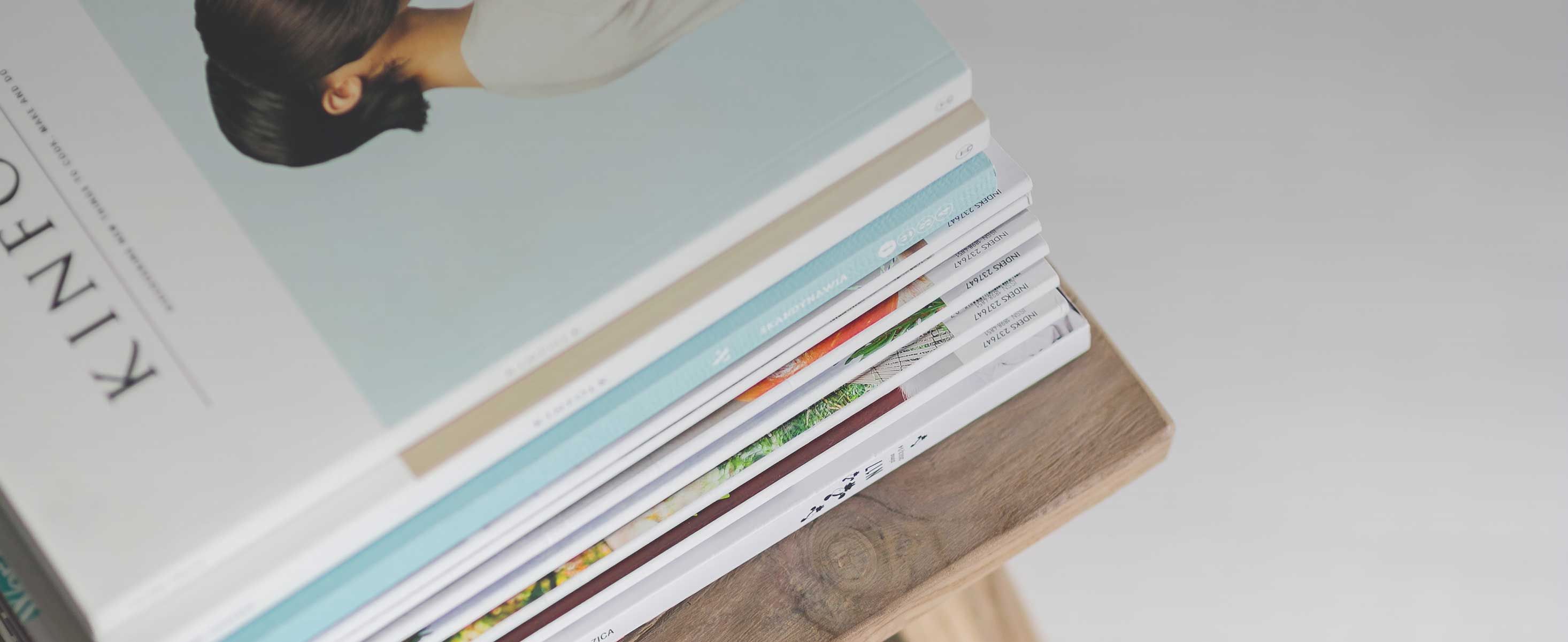
9 minute read
Maintenance Committee
The members of the maintenance committee are Father Peter, Deana Bottei, George Stickney, Sr., Nick Corey and Mike Jacobs. I was asked to chair the committee on or about July 8, 2020. I wish to acknowledge the able and tireless efforts of De Bottei who preceded me as the chair. She continues to clean the church on a weekly basis. All the other committee members have similarly made significant contributions to the efforts of the committee and those efforts are likewise appreciated.
The following is a list of tasks (in no particular order) which have been identified and/or undertaken in 2020. These projects have been funded in large measure through the Building Fund. This was established by the parish council using the proceeds received from the sale of the parish house.
Advertisement
1. Nina’s Nursery was painted and updated. We do have a $6,800.00 bid from Mpire Heating & Cooling to add an air handler and air conditioning to Nina’s Nursery. No action has been taken on that bid.
2. We entered into a Preventative Maintenance Agreement with Mpire for the HVAC system at a cost of $4,600.00 per year. Mpire is to provide quarterly filter changeouts on all equipment, seasonal changeover of chiller and boilers, cleaning of condensers and operational checks of all mechanical equipment. On December 30, it was discovered that the heat exchanger on one of the boilers was clogged beyond repair. According to Mpire, the other boiler, which was supposed to provide redundancy (i.e., backup), is undersized for our building. The committee is investigating our options.
3. Mpire’s work in re-doing all of the drip trays for the radiators has been delayed due to COVID but, hopefully, will resume and be completed soon. They also submitted a bid of $1,260.00 to replace the heating unit in the southeast stairwell adjacent to the men’s restroom with a hanging downflow hydronic heater. It was deemed too expensive and not a priority at this time.
4. Thanks to Frank Brienzo and Dee Skaff for arranging to have the front door stripped and re-finished. This has greatly improved the appearance of the front of the church.
5. Also, thanks to Frank for having the cemetery chapel cleaned up and re-finished.
6. Again, thanks to Frank for having the weeds in the parking lot on the west side of Jones Street sprayed by Jay-Lan.
7. Thanks to Nick Corey for having the retaining wall that prevents the west parking lot from falling into the Lutheran church parking lot rebuilt, fortified and repaired.
8. Thanks to Matt Ameen for cleaning out the vegetation, gravel and debris in the trench drain in the main parking lot. This was necessary to make sure that the winter snow and ice melt will flow to the alley and not place any additional undue stress on the lot and the retaining wall.
9. The sign out front was fixed so that it could be accessed and updated.
10. The damage done to the access ramp to the front porch was repaired.
11. All new locks and keys were obtained at a cost of $1,273.97.
12. Coughlin Landscaping cleaned out and trimmed the overgrown shrubbery on the north and south sides of the church. This was at a cost of $3,390.00 which was a lot of money. It was deemed necessary for two reasons: (1) to get the shrubbery away from the brick and mortar of the building and; (2) to improve the outward appearance of the church. It is now incumbent upon the members of the church to properly maintain the landscaping and shrubbery to avoid the expense of hiring this out in the future.
13. Sarah’s Stitches re-upholstered the pews with commercial grade padding and fabric at a cost of $8,998.70. This was financed for the most part from donations received in memory of Esther McDaniels. Jack from Sarah’s Stitches said we should be satisfied with the 17 years we enjoyed from the previous re-upholstering. It was done with residential grade fabric because of the budget the church had at the time. He emphasized the need to exercise appropriate precautions in the future with this new fabric. Even commercial grade fabric will not stand up to candle wax.
14. In June, 2020, we retained Steve Bruening of Draco Engineering for $1,500.00 to do a site evaluation and generate a report with recommendations. Steve has been an invaluable resource. He has made several return visits and responded to numerous emails and phone calls to assist the committee in its efforts to prioritize its work.
15. Steve concluded the overall condition of St. Thomas was “good” and that the “building has performed well for 70 years.” His main concerns were: (1) the parking lot retaining wall failure; (2) the masonry deterioration of the bell tower and; (3) the settling of the northeast corner of the “New Addition.”
16. At Steve’s recommendation we also enlisted the services of Certified Testing Services, Inc. In July, they did a “geotechnical exploration” (i.e., a soil sample) at a cost of $1,650.00 and in August they did a floor survey at a cost of $500.00. These were very useful, and Steve Bruening thought essential, in identifying the scope of the work necessary to address the northeast settling issue and to provide some insight into the retaining wall/parking lot issue. For example, after these tests both contractors bidding on the northeast corner settling issue, Thrasher, Inc. and Concrete Specialty, Inc., re-worked their estimates and scopes of work and substantially reduced their bids.
17. Thrasher’s original bid was $29,500.00 and Concrete Raising’s was $28,000.00. After the Certified Testing reports, their scopes of work were revised. The bid we ultimately accepted from Thrasher for the stabilization work to be done commencing on February 2, 2021, was $16,184.00. Please note this is intended to stabilize but not lift the northeast corner. The consultants and the contractors agreed trying to lift the northeast corner of this all-brick structure was too risky to the integrity of the brick and not necessary to cure the problem. Also please note, this bid does not account for replacing the tile floor along the east wall of the kitchen when Thrasher’s work is completed. That will be an added expense.
18. A major manifestation of this settling issue was a significant gap running basically the entire length of the vertical joint between the new addition and the old structure on the north exterior wall of the building. This gap has already been patched by Western Specialty Contractors at a cost of $2,700.00. (Western also did some miscellaneous tuck pointing across the north wall as a part of this expense). Both Western and Thrasher assured us that this repair of this vertical joint would withstand Thrasher’s stabilization efforts in February.
19. On July 30, 2020, Steve Bruening and a roofer named Lee Knop did a thorough interior inspection the Bell Tower. They went all the way up into the dome itself. This coincidentally was one day after a tremendous rain storm. The interior was dry. This was followed up by an exterior inspection performed by Steve Bruening and the crew of another roofer, Jerry Croxen. Jerry’s crew did the roof installation in 2007. They were satisfied that neither the roof nor the bell tower was allowing rain infiltration at that time. Nonetheless, it was obvious that the brick and mortar were severely deteriorated and needed attention to help prevent future water infiltration and to prevent the brick from becoming dislodged and falling to the porch.
20. None of the roofing contractors were interested in bidding on this bell tower repair. It is somewhat of a specialty in the concrete trade. Steve Bruening had experience with Western Specialty Contractors out of Omaha, NE. They proposed to rebuild the northwest corner of the bell tower; re-point the rest of it and then clean and seal it at a cost of $21,450.00. By all outward appearances, it appears they did a nice job although they have agreed to return to re-point some additional mortar joints further down the bell tower. I was assured there was simply a misunderstanding between the estimator and the crew that actually did the work.
21. While maneuvering their manlift to work on the bell tower, Western damaged the concrete panel making up the walkway from Jones Street to the east/west public sidewalk in front of the church. Although we already had a bid from Concrete Raising Services to even up and fill voids under some sidewalk sections including these, Western’s damage was such that they ended up busting out the entire panel and repouring it. As a result, we wound up with a brand new section of sidewalk.
22. It is obvious to all observers that in the back corner of the main parking lot, the retaining wall has failed with the middle of the wall severely bulging out while the concrete curb and fence at the top have tipped inward. Also, the pavement in this area has settled. The great unknown is just how much of the parking back to the south of this failed portion of the wall, has been undermined or has voids. The soil sample helped but the true extent can only be revealed once the concrete is removed and remedial efforts commence. We have bids ranging from Andreas Barboza $9,200.00 to Mpire Heating & Cooling $27,000.00 to L&L Builders $30,610.00. Coughlin Landscaping requested $2,500.00 to properly engineer the issue but estimated that to properly address the problem could easily cost in excess of $100,000.00.
23. All have agreed we should be able to survive at least one more winter. We are expecting another bid from Western Specialty Contractors in the coming weeks.
24. We have a bid from Concrete Specialty to patch the front porch at a cost of $700.00. Steve Bruening thinks this is adequate and more than one contractor concurred. We have had all kinds of opinions on what needs to be done to prevent suspected water infiltration into the basement, most noticeably on the back wall of the stage. Steve does not think this is caused by any major leaks. He attributes this to moisture efflorescence which is the natural movement of a certain amount of moisture through dirt and concrete which then turns to condensation when there is not proper ventilation. He advocated for a good patch of the cracks on the front porch and a good seal of the porch between it and the front of the building (and repeated attention to those repairs on a periodic basis) as opposed to busting out the entire front porch and attempting to completely rebuild it. If this works, it needs to be followed up with a good cleaning of the stage wall and then leaving the doors and curtains to the stage open most of the time to allow for greater movement of the humidity and the air.
25. Concrete Raising assured us they would still be willing to do this work to patch and seal the front porch even though they did not get the northeast corner stabilization job, but said they were too busy to get to it in 2020.
26. We have had Mozak Furniture out to look at the flooring issues both upstairs and downstairs but have given those projects lower priority in light of the projects described above. Also, we would like to get the radiator drip tray replacements in place and make sure they work before spending money on new flooring in the sanctuary.
Mike Jacobs