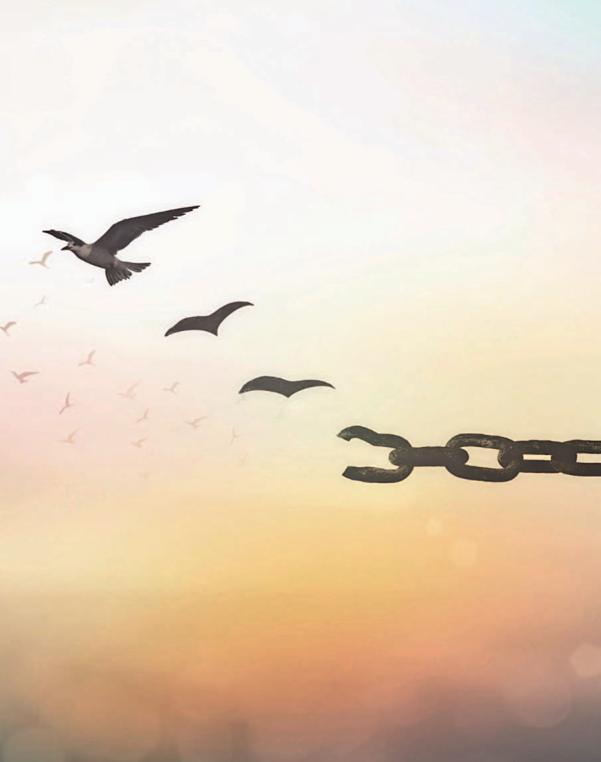
7 minute read
THE SOCIAL ASPECT: COMPANIES WITH SOUL
Arie de Geus’ s seminal book The Living Company presents a new way of thinking about organisations as living systems that can adapt and evolve
The book draws on De Geus’ s experience as a former executive at Royal Dutch Shell and his research on companies that have existed for a long time, which he calls “living” companies.
One of De Geus’ s conclusions is that a company should be seen as a living organism rather than as just a machine designed to maximise profits The writer argues that a company that is able to survive and thrive over the long term adapts to changing circumstances and evolves over time He identifies four key characteristics of such a company:
● Sensing: the ability to be aware of and responsive to the environment in which the company operates;
● Nurturing: the ability to care for employees, customers and other stakeholders;
● Flexibility: the ability to adapt to changing circumstances; and
● Identity: a clear sense of purpose and values that guide the company ’ s actions
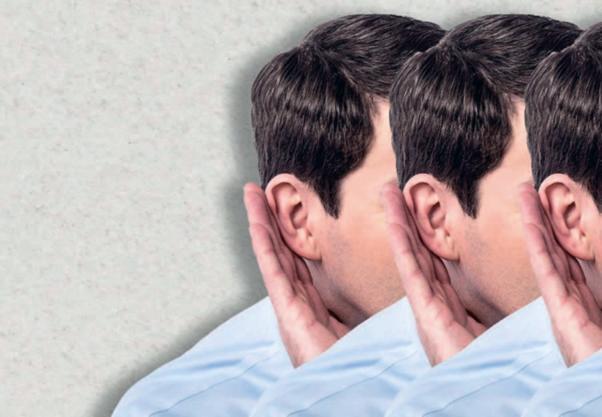
De Geus emphasises the importance of learning and continuous improvement in a living company. He argues that to stay competitive in a constantly changing business environment, companies need to be willing to experiment, take risks and learn from their mistakes
The Living Company provides a thought-provoking perspective on organisational behaviour and encourages companies to think about themselves in a new way
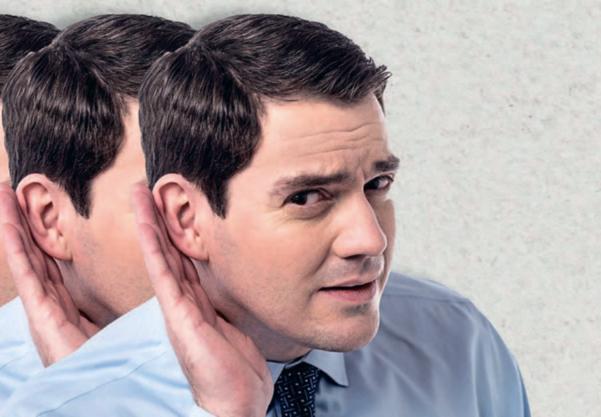
It’ s worth spending a bit of time examining an example of a company that, today, is getting this right South African firm Nando’ s operates in the sphere of local and inclusive sourcing (as do many other local businesses)
Nando’ s is known worldwide for its peri-peri chicken The company has a programme called Nando’ s Peri-Peri Farm, which works with small-scale farmers in South Africa to grow the periperi chili peppers that are used in the firm’ s sauces and marinades The programme provides farmers with training and support to help them increase their yields and improve the quality of their crops, while ensuring that they are paid a fair price for their products
It works like this: Nando’ s is supporting the South African economy by sourcing its ingredients locally In turn, this creates jobs in the community Sourcing locally can reduce the distance that food needs to travel, which can help lower carbon emissions and reduce a company ’ s overall environmental impact (De Geus’ s first key characteristic, sensing) while improving quality and freshness
By working with local suppliers and farmers, Nando’ s has built strong relationships based on trust and mutual benefit (the second key characteristic, nurturing) to ensure a reliable supply chain and consistent quality of ingredients
By supporting underrepresented com- munities, Nando’ s helps create a more equitable and just food system (the third key characteristic, flexibility), while promoting social responsibility and ethical business practices
By demonstrating a commitment to these values through its sourcing practices, Nando’ s can continue to build customer loyalty while differentiating itself from its competitors (the fourth key characteristic, identity) This gives it a unique selling proposition that can attract customers who likewise value these practices At the same time, Nando’ s can engage its employees and create a sense of purpose and pride among them, with the added benefit of improving workforce retention, boosting morale and enhancing its reputation as an employer of choice
Nando’ s has shifted into carpe diem mode, and its value chain agility and product, or market innovation, are solutions which can simultaneously address stagnating economic growth and social challenges
There is the added opportunity factor, which can radically reduce material or energy throughput across value chains Sourcing ingredients locally reduces Nando’ s carbon footprint by minimising the distance food travels from farm to table
Overall, its shared value creation is providing a range of benefits to Nando’ s, including increased innovation, improved reputation, cost savings, access to new markets, improved stakeholder relations and more employee engagement
With a little imagination to see the opportunities, leadership has the ability in the context of current uncertainties to interrogate the context, recognise systemic issues and overcome the dominant industry logic to innovate and expand the total pool of economic and social value
Martin Luther King jnr wrote: “Life’ s most persistent and urgent question is: ‘What are you doing for others?’”
Our suggestion is that at the conclusion of every meeting of management, committees and boards, the question should be asked: “In reaching the decisions we have arrived at today, have we managed to do something positive, constructive and effective for people and for planet and not only for profit?” x
Judin is an attorney and partner at law firm Judin Combrinck, and Russell is the chief risk officer of Sasol
Why It Pays To Pay Attention To Data
With ESG reporting, companies can identify serious risks in their operations and even boost profits
Whereas sustainability reporting has tended to result in many companies producing glossy documents filled with fabulous stories of what the company got right, ESG reporting is forcing businesses to focus less on the wordsmithing of storytellers and to simply give the facts that is, the data
But therein lies the opportunity
Learning how to interpret that data properly can translate into more productive, efficient, and cost-effective ways to operate. There are tangible bottom-line benefits that go beyond simply presenting an image of a good corporate citizen
The “S” in ESG includes matters of occupational health and safety, which, in an era of zero tolerance for the abuse of workers, has become a key contractual element in most global supply chains
For example, in the automotive sector, the global original equipment manufacturers measure and report on the lost-time injury frequency rate (LTIFR) of not only their own manufacturing sites but also those of their supply chains
Toyota, for example, has a supply chain LTIFR target of 0 15, or fewer than 15 losttime injuries per 2-million person hours worked
Let’ s consider two cases in which the use of “S” data, one regarding absenteeism and the other relating to lost-time injuries, benefited the businesses
Case 1: Impahla Clothing
In 2006, three small garment manufacturing companies in South Africa were invited by one of their key customers, Puma, to produce their inaugural sustainability report as part of a global reporting initiative project focusing on reporting in the supply chain
Of the three, only Impahla, based in Cape Town, took note of the value of the data its reporting consultant accumulated to structure what was ultimately a performance-based report
Among the key items discussed was greenhouse gas emissions an already hot topic for reporting and employee absenteeism, which at the time was calculated to be over 7% of total productive time
Through an analysis of the data, it was determined that more than half of the 7% was related not to a failure to come to work, but to late arrivals, which until that point hadn’t been considered
The problem was connected to a variety of factors, not least of which were the unreliability of government-managed rail networks and publicly operated taxis However, it was noted that younger employees, particularly relatively new joiners between the ages of 18 and 25, were almost exclusively responsible for the bulk of all late arrivals
In discussing this with employees, it was determined that a key issue was that of people not feeling sufficiently remunerated to care about whether they arrived on time
To address the problem, Impahla created a revenue-sharing bonus scheme that ultimately rewarded every employee based on a collective ability to reduce total absenteeism, inclusive of late arrivals, to below an industry benchmark of 3%, noting that this meant a productive capacity increase of over 4% On a total turnover of roughly R20m this meant a revenue surge of more than R800,000 a year for the company, and an even greater profit surge due to improved efficiencies resulting from increased “time on task” measures.
Case 2: Metair
JSE-listed Metair produces everything from automotive batteries to wiring harnesses, springs, brake pads, lights and dashboards and other panels for most of the major auto manufacturers, including Ford, Isuzu, Mercedes-Benz, Toyota and Volkswagen
As part of the assurance process, an average of three operations a year are selected for five-day site visits to test the accuracy, consistency, completeness and reliability of the data being reported to the group by the operations for annual reporting purposes
This testing of data at source also helps to determine potential root causes
Of Anomalies
In 2018, one of Metair’ s businesses was measured as having an LTIFR of 3 8, or over 25 times more than Toyota’ s global supply chain benchmark
The problem (at the risk of oversimplification) was that an ageing workforce with increasing rates of obesity, diabetes and hypertension, among other ailments, was working in an ageing workplace in need of important repairs and redesign
Simple slips, trips and falls, due to potholed flooring inside and outside the buildings, coupled with stairways that were slippery thanks to more than 50 years of use-related deterioration, and vehicle pathways that were restricted after years of increased demand for a finite amount of space, were leading to minor injuries (typical first-aid cases), escalating to more severe lost time due to injuries, such as broken hips
Having identified that the business could potentially lose contracts to supply goods to Toyota (or others) should the rate of serious injury not decline sharply, an investment of roughly R50m was made to overhaul the facility to reduce risks, while there was increasing medical observation and treatment in support of workers. By December 2022 the company ’ s LTIFR was zero
Conclusion
The problem we face in the disconnect between the ESG reporters (or the companies) and the ESG users (the analysts) is that of limited understanding of how to unpack the data for modelling and assessment purposes
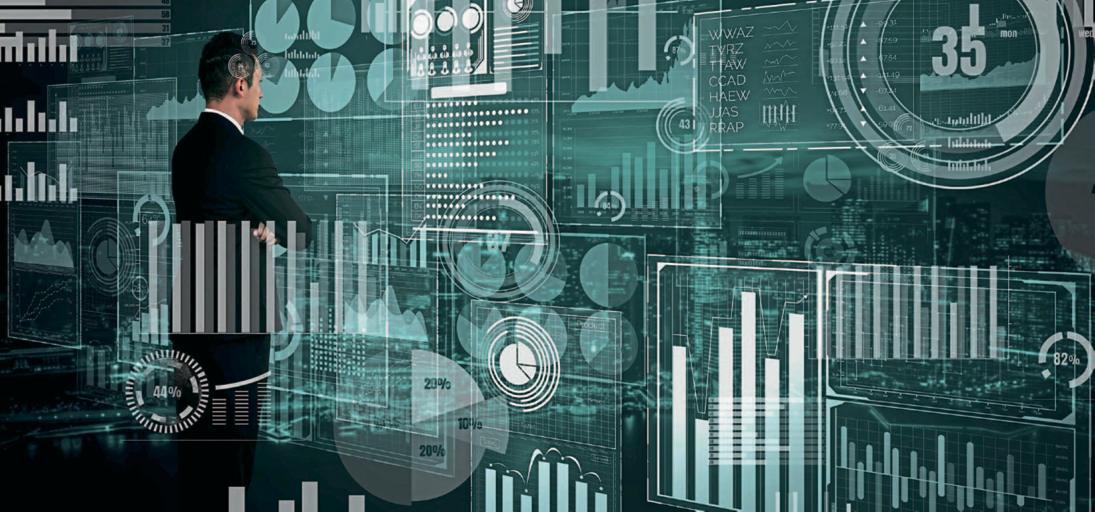
Analysts need to understand that a fatality at a South African mine almost always results in a government shutdown of three days to investigate the death Those three days equal an average of more than R60m in lost production
Analysts also need to understand that inadequate training and development procedures seriously affect flight risk (the risk of key talent leaving for minor increases in salary)
This is costly to the company, not only because the efficiency of processes during transitions to new recruits suffers but also because it is difficult to quantify the effect of lost institutional memory
If the devil is in the detail, he’ s definitely in the data x