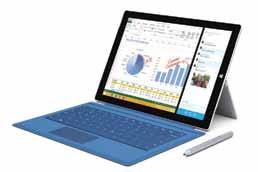
44 minute read
engineeringon-the-go
InSIghtS
new trends, new techniques and current industry issues How much more efficient would structural engineers be if they had access to all of their resources wherever they want? Imagine if resources like construction documents, as-built drawings, project correspondence, calculations, building codes, reference materials, computer analysis programs, product manuals, colleagues, etc. could be carried to every meeting, hauled around to every jobsite and brought home every night. This may not have seemed possible several years ago, but this is exactly what today’s structural engineer can do with the recent advancements in digital technology and tablet style computers.
Resources Go Digital
In today’s digital world, it is easier and more cost effective than ever to create, manipulate, store and retrieve digital media. Phone calls can be recorded by web-based teleconference services and voice over internet protocol (VoIP) systems. Engineering On-The-Go Digital files can be created and manipulated thanks to advancements in digital scanners and portable document format (PDF) software. Storage of digital files can be hosted on office servers or in the cloud By Nick Murphy, P.E. through web-based storage suppliers. Accessing digital media remotely is more efficient thanks to web-based storage suppliers, file transfer protocols (FTP), virtual private networks (VPN) and remote desktop applications. These advancements have changed the way the construction industry shares information. Questions and answers can be created and transmitted almost instantly. Coordination between disciplines can occur in real time Nick Murphy, P.E., is an Associate with teleconferencing and online meeting serwith KPFF Consulting Engineers vices. Permit drawings can be digitally signed in Irvine, CA. He can be reached and posted to web-based servers for submisat Nick.Murphy@kpff.com. sion to the City. Requests for information and shop drawings are transmitted digitally through email, host servers, or online project management systems. Codes, textbooks, testing reports, product manuals, and inspection forms are all available digitally. The digital trend in the construction industry has created

Apple iPad tablet computer. Courtesy of Apple.

Lenovo Yoga Ultrabook computer. Courtesy of Lenovo.
an opportunity for structural engineers to create a virtual workspace with real time access to project files and other resources, provided the engineer has an internet connection and a computer.
Breaking New Ground
Traditionally, laptop computers have been the only mobile computers available to the onthe-go engineer. With the release of iPad and Android tablets in 2010, engineers now have an alternate solution to accessing their resources. The tablet computer, with its slim profile and lightweight design, allows an engineer access to his desktop computer through VPN and remote desktop software applications. Files stored in the cloud can be accessed through other applications which can then be downloaded and installed on the device. Though not as powerful as a laptop, the tablet can still view and manipulate files seamlessly since it is not functioning as a storage device. While tablets hold some capacity to store files directly on the device, the primary function of the tablet computer is as a portal that allows temporary access to the file before saving it back to the cloud or desktop computer. Its efficiency in downloading and saving files is dependent on the strength of the WIFI or cellular signal that connects it to the Internet. Structural engineers who have found a tablet computer to be an efficient alternative to a
laptop computer will be the first to say that the device itself is not what has made their life outside the office more efficient. The efficiency has come from the software that the device utilizes. The applications available to download are as diverse as the engineers who use them. Engineers can take handwritten notes on the tablet during meetings, then convert them to Word documents. They take pictures on a job walk, edit the photos, and insert them directly into field reports. Engineers can also access their construction documents via PDF editors and track field changes as they observe them. Engineers video conference and screen share with their team to resolve issues in real-time. Even drafting and structural analysis applications can allow engineers to answer questions without having to remote access their desktop computer. However, it is not just engineering apps that have made life more efficient. Apps for invoicing, budgeting, expense reporting, traffic, hotel reservations, car rentals, airline reservations, contacts, voice memos, and more are all vital to the engineer on-the-go. The tablet computer has brought all of these resources together in one lightweight package.
Next Generation
For all their advancements and efficiency, tablet computers are not without their drawbacks. Their lack of storage, processing and graphics rendering power, and a USB port are issues that most engineers can work around, but the tablet’s operating system is something that some engineers just cannot adjust to. Structural Engineers typically function in a PC world. A computer that utilizes Windows as its operating system is likely to be the most efficient, since a structural engineer’s work depends on Windows based programs such as Office, AutoCAD, REVIT, and structural design software coded explicitly for the Windows operating system. Recognizing the need for a Windows based tablet, Microsoft and other computer developers released their versions of the tablet computer starting in 2012 with the release of the Microsoft Surface. Some companies, such as Lenovo and ASUS, combined the laptop and tablet designs and released devices known as Ultrabooks or Two-inOnes. Whereas the Surface tablet is true to the tablet design with a single touchscreen without an attached keyboard, the Ultrabook looks more like a laptop with an attached keyboard, but it has a large touchscreen that can be rotated into position to create a tablet
Field Uses for iPad and Android Tablets
• Access office servers via VPN and remote desktop connections • Access cloud storage through Internet connection or applications • Access Outlook emails, tasks, contacts and calendars • Create and manipulate Word docs, Excel spreadsheets and PowerPoint presentations with the Office for Apple application • Create PDF files with applications that print camera images to PDF • View and edit PDF files such as construction documents or site photos with PDF viewing applications • Take and upload site photos while still onsite with built-in camera • Prepare and submit field reports while still onsite • Web conference with design team or contractors • Screen share with design team or contractors • Take handwritten meeting notes that can be transferred to Word documents with note taking applications • View AutoCAD files with Autodesk viewer applications • Use engineering analysis applications
Field Uses for Ultrabooks and Surface Tablets
• Access office servers via VPN connection • Access cloud storage through Internet connection • Access Outlook emails, tasks, contacts and calendars • Create and manipulate Word docs, Excel spreadsheets and PowerPoint presentations with Windows operating system • Create PDF files by printing camera images to PDF • View and edit PDF files such as construction documents or site photos with built-in camera • Take and upload site photos while still onsite • Prepare and submit field reports while still onsite • Web conference with design team or contractors • Screen share with design team or contractors • Take handwritten meeting notes that can be transferred to Word documents with
Windows OneNote • View AutoCAD and REVIT files using the Autodesk programs • Use structural engineering programs installed on the tablet
surface. Both of these new devices can function as a desktop computer by connecting a larger monitor, keyboard (for the Surface), mouse and ethernet cable to its USB and video ports. With the Windows operating system, these devices have their own drives that allow for file storage and program installation directly on the device. This ability to store files and run programs without an Internet connection creates added efficiency for the mobile engineer. Although not as powerful as desktop computers, the Surface and Ultrabooks have a nice balance between portability and computing horsepower. In the end, with structural engineers, there is never a one-size-fits-all solution. Structural engineers are a unique breed that can be quite particular about their tools. Over the last decade, the structural engineer’s toolbox has grown exponentially with advancements in software development, the advent of the digital age, and the portable efficiency of the tablet computers. These tools have allowed structural engineers to be more mobile while maintaining the same level of efficiency.▪
Attention Bentley Users
Have you received your automatic quarterly invoice from Bentley? Would you like to reduce or eliminate these invoices? Use SofTrack to control and manage Calendar Hour usage of your Bentley SELECT Open Trust Licensing. Call us today, 866 372 8991 or visit us
www.softwaremetering.com
“Get in, get out, and stay out” governs the objectives of designing a repair and rehabilitation project on an existing highway facility. Such projects on aging highways need be done as quickly as possible and be long lasting so as to minimize disruptions to a local economy’s infrastructure.
Interstate 280 is a major corridor facilitating traffic in and out of downtown San Francisco. Caltrans maintenance engineers observed the gradual disintegration of hinges on the Southern Freeway Viaduct, a conventionally reinforced box girder bridge built in 1964 and located at the north end of I-280 in the Bay View and Dog Patch Districts of
San Francisco. These hinges are located at the overlap of two frames, each consisting of multiple spans supported continually on columns 30 to 50 feet tall. One frame ends with a “seat” while the next frame is supported on the seat, thus forming a joint to allow for primarily thermal movement. Hinges are located at the transition of a negative moment into a positive one. The seat-side superstructure of a span has a negative moment due to the weight of the support-side superstructure adding a reaction force on the nearest bent. The reaction force on the furthest bent is reduced due to support on the seat, which also results in creating the positive moment on the supported side of the hinge.
Theoretically this is depicted by classical statically indeterminate freebody diagrams for a beam with intermediate supports.
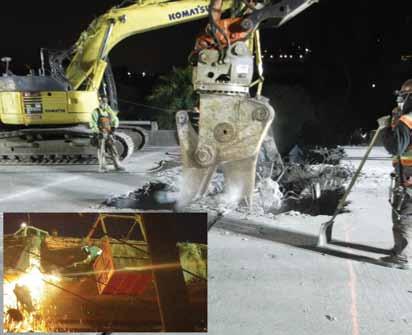
Figure 1. Tailgating into barrier forms.
Bridge Hinge Reconstruction in San Francisco
Accelerated Bridge Construction for Long Lasting Repairs on Aging Highways
By Ric Maggenti, P.E., Sergio Gomez, P.E. and Roberto Luena, P.E.
Rehabilitation work began after constructing temporary supports on both sides of the hinge and closing down this section of viaduct. The existing hinge and 25 to 30 feet of structural box girders of this 53-foot wide bridge were demolished and reconstructed to current Caltrans seismic standards. Removal and replacement included barrier rail and joint seal. The quantity of concrete removed and replaced was approximately 120 cubic yards per hinge. Four hinges and adjacent box girders were reconstructed over 3 holiday weekends. Each weekend consisted of a work window of approximately 100 straight hours, requiring careful planning. Scheduling, logistics, quality control measures, inspections, and selection of materials were paramount to success. Concrete design, mixing, batching and placement technique played no small role.
Project Description
As I-280 is vital to a major urban infrastructure, two approaches to construction of the rehabilitation project were considered. The first was staging partial construction of each hinge where at least a portion of the bridge could be available for traffic during construction. The estimate to do the original 3 hinges earmarked with this kind of staged construction was 140 working days. Working 7 days a week with no weather delays, this would have resulted in inhibiting traffic flow continuously for almost 5 months. When a 4th hinge was slated for replacement, the result would have been over 6 months of traffic inconvenience. Partial construction would also have involved potentially more serious consequences, such as traffic accidents or the hindrance of emergency response vehicles. Additionally, there is a constant risk imposed on construction workers by the proximity of moving traffic. The second construction approach considered was to completely close a portion of the viaduct and do an entire hinge during consecutive shifts, adding up to approximately 100 hours. It was determined viable to close the viaduct for these 100 hour periods and, to minimize commuter disruption, the work was scheduled around three separate 3-day holiday weekends (2014 Memorial Day, 4th of July, and Labor Day). For each of the closures, work commenced on the day preceding the weekend and finished in the early morning hours of the day immediately following the weekend. Two hinges were done during the Labor Day weekend. Three hinges are on the northbound structure while one is on the southbound structure. The 1964 seat and support were 6 inches long across the width of the bridge, while the current seismic standard for hinges in box girder bridges is a minimum of 2 feet long. The 3-mile twin viaduct has hinges approximately every 300 feet. In 1995, the 6-inch seats were retrofitted with bolsters or diaphragms and hinge pipe beams that would provide support if the joint moved more than 6 inches in an earthquake. This was part of the retrofit program following the 1989 Loma Prieta earthquake; the program included enlarging footings and adding steel column casings. Some retrofitted hinges showed signs of distress over the years. Three northbound hinges and one southbound hinge continued deteriorating until it was deemed they were approaching failure, as spalling concrete had to be caught in nets to prevent injury or property damage below.
Removal
To facilitate isolated demolition/removal of the existing structure, temporary supports were required on both sides of the hinge. On
the support side of the hinge, the temporary support was designed to carry the dead load of that span (900 kips). On the adjacent span of the hinge, the temporary support was designed to prevent mid-span deflection and column rotation after the seat was unloaded (800 kips). The demolition was performed from the deck and had to be done very carefully and strategically so as not to damage the existing structure that was to remain, including exposed longitudinal reinforcement. Enough existing longitudinal reinforcement needed to remain intact for mechanical staggered splicing to the new construction. The demolition equipment was limited to 1200 ft-lb hydraulic hammers. A CUT Multi Crusher was used to crush and shear through stems (Figure 1). The final removal was hand labor using primarily rivet busters to prevent damage to the portion of the bridge that was to remain. To maintain a clean construction joint, a 1-inch saw cut was made on the entire exterior and interior surface of the superstructure along the construction joint. The entire demolition had a duration of approximately 16 hours.
Replacement
After demolition, falsework stringers were erected followed by installation of soffit and stem forms. Some of the existing rebar that was to be spliced did not match contract drawings based on archived
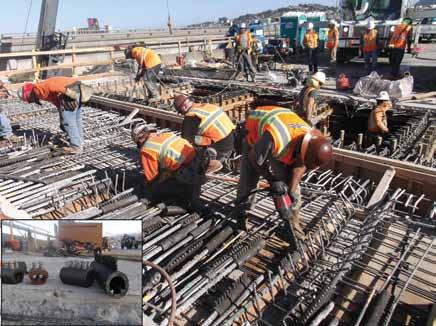
Figure 2. The couplers to mechanically splice the old to the new rebar.
Bridge Hinge Reconstruction in San Francisco
“As-Built” drawings. Anticipating this, extra reinforcement of all sizes and extra mechanical couplers were brought on site along with a mechanical reinforcement bending table (Figure 2). Reinforcement cages for the hinge diaphragms were prefabricated (Figure 3). During the demolition and reconstruction, the structure was monitored/ surveyed continuously at multiple locations for any lateral or vertical movement. Adjustments were made as necessary during demolition and prior to concrete placement.
Concrete
Each hinge reconstruction consisted of four pours: stem and soffit on the seat side, stem and soffit on the support side, deck pour seat side and finally deck pour supported side. Barriers and joint seals were the last order of work, notwithstanding clean-up and traffic markings. Six weeks prior to Memorial Day, the contractor constructed a mock-up consisting of several stems and soffits and a portion of the hinge seat diaphragm. The mock-up was located on the ground in the concrete company’s yard in Sacramento. Batching and mixing was done by a volumetric mobile concrete truck complying with Caltrans’ Standard Specifications. To simulate the actual procedure, the truck was stationed next to a concrete pump and discharged concrete into the pump truck’s hopper. Since each placement sequence required more than the capacity of a truck, the concrete materials were replenished during placement as was the plan for the job site. Aggregates were continually loaded into the truck’s bins with skip loaders while the truck’s cement hopper was replenished using prepackaged 1 ton super-bags lifted by crane. A water truck was used to keep water in the water tanks. A truck could hold about 10 cubic yards so the mock-up was to be more than one cycle, and thus the 16 cubic yard mock-up was deemed appropriate. Also, the largest element was a hinge diaphragm. To ensure compliance with Caltrans’ Mass Concrete requirement that a concrete element does not exceed 160 degrees F, the hinge diaphragm mock-up temperature was monitored. Peak temperature was well under 160 degrees F, thus no additional precautions were required. The truck and 2 back-up trucks were certified during the mock-up. At the bridge site, aggregate stock piles were located on the deck spread out over several bents. Note concrete technology evolved to using the absolute volume method for batching concrete to address the bulking characteristic of aggregate with its changing volume with changing moisture content. Absolute volume practice uses weight to batch ingredients to address effects of bulking due to moisture. The stock piles were covered with plastic sheeting to maintain a near constant moisture content, particularly the sand stock piles, mitigating bulking characteristics and allowing for more accurate batching by volume. Cement super-bags were stored under the bridge. Continuous metering displaying volume per time of the ingredients and automatic
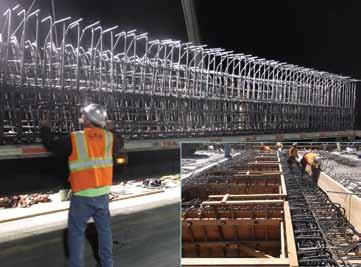
5-hr break (psi)
5/24/14 ES-83, Stem and Soffit, Seat Side 150.2 3598 3780 5/25/14 ES-83, Stem and Soffit, Supported Side 151.14 3718 5/26/14 ES-83, Deck, Seat Side 3385 3683 5/26/14 ES-83, Deck, Supported Side 3560 3793 7/4/14 A-80, Stem and Soffit, Seat Side 151.26 3333 4033 7/5/14 A-80, Stem and Soffit, Supported Side 151.68 3430 3928 7/6/14 A-80, Deck, Seat Side 152.03 3743 7/6/14 A-80, Deck, Supported Side 151.83 3960 8/30/14 A-83, Stem and Soffit, Seat Side 151.63 3283 3888 8/30/14 SE-59, Stem and Soffit, Seat Side 151.83 3650 8/31/14 A-83, Stem and Soffit, Supported Side 151.03 3260 3738 8/31/14 SE-59, Stem and Soffit, Supported Side 150.93 3985 8/31/14 A-83, Deck, Seat Side 3830 9/1/14 SE-59, Deck, Seat Side 151.93 3680 9/1/14 A-83, Deck, Supported Side 4025 9/1/14 SE-59, Deck, Supported Side 3930 Total count 11 9 7 7 Average 151.41 3556 3697 3903 Std. Dev. 0.55 222 225 112 Coef. of Var. 0.4% 6.3% 6.1% 2.9% Figure 4. Unit weights and early strength.

Figure 5. Compressive strength vs. time.
dispatching tickets were required. Unit weights on samples taken during placement were used as a check on proportioning. Figure 4 shows how consistent the unit weight was throughout the entire project. The lowest unit weight correlated with the initial higher slump during the very first placement before water was slightly adjusted to achieve the desired 5- to 7-inch slump for placement. The structural concrete design complied with 2010 Caltrans’ Standard Specifications for Rapid Strength Concrete. This material’s specification is based on the award winning I-10 Pomona Freeway project specifications constructed in 1999. Approximately 2 lane-miles of the 8 lane mile project on a heavily traveled portion of the I-10 was replaced during a 55 hour weekend window, with the remaining 6 lane miles completed during nighttime closures over a period of several months. The specification allows for any fast-setting cement meeting ASTM c219 for hydraulic cement. If other than a Portland cement is used, then some additional requirements are listed to ensure long-term durability. The contractor chose a calcium-sulfoaluminate cement as the fast-setting hydraulic cement ingredient, which happened to be manufactured by the same company providing the cement on the Pomona project. The contractor was able to control the mix with admixture adjustment as the temperature varied and as the placement needs varied. There was no dead time waiting for strengths. The working time was engineered to be about an hour, so by the time the top of a stem was finished, the soffits achieved final set. The contractor’s crews were openly impressed has to how soon forms could be stripped so as to move on to the next operation. The last concrete placement was the barrier rail placement. Because it could be tailgated and a shorter
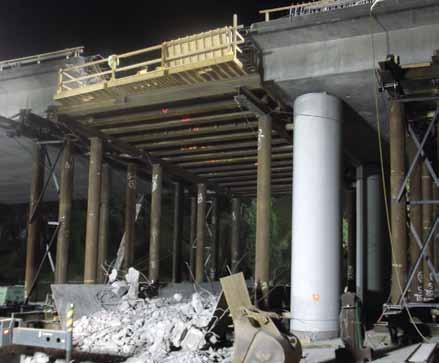
Figure 6. A view of a removed hinge and box from below.
working time could be easily accommodated by the nature of the element, that mix was engineered to produce 1 hour compressive strength of 2,000 psi on cylinders heated to approximately match the actual in-place temperature of the barrier concrete. Cylinder break data are also shown in Figure 4. The cylinder breaks had coefficients of variation falling within the standard of concrete control range category of “very good” as classified by the American Concrete Institute per ACI 214 R-02. This coefficient of variation demonstrated consistent batching and mixing, and consistent properties of cement, aggregate and admixtures, thus achieving the high degree of quality control confirmed by quality assurance results. Figure 5 shows the strength gain with time up to 3 months.
Conclusion
All the preliminary planning and diligence of the contractor, the mockup, calibration of the mixer trucks, unit weight sampling taken during placement confirming proper mix proportions, the required care taken on the aggregate stock piles to ensure uniformity, standard QA sampling and testing, and the attention to detail during design and construction, resulted in achieving the objectives of this rehabilitation project.▪ Ric Maggenti, P.E. (ric.maggenti@dot.ca.gov), Materials & Research/Bridge Engineer, Caltrans; Sergio Gomez, P.E. (Sergio_ gomez@dot.ca.gov), Bridge Construction Engineer Representative, Caltrans; Roberto Luena, P.E. (Roberto_luena@dot.ca.gov), Area Bridge Construction Manager, Caltrans.
Project Team
Owner: Caltrans Construction Contractor: Golden State Bridge Inc. Concrete Supplier: Precision Concrete Materials LLC Fast Setting Cement Supplier: CTS Manufacturing Corp.
AdAptive Reuse investigAtion of Roof fRAming

By D. Matthew Stuart, P.E., S.E., F.ASCE, F.SEI, SECB, MgtEng
Industry City in Brooklyn, New York retained Pennoni Associates, Inc. (Pennoni) to complete an evaluation of the existing roof structures at Buildings 2, 3, 5, 9, 10, 19, 20 and 26 of the historic Bush Terminal Complex (Figure 1). The primary purpose of this effort was to determine the load-carrying capacity for new “green” roofing systems, solar panel arrays and other adaptive reuse proposals. Due to the lack of original structural drawings, it was necessary to field-determine the internal reinforcement of the concrete system at a typical bay in each building. This involved creating small inspection openings to expose the reinforcement at areas of the framing where removing insignificant amounts of concrete material would not compromise structural integrity (Figure 2). This approach, used in conjunction with a Profometer (or Pachometer), enabled the

Figure 1.
determination of the existing reinforcing in the immediate area surrounding the exploratory openings. Pullman Shared Systems Technology, Inc. (Pullman), as a subcontractor to Pennoni, performed the exploratory demolition; WJE, as a sub-consultant to Pennoni, conducted the Profometer readings. The approximate concrete compressive strength was obtained by using a Schmidt (or Impact) Hammer in the same vicinity.
History and Description of the Buildings
The buildings in the Industry City complex were constructed between 1904 and 1911, and were originally referred to as the Bush Terminal Company facility. A search of available historical records revealed
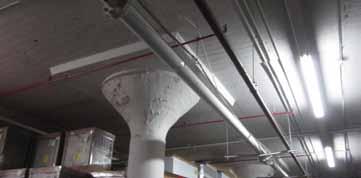
that the architect, engineer and contractor, for most if not all of the buildings, were William Higginson, E.P. Goodrich and Turner Construction Company, respectively. Additional history of the site can be found at http://industrycity.com/history/ All of the buildings associated with the investigation were constructed as conventionally reinforced, cast-in-place concrete structures. Building 26 was constructed as a two-way flat slab with drop panels and column capitals, which were all supported by round concrete columns (Figure 3). All of the other buildings were framed as oneway slabs, joists and beams, which were supported by either round or square concrete columns (Figures 4 and 5). The buildings varied in height from six to twelve stories, not including basements. In general, the existing roof structures were in good condition, with painted soffits, and supported suspended loads such as lighting/ electrical, sprinklers and piping, as well as rooftop loads such as steel piping, electrical power lines and small mechanical equipment. The roofs also included skylight openings, most of which that had been removed and enclosed with supplemental framing (Figure 6). The roofing systems at all of the buildings, except for Building 2 (which had been recently reroofed), were in very poor condition, which was confirmed via roofing cores that were obtained by Pullman. The primary purpose of the roofing cores was to determine the weight of the existing roofing systems, which varied between 1.0 and 6.0 psf.
Analysis and Material Testing
The assumed strength of the reinforcing bars was based on information provided in an out-of-print book entitled Reinforced Concrete in Factory Construction, published in 1907. This publication included an entire chapter dedicated to the design and construction of Building 2 and indicated that the floor live load was 200 psf. Additional research of other historical publications, including the 1911 edition of The American Architect magazine, indicated that the six-story buildings at the complex were designed for a floor live load of 150 to 400 psf and a roof live load of 75 psf. Because of the limited access available to the top flexural reinforcing in the slab, joists and beams, the analysis of these members was based on the positive moment capacity of the sections determined from the exposed bottom flexural reinforcing at the exploratory openings located at the soffit and midspan of the selected typical members. The assumed dead loads included the self-weight of the framing, the weight of the roofing system and an additional 3.0 psf to account for miscellaneous suspended mechanical loads. The minimum roof snow load, based on the governing building code, was 20 psf. The results of the initial analysis and report indicated that, in some cases, the reserve load-carrying capacity of the existing roofs under investigation was considerably less than the 70 psf load capacity documented in the available historical references. As a result of this initial conclusion, which was based on a tensile strength, ft, of the reinforcing bars of 16 ksi as documented in the same historical references, and in conjunction with the proposed use of the roofs as public assembly space with a live load of 100 psf, Pennoni recommended material testing of the reinforcing bars. Samples of the bottom flexural reinforcing of the same roof joists that had previously been subjected to exploratory demolition were obtained at the end of the members immediately adjacent to the supporting beams (Figure 7). An additional similar sample from a beam was also obtained from Building 20 at the end of the member immediately adjacent to the supporting column. The bottom flexural reinforcing sample from the flat slab in Building 26 was removed immediately adjacent to a drop panel. A reinforcing steel sample could not be obtained in Building 9
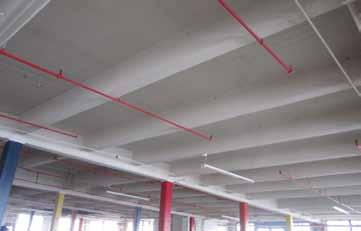
Figure 4.
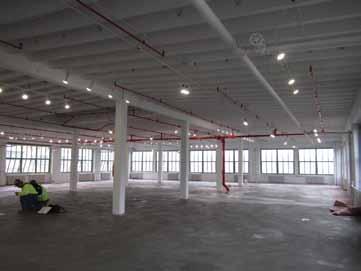
Figure 5.

Figure 6.
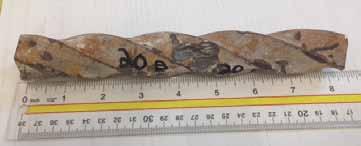
Description Yield Strength (fy) ksi Sample Size
Building 2 Joist 44.8 7/8-inch diameter Building 5 Joist 49.2 0.905-inch square twisted Building 10 Joist 56.0 0.915-inch square twisted Building 19 Joist 44.5 Not Recorded Building 20 Joist 53.5 Not Recorded Building 20 Beam 54.5 0.915-inch square twisted Building 26 Slab 39.6 5/8-inch diameter Building 3 Joist 54.5 0.875-inch square twisted
because of limited access and the lack of bottom reinforcement in the available redundant areas of the joist investigation. The samples were exposed using similar exploratory demolition methods with 6- to 8-inch-long samples of the reinforcing steel removed and sent to a laboratory for testing. The damaged area of the remaining reinforcing steel was not repaired, because the samples were obtained from an area of the member in which there was no positive moment, therefore the presence of the bottom flexural reinforcement was redundant. Table 1 summarizes the test results. The results of the material tests indicated that the actual yield strength (fy) of the reinforcing bars varied from 39.6 ksi to 56.0 ksi. This magnitude of strength is considerably greater than the previously known highest grade of vintage reinforcing steel documented by the Concrete Reinforcing Steel Instituting (CRSI) that was in use at the time, which was Grade 30 (fy = 30 ksi; ft = 16 ksi). CRSI confirmed that the use of reinforcing steel as high as Grade 40 to 56 in the first decade of the 1900s at these buildings is an anomaly from previous historical records for the same era. Reanalyzing the roof framing, based on the actual yield strength per the material testing, resulted in a considerable increase in the Maximum Allowable Reserve Load Capacity noted in Table 2. These values already account for the self-weight of the structure, the miscellaneous mechanical superimposed dead load, the dead load of the existing roofing system and snow load. With the exception of Building 26, and as indicated in Table 2 for Building 20, the results are based on the joist capacities, which were always less than that provided by the beams. In general, it appeared that most of the roofs, except for Buildings 3 and 20, were designed and constructed for approximately the same floor live load of 200 psf as documented in the historical records. It is also not unusual to be able to justify a higher live load capacity than that intended by the original design by using current ultimate strength methods, rather than the working stress methods used at the beginning and middle of the 20th Century. Therefore, it is not surprising that, in some cases, the load carrying capacities documented by the ultimate strength analysis resulted in capacities greater than 200 psf. The primary reason why the capacity at Building 20 is significantly less than that at the other buildings is because it has approximately one-half of the beam reinforcing provided in the other one-way beam roof structures. It is not clear why this was the case. Using the Profometer, an investigation of other similar beams in Building 20 in the same column line as the subject typical beam indicated that
*The value listed for Building 9 is based on an assumed yield strength (fy) of 40 ksi. If material testing is not conducted, it should be reduced to 87 PSF, which is based on a historical maximum available yield strength of 30 ksi confirmed by CRSI.
Building Maximum Allowable Reserve Load Capacity
2 248 psf 5
9
10 188 psf 145 psf *
310 psf
19 277 psf
20 104 psf
26 180 psf
3 143 psf
similar reinforcing – only two 0.915-inch square twisted bars – was provided in all of them. Thus, it is very likely that the reduced load carrying capacity of the Building 20 roof structure is widespread and typical for the entire building.
Conclusions
It is important to note that the results of this investigation were based on a typical, repetitive bay of roof framing in each building. Any atypical bays or framing members that are different from that analyzed may not have a comparable reserve load-carrying capacity as that documented for the typical bay. In addition, the original or supplemental framing associated with existing skylights or subsequently enclosed skylight openings were not included in this investigation, so the capacity of these areas should be investigated before any change in their usage. It was Pennoni’s understanding that the roofs at a number of buildings were intended to be used as public assembly spaces, such as outdoor theatres. Chapter 16 of the NYC Building Code requires a minimum live load of 100 psf for Assembly Areas and Theatres with movable seats, and does not make a distinction about the level of the building at which this occupancy occurs. Except for Building 9 – in the absence of material testing as required to justify a yield strength greater than 30 ksi – it appeared that all of the buildings associated with the investigation had adequate reserve load carrying capacity for this function. Additional adaptive reuse concepts such as that proposed at Building 19, which will include the construction of a new raised roof over a portion of the building footprint and rooftop terrace facilities, should be evaluated on a case-by-case basis. More conventional methods of adaptive reuse, such as solar arrays (maximum 10 psf) and “green” roofing systems (maximum 25 psf), can be installed safely at areas that correspond to the typical bays investigated. This project served as a good example of how a responsible property management company completes the due diligence necessary for a proposed adaptive reuse of an existing facility.▪ D. Matthew Stuart, P.E., S.E., F.ASCE, F.SEI, SECB, MgtEng (MStuart@Pennoni.com), is the Structural Division Manager at Pennoni Associates Inc. in Philadelphia, Pennsylvania.


U.S. ConStrUCtion Spending Up
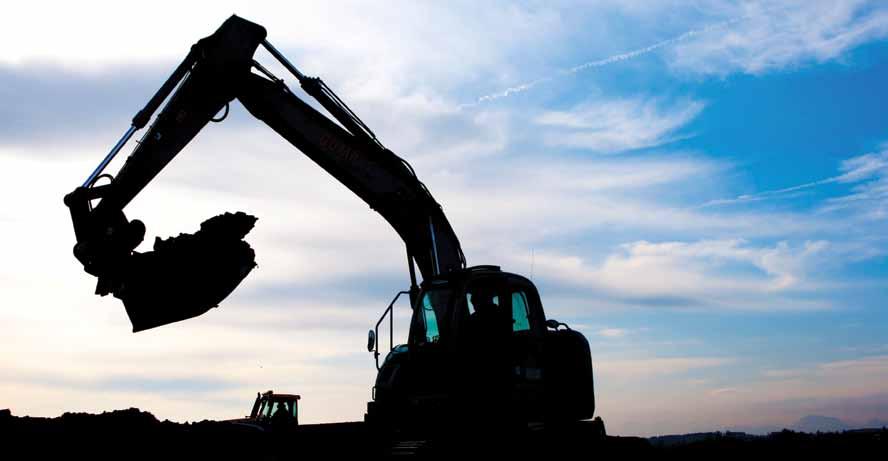
Foundations Companies Offering New Products, Services
By Larry Kahaner
Construction spending in the United States rose more than expected in October – in both public and private sectors – logging a 1.1 percent increase, the largest gain since May according to the Department of Commerce. This data suggests some momentum for the fourth quarter of 2014. Overall, U.S. construction reached an annual rate of $970.99 billion. Construction looks strong on a global scale too, according to KPMG’s 2013 Global Construction Survey which shows “an industry in better shape than four years ago with rising backlogs and largely healthy margins. The recovery in the global economy is driving infrastructure, power and energy projects, while cheaper gas prices are leading to manufacturing growth.” Amid this backdrop of positive data, many foundations companies are seeing increased work. “Although we are staying busy right now in most major market sectors, we are seeing a big increase in the use of ground improvement methods in the construction of multi-use [residential and commercial] structures, in particular in urban areas where old fill soils are a significant concern,” says Lyle Simonton, Director of Business Development for Subsurface Constructors, Inc. (www.subsurfaceconstructors.com) in St. Louis, Missouri. “Projects are using stone columns/aggregate piers in fill soils, providing a significant increase in bearing pressure and therefore a higher ‘trust’ factor with building on marginal sites.” Since the start of its Ground Improvement Division in 2005, the 108-year old company continues to grow its ability to perform work in new areas of the U.S. each year, Simonton says. “By continuing to invest in new technology and with our in-house innovation in improving our equipment and techniques, we have put ourselves in a competitive position for projects across much of the U.S.” Simonton notes that he’s hearing from SEs who want to work with Subsurface Constructors to help develop their projects. “They are trying to bring value to their clients by optimizing the foundation “Although we are staying busy right now in most major market sectors, we are seeing a big increase in the use of ground improvement methods in the construction of multi-use [residential and commercial] structures, in particular in urban areas where old fill soils are a significant concern.”
type for the existing soil conditions and we’re able to help them develop the most economical solution. Subsurface Constructors is one of the only specialty contractors in the U.S. who provides both deep foundations and ground improvement services, so we can provide a true assessment on what foundation type is feasible and economical.” One recent project is “The Streets of St. Charles” site in St. Charles, Missouri, a multi-use project that consists of an apartment structure, retail, office space, and a movie theater. This site had significant grade changes and very soft soils in most areas. Subsurface Constructors worked closely with the general contractor to develop earth retention solutions to support the large cuts on the site, and used multiple ground improvement types to accommodate new construction of footings in soft soils and some restricted access areas. Subsurface was involved in the project planning process for close to two years prior to construction, and therefore could help the design team make important decisions regarding foundation type, earth retention, and construction sequence, Simonton says.
Geopier is Ground improvement.™
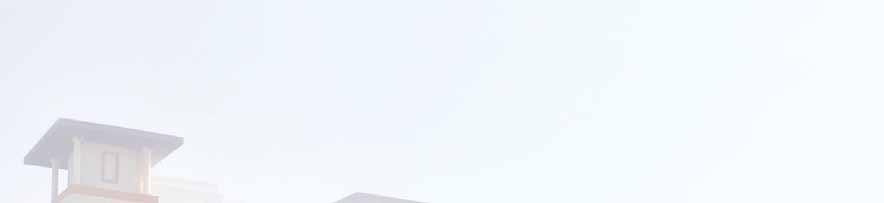
Work with engineers worldwide to solve your ground improvement challenges.
the Geopier Gp3® system: controllinG settlement
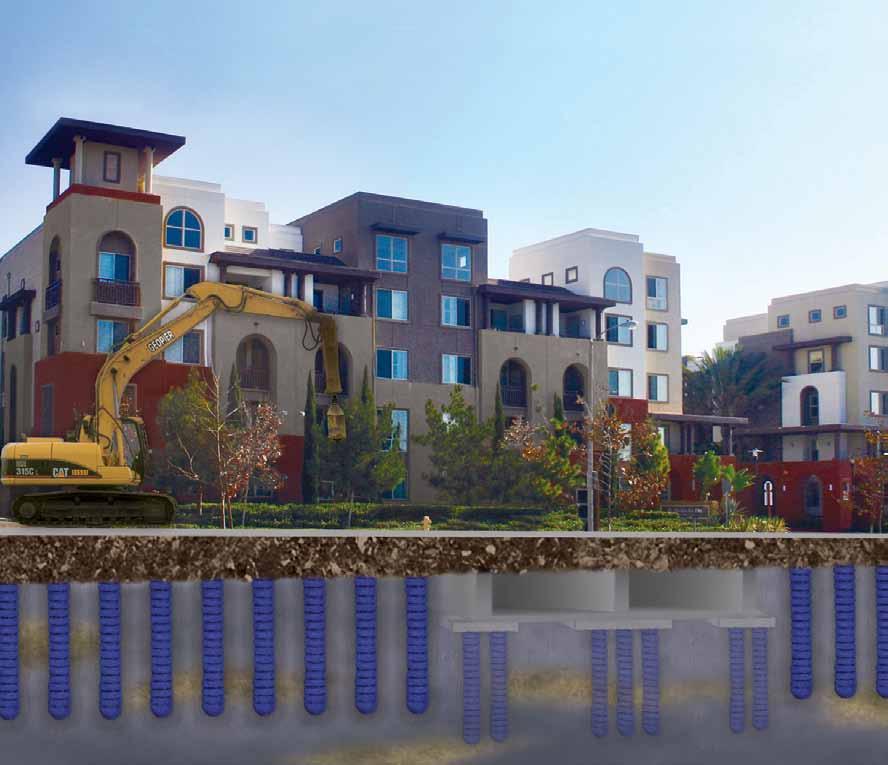
we help you fix bad Ground.
For more information call 800-371-7470, e-mail info@geopier.com or visit geopier.com.
Plans for the 150,000 square foot Avalon Irvine apartment complex in Irvine, CA featured a common “wrap” style structure, with 4-story apartments surrounding a 4.5-story parking garage. The site was underlain by 20 to 25 feet of soft to medium stiff lean clay with groundwater encountered at depths of 8 to 10 feet. The clay was underlain by stiff clay and dense sand to a depth of 50 feet. Reconciling the settlement tolerances between the apartments and the parking structure presented a unique design challenge. The GP3® system was an ideal solution, meeting the specified settlement tolerance for 1” total foundation settlement and ½ inch differential between the parking structure and the apartments. By reducing total settlements and accelerating time rate of settlement for all structures, GP3 eliminated the need for a 6-9 month surcharge.
Foundations

Geopier Foundation Company (www.geopier.com) in Davidson, North Carolina is also experiencing a good year. President Kord Wissmann says: “2014 is a record year for Geopier, and we are looking forward to continued success in 2015. While the overall markets remain strong, we believe that it’s our wide variety of continuously evolving ground improvement solutions that afford great value to our clients.” The company, a subsidiary of Tensar Corporation, says that it developed the first Rammed Aggregate (RAP) system in 1989. Today, Geopier solutions provides an efficient and cost effective Intermediate Foundations solution for the support of settlement sensitive structures, company officials say. They note that its systems have become effective for massive over-excavation and replacement of deep foundations including driven piles, drilled shafts or augered cast-in-place piles. Adds Wissman: “Our GeoConcrete Columns are being used for heavy loads on very soft soil sites, and our Geopier X1 system is providing opportunities to efficiently reinforce deep compressible cohesive soil previously reserved for deep foundations.”

Pile Dynamics, Inc. (www.pile.com) of Cleveland, Ohio redesigned several of its instruments in 2014. “The Pile Integrity Tester model FV and the Thermal Integrity Profiler got larger and more visible screens,” says Gina Beim, Senior Consulting Engineer/ Marketing Director. “But the Pile Driving Analyzer (PDA) system got a complete top-tobottom redesign of both hardware and software.” Says Beim: “The new Pile Driving Analyzer system is the PDA-8G model. Like previous PDAs, the PDA-8G uses data obtained by sensors attached to a pile to calculate capacity and more than 230 other quantities once a driving hammer or other drop weight hits the pile.” “The thickness of the PDA-8G is less than half of the model it replaces and it feels light and ergonomic, like a tablet. Engineers who are familiar with the PDA will appreciate that the data acquisition channels of the PDA-8G are now all universal, allowing the use of various combinations of accelerometers and strain transducers. This is attractive for tests of large drilled/cast-in-place piles,” Beim says. “Data may be collected at 120 blows per minute – almost fifty percent faster than before – making it easier to test piles driven by hydraulic hammers with high blow rates. The PDA software now responds to gesture controls like swiping and pinch-to-zoom, making for a very intuitive interface. It also includes more extensive data input help and output customization. The PDA-8G is SiteLink-ready [SiteLink technology transmits PDA test data via the Internet to an engineer located
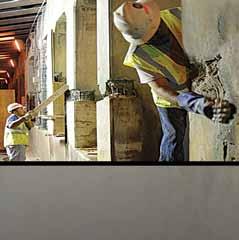
ADVERTISEMENT–For Advertiser Information, visit www.STRUCTUREmag.org
Pile Integrity Tester

Hit, see good data, done. Move to next pile. Repeat. It’s that fast.
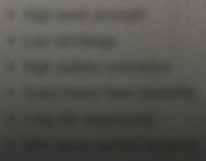
Evaluates foundation integrity and depth. Various models to perform low strain dynamic testing by pulse echo or transient response method. All with powerful data analysis software. Complies with ASTM D5882.
Learn how it works: free PIT-S demo software www.pile.com/pit
CONSTRUCTION CEMENT FASTER
STRONGER MORE DURABLE 3000 PSI IN 1 HOUR
Speci ed Worldwide
ADVANCED TECHNOLOGY
• High bond strength • Low shrinkage • High sulfate resistance • Great freeze thaw durability • Long life expectancy • 65% lower carbon footprint
Available in Bags and Bulk
800-929-3030 ctscement.com
elsewhere who follows the test in real time], giving the engineer the option of conducting the test remotely. A totally revamped version of the CAPWAP software that analyses the data collected with the PDA-8G was also released.” Beim concludes: “Pile Dynamics manufactures an instrument that monitors the installation of augered cast-in-place piles, the PIR [Pile Installation Recorder]. Certain U.S. industry guidance documents recommend the use of such instruments – the generic name is Automated Monitoring Equipment – whenever this type of pile is installed. PDI both sells and rents the PIR, and this year the number of rentals increased significantly. PDI sells this mostly to the U.S. market, where augered piles are typically favored by the private sector. They are a relatively inexpensive deep foundation solution.” At Hayward Baker, Inc., (www.haywardbaker.com) whose North American Headquarters are in Hanover, Maryland, Director Jim Hussin says that soil mixing is continuing to grow. “That’s the process where soils are mechanically mixed with binders, usually cement, to end up with a stronger material. It’s being used more and more, especially in soft sites where you have either soft clays or weak materials that are difficult to treat using other technologies.” Hussin adds: “In the south Florida market we’re using it more frequently to create what we call ‘bathtubs,’ where the [developer] wants to build high-rise condominiums but they also want to put three or four-story parking garages below them which is difficult because it’s right on the beach. A 30-foot deep excavation adjacent to the Atlantic Ocean is extremely hard to do. Before they do an
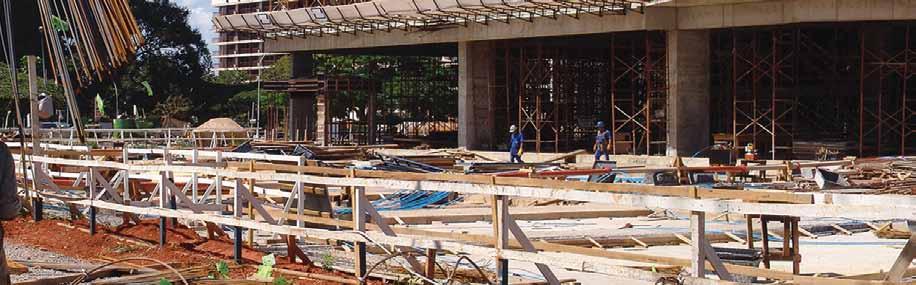
ADVERTISEMENT–For Advertiser Information, visit www.STRUCTUREmag.org
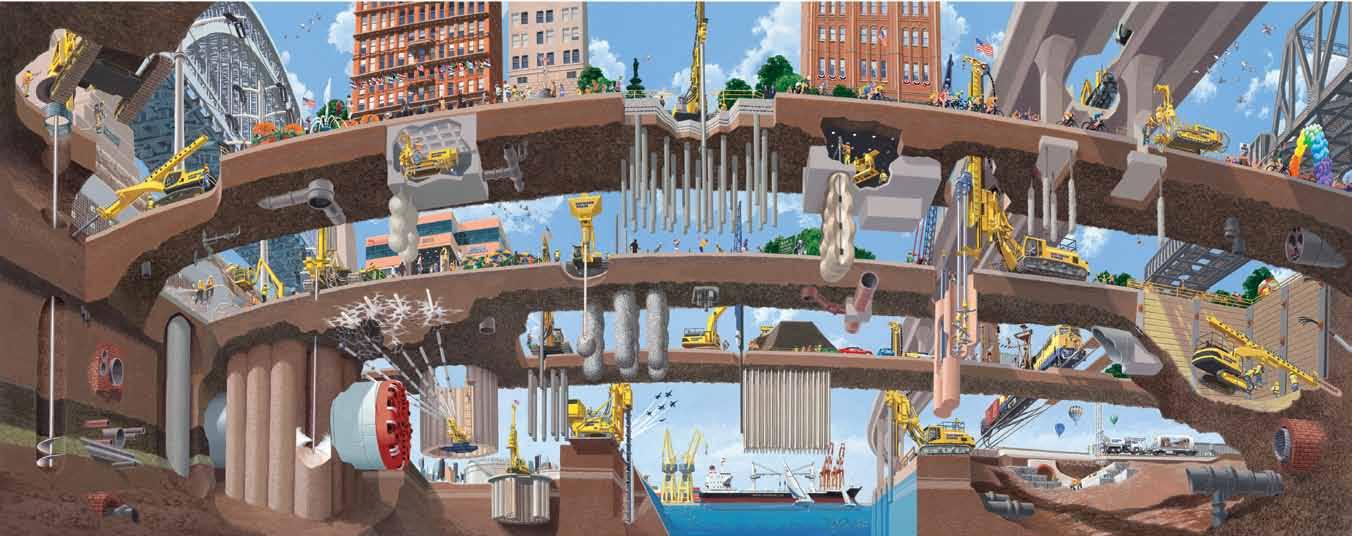
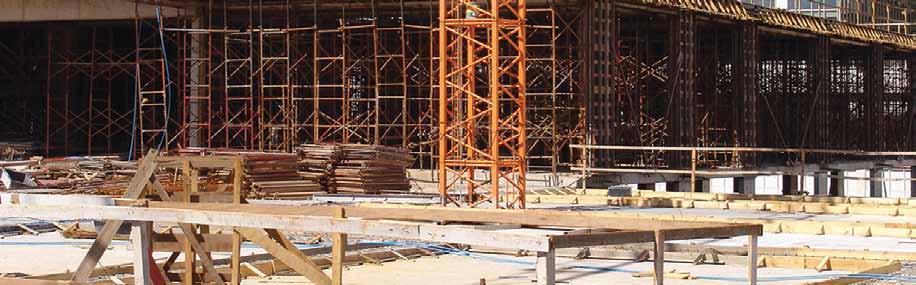
excavation, we’ll spin tools down and mix from 30 to 40 feet. This creates a floor down below the planned excavation. We then create walls on the side. We’re building a ‘bathtub’ which they can dig out and have a dry excavation. Then they’re able to construct lower floors and go on up with their high-rise. That’s something in the last year or so that’s really taken off.” As for the market in general, Hussin sees improvement. “We’re seeing after a couple years of the [the recession and aftermath] that there’s been a steady climb and we’re back to where we were pre-recession days. We’re seeing a nice, steady growth in the construction industry. It’s not extremely fast but nice and steady, so I think it’s probably a good, healthy growth,” he says. Hussin would like SEs to know that Hayward Baker has the ability to construct projects designed by others but also performs design-build projects. “The diversity that Hayward Baker offers, along with our engineering ability, allows us to assist engineers with evaluating and resolving sub-surface issues with the right, best fit for whatever the project is.
At CTS Cement Mfg. Corp. (www.ctscement.com) in Cyprus, California, Marketing Director Janet Ong Zimmerman says the company manufactures Rapid Set fast-setting hydraulic cement and Type K shrinkage compensating cement. “Rapid Set exceeds 3000 psi in one hour, which means you can make structural repairs and rehabilitation and return the concrete to full use in one hour,” Zimmerman says. She wants SEs to know about Rapid Set Flooring Products
ADVERTISEMENT–For Advertiser Information, visit www.STRUCTUREmag.org
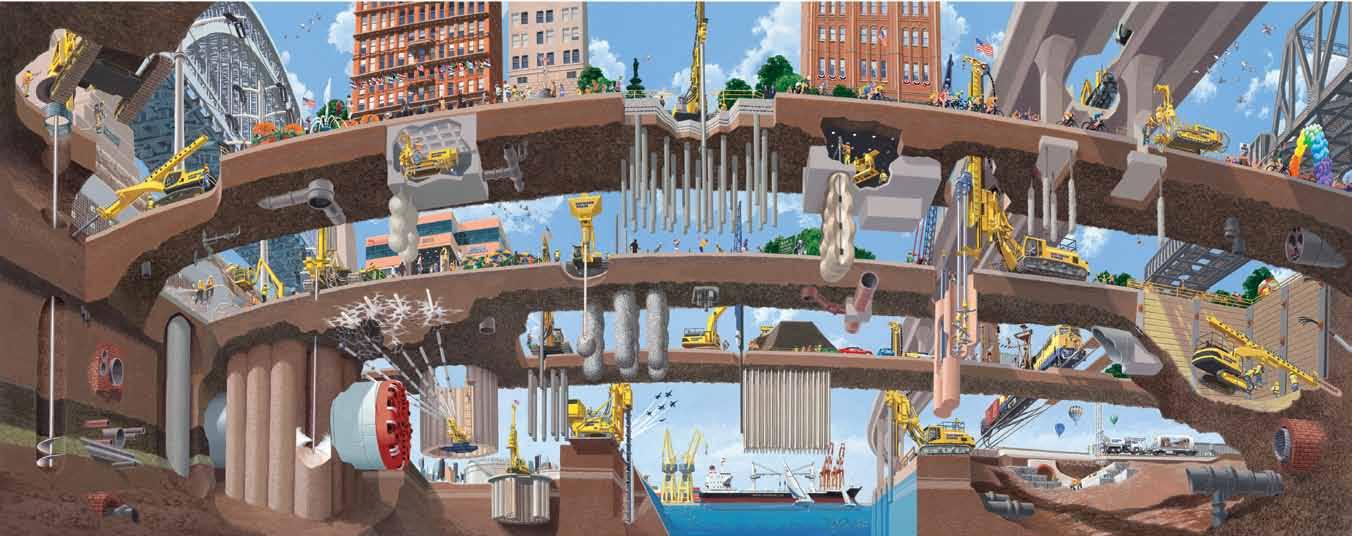
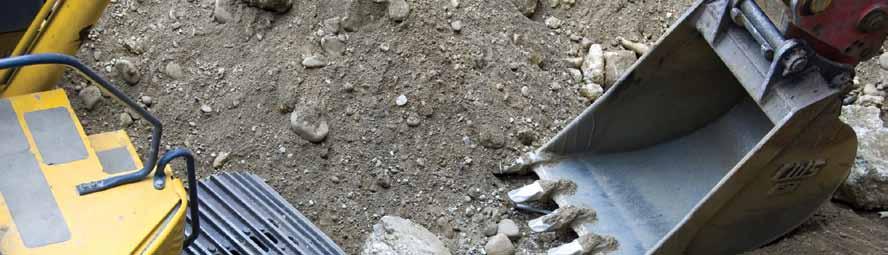
that “offer a complete way to repair, resurface and renew interior and exterior floors.” She adds: “Products include TRU SelfLeveling for polished overlays and toppings, Skim Coat for patching and skim coating, and repair mortars.” In addition, the company is touting Rapid Set Corrosion Inhibitor which provides triple-protection against corrosion. “It increases corrosion resistance when used in areas susceptible to corrosion and chloride. It repels water, thereby preventing an unsightly appearance to concrete. It reduces chloride permeability, thereby increasing the life expectancy of metals, steel and rebar,” Zimmerman says. (See ad on page 41.)
Hollie Furimsky at Ram Jack Systems Distribution in Ada, Oklahoma, (www.ramjack.com) notes that its helical design software Ram Jack Foundation Solutions allows an engineer to custom design a helical pile per their project specifications, share projects with other registered users, and save a PDF output for submittals. “Ram Jack’s engineering department, staffed with structural and geotechnical engineers, assist engineers with designs, drawings, specifications, and technical questions. If the engineer of record is not familiar with helical or hydraulically driven steel pilings, our engineers can provide the pile design, calculations, drawings, and specifications for the engineer’s review,” she says. “Ram Jack Manufacturing ensures the quality and assurance of our products through our ISO-9001 certification. We also hold a Fabricator’s License per the City of Los Angeles Building Department. Ram Jack continues to maintain our ESR report (ESR1854) and have updated it to include compliance to the 2012 IBC and the 2010 Florida Building Code. We have also updated our L.A. Research Report for compliance with the 2014 L.A. Building Code.” Furimsky adds: “Ram Jack Foundation Solutions software and engineering consulting services are provided free of charge to design engineers. Our product reports and ISO certifications demonstrate Ram Jack’s commitment to quality control and assurance of our products, as well compliance to the building codes.” She says that they have seen an average of 20 percent growth in product sales across the board. Helical piles have had the largest growth. “We strive to be a leader in our industry. Our commitment to the engineering community has always been to provide the most trusted steel piling system on the market. Our offerings and services are geared to helping engineers specify our products with confidence,” Furimsky concludes.▪
ADVERTISEMENT–For Advertiser Information, visit www.STRUCTUREmag.org
Helical Pile Technology
Exclusive Patented Technologies for Foundation Solutions
ESR-1854
ICC-ES Recognized as Code Compliant to Meet International Building Code
Patented threaded connection provides a higher torque rating to penetrate dense soils; Rigid connections to maximize lateral capacity

Up to six different pile diameters in stock to provide the most economical solution to meet any design load

Custom fabrication of piles & brackets for residential, commercial, industrial, and utility solutions
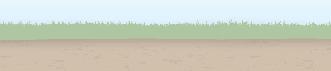

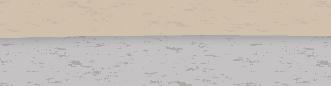
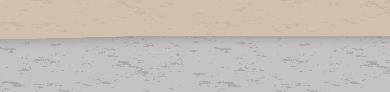
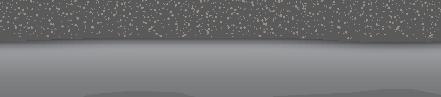
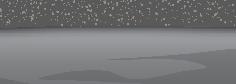


Watch Our Helical Installation Video:
ramjack.com/HelicalTechnology 888.657.0968
Patented threaded connection; Strongest, most rigid in industry
Thermoplastic Helical Piles resist corrosion/ environmentally friendly
Helical Piles stamped into true spiral shape; Penetrates load- bearing strata
Decon® USA Inc.
Phone: 866-332-6687 Email: frank@deconusa.com Web: www.deconusa.com Product: Studrails® Description: e North American standard for punching shear enhancement at slab-column connections. Studrails are produced to the speci cations of ASTM A1044, ACI 318-08, and ICC ES 2494. Decon Studrails are increasingly used to reinforce against bursting stresses in banded posttension anchor zones.
Product: Anchor Channels Description: Decon USA is the exclusive representative of Jordahl in North America. Hot rolled Anchor Channels are embedded in concrete and used to securely transfer high loads. eir main application is for exible connections of glazing panels to high-rise buildings. Anchor Channels with welded-on rebar or corner pieces are available.
Gripple Inc.
Phone: 630-406-0600 Email: grippleinc@gripple.com Web: www.gripple.com Product: Concrete and Metal Deck Insert Solutions Description: e original cable hanger solution for all types of suspended services. Spider: cast-in-place concrete insert solution, designed to prevent accidental movement before or during the concrete pour. Metal Deck Insert: pre-insert solution for metal decks. Both are available as complete kits that include a Gripple cable hanger.
HALFEN USA
Phone: 816-896-4266 Email: pschmidt@halfenusa.com Web: www.halfenusa.com Product: Anchor Channels Description: Halfen is a global leader in design and manufacturing of anchor systems for concrete. Hot rolled anchor channels for edge or top of slab transfer high loads while also providing eld adjustability. Custom anchors are available for special corners and thin slab conditions.
Hardy Frame
Phone: 800-754-3030 Email: dlopp@mii.com Web: www.hardyframe.com Product: Hardy Frame Shear Walls Description: Hardy Frame now o ers pre-engineered anchorage solutions that drastically reduce the large pad footings that have become associated with prefabricated Shear Wall Panels. Standard details are available to include with plan submittals. Hohmann & Barnard, Inc.
Phone: 631-234-0600 Email: weanchor@h-b.com Web: www.h-b.com Product: 2-Seal™ ermal Wing Nut Anchor Description: An innovative Single Screw Veneer Tie for steel stud and concrete construction that features a dual-diameter barrel with factory-installed EPDM washers to seal both the insulation and the air/vapor barrier. e wing section is encapsulated with ul-94 plastic to decrease thermal transfer through rigid insulation and is highly ame-resistant.
IES, Inc.
Phone: 800-707-0816 Email: info@iesweb.com Web: www.iesweb.com Product: VAConnect 2.0 Description: Steel base plates and shear tabs too, are what we will design for you. ose anchor ‘calcs’ (Appendix D) are also dealt with easily.
Kelken Construction Systems, Inc.
Phone: 732-416-6730 Email: ken@kelken.com Web: www.kelken.com Product: Keligrout Structural Anchor Adhesive Description: Keligrout is a superior high strength polyester resin anchoring material with guaranteed pullout values exceeding ACI-349-85. Keligrout can be used in sub-freezing temperatures or in and under water. Every lot of material is guaranteed and certi ed.
Powers Fasteners
Phone: 800-524-3244 Email: engineering@powers.com Web: www.powers.com Product: Type 316 Stainless Steel Wedge-Bolt Description: Powers Fasteners has expanded the popular Wedge-Bolt anchor line to o er a version in Type 316 stainless steel for concrete and masonry. ese new 300 series stainless steel screw anchors are for applications requiring additional corrosion resistance such as railings and exterior attachments.
S-FRAME Software Inc.
Phone: 203-421-4800 Email: info@s-frame.com Web: www.s-frame.com Product: S-CONCRETE Description: S-CONCRETE displays instantaneous results as you optimize and design reinforced concrete walls, beams and columns. Automate your work ow by checking thousands of concrete section at once. With comprehensive ACI1 318-11 design code support, S-CONCRETE produces detailed reports that include clause references, intermediate results and diagrams. Product: S-FOUNDATION Description: Quickly design, analyze and detail your structure’s foundations with S-FOUNDATION, a complete foundation management solution. Run as a stand-alone application, or utilize powerful 2-way integration links for a detailed soil-structure interaction study. S-FOUNDATION automatically manages the meshed foundation model and includes powerful Revit and DXF data links.
Simpson Strong-Tie
Phone: 800-999-5099 Email: web@strongtie.com Web: www.strongtie.com Product: Simpson Strong-Tie® Blue Banger Hanger® Description: Blue Banger Hanger has received the rst International Building Code (IBC) report issued for a specialty cast-in-place insert. e code report (ICC-ES ESR-3707) is the rst one for this type of anchor under ICC-ES AC 446. It covers all sizes of Blue Banger Hanger wood form inserts.
Product: AT-XP® Fast-Curing Anchoring Adhesive for Cracked and Uncracked Concrete Description: AT-XP is a fast-curing anchoring adhesive formulated for high-strength anchorage of threaded rod and rebar into concrete under a wide range of conditions. AT-XP adhesive dispenses easily in cold or warm environments with little to no odor. It has demonstrated superior performance in reducedtemperature testing (14°F (-10°C)).
StrucSoft Solutions
Phone: 514-731-0008 Email: marketing@strucsoftsolutions.com Web: www.strucsoftsolutions.com Product: Metal Wood Framer Description: A template-based and rule-driven extension to Autodesk® Revit® for framing. It empowers users to automate the modeling, clash detection & manufacturing of light gauge steel and wood framing including shop drawings, cut lists, BOM, optional CNC output & more.
Tekla
Phone: 770-426-5105 Email: kristine.plemmons@tekla.com Web: www.tekla.com Product: Tedds Description: Tedds Anchor Bolt and Column Base plate modules analyze cast-in-place and post-installed anchors in concrete. It covers ACI Appendix D along with multiple generations of the ACI 318 codes. Its ease and speed of use have made it a vital addition to many engineering rms around the world.
All Resource Guide forms for the 2015 Editorial Calendar are now available on the website, www.STRUCTUREmag.org.