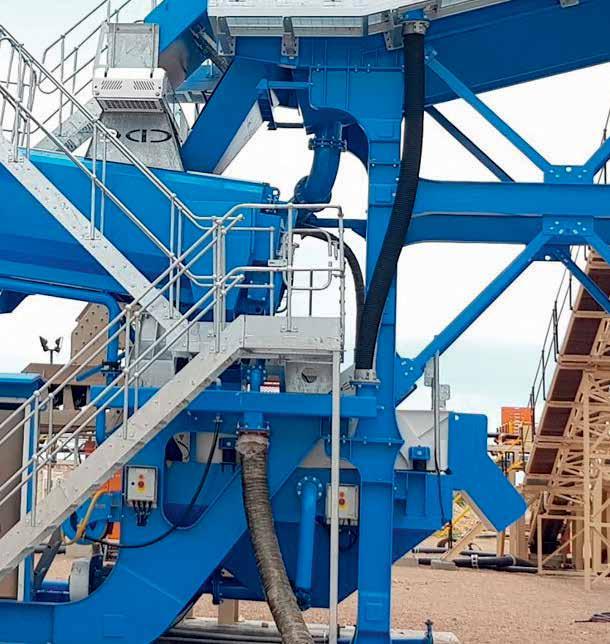
5 minute read
CDE’S AGGMAX KEY IN PARTNERSHIP WITH CONSULMET
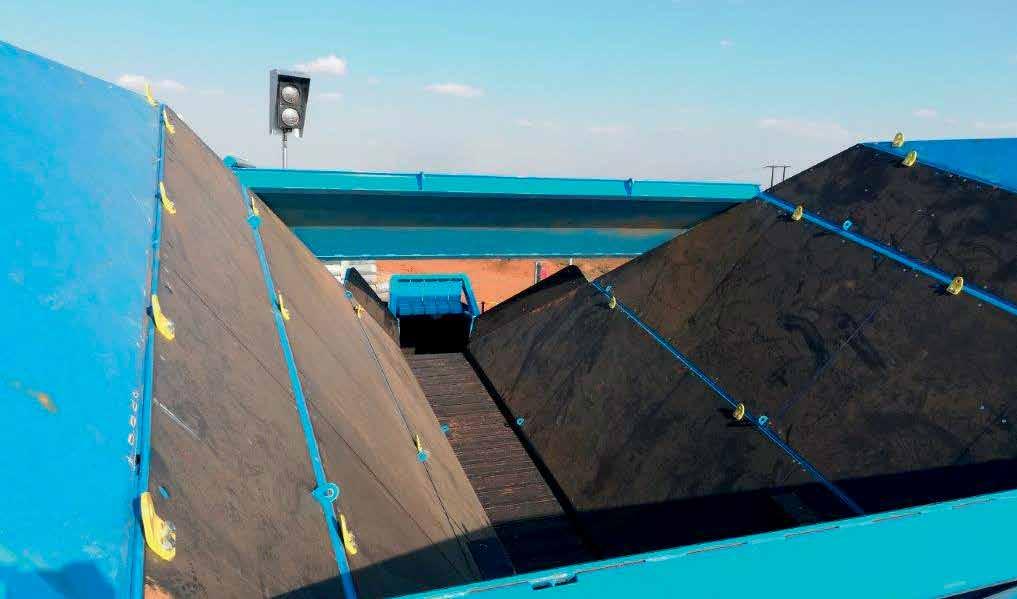
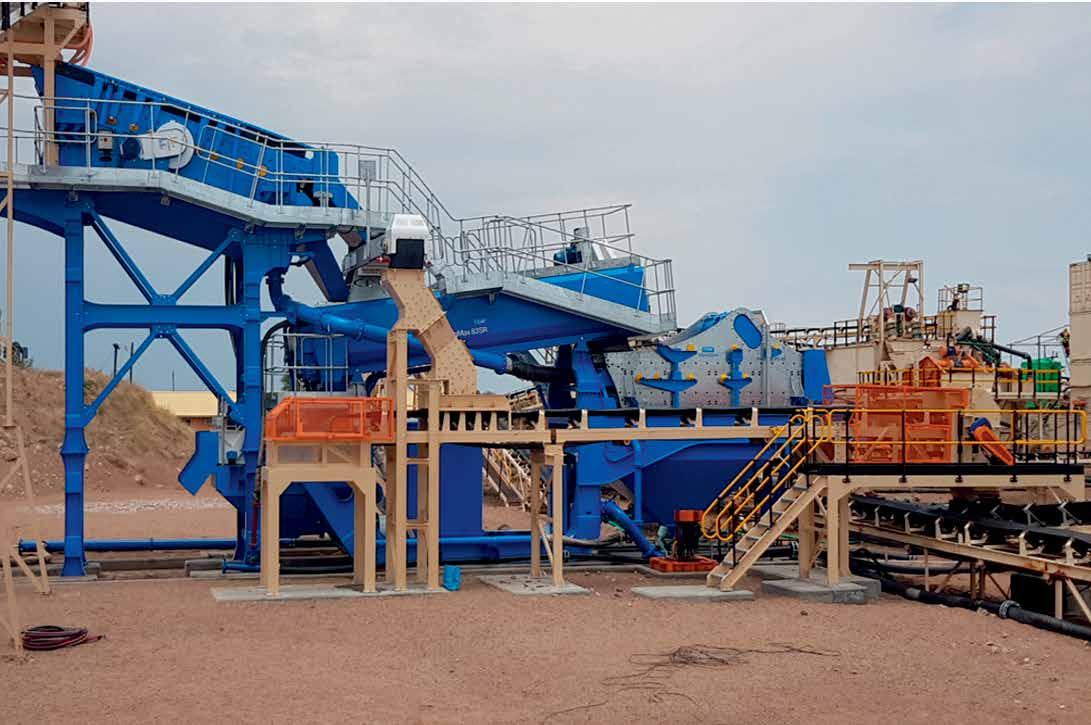

The AggMax 83SR used in a secondary scrubbing vegetation removal application on kimberlite in Botswana.
The AggMax is suitable for various material streams.
The unique spiral alignment of its paddles reduces the shock of intermitting loads on the gearbox, motor and bearings. This design ensures consistent material loading and the unique paddle shape ensures maximum attrition with even the heaviest clay-bound feed material.
Engineered to maximise the operational life of the plant, Xtryl paddles are extremely durable and incorporate integrated wear protection plates to protect fixings. Xtryl is a CDE-developed material for maximum wear properties to be used in abrasive applications such as AggMax paddles. It incorporates CDE’s pioneering Infinity Screen technology, which o ers greater screening capability and reduces power consumption.
Its e ectiveness at scrubbing heavy clay-bound material liberates the valuable materials, removing waste and vegetation to protect the downstream systems, which means XRT sorting systems are also considerably more e icient especially as the plant incorporates a trash screen to float o organic contaminants that are o en classified incorrectly.
CDE’s regional manager for the Middle East and Africa, Ruchin Garg, said the partnership with Consulmet was an opportunity to drive innovation in the region.
“It’s a very exciting partnership and one that provides both companies with the opportunity to grow our presence further in sub-Saharan Africa. CDE is supplying Consulmet with world-class processing technologies that are being widely adapted by mining operations throughout the region.
“Our equipment is delivering major e iciencies, particularly in the diamond industry, through projects delivered by Consulmet. Their success is our success. These projects are demonstrating the capabilities of our technology and the industry is noticing the benefits to be had.”
Derek Lahee, Consulmet’s managing director, said the partnership with CDE had been mutually beneficial.
“Partnering with selected and innovative original equipment manufacturers has been a strategy of Consulmet’s for a number of years now, with the CDE partnership being one of the first that we formalised.
“One of the challenges that we encountered in some of our early diamond plants was heavily clay-bound particles not completely breaking down and carry-over vegetation contaminating our XRT circuits. The AggMax technology proved to be a perfect solution to both of these challenges and the CDE team’s professionalism in assisting us to solve these challenges was most gratifying.”
Wildu Mostert, Consulmet’s operational director, says the units are modular, economical and innovative in design, and robust in terms of general maintenance.
“Consulmet and CDE also worked together to deliver a solution to a longstanding South African client in the coal industry. The materials handling project included two CDE-supplied R4500 apron feeders, complete with 90m3 feed reception hoppers, allowing direct tip feed, which in turn minimises materials handling.
“These units transfer to two Consulmet conveyors, handling 450tph, crossing a road, with a gantry span of 42m, for transportation of coal to the other side.” ■
© ISTOCK – Kuzihar
The AggMax plants are modular, economical and innovative in design, and robust in terms of general maintenance. – MOSTERT
BELL LAUNCHES GLOBAL PREOWNED EQUIPMENT WEBSITE
Equipment manufacturer Bell Equipment recently launched a dedicated global website, pre-owned. bellequipment.com, which is also accessible from the company’s website.
Doug Morris, Bell Equipment’s MD: Europe, Middle East and Africa, who has overseen the project, said: “Previously our efforts were localised, and we wanted to create an online solution to promote our pre-owned equipment globally.
“The website gives Bell operations and dealers access to a fully integrated platform to advertise their pre-owned Bell machines. This means that customers around the world can shop for all the pre-owned equipment we have available from one user-friendly and convenient website.

4 647
Number of detonators BME blasted
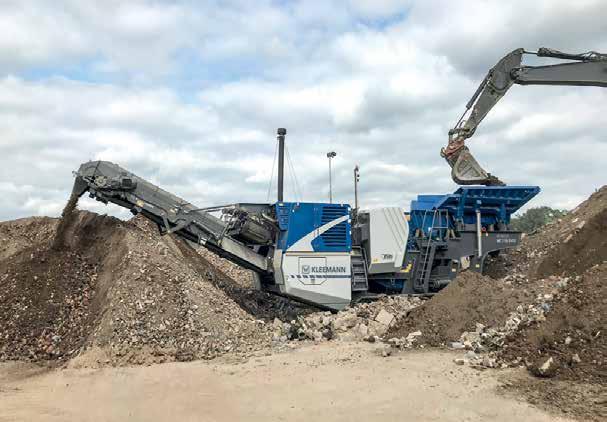
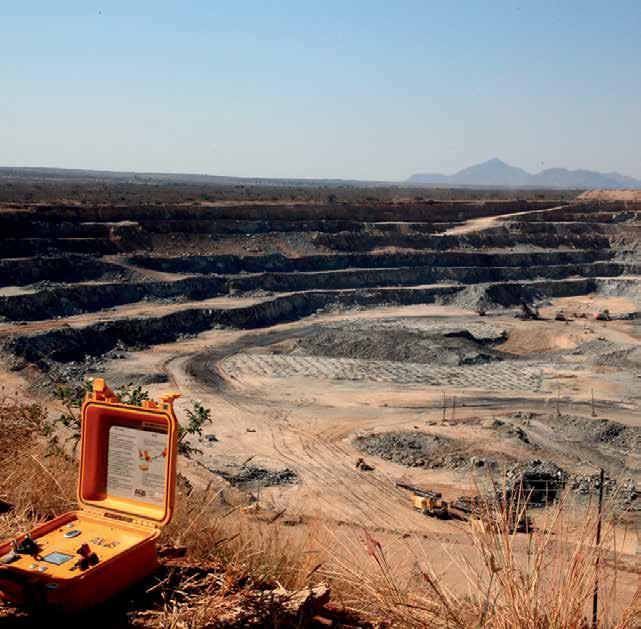
KLEEMANN UNVEILS NEW MOBILE JAW CRUSHER
With the market launch of the new MOBICAT MC 110(i) EVO2, Kleemann has introduced a mobile jaw crushing plant of the new generation. The product offers groundbreaking technologies for optimising all areas of a typical workday, focusing on economy, operability and sustainability.
A special highlight of the MOBICAT MC 110(i) EVO2 is a new effective two-stage overload system, which effectively prevents blockages and material bridging that can often lead to unwanted downtime.
With the further development of SPECTIVE, the digital operating concept has an intuitive structure and revolutionises plant operation with its extensive features. The 12-inch touch panel has been optimised with regard to user guidance and visualisation. Furthermore, new components such as a radio remote control have been integrated in the SPECTIVE world. The new digital solution SPECTIVE CONNECT sends all important plant data to the smartphone.
BME BLASTS ITS WAY TO SA RECORD
Blasting and explosives supplier BME recently broke another South African record for the largest electronic detonator blast, the company said.
The blast was conducted by BME, an Omnia Group company, at the end of 2020 at a manganese mine in South Africa’s Northern Cape province. Using its AXXI electronic initiation system, BME was able to plan and execute a blast of 4 647 detonators.
Just a few months earlier, the company broke a previous record at the same mine by initiating 3 780 detonators in a single blast.
“The latest achievement involved a remarkable 535 tonnes of emulsion explosive in over 2 300 blast holes requiring a total of more than 37 000m of drilling,” said Kobus Boonzaaier, BME area manager in the Northern Cape. “The resulting blast was able to move almost 2.3 million tonnes of rock within a matter of seconds.”
Boonzaaier said the advantage of these large blasts was that they allowed mines to blast less often, meaning less disruption and a more streamlined mining operation.
INTEGRATED INTELLIGENCE. ONE DROP AT A TIME.
Optimising your mining efficiencies through intelligent delivery systems. Our Mobile Manufacturing Units offer a safe and seamless delivery solution that easily integrates with your surface mining process.

Our intelligent Mobile Manufacturing Units are capable of delivering the full range of our bulk explosives for all surface mining applications. These units offer safety control systems, ease of operation, maintenance and reliability.


If its not INVAL, it’s not Invincible
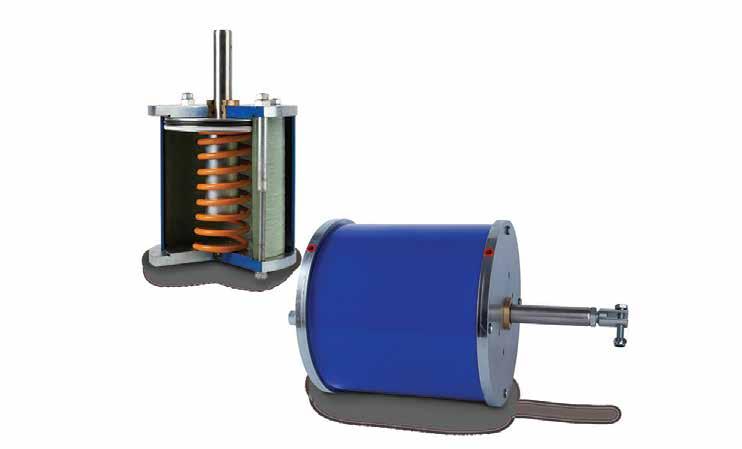