
2 minute read
Anniversary investment at Erodex
Erodex Group, which designs and manufactures graphite electrodes, tooling and fixtures is celebrating 50 years in business by investing £400,000 in automation at its graphite machining facility in the West Midlands.
2023 marks 50 years in business for the family-owned firm, which is looking to the future with the purchase of an automated pallet loading system to work in coordination with existing high speed machining centres.
As a result of the investment, the company expects to maximise efficiencies and output within a high-volume area of the business; creating capacity without the need to layer in additional shift patterns.
In addition, the alignment of existing machining capacity with automation provides Erodex with a portfolio that it has previously been unable to offer customers, therefore creating new business opportunities.
The company’s machining facility in Wednesbury has been established for over 35 years, enabling Erodex to machine its wide variety of graphite grades into highly complex components for a range of industries. It has also been a key driver in the significant growth that the Erodex Group has experienced in recent years, following a £1.75million investment in new machinery in 2021.
Steve Rolinson, Director at Erodex Group, comments: “We are very proud to celebrate 50 years in business, which is a significant milestone for the Erodex Group.
“The fact that we continue to go from strength to strength as a business is testament to the fantastic, loyal workforce that we have here, many of whom have been with us for a significant amount of time.
“Further investment in our machining facility represents the next stage of evolution for the business. Since the mid-1980s the Erodex Group has enabled our customers to benefit from the capabilities of our ISO 9001 accredited graphite machining facility, which is widely regarded as the best graphite machining facility in Europe.
“Continued planned investment as part of our continuous improvement programmeincluding that in automationmeans that we are well placed to capitalise on market opportunities moving forward and further reinforces our position as UK leaders in the design and manufacture of graphite electrodes, tooling and fixtures for the aerospace and IGT sectors”. Alongside the automation investment, Erodex continue to invest in the upskilling of its employees; placing 2 Operators on additional CAD training and will continue this investment in people through the short and medium term. The company is also set to relaunch its apprenticeship scheme this coming summer, developing the next generation of engineers and further future proofing the workforce.
Founded in 1973, the Erodex group employs 90 people across two sites in the West Midlands with headquarters in Halesowen alongside the Wednesbury based machining facility.
8 erodex.com
The need to ease global supply chain disruption has seen Nemco extend its working relationship with customised safety equipment manufacturer Fortress.
The Stevenage-based contract electronics specialist is celebrating 10 years of supplying Fortress with assembled PCBs for a growing range of products that keep hundreds of thousands of people safe every day.
What started as prototype support and a few thousand assembled PCBs has now grown to volumes in excess of 90,000 per year and covering more than 50 different board variations across various solutions, including mGard trapped key, proNet, amgard ethernet enabled interlock, Atom and tGard configurable interlocks.
The business will be worth £2m per year for Nemco, which is on course to hit its best-ever sales year.
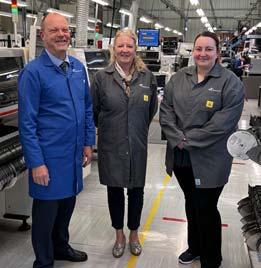
“We work really hard to build strategic relationships with our customers - it’s about a lot more than just supplying boards,” explained Bob Parker, Operations Director of Nemco.
“Our partnership with Fortress is the perfect example of our approach. We work with its design team on new product introductions and then offer technical advice on the most efficient Design for Manufacturing (DfM) process.”
He continued: “This is a real two-way conversation and involves lots of dialogue and collaboration. We’ve also got the