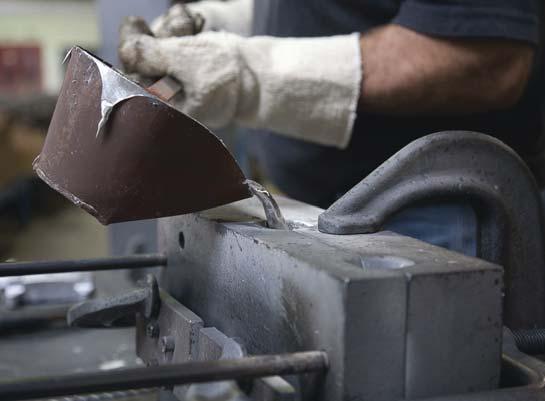
6 minute read
Cast Metals Federation
Several UK foundries offering a wide range of products and processes have recently joined the Cast Metals Federation as the organisation continues to grow.
Chamberlin & Hill Castings Ltd was the latest foundry to join the Cast Metals Federation. Part of Chamberlin PLC, Chamberlin & Hill is the group’s light castings division and is located at Walsall, where the company has been making grey iron castings for over 130 years. The company specialises in producing iron castings up to approximately 25kg, often with complex shapes and fine tolerances requiring highly skilled manufacturing methods, supplied into an increasingly diverse range of markets, such as the automotive and hydraulics industries as well as offering design and rapid prototyping to casting users and sodium hydride cleaning and laser etching of castings for the industry.
Darren Pritchard, Divisional Commercial Manager for the Chamberlin PLC foundries said, “We are looking forward to being able to actively engage with the CMF and other members from the UK industry at this important time for UK manufacturing. We intend to take full advantage of the services offered by the CMF to help us grow our business and ensure we can remain globally competitive.”
Haworth Castings, which supplies aluminium and copperbased sand and gravity die castings to customers from a
Cast Metals Federation continue to grow
wide range of sectors, joined the Federation in the Spring. The company is part of the Expromet Technologies Group, which incorporates Investacast (an investment casting foundry which was already a member of CMF) and CNC machining company, Metaltech Precision. Lachlan Buirds, MD of the company said “We are pleased to be joining the CMF and engaging with other members in the sector through the meetings and information that is provided by the CMF Team. We are committed to providing an excellent customer service by working in partnership with our clients and intend to take full advantage of the services offered by the CMF to help us grow and optimise our business.”
The Cast Metals Federation also welcomed Norfran into membership, which is a supplier of high-pressure aluminium and zinc die castings to international customers from a wide range of industries and sectors. Suppling the automotive sector, parts for white goods, domestic appliances, office furniture and accessories and components for industrial engineering and the electrical and electronic industries the company is certified to ISO 9001 and 14001, and with an integrated Quality Environmental Management
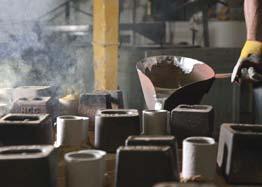
System, the company can offer fully machined or raw castings, with die design and process optimisation through casting simulation as well as project management. “Joining the CMF is an important step for us as we seek to engage with the Federation and our fellow members as part of our vison to continuously improve our operational efficiencies and optimise the performance of the business” noted Mark Smith, General Manager.
Investment foundry Sylatech Ltd joined CMF earlier this year. Producing thin walled, precision parts with a superior surface finish for the aerospace, defence and satellite communications sectors, and offering CNC machining capability, Sylatech utilises rapid manufacturing technologies to offer prototype parts with approval to the AS9100 quality standard. Charlie Breese, Sylatech’s Managing Director said: “We fully intend to benefit from the services and networking opportunities available from the CMF, as well as taking advantage of the range of expertise available from Sharing in Growth’s highly experienced coaches, on topics such as leadership, strategy, culture, lean manufacturing and business development.”
In welcoming the influx of new foundry members, Pam Murrell, CMF CEO said, “As a sector it is import that we work collectively to showcase and support the UK casting and foundry industry as a vital part of the wider UK manufacturing sector. The industry is a key part of the circular economy for metals as it is foundries who take the scrap metal (that arises from other sectors and from parts at end of life) and turn it into new highly engineered components in metal for a wide range of sectors, from automotive to energy generation, from construction to rail transport – all sectors that will be important for the transition to net zero. We are always delighted to welcome new foundries into membership.” 8 castmetalsfederation.com

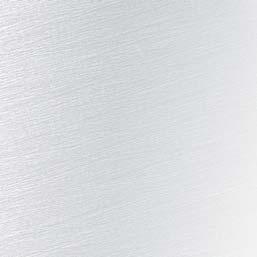





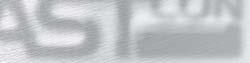



Students can get to grips with the technical side of cast iron metallurgy on a dedicated Institute of Cast Metal Engineering (ICME) course.
Registration for the 2023 course is open now.
ICME’s Certificate Course in Cast Iron Production, Metallurgy and Quality Control saw a successful launch in spring this year, as the learners (who are all from ferrous foundries) started to get the low-down on all things technical with cast iron. The first session saw the learners complete a foundry tour, as well as get a close look at the casting process, safely melting metal and a deeper dive into the chemistry of metal alloys.
Amy Worrallo, Quality Manager for ICME, said: “This course has been developed in response to a clear need from industry for a practical programme, focused on the metallurgy and production of the suite of cast irons,” she explains. “It includes modules on melting and shop floor quality controls, raw material selection, metal treatments as well as testing and quality assurance. With a mix of classroom delivery, practical aspects and project work completed in company, this is a great new offering from ICME and clearly fits with our aims, as the professional body for the UK industry, to support the professional development of our members.”
Michael Cramphorn, Foundry Director for Thomas Dudley Foundry explained why this course is vital to the success and support of the industry. “Finding talent is getting increasingly difficult particularly in the field of metallurgy, where technological changes have transformed process control in recent years. The introduction of the Foundry Metallurgy programme will enable some of our existing melt plant team to extend their current knowledge base and to network with similar people from different backgrounds.”
This course is a joint venture from ICME and the Cast Metals Federation, with the aim of increasing, knowledge, growth and progression within the industry. Dr Pam Murrell FICME, CEO of the Cast Metals Federation, highlighted the importance of this course to the industry, saying, “We have supported the development of this new course, in conjunction with ICME and many of our industry Members, as we recognised the need for a programme that is specific to cast iron metallurgy. It is vital that we have courses that support the future development of our industry. We are also particularly grateful to the Foundry Training Trust who have offered substantial funding to anyone from the UK enrolling for the course, helping to make it more affordable for the industry.”
The new Cast Iron Metallurgy course is designed with progression in mind as ICME is not just about educating those new to the industry, but also about strengthening the talent within the industry.
Registrations for the next cohort, to start in Jan 23, are now being taken, so to find out more about the course please contact 8 info@icme.org.uk
Cast iron facts

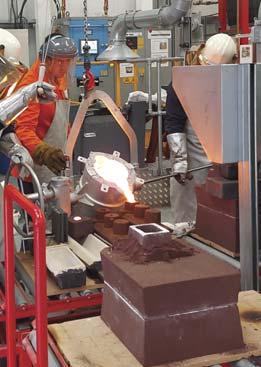