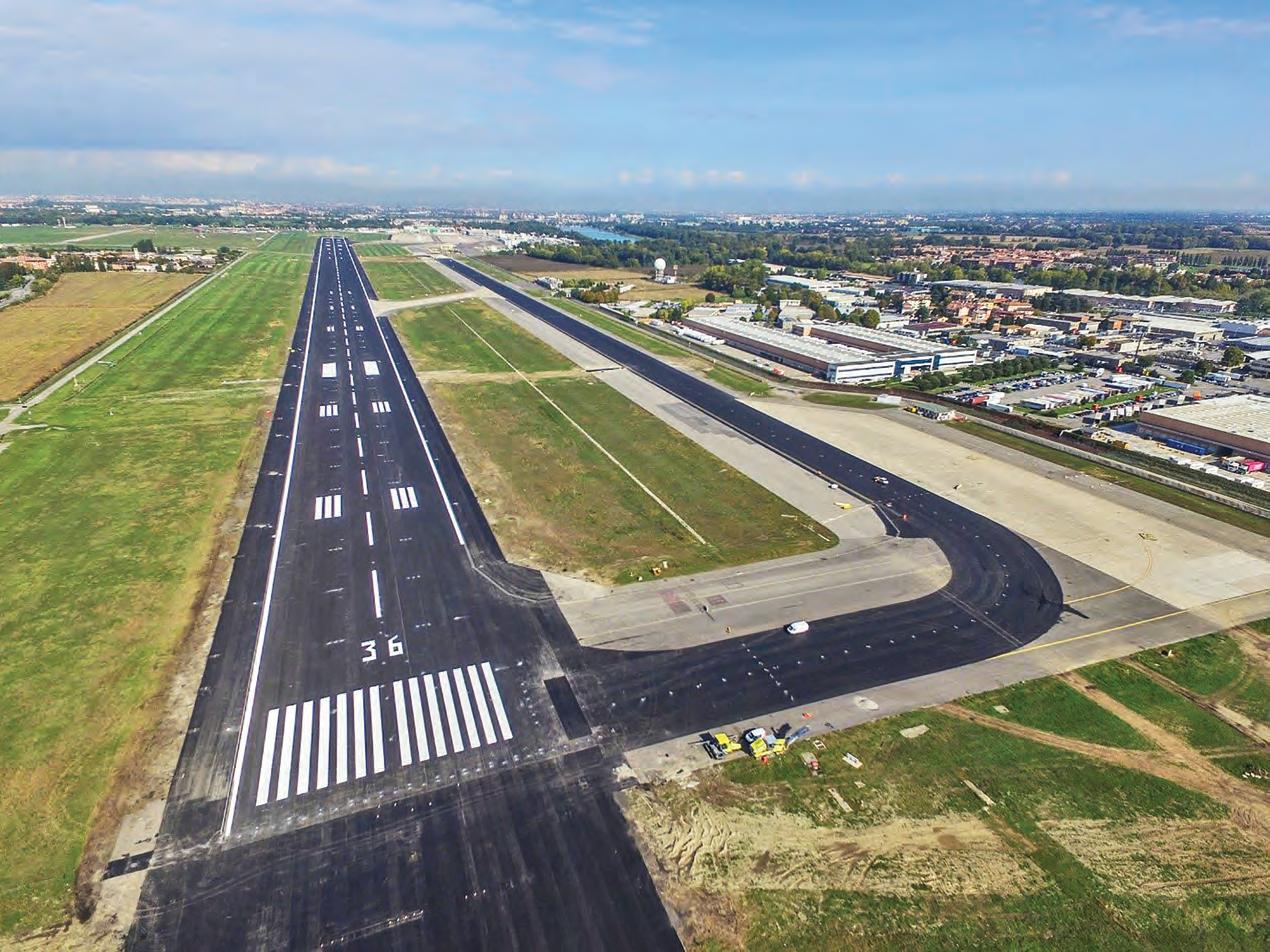
31 minute read
Pavimentazioni aeroportuali sostenibili e performanti
Giovanni Corbo(4) Paolo Morelli(5) Marco Andreula(6) pavimentazioni &manti
PAVIMENTAZIONI AEROPORTUALI
Advertisement
SOSTENIBILI E PERFORMANTI
I MATERIALI INNOVATIVI E LA PIANIFICAZIONE DEI CONTROLLI NELLA RIQUALIFICA DELL’AEROPORTO DI MILANO LINATE
La pista 18/36 dell’aeroporto di Linate in fase di ultimazione dei lavorazioni
La chiusura al traffico aereo per la riqualifica dell’aeroporto di Milano Linate (si veda “S&A” n° 141 Maggio/Giugno 2020 a pag. 64) non è certo passata inosservata, anche ai non addetti ai lavori. Infatti, di grande impatto è stata la eco derivante da tale importante iniziativa, anche amplificata dai mezzi di comunicazione di massa, nonché da eventi e spettacoli che hanno marcato e scandito il periodo di chiusura dello scalo, dandone nuova forma in una diversa e assai singolare prospettiva di utilizzo. Tuttavia, vale la pena qui ancora una volta rimarcare l’imponenza dell’attività svolta, sotto diversi aspetti: logistico, gestionale, organizzativo, professionale, costruttivo e della sicurezza nelle diverse lavorazioni, la maggior parte svolte simultaneamente. Attività che ha coinvolto, giocoforza, tutto il sistema infrastrutturale lombardo, compresi gli altri scali aerei regionali, primo fra tutti l’aeroporto di Milano Malpensa. L’intervento di riqualifica dell’infrastruttura di Linate rientra in un più ampio programma di riqualificazione dello scalo aeroportuale milanese pianificato da SEA con il coordinamento di ENAC; ciò ha ovviamente richiesto uno sforzo fuori dall’ordinario da parte di tutti gli attori impegnati in tali attività, dalla fase di ideazione sino al 27 Ottobre 2019, giorno di riapertura dello scalo. Un elemento da evidenziare in questo contesto, che tuttavia rimane lontano dalle luci dell’opinione pubblica a cui prima si faceva cenno, è relativo ad alcuni aspetti caratterizzanti il progetto delle pavimentazioni a servizio delle movimentazioni a terra degli aeromobili, in grado di coniugare una elevata sostenibilità ambientale dei materiali utilizzati alle attese prestazionali tipiche del contesto aeroportuale. Va da sé che il progetto rimane solo sulla carta se non trova poi debito compimento in fase di realizzazione. È proprio il contesto realizzativo il focus di questo articolo, nel quale verranno messe in evidenza le peculiarità dei materiali di riciclo e di recupero
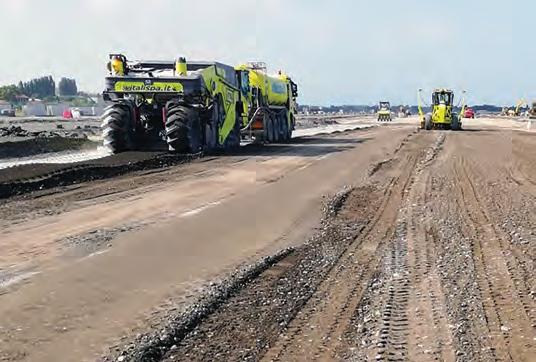
1. Le operazioni di cantiere per la stabilizzazione a cemento in sito
pavimentazioni &manti
utilizzati per la produzione di nuove miscele, nonché le verifiche preliminari, i controlli in corso d’opera e i riscontri a fine lavori che hanno permesso di valutarne qualità e prestazioni in tutto l’iter realizzativo. In tal senso, va sottolineato come ciò abbia permesso all’intervento di riqualifica di incardinarsi compiutamente nei grandi obiettivi propri dell’economia circolare che, a diversi livelli, sia la società civile sia la politica ritengono oramai non più procrastinabili per un uso consapevole e sostenibile delle risorse disponibili.
I MATERIALI INNOVATIVI E DI RICICLO PER LE NUOVE PAVIMENTAZIONI
L’intervento di riqualifica strutturale delle pavimentazioni delle aree di movimentazione a terra dei velivoli ha riguardato la Runway 18/36, la Taxiway T, oltre ad altri interventi finalizzati a riorganizzare opportunamente gli innesti tra la pista e le taxiway, nonché alcune aree dei piazzali di stazionamento dei velivoli. Tranne quest’ultimo intervento, realizzato con pavimentazione rigida, tutti quelli appena richiamati sono stati realizzati con pavimentazione in conglomerato bituminoso. In totale, la superficie ripavimentata è stata pari a circa 210.000 m2, di cui circa 10.500 m2 in lastre di calcestruzzo. Come anticipato e come previsto dal progetto, l’intero intervento di riqualifica è stato effettuato con il duplice obiettivo di: • massimizzare l’impiego del materiale presente in sito, riciclando i prodotti della demolizione, e utilizzare materiali alternativi a quelli naturali, limitando al minimo l’impatto ambientale dell’intervento; • mantenere alti gli standard qualitativi dei materiali e delle miscele, per ottenere prestazioni delle pavimentazioni adeguate all’ambito aeroportuale, conservandole nel tempo. Con riferimento alle pavimentazioni in conglomerato bituminoso, che hanno costituito la gran parte delle pavimentazioni di nuovo impianto, per ovvie ragioni tecniche ed economiche, il progetto ha previsto profondità e caratteristiche di intervento differenziate e graduate in funzione delle richieste prestazionali in relazione alle direttrici di percorrenza dei velivoli. In altre parole, sia per le taxiway che per la runway sono stati definiti pacchetti di pavimentazioni via via più profondi e performanti andando dai margini verso il centro dell’infrastruttura di volo. Nella fascia centrale di dette infrastrutture, il pacchetto di pavimentazione in conglomerato bituminoso è stato realizzato mediante 30 cm di fondazione ottenuta con la tecnica della stabilizzazione a cemento in sito, 25 cm di sottobase in misto cementato riciclato prodotto in impianto; 25 cm di conglomerato bituminoso, diviso in tre strati (12 cm di strato di base, 7 di strato di binder e 6 di strato di usura). Orbene, tutti gli strati componenti il pacchetto di pavimentazione appena richiamato sono stati realizzati con materiali aventi elevate caratteristiche di sostenibilità ambientale. Ciò vale ovviamente anche per tutti gli altri delle fasce esterne a quella centrale dell’infrastruttura di volo, che, nella sostanza, se ne sono differenziati solo per il minor spessore di intervento o per la diversa combinazione degli strati sopra richiamati. Nel dettaglio dei materiali, la scelta di utilizzare la tecnica della stabilizzazione a cemento in sito per la formazione dello strato di fondazione (Figura 1) ha consentito di riutilizzare il materiale presente, senza movimentarlo dalla sede originaria, ma contestualmente incrementandone la valenza strutturale. Tale tecnologia è nota allo stato della tecnica, oramai di largo uso nel settore infrastrutturale, anche in ambito aeroportuale, consolidata e in grado di garantire prestazioni dei materiali del tutto analoghe a quelle di miscele da impianto. Tra i vantaggi di tale tecnica, anche e soprattutto per applicazioni aeroportuali, vanno sicuramente annoverati la velocità di realizzazione e il conseguente incremento di produttività, se confrontata con la produzione in impianto di miscele con prestazioni comparabili, nonché l’impiego di materiali di riciclo al 100%. Quanto sopra è peraltro ampiamente confermato da una corposa e consolidata letteratura tecnica e scientifica di settore [1-4]. Anche nel caso dell’impiego di aggregati di riciclo per la formazione di strati di sottobase in misto cementato vi è un’ampia e consolidata letteratura tecnico-scientifica, che ne garantisce i vantaggi ambientali, coniugandoli a risultanze prestazionali non inferiori a quelle di miscele con aggregati di nuovo utilizzo [5-10]. Nel caso dell’intervento di Linate, il progetto prevedeva che il 90% in peso degli aggregati fosse di riciclo e il 10% da aggregato di primo impiego. In fase realizzativa, a valle delle puntuali verifiche condotte sui materiali, si è potuto estendere al 100% il riciclo di aggregati provenienti dalle demolizioni di cantiere, in particolare utilizzando il fresato ottenuto dalla rimozione dei preesistenti strati in conglomerato bituminoso (15% in peso, rispetto al peso totale della miscela legata), il calcestruzzo derivante dalla demolizione delle lastre delle testate di pista (41%), il macadam ottenuto a seguito della rimozione dello strato in misto bitumato esistente (40%), oltre al cemento (4%). Ovviamente tutti i materiali appena menzionati sono stati sottoposti a operazioni di frantumazione, rimozione di ferri d’armatura, ove presenti, e vagliatura per ottenere pezzature omogenee, poi opportunamente proporzionate per rispondere alle richieste progettuali (fuso granulometrico). In Figura 2 è riportata un’immagine delle fasi di posa in opera dello strato in misto cementato riciclato in impianto. Anche gli strati di base e binder in conglomerato bituminoso sono stati caratterizzati da un’elevata valenza ambientale, giacché, come previsto dal progetto, sono stati realizzati utilizzando fresato rispettivamente in misura del 30% e del 20% in peso. In questo caso, non è necessario invocare, a supporto, letteratura tecnica specifica, poiché sia il tipo di materiale di riciclo, sia i quantitativi definiti nel progetto, sono oramai da considerarsi pratica corrente.

2. Le operazioni di cantiere per la formazione dello strato in misto cementato riciclato in impianto
PAVIMENTAZIONI AEROPORTUALI
Di particolare interesse è la soluzione adottata per lo strato superficiale di usura, per il quale il progetto non prevedeva l’impiego di fresato e poneva limiti stringenti sia con riferimento alle resistenze e alla forma dell’aggregato grosso, sia alla tessitura superficiale dello strato finito. Per tale motivo, la scelta, rivelatasi prima sfidante e poi vincente, è stata quella di coniugare le prestazioni dell’aggregato con la sostenibilità ambientale della soluzione. La scelta è ricaduta sull’impiego di aggregati artificiali derivanti dall’industria della produzione dell’acciaio, in parziale sostituzione dei classici aggregati naturali da cava (tipicamente basalti o porfidi). Ciò rappresenta un elemento abbastanza nuovo dal punto di vista tecnico in Italia, benché la letteratura scientifica disponibile a livello internazionale da tempo ne studi l’impiego nelle miscele bituminose, sempre con ottimi risultati [11-16]. Nel dettaglio delle scelte relative all’intervento di Linate, come riportato in Figura 3, sono state utilizzate due diverse pezzature di aggregato artificiale (8/16 e 4/8), raggiungendo un’ottimizzazione di tali pezzature in corrispondenza del 36% in peso sul totale del mix di aggregati (in combinazione con le altre di origine naturale). Ciò è stato possibile anche a valle di verifiche preliminari relative alla resistenza di tali aggregati. Infatti, misure di laboratorio hanno evidenziato un Coefficiente Los Angeles inferiore al massimo ammesso dalle prescrizioni capitolari, ma soprattutto come tale materiale abbia prestazioni comparabili, se non addirittura migliori, rispetto a quello naturale da cava, peraltro potendo garantire una maggior costanza delle prestazioni nel tempo, essendo di origine industriale e dunque maggiormente controllato. Altri approfondimenti su tali aggregati artificiali hanno riguardato la forma, poiché risulta essenziale ai fini dell’altro elemento cardine del progetto dello strato di usura ovvero la tessitura superficiale, tant’è vero che il progetto ha previsto un tappeto d’usura dotato di elevata macrotessitura, per questo denominato “a tessitura ottimizzata”. Bene, le verifiche rispetto alla frantumazione e ai coefficienti di forma e appiattimento sono risultate abbondantemente entro le richieste di progetto, ma soprattutto, per effetto della derivazione industriale di tali aggregati, è stato possibile fare affidamento su materiali poliedrici e regolari (caratteristica importante sia per l’ingranamento e la mutua collaborazione dei grani all’interno della miscela, sia per la formazione della tessitura superficiale), nonché di superficie scabra (quindi particolarmente adatta a legare con il bitume e a garantire la tessitura superficiale dell’aggregato necessaria alla corretta interazione tra pneumatico e pavimentazione, a base della formazione del fenomeno dell’aderenza). Quindi, tali aggregati si sono confermati una scelta vincente per ottimizzare le prestazioni funzionali della superficie della pavimentazione, sia in termini di macro tessitura, per effetto della forma poliedrica regolare, sia in termini di micro tessitura, per effetto della scabrezza superficiale. Visto l’impiego in campo aeroportuale e considerata la derivazione dall’industria dell’acciaio di tali aggregati artificiali, è stato ritenuto necessario inda-
gare se l’utilizzo di detti aggregati potesse avere effetti indesiderati su aspetti tradizionalmente non valutati nel caso di impiego di materiali di origine naturale. In ragione di ciò, come si dirà in seguito, sono stati condotti approfondimenti in relazione a eventuali rischi di interferenza elettromagnetica con apparecchiature elettriche ed elettroniche di uso aeroportuale. Anche la realizzazione delle pavimentazioni rigide ha avuto una forte connotazione di sostenibilità ambientale. Infatti, gli aggregati per produrre i calcestruzzi sono stati ottenuti mediante processi di demolizione, macinazione, selezione e vagliatura in pezzature dei calcestruzzi da demolizione, principalmente derivanti dalle vecchie testate della pista di volo e dalla Taxiway T. Ovviamente, gli aggregati così ottenuti e divisi per pezzatura sono stati successivamente ricombinati per rispondere alle prescrizioni di progetto (fuso granulometrico). In definitiva, per quanto appena descritto, tutte le diverse tipologie di pavimentazioni utilizzate per la riqualifica strutturale dell’Aeroporto di Milano Linate, nonché le scelte dei materiali impiegati per la formazione dei singoli strati delle suddette pavimentazioni, sono state effettuate avendo come obiettivo sia la massimizzazione dei benefici ambientali associati al loro impiego sia la garanzia di prestazioni elevate dei pacchetti in ragione delle specificità dell’ambito aeroportuale. La sfida è stata di attuare in concreto un approccio non più basato sulla provenienza del materiale impiegato, ma sulle caratteristiche dello stesso in relazione alle prestazioni attese per il materiale posto in opera: una concreta applicazione di un approccio prestazionale per la verifica di rispondenza dei prodotti finiti.
In un contesto come quello dell’intervento di riqualifica strutturale delle aree di manovra e decollo dell’Aeroporto di Linate, il controllo delle prestazioni dei materiali e delle miscele ha costituito, quindi, uno snodo fondamentale nel corso dell’intero iter realizzativo. Ciò almeno per due ordini di ragioni. Da un lato, massima attenzione doveva esser posta nella verifica puntuale e sistemica delle prestazioni attese, in considerazione sia della severità delle future condizioni di carico in esercizio, sia del fatto che, come illustrato in precedenza, la sfida ha riguardato il raggiungere tali prestazioni mediante una forte componente di sostenibilità ambientale. Dall’altro lato, il controllo in corso d’opera doveva esser caratterizzato da efficacia e rapidità, in modo da supportare con riscontri oggettivi le scelte della Direzione Lavori e le verifiche di rispondenza della Commissione di Collaudo incaricata da ENAC. Con specifico riferimento a questo ultimo aspetto, in primo luogo, era necessario assicurare alla Direzione Lavori un immediato ritorno sulla coerenza delle scelte adottate rispetto alle previsioni attese, ma, al contempo, non essere di ostacolo 3. Gli aggregati artificiali di acciaieria utilizzati per lo all’evoluzione delle attività di cantiere, strato di usura in ragione del comunque breve tem-
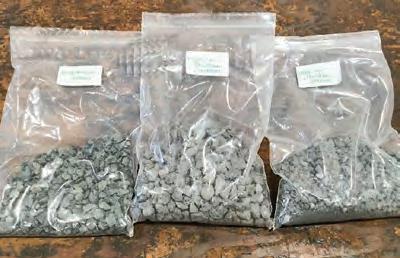
pavimentazioni &manti
po a disposizione per portare l’opera a compimento. In secondo luogo, il controllo in corso d’opera doveva dare riscontri oggettivi alla Commissione di Collaudo incaricata da ENAC sia per l’accertamento dell’agibilità delle opere finali, sia per il monitoraggio in continuo delle caratteristiche dei materiali posati in opera. In questo modo, è stato possibile fornire evidenze, costruite step by step, inerenti alla rispondenza dell’opera non solo alle previsioni di progetto, ma anche ai requisiti tecnici e regolamentari applicabili. Questa impostazione, stabilita all’inizio con i Professionisti ENAC facenti parte della Commissione, ha consentito di poter ottenere, in tempo per la data fissata per la riapertura, l’attestazione di agibilità delle opere. Per i motivi appena esposti è stato elaborato un piano di controllo che, nel rispetto delle prescrizioni del progetto, fosse in grado di rispondere compiutamente e velocemente alle necessità appena descritte. A base di tale piano è stato posto il consolidato schema di indagine diviso in quattro fasi principali: prequalifica di laboratorio dei materiali e delle miscele prima dell’inizio lavori; riscontro in vera grandezza mediante campi prova; controllo durante lo svolgimento dei lavori; verifica finale, al termine dei lavori medesimi. L’organizzazione del piano di controllo nelle diverse fasi appena menzionate ha previsto il coinvolgimento di due diversi laboratori. Per l’Impresa ha operato il Laboratorio Geothema, garantendo la propria presenza mediante l’impiego di laboratorio mobile a supporto del laboratorio fisso situato in provincia di Venezia. In aggiunta, la Committenza, data la natura molto particolare dell’intervento, ha inteso affidare una attività di Alta Sorveglianza al Laboratorio Sperimentale Infrastrutture di Trasporto del Dipartimento di Ingegneria Civile e Ambientale del Politecnico di Milano (InfraLab@PoliMI - Responsabili di Commessa Prof. E. Toraldo e Ing. E. Mariani). InfraLab ha operato in cantiere con una propria unità mobile per le prove in sito e con il proprio laboratorio fisso presso il Politecnico di Milano per quelle di laboratorio, ciò anche in ragione della prossimità con l’aeroporto. Questo ha permesso di agevolare le attività di costruzione, in virtù della celerità di risposta rispetto ad alcuni riscontri prestazionali, non effettuabili su laboratori mobili. Dal punto di vista operativo, i due laboratori hanno condotto attività parallele; InfraLab ha effettuato prove in sovrapposizione a quelle realizzate dal laboratorio incaricato dall’Impresa esecutrice, a cui è stato comunque deputato l’onere di eseguire tutte le indagini previste dalle prescrizioni capitolari. Nella sostanza, è stato messo in piedi un sistema ridondante a doppio controllo che, a seconda dei casi e delle esigenze via via presentatesi, ha visto i due laboratori eseguire la stessa numerosità di prove (come nel caso dei campi prova), oppure il laboratorio di Alta Sorveglianza effettuare almeno il 30% delle prove previste dal progetto, per le attività di controllo in corso d’opera e finali. Ovviamente, la copertura dei due laboratori nel corso della fase realizzativa è stata di 24 ore al giorno e sette giorni su sette. A questo doppio controllo inerente l’esecuzione del piano prove previsto dal progetto, si sono aggiunte le verifiche puntuali richieste dalla Commissione di Collaudo. In questo modo, la Commissione aveva, a campione, un ritorno sulla rispondenza dei materiali a conferma delle attività di indagine svolte in contraddittorio dai laboratori incaricati dall’Appaltatore e dalla Direzione Lavori.
I CONTROLLI PRELIMINARI
Per quanto attiene alla prequalifica delle miscele prima dell’inizio dei lavori, va fatta una differenziazione in ragione del tipo di strato. Infatti, se per quanto riguarda le miscele bituminose, i misti cementati e i calcestruzzi è stato possibile valutare la qualità dei materiali componenti e delle miscele prima dell’inizio delle lavorazioni, durante la fase di demolizione, una volta ottenute i materiali di riciclo in quantità tali da essere rappresentativi, lo stesso non è stato possibile fare per lo strato di fondazione stabilizzato a cemento. Infatti, il campo prova per la fondazione, direttamente eseguito in area di cantiere, è stato anche il primo banco di prova per la verifica delle prestazioni delle miscele e per l’ottimizzazione del contenuto di acqua e cemento. Ciò perché tale strato di fondazione è stata la prima lavorazione ad iniziare, con scorrimento temporale minimo rispetto alla fase di demolizione, sempre per effetto delle strette tempistiche di cantiere. Per le miscele bituminose, la fase di prequalifica ha previsto l’ottimizzazione del contenuto di legante e la verifica di rispondenza alle prestazioni richieste dal progetto, mediante indagini di laboratorio. Per le miscele di base e binder, si è dato inizio a tali indagini appena avuta la disponibilità del conglomerato bituminoso derivante dalla fresatura delle vecchie pavimentazioni. Tale onere di prequalifica delle miscele, di competenza dell’Impresa, ha previsto prove solo per il laboratorio Geothema. La successiva verifica in vera grandezza, con miscele prodotte in impianto, è stata eseguita con ovvio e congruo anticipo rispetto all’inizio delle lavorazioni, presso un sito messo a disposizione a Mozzo (BG) da parte dell’Impresa esecutrice. In tale attività di verifica sono stati coinvolti entrambi i laboratori, che hanno eseguito in doppio le stesse indagini sperimentali, secondo il principio di ridondanza su cui è stato basato il sistema dei controlli. Tali indagini hanno ovviamente riguardato sia i materiali componenti (aggregati e bitume), sia le miscele (caratterizzazione composizionale, volumetrica e meccanica), sia le stese di prova (addensamento e prestazioni meccaniche). Stessa metodologia è stata utilizzata sia per i misti cementati, sia per calcestruzzi, con l’unica differenza che essendo entrambi materiali prodotti in impianti posizionati direttamente in aeroporto, le indagini in vera grandezza sono state effettuate su un’area del sedime aeroportuale appositamente individuata. Sempre in ambito di prequalifica delle miscele e campi prova, è da sottolineare che un’attenzione particolare è stata rivolta all’analisi dello strato di usura e, in particolare, degli aggregati artificiali in esso impiegati. Infatti, come anticipato, detti aggregati artificiali sono stati oggetto di approfondimenti con un doppio obiettivo: in primo luogo accertare se l’origine artificiale degli aggregati potesse avere un impatto in termini di interferenze elettromagnetiche rispetto agli apparati di radionavigazione; in secondo luogo, acquisire le caratteristiche del materiale così da ottenere dati di dettaglio utili a valutare nel tempo le prestazioni dei conglomerati posti in opera. Quest’ultimo aspetto è stato ritenuto essenziale per una corretta calibrazione del comportamento di questi materiali all’interno del Pavement Management System, con l’obiettivo finale di gestire la manutenzione del sistema in modo efficace. Per quanto riguarda l’approfondimento sul comportamento magnetico, questo è stato effettuato avvalendosi di prove specifiche e mirate.
PAVIMENTAZIONI AEROPORTUALI

4. Esempio di report di prova emesso dal Laboratorio Sperimentale Infrastrutture di Trasporto del Politecnico di Milano
Tali prove sono state affidate al Laboratorio di Compatibilità Elettromagnetica del Dipartimento di Elettronica, Informazione e Bioingegneria del Politecnico di Milano. In particolare, sono state sottoposte a prova comparativa le due pezzature di aggregato artificiale (pezzature 8/16 e 4/8) da utilizzarsi in cantiere e un basalto (5/10), come termine di paragone. Nel dettaglio, le prove hanno riguardato la verifica sperimentale di due proprietà: l’emissione permanente di campo di induzione magnetica statico e il possibile comportamento ferromagnetico. In estrema sintesi, dalle indagini effettuate è emerso che tali aggregati artificiali non comportano rischi di interazione elettromagnetica con apparecchiature elettriche ed elettroniche di utilizzo aeroportuale. Ciò perché nelle indagini sperimentali è stato possibile appurare quanto di seguito descritto brevemente per punti: • gli aggregati artificiali analizzati sono un pessimo conduttore elettrico; • è stato rilevato un debole campo statico di induzione magnetica in prossimità dei grani, che di per sé evidenzia solo la presenza diossidi ferrosi e la cui entità è inferiore a quella rilevabile per altri elementi da costruzione dell’ingegneria civile (per esempio ferri di armatura); • il campo magnetico è debole e orientato in modo incoerente, per effetto della forma granulare degli aggregati, ciò comporta che, a 3 cm di distanza dagli aggregati artificiali, il campo magnetico sia pressoché non rilevabile e circa pari a quello del basalto; • campi magnetici esterni non magnetizzano gli aggregati artificiali. A questo va naturalmente aggiunta la considerazione che la miscela per strato di usura è composta per circa il 36% in peso da aggregati artificiali e la restante parte degli aggregati è di natura litica, con conseguente diminuzione dei già deboli effetti elettromagnetici. Per quanto riguarda l’acquisizione dei dati sulle caratteristiche prestazionali, detti materiali di origine artificiali sono stati sottoposti ad un set di prove di caratterizzazione ampio, condotto, secondo le tecniche standard di laboratorio, sia sul materiale tal quale sia sul conglomerato prodotto. In definitiva, le indagini preliminari svolte in laboratorio e nei diversi campi prova hanno permesso di qualificare i materiali componenti e le relative miscele preventivamente al loro utilizzo, confermandone la qualità in termini di prestazioni, anche se caratterizzati da una forte valenza di ecosostenibilità, sgomberando anche il campo da qualsiasi dubbio sulla possibilità di impiego di aggregati artificiali da acciaieria in ambito aeroportuale.
I CONTROLLI IN CORSO D’OPERA
Come anticipato, verifica puntuale e sistemica delle prestazioni unitamente a efficacia e rapidità di riscontro oggettivo per la Direzione Lavori sono stati gli elementi che hanno guidato le scelte nella definizione del piano dei controlli in corso d’opera, ovviamente nel rispetto delle prescrizioni progettuali. Per ottenere ciò, è stata studiata un’organizzazione delle prove che fosse il più possibile aderente con l’evoluzione delle attività di cantiere. In particolare, per ogni strato, data la frequenza di prova definita dal progetto (per esempio, una prova ogni 5.000 m2 di superficie lavorata), l’intera superficie di intervento è stata divisa in aree più piccole, conformate in modo tale da ricalcare le effettive modalità operative. In altri termini, si è scelto di avere aree strette (che comprendessero un numero limitato di strisciate di lavorazioni contigue e, quindi, effettuate in un arco di tempo breve) e lunghe, piuttosto che aree di larghezza pari a quelle dell’intero intervento ma più corte (comprendendo così strisciate di lavorazioni effettuate anche a diversi giorni di distanza). In questa maniera, è stata resa agevole e univoca l’individuazione sul campo di eventuali anomalie dei materiali e/o errori di lavorazione, nonché il riscontro rispetto alla data di posa e all’ubicazione della lavorazione. In Figura 4 è riportato un esempio di report di prova emesso dal Laboratorio Sperimentale Infrastrutture di Trasporto (Infralab) del Politecnico di Milano, nel caso di specie relativo alle prove di carico con piastra su misto cementato riciclato prodotto in impianto, con indicazione dell’ubicazione della prova, dei risultati ottenuti, della data di prova e del tempo di maturazione intercorso tra la realizzazione dello strato e l’esecuzione della prova. Per maggior chiarezza, le diverse colorazioni indicano diverse stratigrafie delle pavimentazioni, le aree contornate con linea bianca indicano le aree di prova necessarie a soddisfare le frequenze previste dal progetto. A riscontro della ridondanza del programma di controlli è possibile far riferimento alla Figura 5, suddivisa tra le attività di controllo effettuate nel corso delle lavorazioni e quelle al termine delle medesime. In tabella, per ogni strato/miscela, è riportato il numero di prove necessarie a rispettare le frequenze definite dal progetto, il numero di prove realizzate, la ridondanza (espressa come rapporto percentuale tra la differenza tra prove effettuate e quelle richieste, fratto il numero di prove richieste) e una breve descrizione delle tipologie di prove prescritte dal progetto. In realtà, il numero di controlli è stato maggiore di quelle riportate in Tabella poiché non sono stati conteggiati quelli effettuati sulle aree non direttamente coinvolte dal transito ordinario dei velivoli (per esempio shoulders), le prove realizzate per verifiche immediate e locali, nonché alcune delle prove sui materiali componenti.
pavimentazioni &manti
Orbene, dalla tabella si evince come la numerosità delle prove sia stata superiore a quella imposta dalle frequenze definite dal progetto, proprio per effetto di quel principio di ridondanza definito in fase di programmazione del piano di controllo. La ridondanza media è stata pari al 39% per entrambe le attività di controllo (in corso d’opera e a fine lavori). Qui si fa notare come nel caso della misura degli spessori delle lastre in calcestruzzo la ridondanza sia stata nulla: ciò è derivato semplicemente dal fatto che tali lastre costituiscono riqualificazione di pavimentazione rigida preesistente. Quindi essendo imposti i piani di appoggio delle nuove lastre e la loro quota finale, perché in continuità con l’esistente, non si è ritenuto di procedere con approfondimenti maggiori rispetto a quelli previsti dal progetto, onde evitare inutili disturbi alla pavimentazione derivanti da un eccesso di carotaggi, oltre ovviamente a contenere tempi e costi delle prove. In questo quadro, le verifiche condotte dalla Commissione di Collaudo ENAC, con specifico riferimento alle prestazioni delle miscele posate in opera, sono state eseguite per ulteriore conferma rispetto ai dati ottenuti in contraddittorio dai due laboratori. Tali verifiche hanno riguardato gli aspetti composizionali e
STRATO/MISCELA
NUMERO CAMPIONAMENTI PREVISTI DA PROGETTO
NUMERO CAMPIONAMENTI EFFETTUATI DURANTE I LAVORI PERCENTUALE RIDONDANZA PRINCIPALI PROVE DA PROGETTO
Attività di controllo in corso d’opera
Fondazione in misto cementato stabilizzato in sito
Sottobase in misto cementato da impianto
Strato di Base in conglomerato bituminoso
Strato di Binder in conglomerato bituminoso 26
20
49
33
34
37
Strato di Usura in conglomerato bituminoso 40
Lastre in calestruzzo 36
Carotaggi strati in conglomerato bituminoso
Prove superficiali pavimentazioni in conglomerato bituminoso Carotaggi lastre in calcestruzzo
Prove superficiali lastre in calcestruzzo 41
41
16
16 45
26
76
48 +73% Prove in sito: • carico su piastra +30% • umidità
+55%
+45% Prove in laboratorio: • composizionali (granulometria, contenuto di legante) • meccaniche (resistenza a compressione e a trazione indiretta)
45
49
52 +32%
+32%
+30% Prove in laboratorio: • materiali componenti: • bitume (penetrazione, temperatura di rammollimento, viscosità dinamica) • aggregati (Los Angeles, coeff. di forma e appiattimento, percentuale di frantumazione) • miscele: • composizionali (granulometria, contenuto di legante) • volumetriche (evoluzione dello stato di addensamento con pressa giratoria; contenuto dei vuoti con PG e Marshall) • meccaniche (rigidezza a tre temperature, resistenza a trazione indiretta, stabilità Marshall)
42
+17% Prove in laboratorio: Resistenza a Compressione su cubetti Attività di controllo a fine lavori
49
66
16
22 +20%
+61% Prove in laboratorio: spessore totale, spessore degli strati, contenuto di vuoti e resistenza a trazione indiretta degli strati Prove in sito: altezza in sabbia e British Pendulum Number
0 Prove in laboratorio: spessore +38% Prove in sito: altezza in sabbia e British Pendulum Number
5. Il quadro riassuntivo dei controlli in cantiere
le caratteristiche volumetriche e meccaniche dei conglomerati bituminosi posati in opera (in particolare dello strato di usura), nonché il controllo, mediante carotaggi, degli spessori e delle resistenze meccaniche dei diversi strati in conglomerato bituminoso. Tali prove sono state condotte dal Laboratorio Sperimentale Infrastrutture di Trasporto del Politecnico di Milano.
I CONTROLLI A FINE LAVORAZIONI
I controlli a fine lavorazioni, oltre a quanto effettuato dai laboratori impegnati nelle fasi di cantiere e riportato in Figura 5, sono stati ulteriormente ampliati mediante attività volte a caratterizzare le prestazioni delle pavimentazioni finite, includendo anche l’utilizzo di prove ad alto rendimento. Per la verifica della portanza, e della conseguente rispondenza del parametro ACN/PCN ai dati progettuali, è stata effettuata una campagna di misure con Heavy Weight Deflectometer (HWD). Per le pavimentazioni in conglomerato bituminoso, le prove HWD sono state condotte lungo sette allineamenti delle infrastrutture di volo, in corrispondenza della center line e a ±3,0 m, ±6,0 m, ±12,0 m dalla center line medesima, in modo da coprire uniformemente l’area di maggior probabilità di passaggio degli aeromobili. Il passo di misura è stato di un punto di battuta ogni 100 m circa, con sfalsamento longitudinale tra punti di misura adiacenti, ma appartenenti a due diversi allineamenti, quindi con disposizione a quinconce. La verifica finale di portanza e della compatibilità ACN/PCN sulle pavimentazioni rigide è stata effettuata sempre con misure HWD, con almeno una battuta per lastra; inoltre, è stata verificata l’efficienza di trasferimento dei carichi su almeno il 20% dei giunti. Prove ad alto rendimento sono state eseguite anche per la verifica della regolarità e della tessitura superficiale delle pavimentazioni in conglomerato bituminoso, combinando le stesse con prove di determinazione del coefficiente di aderenza attraverso l’utilizzo della tecnologia GRID-TESTER. La verifica di regolarità ha previsto anche il rilievo del profilo delle pavimentazioni con ARAN, da cui è stato conseguentemente calcolato il parametro IRI su base 100 m, verificando che fosse non superiore a 2 m/km. Per la verifica della macrotessitura è stato misurato, mediante rilievo con profilometro laser, il parametro MTD, appurando che fosse superiore a 1,14 mm. Entrambe le prove ad alto rendimento appena richiamate sono state condotte seguendo gli stessi allineamenti longitudinali previsti per la prova di portanza. L’elevata numerosità delle tipologie di controlli eseguiti a fine lavori ha consentito di ottenere una raccolta di dati sperimentali consistente e utile sotto vari punti di vista, soprattutto per costituire una base del PMS dello scalo. In estrema sintesi, le prove puntuali di controllo finale effettuate dai laboratori incaricati da Impresa e SEA sui materiali posati in opera e sulle caratteristiche superficiali delle pavimentazioni, nonché le prove ad alto rendimento di portanza e di regolarità/ tessitura superficiale, hanno permesso di valutare compiutamente lo stato dell’opera finita, permettendo così alla Commissione di Collaudo di poter accertare l’agibilità delle infrastrutture oggetto di riqualifica nei tempi e nei modi stabiliti, e al Gestore di avere a disposizione, una volta ottenute le necessarie autorizzazione per la riapertura al traffico aereo, i dati per monitorare efficacemente le prestazioni delle pavimentazioni lungo l’arco della vita utile delle stesse.
CONCLUSIONI
Sostenibilità ambientale e prestazioni delle pavimentazioni adeguate all’ambito aeroportuale sono stati i cardini del progetto e del successivo iter realizzativo della riqualificazione strutturale delle principali aree di movimentazione dei velivoli (principalmente, Runway 18/36 e Taxiway T) dell’Aeroporto di Milano Linate. Ciò è stato ottenuto attraverso un attento studio e una puntuale verifica dei materiali componenti, delle miscele e delle loro prestazioni mediante un piano di indagine diviso in quattro fasi principali: prequalifica di laboratorio dei materiali e delle miscele prima dell’inizio lavori; riscontro in vera grandezza mediante campi prova; controllo durante lo svolgimento dei lavori; verifica finale, al termine dei lavori medesimi. A tale scopo, sono stati coinvolti due laboratori, Geothema per l’ATI Vitali /Artifoni che ha eseguito i lavori e il Laboratorio Sperimentale Infrastrutture di Trasporto del Politecnico di Milano, con funzione di Alta Sorveglianza per SEA. È stato quindi realizzato un sistema ridondante a doppio controllo che, a seconda dei casi e delle esigenze via via presentatesi, ha visto i due laboratori eseguire la stessa numerosità di prove (come nel caso dei campi prova), oppure il laboratorio di Alta Sorveglianza effettuare circa il 39% delle prove previste dal progetto, per le attività di controllo in corso d’opera e finali. Questa impostazione ha consentito alla Commissione ENAC incaricata del collaudo di agire in modo efficace nello svolgimento dei suoi compiti, avendo un monitoraggio in continuo della qualità dei lavori. Con riferimento alle indagini preliminari svolte in laboratorio e nei diversi campi prova, queste hanno permesso di qualificare i materiali componenti e le relative miscele preventivamente al loro utilizzo, confermandone la qualità in termini di prestazioni anche se caratterizzati da una forte valenza di eco sostenibilità, fornendo importanti conferme sulla possibilità di impiego di aggregati artificiali da acciaieria in ambito aeroportuale. Per quanto concerne i controlli in corso d’opera, è stato messo a punto un piano di indagine che permettesse di seguire l’evoluzione del cantiere e dare pronto riscontro da un lato alla Direzione Lavori in merito alla qualità e alle prestazioni dei materiali, delle miscele e delle lavorazioni e dall’altro alla Commissione ENAC per specializzare le proprie verifiche. Al termine delle attività di cantiere, le prove puntuali di controllo finale unitamente alle prove ad alto rendimento di portanza e di regolarità/tessitura superficiale (eseguite dalla società GRS per conto dell’ATI) hanno permesso di valutare compiutamente la qualità e le prestazioni dell’opera nel suo complesso. In conclusione, l’esperienza della riqualifica delle pavimentazioni delle principali aree di movimento dei velivoli presso l’Aeroporto di Milano Linate è risultata essere sfidante e vincente nel coniugare valenza ambientale e attese prestazionali. Il controllo dei materiali e delle miscele nelle diverse fasi realizzative si è rivelato uno snodo cruciale per la corretta realizzazione dell’intervento, avendo sempre l’approccio prestazionale come elemento guida e parametro di valutazione complessivo.
PAVIMENTAZIONI AEROPORTUALI
pavimentazioni &manti
Tra gli altri, gli aspetti connessi alla verifica della qualità dei materiali e delle miscele, nonché all’organizzazione del piano dei controlli, derivanti dall’esperienza di riqualifica delle infrastrutture di volo dell’aeroporto di Milano Linate, si ritiene possano essere di sicuro interesse per i Tecnici del settore e costituire best practice di riferimento per future attività. n
(1) Professionista di ENAC (2) Professore Ordinario di Costruzione di Strade Ferrovie ed Aeroporti presso il Dipartimento di Ingegneria Civile e Ambientale del Politecnico di Milano (3) Professore Associato e Responsabile Scientifico del Laboratorio Sperimentale Infrastrutture di Trasporto del Politecnico di Milano (4) Ingegnere, Responsabile Unico del Procedimento in Fase di Esecuzione di SEA Aeroporti di Milano (5) Ingegnere, Responsabile Progettazione Infrastrutture di Volo di SEA Aeroporti di Milano (6) Architetto, Direttore dei Lavori di SEA Aeroporti di Milano
Ringraziamenti
Il contributo di ENAC nella fase di esecuzione dei lavori è stato essenziale, e pertanto si ringrazia l’Ente nel suo complesso per il supporto, e in particolare i professionisti ENAC Ing. Lucia Ippoliti, Ing. Luca Sandro e Dott.ssa Federica Di Paolo, membri della Commissione di Collaudo presieduta dall’Ing. Davide Drago. Inoltre, un sentito ringraziamento al Laboratorio Sperimentale Infrastrutture di Trasporto del DICA-Politecnico di Milano, in particolare all’Ing. Edoardo Mariani, Responsabile di Commessa e delle attività di prova, e al Sig. Giovanni Lobina.
DATI TECNICI
Stazione Appaltante: SEA Aeroporti di Milano RUP in Fase di Esecuzione: Ing. Giovanni Corbo Project Manager: Ing. Eugenio Cornaggia di SEA SpA Responsabile Progettazione: Ing. Paolo Morelli di SEA SpA Project Engineer: Ing. Giuseppe Pacilli Direttore Lavori: Arch. Marco Andreula
Progetto di fattibilità tecnico-economica e progetto esecuti-
vo: RTI composta da MCI Infrastructures Engineering Srl (Mandataria), Steam Srl, Transtech Srl, Ing. Felice Boneddu e Dott. Geol. Francesco Serra
Responsabile integrazione prestazioni specialistiche e Project
Leader: Prof. Ing. Maurizio Crispino Coordinatore della Sicurezza in fase di esecuzione: Ing. Nicola Piacenza Imprese esecutrici: RTI composta da Vitali SpA e Artifoni SpA Laboratori prove: Geothema, Infralab (Politecnico di Milano) e Grs Commissione di Collaudo ENAC: Ing. Davide Drago (Presidente), Ing. Lucia Ippoliti, Ing. Luca Sandro e Dott.ssa Federica Di Paolo Alta Vigilanza ENAC: Arch. Giuseppe Ferrari
Bibliografia
[1]. R. Bahar, M. Benazzoug, S. Kenai - “Performance of compacted cement-stabilised soil. Cement and concrete composites”, Volume 26, Issue 7: 811-20.ISSN: 0958-9465, 2004. [2]. J. Abdo, J.P. Serfass, P. Pellevoisin - “Pavement cold in-place recycling with hydraulic binders: the state of the art in France”, Road Materials and Pavement Design 14(3), pp. 638-665, 2013. [3]. C. Berthelot, B. Marjerison, G. Houston, J. McCaig, S. Warrener,
R. Gorlick - “Mechanistic comparison of cement- and bituminousstabilized granular base systems”, Transportation Research Record (2026), pp. 70-80, 2007. [4]. S. Kazemian, B.B.K. Huat - “Assessment of stabilization methods for soft soils by admixtures”, CSSR 2010 - 2010 International Conference on Science and Social Research 5773714, pp. 118-121, 2010. [5]. E.A. Amarh, W. Fernandez-Gómez, G.W. Flintsch, B.K. Diefenderfer,
B.F. Bowers - “Nondestructive in situ characterization of elastic moduli of full-depth reclamation base mixtures”, Transportation
Research Record 2641, pp. 1-11, 2017. [6]. A. Bleakley, P. Cosentino - “Improving properties of reclaimed asphalt pavement for roadway base applications through blending and chemical stabilization”, Transportation Research Record (2335), pp. 20-28, 2013. [7]. A.G. Seferoğlu, M.T. Seferoğlu, M.V. Akpinar - “Experimental study on cement-treated and untreated RAP blended bases: cyclic plate loading test”, Construction and Building Materials 182, pp. 580-587, 2018. [8]. R. Soares, R. Haichert, D. Podborochynski, C. Berthelot - “Modeling in situ performance of cement-stabilized granular base layers of urban roads”, Transportation Research Record (2363), pp. 88-95, 2013. [9]. R. Taha, A. Al-Harthy, K. Al-Shamsi, M. Al-Zubeidi - “Cement stabilization of reclaimed asphalt pavement aggregate for road bases and subbases”, Journal of Materials in Civil Engineering 14(3), pp. 239245, 2002. [10]. P. Tataranni, C. Sangiorgi, A. Simone, V. Vignali, C. Lantieri, G. Dondi - “A laboratory and field study on 100% Recycled Cement Bound
Mixture for base layers”, International Journal of Pavement Research and Technology 11(5), pp. 427-434, 2018. [11]. A.S. Brand, J.R. Roesler - “Expansive and Concrete Properties of
SFS–FRAP Aggregates”, Journal of Materials in Civil Engineering 28(2): 04015126, 2016. [12]. M. Fakhri, A. Ahmadi - “Recycling of RAP and steel slag aggregates into the warm mix asphalt: a performance evaluation”, Construction and Building Materials 147: 630-638, 2017a. [13]. M. Fakhri, A. Ahmadi - “Evaluation of fracture resistance of asphalt mixes involving steel slag and RAP: susceptibility to aging level and freeze and thaw cycles”, Construction and Building Materials 157, pp. 748-756, 2017b. [14]. V.J. Ferreira, A. Saez-De-Guinoa Vilaplana, T. García-Armingol, A.
Aranda-Uson, C. Lausín-Gonzalez, A.M. Lopez-Sabiron, G. Ferreira - “Evaluation of the steel slag incorporation as coarse aggregate for road construction: technical requirements and environmental impact assessment”, Journal of Cleaner Production 130: 175-186, 2016. [15]. P. Lastra-González, M.A. Calzada-Pérez, D. Castro-Fresno, I. Indacoechea-Vega - “Asphalt mixtures with high rates of recycled aggregates and modified bitumen with rubber at reduced temperature”,
Road Materials and Pavement Design, 2017. [16]. W. Sas, A. Głuchowski, M. Radziemska, J. Dziecioł, A. Szymański -
“Environmental and geotechnical assessment of the steel slags as a material for road structure”, Materials 8(8), pp. 4857-4875, 2015.
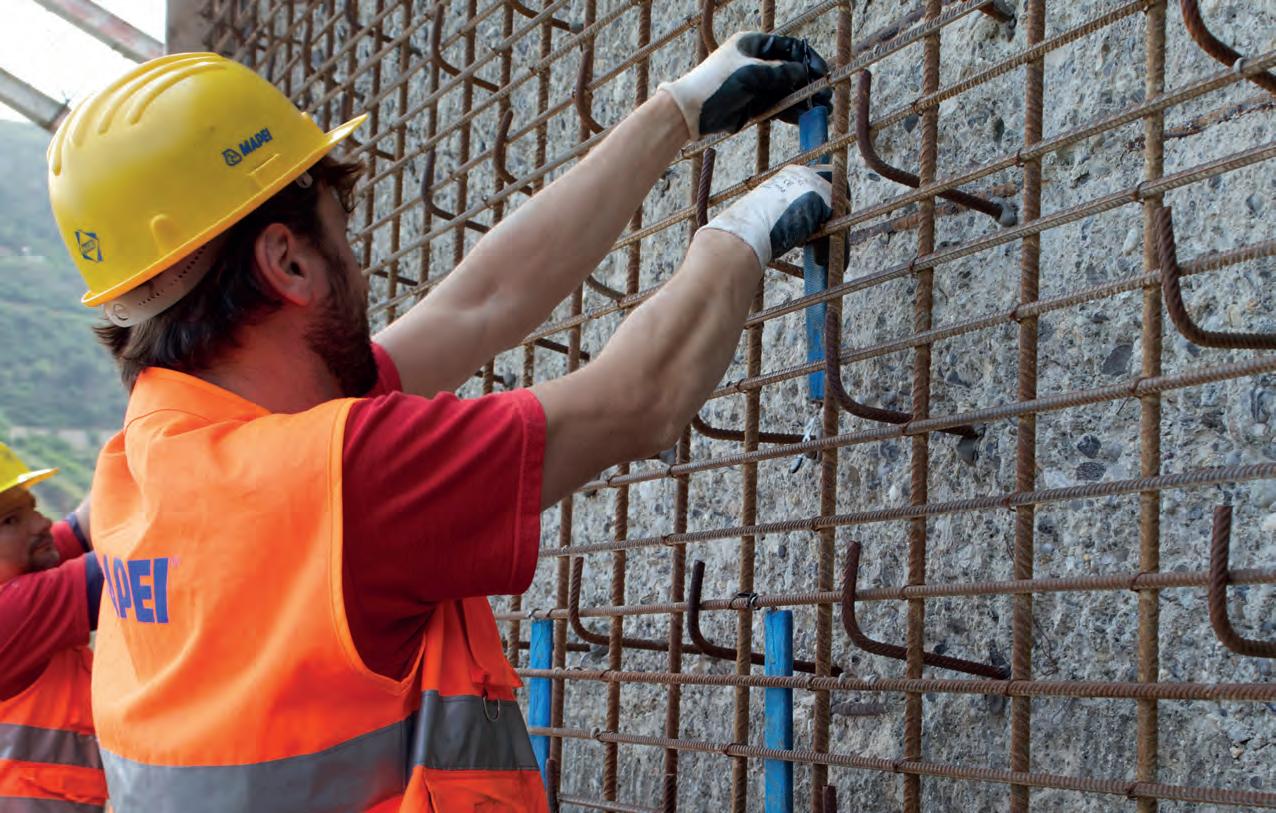
Mapeshield ®
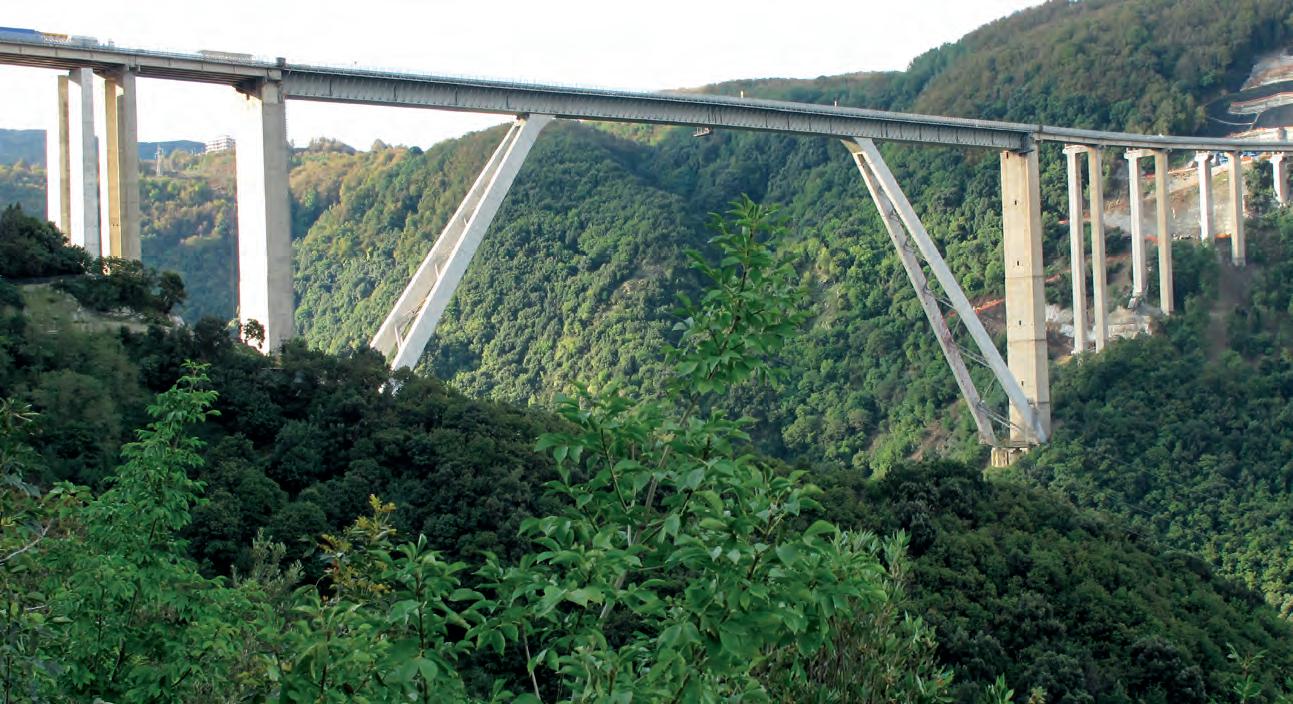