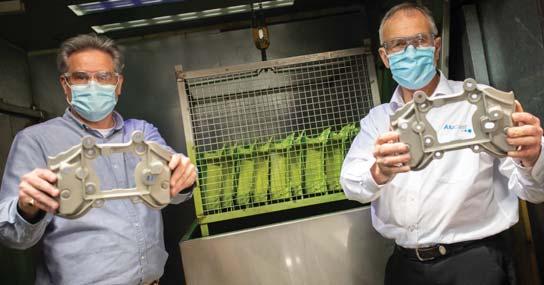
31 minute read
AUTOMOTIVE
Crack-free castings test
Alucast has bolstered its capabilities as a single source manufacturer of aluminium castings with a £200,000 NDT investment.
Alucast, which employs nearly 100 people at its factory in Wednesbury, has secured a number of new wins with major carmakers thanks to its ability to provide simulation, casting, machining and the latest testing facilities.
The latter has been strengthened with the addition of a new dye penetrant offering – a non-destructive process that can assess structural vehicle components and other parts for cracks.
This new line has been successfully operating for several months, with five members of staff fully trained on it.
“The automotive sector is always looking for faster production times and ‘right first time’ quality and this is what our latest investment is delivering,” explained Tony Sartorius, Chairman of Alucast.
“Cast and machined parts are cleaned and treated with a special, coloured penetrant liquid, which searches out minute cracks in the surface of the components. The parts are then left for a period of time, so that the penetrant can soak into any cracked areas, after which they are washed clean, which removes the liquid from the surface.
“A developer is then used on the part and essentially draws out the penetrant from the crack to reveal a coloured line if a fault exists. If cracks are evident, the part is scrapped.”
He added: “What this means to the customer is that they don’t lose time and experience additional costs that arise when a faulty part is sent out for secondary processes.”
Alucast offers sand, gravity and high and low pressure casting to a client base that spans automotive, construction products, electrification and hydraulics.
Dye penetrant testing joins additional complementary services, including casting simulation software, advanced laboratory facilities, X-ray, heat treatment and high-tech metrology.
This is helping the firm, which has recently been re-accredited to the TS16949 automotive quality standard, to create a strong reputation for supporting carmakers and tier 1s with structural lightweight parts for use in next generation vehicles and electric cars.
Tony went on to add: “We have to offer more than just casting if we are going to be successful in the modern auto industry and we started the move to a single source solution five years ago.
“Since that decision, we have invested nearly £3m into upgrading our core making facility and creating a new CNC machining shop with 5-axis capability, as well as the additional technology we have for testing and development.”
He concluded: “Servitization is a big area of potential for us, where customers can access individual services we offer, such as casting simulation and heat treatment, to solve specific production issues or to ensure quality compliance.
“The addition of a Dye Penetrant department is a perfect example of this and we are seeing a steady increase in companies using it to double-check their parts.” 8 alucast.co.uk
William Hughes Group says it has perfected a method of composing and forming complex automotive electric vehicle (EV) busbar geometries out of pre-coated copper stock; and can do so in such a way that the insulation/protective cover remains completely viable along the length of the bar.
Traditionally, busbars are stamped and bent, but stamping cannot always deliver the features required to navigate around the under-bonnet complexity of new-generation EVs. For this reason, bending machines are a far better proposition.
“Battery advances and high voltages mean that busbars are just as at home under the bonnet as they are in a control cabinet backplane,” explains Emma Burgon, Engineering Director at William Hughes. “But automotive applications are not quite as smooth sailing as their significantly less complex industrial peers. As well as electrical insulation, the copper has to be protected from Mother Nature too, which is why the efficacy of the insulation covering is so important.”
The development has been driven by the relative ease with which straight copper bar stock can be more easily coated than bar that has already been shaped. But it is possible to over stress the coating and cause stretches and cracks if the material is bent too far or too tightly. For this reason, significant research and development efforts
New approach for EV busbars
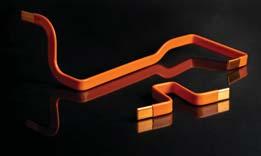
were expended on formulating the capabilities and limits of the materials and the processes.
Using bending machines, the minimum bend radius for the high edge is approximately the same as the material’s height, while the minimum radius for the small edge is approximately the same as the material’s thickness. 90° twisting is also possible for confined areas where a bend could be problematic. In all instances, William Hughes can work with customers to help define the material cross section, the bend radii, the curve forms and the geometry possibilities based on the installation space.
“As a market leader in springs and wire forms, with many customers in the automotive industry, EV busbars were a natural evolution of our capabilities,” Burgon explains.
“We spotted the market requirement for this a few years back and, never being one to shy away from innovation and new markets, we started developing the process and procedures based on the technologies we had in-house. Additional capital assets have since boosted these capabilities, and we are now in a very strong position to serve the needs of the global EV market.” 8 wmhughes.co.uk
DNow Accredited to
FM10101
Manufacturers of High Quality Mill-Turned Parts
HV Wooding is working with the Nuclear AMRC on a new powder coating process that will improve the performance of busbars for electric vehicles.
Supported by Innovate UK through the Faraday Battery Challenge, the project focuses on investigating and developing alternative coating methods that will improve the performance and integrity of the critical components, which carry highcurrent power between different parts of an electrical system.
“Current coating methods are difficult to control, with a high level of components rejected because of poor quality insulation,” explained Paul Allen, Sales Director at HV Wooding.
“There is currently no standard specification or process availability, and our new method will contribute supply chain capability and capacity for battery and energy storage applications.”
He continued: “We will develop a best practice testing method to standardise quality assurance where there is currently no international standard, and this could generate up to £1m in additional sales to our business.”
HV Wooding previously worked with the Nuclear AMRC through the Fit for Nuclear programme, which helps manufacturers meet the quality expectations of the nuclear supply chain.
The company will look to maximise the centre’s advanced manufacturing methods, as well as tapping into university researchers to develop a standardised test procedure for quality assurance, demonstrating that each busbar meets all the required integrity standards with minimal risk of failure in use.
“The current busbar coating process is difficult to control and can’t currently be scaled up to meet customer demands in the UK,” commented Dr Li, head of the Nuclear AMRC’s control & instrumentation research group.
“This funding enables collaboration between a UK SME and academia to tackle a real pressing issue and this project will help ramp up production at HV Wooding whilst also minimising the product failure rate.
“Our team from the University of Sheffield will bring our expertise in electro-mechanical design, process, testing and manufacturing to ensure this collaboration will ultimately enhance the UK’s capability in producing quality busbars for automotive and adjacent supply chains.”
The one-year project will also draw on the specialist capabilities of the University of Sheffield AMRC – like the Nuclear AMRC, part of the UK’s High Value Manufacturing Catapult – and the Department of Electronic and Electrical Engineering.
Paul Allen went on to add: “Powder coated insulated busbars are safer than heat shrink sleeved alternatives. They have better thermal and electrical performance alongside other benefits in compact battery design - for example saving up to 10% clearance and creepage distance.
“If the innovative and optimised epoxy powder coating process is implemented it will definitely open up new markets and will lead to new skilled jobs in our area.
“The successful project will support the overall goal of the Faraday Battery Challenge and scale-up British busbar manufacturing for battery modules and packs in accordance with the UK's Ten Point Plan for a green industrial revolution.” 8 hvwooding.co.uk
EV performance covered
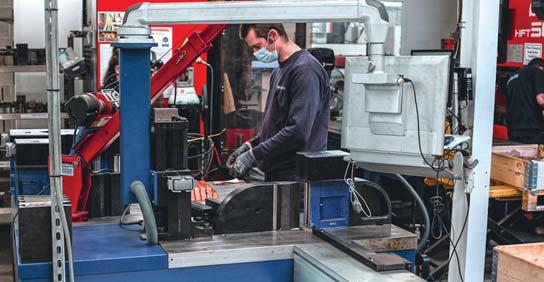
Quality management expert G&P is maintaining quality standards and driving down costs at a European manufacturer of parts for the automotive sector.
The supplier is maintaining quality standards while also making circa 60% cost saving through the deployment of an innovative ‘extended workbench’ solution, developed by G&P.
Central to the success of the operation is the ability to promote best working practice through close teamwork of the supplier’s personnel and G&P’s team members, effectively making them one team.
Meanwhile, logistically an offsite operation was established by
Driving down auto part costs
G&P for the inspection and rework of components, primarily for use in the automotive sector, to ensure they met the correct quality standards. The savings far more than offset any additional logistics costs.
Geoff Cousins, chairman at G&P, said: “G&P has successfully been providing its extended workbench solution for the central European customer through an open and transparent operation with targeted KPIs to drive performance, which remains ongoing today.
“The result for the customer is that quality standards are maintained, efficiency is increased, costs are reduced and its reputation is protected.”
G&P’s off-site facility itself on behalf of the customer housed 90 workstations for inspection and rework, while G&P also handled all the human resource requirements in line with the customer volume demands.
Cousins added: “G&P, in essence, became the customer’s team through our extended workbench solution. It was not G&P and the customer – it was one team.
“Such has been the success that we have subsequently opened an additional facility in central Europe.” 8 gpqm.com
WH William Hughes Group
Bespoke Springs & Wire Forms Secondary processes
William Hughes makes everything possible We’ve been making springs and bending wire for over 200 years. Compression, tension and torsion springs - wire bending, forming and assembly - if something can be made out of wire, we’re just the people to make it. In-house design Rapid prototyping Short & long runs State-of-the-art production facilities
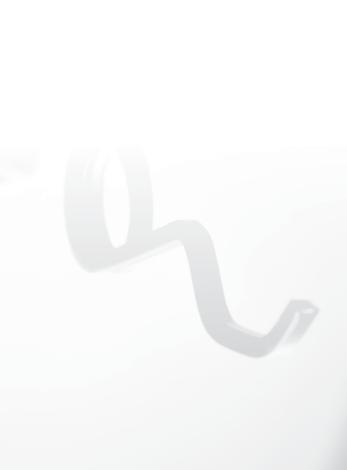

WILLIAM HUGHES Ltd Station Road, Stalbridge, Dorset DT10 2RZ. t: 01963 363377 f: 01963 363640 e: sales@wmhughes.co.uk w: www.wmhughes.co.uk To discuss all things wire, Call now on 01963 363 377

TW Metals, a global supplier of high-performance metals, has invested in a 10kW, 6m-bed laser system for its Longbridge facility.
The TruLaser 3060 fiber has eliminated the time/cost issues associated with using subcontract resources and is now fulfilling next-day delivery demands.
The market segment occupied by the Speciality Distribution business unit of TW Metals has particular focus on materials for critical and hazardous environments, often in sectors such as nuclear, petrochemical, oil and gas, medical and automotive (a separate business unit serves the aerospace industry).
Mike Street, Vice President Europe - Speciality Distribution, said: “The provision of machined or first-stage components is becoming an increasingly common request. We had a plasma cutter for this purpose, but knew a laser cutter would be ideal for our corrosion-resistant and heat-resistant nickel alloys, which extend from thin gauge sheet up to 30mm thick. It would also help us introduce other product ranges, like thin gauge sheets in stainless steel and aluminium.”
David Ellis, Head of Operations - Europe, adds: “We looked at nine machines, ultimately shortlisting two, one of which was the 10kW Trumpf TruLaser 3060 fiber. Certain nickel alloys are notoriously difficult to cut, but in the trials, Trumpf simply programmed the parts on the day we arrived and cut them beautifully, without any subsequent tweaking of parameters.”
Selecting the 6m bed option for the TruLaser 3060 fiber provides TW Metals with a market advantage as it can handle much larger raw material. In addition, the company can get preferential pricing from the mills as they have less processing to undertake, while the large bed also means TW Metals can accommodate four or five large offcuts simultaneously for overnight cutting, should the need arise.
“Although the TruLaser is not yet fully utilised we’re filling it much faster than we anticipated,” says Mr Street. “We have a budget for the machine and we’ve managed to exceed that every month so far. Whereas our previous plasma machine would just cut blocks, the TruLaser has added new dimensions in terms of design and intricate profiling that the plasma was unable to offer, not to mention the dramatically faster cutting speed.”
TW Metals delivers on a next-day basis, so reaction time his key to meeting the service demands of customers.
“The TruLaser 3060 fiber is a game-changer for our customer service because we were previously having to use a subcontractor whenever a request came in for laser-cut parts,” concludes Mr Ellis. “These parts were sometimes taking weeks to arrive and, because we were a small customer to the subcontractor, we were never top of their priority list. The arrival of the Trumpf machine has changed all that.” 8 twmetals.com
6m-bed laser is game changer
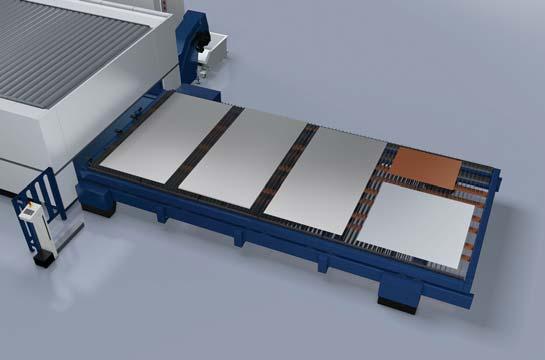
LASER CUTTING Phone: 01782 577929 Email: sales@grenville-engineering.co.uk Website: www.grenville-engineering.co.uk
PUNCHING
METAL FORMING
WELDING
ASSEMBLY
MACHINING
FINIS HING
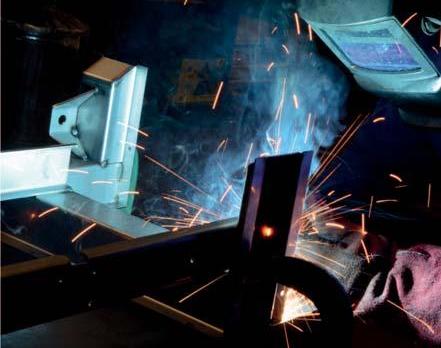
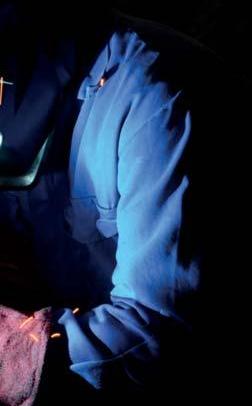

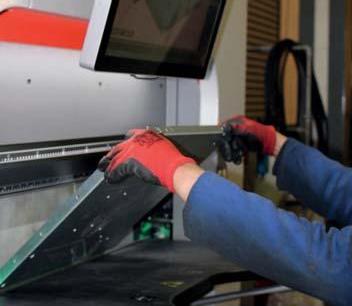



Thanks to a Covid recovery grant, ES Precision plans to offer a subcontract erosion cutting service that gives a degree of precision not possible with flat-bed cutting machines.
ES uses its range of galvo-deflected lasers to provide a laser processing service to medical device, automotive, electronics and other engineering companies. Many of its key sectors were hit hard by the pandemic as there were fewer scheduled operations in the NHS and car plants temporarily closed assembly lines.
ES had been contemplating an expansion of its current laser marking-dominated service to include subcontract erosion cutting but hesitated to do so owing to economic uncertainties and reduced capital available as a consequence of business being hit by the pandemic.
Ultra-precise laser cutting
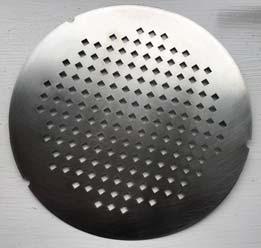
Erosion cutting is a promising application for medium power fibre lasers. It harnesses the flexibility of familiar galvo-driven laser marking systems and meets a demand for precise cutting of thin materials that most commercial flat-bed laser cutters cannot. Such large, expensive CO2- or fibre-based machines with high pressure gas nozzles are not well suited to producing fine features and small profiles in metal sheets which are of order of 1mm thickness.
ES plans to offer a service for profiling, drilling and perforating thin gauge materials – mainly any type of metal, up to about 2mm thick – to high technology manufacturing in Oxfordshire and across the UK and Ireland. In addition to its traditional core sectors it also sees interest from motorsport, solar energy, sensor/ lab-on-achip manufacturers, fuel cell development, instrumentation and aerospace.
Integral to ES’s plans to laser cut structures with great accuracy is a need to precisely measure what has been achieved. This requires investment in an optical measurement system to provide QA and reports for customers in addition the laser cutting workstation.
ES presented its business plans and the impact on Oxfordshire economy in its grant application and the OxLEP committee saw the benefits of funding the project via the government’s Getting Building Fund, which targets capital investment projects which can take part in a much-needed renewal phase for the economy.
ES Precision will take delivery of the erosion cutter and measurement system in the autumn and then launch the service towards the end of 2021. 8 esprecision.co.uk

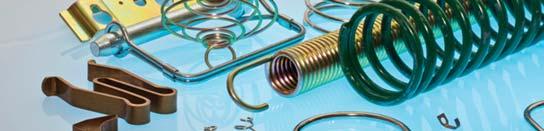
From design, sampling and technical support to manufacture, Simpson Springs & Pressings Ltd provide the complete service.
Tel: 0118 978 6573 Email: sales@simpsonsprings.co.uk
There are multiple benefits from using subcontract rotary friction welding (RFW), including the ability to draw on proven expertise and access industry-leading friction welding machinery without the need for capital investment. A multitude of components can be manufactured across numerous sectors in a range of geometries and material combinations. The subcontractor can advise on materials, geometry, metallurgy and pre and post weld processing.
In the case of bi-metallic, copper-aluminium connectors, there is simply no other viable method of joining these two materials directly thanks to their very different thermal expansion coefficients. Low-cost aluminium is joined directly to high cost copper. Other than the obvious benefit of cost reduction by reducing the use of expensive high conductivity copper, direct costs, waste and the increased threat of theft are also reduced. Aluminium does not impede conductivity and is useful for ease of crimping to electrical cabling. The electrical connector market for power distribution and rail is a significant market for this process.
RFW is a standard bonding method in the automotive sector for producing axles, CV joints, turbo-chargers, airbag canisters, while the aerospace industry uses RFW to manufacture landing gear shafts, steering shafts, ejector seat components and other high integrity parts. The construction industry uses friction welding for piston rods and hydraulic cylinders,
Subcontract rotary friction welding
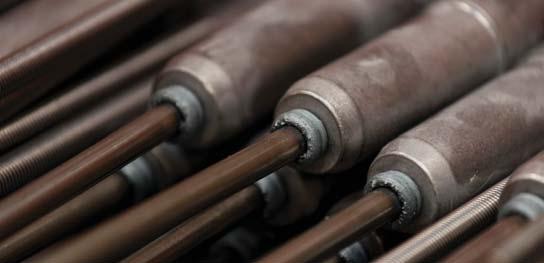
where large diameter high quality steel chromed rods are joined to eyes, yolks and pinions for heavy duty industrial service.
RFW also shows its strength in oil, gas and mining applications where joint integrity in the harshest conditions is paramount, such as drill pipes and rods for deep hole water boring, directional drilling and rock drilling.
The cost of failure in these components can literally cost the operators millions of pounds in lost revenues. The integrity of the friction welded bond is so superior to other joining processes that most OEMs across these industries own and operate their own rotary friction welding equipment to produce their safety critical components in-house.
Cryogenic applications also benefit from the processes’ ability to join dissimilar materials. For instance, stainless steel to copper and interlayered transition joints consisting of stainless steel welded to titanium with an aluminium alloy interlayer. Friction welding has also proved highly successful for welding tools, such as drill bits for example. Stronger than conventional welding, friction welded drill tools have an enhanced join integrity, as the weld is as strong as the parent material.
Whatever the sector, or application in which the component shall be utilised, rotary friction welded products have proven to have an enhanced structural integrity.
The question that engineers and manufacturers ask when considering their production joining and manufacturing processes is can we do this better, cheaper and more efficiently?
The answer is ‘yes’ and the solution lies in subcontract friction welding. For more information please contact: T: +44 (0)121 585 0888 E: frictionwelding.UK@kuka.com 8 kuka.com
Injection moulding company Bloom-in-Box turned to the AMRC North West for help in developing a new high-filtration face mask.
Engineers at the University of Sheffield Advanced Manufacturing Research Centre (AMRC) North West shared their 3D printing skills with a family-run business to create a reliable seal for the mask.
Bloom-in-Box, based in Burscough, has ambitions to show the world the benefits of reusing and recycling plastic across a range of different products.
In 2020, in response to the pandemic and a surge in demand for face masks, the business began to develop a new product - a FFP3 face mask, which is the highest level of filtration a mask can have.
Tom Reardon, Production Coordinator at Bloom-in-Box, said: “We identified a number of opportunities to improve what’s currently on the market and create the best face mask we can. We don’t do things by halves. Not only do we want the highest level of filtration, we want the mask to be reusable and washable, and to explore the use of readily available materials to keep the cost down. We also want to eliminate the use of metal, which limits the medical environments a mask can be used in.
“We were struggling with the seal section of the mask, and AMRC North West helped us by creating some prototypes. We have our own 3D printer but another important element of the support provided by AMRC North West on this project was teaching me how to use it more effectively. The engineers shared their knowledge and expertise, and it was great to learn new skills I can now use to take this product, as well as others, forward.”
Dominic Haigh, a Project Engineer at AMRC North West, said: “Bloom-in-Box is a business that uses recycled plastics and filaments to make a range of products. They came to us interested in options for producing seals for bespoke and small batches of face masks. 3D printing is a great option for this, and there is much less waste in additive manufacturing than in traditional techniques.
“We created a prototype face mask seal printed in flexible material that can fit the shape of a face. Bloom-in-Box is such an innovative company and it was great to work with a business that’s exploring the potential of additive manufacturing technology to create more sustainable manufacturing practices across a range of lines.”
Bloom-in-Box is still developing its face mask and looking for a partner to work with in its production. It has applied to become a supplier of masks to NHS Scotland, which is looking for the specification Bloom-inBox offer. If successful, the company is hopeful the relationship will result in clinical testing of its masks. 8 bloom-in-box.com
Moulders mask up
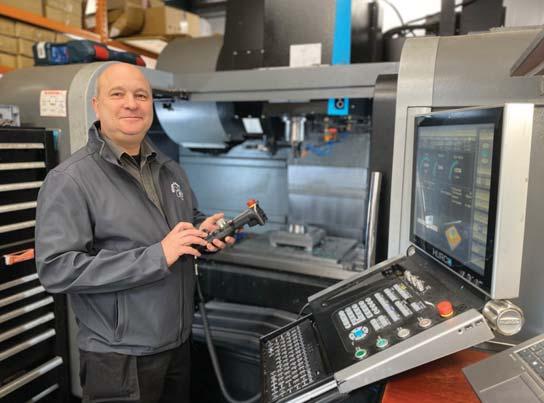
Protolabs has launched a Critical to Quality (CTQ) inspection service for its on-demand injection moulding, whilst maintaining its rapid dispatch times.
This new service will save design engineers days or even weeks of time for the delivery of quality assured parts.
A key aspect behind this rapid reporting and delivery is the company’s new software platform, which creates a digital thread as soon as a customer uploads their CAD into the system.
Working within the new platform, the client simply submits a print of their model and uses red circles on their design to highlight up to five features where dimensions and tolerances are critical.
They can also use a blue circle to indicate additional features they want measuring for reference.
Engineers from Protolabs will then review the model and email an Inspection Statement of Work, which will highlight if any of the features circled as critical have issues with tolerances and mouldability.
After completing the mould development process, Protolabs will inspect the first three shots from the tool using a coordinate measuring machine. It will then inspect a further 30 parts from the order, taken at equal intervals from the production run, to produce the Critical to Quality inspection report.
Lee Ball, General Manager at Protolabs, commented: “This can make a huge difference in the race to get our customers’ products to market first, saving days and in some cases weeks of time. We can complete customer orders from CAD upload, through design for manufacturability and quoting to delivery of the CTQ assured parts in as little as a day.” 8 protolabs.co.uk
Moulding quality service
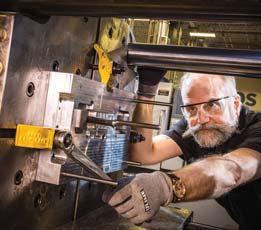
engineering, composites
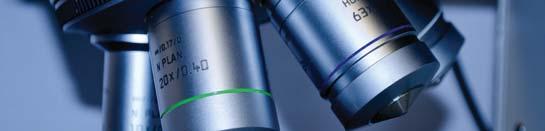
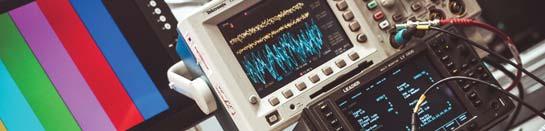
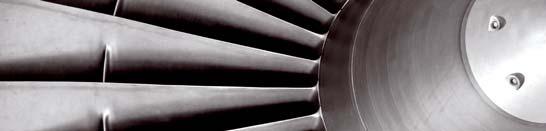
PR | Marketing | | Copywriting | Events Awards | Design | | Web & SEO
01752 894786 www.aroprandmarketing.co.uk
More recycled plastics used
Essentra Components now is using at least 40% postconsumer recycled plastics in components manufactured across its low density polyethylene (LDPE) product lines without any drop in quality or performance.
As part of its journey towards a more sustainable future, nearly all LDPE products produced at the UK facility are now being manufactured using at least 40% recycled plastics, and sometimes even more, without any drop in quality or performance.
Since production began in April 2021, 57 million parts have already been manufactured and distributed across Europe, the Americas and Asia and the Pacific with zero interruption to service, process or increase in cost to customers.
The development is part of Essentra Components’ wider sustainability strategy and part of its Circular Plastics Alliance pledge. Whilst the LDPE range is the current focus, the aim across the division is to incorporate more sustainable materials across the product portfolio so that at least 20% of material processed is from more sustainable sources by 2025.
To reach the 40% initial threshold, Essentra Components has invested hundreds of thousands of pounds into new machinery at its Kidlington, Oxfordshire plant allowing it to mix both virgin plastics resins with post-consumer resin, primarily made from recycled packaging from the bottled drinks industry. The new blending equipment ensure products maintain the same level of quality, integrity and durability but with a more sustainable make-up.
Richard Sederman, Essentra Components’ Strategy and M&A Director said “the move is not only designed to lower Essentra’s environmental impact, but also support its customers’ sustainability agendas: “Manufacturers across all markets are looking at ways to lower their carbon footprint across all scopes. Products like our new LPDE range allow our customers to do that with zero cost or interruption and without having to factor it into their sustainability strategies or budgets.
“The products are already in circulation and have been for 2 months, meaning customers have unknowingly already taken a big step in reducing their environmental impact. This means as we become more sustainable as a manufacturer and distributor, so to do our customers, speeding up the process towards a net zero industry.”
The initial product started at a ratio of 20:80 but continued research and development has allowed Essentra Components to achieve the 40:60 ratio with a view to progress it further to between 50% and 60% within the next few months.
Alongside integrating postconsumer plastics into its new and existing lines, Essentra Components is also researching ways in which to make its supply chain more circular, including collecting and recycling its own products from customers when they reach the end of their lifecycle. 8 essentracomponents.com
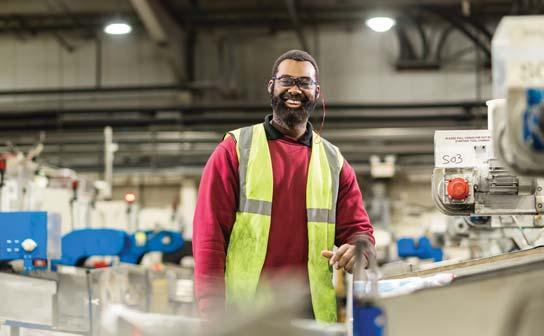
As an alternative to plastics and with an abundance of new alloys being developed, designers are increasingly turning to high pressure die casting for their engineering component requirements. As a near net shape process, and with size envelopes getting wider, metal components can be produced in high volumes and with high dimensional accuracy. From small electronic switchgear through to motor housings and complete Tesla car bodies, the demand for die cast parts is increasing and driving new patents and technology solutions.
The ability for metal parts to be readily recycled at end of life, with an established industry in place to handle the dismantling and recycling of metals alloys compared with other materials, is also a significant advantage, helping companies to meet their sustainability
and circular economy credentials.
Designers need to be able to understand the process to be able to take full advantage of the benefits, and to be able to optimise their designs for metal castings. Early contact with the toolmaker and casting company is of course always recommended when embarking on a component design, or design modification, but there is also a need for training in the process for design engineers and procurement managers, as well as for quality control personnel.
A growing list of companies have found a new way to improve their knowledge through a new online training program in Die Casting Technology. Designers can quickly learn the important technical aspects of the process including the advantage and limitations of metal die casting. This has helped them to have valuable dialog and understanding with their supply chain and get their products quickly created, developed and to their intended user.
Right First Time Design
Completing this specialised and structured course in Die Casting ensures that there are no gaps in their technical knowledge, and can greatly improve performance and the chances of a RightFirst-Time experience during the concept and prototyping stages, through to full series production. The Cast Metals Federation is offering this this online course in the UK with additional support through workshops, mentoring and additional training as required.
To find out more visit: www.castmetalsfederation.com/ training/die-casting-training
Developed by industry experts, the
programme includes access to on-line teaching and as well as tutor support, mentoring and workshops all aimed at supporting the learner and enhancing the learning experience.
formae inFor mor ol tionabouthowtoennr and pricing options please contact: act:options please cont
: 0121 809 3500 email: admin@ .cmfed.co uk
Back with a bang in 2021
The UK’s largest annual gathering of engineering professionals, Advanced Engineering, will return to the NEC, Birmingham on November 3 and 4, 2021. Here, the UK’s talented and vast engineering industry can meet again for the first time in almost two years to do business, make new connections and discover innovation.
This year, there will be seven show zones — aerospace, composites, automotive, performance metals, connected manufacturing, medical devices and, new for 2021, space and satellite. Also, for the first time, Advanced Engineering UK’s sister show, Lab Innovations, will take place in the same hall. Advanced Engineering UK hopes that having so many sectors under one roof will enable crossindustry collaboration and the formation of new business relationships after 18 months of limited interactions.
There will be four forums held during the two-day show, featuring some of the leading voices from engineering and manufacturing. A huge topic at the aerospace forum this year is decarbonising aviation. During the show, there will be presentations on electrification, zero-carbon aviation and hydrogen propulsion from the Aerospace Technology Institute, Rolls-Royce, Ampaire, ZeroAvia and ID TechEx. Supply chain management is a concern for many companies this year, so Advanced Engineering UK will welcome talks from Airbus UK and ADS on supplier expectations and supply chain excellence.
On day two, the forum will have a whole morning dedicated to space and satellite engineering, with talks from the UK Space Agency, Skyrora, DOrbit UK and the Space Applications Catapult.
At the automotive forum, electrification and sustainability will also feature as major themes, with talks from JCB, Ford, the Advanced Manufacturing Research Centre (AMRC), Jaguar Land Rover and many more.
On the composites stage, visitors can find out more about what digitalisation means for composite manufacturing, the 3D printing of composite parts and how composites are enabling the UK’s move towards its net-zero carbon emissions targets. Composites UK CEO, David Bailey will return along with the National Composites Centre’s Head of Digital Engineering, Marc Funnell. BAE Systems and Transport for London will also take to the stage.
During the connected manufacturing forum, Ian Gardner, Industry 4.0 and Oracle Specialist at IBM and Stephen Phipson, CEO of Make UK, will deliver keynote speeches. They’ll be supported by speakers from the Connected Places Catapult, Brunel University London and IoT North, to name a few.
As well as its impressive speaker programme, Advanced Engineering UK will be supported by some of the world’s key industry associations, such as The Institution of Engineering and Technology (IET), Composites
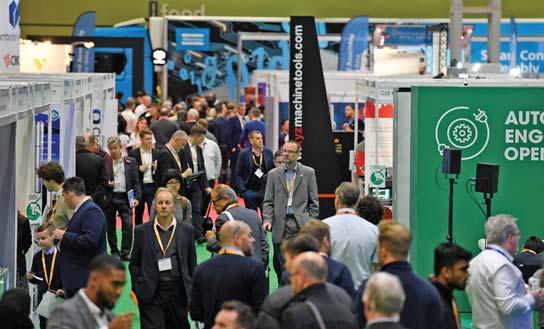
UK, Make UK, the Institution of Mechanical Engineers, GAMBICA, BARA and the Department for International Trade, all of whom now feature as trade body partners.
Advanced Engineering UK is the go-to show for anyone wanting to meet the world’s leading engineering companies, plus the UK’s most innovative start-ups, thanks to the return of the show’s Enabling Innovation zone, supported by Innovate UK. Here, ten chosen start-ups will have the opportunity to showcase their ground-breaking product or technology, before presenting it to a panel of esteemed judges for the chance of winning a stand at next year’s show.
The show already has several exciting features confirmed, including an original prototype of the ExoMars rover, created by Airbus Defence and Space. The rover, commonly known as Bruno, is semi-autonomous and equipped with all the same technology as the final rover, including the sensors, actuators and cameras that allow the rover to see in 3D while navigating Mars. Advanced Engineering UK’s new show zone dedicated entirely to space and satellite innovation will be Bruno’s landing site for the show, and can be found in the existing Aero Engineering floor.
Also on display will be RS Electric Boat’s Pulse 63. The boat’s power source is a battery pack derived from the automotive industry, which harnesses a RIM drive unit rather than a traditional propeller, increasing the boat’s efficiency and offering a
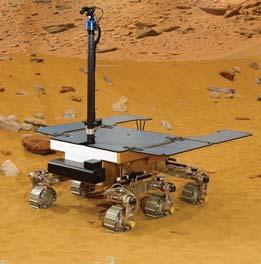
Bruno - ExoMars prototype
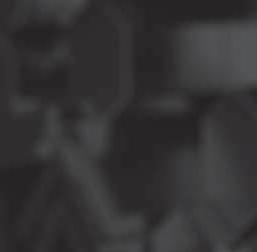
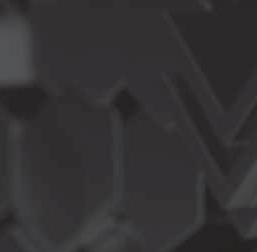
WORKING IN DEMONSTRATING
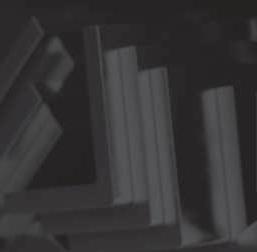
OPERATING WITH

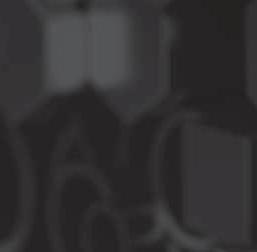
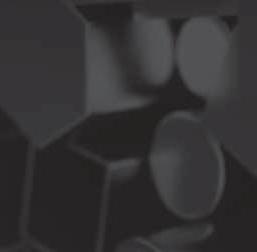
VISIT US ON STAND H74

METALS & PLASTICS
EXPERTISE • COLLABORATION • INTEGRITY
For commercial and aerospace alloy applications, Righton Blackburns has been a trusted supply partner for over a century. Our experience and expertise extends across a wide range of materials, including:
In addition, we are the exclusive supplier in the UK of Hardiall®, a high hardness and low friction copper alloy designed for use in extreme conditions.
Aluminium Stainless steel Brass Copper Nickel alloys Aluminium bronze Phosphor bronze Leaded bronze Copper nickel Bearing steels Titanium Engineering plastics
material. For a dedicated complete supply package to meet choose Righton Blackburns.
Contact your local Service Centre for further information www.rightonblackburns.co.uk
lightweight power solution. The boat is zero emission and the most sustainable laminate of any RIB in the industry. More features will be announced in the coming weeks.
Advanced Engineering offers a great opportunity to meet suppliers, partners and generate business leads for the first time in over a year. Already, the show’s exhibitor space is 90% sold out – a sign that our industry is eager to come together again. In 2019, over 10,000 professionals from the manufacturing sector attended Advanced Engineering. 70% of visitors reported that they planned to place orders as a result of the relationships formed and an impressive 93% of exhibitors reported that they achieved their objectives at the show.
This year, Advanced Engineering UK is also relaunching AE Connect, a digital platform that is used to schedule meetings ahead of the show. In 2019, the platform was used to schedule 588 meetings, which generated an average order value of £200,000 per meeting held. After 18 months of limited inperson meetings, it’s understandable that businesses might not have as many connections as they usually would by this time of year. AE Connect allows both exhibitors and visitors to make the most of their time at the show by filling their diaries with valuable meetings beforehand.
The portal is designed to be very user-friendly. Registered exhibitors receive login credentials to AE Connect, where they can share information about their products and services. Exhibitors can also specify their ideal target audience, as well as their goals during the show.
The smart platform uses this data to find potential matches, allowing exhibitors to contact them to arrange meetings during the show. Meetings can take place in a dedicated lounge area, or directly at the exhibitor’s stand. Exhibitors can also use the platform as a calendar, blocking out periods when they’d like to attend conferences and therefore won’t be available for meetings.
“Advanced Engineering UK marks the return to face-to-face business, which the UK has been craving since March 2020,” explained Alison Willis, Director at Easyfairs, the organizer of Advanced Engineering. “The show offers the UK’s engineering industry the chance to get together again, do business and discover the innovative technologies and products that have been created in the past year.”
Engineering Capacity is an official media partner of the Advanced Engineering Show. 8 advancedengineeringuk.com
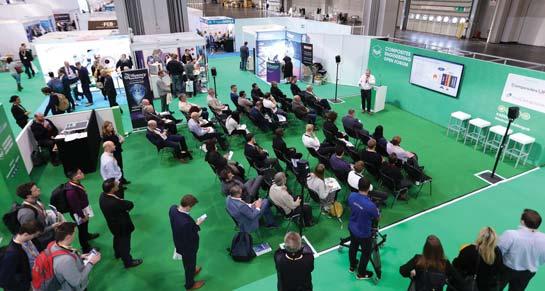
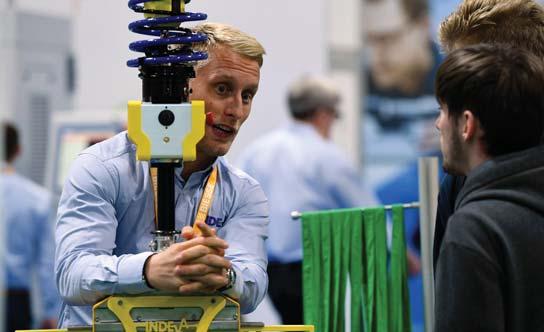