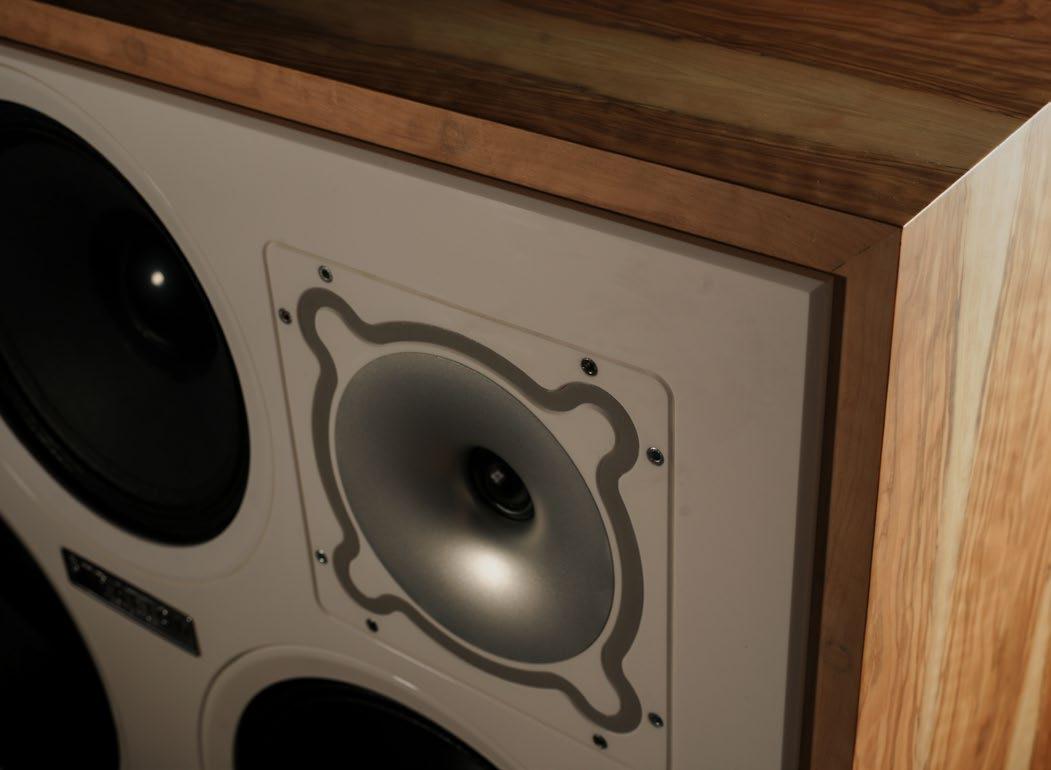
4 minute read
STRATTON ACOUSTICS
generation to generation, mine are strange things like battered Victorian leather stitching clamps (my great-grandfather was a cobbler) and a wonderful brass microscope (my grandfather was an amateur botanist) and my father’s engineering tool chest.
These objects are metaphors for family values and represent family stories that are told and retold. Our goal is to aid in the creation of those stories with our customers and their families in creating products that are metaphors regardless of the level of finish they wish to explore.
NB: Where are your speakers fabricated?
DF: We build entirely within the UK. In fact all of our partners are based in the same region so we can work hand-in-glove with them on each and every pair 1512’s.
Examples of this are that we don’t work with mass-manufactured loudspeaker cabinet builders but instead work with some of the finest bespoke furniture makers in the UK. Equally, when it comes to our machined components, we work with leading vendors in the automotive and aerospace sectors to achieve the quality we require; their machining is more like engineering art than it is metalwork.
Naturally we use bought-in components from a variety of global brands as the very highest performing and most consistent components are often made outside of UK shores. But as far as our cabinet construction, finishing, matching, fabrication, assembly, quality control, kitting and shipping is concerned, everything is made within the UK and always will be.
NB: How important to the brand’s values is it that you use British manufacture and finishing in the construction of your speakers?
DF: It’s a fundamental part of our value set. In the same way as Swiss watches are made in Switzerland, Stratton Acoustics products will always be made in the UK. There are two fundamental reasons for this, the first is quality control; we want to be able to physically see the smallest detail of every single product, not via some emailed photographs on a QC inspection sheet but with our own eyes and to feel the quality of finish with our own hands.
Secondly, is that due to recent changes to the UK’s status within the EU….as in we begrudgingly aren’t part of it anymore… we feel compelled to manufac- ture in the UK. Without the great institutions of free access to education, information and healthcare that are so fundamental to the fabric of the UK I wouldn’t have had the education I have been so fortunate to have. I want to contribute to the country I owe so much to and to assist in some small way in helping the economy, we want to play our part.
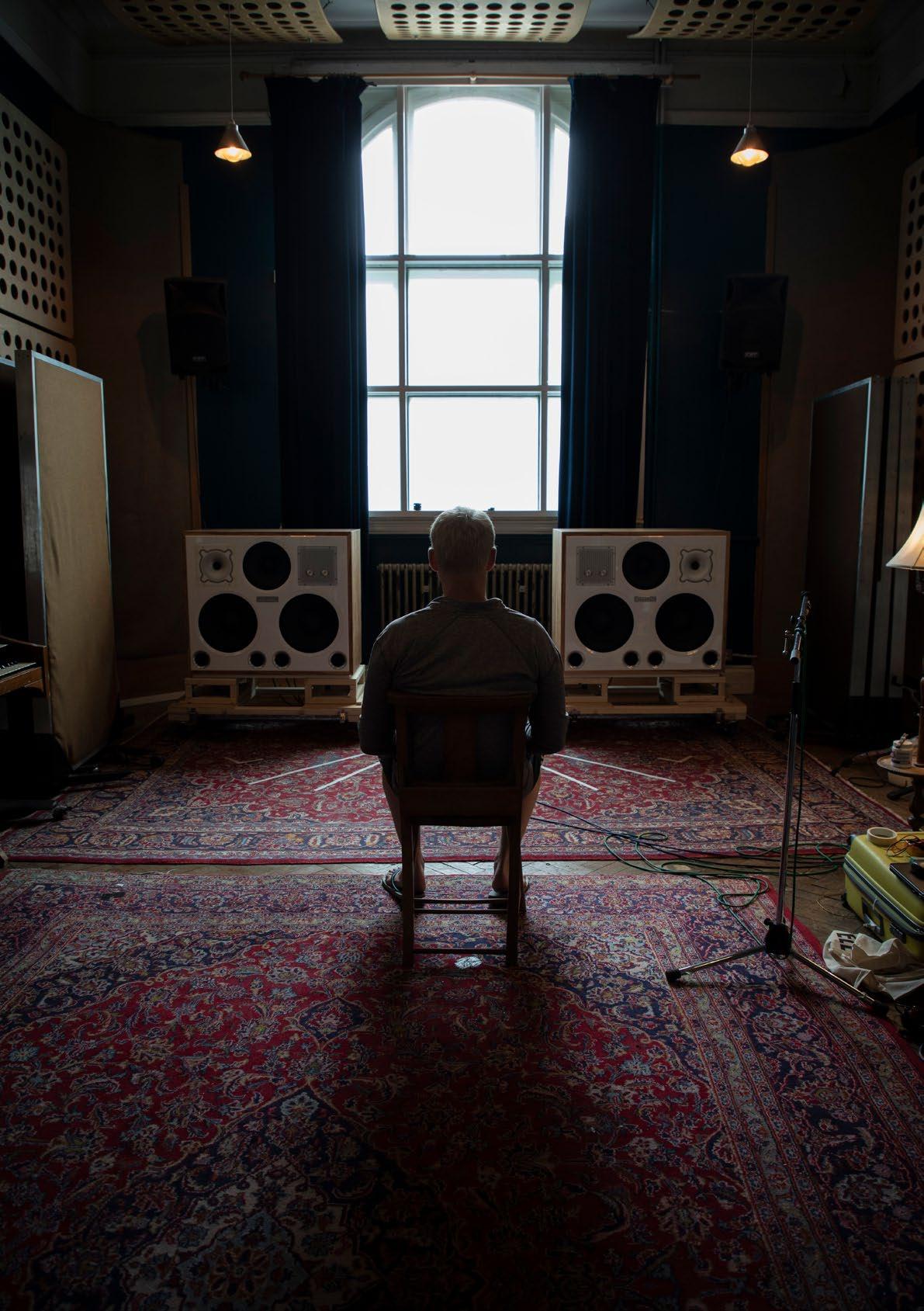
NB: How do you feel that Stratton Acoustics, over and above any other brand out there can create this heirloom status? I suppose the question here is how does a company go about building a reputation where their products are seen as something people will want to pass down to their children?
DF: The nature of heirloom is an interesting one. When we consider heirlooms throughout history they are usually defined as being items that transcend trends, are built to a quality not a price and prove to be functional in their given roles throughout their lives. They are usually produced in small numbers by passionate, driven people who love what they do. When I think of this I think of Martin, Stradivarius, Steinway as much as I think of Chippendale, Aston Martin, Patek and Breguet.
We are not so egotistical as to compare ourselves to such legendary brands and craftspeople, but we can at least aspire to the values that made these products legendary and of heirloom quality. In so doing we have a chance of engendering the same recognition and emotional attachment with our customers, their children and their grandchildren and in time may be recognised as true heirloom products.
NB: Tell us a little about the design of the speakers.
DF: It’s difficult to know where to start, but at the beginning is the usual answer. When we decided to embark on this path it was partly in reaction against the inherent physical limitations of smaller diameter loudspeaker drivers.
Smaller drivers have to work harder to move enough air to play at adequate volume. As they don’t have the diaphragm area, they have to compensate by increasing their excursion. And as diaphragm excursion increases so does compression, colouration and distortion as multiple motor system non-linearities arise, the voice-coil heat up, and the suspension and surround flex non-linearly. Dynamics suffer of course as small diaphragms have to accelerate and decelerate over a significant physical distances - they just cry, “enough!”. With small diaphragms it’s simply difficult to keep the noise floor (any output that’s not present in the input signal) of the speaker adequately low.
Given that smaller drivers have these issues, all of which fundamentally challenge our enjoyment of music, we chose to take a different path. If small drivers introduce these issues, then we simply won’t use them, and the results are remarkable. Bass has unambiguous pitch, texture, harmonics, dynamics and richness. Midrange has a palpability and tangibility with amazing transparency, and, again, dynamics that make vocals feel immediate and present.
An illustration of this is a demo we do for people when listening at higher volume levels. We ask them to touch the bass and midrange drivers. Most small drivers will be working hard at these levels and moving at least ±5mm or more. With the 1512 however the drivers will hardly be moving at all; at most between ±1mm. Needless to say this isn’t even close to approaching the maximum excursion for the drivers so, we minimise all of the diaphragm excursion issues at a stroke. The Elypsis1512 odd order harmonic distortion for example, at typical listening levels, is around 0.3% – closer to amplifier distortion levels than those usually measured in speakers.
Our tweeter is a large soft done and employs a waveguide to optimise both its dispersion and acoustic impedance matching. We have also mechanically isolated it with the goal of eliminating any spurious energy from affecting the tiny amplitude of the dome.
Everything else has been done to support the drivers in doing their best work. Our cabinets are massively braced furniture grade Latvian birch plywood with no internal voids. In fact they are akin to bracing with a skin rather than a cabinet with bracing. We have a separate internal midrange enclosure and another one for the tweeter. The midrange enclosure has non-parallel side panels and a tapering, resin filled back panel to minimise internal resonance and is independently braced as well of course. The tweeter enclosure pneumatically isolates the tweeter from the energy within the woofer cabinet.
The 1512 crossover is split into front panel mounted HF/MF module and a separate LF crossover at the rear of the cabinet floor. Both are housed in fabri-