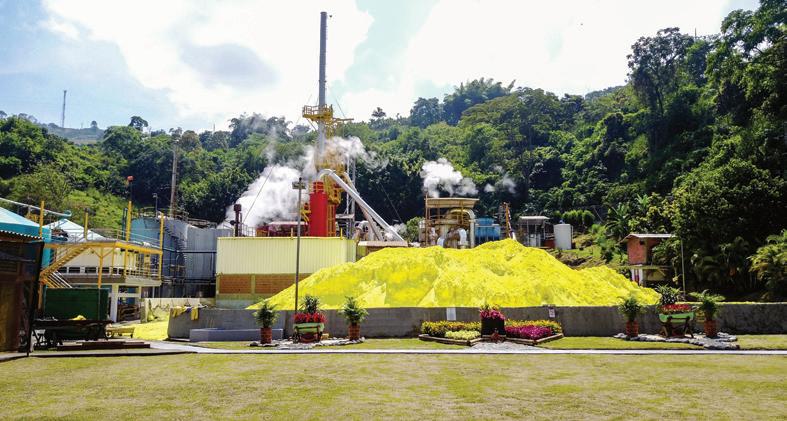
8 minute read
Trash to treasure: IBC reroutes waste SO 2 into sulfuric acid production
When the Colombian government tightened regulations on how much sulfate waste was permissible in wastewater, both Industrias Básicas de Caldas (IBC) and its customer next door were faced with a challenge. IBC supplies SO3 to an adjacent sulfonic acid facility that was releasing wastewater effluent with sulfates—and now the sulfate content must be reduced by at least 90%. After thoroughly testing several possible solutions, the final plan not only brought wastewater into compliance, but recycled SO2 into increased sulfuric acid production and netted a host of other benefits to boot.
About IBC
Located in Manizales city, IBC produces sulfuric acid and provides diluted SO3 gas for a neighbor sulfonation facility. The company was established in 1988 by parent Química Básica Colombiana in association with investors from Caldas to serve the growing sulfuric acid market in central Colombia. Construction of the sulfuric acid plant began that year on the outskirts of Manizales city and by 1990 the first tons were produced and sold. In 1991, another investor built the sulfonic acid plant to use the SO3 supply from the sulfuric plant in the sulfonation process.
The sulfuric acid plant was designed and constructed by Conpancol-Ingenieros
Constructores (a subsidiary of Panamerican Consulting International Ltd.) with conventional technology—direct burning of sulfur followed by catalytic conversion via the contact method with double absorption in a (3+1) arrangement. Process gas flowed through the converter where most of the SO2 gas was converted to SO3. About 10% of the SO3 stream and remaining SO2 stream exited bed 3 and flowed to the customers’ sulfonation plant where the SO3 was used to make sulfonic acid and other surfactant products. Then the remaining stream was cleaned of SO2 and the clean gas released to the atmosphere.
This process worked well for many years while the sulfuric plant’s capacity remained at 100 MTPD. But when capacity increased to 125 MTPD in 2012, the sulfonic plant consumed much more caustic soda to clean the additional SO2 coming from the sulfuric plant’s converter, which in turn significantly increased the flow of sulfites and sulfates in the sulfonic plant’s wastewater. Then, in 2015 when the Colombian government passed stricter regulations for cleaner wastewater, both IBC and its SO3 customer began their quest for a resolution.
Researching the return-gas plan
The new regulations allowed the plant five years to transition its process to compliance level. “The challenge,” explained IBC’s plant manager Héctor González, “was to research and implement an economical, functional, safe, and sustainable solution to remove 90% of sulfates from our customers’ wastewater or prevent their generation all together.”
An interdisciplinary engineering team of professionals from both sites was created to work on the project. After considering the risks, costs, and benefits of several options including replacing the converter and treating wastewater with reverse osmosis, the team determined the best long-term
By: April Smith, Editor, Sulfuric Acid Today
solution was to return the SO2 gas stream back to the sulfuric plant, recover the SO2, and use it to make sulfuric acid. With the plan decided, both plants engaged in two years of feasibility testing to determine the best way to implement it.
Preliminary analysis considered the impacts to both plants given various gas entry points into the sulfuric plant. The team studied three possible entry locations: the drying tower, the converter, and the intermediate absorption tower (IAT). For each location, the team evaluated the pressure required to inject the return gas, the effect of the additional volume of gas, and the gas composition.
The pressure required depends on the distance between the main blower’s discharge and the gas injection point. The team had to select a blower that was suitably powered to accomplish the job, but not over-powered as to waste electricity.
The additional gas volume implies greater pressure loss of the equipment and an increase in flow rate through the beds of the converter, which in turn reduces conversion.
Finally, the composition of the gas is an important factor in the system. “The returning gas has a lower oxygen content than air and therefore will have a negative effect on conversion if fed to the first bed of the converter, but a positive effect if fed to the third or fourth bed of the converter,” said González. “Also, impurities in the return gas, particularly moisture and organic mist, can affect the catalyst, increase cor- rosion, and reduce the quality of the sulfuric acid,” he said.
The team conducted a total of eight tests, analyzing results and modifying the system after each. They began with six tests that returned the gas stream to the IAT; then completed two additional tests directing the flow to the drying tower. Testing the return to the converter ultimately became unnecessary.
Testing: return gas to intermediate absorption tower
For the first six test runs, exit gases from the sulfonic plant were redirected to the intermediate absorption tower of the sulfuric acid plant. A 10” diameter pipeline was installed to connect the plants and a centrifugal blower (50K1) was installed to move the gases. The direction of the gas flow was controlled by an HV01 control valve and pressure transmitters in the suction and discharge lines of the blower. sulfur burner was the way to go and began implementation plans. The team worked with its catalyst supplier, Topsoe of Denmark, to further improve conversion.
There was also very high turbidity in the sulfuric acid that increased as the return gas flow increased (see Fig. 2).
“The new feed to the converter had a higher gas flow rate with a lower O2/SO2 ratio, which made the conditions more challenging for the catalyst,” explained Martin Alvarez, Solution Specialist at Topsoe. “Plus the existing converter had no free room available since the capacity had already been boosted 25% in the past,” he said.
The first test ran for 52 hours and results were mixed. Important successes included reducing sulfate content in the scrubber to below the new regulation level as well as significantly reducing consumption of caustic soda. Plus more than 80% of the SO2 present in the return gas was converted to SO3 in the fourth bed. However, the increased return gas flow (above 2.900 Nm3/h) resulted in considerable acid mist and a positive stick test in the IAT. At this point, the team stopped the test and determined the acid mist was caused by humidity in the gas stream from the sulfonation plant. So before the next test, the team identified the root cause and fixed the issue.
Because of turbidity and the high pressure drop, the team decided to try a variation of option two from the initial planning phase. The original plan directed the gas to the drying tower inlet, but the variation returned the gas directly to the sulfur burner (see Fig.3). The team ran two tests on the new flow design.
Topsoe ran simulations to determine the catalyst requirements needed to reach emission compliance while also minimizing costs. The team decided on an additional catalytic bed (a “pre-bed”) external to the converter positioned just before bed 1. Topsoe supplied 5.5m3 of vanadium catalyst for the new 3.5-m diameter, 304-stainless-steel vessel and replaced existing catalyst in beds 1 and 2.
Using the pressure loss data collected during testing, the team also defined specifications for a new blower capable of feeding all the return gas with no significant pressure loss in the equipment while both plants operate at capacity. For this, a two-stage, 3600 rpm, 450 mbar centrifugal blower was selected and purchased from FIMA, a supplier based in Germany.
To deal with strong and continuous changes of suction gas pressure, the team implemented a redundant and advanced control system. This was designed and installed by DCA Technology of Colombia.
Through the next three cycles of testing, analyzing results, and adjusting, the team moved the system closer to their goal. In addition to fixing the acid mist problem, they adjusted the inlet temperature to the converter’s third and fourth bed which increased conversion and reduced SO2 emissions from the sulfuric acid plant. They also achieved 100% gas return with the sulfuric plant operating below 100 MTPD. “This marked a significant milestone in reaching the required regulatory compliance and eliminating caustic soda consumption,” González said.
The next two test cycles focused on determining the maximum amount of SO2 that was possible to recover with the sulfuric acid plant operating at maximum capacity of 125 MTPD.
The results of these tests were a significant reduction in SO2 emissions and no acid mist in the IAT. But inlet pressure and pressure drop at this tower were very high with further pressure issues in downstream sulfonation plant equipment.
Feeding the gas return to the sulfur burner was very successful on several fronts. Pressure drop of the process equipment remained within normal ranges and the turbidity issue was resolved. The quality of the acid also met company specifications and there was no acid mist in the absorption towers. Sulfuric acid production increased by 10% to 114 MTPD for the same main blower discharge pressure, over 80% of sulfonic plant exhaust gas was returned, and SO2 emissions were within acceptable limits.
There was a clear reduction in caustic soda consumption by the scrubber as the HV01 valve was tightened to narrow the inlet and more gas was returned (see Fig. 4). Zero consumption was reached when the gas was returned completely by fully closing the HV01 valve.
Implementing the plan
Given the positive results of these last two tests, the team decided returning the gas to the sulfuric acid plant’s
The converter pre-bed was installed by Construcciones Montajes y Mantenimiento (CMM) of Colombia in July 2020 with the blower and control system installations completed later that year. By December 2020 the new system started operating at 120 MTPD capacity, returning 100% of the gas from the sulfonation plant. At maximum capacity of 125 MTPD however, the maximum recirculated gas was 90%. In both cases though, the new system complied with regulations on gas emissions and sulfate level in wastewater.
Some final tweaking to raise production capacity to 130 MTPD and eliminate bottlenecks was conducted during a general maintenance shutdown at the sulfuric plant in February 2022. The process gas-gas exchangers were replaced, catalyst in the pre-bed was increased, air fans were installed in the acid cooling tower distributors, and the final absorption tower internals were changed out. The changes enabled production greater than 130 MTPD, however returning 100% the gas was possible only when operating below 120 MTPD.
Results
Along with increasing sulfuric acid production capacity to 130 MTPD, implementing the gas return system generated these benefits:
• SO2 emissions: reduced by more than 7.000 kg/year.
• Water consumption: reduced by over 3.500 tons/year.
• Sulfur consumption: reduced by more than 200 tons/ year.
• Sulfate discharge: reduced by more than 300 tons/year.
• Caustic soda consumption: reduced by more than 500 tons/year.
• Cost savings: more than $300,000 USD/year from reduced consumption of raw materials, supplies, and resources.
These achievements, from cost savings to the many environmental benefits gained by both sites, closely align with IBC’s corporate vision of providing value in a framework of conduct that is deeply responsible of people, society, and the planet. q
What is the real cost and danger of having inexperienced people on the job?
How much is 10-20% of your screening catalyst worth?
What does it cost for an extra day of down-time or worse yet, what does it cost to shut down to repair something that should have been caught during your last outage?
Is VIP expensive? Look at the value.
When you add it up… VIP Service pays for itself.
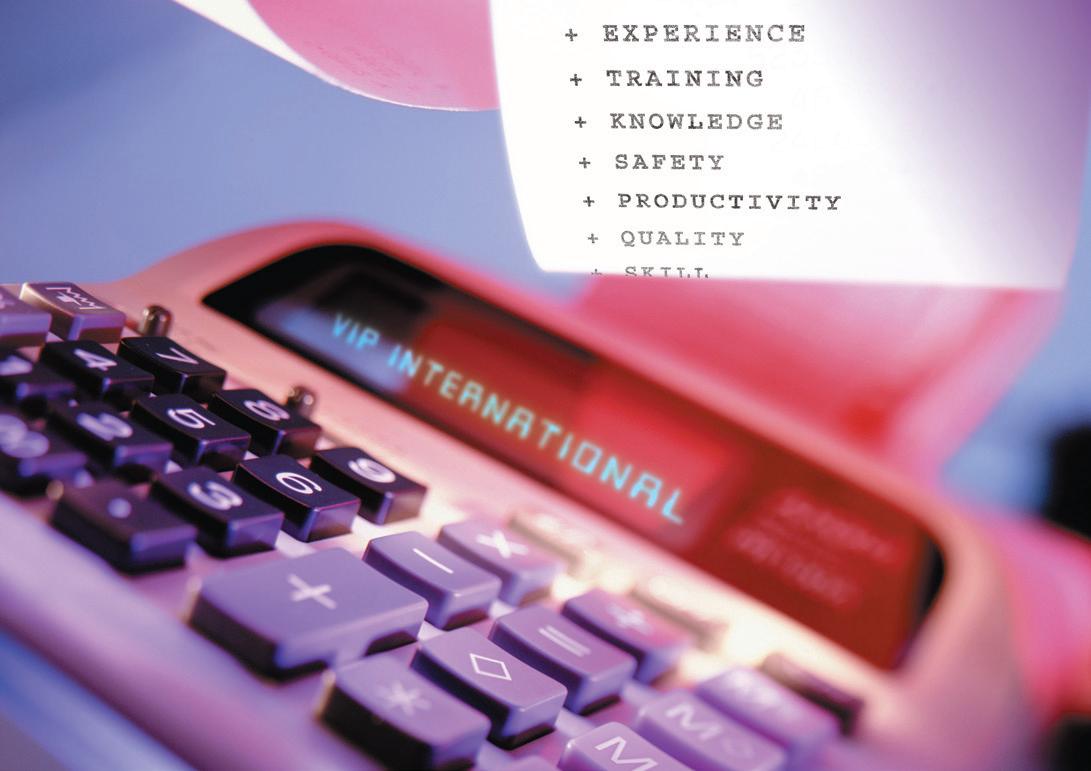