
7 minute read
RUNNING REPORT VOLVO ECR145EL

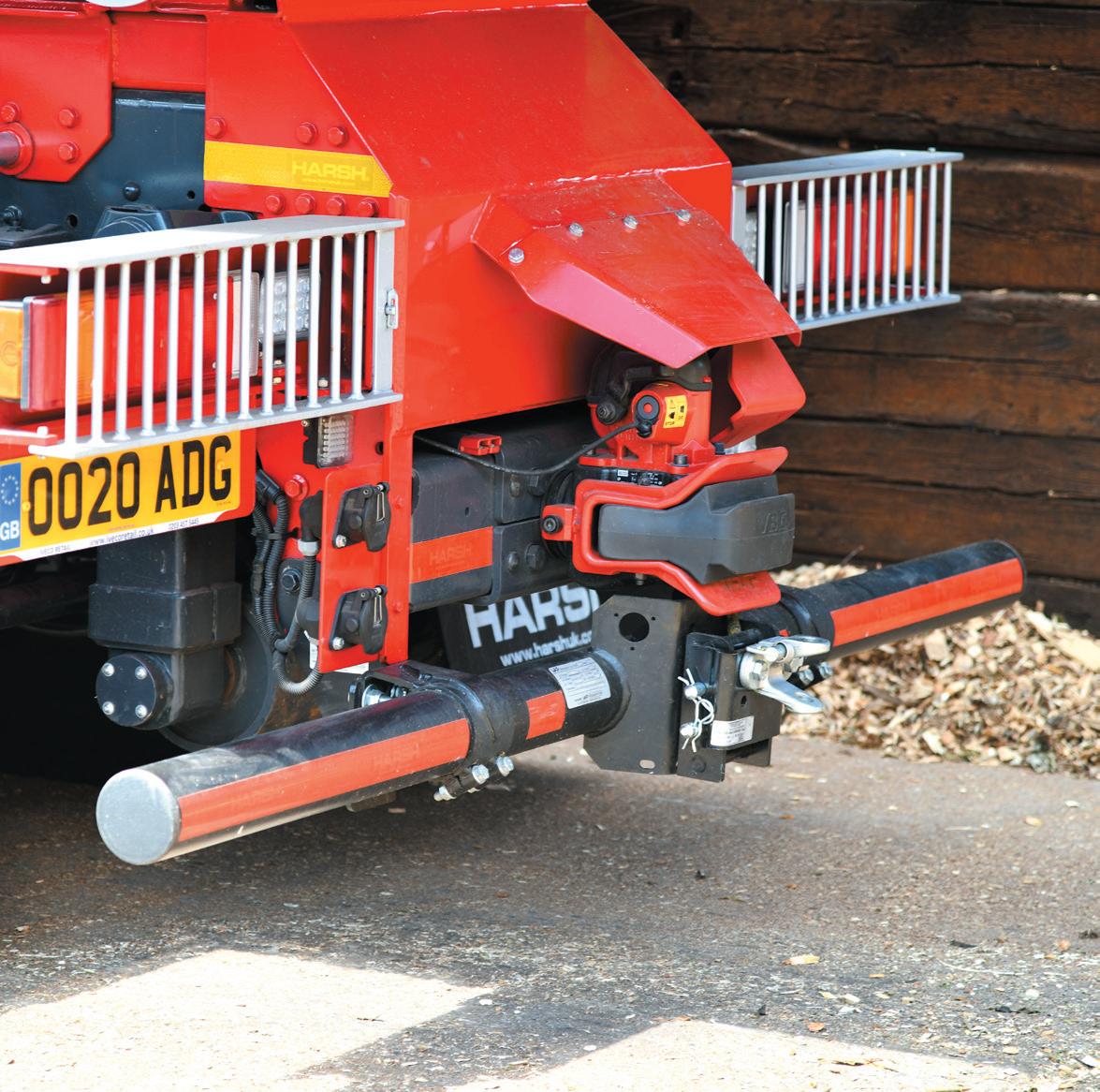
Advertisement
Left: A short tailswing and dozer blade on this excavator.
Right: James Greenwood (right) with his father Alan.
Below left: A nice, wide entry to the ROPS certified cabin.
37-year old now spends much of his time behind the wheel of his company’s vehicles. “We’ve never liked to put all our eggs into one basket, and it means that, no matter what is happening, we’re able to adapt. Something might be affecting the tree work, but we can concentrate on the demolition side, or vice versa. Demolishing a house, demolishing a tree – they’re not so different. The principles and the logistics are similar. You just have to adapt.”
THINKING OUTSIDE THE BOX
Whilst private work slowed down during the grip of the crisis, this has started creeping back in to bolster the large amount of work James and his team undertakes for a handful of local developers. “We regularly undertake the initial tree clearance and are often asked to step in and look at the demolition of existing structures on site, giving the builder a clean and clear slate to start from,” James explained.
Being able to adapt to economic climates has prompted James to look at the way his business operates, and further mechanisation has been the key to recent success. “We have had a Hitachi ZX33U mini-excavator feeding a Bandit chipper for a while now and that has made life a lot easier on site. We took the plunge and purchased a Manitou telehandler to load bulkers and to pull a trailer to and from site with plant and material but to be honest, this didn’t work out for various reasons,” said James.
Wanting to develop the business, the sale of the Manitou led James to look at bigger and better ways to develop the company and subsequently purchase of a new Volvo ECR145EL excavator equipped with a Dragonbite DB015 tree shear. This addition to the fleet has seriously improved productivity and safety on their larger contracts with the sheer able to handle vast quantities of timber compared to previous methods. The choice of the Volvo was relatively straightforward for James as the brand represents quality and reliability, something his company strives to achieve on a daily basis.
Powered by a four-cylinder diesel delivering 121hp, the key to the Volvo’s success is the delivery of constant pressure and flow to the attachment, which is undertaken on this machine by a pair of 124L/min displacement axial pumps. A sturdy dozer blade has been chosen to
Iveco Trakker set up for pulling a 26t capacity trailer.

further increase flexibility, and the 600mm track pads have been fitted with a full set of bolt-on rubber pads to avoid damaging any delicate surfaces. A major plus point for James is the ability to quickly adjust flows and pressures for different attachments just using the touchscreen in the cab.
Looking around the yard and at the impressive a state-of-the-art Iveco Trakker 4x4 hook lift truck the company operates, image is clearly important to James’ company. Immaculately turned out in the red livery that adorns other company vehicles, the Iveco pulls a similarly impressive 26-tonne capacity Andover drawbar trailer used for plant, machinery and round timber transport.
While the new Volvo, in its original yellow paint scheme, would be OK for many, James’s desire to have a uniform brand image meant that any yellow panels were wrapped to match the Iveco’s Maranello Red paint. “Iveco sponsors the Ferrari F1

Above: This Volvo ECR145EL sports rubber track pads. Below: Dragonbite DB015 shear with 745mm jaw opening width.

team and the fire engine spec chassis cab was supplied in that colour,” he explained. “As it looks very impressive, we decided to keep it as our company colour scheme.”
GO WITH THE FLOW
and Iveco combination has added massively to the capabilities of the company in one fell swoop. “We’re now able to look at larger operations and offer our existing and future clients a one-stop-shop service for opening up potential development sites,” James The Volvo has been equipped with a explained. “We have also increased our Dragonbite DB015 shear, a 1.2-tonne productivity, and this has allowed us to mid-range model. The fully rotational streamline what we do.” shear’s impressive capabilities have impressed the operators since its arrival. “THE KEY TO THE VOLVO’S As the cut material produced for biomass is just 3m in length, the Dragonbite is SUCCESS IS THE DELIVERY more than capable of handling the material it faces on a daily basis. OF CONSTANT PRESSURE
With a maximum jaw opening width of AND FLOW TO THE 745mm and a cutting force of over 90 tonnes in the throat, the Dragonbite shear ATTACHMENT” has boosted Greenwood’s production rate. “We have upped production to the point The sides of the large bins carried by the where we can now deliver up to six bulkers of Iveco are emblazoned with ‘Biomasss biomass products per week,” James Energy Suppliers’. “People often don’t like commented. The increase in production has to cut down trees, but if there’s no also put a strain on the loading capabilities alternative, knowing that something good within the yard and the new Volvo has been has come of it can cushion the blow. equipped with a 1.6 cubic metre rehandling Because of how we’ve set things up, we’re bucket in a bid to dispatch the bulk walking recycling our waste and feeding it back into floor trailers quickly. the power grid. It’s going to good use, it’s
Working in a face shovel configuration, not being wasted, and it is the future,” James James can get rid of a full artic load, around enthused. the 27-tonne mark, in under 30 minutes. It’s a future that’s looking bright for James Another addition to the range of bespoke and his team. The coronavirus crisis might attachments is a DHG1102 timber grab from have stopped some of his competitors in Dehaco supplied through local dealer LDH. their tracks, but at Greenwood’s not even
The addition of the Volvo, Dragonbite a pandemic can bring progress to a halt.
Hydraulic flows for attachments can be adjusted on a touchscreen in the cabin.







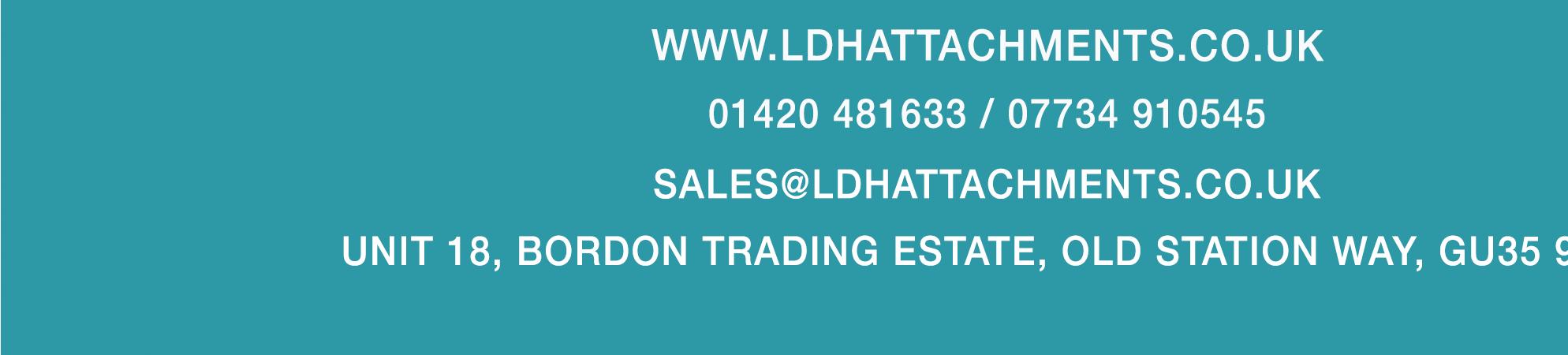
LEITRIM’S WOOD ENERGY PIONEERS Gerry McMorrow with his son Brian.

Wood energy is one area with massive unexplored potential and offers many opportunities for timber harvesting and haulage contractors. Eoghan Daly describes the latest venture of one progressive Leitrim-based operation
PTH 1200/1000 at work chipping logs for woodchip production.
Despite strong roots in the timber
industry’s traditional haulage and harvesting sectors, diversification is hugely important to McMorrow Haulage Ltd, based in County Leitrim, Ireland. The company’s most recent venture is its entry into the wood energy sector, with the aim of establishing a reputable wood energy hub in their area.
Diversifying into a new field served by a minority always presents risk, but with the potential for great reward, as company managing director Gerry McMorrow explained. “We may have a lot of experience of timber harvesting and haulage, but this is a new challenge and one we believe will be worth the effort since there is so much unexplored potential for wood energy in Ireland. We have a lot of young plantations coming up to thinning, which will yield much pulp grade material that can be directed towards chipping to produce a renewable fuel source. “We started looking at chipper options well in advance of any decision,” Gerry continued. “Many large chippers already in use in Ireland were from Jenz, and at first we thought this was the best route to take. However, as we went to the market with an open mind, we were inclined to look at all the options and found that Pezzolato was offering the best package.”
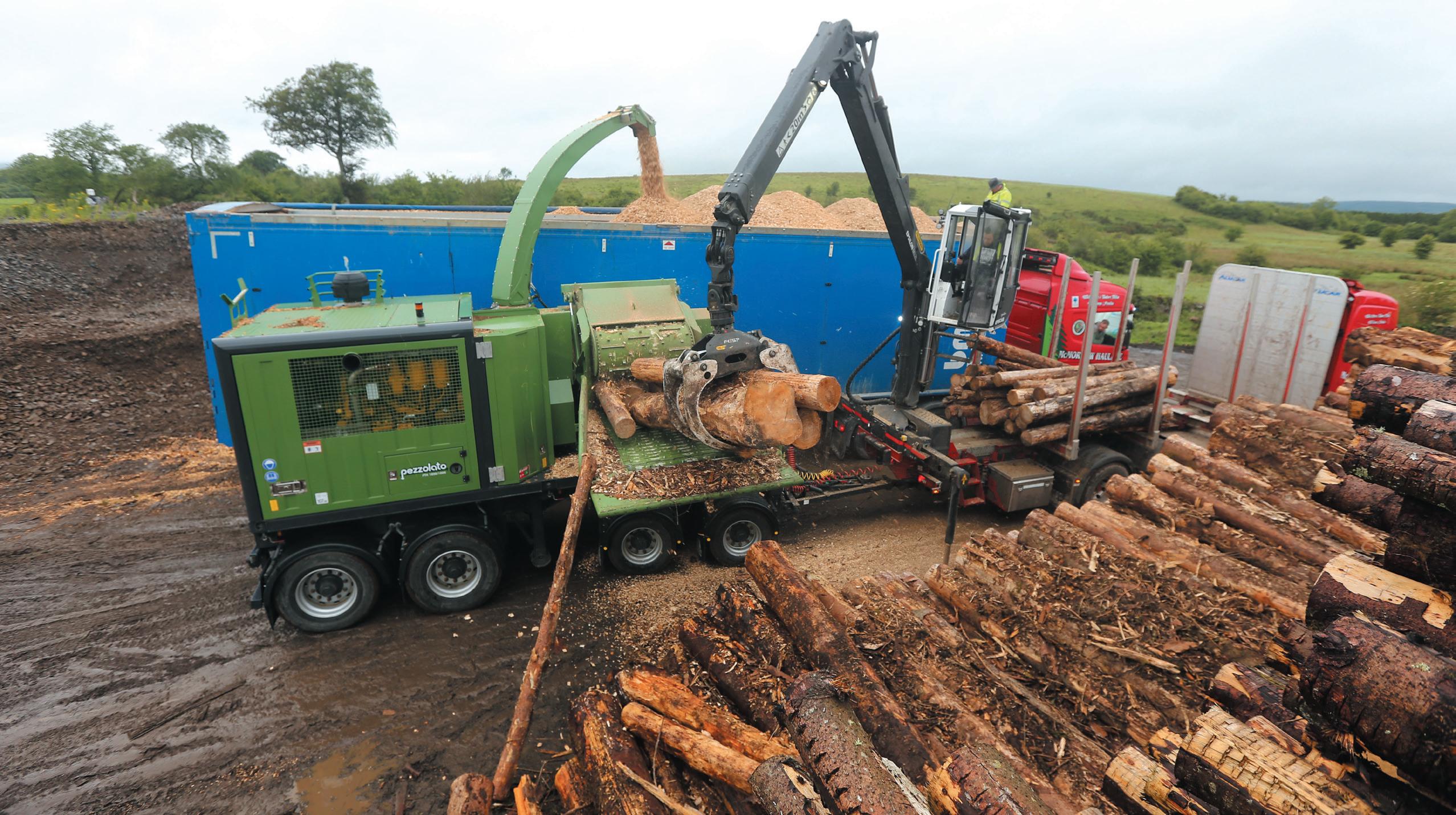
PERSONAL SERVICE
The manufacturer’s willingness to build a machine around the individual requirements of McMorrow’s application was very much central to the decision. With vast experience of chipper design and manufacturing, Pezzolato has served the sector since 1976 and operates from two factories in Italy. For McMorrow, the PTH 1200/1000 drum chipper was considered the best long-term option, as it offered high output to cope with current and future demand as the venture becomes more established, plus additional working flexibility. “It was important to have a machine that would fit in with our existing