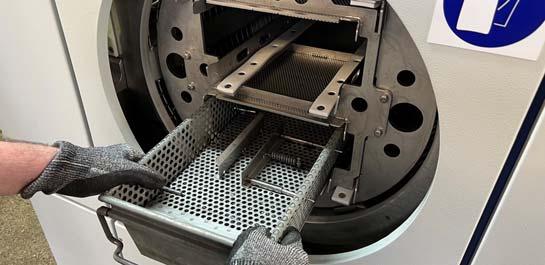
1 minute read
Environmentally friendly precision
towards sustainable CNC manufacturing processes. The machine's efficient cleaning cycle and water recycling capabilities reduce reliance on single-use resources, supporting a circular economy approach.
As an AS9100 aerospace accredited company, APT upholds the highest standards of quality and precision. The MecWash system not only meets APT’s stringent aerospace requirements but also ensures the consistent delivery of pristine CNC turned components adhering to industry specifications.
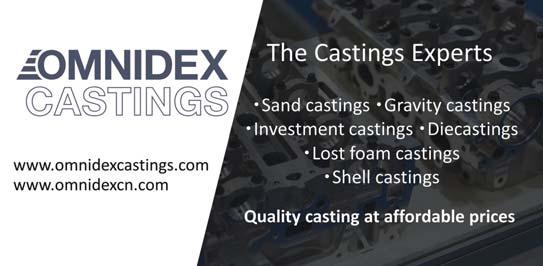
APT Managing Director, Nick Baller, emphasised, "The adoption of the MecWash MWX300 further strengthens our commitment to reducing waste, conserving resources, and minimising our overall environmental impact while maintaining the highest standards in the production of turned parts produced to aerospace standard for our valued customers."
8 aptleicester.co.uk
A large proportion of work going through subcontractor
C&M Precision's Maldon factory involves machining copper bar fed into CNC mill-turn lathes.
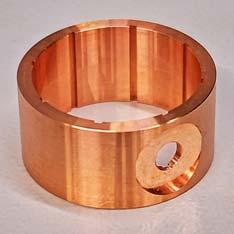

Two sliding-head models out of the nine turning centres on the shop floor, all of which have been supplied by Citizen Machinery UK, have LFV (low frequency vibration) functionality in the operating system of their Mitsubishi controls. It results in much higher productivity and increased yield when converting malleable copper into high-end electronic components for OEMs in the medical, radar, satellite and broadcasting sectors.
Owner John Cable explained that for many of these jobs, a particular grade of copper known as OFHC (oxygen-free high conductivity) has to be used, which is more than 99% pure. One 60 mm long, tight-tolerance component previously produced from 3 mm diameter bar on an early Citizen Cincom M16 slider without LFV had to be turned in one pass through the guide bush down to 1.20 - 1.22 mm diameter along half its length. The continuous string of copper swarf frequently damaged the component and often became lodged in the counter spindle, preventing synchronous transfer after part-off and causing the machine to alarm out. Productivity was severely impacted and up to 20% of parts had to be scrapped.
Mr Cable said: "Transferring the job to a Cincom L12-VIILFV we bought in 2019 was a real winner. With the LFV function turned on,