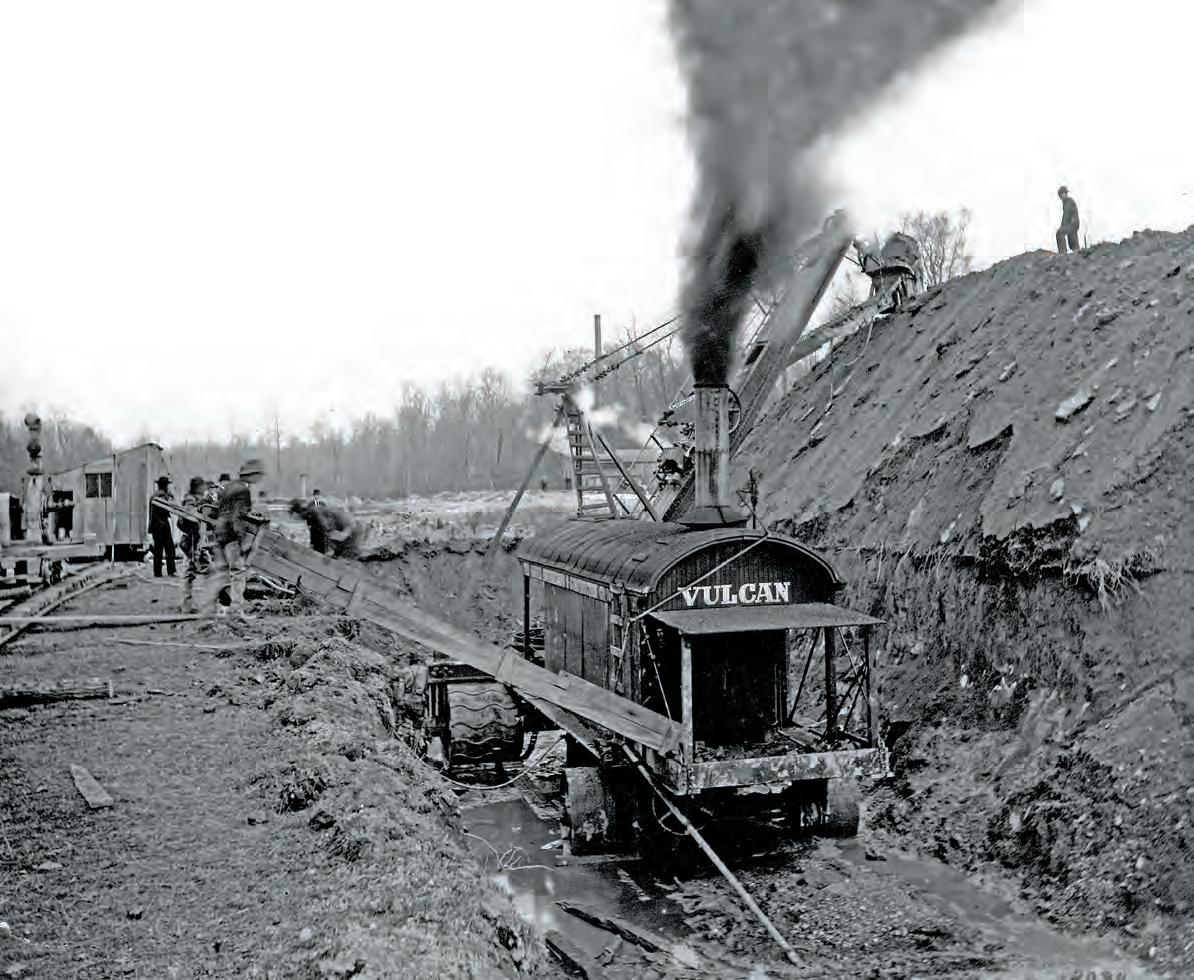
6 minute read
LARGEST MACHINES ON EARTH
Keith Haddock looks at the history of giant stripping shovels, focusing on the rivalry between American manufacturers Marion and Bucyrus
Once popular for removing relatively shallow depths of overburden, there is no known example of a mining stripping shovel still in use today. These long-reach, rope-operated face shovels were not designed to load trucks. Rather they cast the material aside, thereby uncovering the next strip to be mined without the costly need for a fleet of dumpers to move the overburden.
Advertisement
Stripping shovels were to become the giants of the earthmoving industry and included some of the heaviest pieces of equipment ever to move on land. Most notable was the 15,000-ton Marion 6360 with a 180-cubic-yard dipper, more about this later.
As shallow deposits of valuable minerals around the world became exhausted, large-scale surface mines increasingly turned to the greater working range provided by walking draglines. They are designed to remove deeper layers of overburden, casting the material directly into the previously mined-out cut. In their day, however, where the depth was within range, stripping shovels were the more efficient means of moving overburden. They offered a shorter cycle time than a dragline and could dig through harder material, often eliminating the cost of drilling and blasting. They reached their zenith in the 1950s and 1960s, uncovering the coal deposits of the Illinois Basin.
From Rail To Tracks
The need for a long-reach, rope-operated shovel was recognised as early as 1899, when American manufacturer Vulcan produced a steam-powered version, initially working on rails. Providing a boom swing of just 200 degrees, such small machines went on to pioneer the concept, but proved of limited value in stripping applications. A decade later, much larger fully- revolving, steam-powered stripping shovels were developed, requiring two sets of parallel rail tracks to support their weight. The first commercially available example was the 1911 Marion 250 model, carrying a 3.5-cubic-yard dipper on a 65ft-long boom. It was followed almost immediately by the Bucyrus 150-B, featuring a 2.5-yard dipper on a 60ft boom.
In the early part of the 20th century manufacturers in Europe, Russia and the USA began to produce steam-powered stripping shovels. However, only a few ventured into designing and building increasingly large machines. Marion and Bucyrus came to dominate the huge American market, and their stripping shovels were also used throughout the world.
Such shovels first came off rail tracks and travelled on their own crawler undercarriage in the early 1920s. A 40% cost increase over the rail-mounted version resulted in a slow uptake of tracked stripping shovels at first. Then early adopters of the concept proved that the additional capital cost was soon offset by the machine’s superior mobility, and ground crews could be reduced from eight to one. Orders for rail-mounted stripping shovels quickly diminished.
Steam Shovels
The first crawler-mounted stripping shovel was the 81-ton, 2.5-yard Bucyrus 80-B model, the first example of which was delivered in 1922. This heralded a new class of machine, but offered a small capacity in comparison to early 1920s rail-mounted machines.

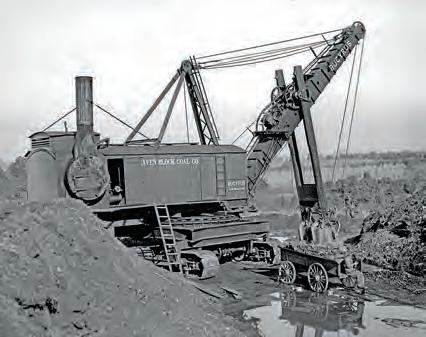

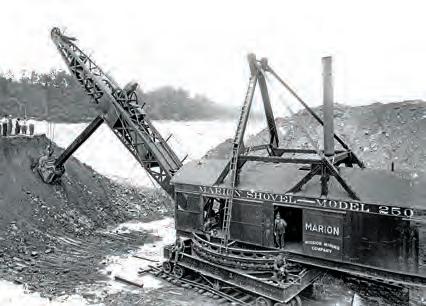
The 80-B did, however, mark the introduction of the Bucyrus four-crawler track system, which would become a feature of their stripping shovels for the rest of the decade. Two of the four-crawler assemblies were attached to a pivoting beam to equalise stresses when passing over uneven ground. To stabilise the machine while digging, a screw jack at each end of the beam locked it tightly to the lower frame. On earlier machines, these screw jacks were hand operated, and the driver and his oiler had to remember to slacken them before moving the shovel.
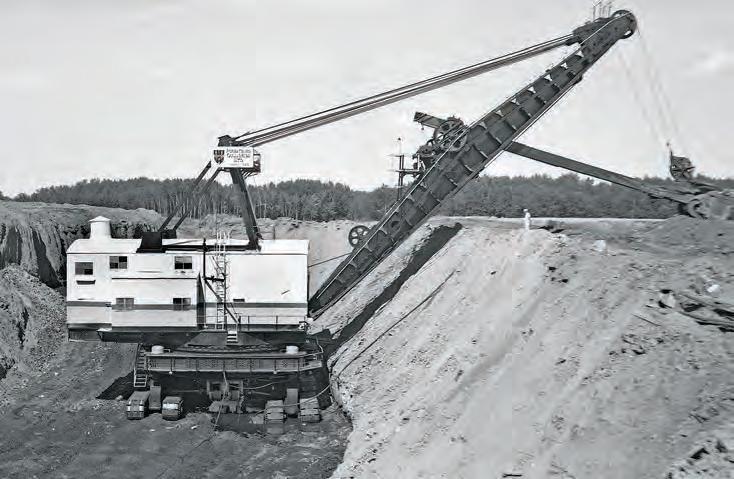
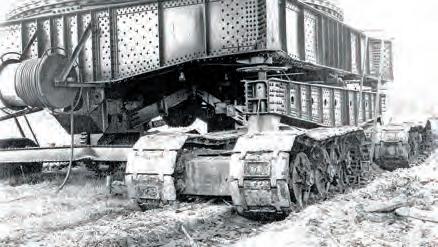
In 1923, the Marion model 350 broke the world record for stripping shovels. It weighed a massive 560 tons and wielded an 8yd dipper on a 90ft boom. Initially rail-mounted, this huge machine was offered with crawler tracks from 1925.
Drive to the crawlers was transmitted from the main hoist motor, located in the revolving frame, through the centre pintle, then out to each of the four crawler assemblies through a series shafts, gears and clutches. They were operated by the groundman, who would receive hand signals from the operator high above. The Marion 350 series machines were a great success, and 47 units were sold before production ended in 1929. Bucyrus responded with its largest stripping shovel to date, the 320-B model that first appeared in 1924 as an eight-yard, railmounted machine weighing 490 tons. The first machines were steam powered and moved on twin rail tracks; later machines were upgraded to electric power and gained crawler undercarriages. They featured the first use of eight crawler tracks, arranged in pairs at each corner of the machine.
The 500t class Bucyrus 320-B and Marion 350 stripping shovels were probably the largest steam-powered machines ever to move on land. These 8cu.yd capacity machines were pinnacles of 1920s earthmoving technology. They also appeared to have reached the practical limit for steam-powered tracked stripping shovels, particularly as customers were demanding significantly higher capacity machines.
Giant Shovels
In 1935 Bucyrus-Erie introduced the 30-yard 950-B model, at 1250 tons, it was the world’s largest stripping shovel. The 950-B pioneered many features that would be seen on subsequent Bucyrus machines. They included a two-part pinned boom with single tubular dipper, which eliminated torsion stresses. The rope crowd machinery was mounted on the revolving frame, minimising swing inertia. Independent motors in each of the four crawler assemblies eliminated the need for a complicated gear and shaft drive from the upper works. There was even an automatic hydraulic levelling system that dispensed with the need for screw-type jacks.
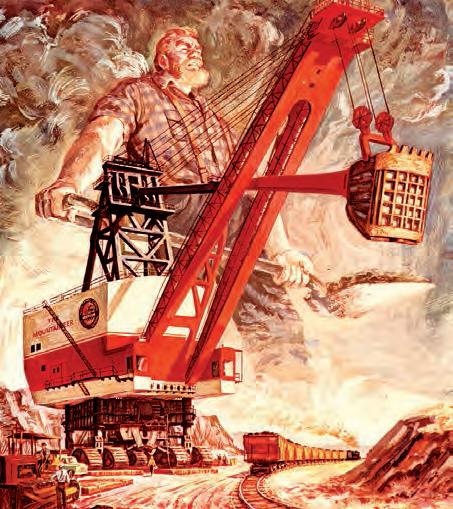
The 950-B also featured a balanced hoist system, in which a moving counterweight at the machine’s rear balanced the weight of the arm and bucket as it moved up and down. This system was pioneered on the 18-yard 750-B shovel launched a few years earlier in 1930.
Stripping shovels gradually increased in size during the 1940s, principally driven by demand from American surface coal sites. The following two decades saw the development of the largest single-bucket earthmoving machines ever made. A breakthrough came in 1955, when
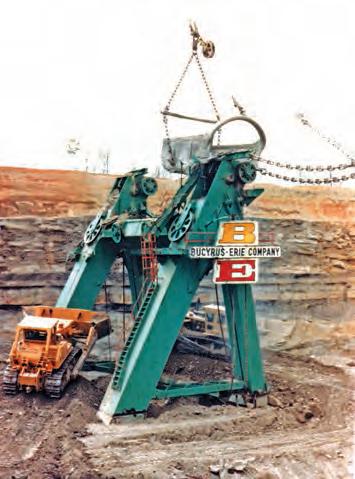
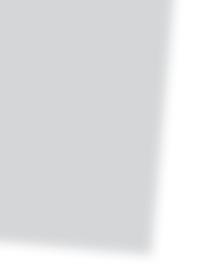
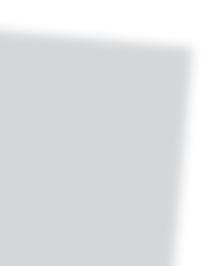
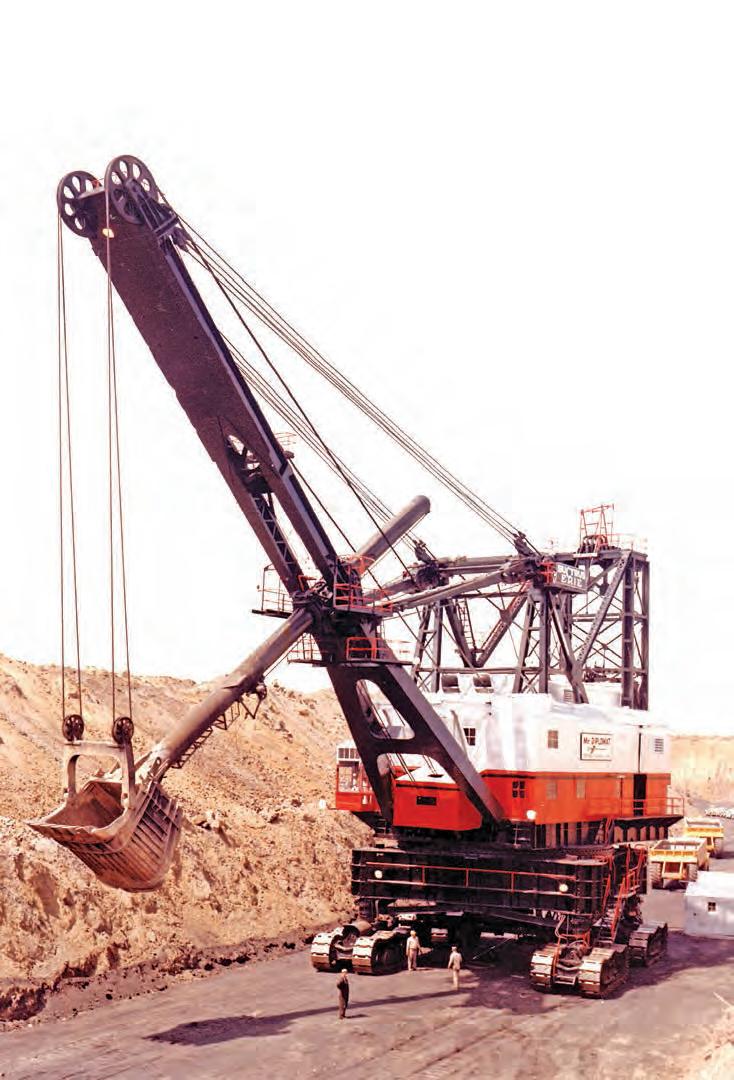
Hanna Coal, now Consol Energy, ordered a stripping shovel of record proportions for its coal mining operations in eastern Ohio. Christened the ‘Mountaineer’, the Marionbuilt 2750-ton monster wielded a dipper rated at 65 cubic yards, on a boom 150ft long. The single feature that most fascinated visitors was the three-passenger lift installed in the machines 6ft-diameter centre pin.
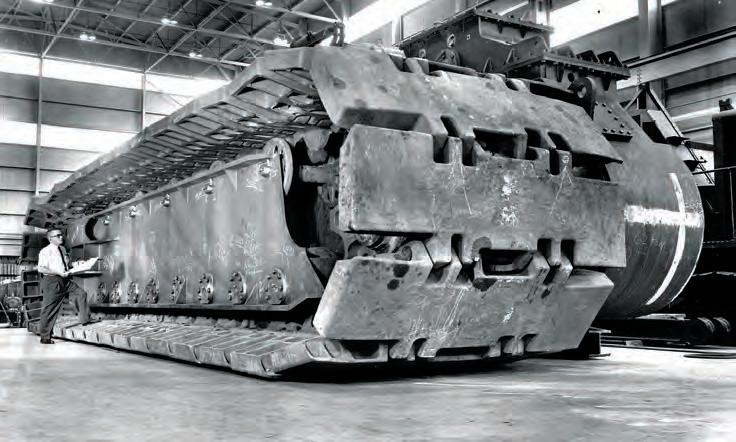
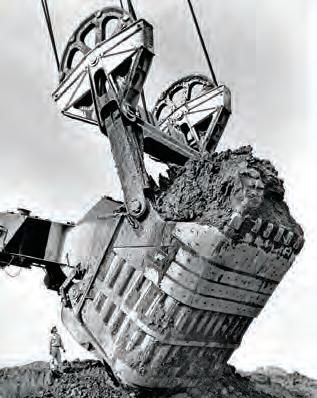
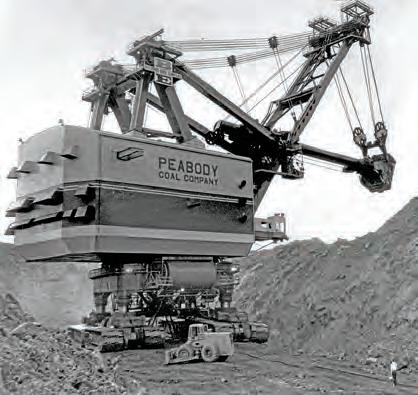
The machine also featured Marion’s patent knee-action crowd system, which first appeared on the 35-yard 5561 model shovel of 1940. The knee action takes the weight and bending stress off the boom, due to the dipper stick being mounted on a moveable and independent stiff leg. The crowd mechanism is located on the gantry. For Bucyrus-Erie, the first 1650-B model delivered in 1956 marked the start of the super-stripper era, when coal operators could efficiently move into higher stripping ratios and deeper overburden. The 1650-B was designed on similar lines to the smaller 1050-B model, including a counterbalanced hoist and independent motordriven crawler assemblies. The first example of the 1650-B carried a 55-yard dipper on a 145ft boom and was purchased by Peabody Coal for its River Queen Mine
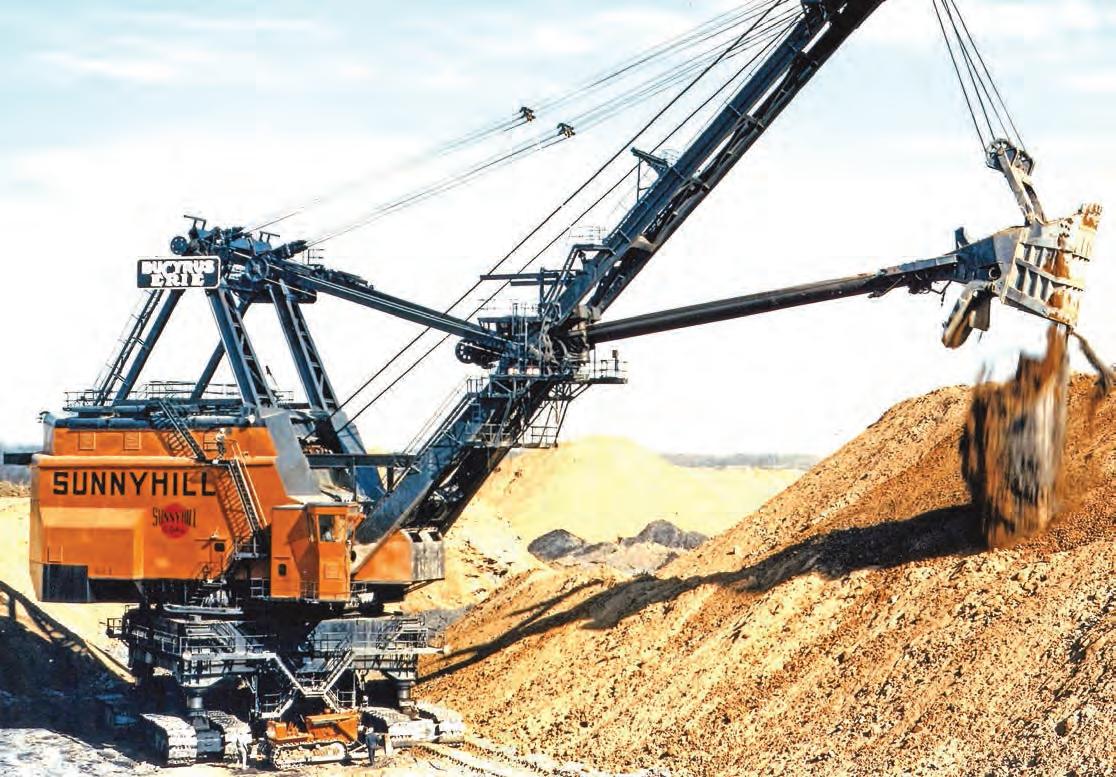
Right
Making international news around the world in 1960, Peabody Coal ordered a 115-yard stripping shovel from Bucyrus Erie, which would weigh some 9000 tons. Before this first example of the 3850-B model went to work in 1962, Peabody ordered a second example with a slightly shorter boom carrying an even larger 140-yard capacity dipper. Weighing 9350 tons, the new world record holder began stripping in 1964.


Largest of all stripping shovels, and billed as the world’s largest mobile land machine of any type, was the Marion 6360 shovel. Erected at the Captain Mine of the Southwestern Illinois Coal Corporation, the machine worked from 1965 to 1991 when it was destroyed by fire. Weighing some 15,000 tons, the 6360 moved some 810 million cubic yards of overburden during its lifetime. The eight-crawler undercarriage, with 15ft-high crawlers, was the same design Marion used to build the two giant transporters, still used today, for moving rockets to their launch pads at Cape Canaveral, Florida.
End Of The Giants
Although giant stripping shovels served their owners handsomely, uncovering huge amounts of coal to meet the hungry appetites of the coal-fired generating stations, they worked their way into obsolescence.
The main reason for their demise was that during the 1980s the USA saw a rapid rise in coal output from the western states, particularly Wyoming. This low-sulphur coal was found in thick seams under shallow overburden and was cheaper to mine. This more environmentally-friendly western coal captured markets traditionally supplied by