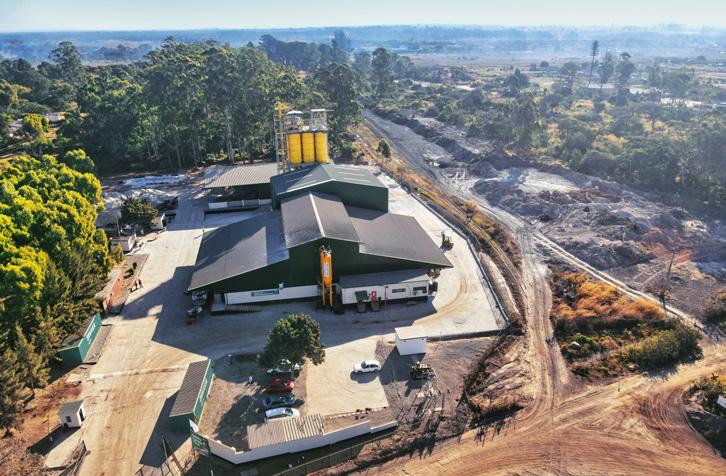
6 minute read
Lafarge’s New Dry Mortars Plant
Lafarge Cement
text by Michael Nott photos by Structure and Design
Advertisement
Zimbabwe Opens Their New Dry Mortars Plant
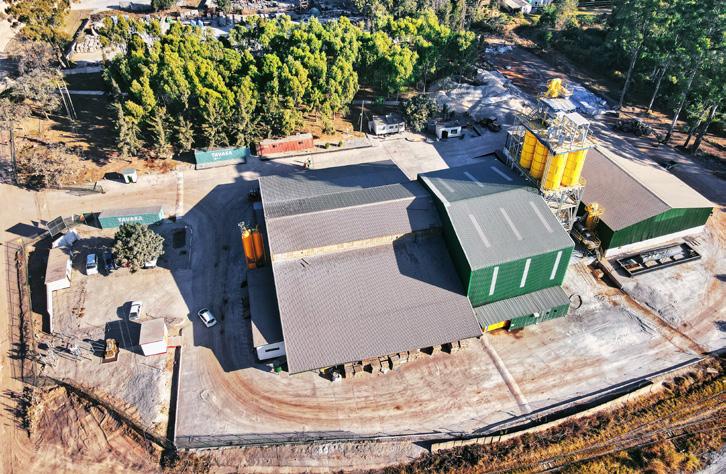
On 28th April President Mnangagwa officially opened one of Lafarge Cement Zimbabwe’s hugely ambitious three phase expansion plan projects; the Dry Mortars Plant. He was accompanied by Vice President Constantino Chiwenga, Finance and Economic Development Minister Professor Ncube and Industry and Commerce Minister Dr Nzenza.
The first stage of the three part plan, which was installed in 2019, is the 3 Megawatt alternative power generator and this Dry Mortars (DMO) plant is the second phase. The final phase, which is currently underway, is the installation of their vertical cement mill expected to come on line in January 2022. The total investment by the Swiss based Lafarge-Holcim Group will be around US$25 million, making it one of the most significant investment in industry and agriculture in recent times. This long term investment plan is a demonstration of the Lafarge-Holcim Group’s commitment to the economic recovery and development of the country and demonstrates that Lafarge-Holcim is optimistic about Zimbabwe’s future growth. The projects were awarded National Projects status by the Government of Zimbabwe.
The DMO plant will increase Lafarge’s capacity to produce dry mortar products from the current 7,000 tonnes to 100,000 tonnes per annum. The added production volumes will improve domestic supply, thereby creating leverage for import substitution and subsequently saving foreign currency. In addition, the business will also be exploring export markets.
The DMO plant manufactures cement based value added products which include pre-mixed dry mortar (just add water), tile adhesives, grouting, plasters, renders, screeds and waterproof cement all of which is packaged on site into 20 or 40 kg bags and distributed mainly through hardware stores and other outlets. Also coming out of this plant is the agricultural lime range which is a soil enhancing product. The plant can also produce customised products for specific applications.
99% of the raw materials for these new products are sourced locally with cement supplied by Lafarge, sand and aggregates sourced from their own quarries, while only around 1% of the additives are imported.
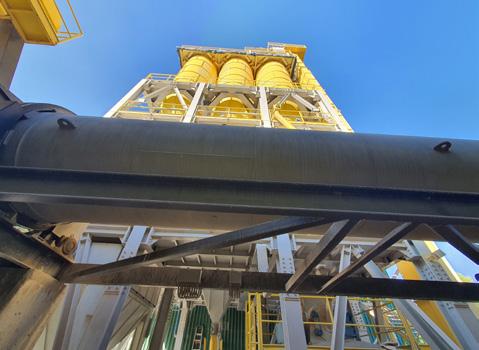
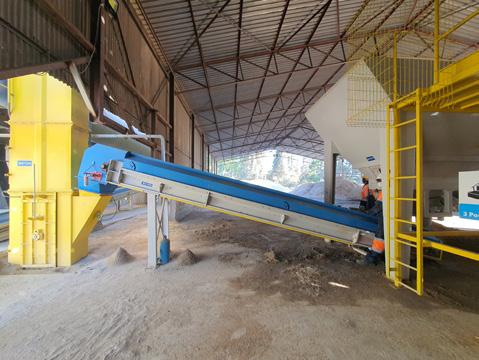
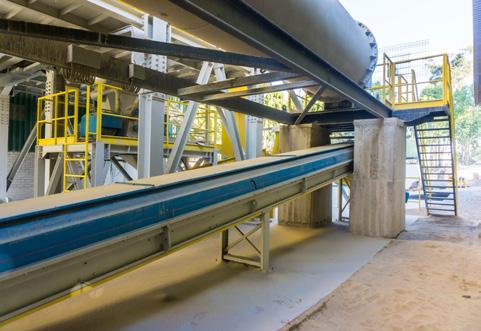
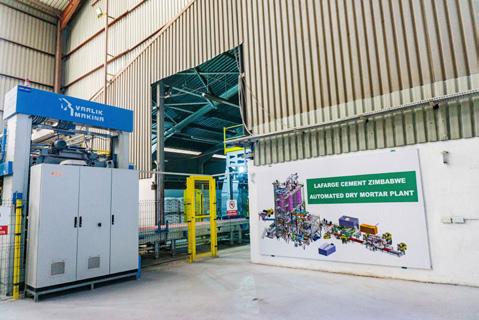




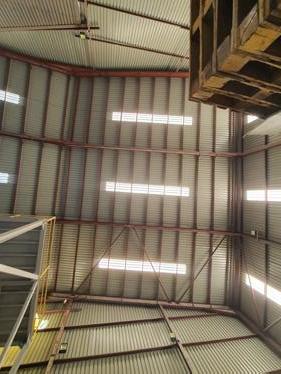
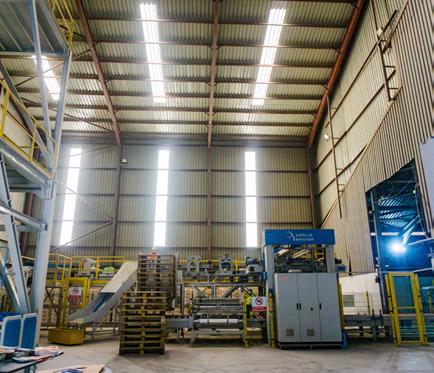

An exciting new product which the plant has the capacity to produce is the specialised mortar used in Construction 3D Printing. This new technology is set to revolutionise the construction industry across the world. It’s already being explored and developed in other countries where buildings can be created in a remarkably short time, reducing the waste often associated with construction and ensuring that the raw materials are used most efficiently. Remarkably, the superstructure of a standard house can be constructed in around 12 hours.
Lafarge chief executive officer, Mrs Precious Nyika, was quoted in The Chronicle, saying, “Imagine the difference this technology can bring to cover the infrastructure backlog we have today. We anticipate that we will receive the printer in the third quarter through a subsidiary of Lafarge-Holcim called 14 Trees and we look forward to the usual Government support in its importation and subsequent approval for use.” 14 Trees is a Lafarge-Holcim and CDC Group joint venture committed to providing affordable housing options across Africa and is already operating in Malawi and Kenya.



The DMO plant was designed and manufactured by Turkish company Varlik starting in 2019. It was shipped to Zimbabwe in April 2020 to be assembled and installed. The civil work began in May 2020 and installation was completed in December the same year. Three months of commissioning and performance testing followed before the plant was officially opened in April this year.
Four local companies were involved in the project with Sinoma Zimbabwe doing the civil and construction work, AGES as the main installation partner, GEC supplying the transformer and electrical work and WCrane supplying the specialised lifting equipment. Because of the travel restrictions brought about by the pandemic Varlik supplied remote assistance and oversight, although they did send out a small team to provide training for their Zimbabwean counterparts in the operation and maintenance of the plant. The entire installation took around 34,400 man hours and was completed without a single Health and Safety incident.
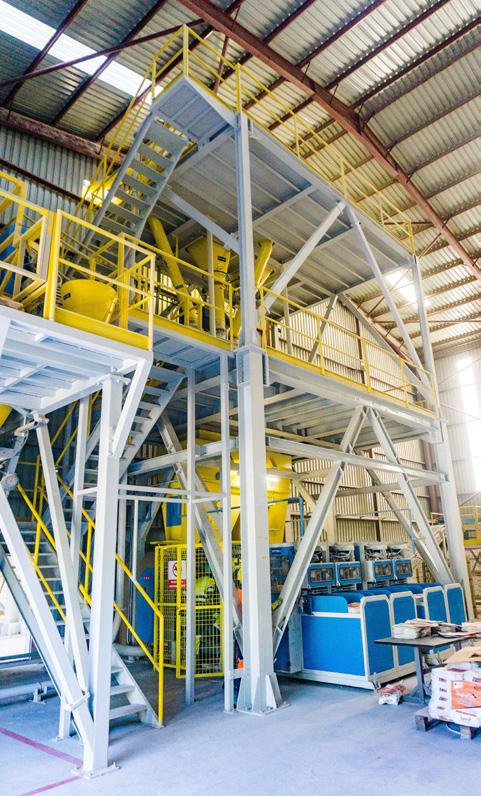

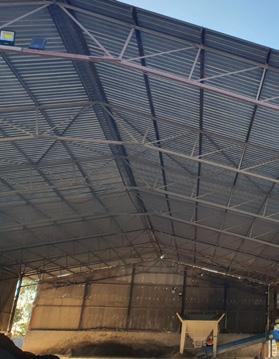


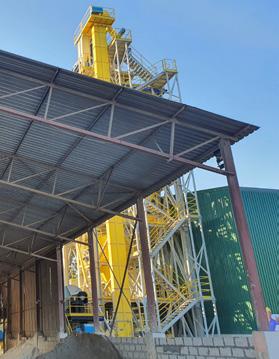
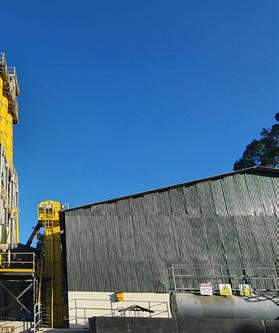
Apart from radically increasing Lafarge’s production capacity the plant has other advantages. The manufacturing process is fully automated from the control room which improves and standardises productivity, ensures that the quality of each product is consistently and dependably the same, and it allows for a wider range of products – and customised products – to be produced. It also operated in line with Lafarge’s commitment to Health and Safety standards and Environmental Management Systems.
The new DMO plant has created a number of new employment prospects – these being highly skilled and well trained technicians, and a huge increase in their Sales and Marketing contingent. In addition the plant will boost the local construction industry creating downstream job opportunities.
The last phase of the expansion programme, the vertical cement mill, is set to increase Lafarge’s production of high quality cement from the current 450,000 tonnes to around one million tonnes per annum. Even with the introduction of the 3D Printing technology this is expected to exceed local demand opening the avenue for exports to the region.
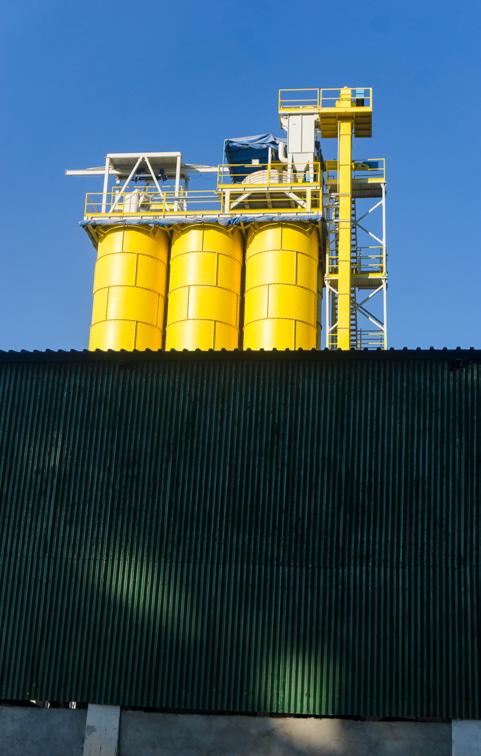
LAFARGE CEMENT PROJECT
Ages GEC W-Cranes Sinoma Zimbabwe
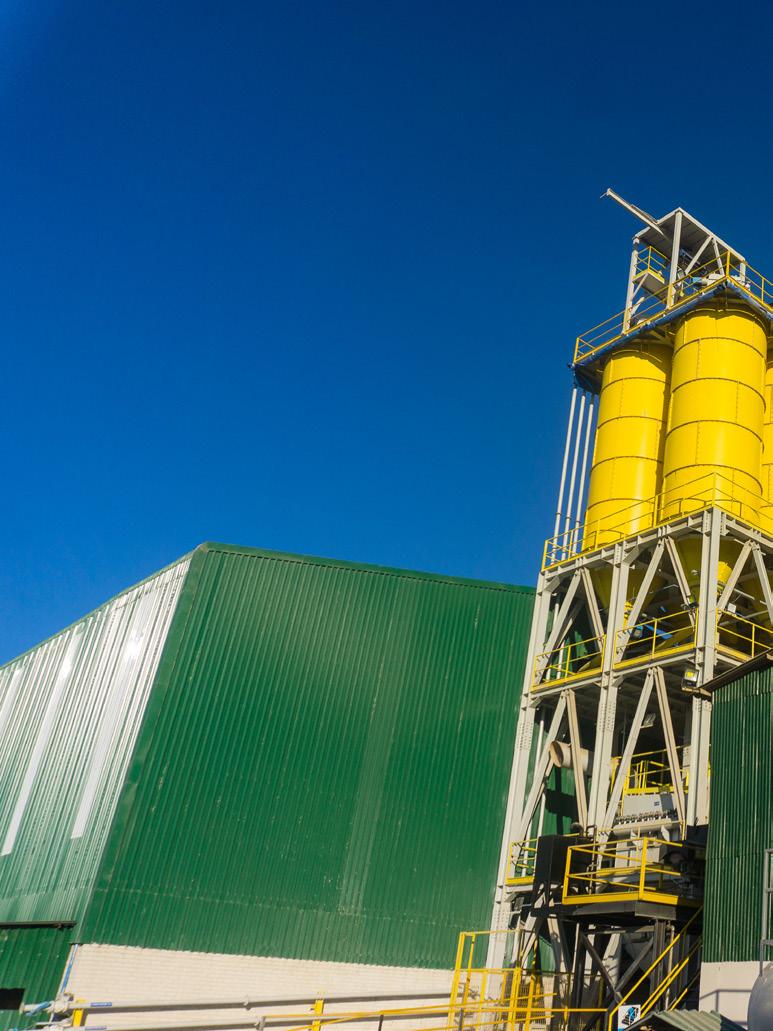
Lafarge has been operational in Zimbabwe for over 60 years, contributing to the growth of the construction industry, infrastructure development and the agricultural sector. They currently employ around 800 people directly and create thousands of jobs in their up and downstream value chain. As a subsidiary of Swissbased Lafarge-Holcim, Lafarge Cement Zimbabwe has access to the most modern and sustainable technology and production methods.
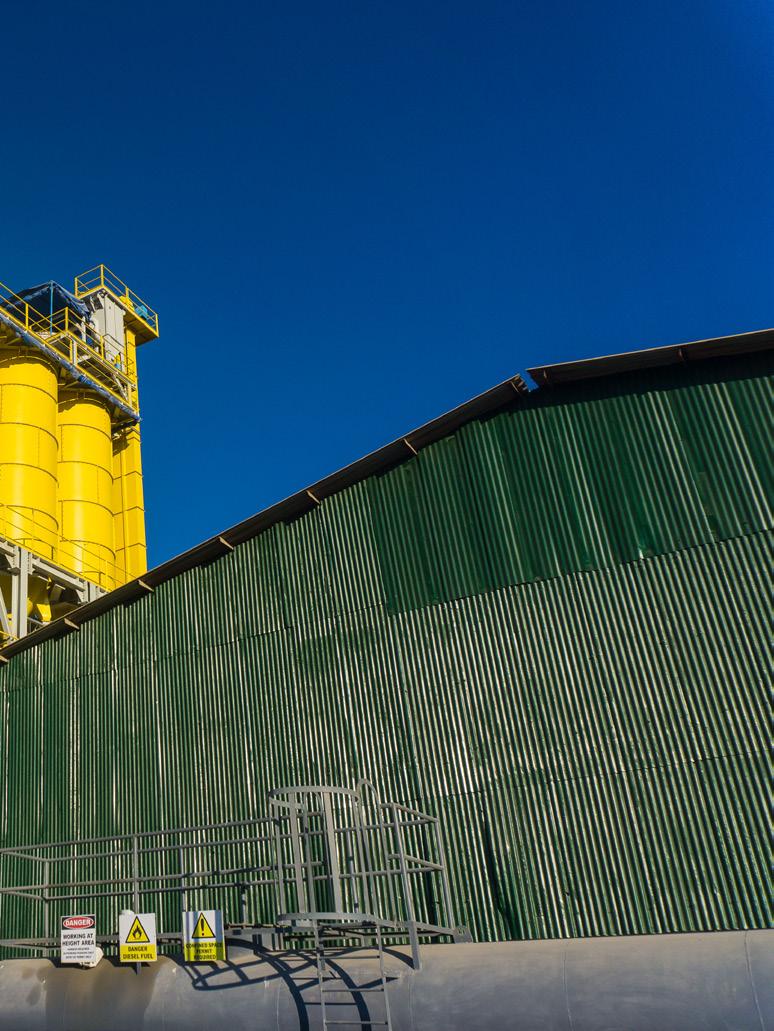