STONDECK PARKING DECK SYSTEMS
DESCRIPTION
1.1 This document is designed to provide system application information for various StonDeck Parking deck systems and describes in detail how cracks and terminations etc. should be dealt with on site. The techniques involved may require localized modification dependent on jobsite conditions. For additional information contact Stonhard Technical Services Department
SUBSTRATE PREPARATION
2.1 Surface preparation should take into account various site conditions including area size, location and nature of project (small scale repair V’s complete decks). In all instances refer to ICRI’s Technical Guideline No. 03732- Selecting and Specifying Concrete Surface Preparation for Sealers, Coatings and Polymer Overlays for advice on selecting the appropriate method of concrete preparation.
Our preferred surface preparation method is Blastrac to achieve a minimum surface profile of CSP 2-4.
SUBSTRATE REQUIREMENTS
3.1 Concrete substrate should be a minimum of 25 MPa, sound and free from laitance, dust, oils and other contaminants. Substrate should be dry to 80% Relative humidity. For surfaces that are outside these parameters please contact Stonhard Technical Services Department for additional information.
3.2 Concrete surfaces shall be properly prepared so that the surface to receive the StonDeck Parking Deck System is free of sealers, curing agents, loose particles and other contamination or foreign matter which may interfere with adhesion.
3.3 Shrinkage crack that are 1/16” (1.6 mm) wide or greater shall be ground out to a minimum 1/4” wide x 1/2” (6 mm x 12 mm) deep shall be caulked with Dymonic 100 then treated according to the instructions in Section 5, Detail Work.
3.4 Structural cracks regardless of width shall be ground out to a minimum 1/4” wide x 1/2” (6 mm x 12 mm) deep and caulked with Dymonic 100 then treated according to the instructions in Section 5, Detail Work.
3.5
Spalled areas shall be cleaned and free of loose contaminants prior to repair, Stonhard Construction Solutions offers a complete range of compatible restoration materials, for additional information please contact Stonhard Technical Service Department for the best repair options.
3.6 In the event of exposed reinforcing steel, it is recommended that the structural engineer of record be contacted for investigation of the condition and for the best method of repair.
3.7 Surfaces shall be made free of defects that may telegraph and show through the finished coating. Surfaces that are rough (fins, ridges, exposed aggregate, honeycombs, deep broom finish, etc.) shall be leveled/ ground and repaired as necessary.
3.8 Prior to application of the StonDeck System verify that all drains are clean and operative. Drains shall be recessed lower than the deck surface and the surface shall be sloped to drain to provide positive drainage.
3.9 Concrete surfaces at drains, expansion joints and ramp terminations should be detailed as follows:
Cut a 1/4” wide x 1/2” deep (6 mm x 12 mm) keyway into the concrete surface at any point where the coating will have an exposed terminating edge, ie. any point where the coating will end in an open area subject to traffic.
3.10 If the project is a restoration deck, old sealant and backing material shall be removed. The joint interface will require a thorough wire brushing, grinding, sandblasting, solvent washing and/or primer.
JOBSITE MATERIALS
4.1 Recommended materials and their use are as follows:
Dymonic 100: A one-part, moisture-curing, gun grade polyurethane sealant used to seal cracks, control joints, drain detailing, and forming cants.
StonDeck FD membrane: Low VOC, epoxy hybrid membrane used as the elastomeric waterproofing membrane and for detailing of cracks and upturns.
STONDECK PARKING DECK SYSTEMS
StonDeck Basecoat: A semi-flexible VOC compliant, highsolids polyurethane body coat providing a durable chemicalresistant, weatherproof wearing surface, designed to receive aggregate broadcast.
StonDeck Finish: A two-part, aromatic, low odour, VOC compliant, high-solids polyurethane top coat providing a chemical resistant, durable and decorative wear surface.
StonDeck UV Finish: A two part, aliphatic low odour high solids polyurethane top coat designed to provide a UV and chemical resistant, durable decorative wear surface.
Backer Rod: A closed-cell polyethylene backer material used in expansion joints and at the base of cants to prevent threesided adhesion, and to control the depth of the sealant.
Aggregate: 20-40 mesh silica sand or alumina oxide, which imparts a textured finish and contributes to slip and wear resistance.
DETAIL WORK
Note: Do not apply sealant or coatings to a frosty, damp or wet surfaces or when air or surface temperature is below 50˚F (10˚C) or the surface temperature is above 80˚F (30˚C). Cure times as stated below are based upon standard ambient conditions of 75˚F (25˚C), 50% RH. A decrease in ambient temperature will significantly lengthen the cure time.
5.1 Apply a 1/4” (6 mm) diameter backer rod into the corner at the juncture of all horizontal and vertical surfaces such as curbs, wall sections, columns, or penetrations through the deck. Apply a bead of Dymonic 100 1” (2.5 cm) wide over the backer rod. Tool the sealant bead to form a 45° cant. Use sufficient pressure to force out any trapped air and to assure complete wetting of the surface. Remove excess sealant from the deck or wall joint. NOTE: Backer rod is only required for moving joints.
5.2 Install a backer rod, 1/8” to 1/4” (3 mm to 6 mm) diameter larger than the joint width to all prepared control joints. Set depth of backer rod to control the depth of the sealant. (Depth of sealant is measured from the top of the concrete surface.) Proper depth of sealant is as follows:
For joints 1/4” (6.4 mm) to 1/2” (12.7 mm) wide, the width to depth ratio should be equal.
Joints 1/2” (12.7 mm) wide or greater that are not expansion joints should have a sealant depth of 1/2” (12.7 mm). The minimum joint size is 1/4” x 1/4” (6.4 mm x 6.4 mm).
All cracks and joints shall be sealed with Dymonic 100, and tooled flush with the surface. Note: Expansion joints should not be coated over. For treatment of expansion joints, contact Stonhard Technical Service Department.
5.3
5.4
Allow sealant to cure overnight.
Apply a strip of masking tape or duct tape to the vertical sections, 2” or 3” above the Dymonic 100 Sealant cant to provide a neat termination of the vertical detail coat.
5.5 StonDeck FD Membrane shall be mechanically mixed in accordance with the Product Data Sheet and applied as detailed below.
DETAIL WORK
5.6 Apply 25 mil thick detail coat of StonDeck FD membrane over the treated cant, and extend it to the tape on the vertical surface and 4” (100 mm) onto the horizontal surface. Feather-edge the detail coat on the horizontal surface so it will not show through the finished system.
5.7 Apply a 25 mil thick detail coat of StonDeck FD membrane 6” (150 mm) wide, centered over all untreated cracks, all routed and sealed cracks, and over all cold joints. Featheredge termination of the detail coat to prevent these edges from showing through the finished system.
5.8 Allow all detail coats to cure for a minimum of 24 hours (depending on temperature and humidity).
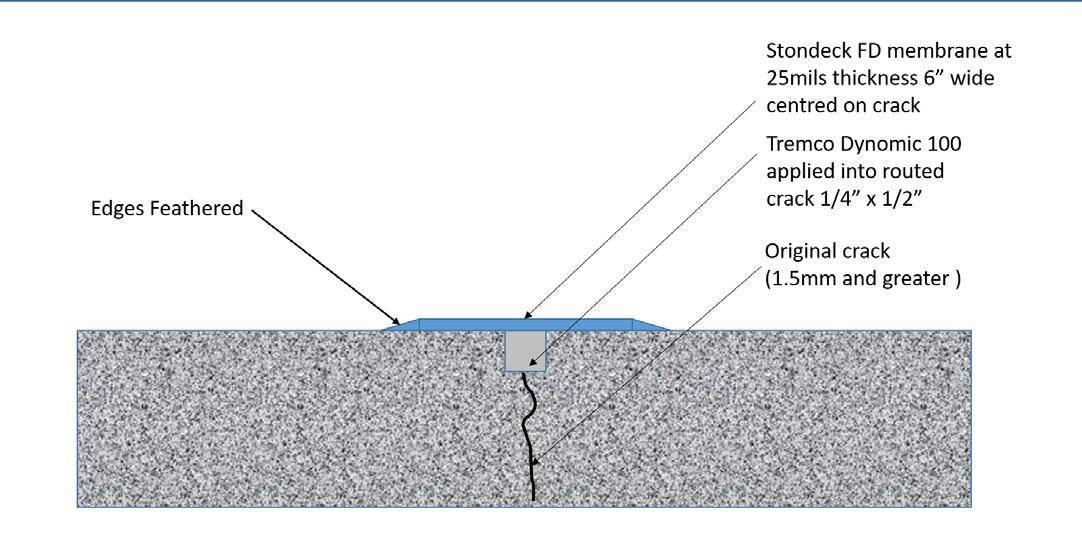
COATING APPLICATION
NOTE: Refer to System Product Data Sheets for application information.
This data should be read in conjunction with the Product Data Sheets for the following StonDeck Systems:
• StonDeck FD2 Medium Duty Intermediate Deck System
• StonDeck FD2 HD Intermediate Deck System Heavy Duty
• StonDeck XD2 Intermediate Deck System
• StonDeck XD3 Ramp System
• StonDeck FD4 Exterior Deck System
• StonDeck XD4 Exterior Ramp System
STONDECK PARKING DECK SYSTEMS
CLEAN UP
7.1 Clean all adjacent areas to remove any stains or spills with Toluene or Xylene.
7.2 Clean tools or equipment with Toluene, or Xylene before material cures.
7.3 Once cured StonDeck can only be removed by mechanical means.
7.4 Exposure to skin should be avoided, in case of contamination, clean by soaking in hot, soapy water then brushing with a stiff bristle brush.
MATERIAL USAGE GUIDELINES
• Dymonic 100: For a 1” (25.4 mm) cant bead over a 1/4” (6 mm) backer rod, 1 case of sealant for every 48 if (14.6 M) is required.
• Dymonic 100: For a crack/joint routed to 1/4” wide x 1/2” (6 mm x 12 mm) deep approximately 25 ft per 600 ml sausage.
• StonDeck FD Membrane: Approx. 50 ft2 per gallon at 30 mils
• StonDeck Basecoat: Approx 80ft2 per gallon at 20 mils
• StonDeck Finish: Approx 80ft2 per gallon at 20 mils
• StonDeck UV Finish: Approx 100ft2 per gallon at 15 mils
• Aggregate: Full broadcast System approx. 0.55lbs/ft2
PARKING STALLS
8.1 Parking Stalls should receive StonDeck FD2 to be applied once the crack treatment has been completed.
8.2 Mix FD membrane in accordance with the product data sheet and apply to the prepared substrate with a 30 mils notched squeegee to achieve a nominal thickness of 28 mils. Each 4.5 gallon unit should yield approximately 250ft2. Allow to cure overnight, at lower temperatures cure times may be extended.
8.3 Once the FD membrane has cured to a tack free state, mix and apply a layer of StonDeck Finish which shall be applied with a 30 mils notched squeegee. Apply to a nominal thickness of 20 mils and broadcast and back roll with StonDeck Quartz aggregate applied at a rate of 0.1 lbs per ft2 to achieve an even and uniform texture.
8.4 Bring StonDeck Finish up and over the FD membrane applied on the upturns to seal the surfaces and provide a decorative finish. Any tape applied should be removed prior to curing. Aggregate is not required for upturns.
8.5 Allow to cure for a minimum of 24 hours prior to opening up to traffic. Cure times will be extended at lower temperatures.
DRIVE LANES AND TURNING AREAS
8.6 Drive lanes and turning areas should receive StonDeck XD2 applied in accordance with the Product Data Sheet and once the crack treatment has been completed.
8.7 Mix StonDeck Bodycoat in accordance with the Product Data Sheet and apply to the prepared surfaces with a 30 mils notched squeegee to achieve a nominal thickness of 25 mils.
8.8 Broadcast the StonDeck Bodycoat with StonDeck Quartz aggregate to saturation at a nominal rate of 0.75lbs/ft2 and allow to cure for 8 hours.
8.9 Remove excess aggregates by sweeping and vacuum prior to sealing.
8.10
Seal the swept and prepared surface with StonDeck Finish applied with a flat squeegee to achieve a nominal thickness of 20 mils. Bring the StonDeck Finish onto the upturns to seal the system and provide a decorative finish. Any tape should be removed prior to curing.
8.11 Allow to cure for 24 hours prior to opening to traffic. Cure times will be extended at lower temperatures.
TROUBLESHOOTING
9.1 This section describes common industry application issues when certain environmental conditions exist. Below are some commonly seen issues and remedies. If any of these should occur, it is always recommended that you contact Stonhard Technical Services Department.
TROUBLESHOOTING
9.2 When a deck contains too much moisture, the moisture may change into a vapour, which then condenses at the concretemembrane interface before the coating has cured and may cause blisters or bubbles, ultimately interfering with proper adhesion. If this should occur, the blisters can be cut out, allowing moisture to escape. After moisture has escaped and the surface is dry, the area can be repaired.
9.3 If the coating application has been installed at a thickness that is greater than directed in our installation instructions, pinholes, blisters or bubbles may occur in the coating. To avoid this occurrence, the material should be applied in accordance to the installation instructions.
9.4 If the coating is applied in very hot ambient temperatures, the air in the small spaces between the concrete particles increases in volume and forms blisters. Contact Stonhard Technical Services should this occur.
STONDECK PARKING DECK SYSTEMS
9.5 If the previous coating application has not fully cured, solvent may become trapped between the coats and lead to large blisters that will most likely be tacky on the backside. Blisters may be cut out and repaired after the surface has been allowed to fully dry.
WEATHER IMPACT ON COATING APPLICATION
10.1 Deck and ambient temperatures will effect the way the StonDeck material behaves and cures.
10.2 Lower temperatures will extend cure times and materials will become more viscous, affecting both productivity and product yields.
10.3 Higher temperatures will reduce working and cure times, excessively high temperatures may make products cure so quickly that yields are affected.
QUICK REFERENCE APPLICATION CHART
Bodycoat (Drive lanes, ramps, turns, ticket areas)