
1 minute read
Emmerdale in 3D
Once the scanning was complete, we processed the files back at Europac3D to prepare them for print, with every model edited to enable two different sized versions of each to be produced final models, printing them on the high-end Mimaki 3DUJ-553 full colour 3D printer. “The Mimaki was the only solution available to us to complete the job,” cites Kenny. “We needed full colour output that would stand up to close scrutiny on the nation’s TV screens, and with its ability to print up to 10,000,000 colours, the Mimaki fit the bill perfectly.”
Aired in the weeks prior to the landmark episode, the trailer is a
1-minute animated scene, depicting the explosive impact of a huge storm on the fictional village. Key characters are shown in emotive poses, suspended in time as the storm wheels around them, and as the camera pulls back, it becomes apparent that they’re actually portrayed as decorations, set amidst a vast cake situated in the village pub.
“The finished trailer is a really dramatic watch, and the 3D printed models were really put to the test during the filming,” concluded Dannielle Kenny. “The producers were delighted with the results of the scanning and printing – and It was a privilege to be able to contribute to a memorable bit of TV history.”
8 europac3d.com
Company of the year at the UK Cast Metals Industry Awards was MRT Castings, which tripled the size of its business in weeks to support the Covid-19 effort.
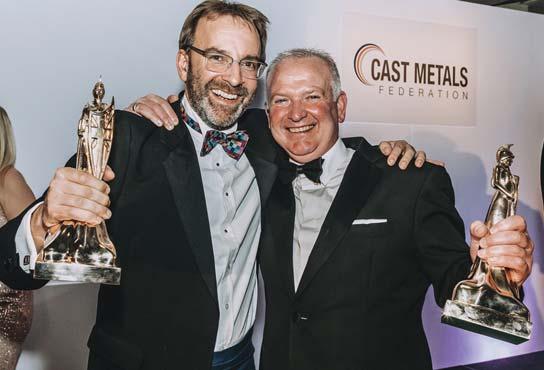
The Andover-based company impressed judges with the way it scaled up rapidly to supply cast aluminium components to one of the world’s largest producers of critical care ventilators.
The firm invested over £3.5m in two additional diecasting cells, seven additional CNC machines and recruited 45 staff to meet huge increases in volumes that saw it grow from £7.8m to £20.8m in a matter of months.
Organised by the Cast Metals Federation, the Awards also saw major accolades going to Sarginsons Industries’ digital twin activities (Innovation) and Atkinson Vos who, working in partnership with The Boro Foundry, ADI Treatments, Partline and Lancaster University, claimed the ‘Component of the Year’ title.
The award-winning part is a 3-point linkage power lift arm for Unimog, which produces a range of multi-purpose tractors, trucks and lorries used in agriculture, forestry and rail sectors.
Initially a steel fabrication, consisting of 9 laser-cut parts, the component was inelegant and prone to distortion and failure.
By converting it from a fabrication to a casting in Austempered Ductile Iron (ADI), the new cast design is four times stronger in the critical areas, whilst being lighter due to the inherent stiffness of the ADI