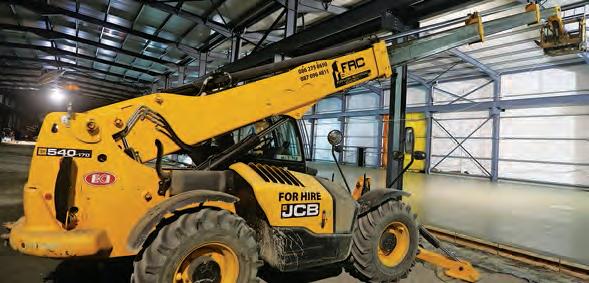
8 minute read
FINE FLATWORKS
Eoghan Daly reports on the high-tech kit used by Kerry-based FRC Construction to construct large, super-flat industrial concrete floors
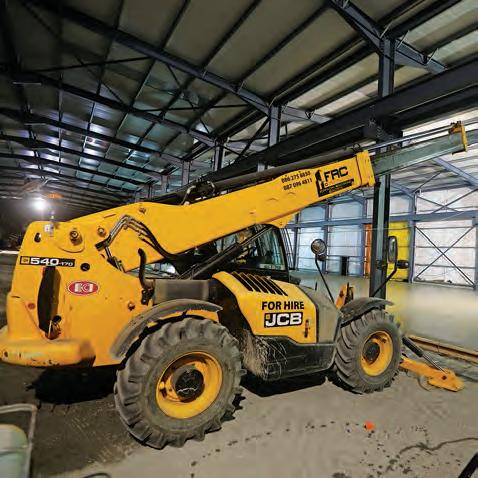
Advertisement
When it comes to warehousing, manufacturing and other specialist industrial buildings, the performance and flatness of the concrete floor slab is of critical importance. By the very nature of commercial structures, they often require substantial concrete pours, adding to the challenge of producing a high-class finish within precise levels of flatness and gradient.
County Kerry-based FRC Construction was established in 2014 by Denis Riordan and Damien Griffin, focusing on formwork, reinforcement and concrete, hence the company name. Denis has a 20-year track record in concrete works over a wide range of project types. In addition to much experience of concrete works, Damien has run his own groundworks company. He said, “We have proved our ability to deliver the specification demanded on large-scale warehouse and commercial building flooring projects. Even though we have a wide range of plant and equipment to cater for formwork and other aspects of concrete construction, flooring has become one of our main specialities.
“Investment in the latest equipment has meant we can cater for large projects and maintain the kind of progress needed, while keeping the quality of the finish we achieve to the highest standards.”
SKID-STEER GRADING
When in the market for a machine to perform precise levelling of the substrate, often within structures, FRC decided that a tracked skid-steer loader was their best option. Hosting a grader attachment and controlled by a 2D laser-based guidance system, it would quickly leave the surface within a few millimetres of the design level. A used TR320 model was sourced from the local Case dealer, as Damien continued, “Availability of tracked skid-steer loaders, new or used, at the time we were looking to purchase was very limited. Luckily Macadam Equipment had a Case TR320 in stock, which they had taken as a trade-in machine from one of their customers.

“We found them good to deal with and since then the service has been good. The dashboard display gave some problems, but they had us back to work as fast as possible. Any parts we need are always with us within 24 hours.”
The TR320 has proved to be a proficient host machine in this application. It is highly manoeuvrable in tight spaces and provides the necessary power, traction and oil flow to get the best from the specialist attachment. Its traction is particularly evident while quickly pushing out piles of material, which it will then precisely grade.
A grader blade was seen as being too cumbersome for operating inside structures, and the FRC team considered that a grader box was better suited to their work. Coupled to the tracked skid-steer, this combination could work close in to any supporting columns and to the edges of the floor area, minimising the need for manual intervention. A grader box would also achieve the final grade in fewer passes than a grading blade, as there is no side spill or micro-drifts of material between passes.

After evaluating numerous grader boxes available for skid-steers, based on a combination of specification and value for money, FRC opted for an American-built Level Best PD model. This design offers bi-directional working, grading can be conducted in both forward and reverse, maximising the productivity of the combination.
Equipped with a Leica 2D laser guidance system, the Case/Level Best combo is grading sub-base material within tolerances of 2mm to 3mm. FRC has recently invested in a Trimble 3D machine guidance system for their strange-looking concrete levelling screed, which is also compatible with this skid-steer and grading box.
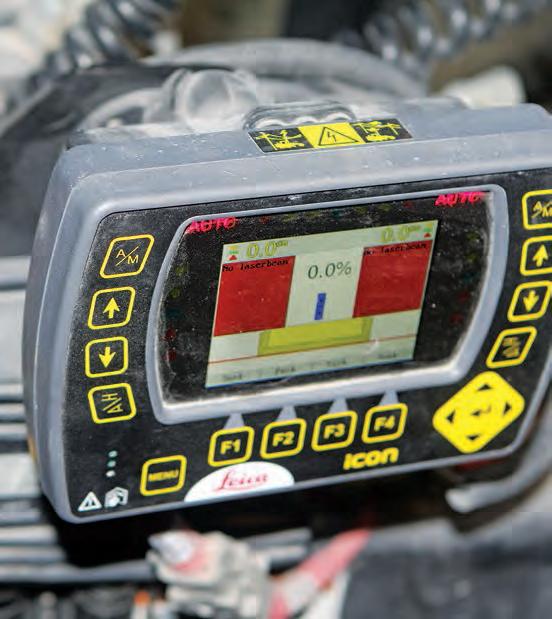
Site Visit
We met the FRC team undertaking a large project at Nenagh, County Tipperary, where the works focused on constructing a high-performance concrete floor to accommodate a major factory extension. The floor area of 8500 square metres was to be formed by six separate pours, leaving the external hard standing and concrete aprons to cover an additional 4500sq.m.
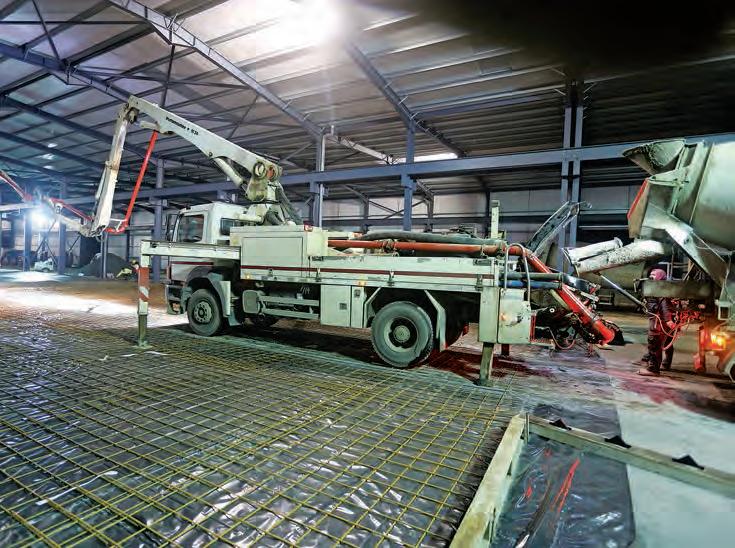
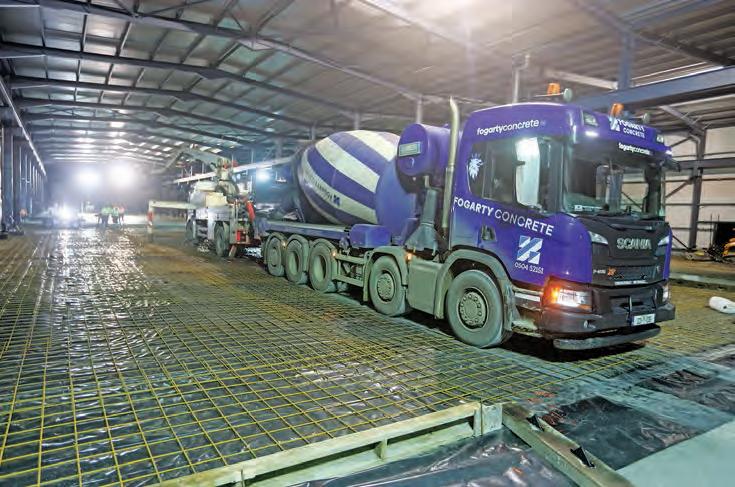
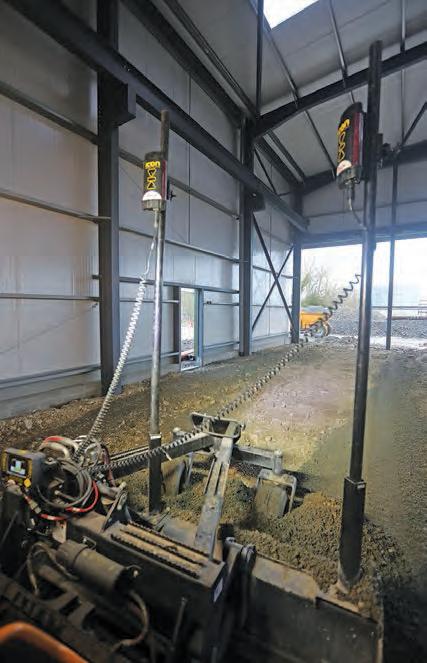
Part of FRC’s success in this specialist work is having in-house plant to cover every aspect of such a project, giving control over the whole process and helping them to meet their commitments on completion targets. Damien is a big fan of JCB excavators, of which FRC has a JS130 and a 67C midi to undertake any groundworks required prior to installing formwork.
The firm also runs a pair of JCB telehandlers, a 13m 540-140 model and a 17m 540-170. They are extensively used on such a project, assisting the formwork crews, handling the rebar mesh sheets and moving the power float kit around the site.
It goes without saying that the accuracy obtained with the Leica-controlled grader attachment on the Case skid-steer is superb, but the most noticeable element of this combination at work is how fast it performs these duties. At first sight, the Level Best grader box seems relatively simplistic, but clearly is a result of decades of experience in this specialist application, as every aspect of its design has been carefully thought through. It can achieve a phenomenal work rate at whatever level of accuracy a machine control system can provide.
Damien continued, “Not only does the TR320 and Level Best box grader allow us to get the preparatory work on floor bases completed extremely quickly and accurately, it also means we have a very high level of control over our projects. Since we are working to such a high level of accuracy, there are no cost overruns on projects due to greater concrete requirements. The contribution of technology makes our work as precise as it possibly can be.”
The Case skid-steer forms the substrate base in two layers, a double-drum vibratory roller constantly working in its wake, which is shortly to be replaced by a new Bomag tandem roller. Following grading and compaction, the damp course membrane and rebar steel are laid by the FRC team.
Inside the structure, different sections of the works are advancing in a production-like manner. As one pour is being completed, the team will be finishing off the rebar work on the following section, and the skid steer working on the next in line.
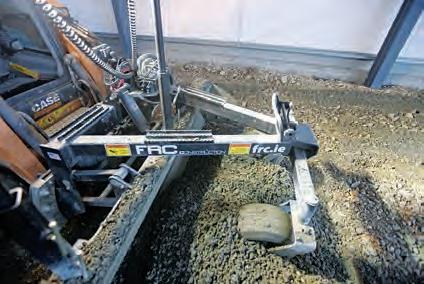
This factory extension project at Nenagh demonstrated the massive logistics effort required for each pour. Due to the large volume of concrete required for a single pour, the contract was split between two local suppliers, Kellys of Fantane and Fogarty Concrete. Both suppliers assigned the maximum number of trucks to support the pour, ensuring an uninterrupted flow of material to the concrete pump serving the project.
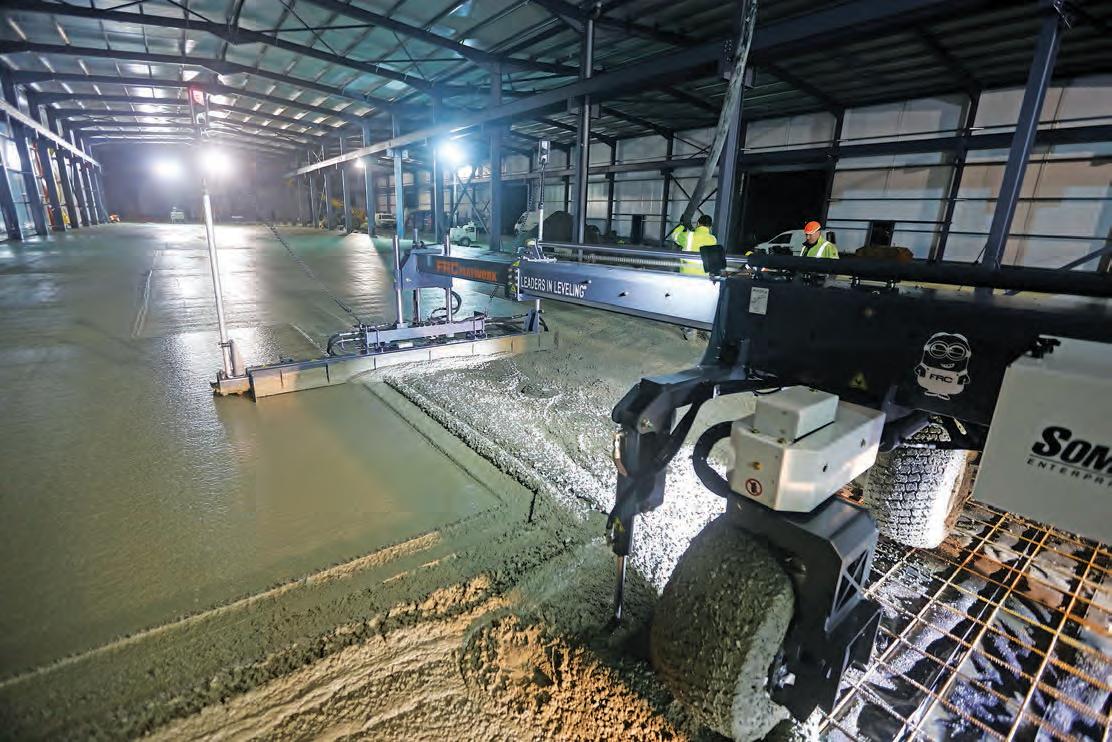
Advance planning eliminated the need to relocate the pump during the pour, resulting in more consistent concrete placement. Even with headroom restrictions within the structure, in the hands of its experienced operator, the concrete pump worked to its full capability.
Concrete Screeding
Despite the concrete pump on this site typically delivering between 300 and 350 cubic metres of concrete for a single pour, the FRC team did not seem intimidated by the enormity of the task in front of them. A long-term user of well-regarded, American-built Somero equipment, their ride-on S-485 laser screed has proved to be highly effective over the years. However, 18 months ago, FRC supplemented it with a two-tonne remote- controlled SRS-4 model, which has taken this aspect of their operation to a new level of efficiency. Working from the adjacent rebar level, the machine reaches across the freshly-poured material with its telescopic boom to level the concrete to a precise grade thanks to its laser system.
It then moves across the rebar and performs the same cycle, until the whole width is levelled and finished, before relocating to allow the concrete pump to fill the section it has been working from. Fitted with four flotation tyres, the machine has no impact on the rebar or damp course membrane. All four wheel stations are on a rotating mount, so it offers tremendous manoeuvrability.
All the functions of the SRS-4 are accomplished by the operator using a remote-control unit. Once in position along the edge of the pour, the machine is levelled with three jack-up stabilisers. This leaves the machine ready to extend its two-section, 5.48m telescopic boom, which carries a standard 3.1m laser screed head.
Employing the Somero soft landing feature, the screed descends on the concrete to the predefined level. The first pass is to level the material and remove any excess. Following passes use the integrated vibrating auger, which achieves a smooth and uniform finish, irrespective of the concrete slump.
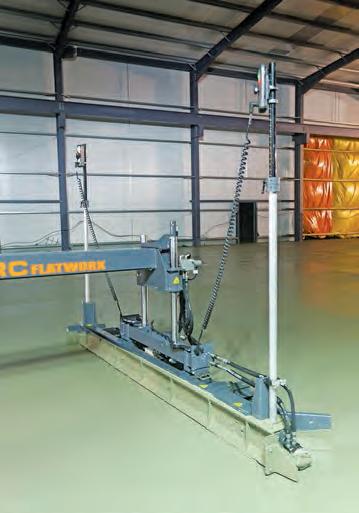
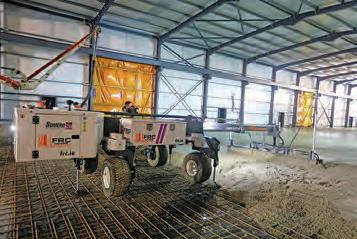
For most of this project, the SRS-4 screed has been working with a laser-based 2D machine control system, producing incredibly flat large surfaces at pre-defined gradients, but without really knowing where it is on the face of the earth.
3d Positioning
One of the final stages of the works at Nenagh was to form the yard surrounding the new factory extension. This was to feature several surface angles, accommodating manhole covers, storm water grids and the like. A labour-intensive task, it could have been tackled in separate sections, but with time and cost implications, and the loss of any technical advantages of a single large pour. FRC therefore invested in a specialist Trimble 3D machine guidance system to help them undertake the screed work on the later stages of this project.
Somero’s Derbyshire-based European dealer greatly assisted in setting up the system on the SRS-4 laser screed and, critically, spending the previous day surveying the pour site. With a base station set-up, the perimeter of the pour was plotted, followed by points for all the different cross falls, manhole covers and surface drainage grids. A digital site plan was generated on the same Trimble module that had been used on a staff to survey the site, before it was physically mounted on the Somero screed.
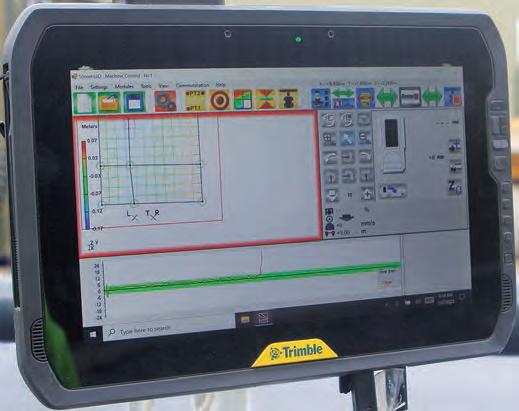
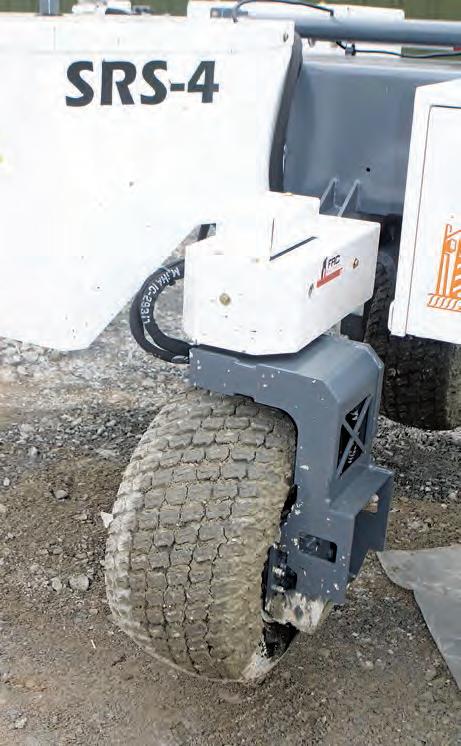
Damien commented, “Working with the 3D-based guidance system on the laser screed has made a major difference. Without it, we would have had to greatly reduce the size of the pour, based on the amount of manual finishing that would have been involved. The whole pour went very smoothly and the ease of use of the system was unbelievable. Technology like this really brings new levels of productivity to the equipment we use and it simply is a vital part of the job we do.”
Finishing Works
Once the concrete has begun to cure, the power floating process can begin, and FRC has a range of ride-on and pedestrian floats to undertake this work. They include machines with combination floating plates as well as dedicated finishing machines.
The latest power float to join the fleet is the Belgian-manufactured Beton Trowel BT1200HH unit. A twin-rotor, ride-on machine, it is designed to cover large areas quickly. It includes integrated water mist dispensers, which assist greatly in achieving the desired finish. In addition to the finish of the floor slab, a power-floating process enhances the concrete, resulting in a harder wearing upper surface. Another key part of the process is cutting expansion joints, which is completed as soon as practicable, using high-capacity, walkbehind floor saws.
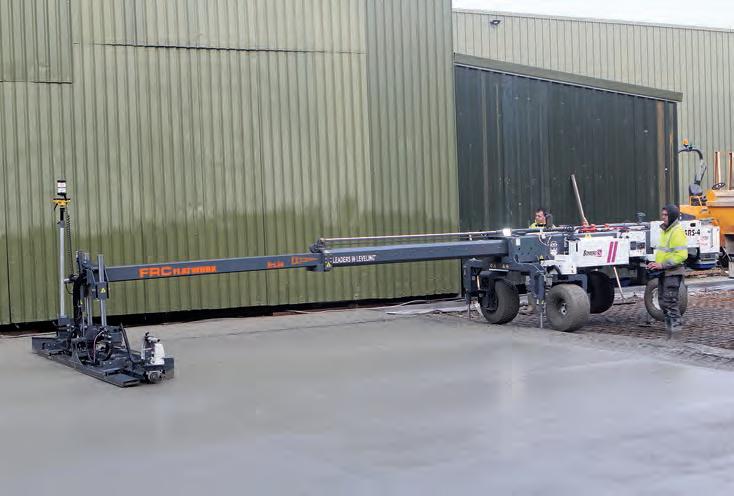
The FRC team worked through the winter months of 2022/23 on the Nenagh project. During windows of appropriate temperatures and weather, every opportunity was taken to advance the project with carefully-planned large pours, including late night and early morning stints.
With skilled operators and specialist machinery to undertake high-value work on large concrete pours, FRC Flatworks continues to invest in technology. Their recent move into 3D machine guidance/ control systems is already getting the maximum benefit from their futuristiclooking telescopic screed, which will also open up more opportunities for their skid-steer/grader combination.
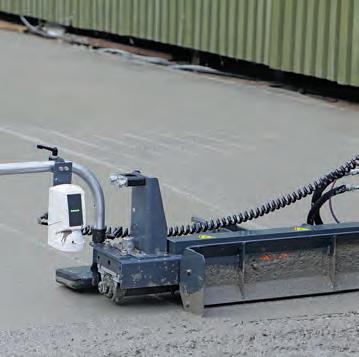
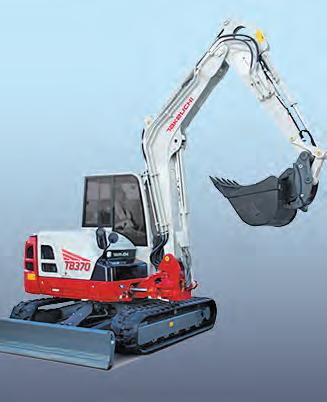
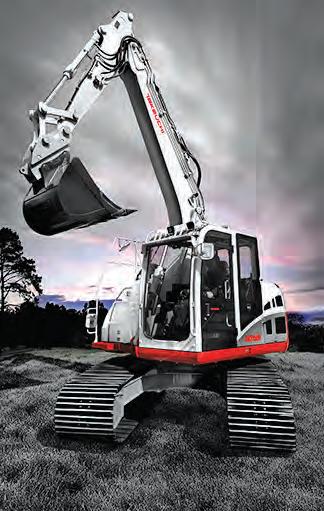
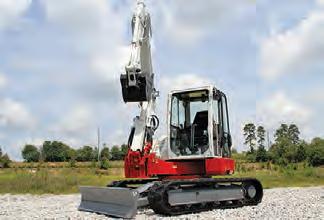
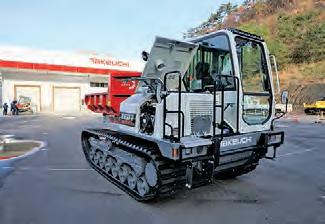

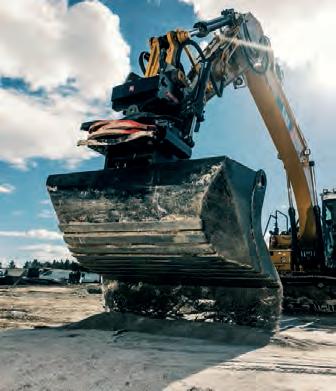
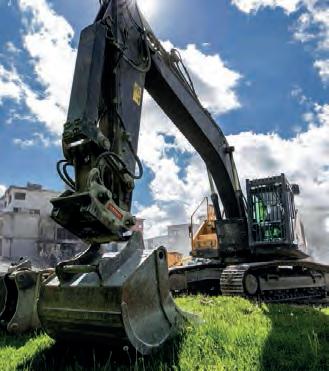

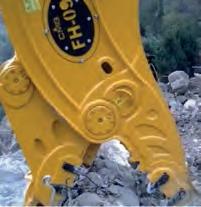
