
22 minute read
Paper thin advantage
Brandauer is using its ability to deliver motor laminations thinner than a piece of paper to help develop a new electric machine.
The company is part of the UK-ALUMOTOR consortium, led by multi-industry engineering consultancy Ricardo and partners Aspire Engineering, Global Technologies Racing, Phoenix Scientific Industries and the University of Warwick.
Brandauer will help develop the stator and rotor used in the electric motor, using its micron capable toolroom, wire electric discharge machines (WEDM) and design and engineering consultancy facilities.
Fifteen engineers will be working on the project - which is backed by the Driving Electric Revolution Challenge Fund through UK Research and Innovation - and will be involved in developing low volume parts that will be used to fine tune processes, technologies and achieve the high volume UK
Heat management specialist Zircotec is working with Dolphin N2 and Brighton University to develop a near-zero emission internal combustion engine that has the potential to transform the commercial powertrain market.
Zircotec provides the advanced thermal coatings and precision, ceramically coated components, along with its patented encapsulated heatshields that meet the very high demands of this
manufacture of a next generation electric machine design.
“Our ability to manufacture to microns is proving a very attractive commodity to some of the major OEMs and technology partners looking to establish an electrification supply chain in the UK,” explained Mark Parsons, the recently appointed Innovation Project Manager at Brandauer.
“This project is all about working towards an electric machine that can be built in high volumes and our role will be to produce laminations that deliver the magnetic field to power the motor.
“Our growing reputation for delivering precision tooling solutions that can be adapted to high volume stamping of 0.1 mm thick materials sets us apart from other European press workers.” 8 brandauer.co.uk
Carbon-zero truck engine recuperated split-cycle, next The Zircotec coatings generation engine. massively reduce the
Graeme Barette, sales and temperatures in the areas of the marketing director said: “We’re engine where heat is not wanted, really proud to be involved with this reducing heat transfer, keeping ground-breaking project and to be the heat in the hot part of the part of the carbon-zero engine engine. Through the retention of revolution. This is a massive project heat in the combustion cycle, for us to be involved in and our significantly less energy is lost involvement demonstrates the trust through the cooling system, we have earnt over many years thus a high-performance working with some of the biggest efficiency is produced. automotive performance brands.” 8 zircotec.com
Gareth Jones
has returned to In-Comm Training after leading the integration of HK Technologies into the Engineering Technology Group. He will be responsible for operations, sales and marketing, growth strategies and product development alongside the continued expansion of the Group.
Katherine Bennett
currently Senior Vice President, Airbus in the UK will take over as CEO of the High Value Manufacturing Catapult when the current CEO, Dick Elsy, retires this year. A formal recruitment process was led by HVM Catapult Chair, Allan Cook CBE.
Sir Donald Spiers
has announced he is to step down as chairman of the Farnborough Aerospace Consortium (FAC) after almost 20 years. The government and industry veteran who was previously head of aerospace procurement for the UK’s armed forces started his career as a
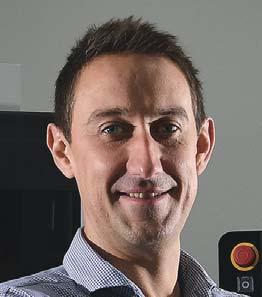

graduate apprentice.
Andy Hodgson
Strategic Lead: Digitalisation at Siemens, was welcomed as MTA President at the Association’s first ever virtual AGM, taking over from Marcus Burton MBE. Mr Hodgson has played an active role in the MTA for many years as a Board Member


Trade Leads from the EIA
The following FREE OF CHARGE trade leads for the UK engineering industry are currently appearing on the Trade Board pages of the Engineering Industries Association at www.eia.co.uk
Welding distributor
Russian manufacturer of aluminum welding wires enriched with scandium for automatic welding is looking for to conclude a distribution services agreement.
Reference: JV1442
Closing Date: 06/02/2021
Pipe fitting distributors
A Russian company is developing a ball valve with a metal-to-metal seal, designed to operate under conditions of high thermal loads at nuclear power plants. The company is looking for reliable partners to conclude a distribution services agreement.
Reference: JV1443
Closing Date: 13/02/2021
Anodised aluminium sheets
A Polish company working in animal care is looking for anodised aluminium sheets to make ID tags for pets. Sheets should be 1000mm by 500mm by 1mm in red, navy blue and purple.
Reference: JJV1445
Closing Date: 13/02/2021
Heat power valves
A Russian maker of enhanced performance valves for heat power systems is looking for partners for a distribution services agreement.
Reference: JV1444
Closing Date: 13/02/2021
For more information please email head.office@eia.co.uk quoting reference number. Please remember to use due diligence in responding to Trade Leads. Engineering Capacity provides you with the above information in good faith, but is unable to accept any responsibility or legal liability arising from any use of these leads.
Nuclear business booming
Birmingham-based Burcas has invested in a new large-capacity vertical machining centre to produce tooling, prototypes and high precision components for the nuclear sector.
The Doosan Mynx 9500/50 machine was supplied by Mills CNC and has also been used to machine high-precision tungsten carbide and HSS knives and blades for customers in the paper and packaging sector.
The nuclear sector has always been important to Burcas and, over the last 10 months has become even more so owing to a decline in the company’s other major business areas, such as aerospace, oil and gas, due to the effects of the pandemic.
In fact, says owner and MD Mike Burrows, it was the increase in demand for Burcas’ machining services from customers in the nuclear sector that was the catalyst behind the new Doosan machine tool investment.
“To capitalise on the growing business opportunities in the nuclear sector we, at the beginning of the year, audited our existing machining capacity and capabilities.
“The results of the audit combined with our knowledge of the sector highlighted a need for us to strengthen our milling capabilities as a matter of some urgency.
“As a consequence we specced out the type of machine we knew we required in terms of its size and capacity, spindle configuration and speed, torque rating etc., and began researching the market for the ideal machine.
“Although the new machine tool purchase was driven, almost entirely, by an increase in demand from customers in the nuclear sector we never lost sight that it would also become a major machining asset for our future aerospace and oil and gas business - when both returned to something resembling normality.”
The key criteria when selecting the machine were the ability to machine a wider range of larger and longer components, and the need for a rigid design and construction to cope with materials such as stainless steels, Hastelloy, titanium and exotics as well machining routines featuring heavy duty cutting and interrupted cuts.
The machine selected, the Mynx 9500/50, is a large-capacity machine with a working envelope of 2500mm (X) by 950mm (Y) and 850mm (Z) and a maximum table load of 3,500kg.
It is equipped with a powerful, two-speed gear box driven (22kW/10,000rpm), high-torque (452 Nm) spindle, with a BT50 face and taper configuration that makes it ideal for heavy-duty cutting operations, long machining runs and the efficient and accurate machining of ‘difficult-to-machine’ materials. The machine has a 40-position automatic tool changer and a four row screw chip disposal system that delivers improved efficiency and process reliability.
Mike Burrows concludes: “We constantly monitor and evaluate all aspects of our business. If, and when, we identify an area that needs attention or improvement we act decisively.
“The new Mynx 9500/50 investment is another example of Burcas’ commitment to continuous improvement and of us striving to be the best we can be.” 8 burcas.co.uk
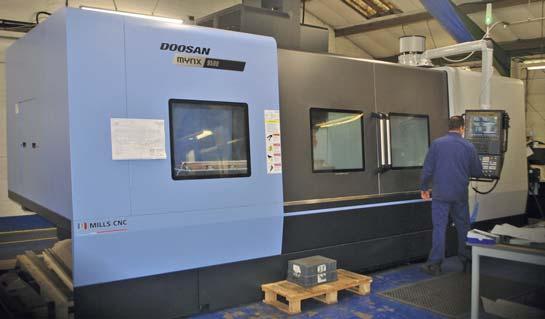
Fabrication is nearing completion and assembly underway on a £1 million 250kW gravity-based energy storage demonstrator at the port of Leith.
Fife fabricator AJS Production was contracted to deliver the base frame and the weight baskets for the innovative Gravitricity prototype. The system’s lattice tower has been fabricated by ESL engineers in Hull, while custom-built winches and control modules have been made by international winch specialists Huisman at its factory in the Czech Republic and are currently being shipped to Leith.
The full 15-metre high rig will now be assembled at the gridconnected site for testing to begin in February 2021.
Commenting on the project, Steven Kirk, Senior Mechanical Engineer said: “AJS is fabricating two vital components for our demonstrator – the grillage (or base frame) will sit on the concrete plinth and will support the lattice tower, and the two weight baskets will be filled on site with high density aggregate, to create two 25-tonne weights.
“These weights will be suspended by steel cables within the tower, and in one test we’ll drop the weights together to
KEY FACTS
Rig height – 15 metres Weights – 2 x 25 tonnes Weigh composition – steel vessels filled with high density aggregate Cables – steel Stroke – 7 metres Time to drop (full power – 250kW) –14 seconds - 0.6 m/s (1.3 mph) Half power (125kW) – 28 seconds
Tower of power
generate full power and verify our speed of response. We calculate we can go from zero to full power in less than a second – which can be extremely valuable in the

DNow Accredited to frequency response and back-up power markets
“We’ll then run tests with the two single weights, dropping one after the other to verify smooth energy output over a longer period, alongside a programme of other tests to demonstrate and refine the full capabilities of the system.
“Our two-month test programme will begin in February and will confirm our modelling –and give us valuable data for our first full-scale 4MW project which will commence later in 2021,” Kirk concludes. 8 ajs-ltd.co.uk
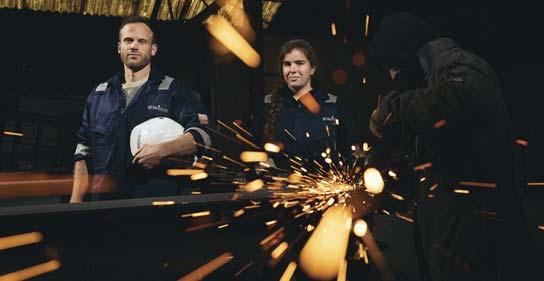
FM10101
Manufacturers of High Quality Mill-Turned Parts
A Scottish supply chain collaboration is aiming to deliver a production-ready and safety certified hydrogen powered train by November 2021.
Scottish Enterprise, Transport Scotland and the Hydrogen Accelerator, based at the University of St Andrews, have appointed Arcola Energy and a consortium of industry-leaders in hydrogen fuel cell integration, rail engineering and functional safety to deliver Scotland’s first hydrogen powered train. A key objective of the project is to create opportunities for the Scottish rail supply chain through skills development and industrialisation of the technology.
The project is supported by rail engineering and safety experts Arup and Abbott Risk Consulting to form an integrated delivery team, with AEGIS providing regulatory third-party verification.
“Hydrogen traction power offers a safe, reliable and zero-carbon alternative for Scotland’s rail network. The hydrogen train project is an excellent opportunity for industry leaders in hydrogen, rail engineering and safety to collaborate with Scottish technology providers to develop a deployment ready solution,” said Dr Ben Todd, CEO of Arcola Energy. “We are delighted to be working with Scottish Enterprise, Transport Scotland and the Hydrogen Accelerator, to support Scotland’s strategy to make passenger railways emission free by 2035.”
Arcola Energy will develop the technology platform for the train’s new powertrain from its planned
Hydrogen train supply chain
new Scottish base. Arcola’s existing A-Drive platform will be extended to meet rail safety and compliance requirements, thereby enabling the consortium to significantly reduce development time and cost to deliver a complete hydrogen powered solution in just 10 months.
Project partner Arup will use the learnings from the project to develop a roadmap to roll out hydrogen trains to support the decarbonisation of Scotland’s network.
“With Scotland’s focus on achieving net zero emissions by 2035 and rail playing a leading role in this, hydrogen offers a safe, reliable and zero carbon alternative to other forms of rail propulsion,” said Clare Lavelle, Scotland Energy Business Lead, Arup. “This project is not only a crucial step in helping us understand the practical challenges of using hydrogen traction power on our railways, but an example of the type of investment Scotland needs to take advantage of the opportunity to build a secure, flexible, cost effective and zero carbon energy network.”
Based at the Bo’ness and Kinneil Railway, the consortium will convert a Class 314 car passenger train, made available by ScotRail, into a deployment-ready and certified platform for hydrogen powered train development.
Following demonstrations, the train will serve as a development platform for Scottish technology providers and academics as Scottish Enterprise and the Hydrogen Accelerator explore opportunities for Scotland’s hydrogen-enabled low carbon strategy.
The Consortium will demonstrate the hydrogen powered train during COP26, in Glasgow from 1 - 12 November. 8 arcolaenergy.com

Springs made in Cornwall are helping buildings across the world withstand the force of earthquakes.
European Springs & Pressings in Penryn, Cornwall, manufactures springs for South Brent based Vexcolt, one of the world’s leading producers of expansion joints and movement control joints.
Covering every continent across the globe, including buildings as iconic as Jeddah airport in Saudi Arabia to The Shard, to Jewel Changi airport in Singapore to the O2 arena, Vexcolt design and manufacture joint systems that enable buildings to absorb up to one metre of movement, when an earthquake strikes.
Arun Kingwell, Technical Specialist at Vexcolt says: “The UK is often misrepresented for its manufacturing capabilities, let alone Devon and Cornwall. However, here we are with two SMEs, working together, making a product that significantly contributes to the safety of infrastructures around the world.
We have technical sales offices in the UK, Europe, India, China and South-East Asia but we manufacture in the South West. It’s great to work with European Springs & Pressings as it enables us to not only deliver a high-end quality manufacture message but also a Made in Britain status that we’re very proud of.”
Michael Gibbs, Managing Director of European Springs & Pressings concludes: “It always surprises people how much a spring is depended on for multiple
When the earth moves…
functionalities across so many diverse industries.
Vexcolt’s global influence in construction management, delivering solutions to complex building movement problems across all building types, is an engineering feat to behold. It’s an honour working with them and it puts a huge smile on the team’s faces, knowing their spring production is at the centre of safety for so many buildings across the world.” 8 europeansprings.com


From design, sampling and technical support to manufacture, Simpson Springs & Pressings Ltd provide the complete service.

Tel: 0118 978 6573 Email: sales@simpsonsprings.co.uk
Corbetts, the UK’s oldest hot dip galvanizer, bounced back from Covid-19 disruption to process nearly £1m or orders in October – a record amount for the firm.
It used downtime in summer to improve productivity and modernise processes and this has now paid off.
Celebrating 160 years in business in 2020, the Telfordbased company processed 34% more volume than the same time last year for customers involved in street furniture, transport and construction.
With volumes continuing to rise and new contracts being secured, the recently strengthened management team are now planning to reopen the smaller Plant to increase capacity.
“This is a phenomenal achievement by our workforce and highlights growing optimism in our sector,” explained Sophie Williams, Finance Director and General Manager at Corbetts the Galvanizers.
“It proves that the manufacturing best practice improvements we have undertaken over the last six months are working, including throughput, how we hang work, process speed and upgrading the pre-treatment process. There’s also been considerable investment in upskilling the workforce and bringing in new team leaders.”
She went on add: “All this has led to a record month in terms of volume and sales, but, most importantly, we have done all of this whilst maintaining outstanding quality and
Shining performance from galvanisers
24 to 48 hour turnaround time for existing business and 5-10 days for new clients.”
Corbetts the Galvanizers has been supplying world class hot dip galvanizing to thousands of customers across the UK and Europe for 160 years.
This process is the most effective and environmentally friendly way to protect steel from the elements and provides a longterm solution to corrosion (rust) and maintenance free protection in excess of 100 years.
From its purpose-built facility in Telford, it operates a number of galvanizing baths that give it the opportunity to process in excess of 50,000 tonnes every year and the ability to double dip material up to a length of 14 metres.
Product is then loaded on to the company’s fleet of 13 vehicles that make up to 5000 different journeys every year, with the latest investment meaning that the oldest lorry is less than five-years-old.
Sophie, who recently oversaw the appointment of new managers for Sales and Marketing, Procurement and Operations, concluded: “2020 hasn’t been the year we were expecting to celebrate our big birthday, but what it has done is given us time to look at how move forward for the next 160 years.
“This means we are now a more efficient operation and we have been looking at new ways in which we can grow the business. One big plan is currently in the final stages of negotiations and, if it comes off, could change the way the galvanizing sector operates forever.” 8 wcorbett.co.uk

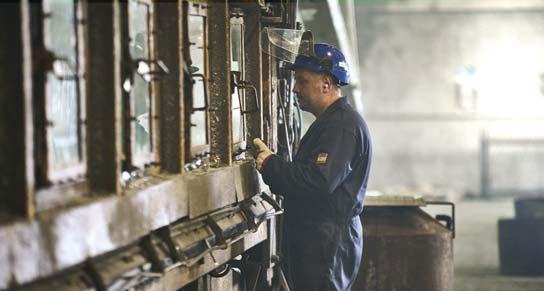
Blackhill Engineering is fabricating large steel structures for the Navy’s new Thanckes Oil
Fuel Depot Loading Facility
Refuelling Jetty.
This is Blackhills’s first contract for VolkerStevin which is responsible for the £43m Defence
Infrastructure Organisation project to modernise refuelling facilities for Royal Navy warships and Royal
Fleet Auxiliary.
Blackhill Engineering has a double overhead gantry crane lifting capability of 40 tonnes and 20 tonnes and this tandem lift capability allows safe loading of structures up to 25m long.
Blackhill fabricated 15 sacrificial casings measuring up to 18m long with a diameter up to 2.3m and weighing up to 23 tonnes each, which will be embedded into the rock strata of the River Tamar to form stanchions supporting the jetty head structure. Blackhill is also fabricating dolphin tops, rails, frames and access equipment.
Joe Wilcox, General Manager,
Blackhill Engineering, said, “Being engaged by VolkerStevin on this major project is an achievement ‘‘Being engaged by VolkerStevin on this major project is an achievement for our
highly skilled and flexible workforce

Navy oil loading contract
for our highly skilled and flexible workforce. Our BS EN 1090 Structural Steel and Aluminium capabilities project us ahead of our competition regionally, and our embrace of a Nuclear Safety Culture reflects the pride we take in our workmanship”.
The contract’s initial Scope of Works has expanded with Blackhill building 6m wide platform structures. The feasibility of assembling the completed platforms on its Exeter site and the logistics of transporting the finished units to the customer are being assessed as they would require an escorted convoy of vehicles. 8 blackhillengineering.co.uk/
engineering, composites

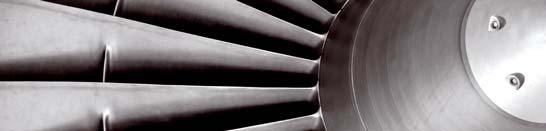
PR | Marketing | | Copywriting | Events Awards | Design | | Web & SEO
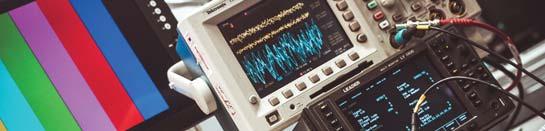
01752 894786 www.aroprandmarketing.co.uk
Laser texturing possibilities
A new laser machine tool is opening up application opportunities for Fimark, a specialist subcontractor focused on laser etching, engraving, cutting and texturing.
The AgieCharmilles LASER P 400U has strengthened the company’s existing capabilities and enabled it to develop new application opportunities in the laser 3D market.
Charles Dean, Fimark’s managing director, says: “Laser texturing is a fully-digitalised surface engineering process that has huge potential.
The technology enables precise 2D and 3D textures to be machined accurately and directly onto complex parts and its application is being used by across a diverse range of industry sectors. These include automotive, aerospace, medical devices, watch making and jewellery.
Fimark was established in 1997 and in its early days was primarily focused on providing high-quality laser engraving and marking services to customers.
By late 2019 an increase in demand for high-quality laser machining services was putting pressure on the company’s existing laser resources.
Charles Dean says: “It was clear that we needed to increase our laser machining capacity and capabilities.
The new LASER P 400U is a compact and versatile 5-axis machine that can accommodate workpieces up to 600mm x 400mm x 250mm.
The machine features a dual laser head that can incorporate both an ytterbium pulsed (nanosecond) fibre laser and an ultra-short femtosecond pulsed laser.
This allows different laser operations to be undertaken on a single machine and significantly increases the range of materials that can be processed.
The machine, with its 30μm laser beam width, is ideal for machining small components with delicate and intricate shapes, features and textures- with 3D functional textures a potentially significant growth area.
Specific textures can be created, for example, to enhance the tribological properties of surfaces to improve their load bearing capacities or to reduce friction and wear.
In addition to ‘functional’ textures, surface texturing can also be used for aesthetic effect. Typical examples of this include special editions and customised versions of luxury goods with laser texturing technology providing a cost-effective alternative to more traditional methods such as engraving and chemical etching.
Charles Dean says: “In many aesthetic and functional applications laser texturing has a number of undoubted advantages over more conventional surface etching processes. For example it is less harmful to the environment; less labour intensive; and a more reliable and repeatable process.
“This is where the future of laser machining lies and, with our latest investment, we are making sure that we are positioned at the forefront of these developments.” 8 fimark.co.uk

Lincoln-based Micrometric has identified new applications for a high-precision tube laser that is predominantly used to produce medical components.
The company, which produces fine parts and precision components for a range of customers in the UK, Europe and across the world, has now added a Coherent’s StarCut Tube system to its range of cutting equipment.
The fully automated machine is designed to laser cut, drill and mark tubular or flat metal components and is traditionally used by subcontract manufacturers to produce exclusive medical instruments with extremely high precision.
Since investing in this equipment, Micrometric has found new uses for this machine; unlike most UK subcontractors, the company has been using it to produce a flexible range of tube components in large volumes as well as finer, more precise parts for a wide range of sectors other than medical.
Neil Main, Managing Director at Micrometric, said: “We invested in the StarCut Tube machine as we knew it could deliver the required performance for a wide range of projects and had a long, low-maintenance lifetime which is necessary for cost-effective operations within our working environment.
“The machine´s versatility allows us to cut thinner tubes than our other machines and has allowed us to extend our capabilities and the range of customers we can service.”
More than medical components
Micrometric has already used the machine to cut, assemble and weld complex medical, and aerospace components for companies which produce aerospace filters, automated injection needles, endoscopy components and MRI scanning equipment.
Neil added: “Thanks to this machine, we can produce components for different types of sectors, including airflow sensors, flexible protective covers, valves used for car suspension systems, industrial and medical endoscopy equipment, printing machines and food production.
“We’ve always tried to address difficult tasks by investing heavily in our equipment and in staff training. This machine is perfect for customers looking to produce reliable components with extremely precise design criteria, as well as those using materials which are less common than sheet steel.” 8 micrometric.co.uk

Visit our website or contact us for a quote or advice
Cambridge Vacuum Engineering (CVE), a specialist in the design and manufacture of electron beam welding (EBW) machines, has built its very first laserwelding system for a tier one automotive customer.
The machine relies on a Trumpf TruDisk 1000, a 1kW solid-state laser with optimised beam quality for welding metals, in this case steel and Inconel.
The origins of CVE can be traced back to the late 1950s when two Cambridge graduates founded the company and its focus has remained the same: EBW and vacuum furnaces, largely in support of aero-engine manufacture.
“In recent years we’ve been supplying a lot more machines to automotive customers, some of which are beginning to make enquiries about EBW alternatives,” reports Steve Horrex, Sales Director at CVE. “Traditionally, EBW works in a vacuum, which is great from a process quality perspective, but vacuum generation and maintenance is sometimes seen as burdensome. For this reason, laser welding is gaining attention in certain applications as it can operate using nothing more than a shield gas.”
Indeed, the company recently received an enquiry for a fully automated, bespoke laserwelding system from an existing automotive customer. It would prove to be CVE’s first laserwelding machine, marking the beginning of its association with Trumpf. The machine is being used by a tier-one automotive
Automotive laser welding
supplier to weld small (approximately 50mm long) steel and Inconel parts together in reasonably high volumes.
“In this particular application, the join quality produced by laser welding with a shield gas was perfectly adequate,” explains Mr Horrex. “Trumpfwas chosen for its track record in the automotive sector and its reputation for quality engineering. The customer’s R&D centre also had a Trumpfsystem, which definitely helped steer the purchase decision.”
Laser welding is a technique known for its versatility and high productivity, especially when joining thin-section materials and welding at high speeds. Compared with other welding techniques, laser welding has relatively low heat input, resulting in low distortion, excellent mechanical properties and minimal post-weld machining.
Shield gasses protect the weld area from oxygen and water vapour. In addition, unlike EBW, no X-rays are produced, so the process does not require an expensive vacuum chamber. This fact also means that higher productivity can be achieved.
Alongside machine reliability, traceability is vital to CVE’s customer. The laser-welding system is required to provide full traceability of all weld parameters and process details. This data is then shared with the end user’s MES (manufacturing execution system).
Offering a compact footprint and increased robustness, the latestgeneration TruDisk 1000 works economically in all laser states thanks to a new pulse function with greater energy efficiency and intelligent energy management.
“Moving forward, the end user is looking to introduce further new parts to the laser-welding machine,” says Mr Horrex. “The tooling, work-holding and automation that we devised facilitates rapid component changeover, thus future-proofing the system.” 8 camvaceng.com
