
3 minute read
HP Dairies Canterbury
by Sun Media
to new dairy!
Clare Bayly
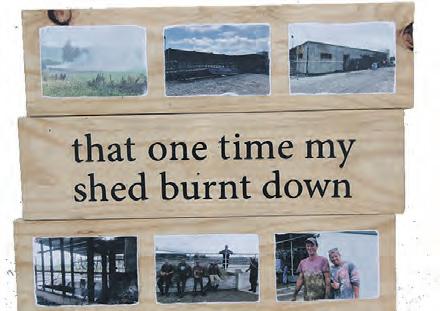
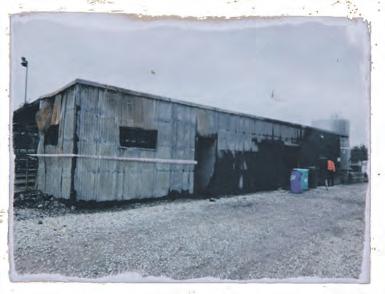
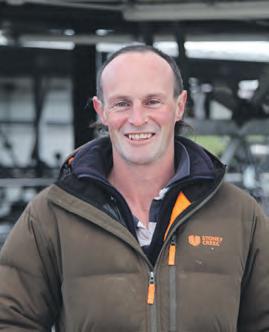
One year on, Hamish Pearse says ‘his worst nightmare’ has turned out to be a blessing.
A photo-board is a reminder of the devastation to the Pearse dairy. The AB facility, previously an 18-aside herringbone, to the left; and the extended 41-aside herringbone to the right.

View from the dairy – the Southern Alps.
The first alert that a fire had broke out in Hamish Pearse’s Temuka dairy came from exploding marker spray cans. It was around 8pm on a still February night and the sound of the cans exploding – akin to gunshots – alerted Hamish’s milker who, on seeing the flames, rang him
“It was an electrical fire which started in the office. We alerted the local fire brigade and se about trying to contain the fire but the fire ha tripped the fuses to the yard-wash hoses – so by the time we worked out which fuses we could turn out, the fire had gone through the wall and into the dairy,” says Hamish.
“By the time the fire was extinguished the office, milk and store rooms and the poly panel wall, which separated the service rooms from the dairy, were destroyed with the damage in the dairy extending to the wooden roof beams and all rubberware.
“It was devastating. At that time it was hard to see how we’d manage given we were still milking twice-a-day – but manage we did.” Milking next door
Hamish’s father Jeffrey Pearse, and Jeffrey’s business partner Evan Agnew, built the 25-aside herringbone shed in 1990, two years later adding another 18-aside herringbone alongside it rather than extending the original pit, because they didn’t want to upset cow flow, and milked through both sheds.
Hamish took over the farm in 2011 as a 50/50 sharemilker for his father and Evan, eventually buying out the latter. Today Hamish and wife Zoe Pearse own the 200 hectare, 650 cow, farming 48 per cent and 52 per cent respectively with Hamish’s father.
With the shed destroyed by fire and unable t be used, Hamish turned to his neighbours and milked in their rotary dairy for four or five days
“While we were milking next door our local engineers worked frantically to patch the fire ravaged shed to a stage where we could resume milking in the 18-aside.
“It looked terrible, but we were able to bring the cows home and continue milking once-aday until they were dried off on May 28.”
Hamish says once he’d gotten over the shock of the fire, he began planning a rebuild
“It was a chance to rethink the layout and efficiency of the shed. There were some aspects we wanted to retain – like the 18-aside – because repurposed, it would provide a large, covered animal handling facility. The opportunity
“The old set-up had a square collection yard with no backing gate and we had virtually no technology – so rebuilding gave us an opportunity to modernise and automate the dairy for the future.
“And we wanted to extend the pit of the 25-aside to 41-aside herringbone.”
The rebuild started May 10 with the cows milked through the 18-aside until they had dried off.
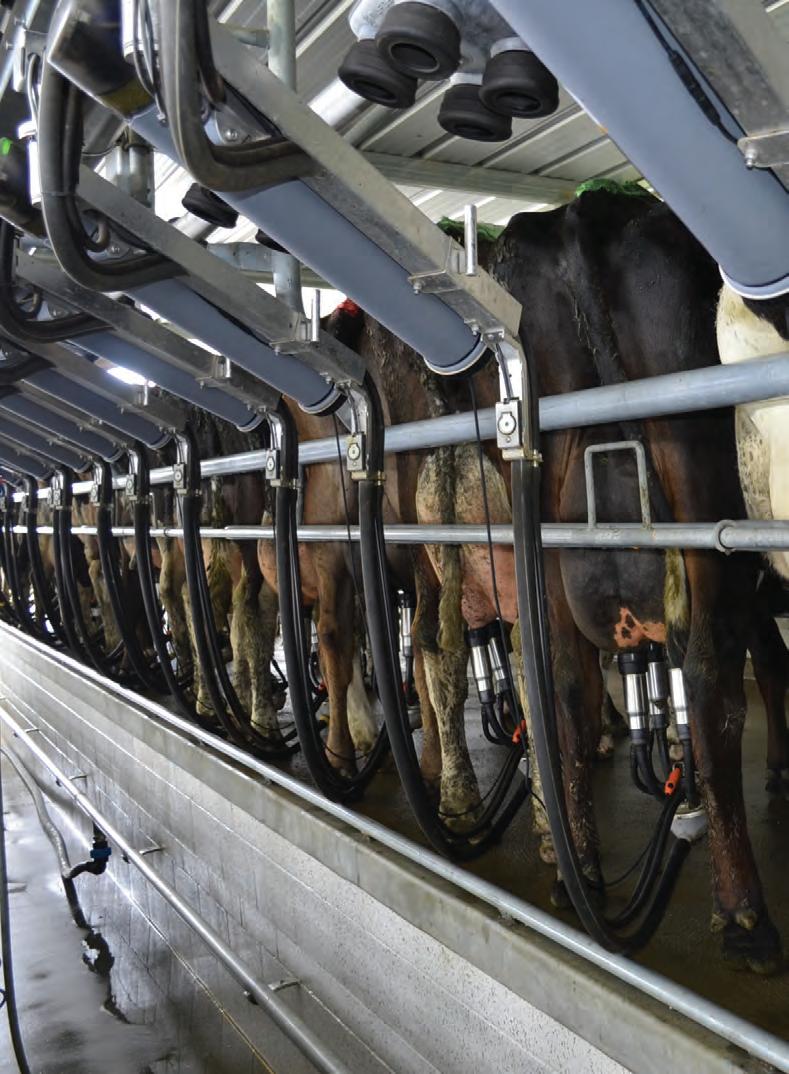
STRAIGHT FORWARD PERFORMANCE.
Looking for a proven, easy-to-maintain herringbone that’s efficient and future-proof? Our iXPRESS4+ offers reliable performance and a higher cow throughput with fewer operators.
Build new or refit Milk 400 cows per hour with 1 operator Automation upgrade pathway
For straight-forward performance: GEA.com/new-zealand