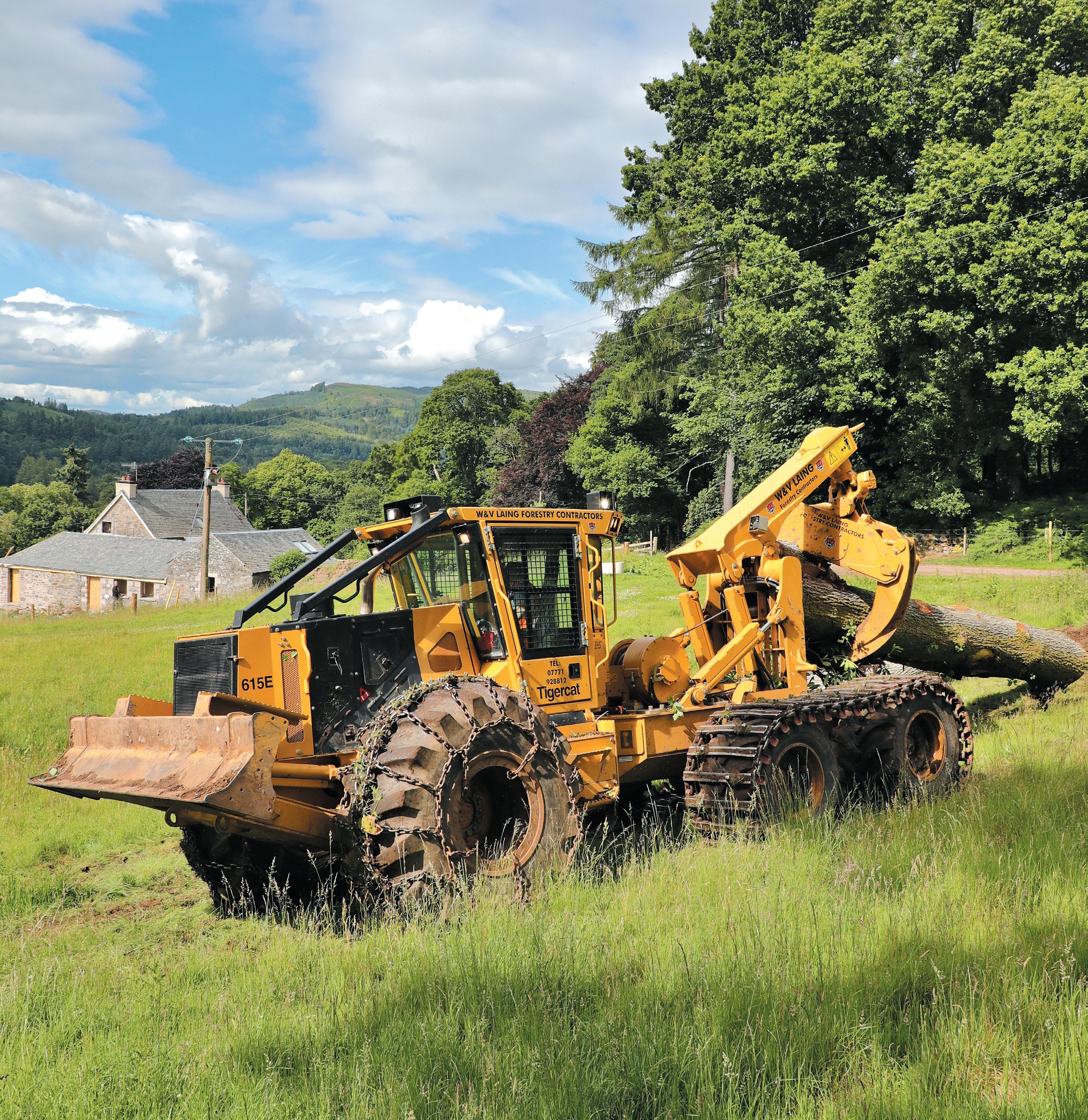
11 minute read
HARDWOOD EXTRACTION
SWEET SIX
W & V Laing Timber Contractors gives David Wylie its verdict on its six-wheeled Tigercat 615E skidder operating on a hardwood extraction project near Dunkeld in Scotland
Advertisement
Pitlochry-based W & V Laing Timber
Contractors is a family business established in 1983 by Willie Laing and his wife Violet. In 1977, Willie – aged 19 – began his career at the forestry commission, working with skylines to extract timber from clearfell sites. Six years later, Willie started his forestry business with just a chainsaw, hand-cutting trees for a number of years and buying his first piece of forestry machinery in the shape of an old Ford County four-wheel drive tractor, which pulled a logging trailer operating as a timber forwarder.
As Willie was building up the business, he invested in his first skidder machine – a Clarke Ranger model which gave good service. Then Willie bought a pre-owned John Deere 648 model in France, which he later discovered was limited by its grab lifting height and winch performance, as the winch power was either on or off, therefore getting a progressive pull in some applications was a real challenge, although the machine served the company well enough to last four years.
In 2015, Willie started looking at buying a Tigercat skidder. A pre-owned unit was located in Belgium, but it had no winch fitted and the second-hand price was not that far off a new Tigercat 615E once a new winch was added to the equation. So, Willie decided to take the plunge and bought a new Tigercat 615E model from UK dealer Treetop Forestry and paid £270,000 including band tracks, front wheel chains and so on. This 615E model was commissioned in December 2015 and has been used very successfully, albeit for a mere 700 hours, but more on this later…
W & V Laing Timber Contractors predominantly undertakes forestry projects
Steep slopes are no problem for the sixwheeled Tigercat.
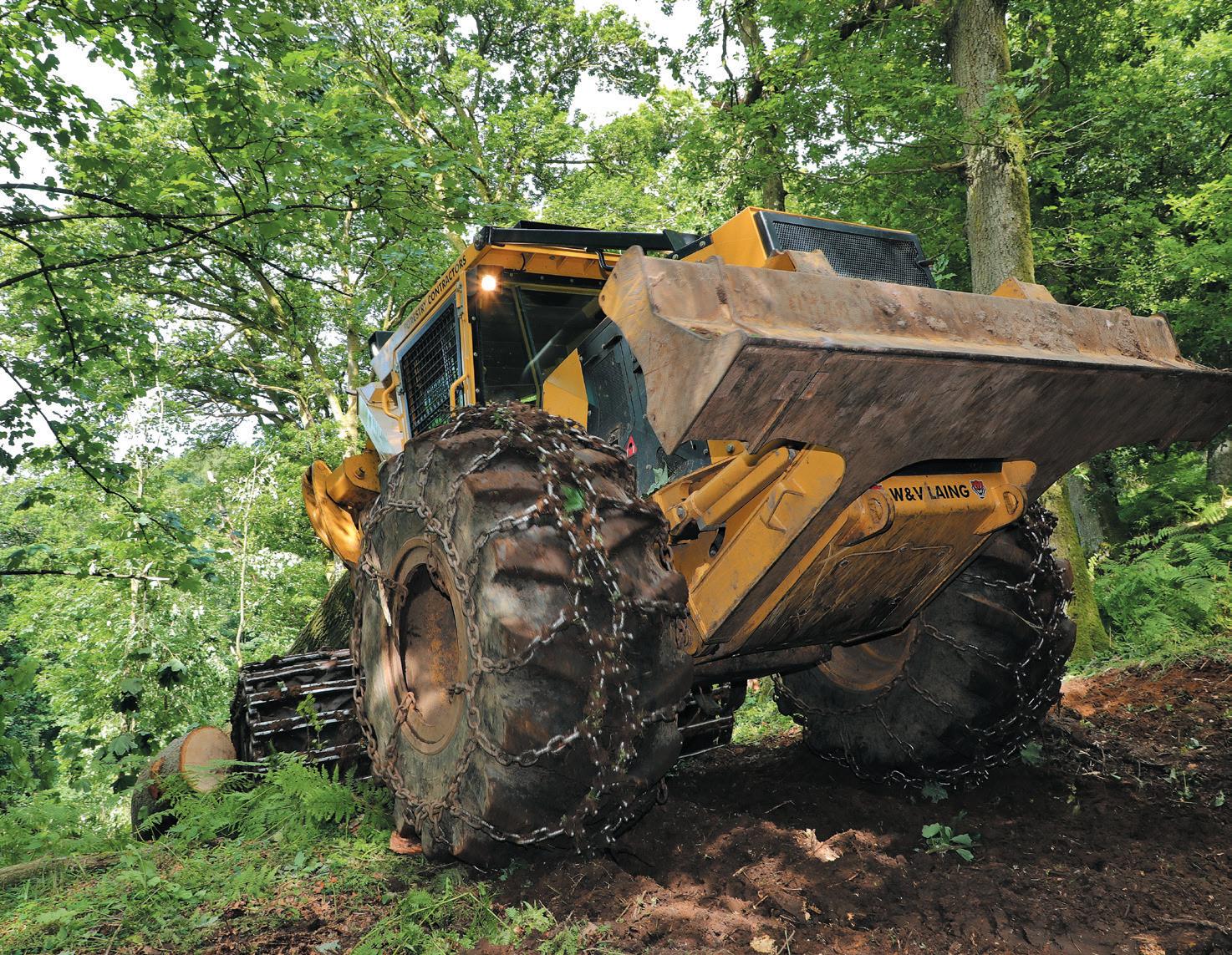
in Scotland and has also covered a number of special projects in the UK where its skills, experience and Tigercat 615E skidder are required. The company also operates new Komatsu 875, 890 and 895 model forwarders (one of which was temporarily converted into a makeshift haulage vehicle – see separate box), and its services include: site clearance, large vehicle recovery, tree surgery, dangerous tree removal, chipping and mulching, and tree recycling timber contractors, to name but a few.
SITE VISIT
I met up with Willie Laing and his experienced crew in a managed woodland
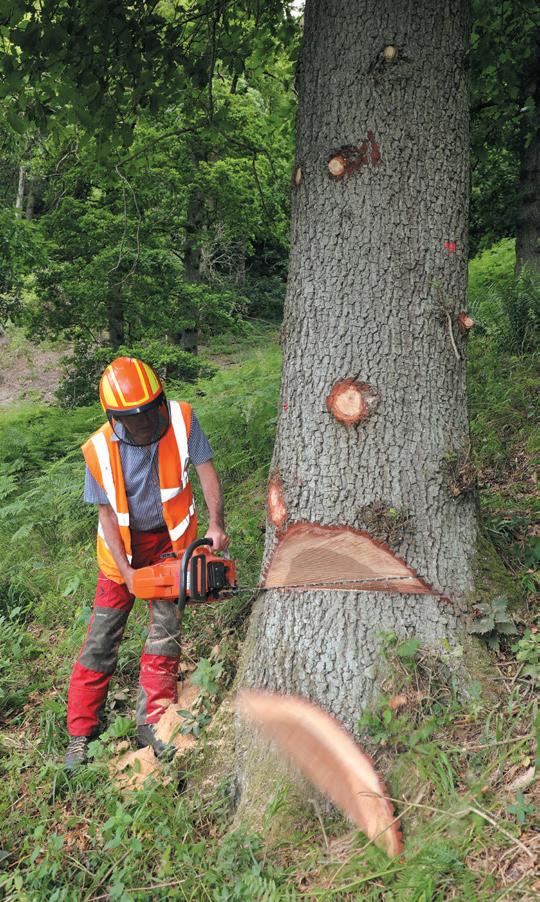
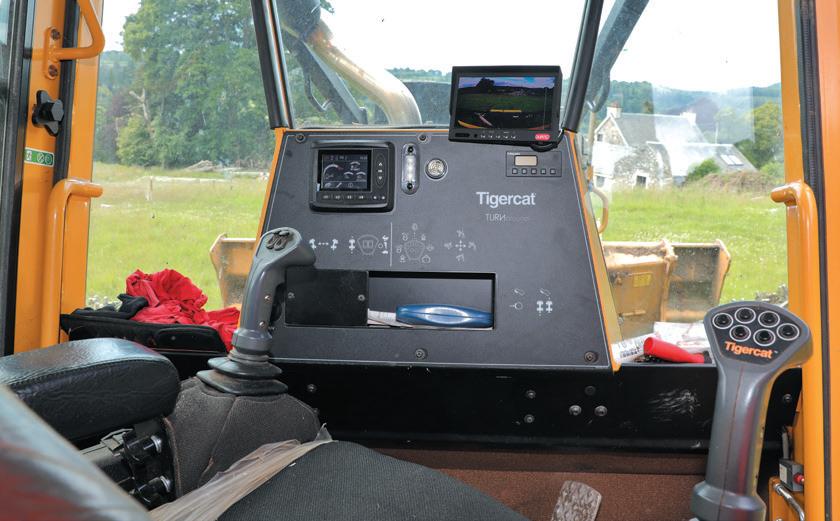
Willie Laing at the controls, perched on the swivelling seat.

near Dunkeld in Perthshire, Scotland. Willie explained that he has been working for his client – Chantler Timber which is one of Willie usually carries Britain’s largest round the responsibility for hardwood timber this part of the job. purchasers – on this and other projects for over 30 years. The original contract was to carefully fell 75 high-value oak trees that have been maturing for over 150 years or more. However, the woodland is carefully managed by the local landowner and the final total will be just under 60 oak trees, which will be harvested in a carefully designed thinning plan.
At the time of our visit, Willie was ably assisted by two local self-employed experienced hand-cutters – equipped with
Husqvarna chainsaws – that Willie had hired, and was a family affair, with one of the men being his brotherin-law. As an aside, his fatherin-law (at 78 years young), currently working on a soft
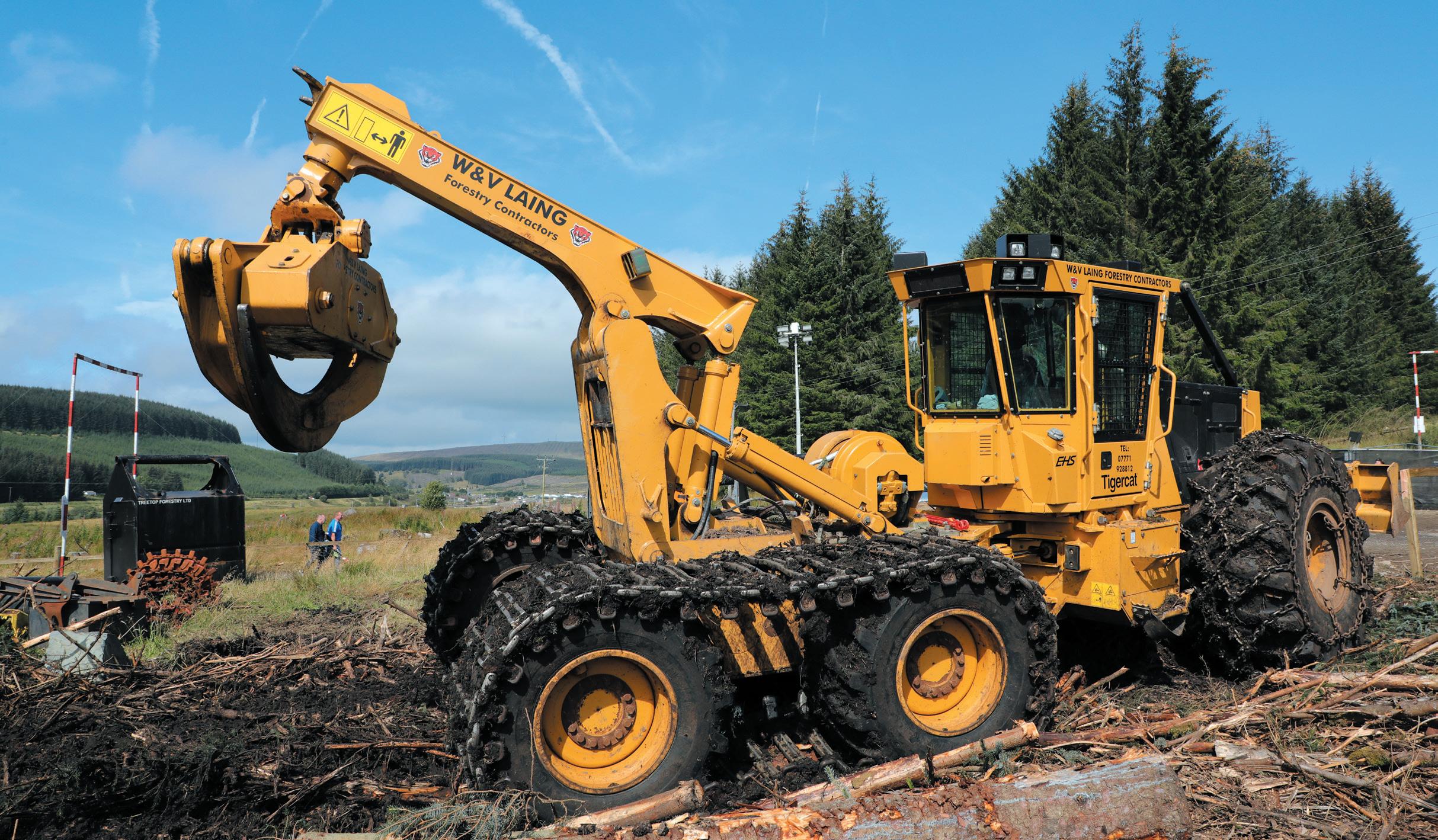
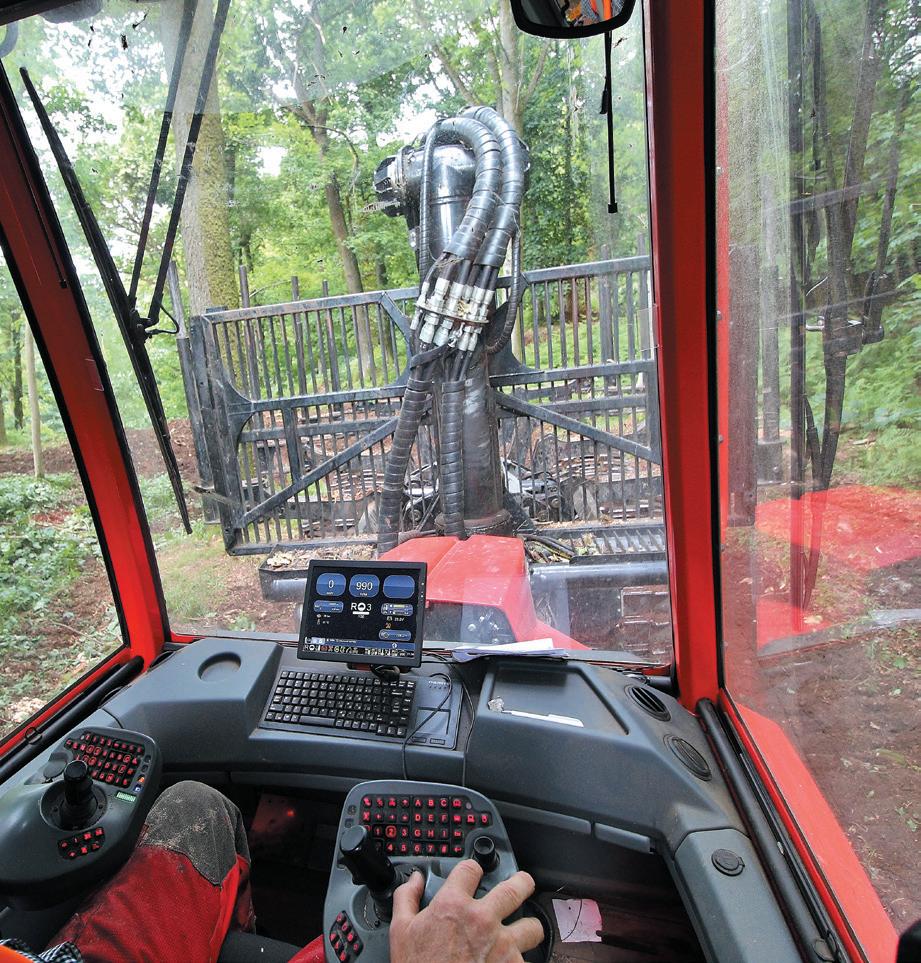
wood clearfell site, is a regular operator of another forwarder, a 2017 Komatsu 875 model.
Felling high-value timber such as oak is a highly skilled job, Willie explained. On this site, the crew manage to fell around 10 trees on a good day, and as few as four (it is worth bearing in mind a harvester clearfelling softwood will cut and process approximately 10 trees in around six minutes) if the tree is laying in a difficult angle or is likely to impact on surrounding trees or structures. In which case, the Tigercat’s powerful 65m long winch rope will be attached and pulled in the correct direction for safe and undamaged felling operations.
The other key consideration is the tree’s branch structure, particularly at the top, if the tree is divided into two large branch limbs. If these are not felled in the right direction, the thick upper branches could cause the entire tree to split right down the middle of the trunk when it hits the ground, which will significantly devalue the timber for his client. This is even more important with the highest value hardwood timber, such as burr oak or burr elm wood.
With this in mind, great care is also taken when sawing the base of the tree. Willie normally carries the responsibility for this part of the operation himself. He starts off by cutting out a mouth shape – known as the sink cut – in the direction he wants the tree to fall. Once this is done, he then cuts directly and straight into the centre of the tree trunk in order to break as much centre contact as possible, leaving the outer wood holding the tree steady.
He then carefully cuts off any outer buttress parts that could remain attached – and also cause the tree to split apart as it falls – before cutting around the remaining tree with his powerful 90cc two-stroke long chain bar Husqvarna chainsaw. The final cut is normally carried out at the back of the tree, so that Willie can make a safe and fast exit in the opposite direction just as the tree starts to fall over.
During this operation, Willie and the tree are watched over by the two hand-cutters, who are positioned up the hill and act as his extra eyes and ears to help ensure each tree is felled as safely as possible. Once the tree is felled, the two hand-cutters move in to delimber the tree. Some of the thinner sections are marked off for cutting and then loaded onto the big Komatsu forwarder. High voltage power lines are another

Left: The Tigercat 615E is kept busy all year de-bogging other forestry equipment.
obvious hazard on this operation (the Tigercat has an advantage in this area, with its lower height profile and grapple), so measures have been taken to safely route the tall forwarder to another stockpiling area, which also has good access for the HGV timber wagons. Once all the timber has been felled and stockpiled, the client attends site to mark up the high-value timber to their own requirements, before heading to the sawmill to be cut for high-end timber products.
Cab view from the Komatsu 895 forwarder.
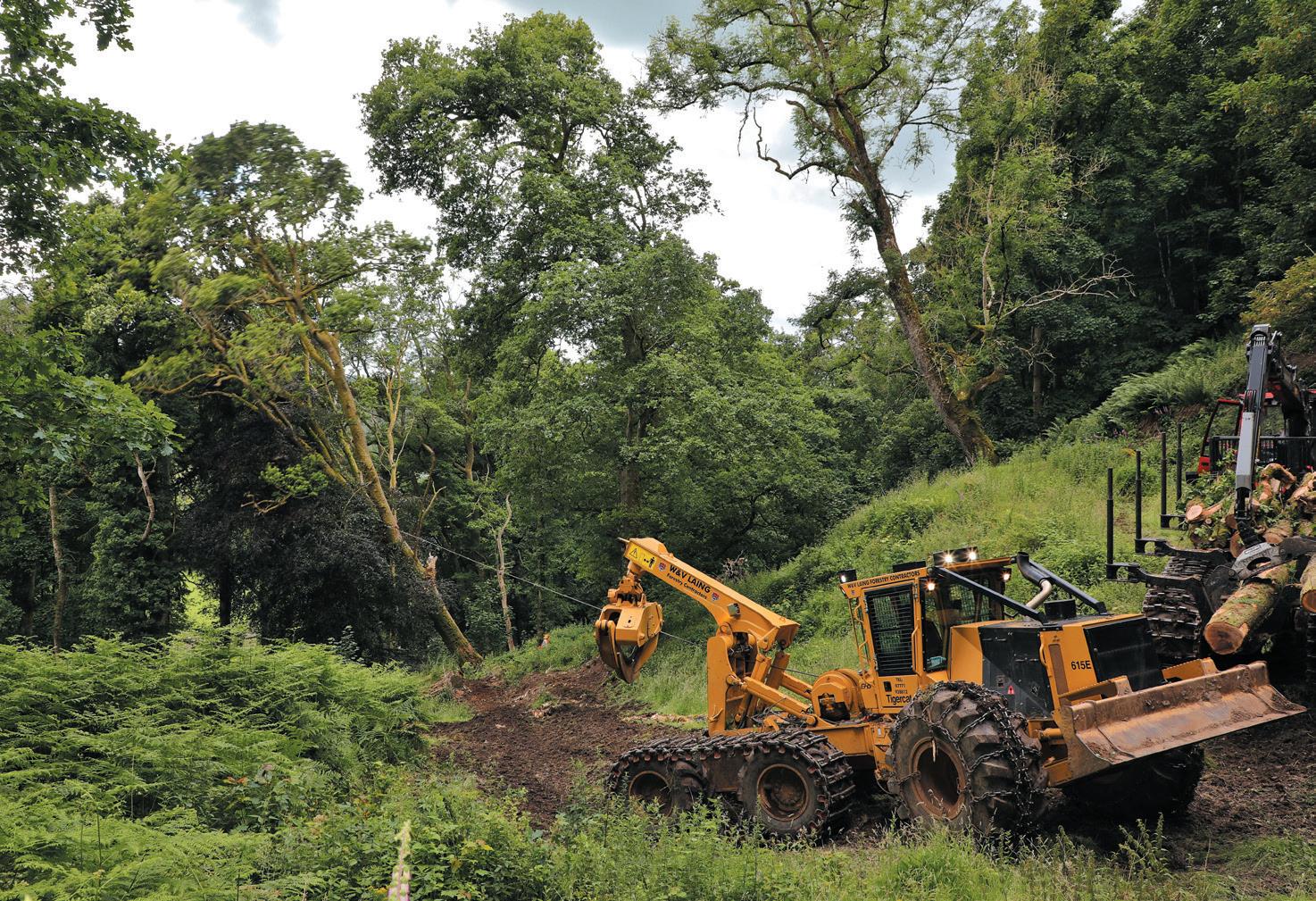
PUNCHING ABOVE ITS WEIGHT
Willie explained that the 2015 Tigercat 615E is one of the smallest machines in Tigercat’s range of skidders. However, he considers it ideal for the UK market for extracting hardwood. He said the traction, manoeuvrability and shear lifting power, with the dual-cylinder rear grapples, is exceptional. It’s capable of ‘dead-lifting’ a 10-tonne tree clean off the ground and has pulled a felled tree in excess of 20 tonnes out of the felled area with ease.
Left inset: Large capacity dual-cylinder grapples and 20t pull winch a great combo. Far left: Exceptional traction, manoeuvrability and lifting power with the dual-cylinder grapples.
Below: Highly skilled directional felling operation with the Tigercat winch; the 19mm thick rope can reach to 65m.
Willie feels the six-wheeled 615E provides the operators with a great deal of confidence on very steep ground, and provided you are operating it sensibly there will be no hair-raising moments with its performance, due to the even weight distribution (front and rear) and the long chassis and rear bogie design.
Willie commented, “I like the build quality of the Tigercat 615E as its been very reliable, and whilst it’s not highly used due to limited hardwood timber felling operations these days, it will probably last me until it’s time to hang up my chainsaw and retire. Tigercat builds bigger skidders than our machine, however we find this 20-tonne 615E is the right size of skidder for the UK and we are pleased with our decision to opt for a six-wheel drive model, as it has proven time and again to be the right choice in terms of manoeuvrability, balance and traction on various applications with steep ground conditions.”
Willie is delighted with his 615E, however he would like to see a slightly bigger LCD machine performance display and more rotation of the operators seat as you switch from front to rear driving position. This will soon be addressed as production of the 615E ended last year and the current replacement model – the smallest six-wheel skidder in the Tigercat range – is now the 625E, which is soon to be replaced again with the much upgraded 625H series of machines. Tigercat says its new range of THE 615E HAS H-series skidders, PULLED A FELLED including the TREE IN EXCESS latest 625H will have improved ease of maintenance, OF 20 TONNES OUT OF THE FELLED AREA as well as a 30% WITH EASE larger cab complete with seat that rotates more than 180 degrees, so operators can enter the right-hand door and spin around to fully face the rear of the machine. The 615E has been serviced from new by Tigercat dealer Treetop Forestry Ltd, which Willie cannot praise enough for its support; the company proactively brings along any new Tigercat factory upgrades or replacement parts when servicing the 615E, such as a strengthened new belly plate that protects the engine
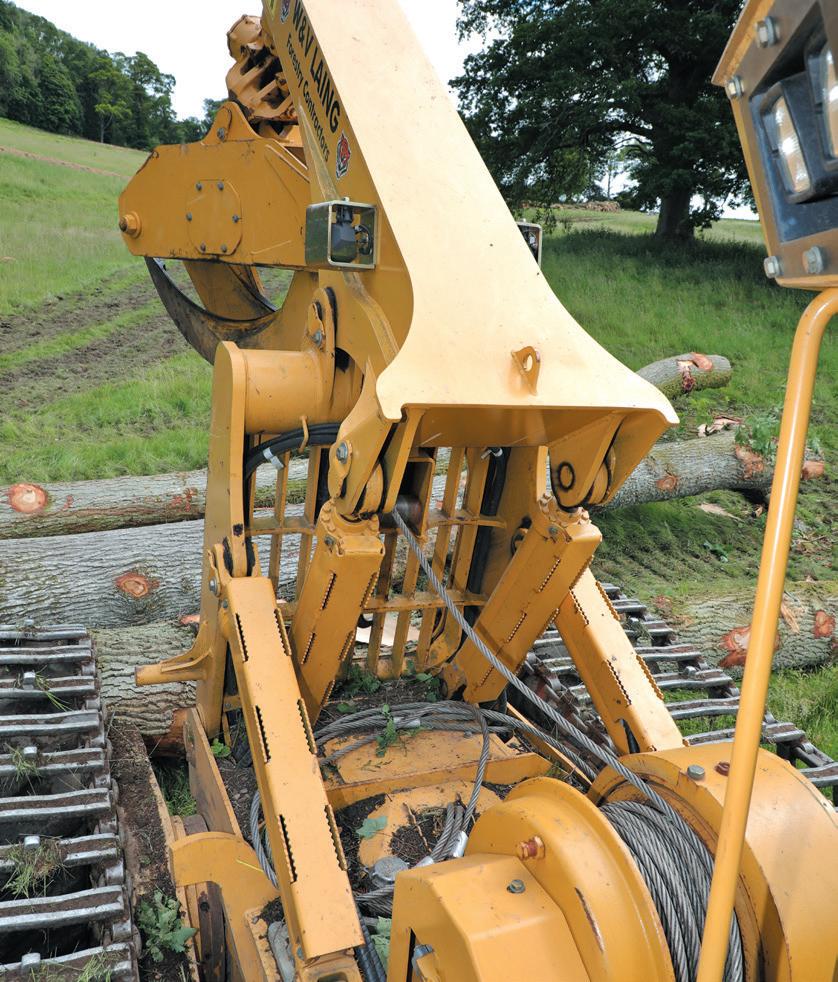
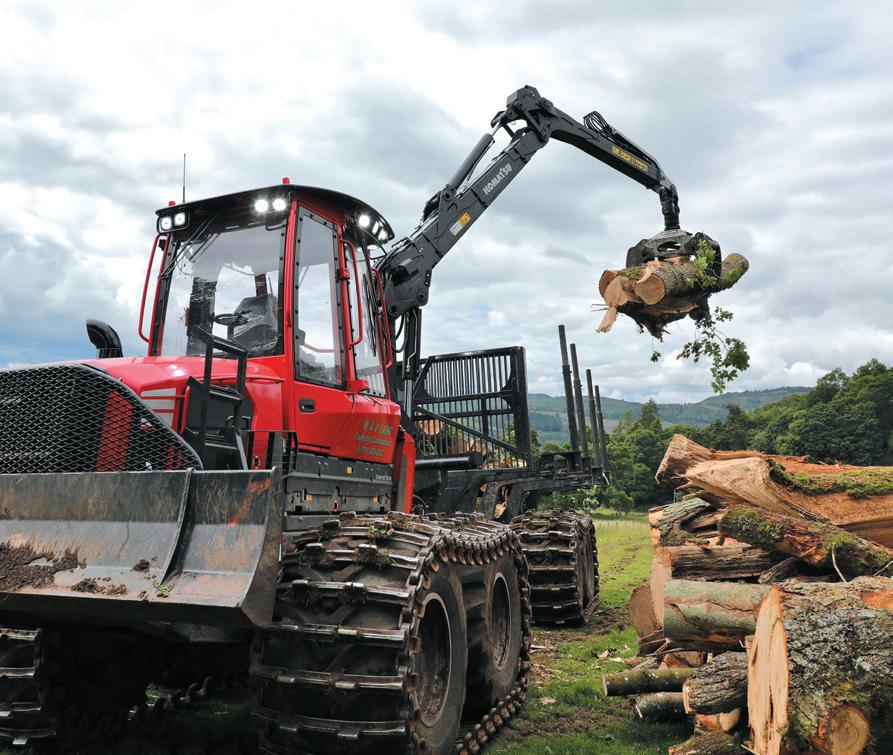
Above: Once all the timber has been felled and stockpiled, the client marks up the high-value timber. Right: Sections are marked off for cutting and then loaded on to the Komatsu, which makes it look easy.
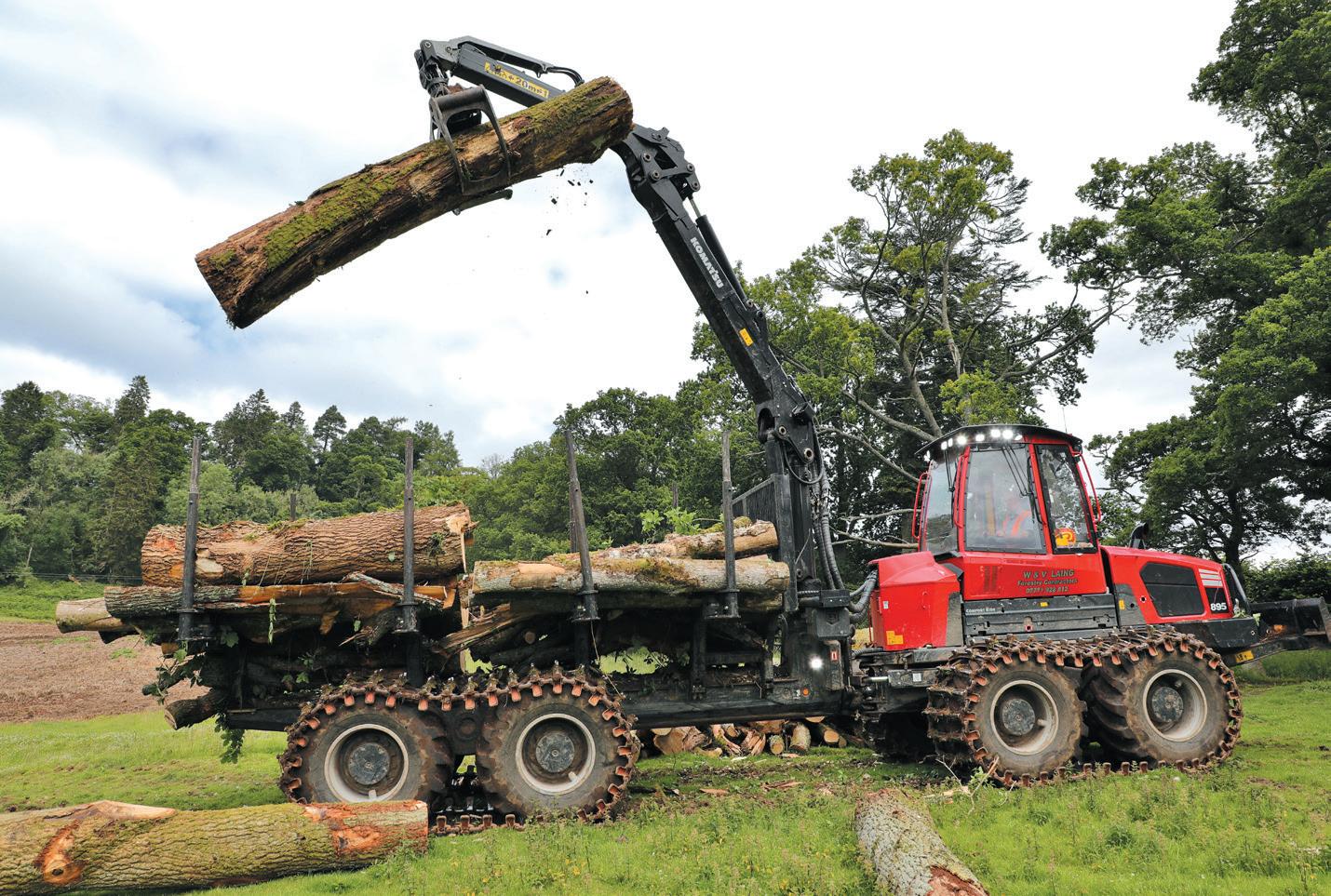
The 615E has pulled a tree in excess of 20 tonnes with ease.
LIKE ALL OTHER TIGERCATS, THE 615E IS sump from damage, which was fitted free of charge. Tigercat reckons the 615E is a quick, DESIGNED TO compact, agile, and BE INCREDIBLY versatile model for STRONG selective felling and clearfell applications. The machine employs a powerful and efficient, 220hp Tigercat FPT engine with automatic variable engine speed for high fuel efficiency and SCR and AdBlue emission control technology for Tier 4F emission standards.
The diesel engine is matched to the company’s EHS ‘efficient high speed’ hydrostatic drivetrain to offer an efficient driveline, with electronic control system for high speed and powerful tractive effort in forward or reverse with minimal wheelspin in adverse terrain. EHS is capable of providing the tractive effort of the deepest gear ratio offered in Tigercat’s standard transfer case, as well as the top speed of the shallowest gear ratio offered in the standard transfer case. This is said to be accomplished with sophisticated computer logic and the ability to take one of the drive motors offline when high tractive effort is not required. In this case, all pump flow is directed to one hydraulic motor, increasing both travel speed and motor efficiency.
When operating conditions demand high tractive effort, both hydrostatic motors work with independent front and rear differential locks. When tractive effort requirements are reduced – for instance, when traveling empty or loaded on flat terrain – all of the pump flow is directed to one motor for higher travel speeds up to 14mph.
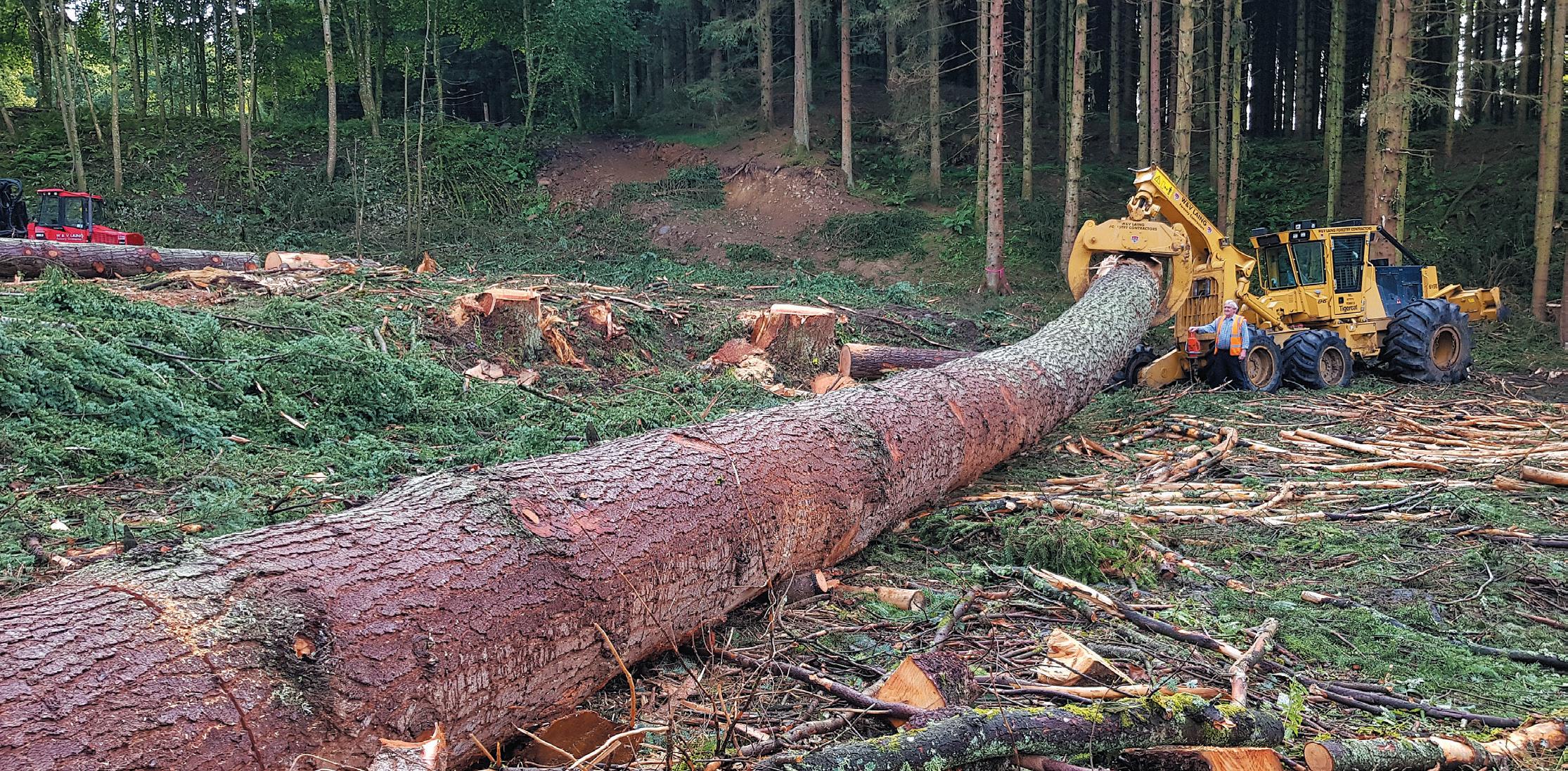
TRACTION SATISFACTION
Like all other Tigercat’s, the 615E is designed to be incredibly strong – its long-life centre section is constructed with thick steel plate, oversized pins and tapered roller bearings. A two-position turnaround seat and joystick steering help to provide rear-facing drive controls. Grapple and arch functions are controlled by just one joystick. Willie is impressed with the powerful hydrostatic drivetrain as he just uses the throttle pedal to control the speed and bring the machine to a halt without using the foot brake, making the machine easy to operate, even in challenging conditions.
FIT FOR PURPOSE
Laing’s Tigercat 615E was on display at the 2019 Forestry Expo Scotland on a modern clearfell operation where the timber can be either be shipped to the sawmill full length and or stockpiled for processing later on. Laings has even temporarily converted one of its Komatsu forwarders into a makeshift haulage vehicle on a highland hydro project, where a massive water turbine feed pipe control valve needed to be hauled up a steep hillside in order to replace the unit under planned maintenance!
In de-bogging work, the company’s 20-tonne pull winch can be combine with pullies and snatch blocks and additional machines to provide suitable anchorage to increase the capability up to 120 tonnes, although a 40- to 60-tonne pull is normally deployed in this situation. And the 19mm thick rope can reach to 65m or by fitting thinner 16mm rope to the winch drum it can reach 100m.

Komatsu forwarder now a makeshift haulage vehicle. Above: Laings Tigercat 615E on display at the 2019 Forestry Expo Scotland.
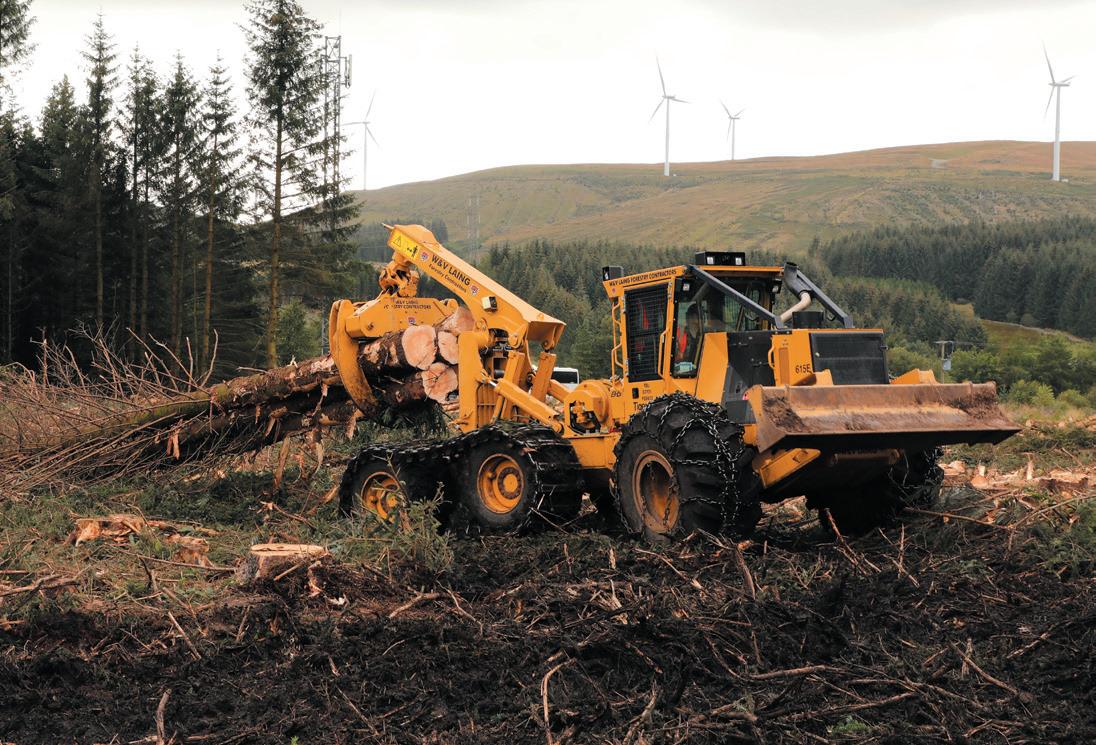