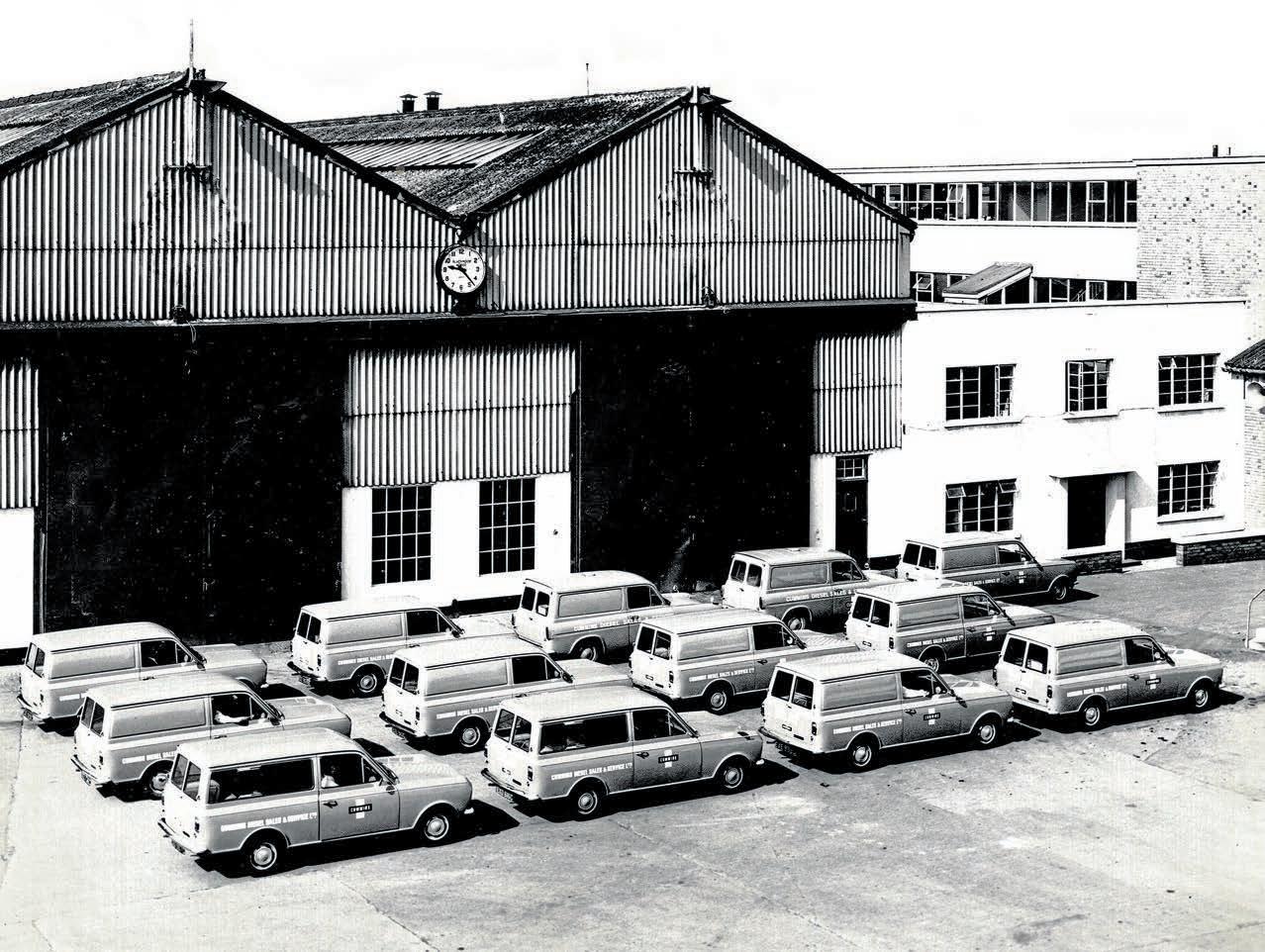
4 minute read
ENGINES PAST, PRESENT & FUTURE
David Wylie reports on the latest developments at Cummins, a long-term manufacturer of heavy-duty engines in the UK
Last year Cummins engines celebrated 70 years in the UK, representing a significant milestone in the story of British industry. More recently, their massive factory at Darlington has been testing hydrogen combustion engines and fuel cells, a far cry from powering post-war earthmoving machines.
Advertisement
The Cummins story in the UK starts in the late 1940s, when Blackwood Hodge became the distributor for American-made Euclid machines, whose 15-ton dump trucks were ideally suited to helping Britain back on her feet after WWII. Then a Euclid factory was established near Motherwell in Scotland for machines that came with either a General Motors or a Cummins engine.
At the time, Blackwood Hodge was one of the world’s largest sales and services organisations for construction machinery. As the machinery dealer was impressed with Cummins powerpacks across their various product lines, they began negotiations to become the American engine manufacturer’s UK distributor, going on to form Cummins Diesel Sales and Service in 1952.
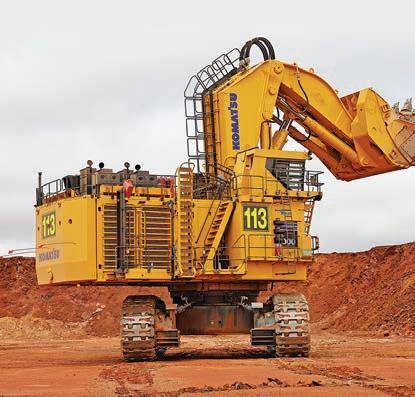
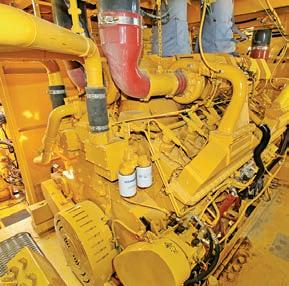
Just four years later, Cummins took the decision to establish their first engine factory outside of the USA, located halfway between Edinburgh and Glasgow at Shotts, close to the Euclid plant. This resulted in several truck manufacturers also offering Cummins engines, including Seddon Atkinson, ERF, Foden, Guy and Scammell.
In 1965 Cummins opened its Darlington factory in northern England and started production of its ‘Small Vee’ family of V6 and V8 diesel engines. Twenty years later, production switched to its mid-range engines. At the beginning of 2022, the factory built its 1.5 millionth mid-range engine, a 5.9-litre unit exported to South Korea for fitment into a Hyundai HX220 excavator.
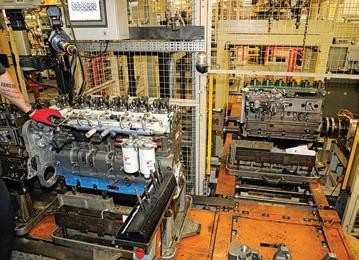
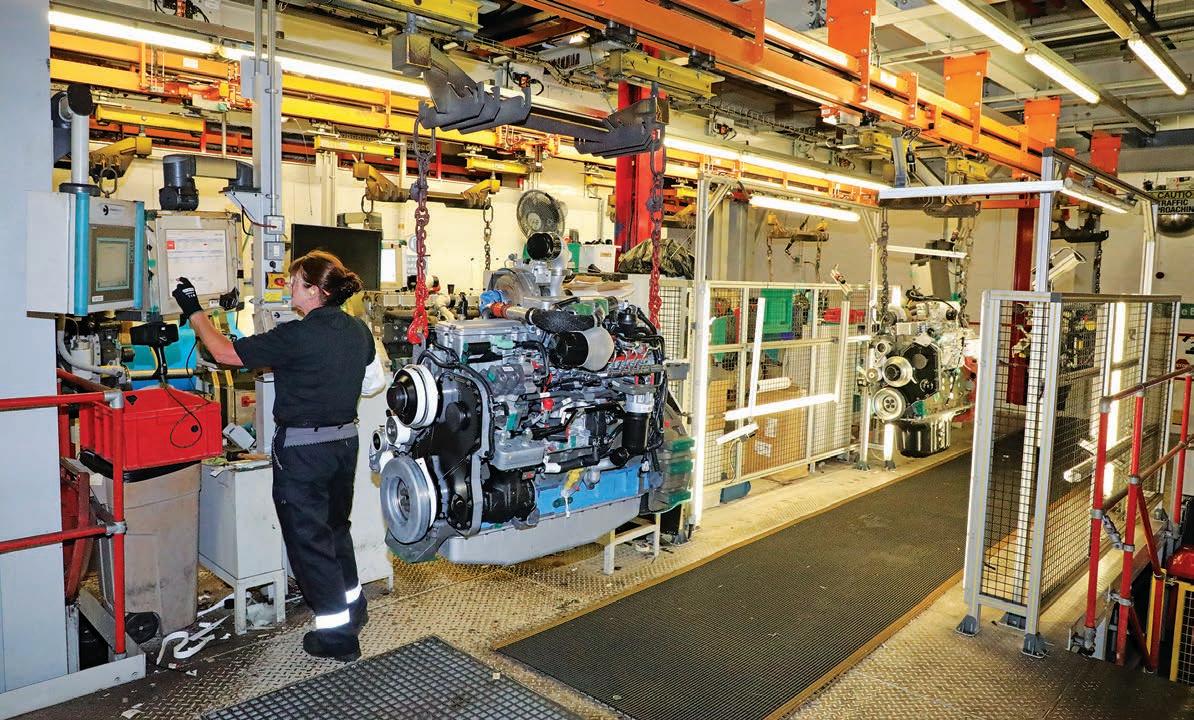
Cummins’ other UK factory is at Daventry and was opened in the early 1970s to build the K-series and other heavy industrial engines, serving the power generation, marine, rail and mining sectors of the market. Daventry-built engines would go on to power legendary mining kit such as the O&K RH120-C and Demag H225 mining excavators. This year marks the 50th anniversary of Cummins Daventry factory, where today the site produces engines above 38 litres, right up to the massive 78-litre QSK78, a V18 powerpack rated at 3500hp. To better serve a wide user base across many industry sectors, in 1984 Cummins bought out Blackwood Hodge’s interests in the UK Cummins Diesel Sales and Service firm. A broader range of services was then introduced, including maintenance contracts and engine rebuilds.
UK R&D INVESTMENT
In the next few months Cummins is expected to open the first phase of a £14m investment in its Darlington site to develop a new powertrain test facility. It is designed to be fuel-agnostic, able to cope with combustion engines powered by hydrogen, other gases or sustainable diesel, together with hydrogen fuel cells and battery-electric drivelines.

This facility will not just test driveline components, but also chassis-installed powertrains and completed vehicles, including heavy-haulage trucks and double-deck buses, in addition to construction and agricultural machinery. They will be able to be dyno-tested on site, and the heavy-duty dynamometers within the test cells feature an energy recovery system, pumping electricity into the ring main of the Cummins site.
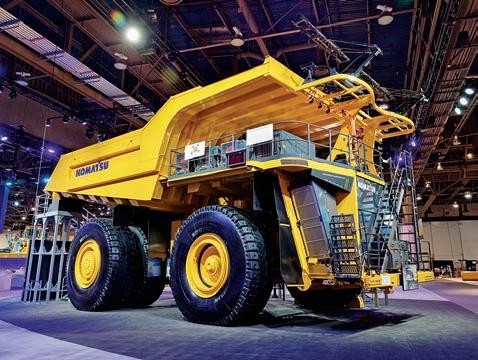
For on-road vehicles, the impending introduction of Euro 7 emissions standards, which will apply to petrol, diesel, hybrid and electric powered kit, presents significant challenges to engine and vehicle manufacturers. In the off-road machinery market, there is accelerated demand for the next generation of zero carbon solutions, all of which require considerable development to translate the theory into sellable products.
Cummins will take a big step towards a net zero carbon environment at the forthcoming ConExpo show in Las Vegas, with their new fuel-agnostic 15-litre engine. This is a power dense design, resulting in a more compact form, allowing easier integration by machinery and vehicle manufacturers.
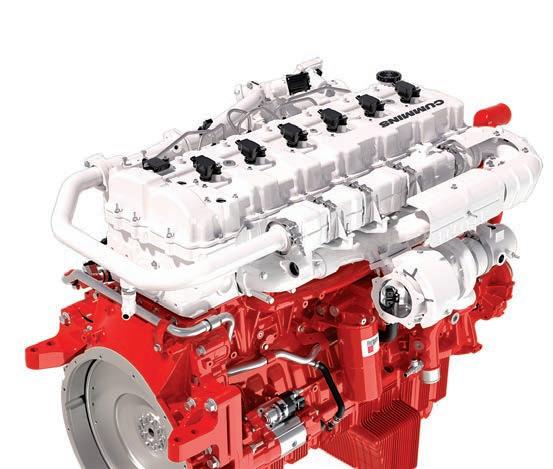
Using a common base engine, a variety of cylinder heads and fuel systems are available, tailored for using hydrogen, natural gas, diesel and biofuels as a fuel. The hydrogen engines will be rated from 400hp to 530hp and offer a peak torque of 2600Nm, and the renewable biogas version rated from 400hp to 510hp and 2500Nm of torque. The advanced diesel version will feature a broad power range of 450hp to 650hp, with an impressive 3200Nm of peak torque.
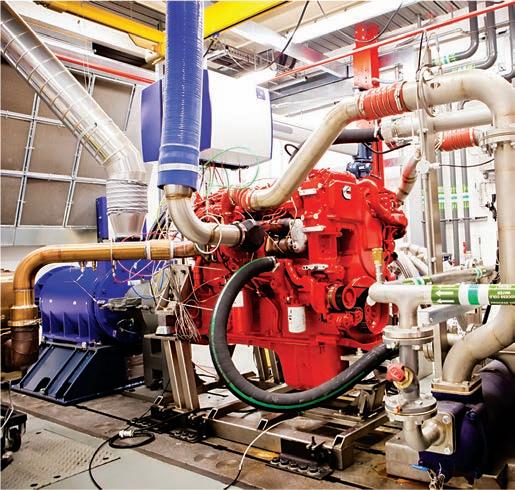
Early Adopters
The first off-road user of this new Cummins 15-litre engine in its hydrogen-powered form is likely to be Buhler, the North American manufacturer of the Versatile brand of large articulated agricultural tractors.
Komatsu and Cummins have a long history of working together in the large mining machinery sector of the market. For example, the ultra-low emissions engine in the PC4000-11 mining shovel is a 1877hp 60.2-litre V16 Komatsu-branded component, based on a Daventry-built Cummins QSK60.
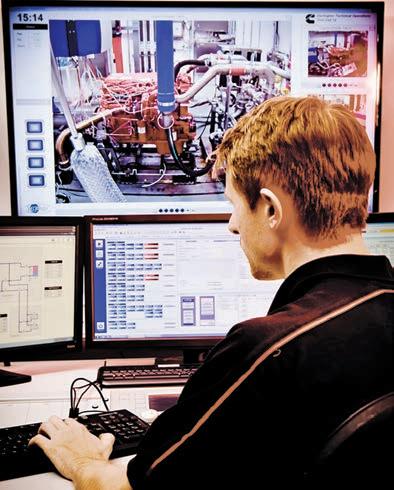
At the MinExpo 2021 show Komatsu unveiled an early prototype of a fuelagnostic mining dump truck, designed to accept a variety of powerpacks, from diesel-electric, through batteries to hydrogen fuel cells. The following year, Komatsu and Cummins announced that they were collaborating on the development of zero-emissions haulage equipment. Best known for their internal combustion engines, today Cummins has a broad portfolio of batteries, fuel cell systems and electrolysers – used to generate hydrogen –in its portfolio.
Masayuki Moriyama, president of Komatsu Mining, said, “Cummins has been a long-term partner of Komatsu and has been investing in the key technologies required to support the energy transition in mining. These are critical technologies for helping mining customers reduce carbon emissions and accelerate carbon neutrality. Building on our partnership with Cummins, we are working to accelerate sustainable solutions for our customers.”
Hydrogen Supply Chain
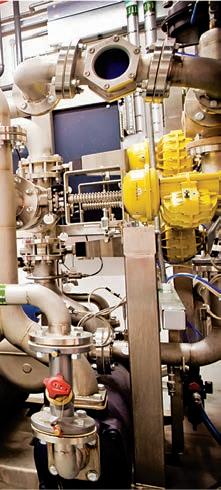
Recognising that storage and transportation of hydrogen is a vital part of this emerging technology, back in 2020 Cummins announced a joint venture with NPROXX, a leader in hydrogen storage and transportation, for the development of hydrogen storage tanks. The joint venture will provide customers with hydrogen and compressed natural gas storage products for both on-highway and rail applications. Cummins has more than 2000 fuel cell installations across a variety of on- and off-highway applications, as well as more than 500 electrolyser installations.
At the time of the announcement, Tom Linebarger, chairman and CEO of Cummins, said, “In order to move toward a decarbonised future, the world will require multiple power solutions, including advanced diesel, natural gas, electrified power, fuel cells and hybrids. The addition of hydrogen storage to our existing capabilities in hydrogen production and fuel cells enables us to accelerate the viability and adoption of these technologies in commercial markets.”