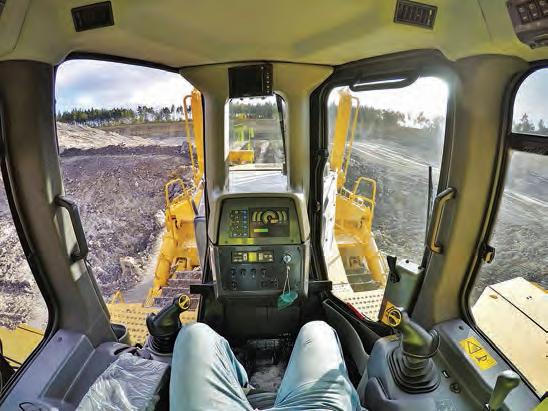
4 minute read
DRIVETRAIN
At the heart of the D475A-5 beats the well-proven 30-litre V12 Komatsu engine. In this dozer application it is rated at just 900hp at 2000rpm, compared to 1200hp when used in an HD785-7 mining dump truck. The planetary powershift transmission offers three forward and three reverse speeds. Maximum forward travel speed is 11.2kph, reaching an impressive 14kph in reverse.
A key to translating this power into consistent ripping performance is to maintain good track shoe-to-ground contact. This means that the track pads on this example, working in a highly abrasive material, have been changed every 3000 hours or so. The standard 710mm-wide single grouser shoes run on Komatsu’s K-Bogie undercarriage system, using eight flexible-mounted lower track rollers and two upper rollers on a twin bogie system. This allows a high vertical track roller movement over the undulating terrain.
Advertisement
This example is fitted with Komatsu’s optional traction control system, which has proved to work well when ripping the hard silica stone. In the hands of skilled operators, the big dozer’s telematics system indicates a lifetime average fuel burn of just 79.9 litres an hour. In practical terms, it gets through half the contents of its 1670-litre diesel tank in a 10.5-hour shift.

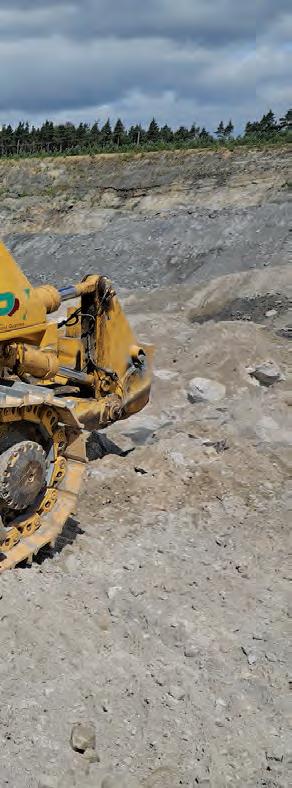
quarry operations. However, if you take its availability over the last five years, and given it’s the prime mover for extracting over 500,000 tonnes of material per annum, it’s been a good, reliable machine.
“One of the outstanding aspects of this machine, in comparison to its competition, is its consistent ripping performance. For maximum production and efficiency, we need to rip and cross-rip the various quarry benches, using most of the available ripper shank length.
“The other impressive aspect of the ripper and undercarriage geometry is how it keeps the tracks flat and in contact with the material. Changing the track pads on a regular basis makes economic sense, to keep the big dozer operating at peak performance and maximising the planned uptime of the machine.
“It’s also certainly not short of performance when it comes to the dozing phase of extraction and stockpiling. After moving over 2.5 million tonnes of abrasive silica sand and rock, the dozer blade finally needs to be re-skinned, which is quite an impressive performance.
“We are also pleased with the Hardox wear package that was fitted by the dealer back in 2017. The protection plates on the draught arms, belly plates and final drive heel blocks are the original items.”
Other Fleet
Patersons of Greenokhill has invested in a range of other Komatsu machinery, including a PC490 excavator, together with a WA470 and a WA380-8 wheel loaders for the Burrowine Moor Quarry. More recently, they have bought a pair of WA500-8 wheel loaders, together with the first Komatsu WA475-10 loader to be supplied in Scotland. It features Komatsu’s new hydraulic-mechanical transmission, getting the best of both worlds in helping to improve both machine performance and fuel economy.
Operator Feedback
Colin Keir, who is normally to be found in one of the site’s Volvo ADTs, provides holiday cover for the big dozer’s main operator. He said, “With the new track shoes fitted, you feel an immediate improvement in the ripping performance, as the single grouser pads bite into the harder rock for much improved traction. It’s a hard-working machine and requires a fair degree of concentration from the operator to get the best out of it. It is also quite rewarding when you see the amount of material it can rip and then doze into a big stockpile. It has amazing performance for sure.
“When its usual operator, Rab Bryson, takes annual leave, I really enjoy the D475A-5. It is quite an experience to sit at the controls of the biggest dozer in Europe.”
Not only is the D475A-5 mechanically well maintained by Marubeni-Komatsu, clearly it’s well looked after by its operators. After thousands of hours operating in abrasive silica sand, the paint on the bodywork is in remarkably good condition and the cab interior looks like new.
Quarry manager Martin commented, “While the dozer comes with many advanced driver aids, such as the anti-track slip feature and torque converter lock-up system, it takes an experienced operator who really knows the quarry geology to get the best out of the machine. We are fortunate we have people who can do just that.”
Dealer Support
Martin declared that the back-up from the dealer has been excellent, as their team carry out regular inspections and routine maintenance to maximise the big dozer’s uptime and performance. He also reports that, given it is an ultra-class dozer not usually seen in Europe, parts availability and response times from Komatsu have been impressive.
He has also been impressed with the commitment and standard of workmanship shown by the recently qualified MarubeniKomatsu field service team. In particular, their recent replacement of the big dozer’s undercarriage was undertaken without incident, making the machine available for work when promised.
At current extraction rates, the site has sufficient reserves to last at least another 55 years. There is no telling what machine technologies will be developed over the next decades, but in the meantime an ultra-class ripper dozer is considered the best way to extract high production volumes of this abrasive and tough material.
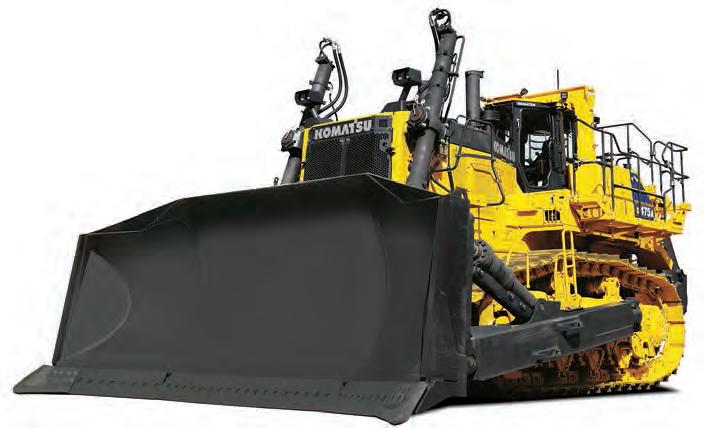
The 115-tonne Komatsu dozer has proved its worth in this demanding application, undertaking the work at an average fuel consumption of just 80 litres of diesel an hour. However, now at over 9000 hours, it is entering the last phase of its carefully planned and monitored first working life.
As exclusively revealed in the previous issue, site owners Patersons of Greenokhill have ordered its replacement. A 1000hp ultra-low emissions Dash 8 version of Komatsu’s D475A ultra-class dozer is due to be commissioned at the Burrowine Moor Quarry within the next few months. Watch this space.
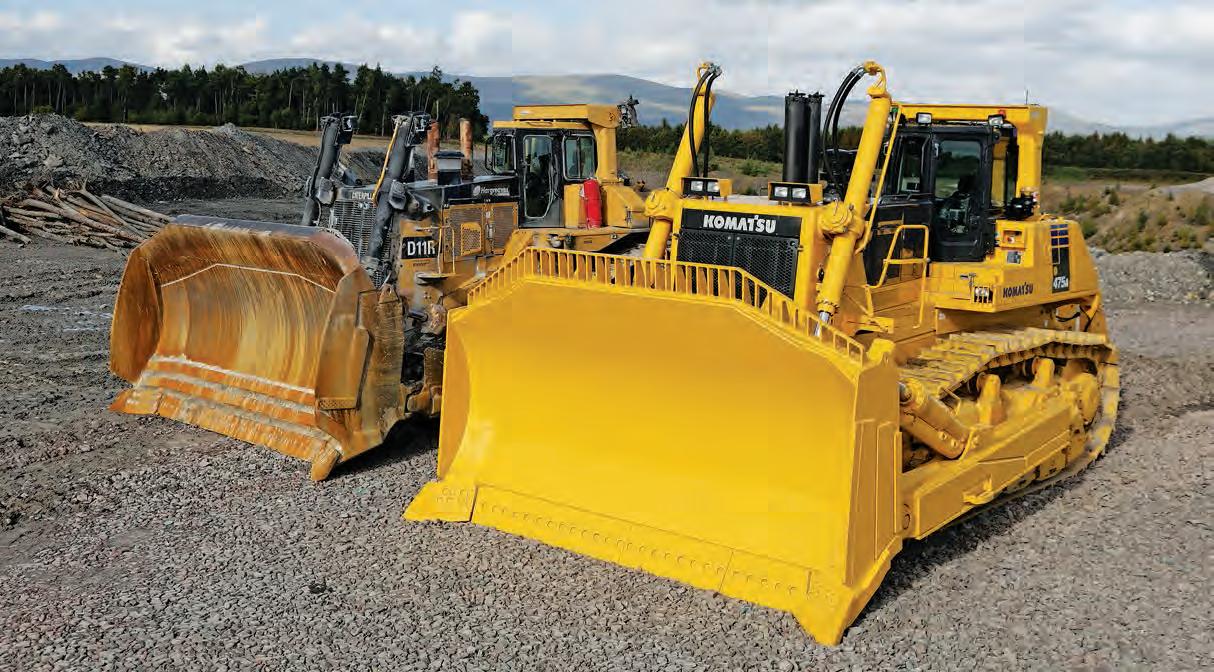
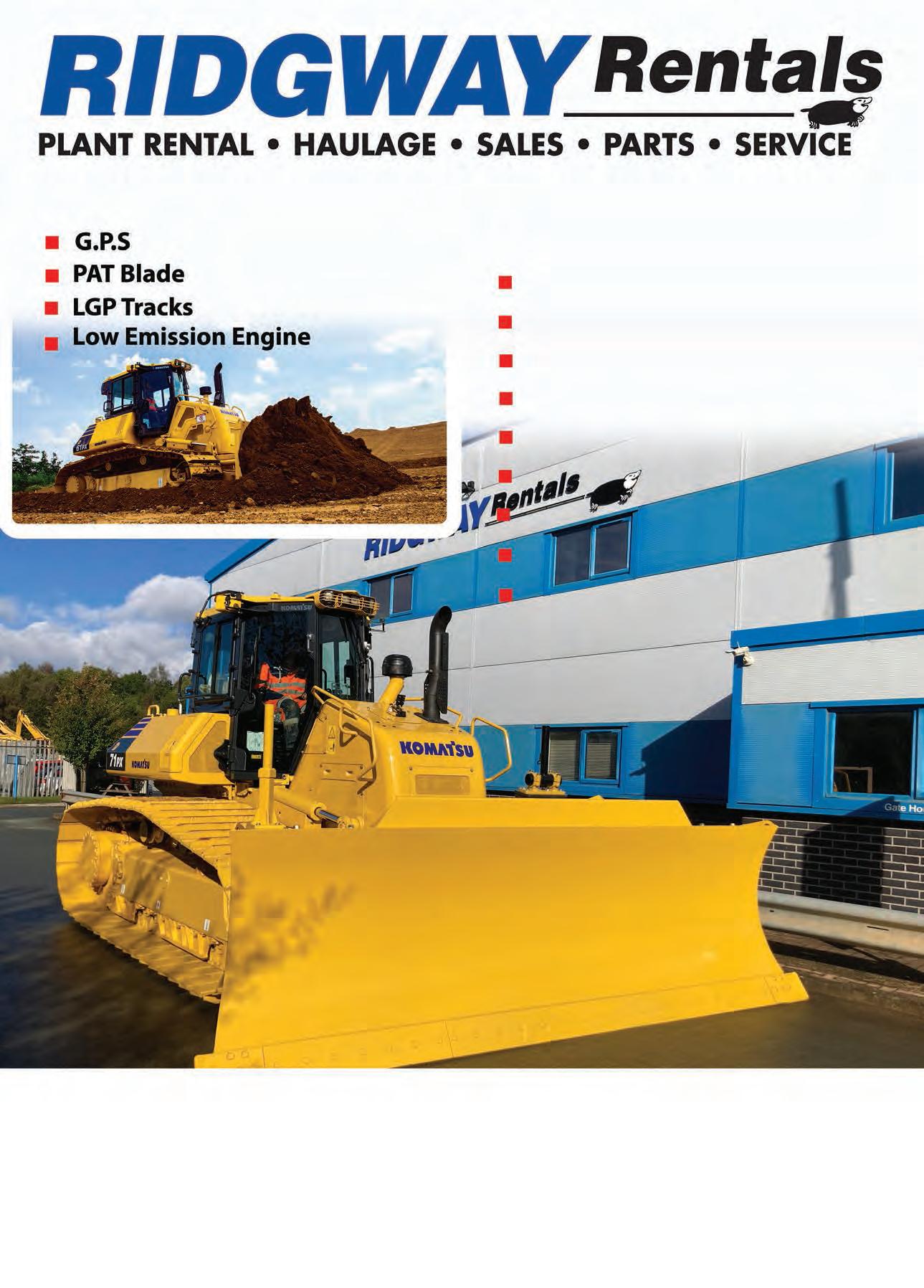
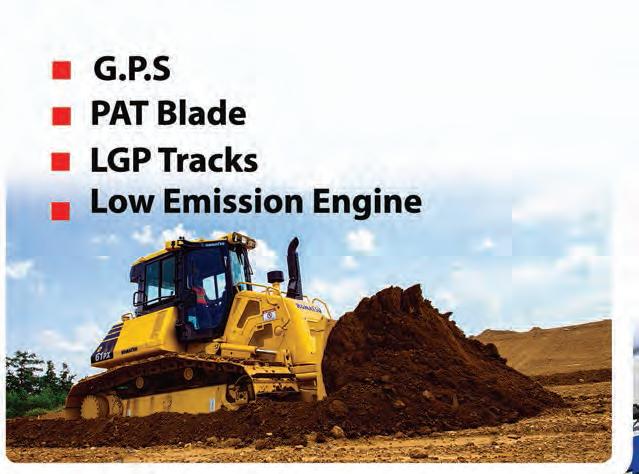
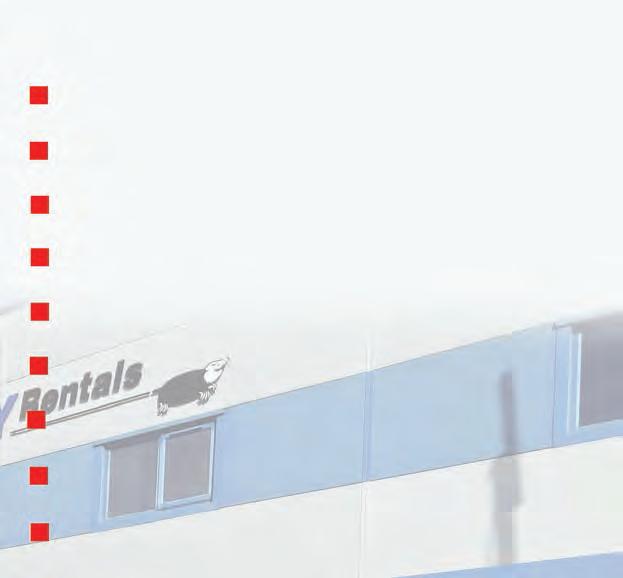
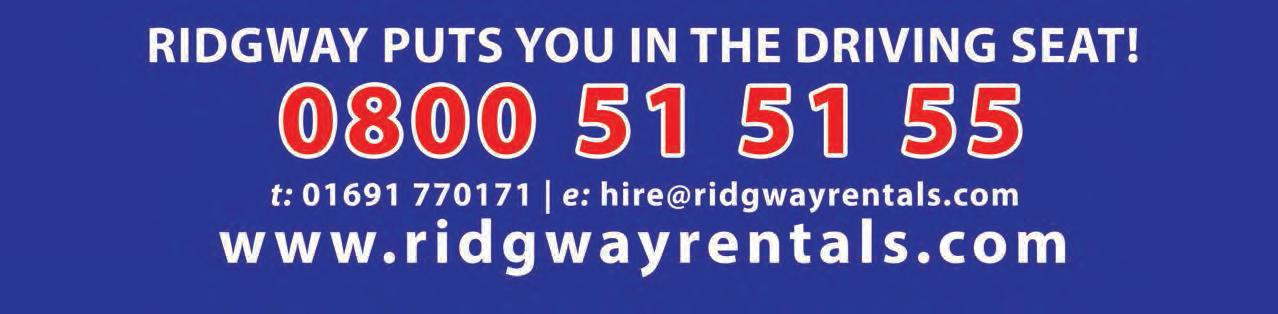
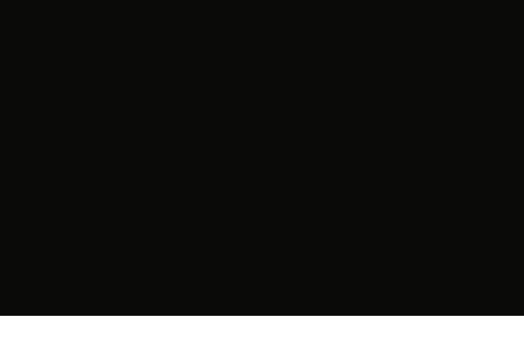
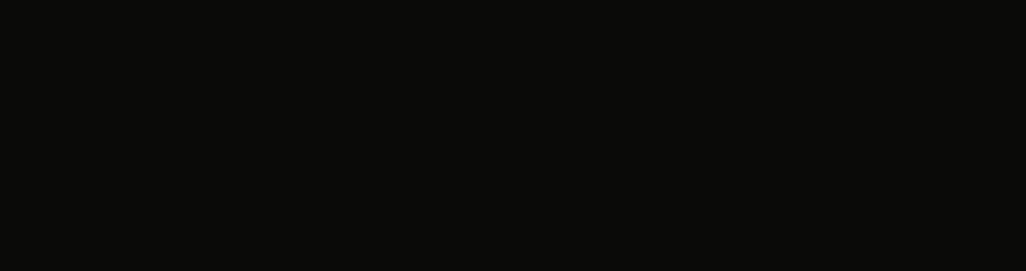
Imagine a skid steer with the power and capabilities of world class loaders but with one difference – fully electric with zero environmental impact.
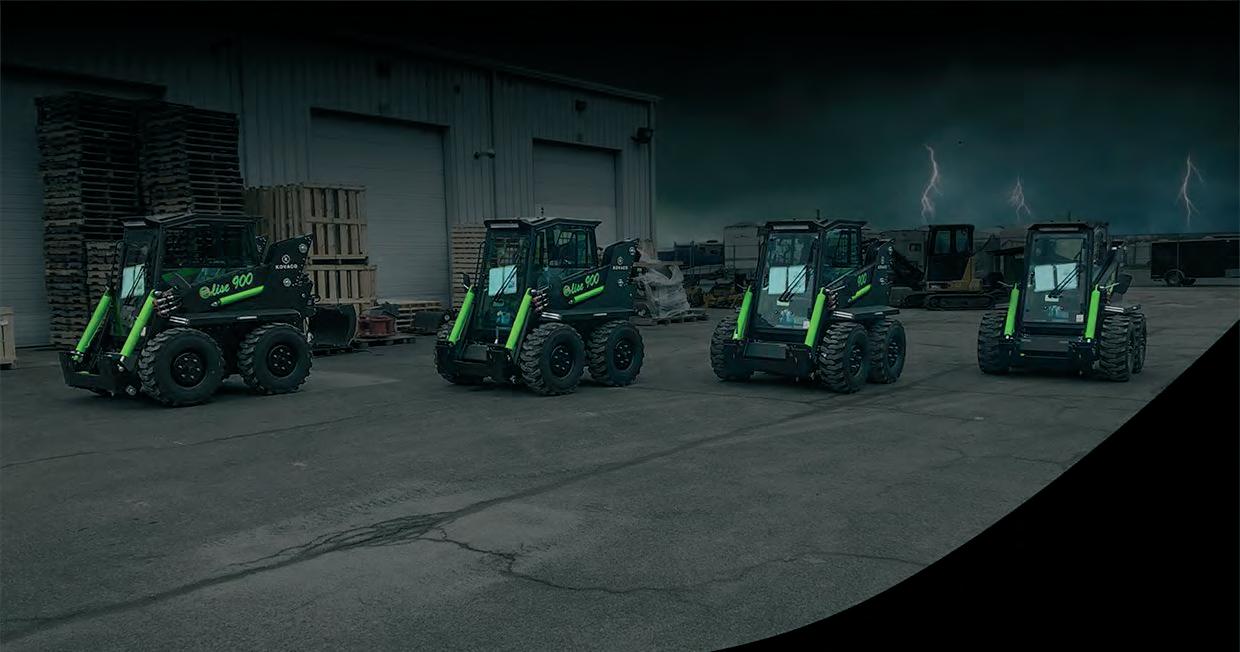
The Elise 900 is the first fully electric skid steer that is 100% environmentally friendly and remains unique to the plant machinery industry.
A fully electric remote controlled compact loader. 100% zero emission and environmentally friendly.
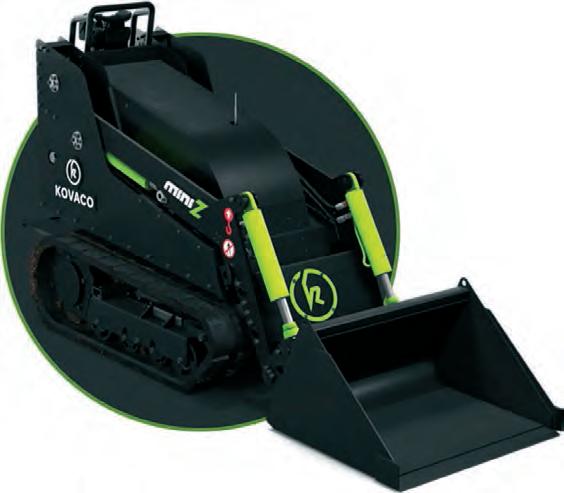

With its compact dimensions, the MiniZ is perfect for work in complicated interiors.
It is suitable in many different environments; agriculture, landscaping, demolition and many more.
