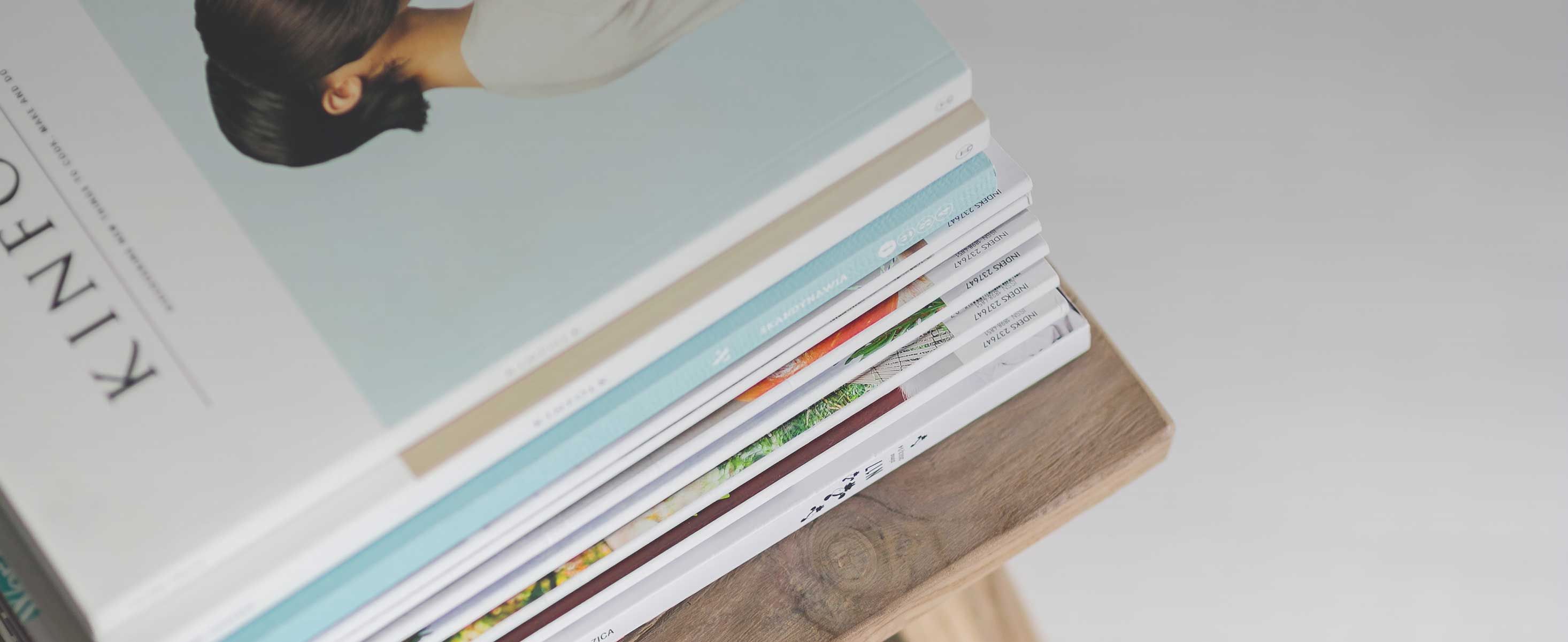
1 minute read
Insert problem handled
height, which would not comply with health & safety guidelines. And thirdly, cobots are inherently slow, whereas the key with injection moulding is to minimise mould open time for maximum productivity.”
Instead of a cobot, FANUC proposed a simpler, faster, more efficient and more flexible solution, comprising a six-axis robot cell. To assist in this alternative approach, it engaged Hi-Tech, its long-term strategic partner for injection moulding handling and integration. The two companies worked seamlessly to devise a solution that involved replacing the existing three-axis robot with a side-entry six-axis robot. This would take four inserts from a bowl feeder, enter the moulding machine through the side door, place the inserts into the mould in the correct orientation, demould the finished component and conduct post-mould checks – all within the specified cycle time.
“With the aim of reducing cost and complexity to the existing system, we designed a selfcontained industrial automation cell,” said James.
Flexibility was also an important consideration in this project as, although the contract was large, other work still needed to be kept on the moulding machine.
“As the name suggests, with a three-axis robot you have three axes of movement: up and down, left and right, forwards and backwards, so when the gripper comes down you can’t change the angle. A six-axis, in comparison, gives you full rotation and therefore free movement. For the manufacture of plastic parts with over moulded inserts, this freedom of movement is invaluable, as precision and accuracy are key to successful production,” added James. 8 mitreplastics.co.uk
William Hughes has been helping a prominent European car manufacturer develop an over-moulded carrier plate and wire frame for use as the backrest on the driver and passenger seats in its range of saloon cars and SUVs.
What started out ten years ago as a reasonably simple wire assembly project involving only wires with a plastic backplate pressed into them has evolved, with William Hughes’s expert guidance, into a much more sophisticated over-moulded assembly with a pressed bracket.