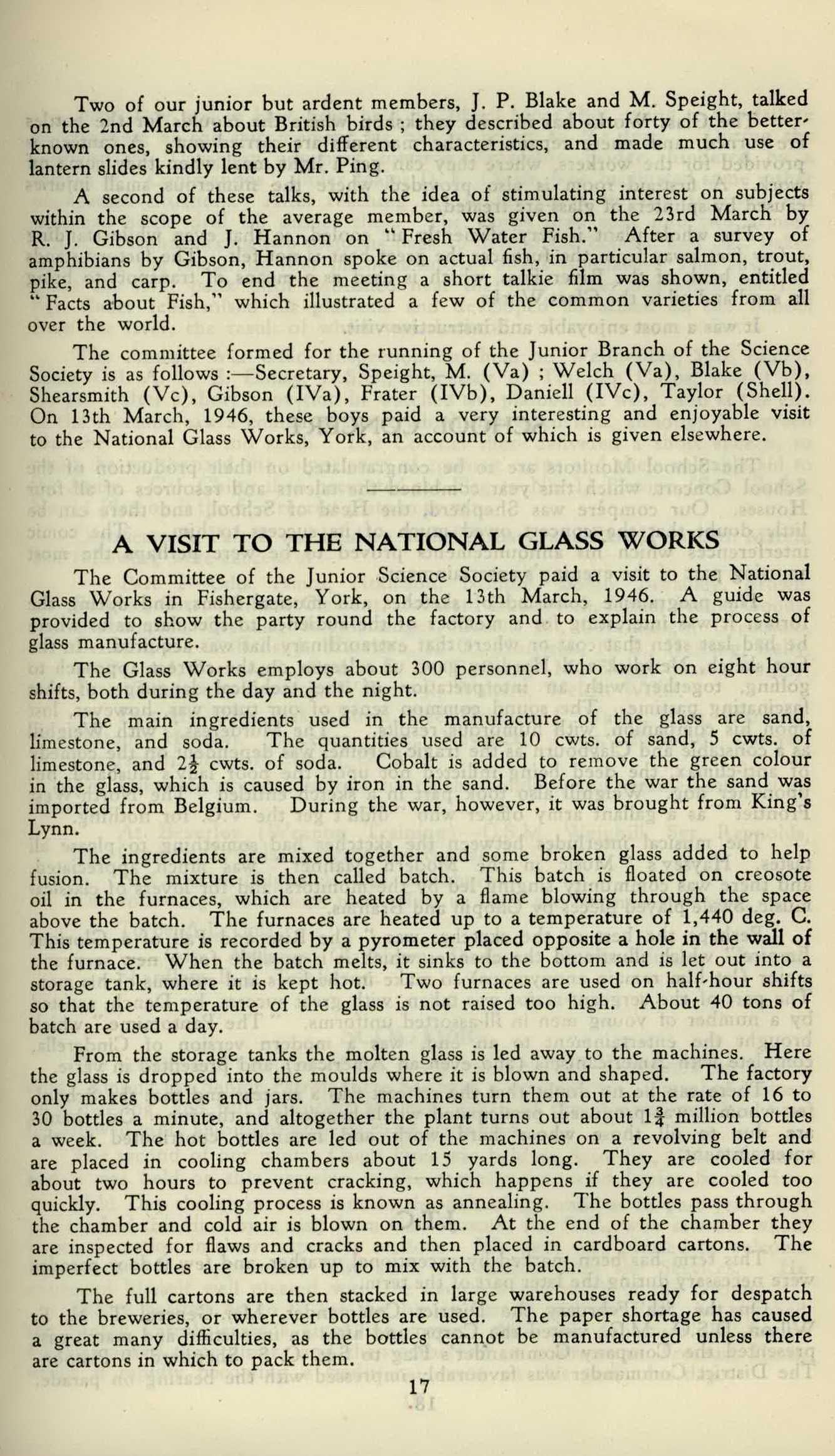
3 minute read
A Visit to the National Glass Works
from May 1946
by StPetersYork
Two of our junior but ardent members, J. P. Blake and M. Speight, talked on the 2nd March about British birds ; they described about forty of the betterknown ones, showing their different characteristics, and made much use of lantern slides kindly lent by Mr. Ping.
A second of these talks, with the idea of stimulating interest on subjects within the scope of the average member, was given on the 23rd March by R. J. Gibson and J. Hannon on " Fresh Water Fish." After a survey of amphibians by Gibson, Hannon spoke on actual fish, in particular salmon, trout, pike, and carp. To end the meeting a short talkie film was shown, entitled "Facts about Fish," which illustrated a few of the common varieties from all over the world.
The committee formed for the running of the Junior Branch of the Science Society is as follows :—Secretary, Speight, M. (Va) ; Welch (Va), Blake (Vb), Shearsmith (Vc), Gibson (IVa), Frater (IVb), Daniell (IVc), Taylor (Shell). On 13th March, 1946, these boys paid a very interesting and enjoyable visit to the National Glass Works, York, an account of which is given elsewhere.
A VISIT TO THE NATIONAL GLASS WORKS
The Committee of the Junior Science Society paid a visit to the National Glass Works in Fishergate, York, on the 13th March, 1946. A guide was provided to show the party round the factory and to explain the process of glass manufacture.
The Glass Works employs about 300 personnel, who work on eight hour shifts, both during the day and the night.
The main ingredients used in the manufacture of the glass are sand, limestone, and soda. The quantities used are 10 cwts. of sand, 5 cwts. of limestone, and 2i cwts. of soda. Cobalt is added to remove the green colour in the glass, which is caused by iron in the sand. Before the war the sand was imported from Belgium. During the war, however, it was brought from King's Lynn.
The ingredients are mixed together and some broken glass added to help fusion. The mixture is then called batch. This batch is floated on creosote oil in the furnaces, which are heated by a flame blowing through the space above the batch. The furnaces are heated up to a temperature of 1,440 deg. C. This temperature is recorded by a pyrometer placed opposite a hole in the wall of the furnace. When the batch melts, it sinks to the bottom and is let out into a storage tank, where it is kept hot. Two furnaces are used on half-hour shifts so that the temperature of the glass is not raised too high. About 40 tons of batch are used a day.
From the storage tanks the molten glass is led away to the machines. Here the glass is dropped into the moulds where it is blown and shaped. The factory only makes bottles and jars. The machines turn them out at the rate of 16 to 30 bottles a minute, and altogether the plant turns out about 1i million bottles a week. The hot bottles are led out of the machines on a revolving belt and are placed in cooling chambers about 15 yards long. They are cooled for about two hours to prevent cracking, which happens if they are cooled too quickly. This cooling process is known as annealing. The bottles pass through the chamber and cold air is blown on them. At the end of the chamber they are inspected for flaws and cracks and then placed in cardboard cartons. The imperfect bottles are broken up to mix with the batch.
The full cartons are then stacked in large warehouses ready for despatch to the breweries, or wherever bottles are used. The paper shortage has caused a great many difficulties, as the bottles cannot be manufactured unless there are cartons in which to pack them.