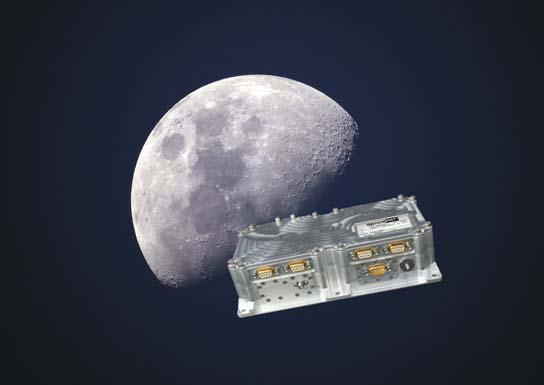
11 minute read
ELECTRONICS
Don’t get lost on the Moon
European Engineering & Consultancy (EECL) and SpacePNT have been awarded a contract by the European Space Agency’s (ESA) Navigation Innovation and Support Programme (NAVISP) to manufacture, test and deliver a Moon GNSS (global navigation satellite system) module.
The space-borne receiver will be flown aboard ESA's Lunar Pathfinder Spacecraft in a low orbit around the Moon and is due for launch in 2024. EECL will deliver the necessary hardware for the advanced satellite navigation payload.
Dr Ben Kieniewicz, EECL founder, said; "The world is heading back to the Moon. The major space players including NASA, SpaceX, and ESA are advancing towards a permanent colony on the Moon." He continued; “In preparation for this, ESA has commissioned the Lunar Pathfinder Spacecraft (LPS). This spacecraft will be placed in a low orbit around the Moon to provide high speed communications from the Moon to Earth (400,000 km). We will provide the navigation system for the LPS, which is a world first and we’re delighted that EECL has been chosen to be part of it."
Earth-based GPS technology does not currently work on the Moon making it impossible to accurately locate satellites in its orbit or astronauts and other objects on the surface. However, LPS aims to change this by flying an ultra-sensitive high-gain antenna receiver pointing towards Earth. The antennas pick up weak signals from Earth-based GPS which leak into space, allowing an accurate position fix, timing and velocity anywhere around the Moon or on its surface to be generated.
Javier Ventura-Traveset, leading ESA’s Galileo Navigation Science Office and coordinator for ESA lunar navigation activities, explained more: "This is an exciting and challenging project because acquiring satellite navigation signals and performing a positioning fix has never been achieved from distances required for lunar orbit. The signals involved will be millions of times fainter than those employed for satellite navigation on Earth, making the engineering requirements extremely demanding. However, we have full faith in our project partners."
The antenna requires an amplifier and receiver module which is one of several components being manufactured by EECL. EECL’s unit measures only 24cm x 12cm x 7cm and is a highly complex microwave radio receiver with advanced signal processing technology. EECL is also providing custom best-inclass, low noise amplifier technology to pull these weak signals from Earth out of the background radiation of deep space. The receiver technology and its complex software algorithms are being manufactured in partnership with Swiss Company SpacePNT, who have decades of experience in weak signal tracking and specialist GNSS algorithms. EECL will bring its extensive RF (radio frequency) design skills, manufacturing and
space experience to ensure mission success. The radiation in the Moon's orbit is particularly challenging and the hardware will be sufficiently robust to survive this hostile environment. "If successful this will be the first demonstration of navigation using GPS away from the Earth and it will enable precise navigation, timing and positioning on the Moon's surface. It is a once in a lifetime opportunity;" said Dr Kieniewicz.
Significant investment to meet exacting manufacturing standards The design, manufacture and testing are taking place at EECL's laboratory in Kingston-UponThames, UK. The company has made significant investments to bolster its production capability and support its industry-leading skills in RF and Space electronics. These include a new ISO-Class-7 cleanroom and thermal test chamber allowing EECL to minimise contamination from unwanted particles during construction. EECL has also acquired sophisticated testing instruments, high-end manufacturing equipment and invested in quality-assurance expertise, mechanical and electrical engineering resources with the expectation to serve the UK Space Sector as it sees exceptional growth over the next decade.
The contract was awarded in April 2021 and envisages a tight time frame. The first two engineering models are due for delivery in early 2022, and the flight unit in Summer 2023. UK Space Agency chief executive, Dr Paul Bate, said; "With humans set to return to the Moon and ambitious plans to explore even further, we need more advanced navigation systems to guide the way. By bringing SatNav to the Moon, EECL is making a significant contribution to global space exploration efforts, and it is fantastic to see a UK SME demonstrating such expertise and innovation."
“This is a great example of how our leading role in the European Space Agency is building UK space capabilities and supporting our thriving space sector, in line with our National Space Strategy.”
The project is a key milestone for EECL. This mission is exceptional due to the requirements for hardware to be flown to the Moon. "This is a big deal. For us to be selected to provide this, before larger, more established suppliers, is significant. It shows that UK SMEs have the capability to make an impact in a domain that was once only supported by government agencies or transnational companies such as NASA or Airbus;" said Dr Kieniewicz.
The close collaboration of EECL with SpacePNT, experts in providing GNSS algorithms and the highly complex technology to track small signals, reflects the UK's continuing supporting for international collaboration. The SpacePNT GNSS receiver module will be validated on the most prestigious of missions. "This demonstration will provide a critical step in humankind’s return to the Moon;" said Dr Kieniewicz. 8 euroecl.com
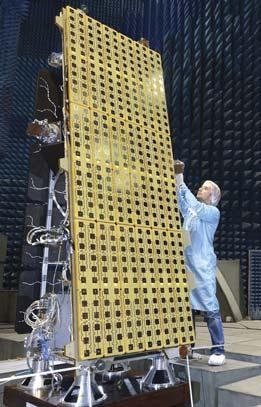
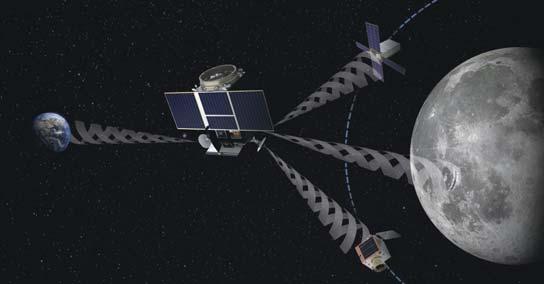
Bridging supply chain gaps
Optimised supply chains can offer huge potential for OEMs to increase profitability, writes Dr. Henrike Wonneberger, and additive manufacturing methods can bridge supply chain gaps and add resilience
Reducing inventory costs with punctual delivery has been, for many years, the focus of supply chain management. Over the years, supply chains have been optimized to perfection, using algorithms and digital tools, but it is a balance on a knife’s edge. COVID-19 and the subsequent closing of borders have revealed the limits of planning and the fragility of supply chains to suppliers, OEMs, and end customers.
Ways to mitigate supply chain risks When a part is needed urgently, every hour can cost manufacturers hundreds and thousands of pounds with the cost of the spare part itself often negligible compared to the economic and reputational damage caused by its absence. Increasing the buffer in warehouses could minimize the risk of supply gaps, but counteracts previous efforts to reduce inventory and increases tied up capital, warehousing costs and obsolescence.
Another option is to source from several suppliers in multiple locations; should one supplier fail, others can cover the demand. However, interconnected global supply chains are often dependent upon a few suppliers of basic materials. Subsequently, for specific parts or components, all worldwide suppliers might be affected by the material shortage. A better solution is not only supplier diversification, but also in material alternatives.
A third way to improve the resilience of the supply chain is to return to localized manufacturing – as witnessed at the beginning of the COVID-19 pandemic. This saw many manufacturers 3D print critical parts needed to fight COVID-19 – such as face shields or valves for respiratory devices. This manufacturing philosophy, named bridge manufacturing, can be used as a blueprint to generally improve supply chain resilience.
Essentially, bridge manufacturing means having a technically viable alternative to bridge a gap. This gap can be economic if other technologies are too expensive, or an availability gap, if parts produced in another manufacturing technology are unavailable. Bridge manufacturing requires a manufacturing alternative for the part that allows on-demand, decentralized production. This ensures the part can easily be made available anywhere globally in the event of a sudden unexpected shortage. Consequently, should supply chains be disrupted, the OEM or supplier has alternative options, potentially saving money and reputation. As a concept, bridge manufacturing comprises three different types: provisional solution, equivalent manufacturing solution, and ramp-up/phase-out bridging.

Provisional solutions Well known in dentistry, this is where a transitional prosthesis –
using a different material and a different technology – is provided as a makeshift solution while the actual prosthesis is manufactured. Requirements for a makeshift solution are often lesser than for the original, making bridge manufacturing a second-best alternative from a technological standpoint.
Whether a part is used as a stop-gap until the ‘original’ spare part is delivered, or until it breaks down and is replaced by the ‘original’ spare part, bridge manufacturing of the part takes place in parallel to ordering a standard ‘original’ spare part. Like this, the machine downtime is reduced in the same way, saving the OEM money and reputation.
Equivalent Manufacturing However, bridge manufacturing can meet all requirements and specifications of the ‘original’ part. In this case, bridge manufacturing might be more expensive, making it inappropriate for standard production, but it might have certain advantages when other constraints occur. For example, a polymer part could be manufactured at low cost per part in large quantities in a central location.
In the event of a global supply chain disruption and the part is needed overseas, this can be bridged by localised 3D printing close to where it’s needed in the required (probably low) quantity. If the manufacturing alternative was set up conforming to specifications, a part produced correspondingly might last as long as an ‘original’, eliminating the need to parallel order the ‘original’ spare part.
Ramp-up/phase-out bridging Change in demand over a product’s lifecycle can vary drastically and upon launch, it’s hard to forecast future demand. For small and mid-volume series, additive manufacturing is an attractive option throughout the whole lifecycle.
If product demand rises quickly, manufacturing methods like injection molding are best from a price-per-part standpoint. Once manufacturing alternatives are in place, bridge manufacturing enables companies to switch as needed to optimize manufacturing costs. 3D printing is often favourable upon a product’s launch when only small quantities are needed, but when demand increases the OEM would benefit from another manufacturing method. Towards the end of the lifecycle, when demand decreases, the OEM can easily switch back to 3D printing.
With bridge manufacturing, it is important the technology does not need significant ramp-up time, is flexible insofar as quantities and is locationindependent. Few manufacturing technologies meet these criteria.
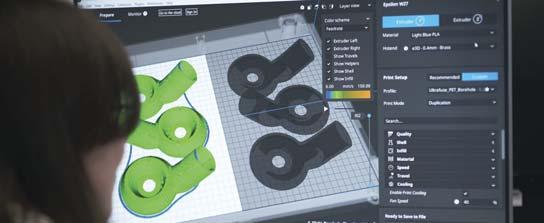
Adding value with additive manufacturing The most viable option for bridging is additive manufacturing.
Once a part is qualified and print parameters are set, it does not need any ramp up but can simply be sent securely to a 3D print service bureau for fast, costeffective production. That’s to say, exactly where the part is needed, when it is needed and in the precise quantity needed –even a lot size of just one. It is these basic principles of 3D printing that continue to make it an agile and benefit-enhancing option for low-volume manufacturing requirements among OEMs large and small.
8 Dr. Henrike Wonneberger is COO
and Co-Founder of industrial 3D printing platform Replique
The road ahead in 2022
Jimmy Saunders, Managing Director of Kroll Restructuring Advisory, asks what 2022 has in store for the automotive supply chain.
As we look ahead to 2022, the automotive sector continues to face structural issues within the industry alongside the wider economic challenges.
Structural Issues During 2019, growing uncertainty around Brexit led to a number of vehicle manufacturers announcing the movement of production to mainland Europe. This was at the same time as customers were already cautious when buying cars because of the evolving electrification of vehicles and concerns around the diesel emissions scandals. Compounding this during early 2020 was the impact of the pandemic, and according to the Society of Motor Manufacturers and Traders (SMMT), new car registrations between 2019 and 2020 fell by 29%.
The impact of this downturn in vehicle sales on the automotive supply chain was in part mitigated by the raft of government support schemes, not least the ability to furlough employees, the various government loan schemes and the VAT deferral scheme.
As different countries emerged from lockdown at different times, the uncertainty of demand and fluctuating availability of parts supply led manufacturers to rationalize their number of vehicle programs to focus on producing core models. This served to create capacity in factories that, as demand improves going into 2022, is being used to accelerate electric vehicle production. Recent statistics from the SMMT suggest that there will be more electric vehicles registered in 2021 than were registered between the whole of 2010 through to 2019. In fact, in the year to October 2021, new car registrations have only grown LFL by 2.8%, behind this number is a reduction in petrol and diesel cars (which for now make up the majority of vehicles) of 22.1%, which is offset only by the significant growth in electric vehicles and hybrids of 65.4% and 82.5%, respectively.
What this shift from internal combustion engines to electric vehicles means is that significant investment is expected in both research and development of the new electric technologies but also into capital expenditure (capex), particularly powertrain suppliers, at a time when businesses are already struggling. Furthermore, both original equipment manufacturer (OEMs) and lenders are putting heavy emphasis on environmental, social and governance (ESG) and sustainability matters, which potentially brings a whole new
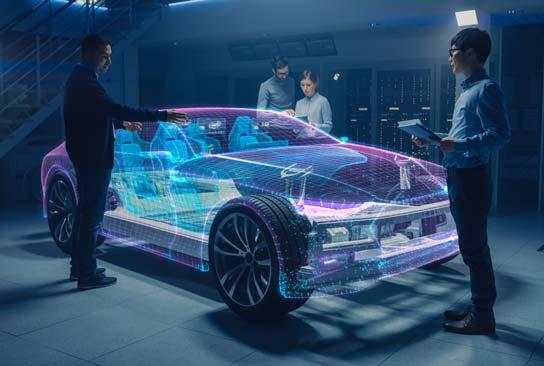