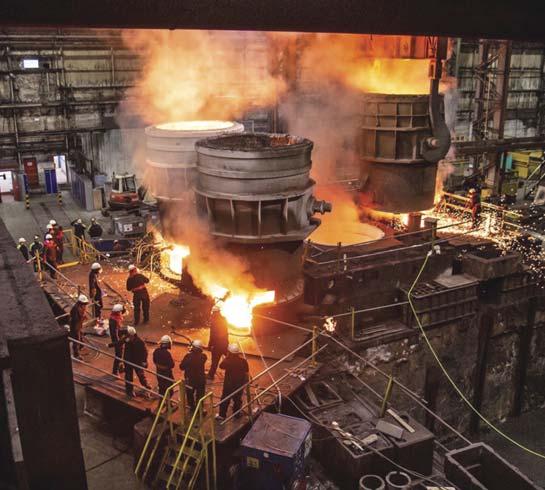
3 minute read
INDUSTRY NEWS
Casting for massive hammer
Sheffield Forgemasters has poured a vast, multi-ladle casting to supply a crucial component for one of the world’s largest counter-blow hammers.
The contract, with the Forged Products business of global specialty materials and solutions company, ATI, builds on a longterm partnership between the two companies. Sheffield Forgemasters has supplied multiple large castings to service ATI’s forging operations for more than ten years.
Weighing in at 155 tonnes, the lower ram for ATI Forged Products’ counter-blow hammer will be delivered to Cudahy Forging plant, which supplies the aerospace industry with titanium and nickel-based forgings.
ATI Forged Products (formerly Ladish) appreciates Sheffield Forgemasters’ technical expertise in this field and the companies’ partnership.
Ryan Edmonds, Customer Programmes Director at Sheffield Forgemasters, said: “We have been working with ATI for more than a decade and through our close partnership, consider them to be one of our best commercial clients.
“The new order is one of a series of contracts that we have completed over the years for cast forging hammer components.
“The size of this latest casting requires it to be finish-machined in a CNC vertical boring machine, which is capable of operating up to five and a half metres in height.
“Sheffield Forgemasters has the only facilities in the UK with the dimensional capacity to finish machine a component of this size.
“In addition, our Foundry is the only one in Europe that can produce castings of this size and weight, a process taking months of planning and work, from building the casting mould, to computer simulating the cooling process to ensure the best material characteristics.”
Sheffield Forgemasters conducted a highly complicated, simultaneous multi-ladle pour to create the casting, requiring four ladles of molten steel weighing in at 380 tonnes.
Counter-blow forging hammers operate with two rams, which work in opposition to deliver the huge forces required for specialist forgings.
The casting will form the lower of two main rams, which drive the counter-blow hammer faces together and the finished cast component will measure 3.5m in height x 3.3m wide x 3.0m deep.
Both rams for this ATI counterblow hammer deliver 125,000Mkg of forging pressure during operation, placing the Sheffield-made casting under immense stresses throughout its operational life.
The contract is due to complete for dispatch to the US in 2023. 8 sheffieldforgemasters.com
Scottish subcontractor 247 Machining Services has added to its fleet of Yamazaki Mazak machines with the installation of a new multi-tasking five-axis machining centre.
Aberdeen-based 247 was founded by husband-and-wife director team, John and Aileen Forrest, in 2018 after 30 years working in the steel fabrication and engineering sector. The company specialises in providing performance-critical parts for the oil and gas industry, and traditionally produces low-volume, high-quality batches of components.
Having previously purchased multiple Mazak Quick Turn turning centres machines over the company’s three-year history, including a QT-Compact 200M and two QT-350MY machines, the Forrests have now invested in a Integrex i-400 full 5-axis multitasking machining centre, to increase the complexity of its production capabilities.
“When we first formed 247 Machining Services, we knew it was key to employ a highly skilled team of machine operators if we were to enjoy the strongest start possible,” explained John Forrest. “So, while we had found a premises to begin operations, we were reliant upon the recommendations of our employees when it came to specifying the right machine tools for the business.
“The quality machining offered by our existing QT turning centres meant that when we were looking to expand our portfolio further, Mazak was our first choice. We wanted to make the move into high-volume, high-quality batch machining for the oil and gas sector, and look at branching into additional industries in the future, and the Integrex fitted the bill.”
The Integrex i-series has a maximum machining diameter of 658 mm and is capable of processing on the X-, Z-, Y-, W-axes, the unit fits 247’s ambitions to produce a wider range of more complex parts.
Aileen Forrest said: “The lockdowns over 2020 and into 2021 obviously posed challenges, but as social restrictions have fallen away, the oil trade has really picked up and demand for parts has grown with that.” 8 247machiningservices.com/
5-axis for 247
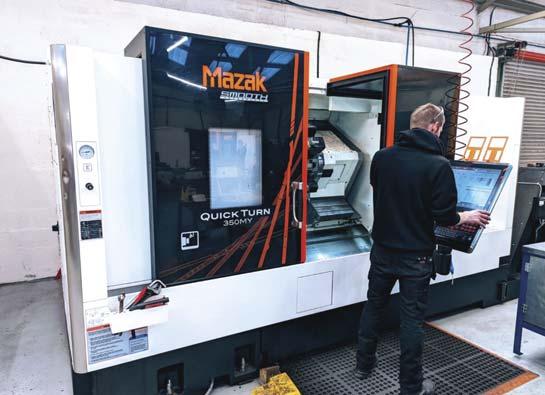
PRECISION ENGINEERING
Aerospace Oil & Gas Nuclear Defence
www.thomas-brown-engineering.co.uk
Tel: 01484 548903
Automotive Electronics Hi Fi Industrial & High Volume Machining