading times, the company states.
Increasing demand, new areas of application and steady growth in customer numbers were behind the decision to extend the capacity of the Steel Service Centre yet again. Priority was given to increasing the safety and speed of the overall intralogistics ca pacity of the new building. These goals were achieved by a new unloading and loading concept, which allows a higher throughput and at the same time minimizes turnaround and waiting times for trucks. This guarantees smooth loading in a three-shift operation. The new intralogistics are controlled by a warehouse management system, which is designed to comprehensively map and permanently im prove all requirements. The system receives the data required for control via a direct connection to the SAP system and so, by integrating control of the raw material stock, production and dispatch, an optimal material flow can be created.
Perforated sheets by Schäfer
Since the middle of this year, Schäfer Perforated Metal has been on the market with an extended portfolio of instock perforated sheets, new perforation patterns and stainless steel grades. The aim is to respond to current market demands with new products and focus even more on digital services. Since 2018, the entire range has been available in an online shop, which guides users to the very product they are looking for in just a few clicks and with numerous filter and selection options. The online shop can be found at lochblech-shop.de.
“This comprehensive digitalisation will improve both the production processes as well as our customer-oriented processes. If you’re the type who prefers direct contact, we are happy to arrange personal meetings, and if you feel more at home online, we can now offer you an extensive range of digital services,” says Alexander Tumasjan, head of sales at SchäferPerforated Metal.
Cooperations with Daimler and Schürholz
For more than 20 years, the EMW Steel Service Centre has been supplying premium car manufacturer Daimler AG with cut-to-size blanks and slit strip. During this time, EMW has seen and accompanied many changes in grades and coatings at Daimler AG. Whether Bonazink or Granocoat, electrolytically galvanised or hot-dip galvanised, all product changes were mastered together, EMW claims. Deliveries go to the sites in Bremen, Hamburg, Sindelfingen, Mettingen and Gaggenau. The slit strips are then processed into so-called structural elements (connecting plates, reinforcements and supports) at the Daimler production plants.
EMW also highlights its long-standing cooperation with automotive supplier Schürholz Group, of which it says “is more of trusting partnership than a conventional business relation.”
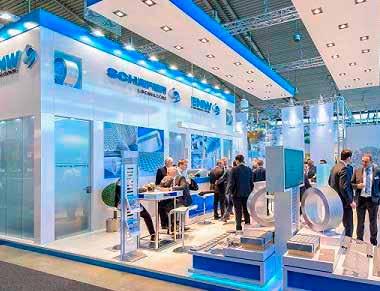
For Schürholz, the focus of this cooperation lies on the lowest thickness tolerances, specially limited strengths and edges that can be rounded. All these material demands have been worked out and defined by Schürholz and EMW in numerous talks and trials over recent years to ensure the input material is of a consistently high quality.
Background information
Since it was founded in 1952, EMW has developed into one of Germany’s largest independent steel service centres and will deliver over 900,000 tons to its customers this year alone. To warrant the right material at the right time is only possible with over 130,000 tons of stocks specially geared to the needs of the automotive industry and a logistics concept specially devised together with the customer. For the production of slit strip and cut-to-size blanks, there are five slitting and multi-blanking lines available with thickness ranges of 0.4 to 4 millimetres and coil weights of up to 32 tons.