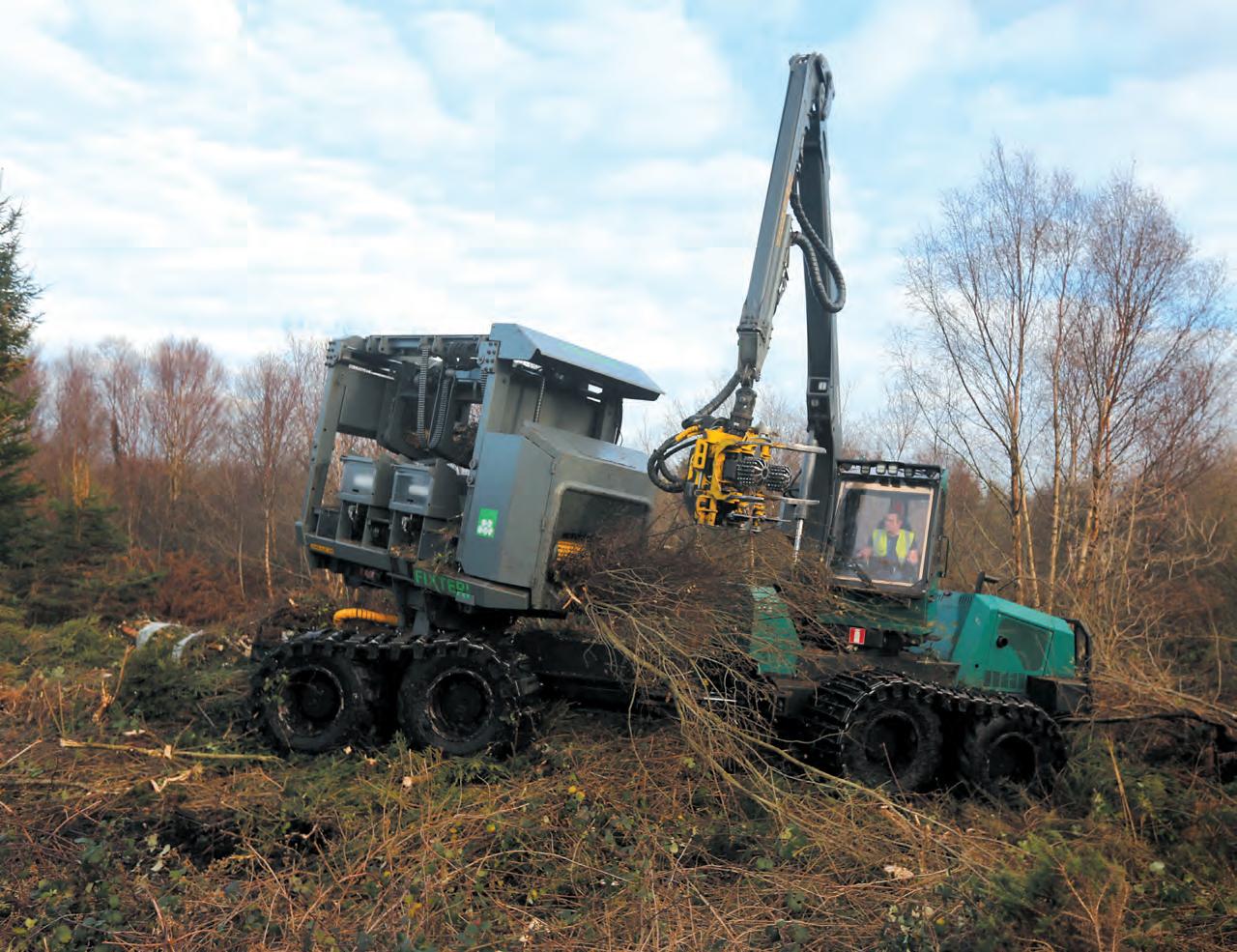
9 minute read
TIMBER HARVESTING
BUNDLER’S IRISH EXPERIENCE
Eoghan Daly reports on the use of a Fixteri bundler as a management tool to help turn infested plantations back into productive forests
Advertisement
IMAGES EOGHAN DALY
When it comes to developing new and innovative methods of harvesting, our Scandinavian friends are among the best in the business. By developing the cut-to-length harvesting and extraction system, they made a massive contribution to the evolution of mechanised harvesting. This spirit of ingenuity lives on, as seen by their recent solutions for timber harvesting.
When Coillte, the Irish forestry board, sought a machine for a specialised application, Scandinavian manufacturers were an obvious choice. A number of second rotation sites across the Irish midlands were affected by naturally regenerating invasive species, including birch, which thrived on peat-based forest properties. The spruce’s growth was being heavily compromised, as their unwelcome neighbours literally closed in the canopy, leaving little chance of a productive stand of conifer species to develop.
With these sites subsequently written off, Coillte took the decision to revive the areas, starting with the removal of the competing species, for use as biomass for energy production – a first for the country of Ireland.
Coillte required a machine capable of travelling through the stand and removing the invasive species while retaining the spruce material. A range of options were considered and one of the most impressive was a self-contained machine with felling capability and incorporating a Fixteri
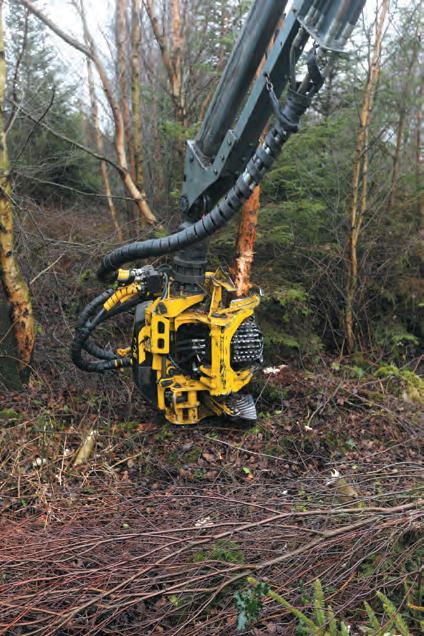
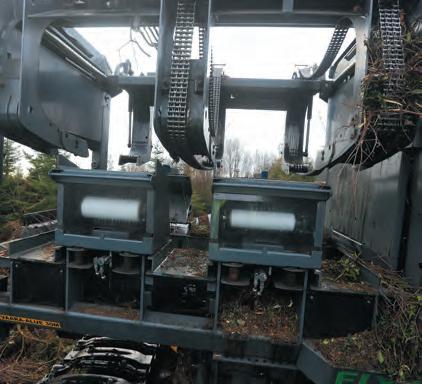
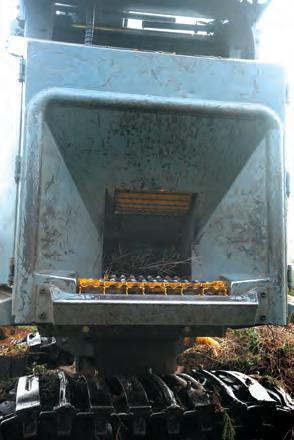
Right: Moipu head felling and bunching birch in a spruce stand.
Below: Bunching the stems improved productivity.
Below right: The versatile Moipu head in the open position. Above: Forming chain system compacts the bundle.
Right: Infeed table provides some support for the material.
Bottom left: Even Cuddy operated the Logman/Fixteri in Irish trials.
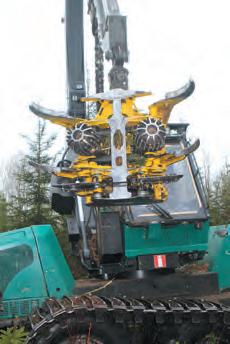
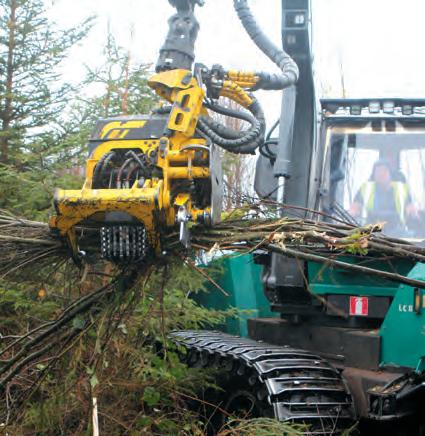
bundler, which left the material in a presentable state for subsequent extraction by forwarder to the roadside.
Recognising the unit’s potential, Coillte personnel travelled to Fixteri in Finland for further evaluation before agreeing to a more detailed trial of the equipment back in Ireland. It was originally envisaged that a Finnish operator would run the unit, however the coronavirus pandemic saw off that idea, and the trial was put on hold until an Irish operator was trained up to operate the machine correctly.
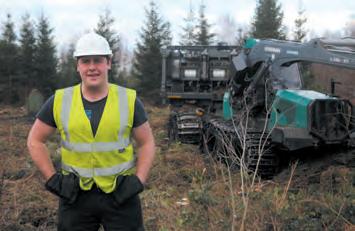
WORTH THE WAIT
Concentrating on sites across the Irish midlands close to Monasterevin, County Kildare, each presented dense and competing, naturally regenerating birch and other invasive species. The machine had to travel on the existing brash from the harvesting of the first rotation, which had been accumulated in windrows in preparation for planting of the second rotation crop.
The unit reached into the stand at each side and felled invasive species using its accumulating harvesting head, and fed the material to the Fixteri unit mounted at the rear. Bundles were discharged from the machine and left on the ground for extraction by a forwarder, before being allowed to air dry on the roadside and then transported to the power plant for chipping and ultimately power generation.
Taking a closer look at the Fixteri bundler, even though the machine can be mounted on a wide range of base unit types, the choice of a Logman 811FC is clearly the ultimate solution for this application. “The Logman base machine was originally chosen due to the need for a 360-degree rotating cabin and a crane in the same package,” explained Fixteri Oy partner, Juha Tapanen. “This combination is essential in dense forests here in Finland when you need to cause as little damage to the remaining trees as possible. It’s like having an agile harvester pulling a bundling trailer. All Finnish customers are operating the bundler in same kind of environment and all of them have chosen the same platform.
However, other type of base carrier solutions like tractor and trailer or excavator plus trailer are also possible as long as the hydraulic and electrical power are available,” he continued. “The customer’s needs and the operating environment are the key factors that determine what the right machine combination is in each case.”
Obviously, much of the operation’s success is determined by the effectiveness of the felling and accumulating head utilised in the set up. While a range of heads are available and a high percentage of the machines operating across Finland utilise Nisula accumulating harvesting heads, a Moipu 300 accumulating harvesting head was chosen for the Irish trials. Despite the head’s accumulating multi-stem capabilities, it also incorporates many features associated with a standard harvesting head including feed rollers and delimbing knives.
Deceptively compact in size, the Moipu 300 head has a broad operating capacity thanks to its 30cm cutting diameter. Interestingly, the felling action is conducted by a shear-type arrangement instead of a chainsaw configuration that would find handling multiple smaller stems at once difficult in this application. With a number of stems successfully cut and grouped, they are then fed into the Fixteri bundler that can accept material from either side thanks to its mounting on a rotating base. With the material placed on the intake table, contact is made with the intake rollers, which guide it into the first chamber of the machine to begin the bunching process. From here, the entire process is automated and is subject to manual override when necessary.
STEP BY STEP
As material is fed into the reception chamber and reaches the rear wall, a large panel with guillotine edge descends behind the infeed rollers to cut the material to length. The material is then raised to the next section of the unit located overhead, which serves to form and compact the bundle as more material continues to be raised from below. The compaction
Above: Cabin of the Logman includes the control unit for the Fixteri bundler. Right inset: Tamtron weighing system is controlled by the monitor on the right.
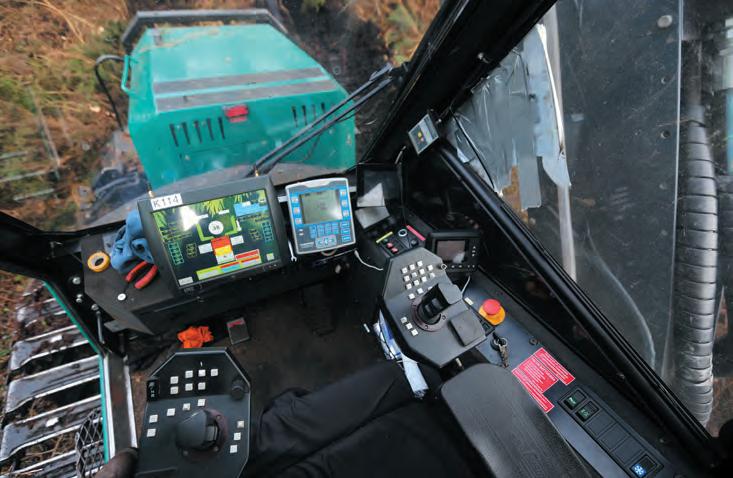
Below: Despite being a large machine, the Logman/Fixteri combination negotiated its way through the stand with ease.
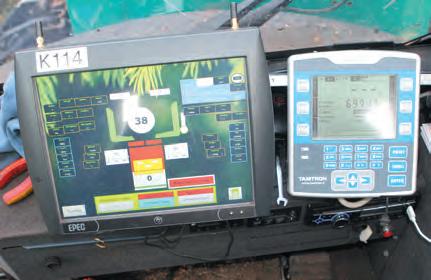
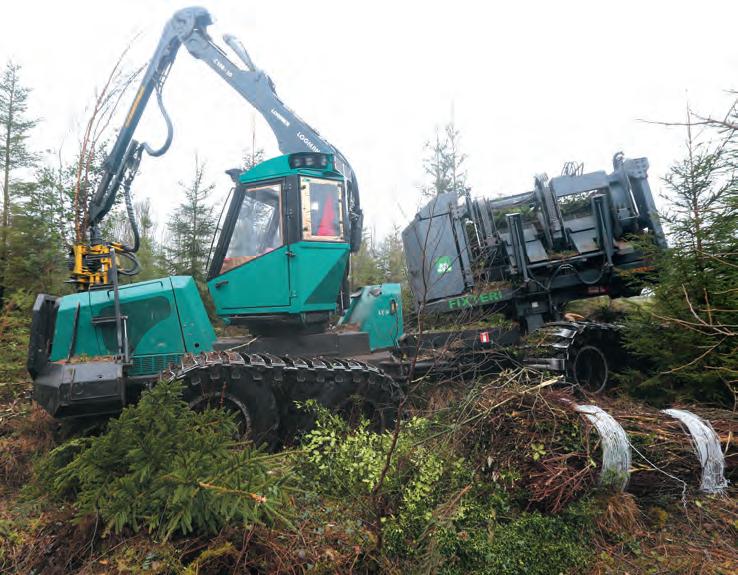
OPERATOR’S PERSPECTIVE
Despite the high level of automation involved in the bundler’s working processes, the Fixteri bundler still requires a skilled hand to operate effectively, not least due to its unique design. Irish operator Evan Cuddy told us about his experiences with the equipment. “The Fixteri machine is different to anything else I’d operated before, but once I got into using it then I could appreciate how it is so useful for this specialised kind of work. As the bundler is automated, it left me free to get on with felling and bunching the trees and keeping it fed. The Logman base unit is an ideal carrier with the crane and cab on the same slewing base, which meant it provided equal visibility and reach all around the machine, and made feeding very easy from either side,” he continued.
“Between the base machine and the bundler, it is a heavy machine, though. It weighs up to 30 tonnes with band tracks on all four bogies, so keeping attention on the brash mat under it was a must, especially as most of the sites worked were peat-based.”
BACKGROUND
The current generation Fixteri bundler is the result of almost two decades development. The original design brief was a machine that combines the management of young forests with material production suitable for power generation following chipping. All whilst attempting to set new standards for efficiency.
It goes without saying that achieving these goals wasn’t easy, as Juha Tapanen, partner in Fixteri Oy, confirmed. “Fixteri was established in 2003 around the need to get small wood out of the forest and to the power plant easier than before. The first six to seven years were spent building the machine, testing it and finding the proper technical innovations to make the idea to work.
“From 2010, the machine had its basic structure ready and the first customer started working with it,” Juha continued. “In 2012, the design was changed a lot and more ‘manufacturing-friendly’ solutions were adopted. Between 2012 and 2015, the final mechanical solutions were achieved and a few machines per year were manufactured with that design. Software and sensor solutions continued developing after that, however, so it is true to say we are continually finding new ways of making the equipment more user friendly and effective.”
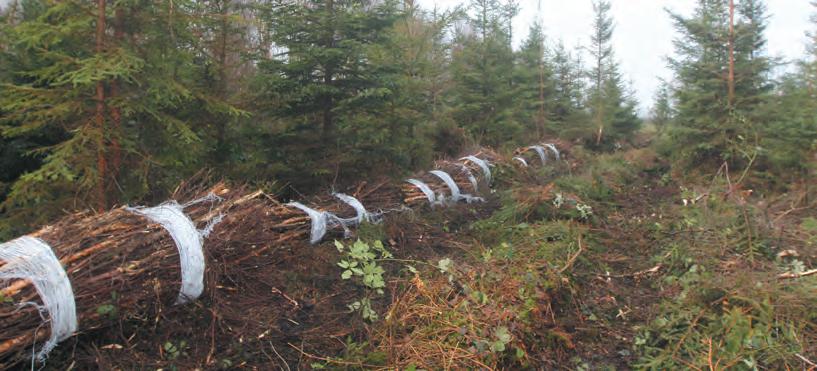
This picture: The Fixteri unit is mounted on the host machine’s rear chassis and can be fed from either side.
Far right: Side discharge arms lower from the machine and weigh the bundle before releasing it. Bundles in the forest awaiting collection by the forwarder.

process is achieved by chain mechanisms, which exert a tightening action on the material to achieve a high density bundle before the material ascends to the top section of the unit where netting is applied in two bands from two dispensers located on the side of the machine.
With the bundle formed, the discharge process begins with the side discharge arms dropping down from their concealed retracted position and cradling the bundle for weighing by sensors within the arm structure. Once the weight has been recorded, the arms lower and drop the bundle onto the ground.
The user-friendliness of the machine lies in its high degree of automation honed during an arduous development process. That’s not to say Fixteri isn’t continuing to develop the machine, though. Juha explained how small mechanical changes to chain drives made in recent months have smoothened operation with very small and weak stems, without affecting performance on bigger stems.
LEAVING A POSITIVE IMPRESSION
While on trial in Ireland, the machine successfully cleared problem sites of invasive species, with only heavy rain and deteriorating ground stopping it being even more prolific. Of course, final judgement will have to wait until the sites begin to recover, but there’s no doubting the Fixteri’s ability to streamline the formation of bundles within the stand and generally make the whole process of extraction easier.
It also improves the quality of the wood energy material, while ensuring high energy content thanks to the uniformity of the drying process with baled material over conventional wood energy stockpiles.
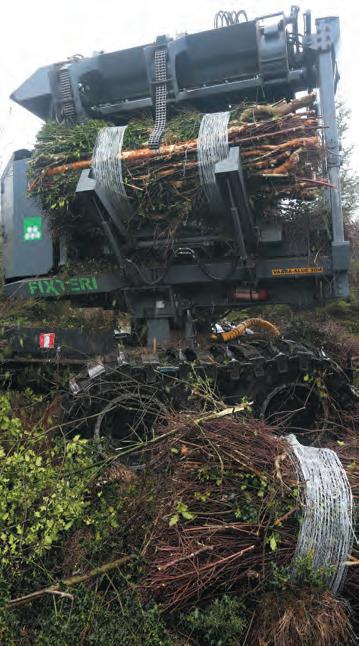