
7 minute read
TRACTION WINCH
Traction assist winches have become a popular choice for steep slope logging and offer benefits from operational, environmental and safety enhancing perspectives, as Eoghan Daly reports A HELPING HAND
Advertisement
IMAGES EOGHAN DALY
An increase in clearfells located on steep terrain meant Brophy Timber Services Ltd was on the look-out for equipment that allowed safe harvesting and extraction. Recognising the appeal of harvesters and forwarders used in combination with a traction assist winch, a Timbermax T10 mounted on the boom of a Doosan DX300LC-3 was accepted on trial from UK and Irish agent RJ Fukes Forestry Services.
The machine’s arrival coincided with commencement of a clearfell comprising 3,300 cubic metres with an average tree size of 0.31 cubic metres on a steep hillside at ‘The Cut’ deep in the heart of the Slieve Bloom Mountains in scenic County Laois in the Irish midlands. With the necessary induction and training completed by RJ Fukes in advance, coupled with installation of the necessary kits within the machines to work with the winch, harvesting was ready to commence.
Steepness of the terrain coupled with the requirement to extract all material uphill meant conventional working approaches were impractical. This was exacerbated by a deep layer of peat occupied by a block of fire damaged Lodgepole Pine across which marked part of the extraction route. Combining these factors meant the site had everything necessary for the Timbermax T10 to prove itself.
ON A HIGH
Looking beyond the initial lodgepole pine, a quality block of Sitka spruce was encountered and yielded a range of quality log lengths including sawlog, various pallet
Overview of the clearfell site at The Cut in County Laois. Ponsse Wisent forwarder at the summit of the slope.

Host excavator set up on road verge due to deep peat conditions. Antenna and receiver on boom talks to tethered machine.
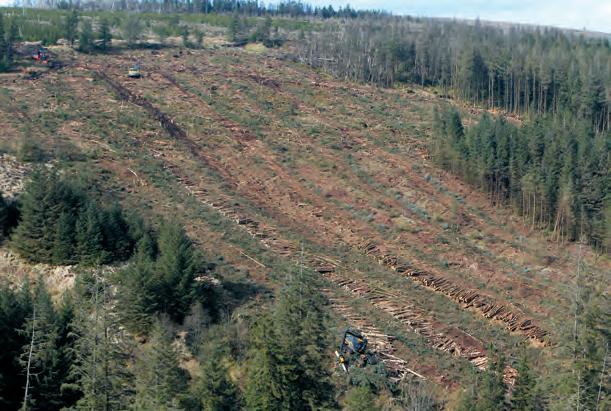
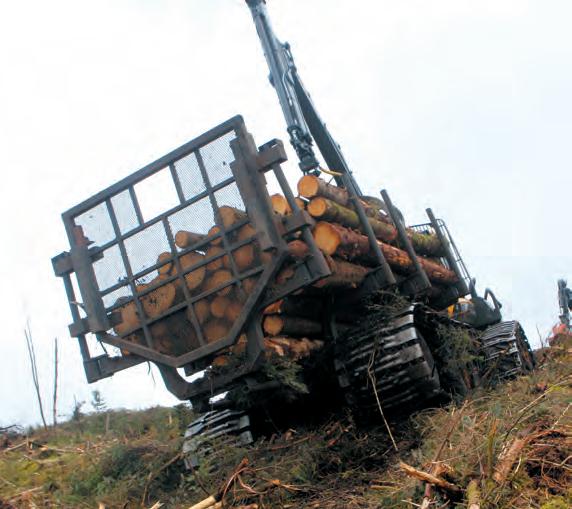
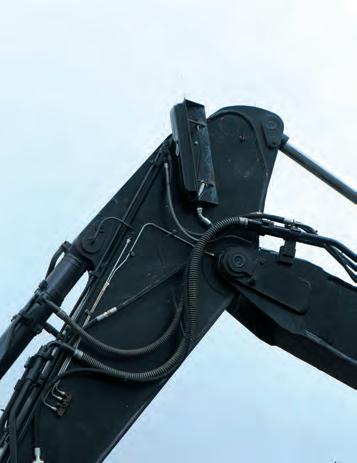
lengths as well as pulp wood while chip wood was derived from lodgepole pine area of the site. Machines assigned to site included a Ponsse Scorpion eight-wheeled harvester fitted with H63 harvesting head and 11m reach crane, while extraction was taken care of by Ponsse Wisent and Buffalo forwarders.
Following considerable advanced planning to ensure all machines were fully utilised, the T10 performed admirably, as Damien Brophy explained. “Using the Timbermax traction assist winch on this site and subsequent sites with similar challenges has been very successful for us. It makes the operation safer but also takes much of the pressure off the machines doing the work and reduces ground damage. The system requires minimal set up, meaning the machines get to work with no delays involved.”
As a consequence of the deep peat at the summit of the slope close to the forest road, and the scale of the base unit employed by this Timbermax winch, set up of the machine was restricted to the forest road verge. Providing a firm base, the boom and its mounted Timbermax winch were lowered into the adjoining embankment. When
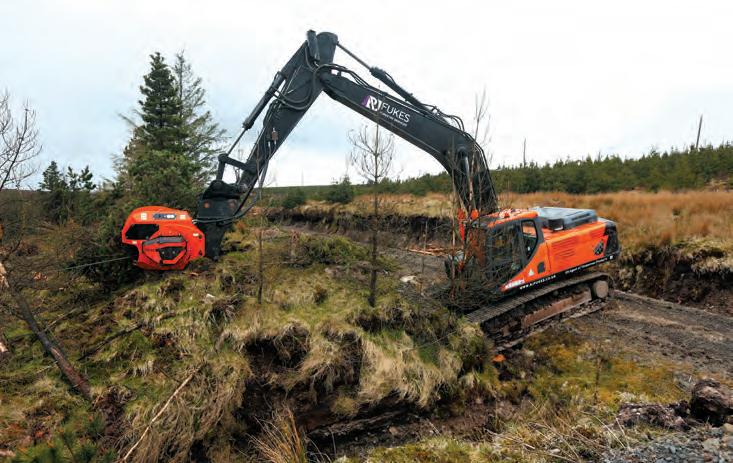
Headboard at rear stops logs sliding off down the slope.
commissioned for mounting on the boom end, the winch has a specialised base formation.
Should the machine be setting up off-road on firmer ground conditions, the toothed spade base design provides a climbing aid and opens up the possibility of spragging the tracks with its stalwart construction, ensuring it can withstand the challenges of such operations. The design of the base eases the process of firmly anchoring the machine. Further aspects of set up include the insertion of a ground probe, which is connected to the winch and informs the tethered machine operator of concerning ground instability.
SEND AND RECEIVE
However, this is just the start of the in-built safety features. Signals from the control unit inside the cab of the tethered machine are relayed to the winch via a roof antenna in real time. Connected to the tethered machine’s

transmission, the control system recognises the need to reel out or haul back with signals picked up by the receiver, which is mounted on the side of the dipper arm of the winch’s host excavator. The winch’s standard weight of 3,000kg increases to approximately 4,500kg through the which incorporates a pre-tension spooling arm and motor assembly that spools the rope onto the drum in a controlled way. “Looking at every part of the Timbermax winch’s design, it shows real experience,” said Damien. “The whole unit is very well constructed and, with the dedicated control systems it runs with, is very user friendly.”
incorporation of the ground anchoring base, and the unit has a working range of 450 to 480m.
Mindful of the need to eliminate the possibility of the winch line being reeled onto the drum in an improper fashion, Timbermax developed an ingenious system
FIGHTING GRAVITY
The control system comprises a large in-cab touchscreen monitor which is easily transferred between machines set up to work with the Timbermax system. There’s a remote control complete with neck strap, too. Before starting a working cycle, the system needs telling which direction the harvester or forwarder is facing. This input serves to inform the Timbermax system if the machine will be driving forward or reversing down the slope.
The next parameter to be set is the force supplied to the line by the winch, which can be adjusted by rotating the accompanying dial. With these settings completed, the machine travels down the slope in a normal fashion and, upon coming to a stop, the control system performs a test to establish if the machine is capable of maintaining its position without support from the winch as an added safety feature.
Developing a high level of competence in its use over the first month of operation and subsequently moving to an even more challenging site in County Leitrim, Brophy Timber Services remains extremely impressed by the Timbermax T10. Working in the Slieve Bloom Mountains, the Timbermax unit proved extremely effective while only applying half of the possible
Winch attached to rear of Scorpion as it moves down slope.
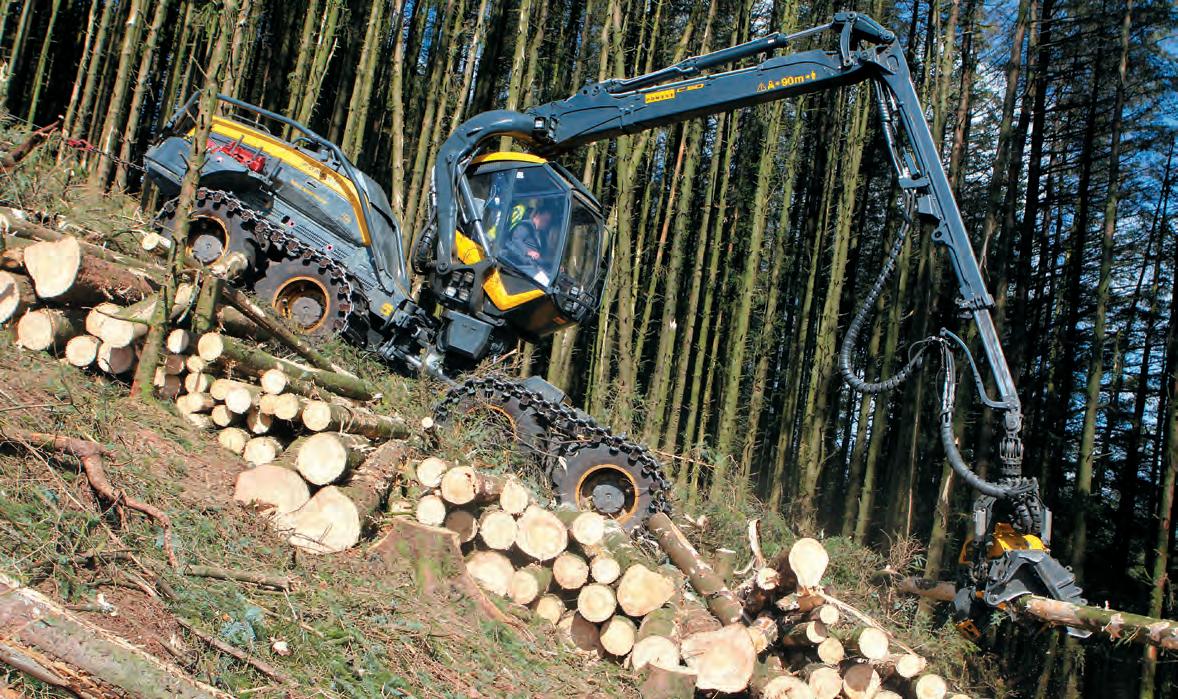

winch line haul back pressure in most cases, which demonstrates the difference it can make even when working at a fraction of its full capacity.
While working with the Ponsse Scorpion harvester, the maximum working width could be utilised with great confidence while the harvester surefootedly reversed back up the slope on completion of each harvesting cycle without damaging the brash mat, as the aggression of the tracks did not need to impact on the material below.
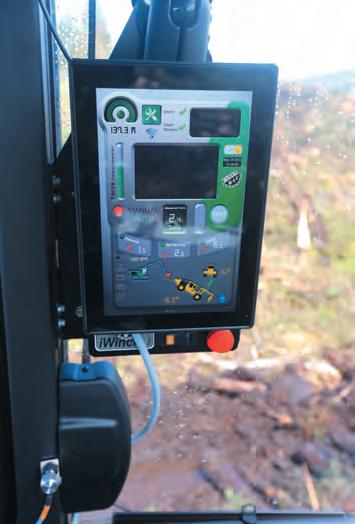
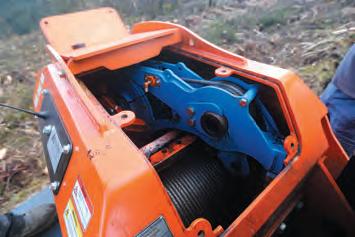
However, it was when working with the forwarders that the T10’s real value emerged. Facing a demanding uphill extraction cycle with the challenge worsened by the peat and far from ideal fire damaged lodgepole pine brash mat at the summit, both the Wisent and Buffalo forwarders carried out their work in unflustered fashion. With rear headboards fitted to address the problem of logs sliding off due to the severity of the slope, the machines confidently advanced up the hillside.
Successful timber extraction followed great team work.
This large in-cab screen is linked to the Timbermax winch.
HANDLING WITH CARE
A number of working approaches were adopted to suit the demands of each area. For example, in sections presenting a less severe slope for much of the haul, a single machine often focused on extracting timber to less severe ground within the harvested block for onward extraction by the second forwarder to the roadside. While this approach did present a degree of double handling, it eliminated the need to attach and detach the winch line each
Remote control useful when relocating host.
Special cable spooling system inside drum.
time between hauls.
“The Timbermax winch has performed very well for us,” Damien confirmed. “Long term, mounting one on the rear of an excavator in the 21-tonne class would be a more ideal solution, allowing it to be set up off-road and making the whole system more versatile. RJ Fukes Forestry Services has already proven this can work as the company has experience in adapting the system to a wide range of situations and base machine types.”
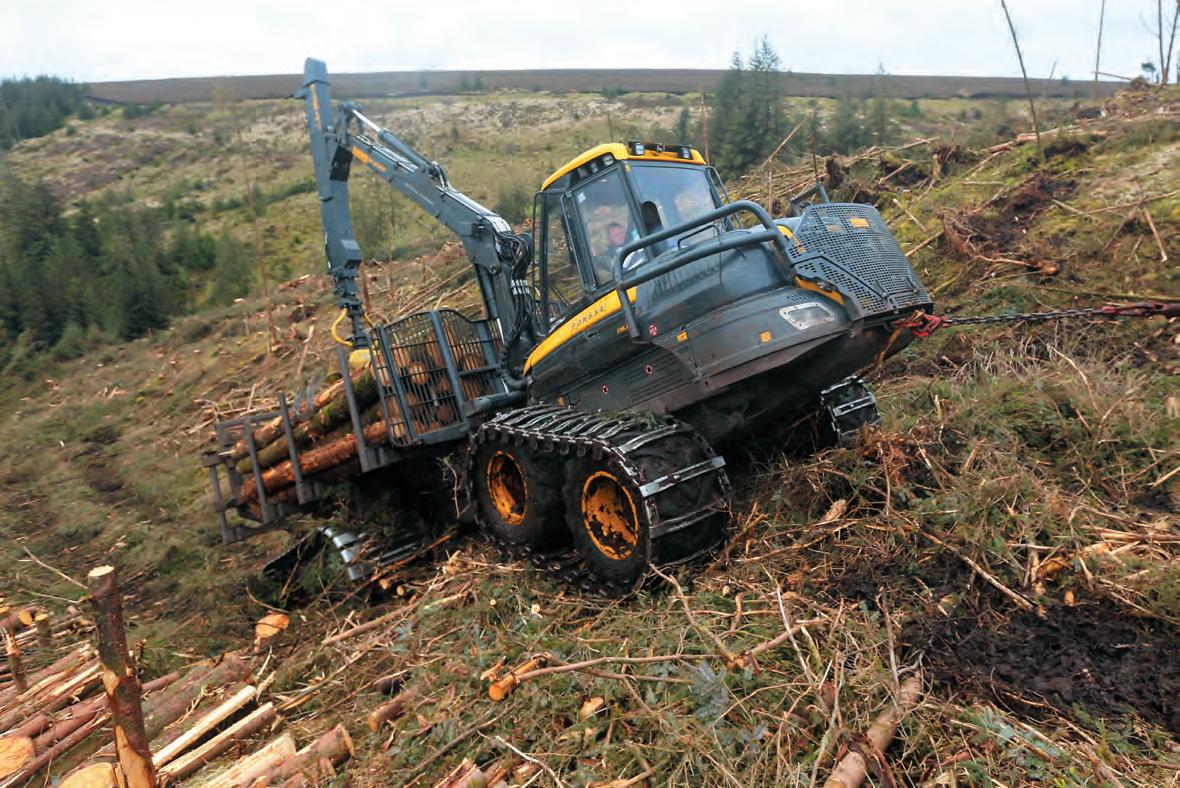