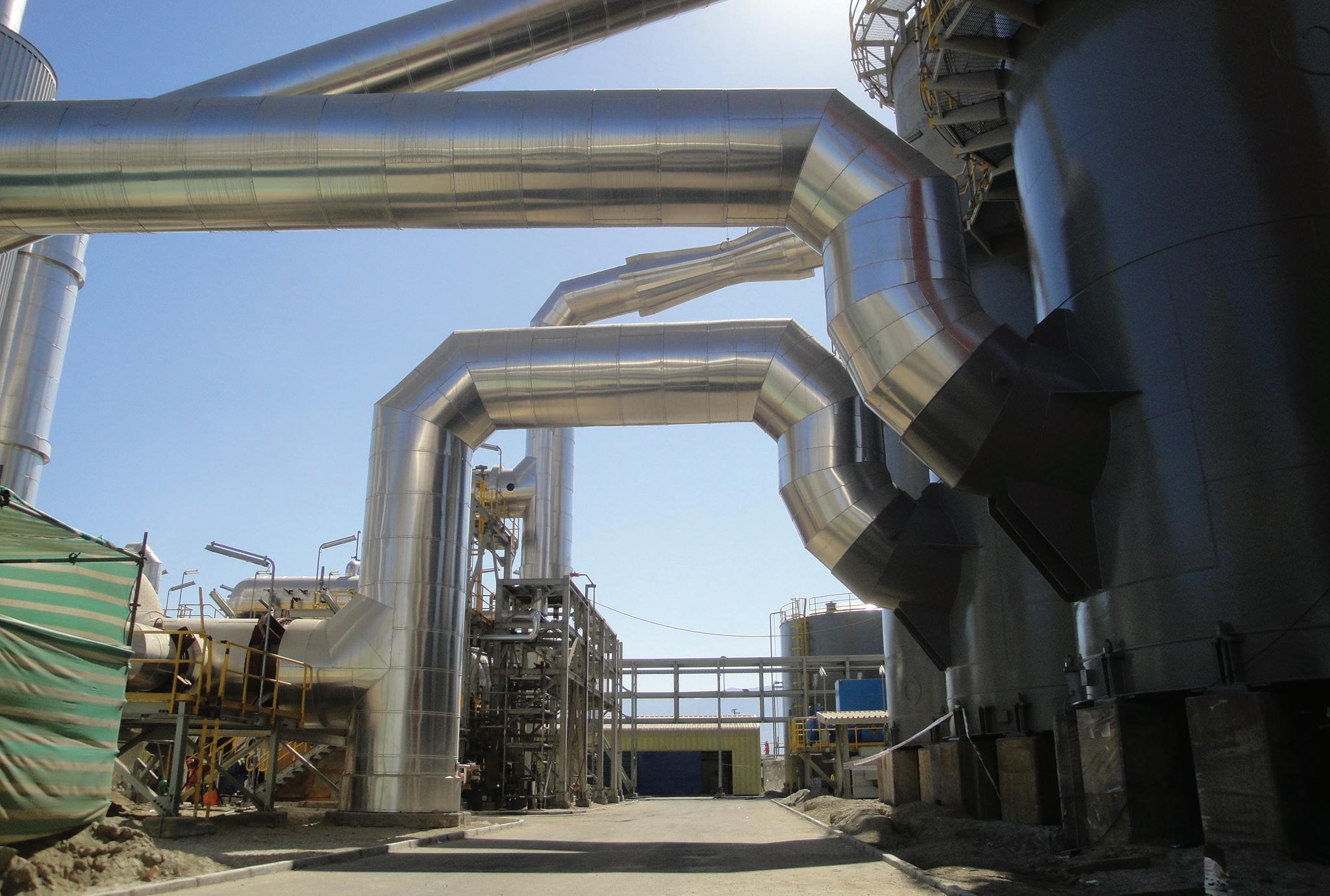
27 minute read
Noracid marks ten
Noracid: A decade of progress
By: April Smith, Editor, Sulfuric Acid Today
Noracid is marking its ten-year anniversary manufacturing sulfuric acid at its plant in Mejillones, Chile. Over the last decade, the facility has been stalwart in supplying local copper mining operations with the necessary ingredient for separating metal from ore. The plant has also been a model for longevity and plant availability. Recently Noracid’s managers, together with representatives from the plant’s designer, Metso Outotec, reviewed the facility’s performance and cataloged its operational statistics. They reflected on the how the design and maintenance practices have driven the plant’s success; and consider what needs to happen next to keep the facility performing optimally in the decade to come.
Noracid’s founding
Noracid was founded in 2007 to supply sulfuric acid to the key mining companies in the northern region of Chile. The plant came online in 2012 and was the country’s first large-scale producer of sulfuric acid, which it manufactures from the combustion of elemental sulfur. The plant’s proximity to the Mejillones port on the Pacific Ocean facilitates the movement of supplies and products. In addition to sulfuric acid, Noracid imports sulfur for use as feedstock and to sell to regional markets. The facility also generates electricity using heat released from the acid production process, and delivers it to the local power grid.
Noracid began as a business consortium between Grupo Ultramar and Belfi. Grupo Ultramar provides marine port handling services, shipping, freight, and other logistics services. Belfi is an engineering and construction company; it provided the construction services that built the Noracid plant. Metso Outotec was granted the contract to design and supply the plant in 2009, and construction began the following year.
The products
Noracid consumes 240K tons per year of sulfur as feed stock to its acid operation. Bulk solid sulfur is also distributed to the iodine industry and boric acid manufacturing plants located in northern Chile and Argentina. On-site sulfur storage capacity is 100K tons.
Sulfuric acid manufacturing capacity is 720,000 tons per year with storage capacity at the Mejillones terminal of 40,000 tons. From storage, 2,000 tons are transported daily, by trucks and trains, to mining operations in northern Chile.
The plant also generates electricity by channeling the heat released from acid production into a steam turbine. The cogeneration process has a capacity of 26 MW. Of this, 9 MW is consumed at Noracid’s facilities while the surplus 17 MW is delivered to the local power network. Operating independently from the local power supply provides the key benefit of enabling continuous operation in the event of an outage in the public power network.
Milestones
Noracid has logged a strong performance history over the last ten years. “Their results in terms of availability and utilization of the plant are very high, particularly with regard to availability,” said Collin Bartlett, Director of Business Development at Metso Outotec. “Average availability is greater than
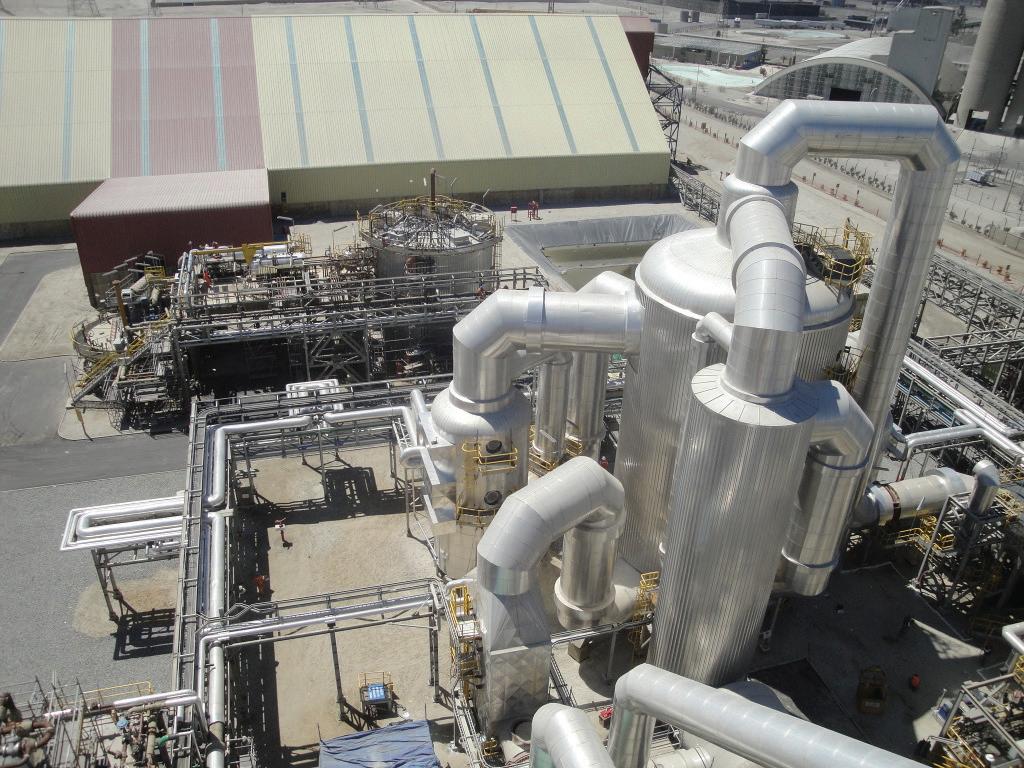
Converter section (foreground) with sulfur melting and covered sulfur storage (background). Noracid marks ten years of service at its sulfuric acid plant in Mejillones, Chile.
98.5 percent and they’ve had few unscheduled shutdowns.”
From 2012 through 2021, unscheduled shutdowns averaged once per month for a period of 6 to 8 hours. And in all of 2020, unscheduled outages totaled only two days. These shutdowns were typically because of high vibrations of the sulfur burner, repairs to an expansion joint, or replacement of an acid recirculation pump.
The plant’s operational timeline shows long stretches of continuous production. Since mid-2012, the plant has run for 24 to 36 months, pausing in between to carry out three main shutdowns.
How did the plant achieve this success? Noracid and Metso Outotec credit two main factors: a robust design and an exacting maintenance protocol.
Design for longevity
In 2009 when the design phase began, the term “sustainable” was not the buzz word it is today. Yet Noracid’s vision, carried throughout the project, was rooted in sustainable principles.
“From the beginning, Noracid focused on reliability and operational cost efficiency,” said Bartlett, “and they have been willing to consider incrementally higher capital cost to reduce operating costs over the lifecycle of the plant.”
A few of the ways in which these principles manifested was in a design that maximized electricity generation as well as minimized overall water consumption. For the electricity piece, the facility integrated a steam turbine, which has consistently powered the entire operation, while also supplying 17 MW/year to the local power grid. In terms of water usage, a plan was formed to minimize both water consumption and energy use.
Rather than implementing a water-based acid cooling system, which is standard for the industry, Metso Outotec designed an airbased cooling system instead. A water-based system would require desalinating the water before using it in the cooling process and then draining warmed effluent water into the Bay of Mejillones. Since local regulations at the time limited temperature increases in the bay, cooling by air made much better sense. “It was a fairly unique solution in the acid industry,” said Hannes Storch, Vice President at Metso Outotec.
There was ample space on site for the cooling system, plus powering it from the facility’s own electricity supply provided an extra degree of plant independence.
Planning for long-haul efficiency also meant the design would be capable of meeting current and future SO2 emission standards.
Sustainable sulfur storage was another
significant feature. There were no sulfur pits, which eliminated the associated maintenance and emissions. Covered sulfur storage limited the amount of corrosive dust settling in the plant or migrating to the local township. Over time, ingress of salt and sand into the sulfur melter has been minimal, contributing to more stable plant operation and higher availability.
Overall, a robust process design and plant layout has enabled the plant to operate under very stable conditions with less chance of process upset and less wear on equipment.
Maintain for longevity—the four pillars
Birthing a plant is one thing. Care and feeding is everything else. Noracid has carried out strong maintenance protocols since the beginning with a strategy based on four key pillars: condition-based maintenance, well stocked critical spares, efficient turnarounds, and a support network of industrial specialists.
Pillar 1: Condition-based maintenance
Noracid’s maintenance program involves careful monitoring of three main conditions: vibration, corrosion, and temperature.
Vibration is monitored online using the Intellinova System on the main process equipment: sulfur burner, primary air blower, water feed pump, acid pumps, sulfur pump, and cooling system pumps. Vibrations are viewed in the OSIsoft PI System and the data is collected to create history and equipment alarm set points. The main blower is monitored and protected with the Bently Nevada system.
Noracid’s turbine-generator undergoes periodic vibration and oil analysis. It’s operating status is also continuously monitored via remote service that provides 24/7 support.
Corrosion is tracked by non-destructive testing (NDT) of components such as the drying tower, IAT, FAT, sulfuric acid piping, pressure leaf filter, sulfur tanks, sulfuric acid tank, etc. NDT techniques include ultrasound, long range ultrasonic testing (piping), phased array ultrasound, and eddy current (tube).
Temperature monitoring is accomplished using thermographic photography for transformers, electric motors, and checking levels in tanks and pipelines.
“Condition-based maintenance is of limited value if there’s no response to the condition,” said Bartlett. “What’s notable here is not all the monitoring systems, but that Noracid has been willing to drive its operational efficiency based on the results of such systems in a consistent manner.”
Noracid uses software management tools to ensure spares are available and work is carried out at the appropriate time. A full software suite of tools (Infor EAM) helps plant personnel optimize maintenance tasks, including: managing scheduled procedures; entering corrective works; and tracking key performance indicators (KPIs), work orders, corrective/preventative ledgers, etc.

Inside the covered sulfur storage facility.
Pillar 2: Critical spare parts
Noracid’s remote location has driven maintenance protocols built on self-sufficiency, particularly with regard to spare parts availability. The core strategy is to have all major spare parts available at the plant. Plant personnel also meet regularly to reassess requirements for critical spare parts.
The strategy has served the operation well. Even pandemic-induced global supply scarcity was not an issue.
“Our strong inventory and outage planning team has allowed us to weather the pandemic and the associated supply chain issues with reasonable ease,” said Elio Barraza; Noracid’s Operation Manager. “In early March, we entered our plant shutdown with no real expectation of challenges.”
Pillar 3: Plant turnarounds
Noracid prides itself on their extensive plant turnarounds, which have taken place at ever increasing intervals. Their last shutdown, in early 2022, took place after 38 months.
Noracid’s carefully planned and fullyresourced turnarounds have ensured plant reliability and availability over the last decade. Turnaround expenditures have averaged approximately 7M USD, of which 40 percent is associated with equipment and spares, and the rest associated with labor costs.
The scope of these turnarounds includes: • High priority tasks identified during the preceding operational period. • Maintenance tasks to be performed only during a plant outage. • Backlog tasks originating during the previous operational period. • Inspection of components subjected to corrosion or wear. • Improvements, upgrades, and design changes.
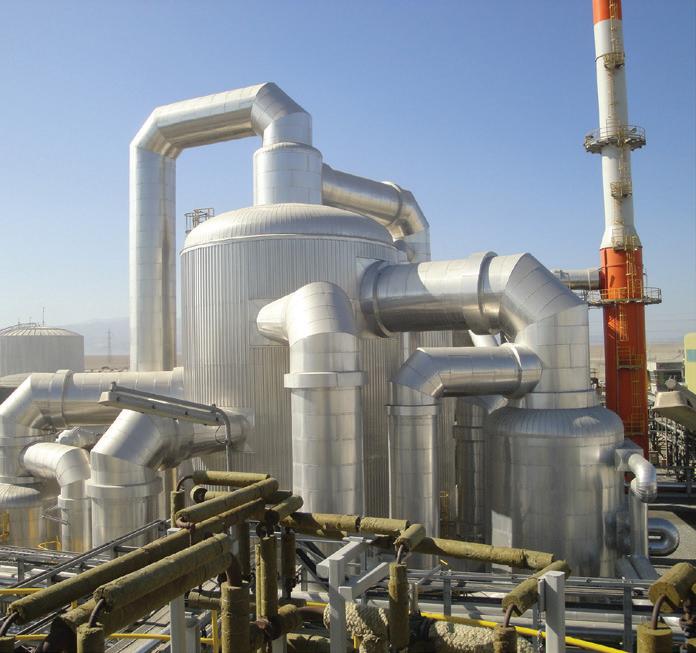
Converter section.
Pillar 4: Third-party specialist support
“Our overall maintenance strategy involves using only original spare parts and keeping a well-stocked inventory,” said Barraza. In many cases Noracid has direct contact with the fabricator of the spares, enabling them to have a guaranteed availability for turnarounds with the QA/QC accuracy of the original part.
The plant also maintains strong ties with technical specialists from key suppliers, often seeking and acting on their advice. “These companies have committed to support us in the longer-term aims of the business and are available to support 24/7 for the short-term issues that emerge from time to time,” said Cristian Roempler, Development Manager at Noracid.
The next step
Having consistently achieved high plant availability and utilization for the better part of a decade, plant managers are looking ahead to the next ten years.
“Once we raised plant availability levels up a few years ago, it has been a big challenge to maintain them,” Barraza said. “As the plant gets older, we need to anticipate problems, seek them out, and remain organized so that we don’t get into a situation where issues become overwhelming.”
To improve performance further, the company is evaluating a ‘digital transformation’ of their operation via computer optimization. “Our wish to improve our productivity further requires us to invest in ‘next generation’ tools to assist us in reaching this goal,” said Roempler. “Without these tools further improvements can only be incremental.”
“Many of the optimizer concepts currently being considered for use in the acid industry already have proven roots in the metals mining industries that we serve,” said Storch. “Metso Outotec’s optimizers are based on twenty years of continuous improvement as IT based technologies became available.”
Metso Outotec’s optimizer compares an aspect of sulfuric acid production to theoretical data, and, based on actual data on how that aspect of the process is trending, support operators with practical advice on corrective action.
“The optimizer allows customers to make process adjustments based on operational key performance indicators (KPIs),” said Bartlett. “Though KPI’s vary depending on client needs, electricity use is a common one. In some metallurgical plants, for example, the optimizer helps reduce electricity consumption over the entire process chain, starting from the feed bin of the metallurgical process and ending at the stack of the acid plant.”
Implementing an optimization system is a multi-step process requiring careful consideration. In keeping with its exacting operational standards, Noracid’s planners are assessing how the system would best serve the facility over the next ten years. q
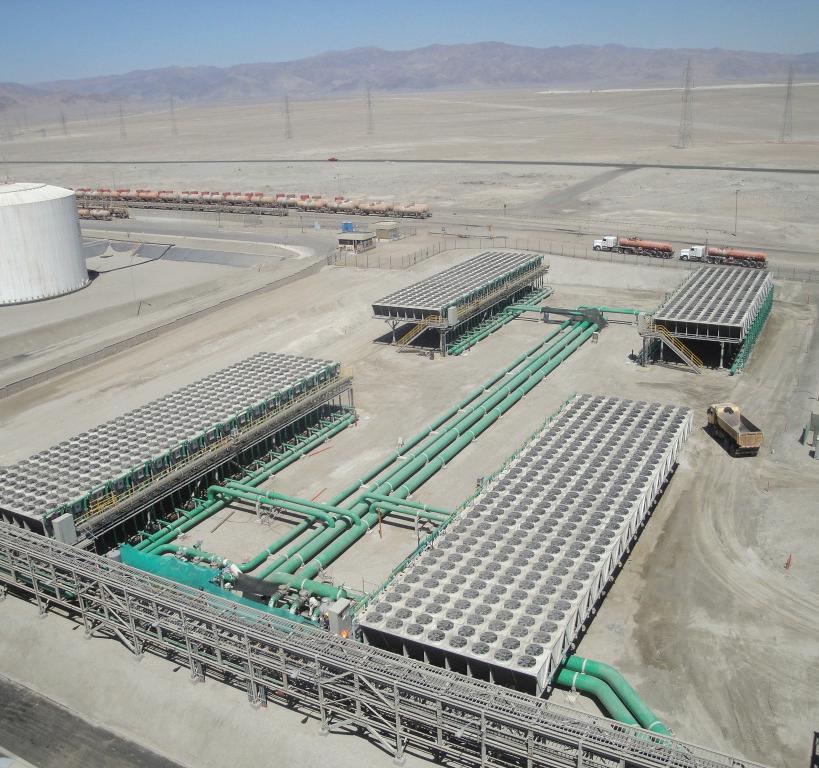
Aerial view of the fin-fan water cooling farm.
Metso Outotec’s work scope
Metso Outotec designed Noracid’s sulfuric acid plant and supplied the following equipment: • Sulfur melting and filtration area • Sulfur combustion area • Converter area • Drying and absorption area • Infrastructure, including air cooling systems, T/G set, etc. Since plant commissioning, Metso Outotec has supported Noracid in plant operation, minor plant upgrades, and maintenance activities.
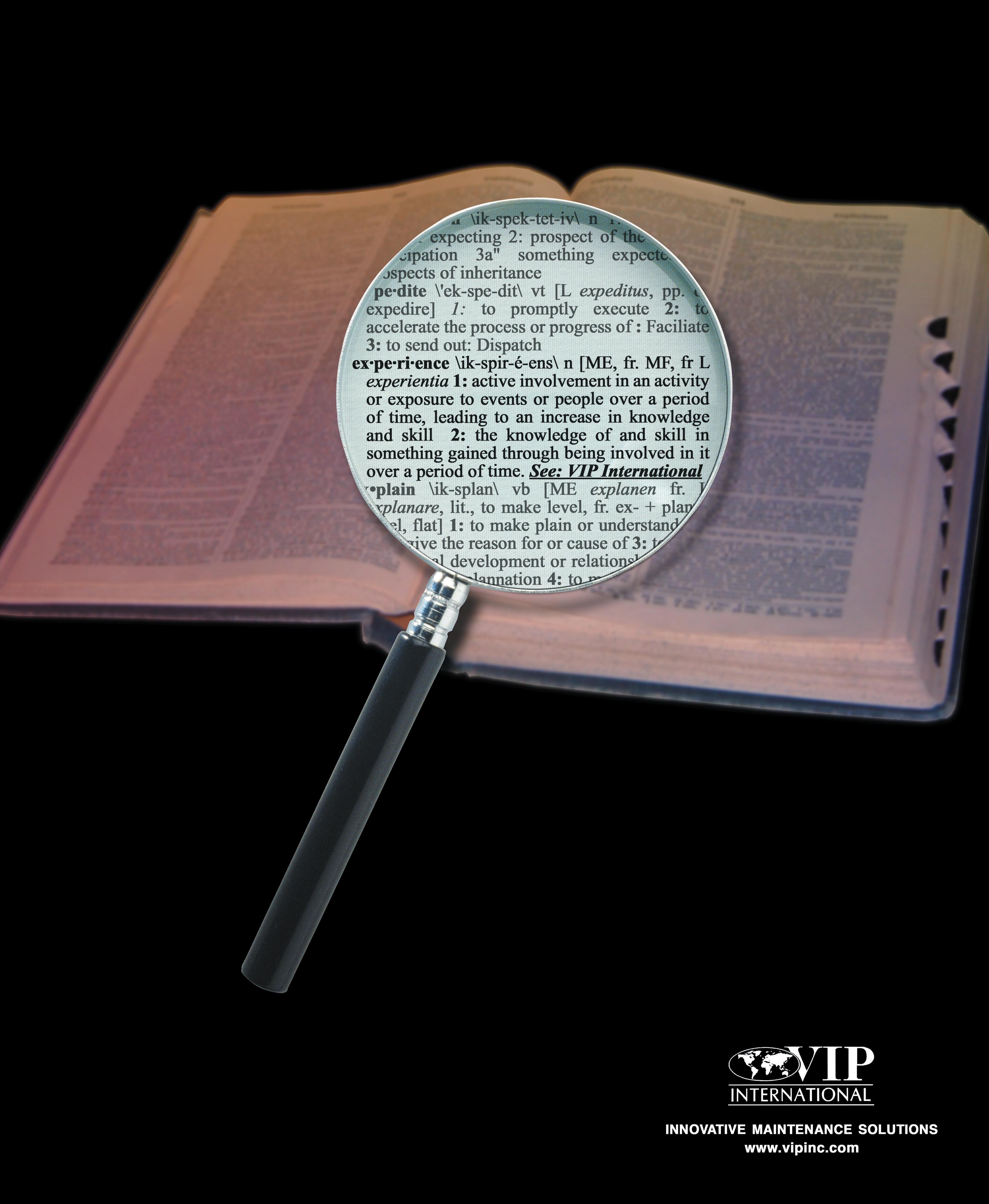
Supply critical for 2022
By: Fiona Boyd and Freda Gordon, Directors of Acuity Commodities
Fiona Boyd, Acuity Commodities Freda Gordon, Acuity Commodities
Since our last article in the Fall Winter 2021 issue of Sulfuric Acid Today, many commodity prices have continued to firm. This includes sulfur and sulfuric acid, where supply remains overall snug and demand firm, which in turn is providing price support.
Looking first at sulfur, the key raw material for most sulfuric acid production, throughout last year the market continued to rebalance following the impacts of the Covid-19 pandemic. One of the largest impacts of the pandemic was the loss of sulfur production due to lower by-product output of sulfur at the refinery level because of refined product demand destruction. On the other side, sulfur demand was not as negatively impacted as on the supply side, demand for most of these goods remained firm, or firmer. As such, sulfur consumers spent 2021 readjusting to what supply was available and, in some cases, developing new trading partners.
Meanwhile throughout 2021, the rollouts of Covid-19 vaccines and fiscal support helped to boost investment and spending, spurring demand for various commodities including copper, cobalt, and fertilizers.
With all this came a squeeze in the supply chain and sulfur, like many other commodities, was experiencing shortages of supply and strong demand. At the same time, other raw material prices were growing, such as ammonia driven by increases in natural gas pricing. Prices of fuel and many items also grew, pushing inflation rates to new multi-year highs in many countries.
Many sectors have been successful, however, in passing higher costs on to consumers. This includes fertilizers, where faced with record-high ammonia and increasing sulfur prices, producers increased their end product prices accordingly. In turn, these higher input prices have been accepted by farmers due to strong grain economics with phosphate fertilizer applications ongoing to support yields.
We noted in our last article how the Tampa molten sulfur quarterly contract price jumped from $96/lt DEL in 1Q21 to $192/lt DEL in 2Q21. Today, the benchmark price is $282/lt DEL for 1Q and global pricing at the time of writing would suggest an increase for 2Q. This reflects the impact of ongoing tight supply availability and robust demand – higher prices.
The outlook for sulfur is somewhat clouded, however, by the developing situation in the Ukraine/Russia region. Any developments there, including sanctions and Russia’s potential retaliation, could impact both sulfur and phosphate fertilizer availability and pricing as Russia is a key producer of both. Russia is also a key exporter of natural gas, copper, nickel, and wheat so any disruption to the country’s exports will influence not only its fertilizer and metal production, but the cost of food globally.
Outside of fertilizers, sulfuric acid demand remains firm. This includes copper leaching in the key import market of Chile. The ongoing strong fundamentals there as discussed in our last article resulted in Acuity assessing the 2022 Chilean annual copper price as $235-244/t CFR Mejillones, up from $55-62/t CFR Mejillones for 2021. The settlement at this level followed business for 1Q22 delivery being concluded as far back as October 2021 in the mid $240s/t CFR for 1Q22 delivery, partly setting the tone for annual negotiations.
What was different, however, was because of the perceived high prices by the buy side, buyers were not in favor of typical fixed-price contracts, which resulted in some pricing flexibility in contracts. While the sell side was hesitant in agreeing after selling at negative FOB levels as recently as 2020, some suppliers did agree to nontraditional terms.
Much like sulfur supply, acid supply is constrained too with the situation most notable in Europe. In 4Q21, we saw supply availability tighten further when some producers reduced smelter operating rates due to high energy prices. With European smelters a key source of acid supply for regions such as the Americas, we saw more product from other regions moving in its place. This included Asian acid moving to Latin America and the United States, with high freight for the trade routes providing some price support.
As planning for 2022 was underway, we did see more offers of acid from Chinese smelters emerge, and at slightly lower levels compared with product from Japan or South Korea. As we discussed in our last article, the acid market in China is unpredictable and what will be key this year is domestic pricing versus what is achievable offshore. Logistics are a notable issue in China, however, which could constrain vessel movements. The country’s zero-Covid policy, if maintained for the remainder of the year, could continue to cause logistical disruptions to cargoes going in and out of China.
In the meantime, it became evident that the supply of acid from Europe would not improve in 1Q22, in part as copper smelters prepare for major turnarounds in 2Q and zinc smelters continuing to run at reduced rates.
In the United States, less acid was imported in 2021 with pricing out of Europe a key constraint. This is because unlike other markets, such as Chile, where acid is imported for direct consumption, most imported acid in the United States is for distribution. This is largely against domestic contract business for a variety of downstream applications, such as pulp and paper. With annual pricing agreed at the end of the year for the following year, domestic pricing was not at a level to cover the costs of imported material.
While North American suppliers did increase 2022 contract pricing notably, it was still not enough to support the level of pricing needed to make imports workable, along with lower overall availability. This means dependency on domestic supply is critical this year, and we have already seen supply disruptions and a heavy planned maintenance schedule, particularly in 1H.
Despite price resistance being seen globally, in the end business is usually concluded due to a lack of other options. This is highlighting what has carried over from 2021 – supply is tight and higher input prices are being accepted because of firm downstream fundamentals.
Acuity Commodities provides insight into the sulfur and sulfuric acid markets through price assessments, data, and supporting analysis. Offerings include weekly reports on the global sulfur and sulfuric acid markets. For North America, we offer a bi-weekly report on sulfur and sulfuric acid as well as a monthly report on industrial chemicals, including caustic soda and hydrochloric. In addition, Acuity does bespoke consulting work. Please visit www.acuitycommodities.com for detailed information. q
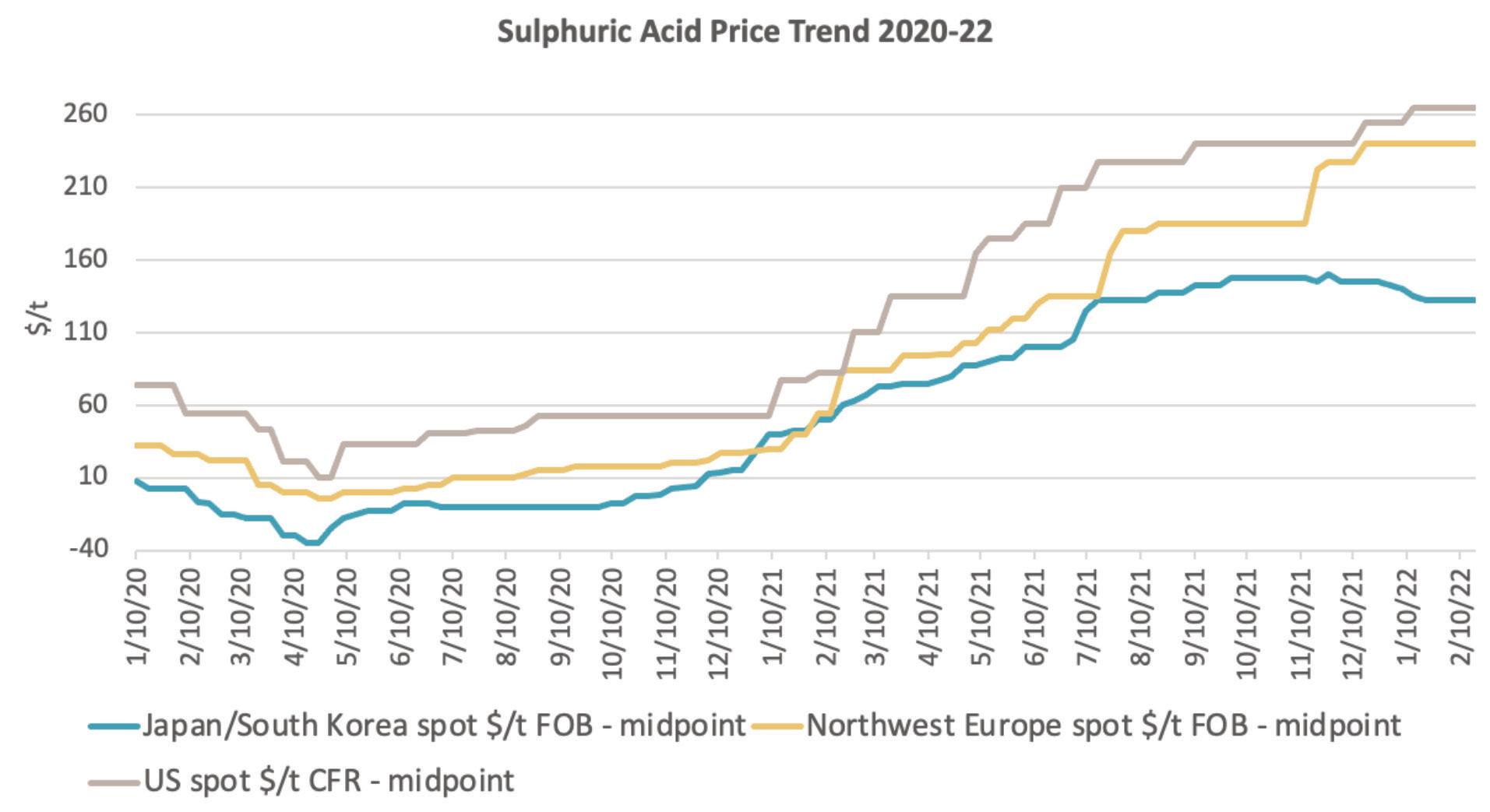
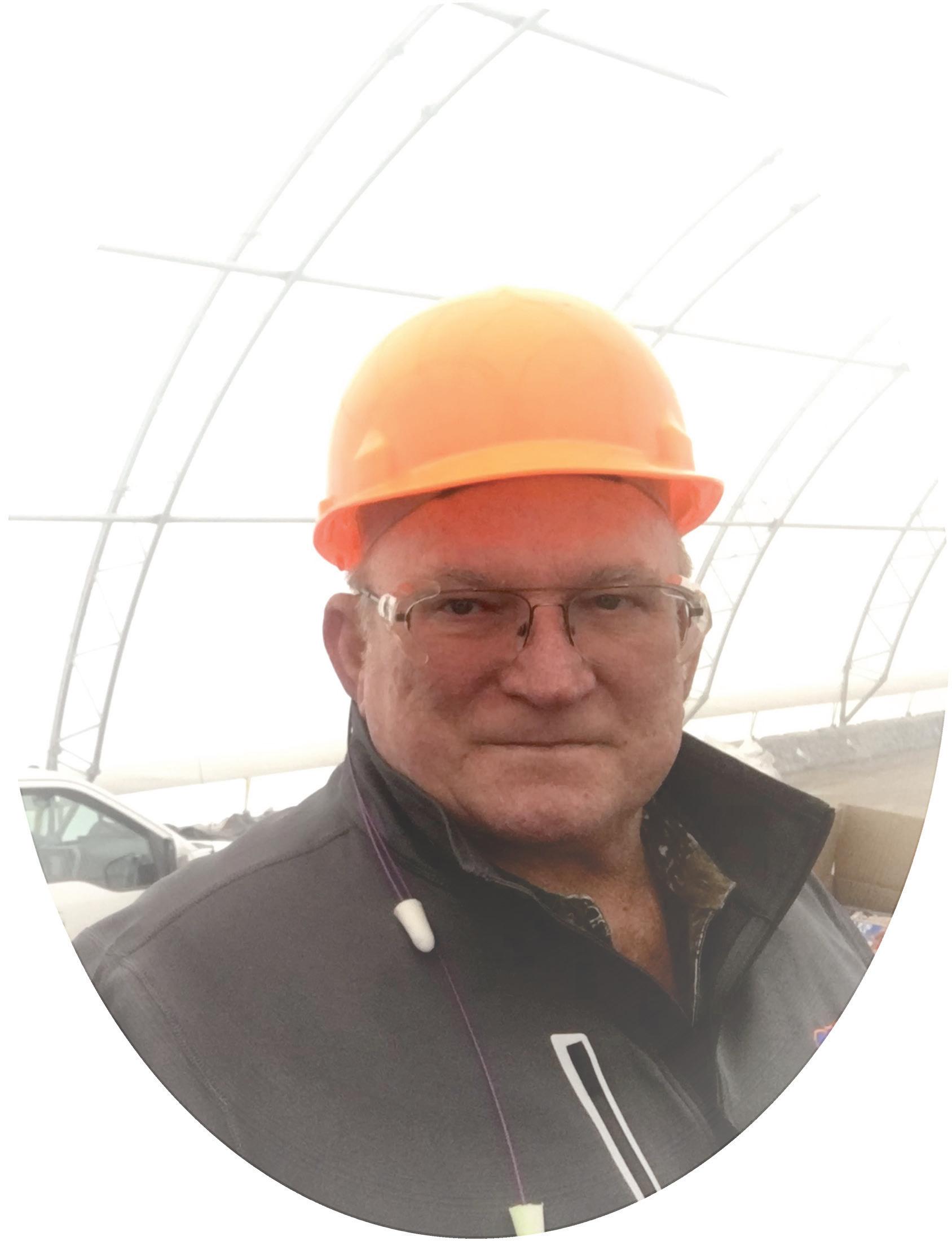
David W. Bailey

1953-2022 You will be missed
With considerable sorrow CMW shares the news with our Sulfuric Acid family of the passing of our mentor, colleague and good friend David Bailey. David enjoyed a long career as a boilermaker, including 35 years with us at CMW leading our chemical field crews. It was always a treat to see David interact with new clients and see their reactions at the realization as he talked that, not only did he speak the sulfuric acid language, but he had seen it, done it and fixed it, whatever ‘it’ was many times and more times than not had the solution for which they were looking. He was adamant that CMW deliver quality work, safe solutions and on schedule performance. So much of our reputation is due to him. David was well renowned for his food, and delighted to cook for his crews while they were out of town to bring them a taste of home on long turnarounds. Always available to answer a call and find a solution, David will be sorely missed by our industry and certainly missed by those of us honored to work alongside him.
Feature NOx! The other acid gas
By: Darwin Passman, CSP, Safety Director, VIP International Inc.
NOx is an unwanted by-product created in three areas of a sulfuric acid plant. The first and primary place NOx is created is the furnace. Higher operating temperatures coupled with increased oxygen enrichment and longer residence time form nitrogen oxides. This type of formation is referred to as thermal NOx and represents the majority of nitrogen oxides formed in the gas. Nitrogen oxides may also be present in the fuel or feedstock used in the furnace. This type of NOx is referred to as chemical NOx. A third source of NOx, specific to smelters, results from the operation of wet electrostatic precipitators (WESPs). Electrical arcing in the WESPs causes the formation of nitrogen oxides.
The nitrogen oxides react with sulfuric acid to form the compound nitrosylsulfuric acid (HNOSO4). NOx, in the gas stream, is readily absorbed by the submicronic acid mist particles due to the high surface area to volume ratio. Therefore, most of the nitrosylsulfuric acid is concentrated in the acid draining from the mist eliminators. The mist eliminators are saturated with this NOx-laden acid and sulfates. This acid is readily soluble in sulfuric acid at low temperatures and accumulates in the acidic sulfates of cold exchangers and the false bottom of the stack.
Exposure to NOx is most prevalent during a turnaround. Once the system has been purged and cooled down, the system is de-energized and prepared for inspections and repairs. Inspection entry points are opened on the dry side as well as the wet side. Due to the natural draft of the plant, ambient air is drawn into the entry points.
The humidity in the ambient air is absorbed by the nitrosylsulfuric initiating a reaction that releases NOx primarily as nitrogen dioxide (NO2). NO2, unlike sulfur dioxide, does not have adequate warning properties at low but toxic concentrations; therefore monitors with electrochemical NO2 sensors must be used for detection and quantification of NO2. It’s worth noting that atmospheric testing of any confined space must follow the OSHA procedure for testing in the following order:
OSHA exposure limits: • Percent oxygen: 19.5 - 23.5% • Lower explosive limit: 0.0 - 10.0% • Toxics: carbon monoxide, sulfur dioxide, hydrogen sulfide, or nitrogen dioxide.
Initially there may be a low or no reading of NOx. The nitrosylsulfuric is relatively stable until it begins to absorb moisture. Once exposed to moisture, the reaction begins to release NOx and produces heat. The reaction increases as the acid gets hotter and absorbs more moisture. As a result of this delayed process, we often see NOx levels start out low at the beginning of a turnaround and increase as time progresses. Areas of significant exposure are from sulfate buildup in the cold exchangers, stack, and other areas of potential sulfate buildup. The gas outlet section of the interpass absorption tower and final tower, including the tube-sheet and mist eliminators, can also be primary sources of NOx exposure. • The OSHA permissible exposure limit (PEL) for nitrogen dioxide is 5 ppm. • The Cal OSHA (PEL) is 1 ppm. • The immediately dangerous to life and health exposure (IDLH) is 20 ppm.
NOTE: Nitrogen dioxide interferes with the sulfur dioxide electrochemical sensor on the atmospheric monitor. For example, if the nitrogen dioxide level is 25 ppm and the sulfur dioxide level is 0 ppm the electrochemical sensor for sulfur dioxide will read -25 ppm or negative 25 ppm. Sulfur dioxide does not interfere with the NO2 electrochemical sensor.
When attempting to mitigate NOx exposure consider the following: • Vessels being entered for inspection or work. • The actual work being performed. • Isolating NOx laden equipment. • Hydrogen buildup.
Since NOx emissions increase when nitrosylsulfuric acid is exposed to moisture, a plan to minimize that exposure during turnaround should be created to decrease emissions. Removal of material (sulfates on mist eliminators) at the beginning of the turnaround will decrease the NOx exposure. Also, isolation of specific equipment that is NOx laden will keep the rest of the equipment free of contamination but may also increase the risk of hydrogen build up in a dead zone area.
Once the material is removed, the NOx can be treated with a process that breaks it down to free nitrogen (N2) and weak sulfuric acid (H2SO4).
When working in a potential NOx environment, proactive monitoring is the first step to minimizing exposure. If NOx is present, ventilation is a possible remedy for removal while working in the vessel. If an immediate source of NOx is in the vessel, ventilation may increase the exposure risk by injecting humid air. If NOx is present and work must be performed, immediately dangerous to life and health (IDLH) protocol must be followed. This requires training, experience, and the equipment to safely enter and work in an IDLH atmosphere. The goal in any IDLH entry is to reduce the atmospheric conditions to non-IDLH as quickly and safely as possible.
If NOx is here to stay, mitigate exposure when possible, educate the workforce, and provide training in the safe handling and atmospheric exposure during a turnaround.
For more information, please visit www. vipinc.com. q

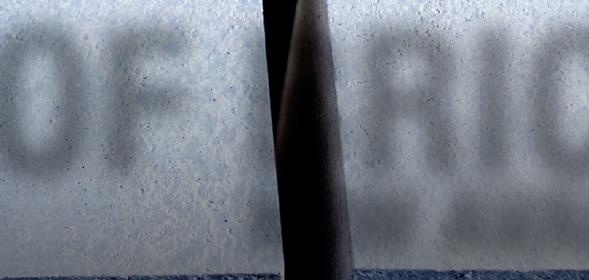
THE ACID PROOF BRICK
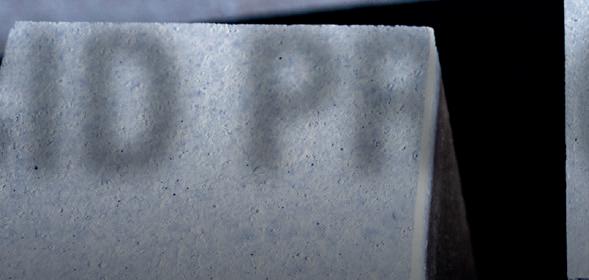
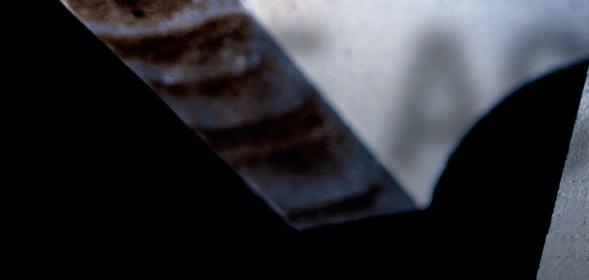
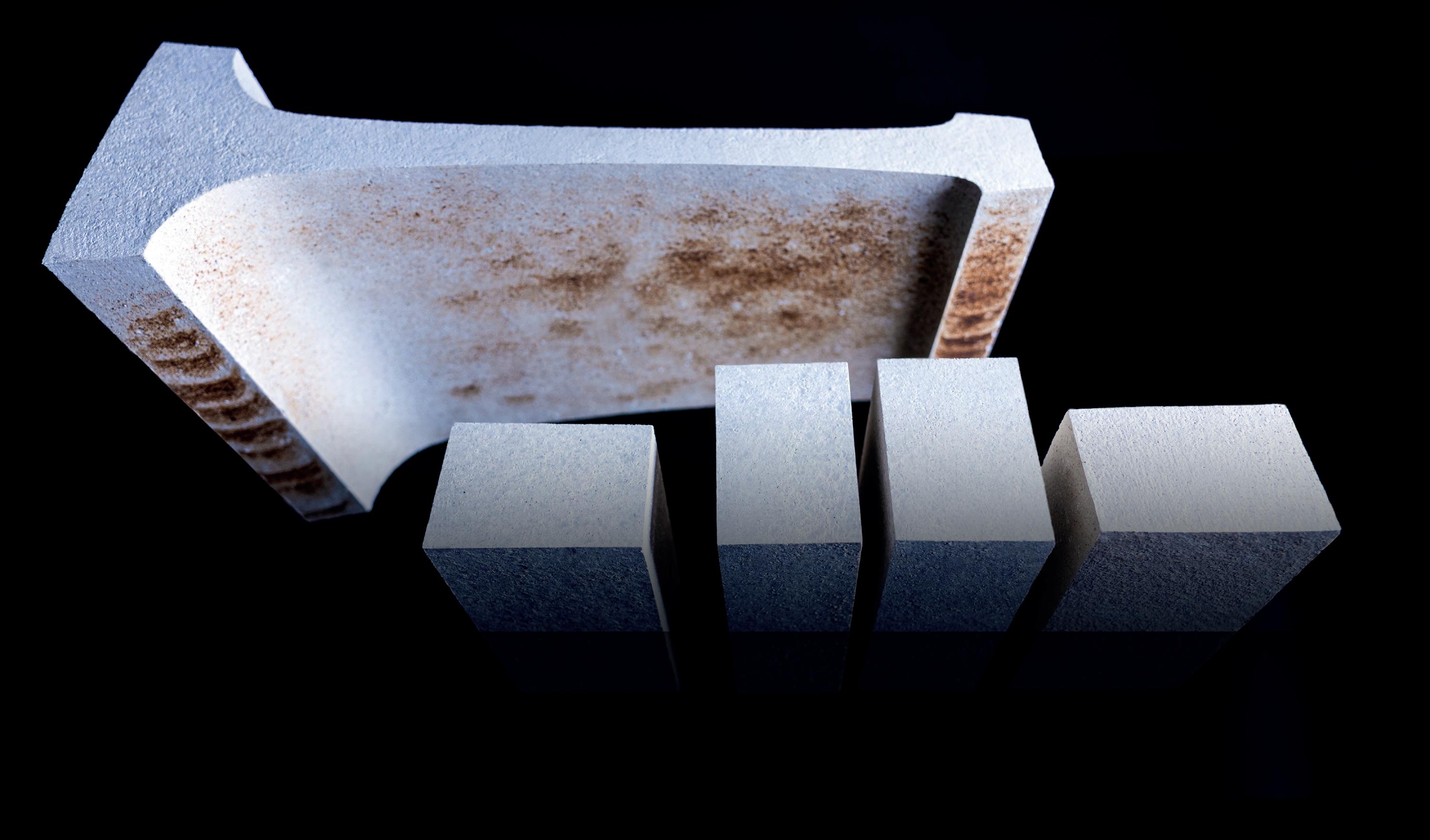
NOW AVAILABLE IN US-SIZES
Protection against extremes is what our bricks stand for more than 111 years – worldwide.
No breakage on pallets to be calculated - just order the amount you need for a direct, safe and binding delivery! What other challenges can we solve for you? Please reach out to us and we will find the right lining system for any kind of specifi cation.
Directly from our warehouse in Houston, Texas - Just call us - We deliver! STEULER-KCH GmbH
Feature Common pitfalls of sulfuric acid piping and ducting
By: CJ Horecky, Executive Director, INTEREP
Keeping a sulfuric acid plant operating efficiently is a delicate science. Almost every piece of equipment in operation has the potential to bring the whole plant offline if it fails. And each piece of equipment is usually complicated in its own right. Understanding the intricacies of the way each piece interacts with adjacent systems in a plant adds a whole other level of complexity. Thankfully, piping and ducting systems are simple, straightforward, and don’t ever bring plants offline, right? Taking an unplanned shutdown because of a failure in piping or ducting systems is embarrassing. Sure, the ductwork, like a network of veins and arteries, ties everything together, but it’s more of a peripheral feature. Ductwork is not the core equipment that the whole plant runs on, it’s just a system connector, so there is little grace for plant managers who experience a ductwork failure, and even less for maintenance managers who didn’t see it coming.
As King Solomon said, “there is nothing new under the sun.” The saying applies to acid plants as well. Technology has come a long way in the last 40 years, but INTEREP has consistently found the same telltale signs of imminent piping and ducting failures. Watch for these, and avoid an unplanned shutdown.
Hidden leaks
Acid pooling on the ground, corroded structural steel, plumes in the air… these are all signs of a positive pressure leak, and need to be fixed fast to avoid all kinds of damage, safety issues, and environmental hazards. What about negative pressure leaks though? They’re just as detrimental in the long term, yet tend to be overlooked. “Out of sight, out of mind,” right?
A negative pressure leak means ambient air being sucked into the system, and what’s doing the sucking? The ID fan/blower. If the ID fan/blower is pulling in ambient air, it’s pulling in less process-gas or using more electricity—both cause trouble. Now let’s talk about that ambient air: it’s wet. Even in the Sonoran Desert of the Southwestern US (home to several acid plants) the average relative humidity is 38.5%, double that number if you live outside that area. So, your unseen leak is now bringing water into the sulfur gas stream, and making sulfuric acid in places it shouldn’t be.
This will exhibit itself in the following symptoms: • Slow drips or crystalline minerals/acids running from beneath insulation or from gaskets/expansion joints. • Loss of fan capacity (or becoming ID fan/blower limited in worst-cases). • Internal corrosion in non-acid containing equipment. • Elevated O2 process gas levels.
These are the most common hidden leak points: • Fabric expansion joints that have outlived their useful life. • Fabric expansion joints that have not been properly spliced. • Holes in ductwork that are hidden beneath insulation. • Loose flanges or equipment connections. • Equipment doors/manways upstream (dry gas area). • Expansion joints that have been insulated over and not documented.
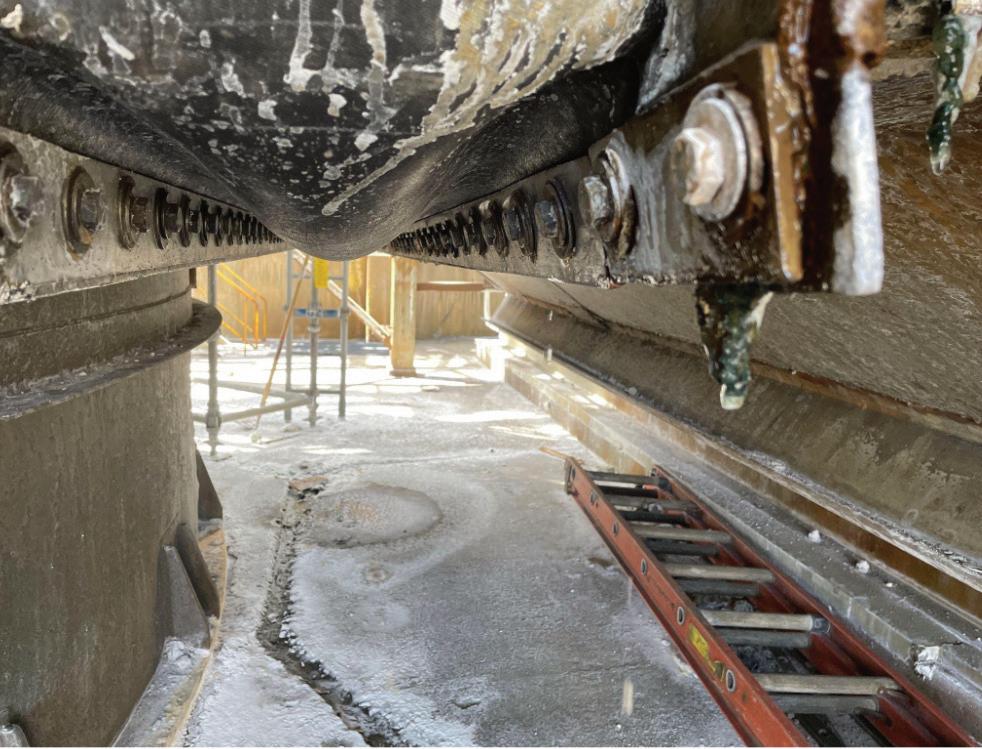
Low-point acid collection found by INTEREP during an inspection at an acid plant in North America. Galvanic metallurgical corrosion found by INTEREP during an inspection at an acid plant in Europe.

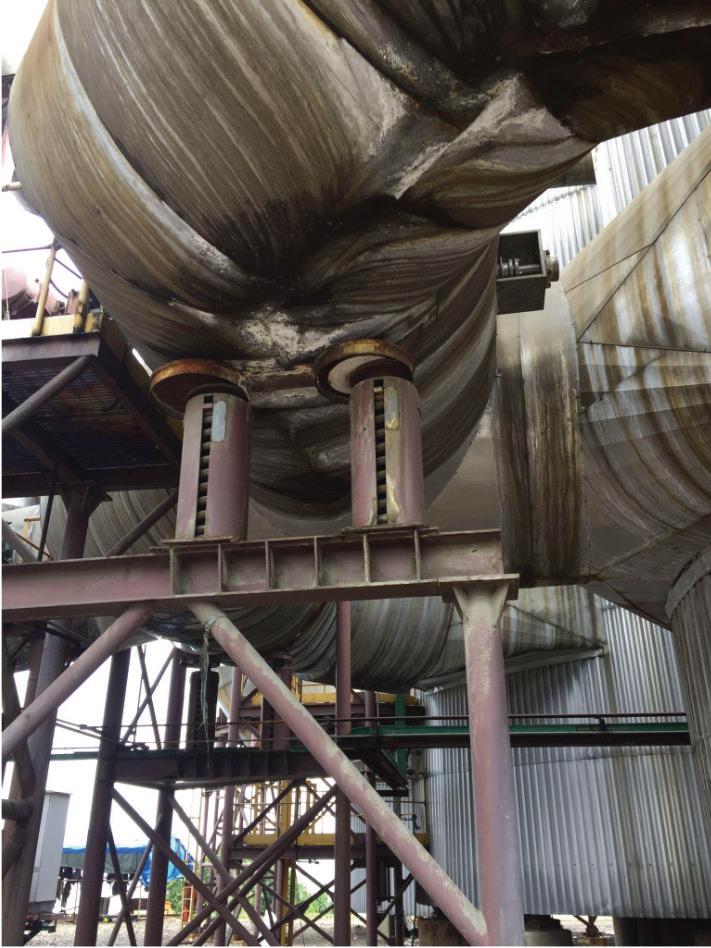
Low points
Condensation and precipitation getting into a ducting system is an issue. But what about when liquid gets out? Liquid seeks the lowest point in your piping and ducting systems. This often occurs near elbows, in the bottom of vessels, or in the convolutions of horizontal expansion joints. If there is a sagging area in the ductwork, or a low elbow or bend, a drain can be installed to tap this dilute acid off into a sump, until the system can be properly leveled at the next major shutdown. However, if it’s in a metal bellows expansion joint (ubiquitous across the large diameter ductwork in sulfuric acid plants), what can be done? A drain can’t simply be added because there may be as many as 20 or 30 convolutions (the accordion shaped expanded pieces of a metal bellows) which are all their own low points and which will collect dilute acid that gets into the system.
What to do if acid is pooling in a horizontal expansion joint: • Externally insulate the expansion joint (check to verify metallurgy temperature first) to bring everything above dew point. • Change the metallurgy to something that can handle the dilute acid and will last between shutdowns. • In certain circumstances, it may be possible to add a drain to the bottom of a “heavy wall” single convolution expansion joint. • Upgrade to 2-ply designs with a monitoring system that will alert operations when the inner ply fails, so a routine maintenance system can be developed. • Add either steam or electrical tracing to increase the bellows temperature above dew point.
Metallurgical corrosion
Carbon steel, high-nickel alloy, FRP, thermoplastics—you’ve seen it all, and you know what you like to use. Most plants have a specification for the type of steel to use in piping and ducting systems, and it’s probably followed fairly well. Here’s where things sneak though: piping and ducting accessories. Does the pump vendor know that the flanges should be made of 316L to match the adjacent piping? Does the expansion joint vendor know that the T304 metal bellows are getting welded onto carbon steel? Does the damper manufacturer build shaft packing glands to the same spec as the ductwork is built to? It’s easy to end up with a slew of different pieces of equipment in the system, and it’s hard to vet them all first. Obviously, try to replace any piece that has an incompatible metallurgy with an upgraded one, but sometimes the downtime or the upgrade cost is simply too much.
What are the options if ductwork accessories are corroding and the plant can’t come offline? • Determine if the part is acting as a heat-sink and dropping the process gas within below dew point. • Determine if the area upstream is airtight or if there are any major infiltration points contributing to the issue. • Check metallurgical compatibility between accessory and adjacent ductwork. • Take UT readings to determine corrosion rate and projected lifespan. • Perform thermal scans to look for hot and cold spots or potential failure points.
For more information, visit INTEREPinc.com. CJ Horecky of INTEREP will also be leading a deeper discussion of this topic at the Sulfuric Acid Roundtable, April 4th-7th in the Woodlands, TX. q