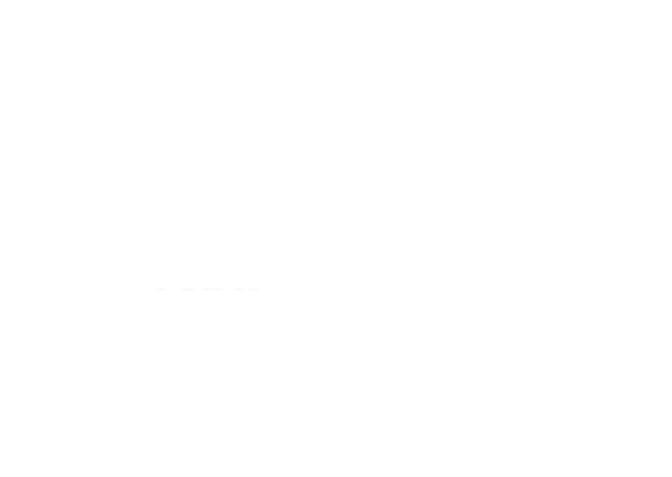
49 minute read
Top 10 Trends for Smart PV for a Greener Future

TOP 10 TRENDS OF SMART PV FOR A GREENER FUTURE
Advertisement

Huawei held the Top 10 Trends of Smart PV (photovoltaic) conference, with the theme of ''Accelerating Solar as a Major Energy Source''. At the conference, Chen Guoguang, President of Huawei Smart PV+ESS Business, shared Huawei's insights on the 10 trends of Smart PV from the perspectives of multi-scenario collaboration, digital transformation, and enhanced safety.
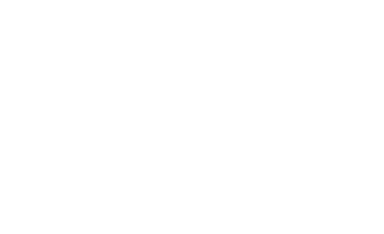
As the proportion of renewable energy keeps increasing, the PV industry acquired a booming growth, yet, the industry still faces many challenges, including how to continue reducing the levelized cost of energy (LCOE), how to improve the O&M efficiency, how to maintain power grid stability as more renewable energy are feeding in, and how to ensure end-to-end system safety. "Amid the rapid growth of the PV industry, these challenges also bring opportunities." said Chen Guoguang. As a forward-looking enterprise, Huawei is keen to sharing our insights and thinking with our partners, as well as organizations and individuals who are interested in green and sustainable development.
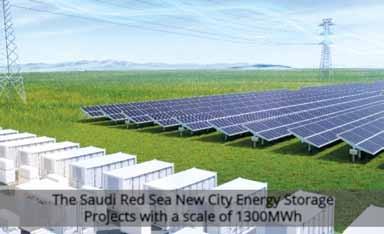
TREnD 1: PV+ESS GEnERATOR As more renewable energy is feeding into power grids, various complex technical problems arise in terms of system stability, power balance, and power quality.
Therefore, a new control mode is needed to increase active/reactive power control and response capability, and actively mitigate frequency and voltage fluctuations. With the integration of PV and ESS as well as the Grid Forming technology, we can build 'Smart PV+ESS Generators' that use voltage source control instead of current source control, The Saudi Red Sea New City Energy Storage
Projects with a scale of 1300MWh
provides strong inertia support, transient voltage stabilization, and fault ride-through capabilities. This will transform PV from grid following to grid forming, helping increase PV feed-in.
A milestone in practice of these technologies was the Red Sea project in Saudi Arabia, which Huawei provided a complete set of solution including smart PV controller, lithium battery energy storage system (BESS) as one of the major partners. This project uses 400 MW PV and 1.3 GWh ESS to support the power grid which replaces traditional diesel generators and provides clean and stable power for 1 million people, building the world's first city powered by 100% renewable energy.
TREnD 2: HIGH DEnSITy AnD RElIABIlITy High power and reliability of equipment in PV plants will be the trend. Take PV inverters as an example, nowadays, the DC voltage of inverters is increased from 1100 V to 1500 V. With the application of new materials such as silicon carbide (SiC) and gallium nitride (GaN), as well as the full integration of digital, power electronics, and thermal management technologies, it is estimated that the power density of inverters will increase by about 50% in the next five years, and the high reliability can be maintained.
The 2.2 GW PV plant in Qinghai, China is 3100 m above sea level and has 9216 Huawei Smart PV Controllers (inverters) running stably in this harsh environment. The total availability hours of Huawei inverters exceed 20 million hours, and the availability reaches 99.999%. rate of MLPE in the distributed PV market is expected to reach 20% to 30% by 2027.
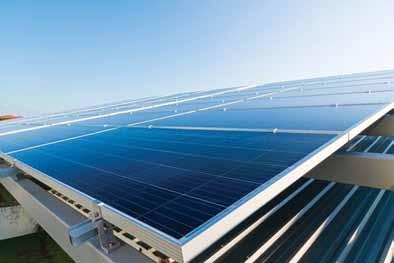
TREnD 3: MODulE-lEVEl POwER ElECTROnICS (MlPE) Driven by industry policies and technology advancement, distributed PV has witnessed vigorous development in recent years. We are facing challenges such as how to improve the utilization of rooftop resources, ensure high energy yield, and how to ensure the PV+ESS system safety. Therefore, more refined management is a must.
In a PV system, module-level power electronics (MLPE) refer to power electronic equipment that can perform refined control on one or more PV modules, including micro inverters, power optimizers, and disconnectors. MLPE brings unique values such as module-level power generation, monitoring, and safe shutdown. As PV systems are becoming safer and more intelligent, the penetration TREnD 4: STRInG EnERGy STORAGE Compared with traditional centralized ESS solutions, the Smart String ESS solution adopts a distributed architecture and modular design. It uses innovative technologies and digital intelligent management to optimize energy at the battery pack level and control energy at the rack level. This results in more discharge energy, optimal investment, simple O&M, as well as safety and reliability throughout the lifecycle of the ESS.
In 2022, in the 200 MW/200 MWh ESS project in Singapore for the purpose of frequency regulation and spinning reserve, the largest BESS project in Southeast Asia, the Smart String ESS implements refined charge and discharge management to achieve constant
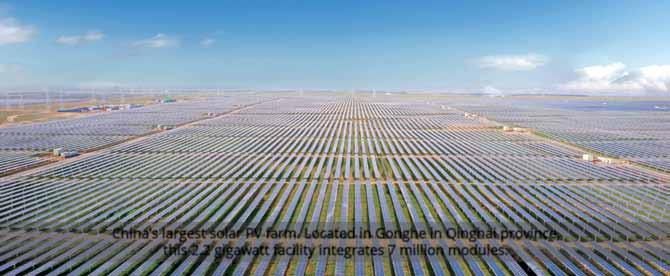
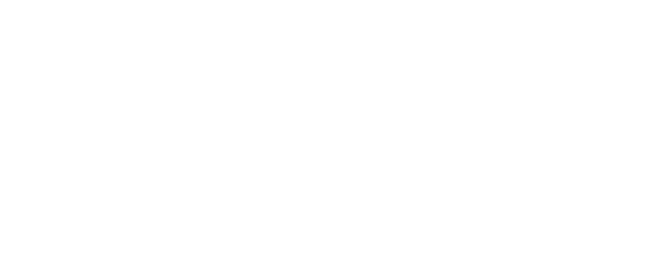
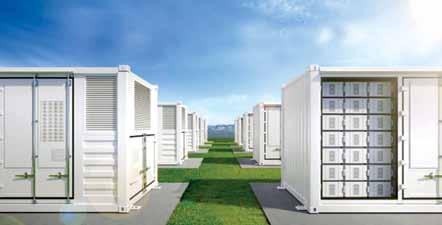
power output for a longer time and ensure frequency regulation benefits. In addition, the automatic SOC calibration function at the battery pack level reduces labor costs and greatly improves O&M efficiency.
TREnD 5: CEll-lEVEl REFInED MAnAGEMEnT Similar to PV systems shifting towards MLPE, lithium BESSs are set to develop towards smaller management level. Only refined management at battery cell level can better cope with the efficiency and safety problems. Currently, the traditional battery management system (BMS) can only summarize and analyze limited data, and it is almost impossible to detect faults and generate warnings in the early stage. Therefore, BMS needs to be more sensitive, intelligent, and even predictive. This depends on the collection, computing, and processing of a large amount of data, and AI technologies to find the optimal operating mode and make forecasts. loads, and implement flexible scheduling to power generation units and storage units to achieve peak shaving etc.
Therefore, building a stable energy system that integrates the PV+ESS+Grid to support PV power
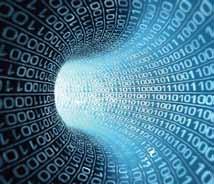
supply and feed-in to grid will become a key measure to ensure energy security. We can integrate digital, power electronics, and energy storage technologies to achieve multi-energy complementation. Virtual Power Plants (VPPs) can intelligently manage, operate, and trade power of massive distributed PV+ESS systems thru multiple technologies including 5G, AI, and cloud technologies, which will come into practice in more countries.
TREnD 7: uPGRADED SAFETy Safety is the cornerstone of the PV & ESS industry development. This requires us to systematically consider all scenarios and links and fully integrate power electronics, electrochemical, thermal management, and digital technologies to upgrade system safety. In a PV plant, faults caused by the DC side account for more than 70% of all faults. Therefore, the inverter needs to support smart string disconnection and automatic connector detection. In distributed PV scenario, the AFCI (Arc Fault Circuit Breaker) function will become a standard configuration, and the modulelevel rapid shutdown function will ensure the safety of maintenance personnel and firefighters. In ESS scenario, multiple technologies, such as power electronics, cloud, and AI, need to be used to implement refined management of ESS from battery cells to whole system. The traditional protection mode based on passive response and physical isolation is changed to active automatic protection, implementing multi-dimensional safety design from hardware to software and from structure to algorithm.
TREnD 8: SECuRITy AnD TRuSTwORTHInESS
In addition to bringing benefits,
TREnD 6: PV+ESS+GRID InTEGRATIOn On the power generation side, we see more and more practices of building clean energy bases of PV+ESS that supply electricity to load centers through UHV power transmission lines. On the power consumption side, virtual power plants (VPPs) become increasingly popular in many countries. VPPs combine massive distributed PV systems, ESSs, and controllable
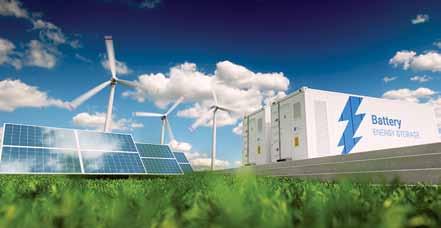
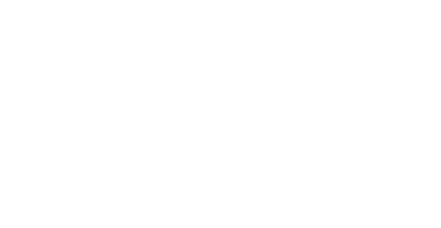
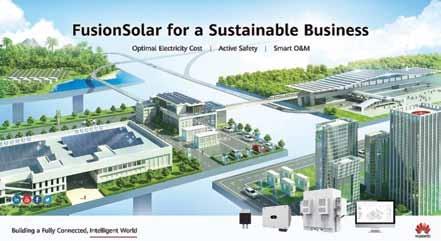
PV systems also have various risks, including equipment safety and information security. Equipment safety risks mainly refer to the shutdown caused by faults. Information security risks refer to external network attacks. To cope with these challenges and threats, enterprises and organizations need to establish a complete set of "security and trustworthiness" management mechanisms, including the reliability, availability, security, and resilience of systems and devices. We also need to implement protection for personal and environmental safety as well as data privacy.
TREnD 9: DIGITAlIzATIOn Conventional PV plants have a large amount of equipment and lack information collection and reporting channels. Most of the equipment cannot 'communicate' with each other which is very difficult to implement refined management.
With the introduction of advanced digital technologies such as 5G, the Internet of Things (IoT), cloud computing, sensing technologies, and big data, PV plants can send and receive information, using "bits" (information flows) to manage "watts" (energy flows). The entire link of generation-transmission-storage-distribution-consumption is visible, manageable, and controllable.
TREnD 10: AI APPlICATIOn As the energy industry moves towards an era of data, how to better collect, utilize, and maximize the value of data has become one of the top concerns of the entire industry.
AI technologies can be widely applied to renewable energy fields, and play an indispensable role in the entire lifecycle of PV+ESS, including manufacturing, construction, O&M, optimization, and operation. The convergence of AI and technologies such as cloud computing and big data is deepening, and the tool chain focusing on data processing, model training, deployment and operation, and safety monitoring will be enriched. In the renewable energy field, AI, like power electronics and digital technologies, will drive profound industry transformation.
At the end, Chen Guoguang remarked that the converged applications of 5G, cloud, and AI are shaping a world where all things can sense, all things are connected, and all things are intelligent. It is coming faster than we think. Huawei identifies the top 10 trends of the PV industry and describes a green and intelligent world in the near future. We hope that people from all walks of life can join hands to achieve the goals of carbon neutrality and build a greener, better future.
Huawei offers leading Smart PV solutions harnessing more than 30 years of expertise in digital information technology.
By integrating AI and Cloud, Huawei further incorporates many latest ICT technologies with PV for optimal power generation, thus making the solar power plant to be Highly Efficient, Safe & Reliable with Smart O&M and Grid Supporting capabilities and builds the foundation for solar to become the main energy source.For solar energy users, Huawei launched advanced solution for C&I and residential customers based on the‘Optimal Electricity Cost and Active Safety’ concept. By improving the utilization of solar power, Huawei has helped to power millions of residents and hundreds of industries globally. Huawei will continue to innovate and enable renewable energy to empower each individual, home, and organization
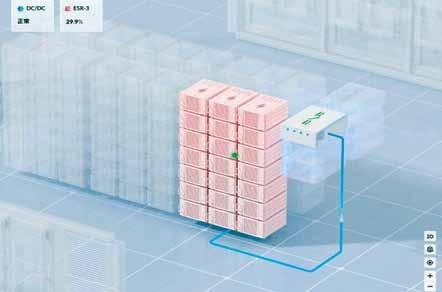
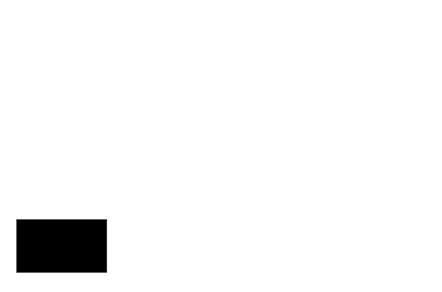
Challenges & OppOrtunities in Global PV SuPPly DiVerSification
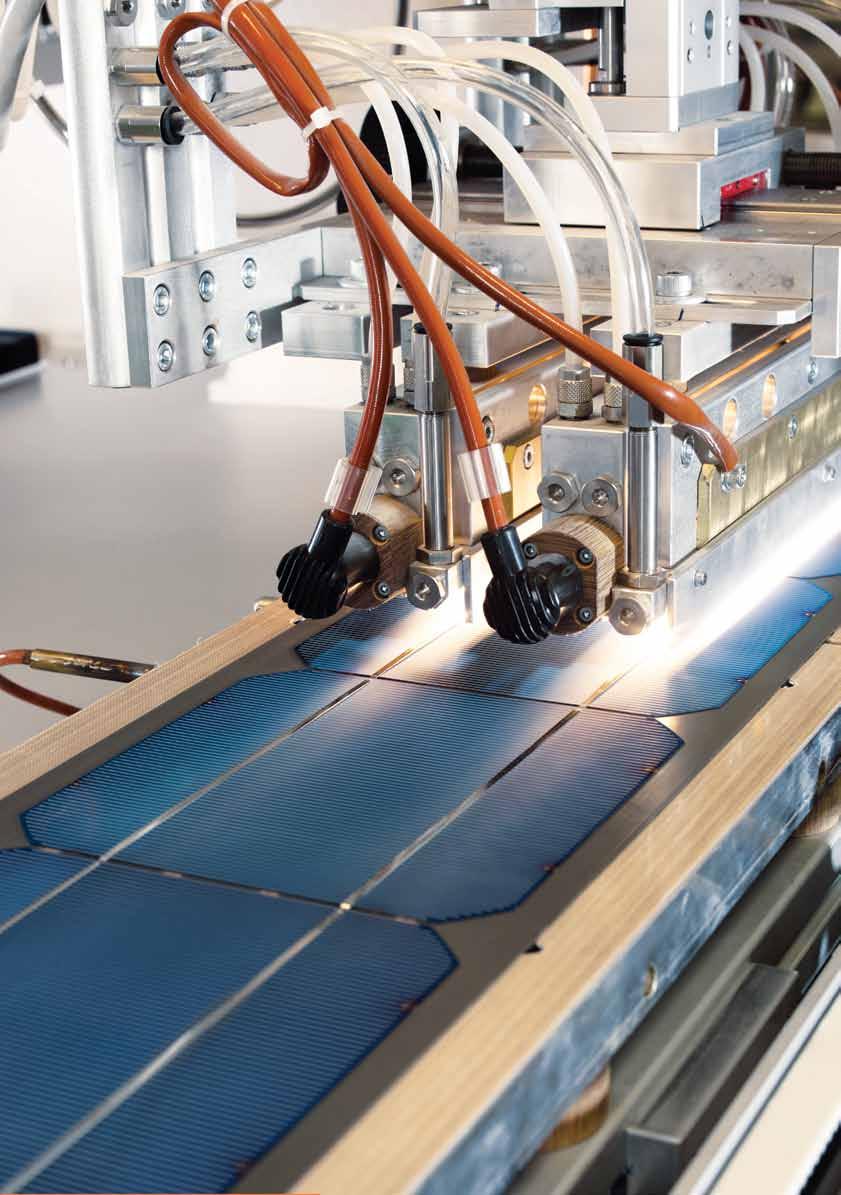
Diversification is one of the key strategies for reducing supply chain risks, the one faced due to fires in some Chinese manufacturing units, COVID 19 outbreak or the ongoing war between Russia & Ukraine. In this article the editorial team at Smart Energy Magazine assesses the opportunities and challenges of developing solar PV supply chains in terms of job creation, investment requirements, manufacturing costs, emissions and recycling. Finally, the article summarises policy approaches and recommendations for creating a globally competitive domestic manufacturing industry.
Solar PV is a crucial pillar of clean energy transitions worldwide, underpinning efforts to reach international energy and climate goals. Over the last decade, the amount of solar PV deployed around the world has increased massively while its costs have declined drastically. Putting the world on a path to reaching net zero emissions requires solar PV to expand globally on an even greater scale, raising concerns about security of manufacturing supply for achieving such rapid growth rates – but also offering new opportunities for diversification.
thE currEnt stAtus of GLoBAL pV suppLy chAin
A major geographical shift has occurred in solar PV manufacturing capacity and production over the last decade. China has strengthened its leading position as a manufacturer of wafers, cells and modules between 2010 and 2021, while its share of global polysilicon production capacity almost tripled. Today, the country’s share in all manufacturing stages exceeds 80%, more than double its 36% share in global PV deployment.
For wafers, China has very little competition, while for cells and modules Southeast Asia has considerable manufacturing capacity, mostly in Viet Nam, Malaysia and Thailand. For polysilicon, Germany continues to be a major supplier for the c-Si PV modules industry, while the United States and Japan possess significant capacity but focus their production on semiconductor-grade products. Considering manufacturing plants under construction and planned, China’s dominance in solar PV manufacturing is expected to persist or even expand in the short term.
Although countries in North America and Europe have significant module-manufacturing capability, they depend almost entirely on China and Southeast Asia for solar cells, except for manufacturing capacity linked to thin-film technology, which relies less on the Chinese supply chain. In addition, China is also the main manufacturer of module components including glass, EVA, backsheet and junction box.
Low solar cell prices, the possibility of sourcing several panel components locally (frame, glass, wiring and packaging), trade restrictions and government support have encouraged many companies around the world to invest in module assembly lines. Accordingly, 38 countries had module assembly capabilities in 2021, by far the highest of all steps of the PV manufacturing process. In many cases, however, investments were relatively small or stopped at the pilot stage, with just 19 countries having assembly capacity of at least 1 GW.
Companies in several countries and regions are contemplating significant expansions to their manufacturing capacity in upcoming years, notably in India, Viet Nam, Thailand, the United States and the European Union. However, with over 300 GW of new assembly plants under consideration in China, its market share is expected to remain high in the medium term. Given ongoing and planned investments in manufacturing capacity, in addition to innovation and further potential for efficiency gains, crystalline silicon technology is expected to dominate the solar PV market for many years to come.
Taking together polysilicon, wafers, cells and modules, the total value of PV-related trade reached USD 40 billion in 2021 – an increase of over 70% from 2020. International solar PV trade volumes depend strongly on China’s domestic demand because the country is both the largest producer and consumer of polysilicon, wafers, cells and modules. Furthermore, in the last five years it has been the main importer of PV-grade polysilicon, mainly from Germany, Malaysia and Japan, as its domestic production has fallen short of local demand for wafer production.
In 2017-2021, Southeast Asian module manufacturers were responsible for onethird of global PV module exports, directed mostly towards the United States and the European Union, where Chinese modules were subject to
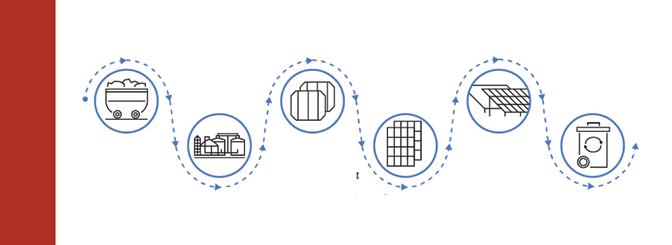
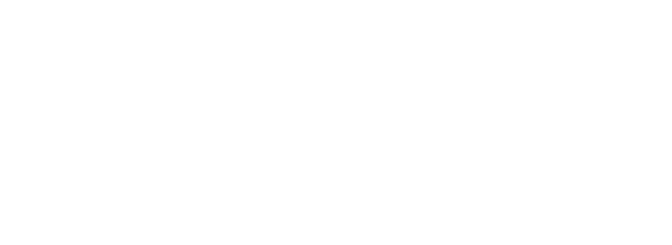
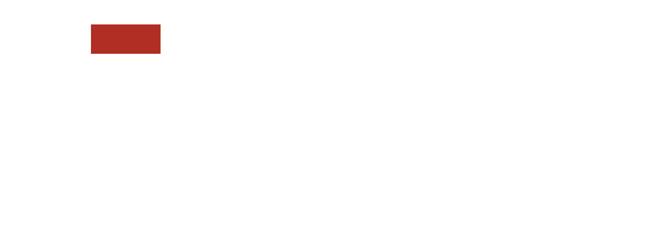
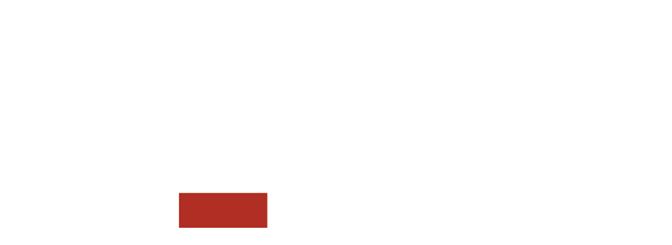
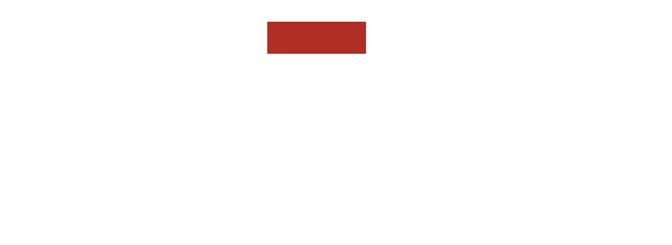
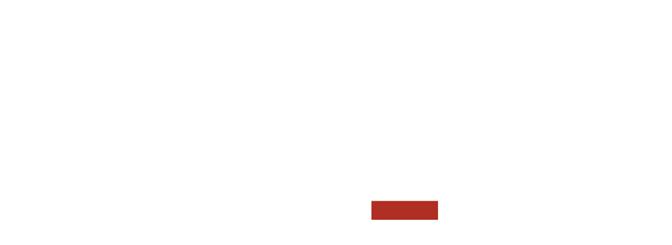
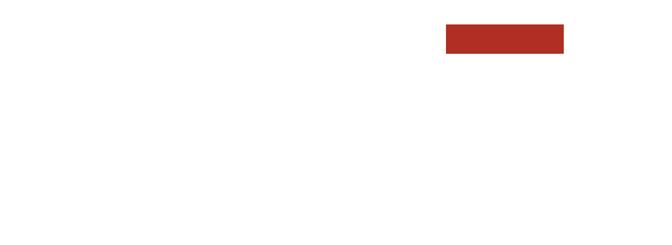
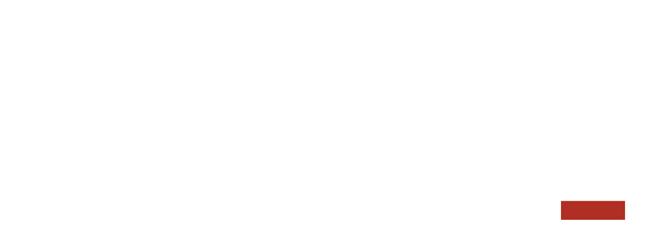
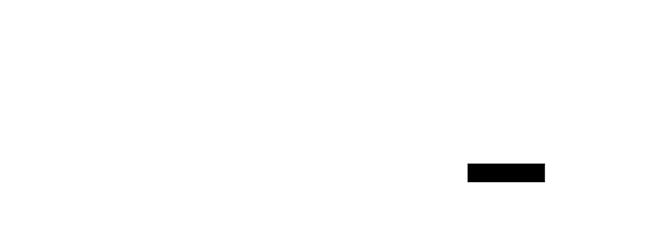
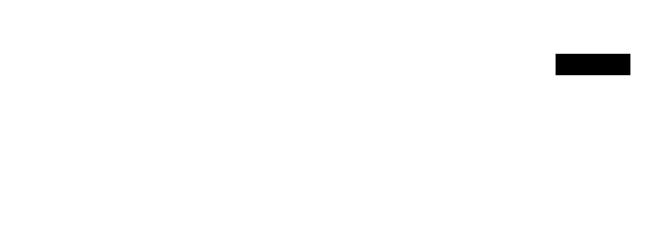
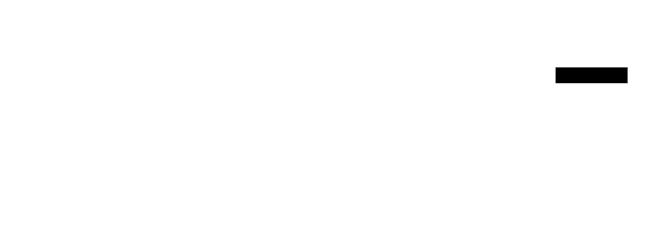
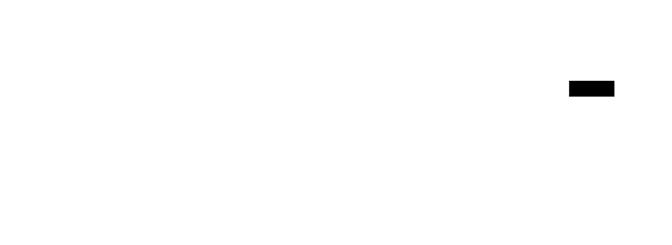
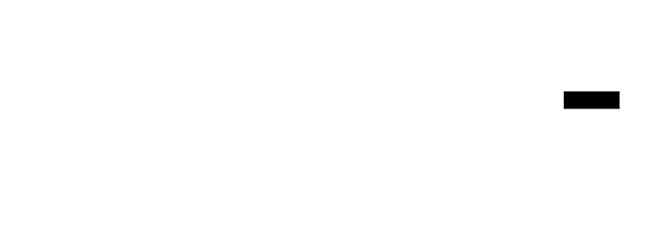
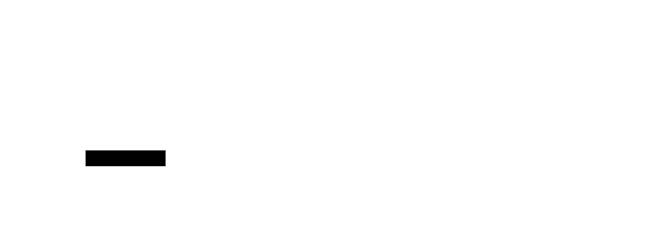
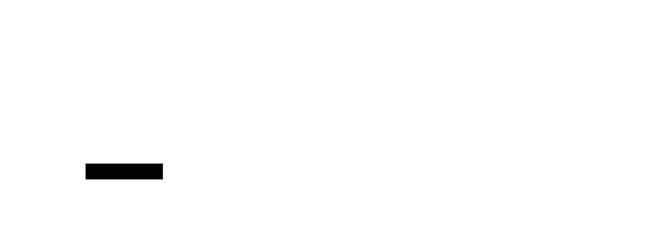
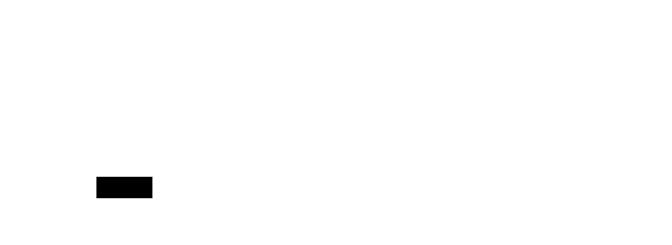
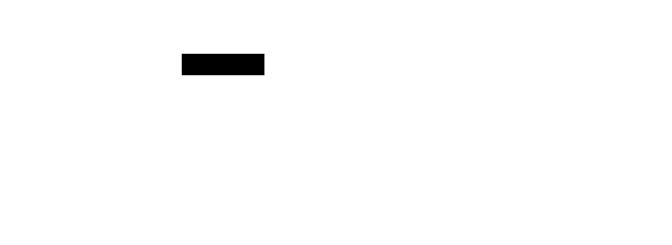
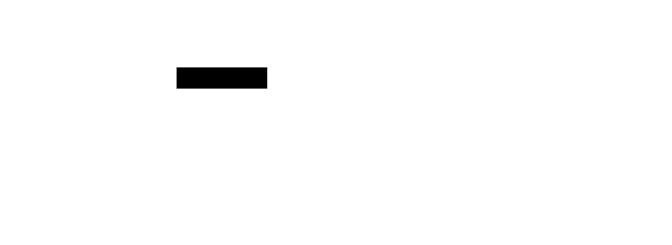
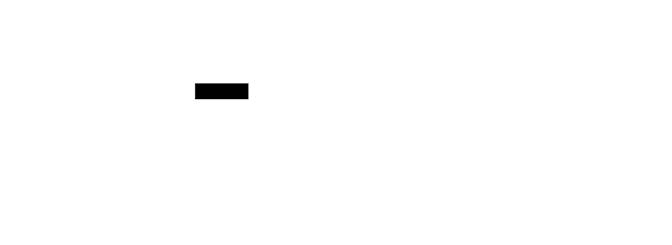
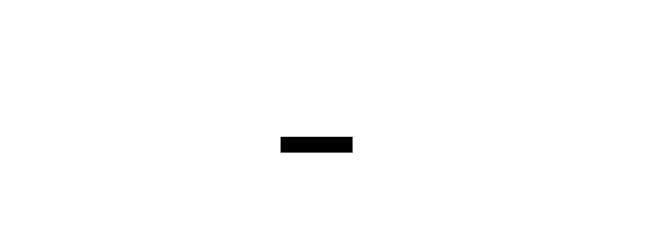
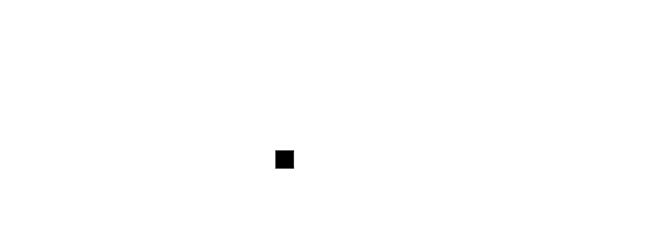
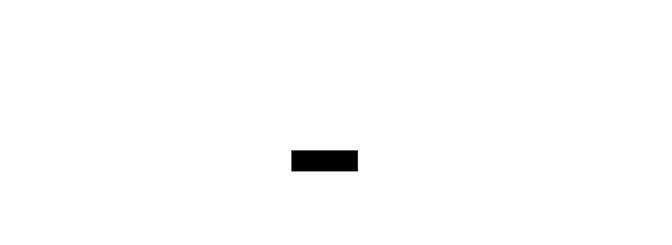
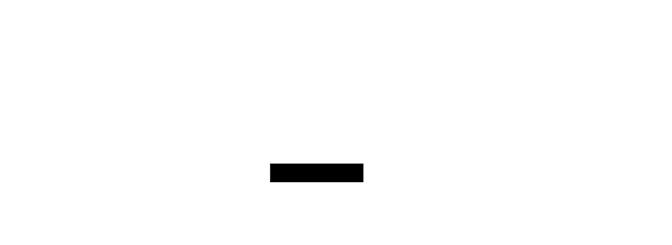
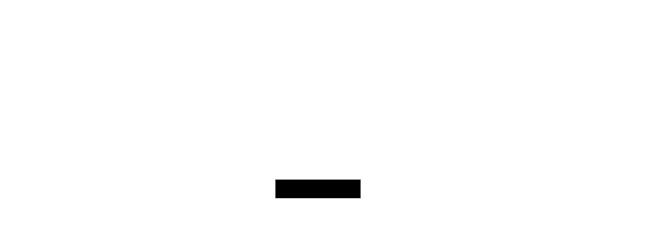
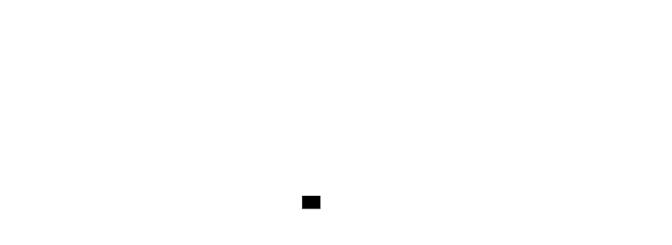
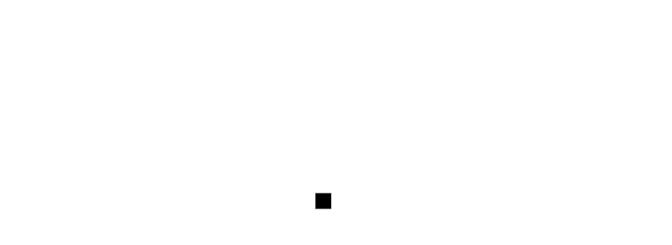
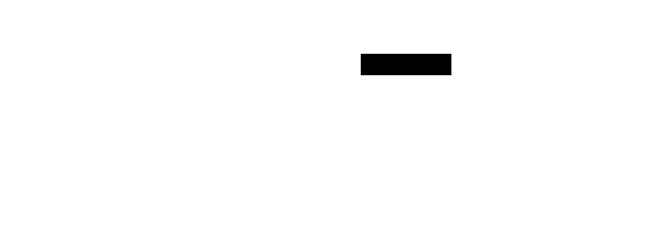
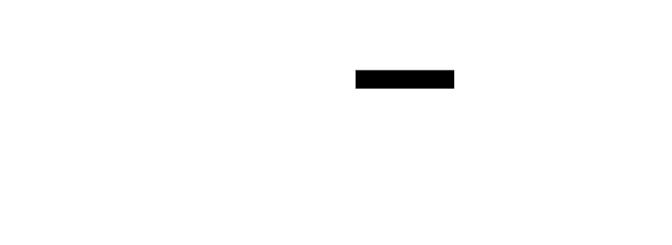
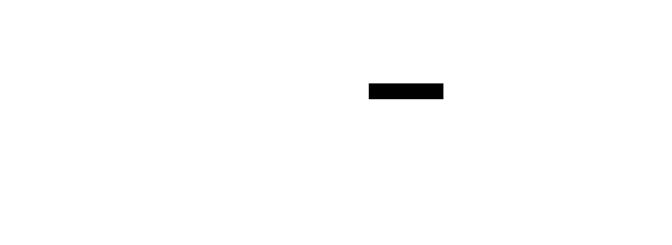
various trade restrictions. The rest of the market was dominated by China, with its shares in India and Brazil exceeding 90%.
When it comes to PV equipment manufacturing, the market have changed dramatically over the past decade, with leadership shifting from Europe, the United States and Japan to China. Driven by the exponential expansion of global demand, the total number of firms entering the PV equipment manufacturing market surged 150% during 2007-2020 to almost 1 900, with the number of Chinese firms almost quadrupling during this period to more than 700 (RTS, 2021). Today, all top ten equipment manufacturers are in China and claim over 45% of the global market share.
soLAr pV suppLy chAin VuLnErABiLitiEs:
Concentration along the PV supply chain at the jurisdictional, geographical, plant and company level make the supply chain vulnerable to single incidents, whether they be a country’s individual policy choices, a natural disaster, a war, a pandemic, technical failures or individual company decisions. Historically, all these risks have materialised, leading to higher prices and likely slowing the pace of solar PV deployment.
For instance, a 2020 explosion at a polysilicon facility in China put 8% of global polysilicon production capacity out of operation. This is the largest of four polysilicon plant closures in 2020 resulting from flooding and technical issues. While each incident occurred at a different time, together they led to an estimated 4% decline in annual production in an alreadytight polysilicon market, contributing to the near tripling of prices between 2020 and 2021. In 2021, silicon and wafer production in China were also curtailed when regulators required producers to cut production as part of energysaving measures. As of early July 2022, a fire at polysilicon facility in Xinjiang and the ensuing maintenance requirements reduced global production by 0.5%. Even this comparatively small disruption contributed to price increases.
Concentrating production within a single geographical region or country also exposes the supply chain to risks from changes in diplomatic relations among countries as well as alterations in domestic policies and infrastructure. For instance, shipping times from China to US and European ports increased from around 40 days to more than 100 following the Covid19 outbreak. Overall, polysilicon, wafer, cell and module production capacities are all becoming more concentrated, leaving the supply chain more vulnerable to risks.
The production capacity of solar PV supply chain segments is also concentrated at the company level, introducing vulnerabilities to another set of risks. Concentrating production capacity among just a few companies introduces the risk of having a small set of companies working together to increase profits at the cost of higher consumer prices and quicker dissemination. This situation can lead to collusion, price fixing, dumping and other behaviours that reduce competition and ultimately boost prices and retard deployment.
Wafer production capacity is considered moderately concentrated. Polysilicon market shares are more distributed among the top five companies, so production is less at risk of competitiveness impacts than that of wafers. Meanwhile, cell and module manufacturing capacity is more distributed than that of polysilicon and wafers, implying fewer competitiveness risks.
High company concentration in the solar PV supply chain makes the financial health of large companies key to the sector’s longterm sustainability, especially considering the formidable investments and expansions needed by 2030.
Poorly designed and implemented trade policies, and uncertainty around them, can lead to price increases, delayed investment and slow solar PV deployment. As trade is critical to provide the diverse materials needed to make solar panels and deliver them to final markets, supply chains are vulnerable to trade policy risks.
Supply Chain Risk Assessment Framework
Criteria Description
Supply chain concentration
Likelihood: How likely is there to be a significant and widespread disruption to that element of the supply chain?
Impact: If a disruption happens, how effectively and quickly could the supply chain reorganize to allow production to continue or resume?
Supply chain concentration Highly concentrated production, either geographically or by firm, will increase the likelihood of a significant disruption due to increased risk of the entire market being exposed to the same shock. How concentrated is the production at a firm level? How concentrated is the production geographically both country and region)?
Pace and scale of growth A larger scale-up requirement compared to the average pace observed in that market, or the rapid development of a new supply chain to reach net zero, will increase the likelihood of a situation where demand and supply become imbalanced. What is the scale-up requirement in percentage terms, for 2030 & 2050 in the Net Zero Emissions by 2050 Scenario compared to the pace observed in the past 10 years? How in-demand is the element a across other supply chains?
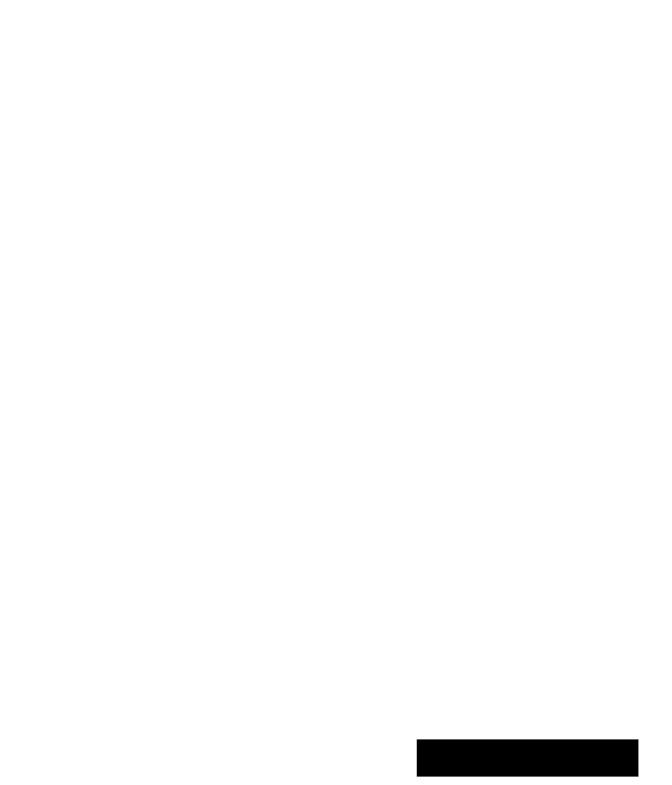
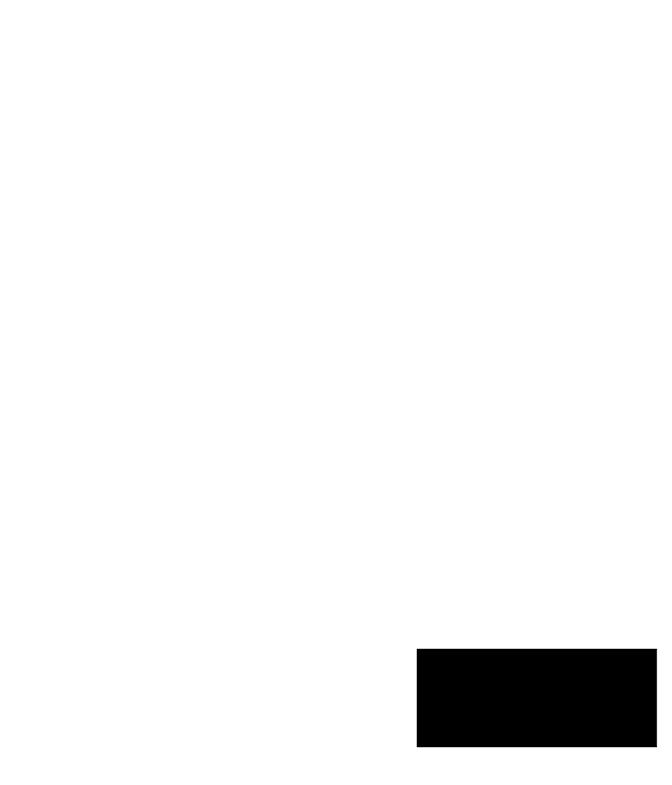
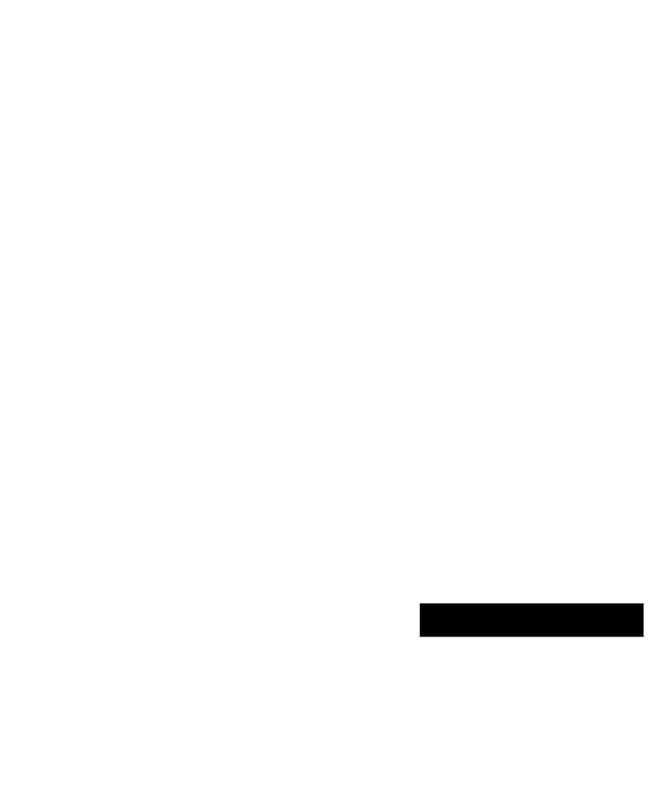
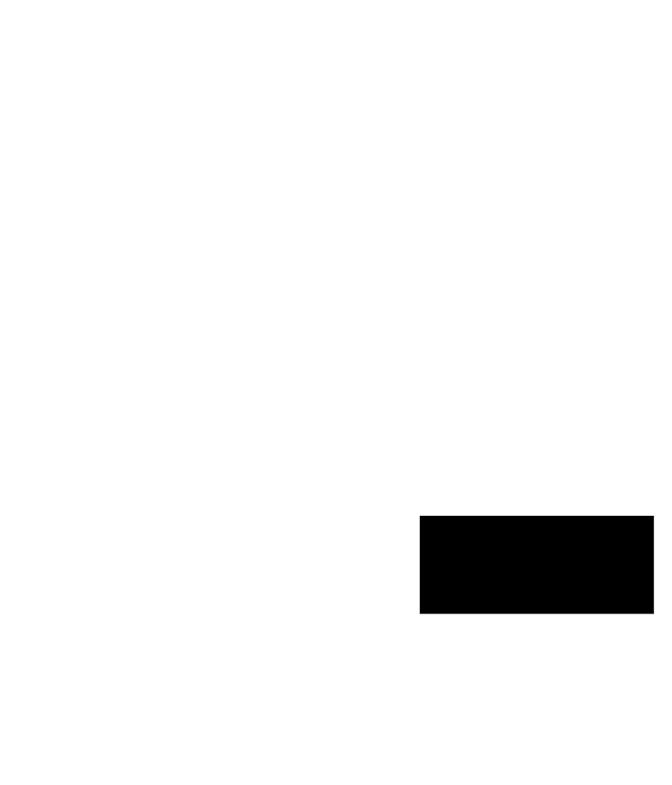
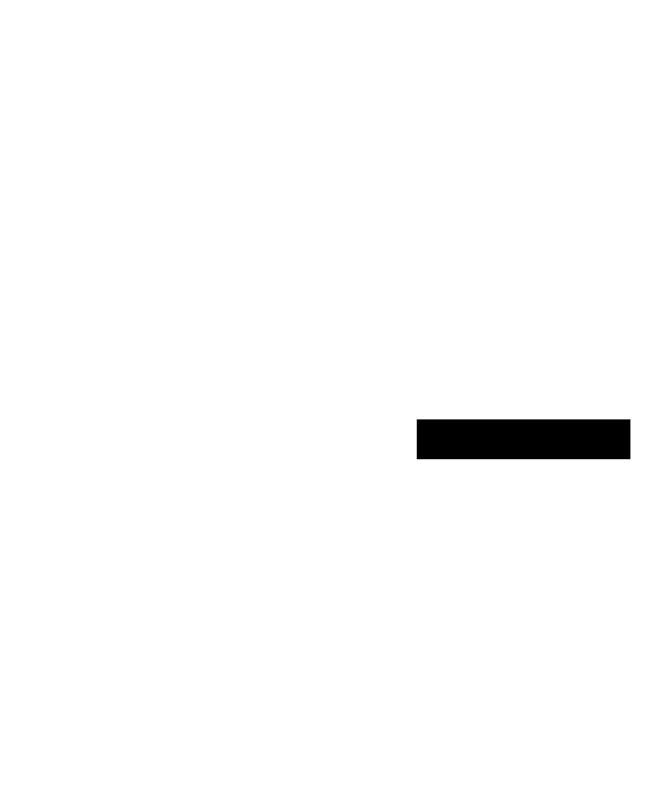
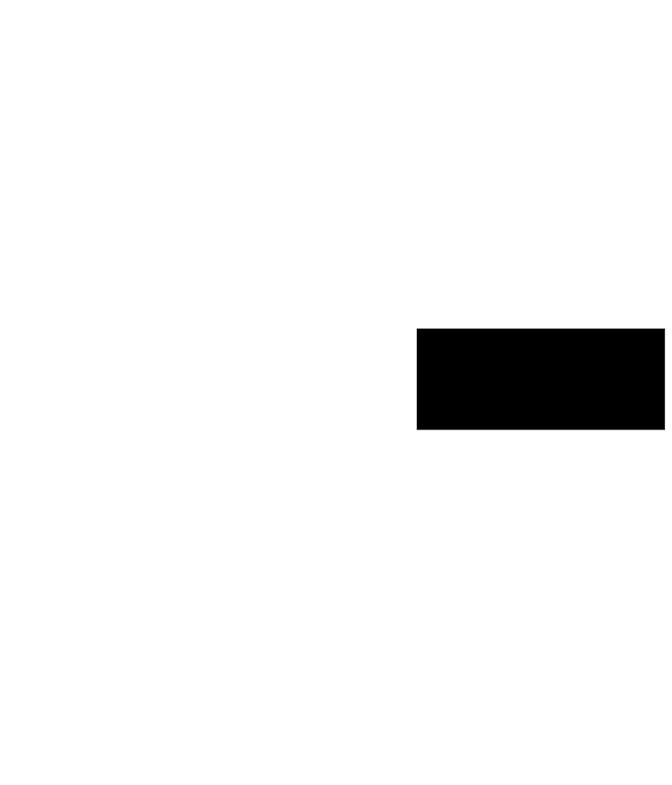

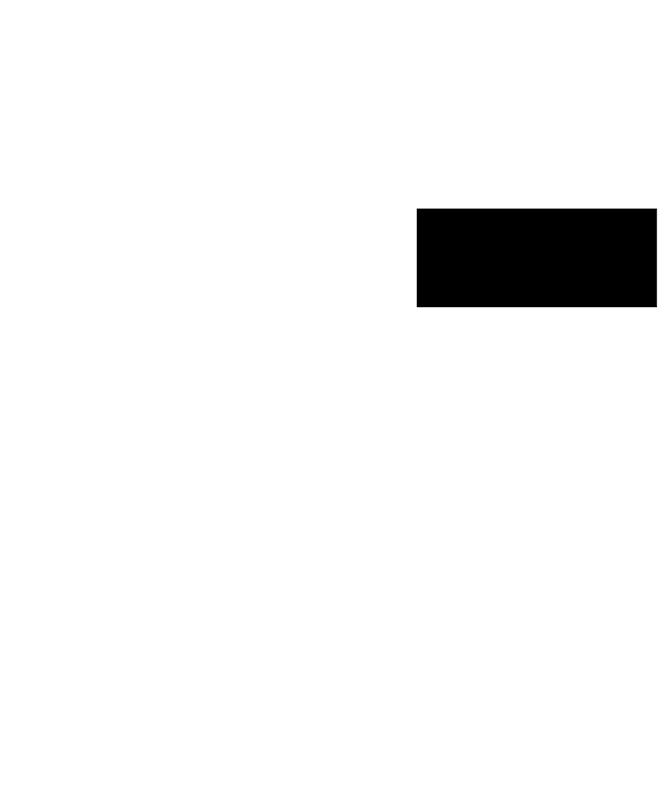
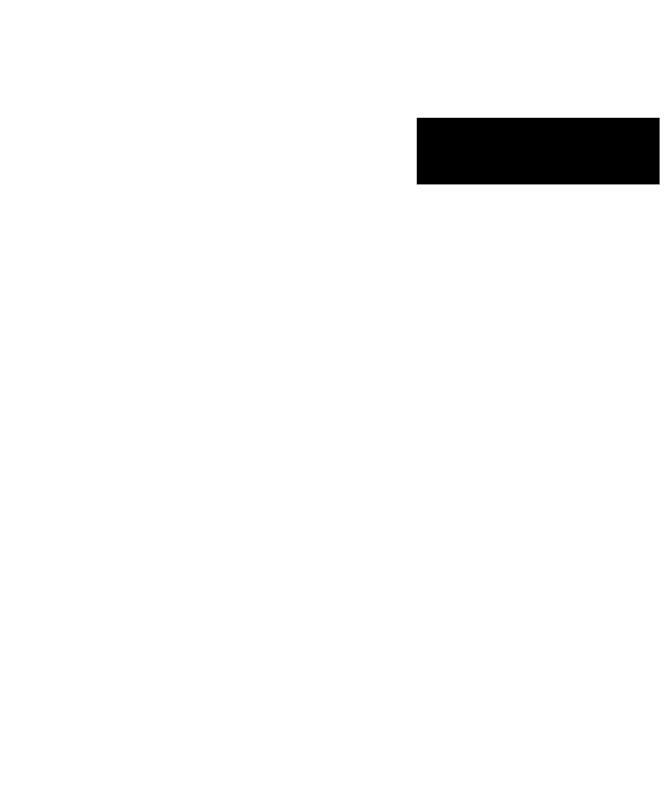

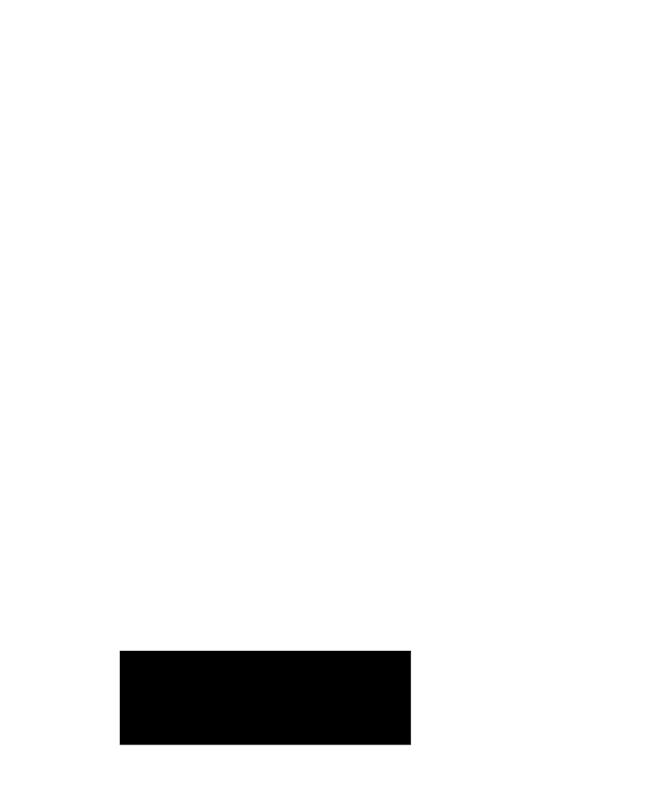
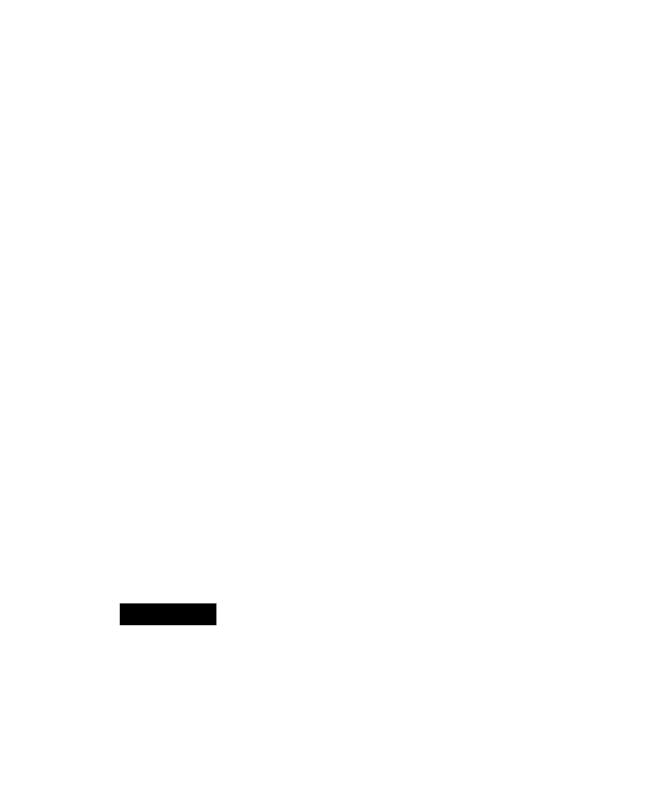
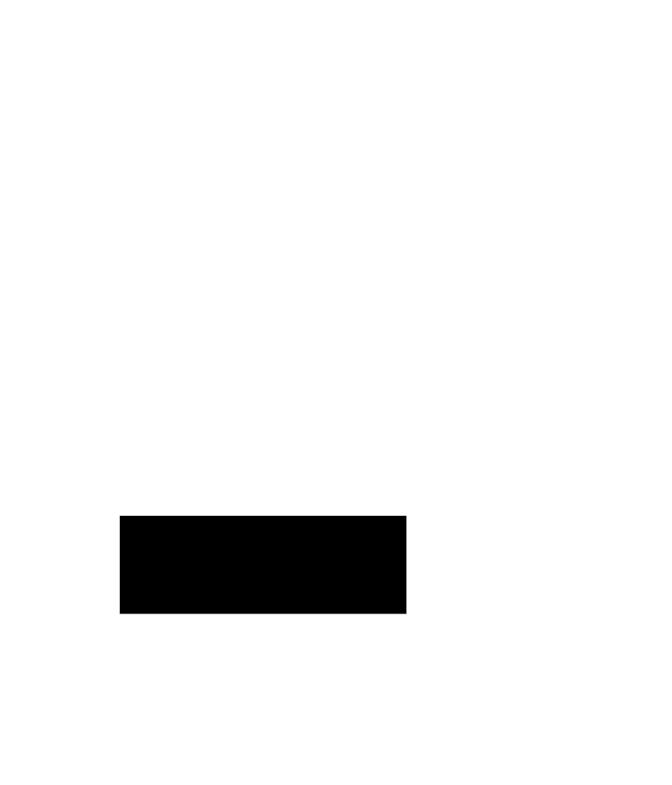
Exposure to trade, natural, technical or geopolitical risks High exposure to potential disruptions, such as trade restrictions, natural disasters, conflict or political instability will increase the likelihood of a disruption - especially when coupled with a highly concentrated market. Are the major producers located in areas prone to natural disasters that are likely to cause prolonged disruption? Do the major producers uphold ESG standards? Are there geopolitical risks and how well e established is the market in the international trading system?
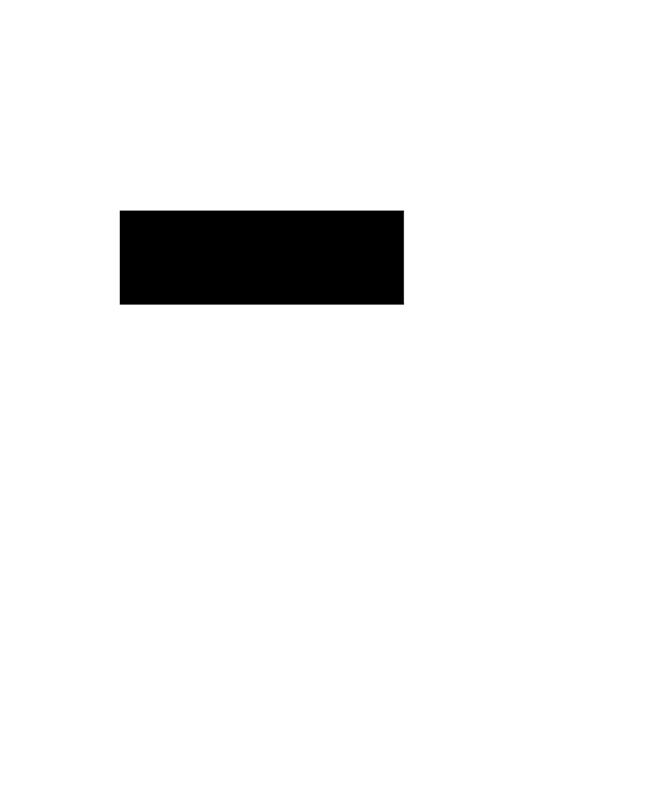
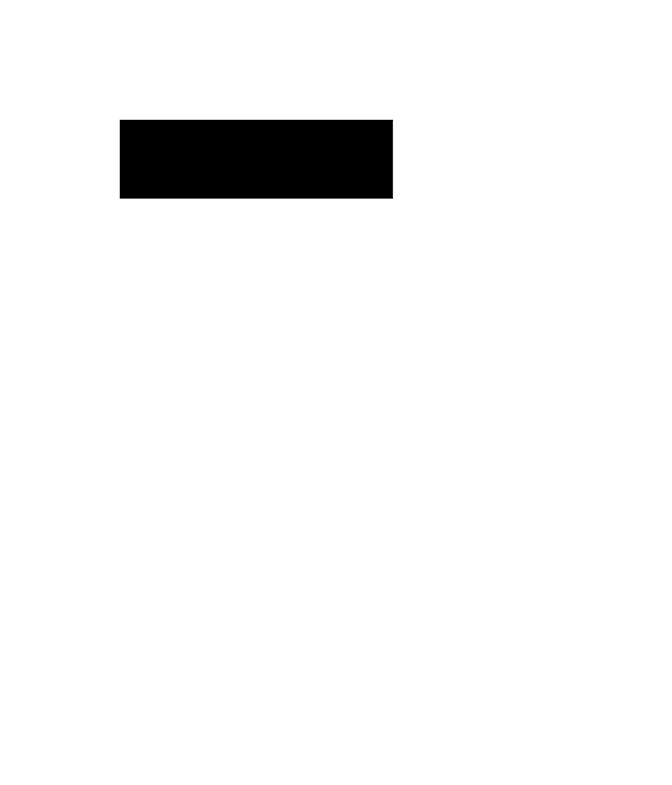
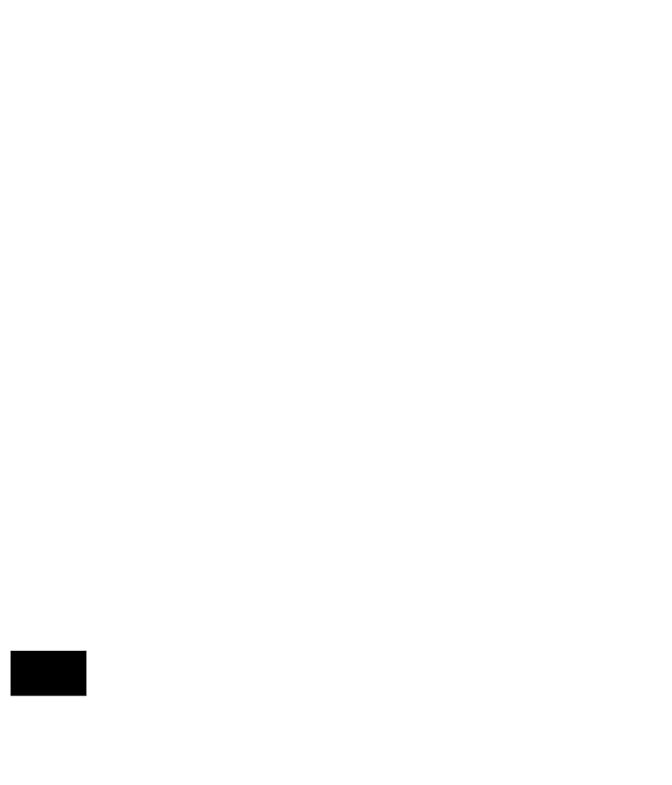
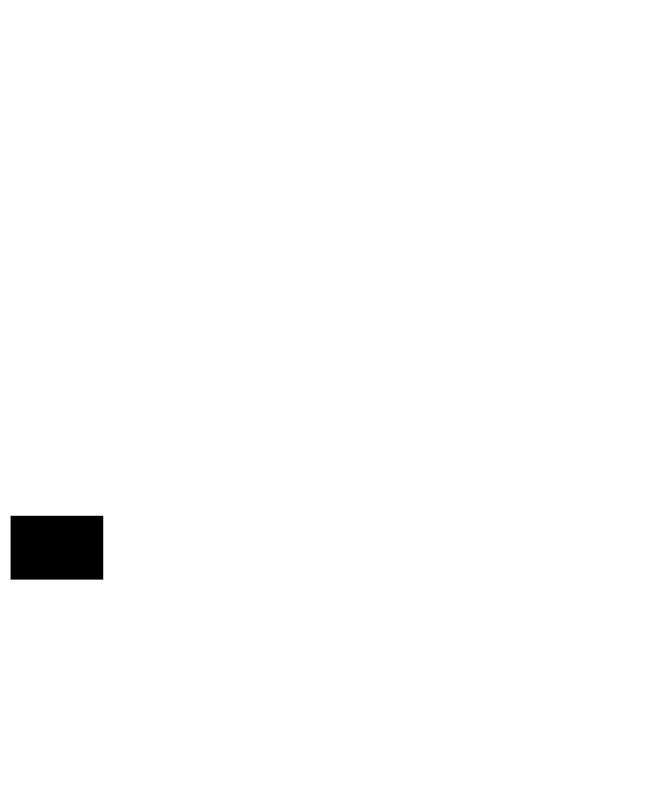
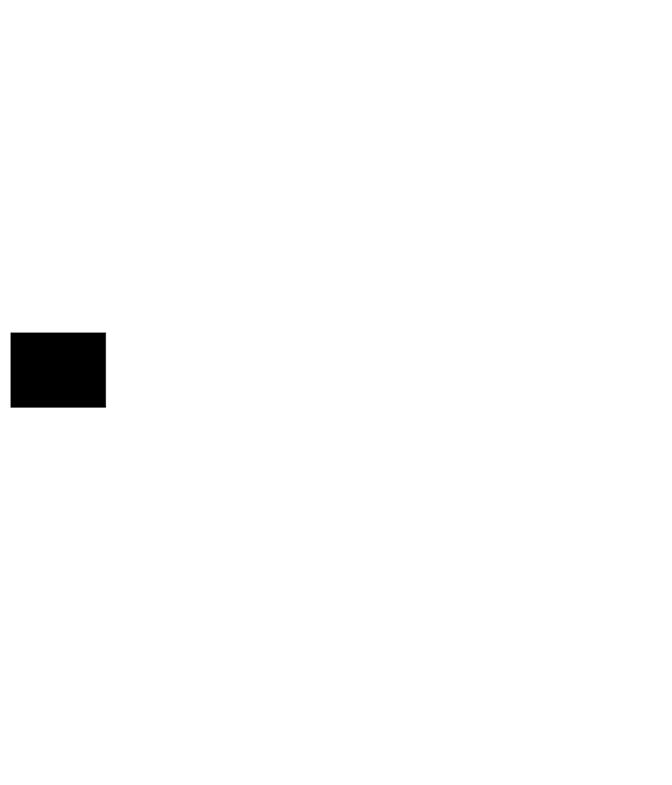

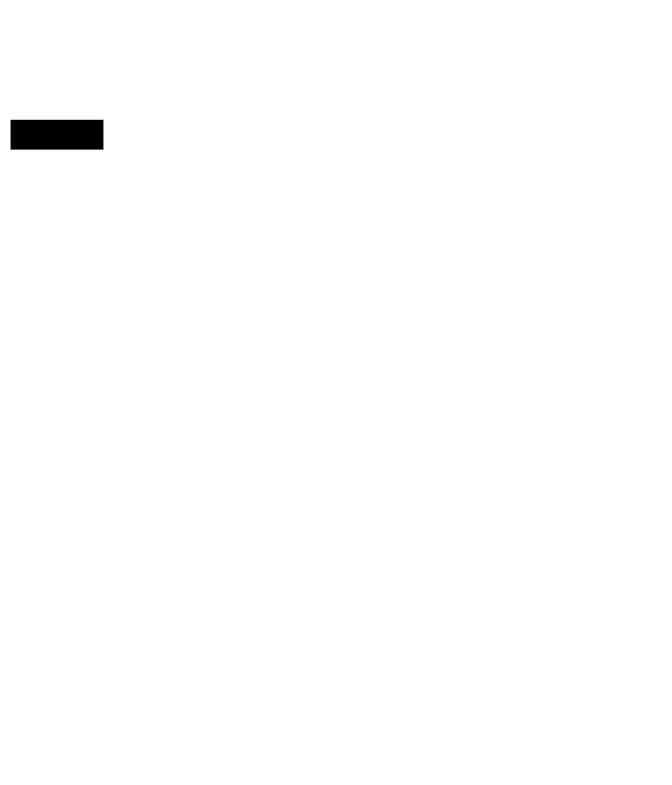
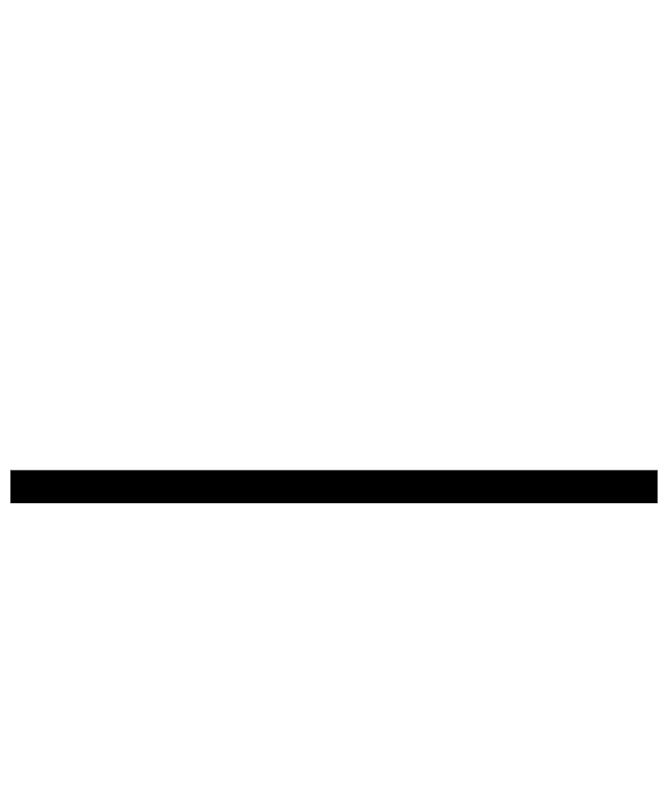
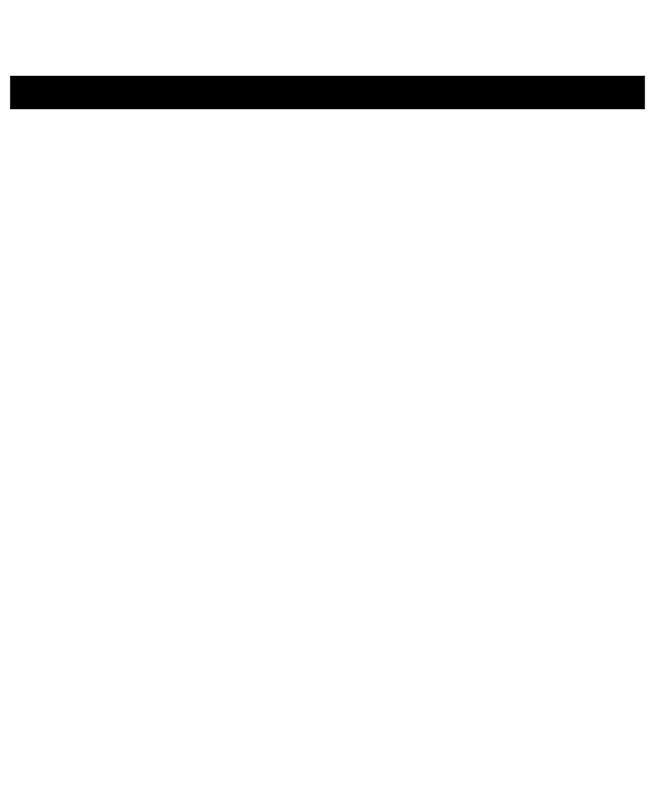
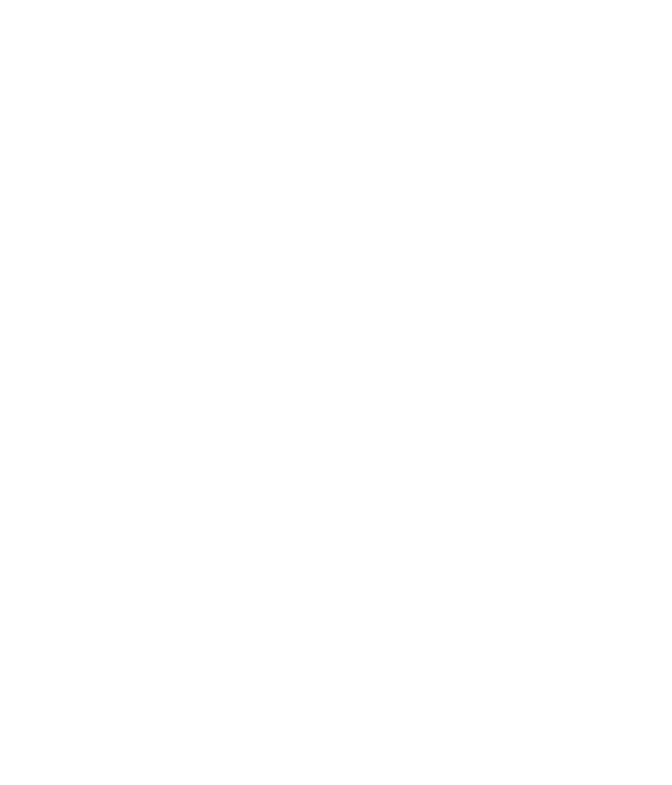
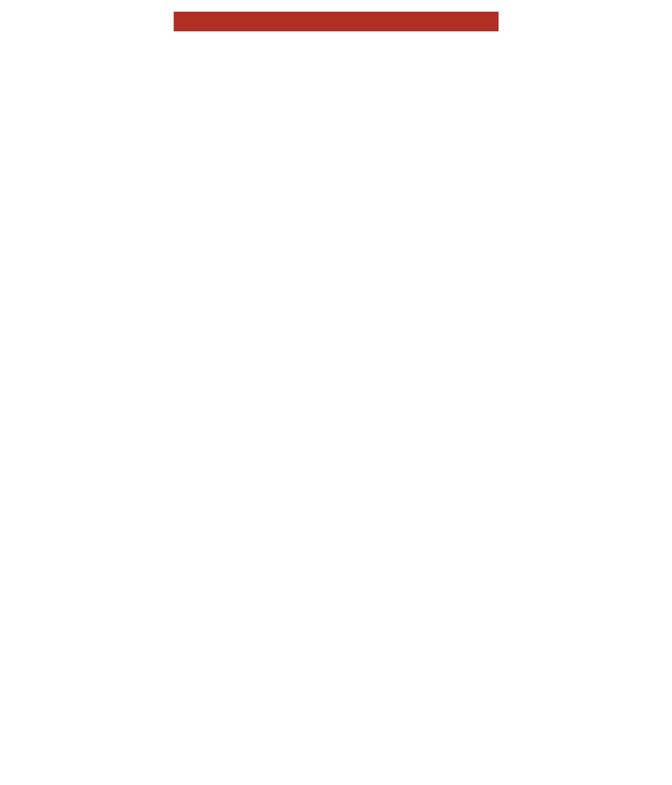
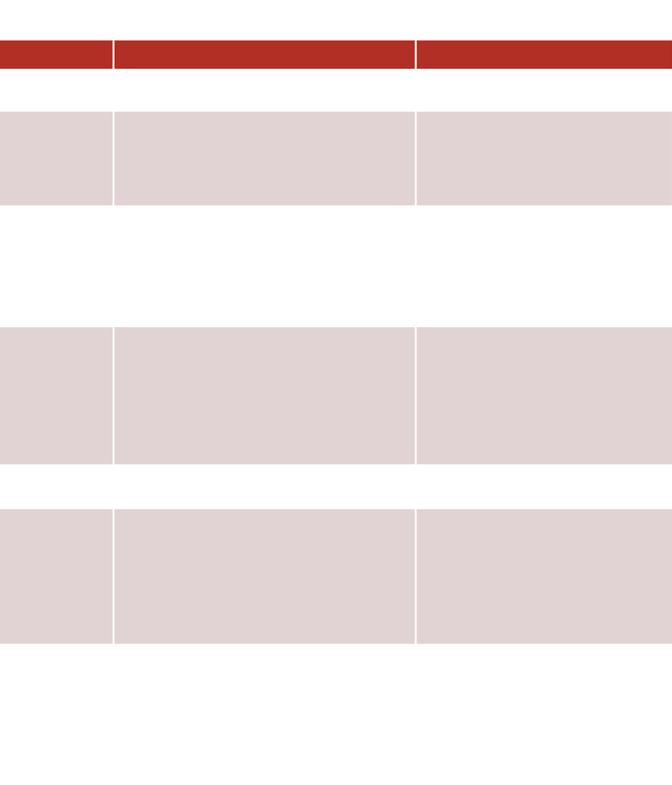
Ability to pivot to other materials or technologies In the event of a disruption, the impact will be reduced if there are readily available substitutable technologies and materials, & the supply chain can pivot to them with relative ease. Using a range of materials and technologies would reduce the supply c chain impact. Can the materials be directly substituted with alternatives? (i.e., synthetic for natural graphite) Are there alternative technologies available? (i.e., battery chemistries) Is it possible to use recycled m materials? How advanced are the alternatives?
Scale-up or conversion lead times The speed at which a supply chain can reorganise will have significant impact on the extent of the disruption & the supply chain's resilience. The scale-up & conversion times for infrastructure will be a critical element of the reorganisation. Is there infrastructure that could be converted or leveraged? Is there latent capacity or inventory that could be utilised? How quickly can new sources of supply (mines, factories, etc.) be scaled up? How r responsive is the market to price signals?
Supply chain disruptions during the Covid-19 crisis, record raw material prices and the Russian Federation’s (hereafter, “Russia”) invasion of Ukraine have raised numerous questions concerning the high dependency of many countries on imports of energy, raw materials and manufacturing goods that are key to their supply security. The solar PV supply chain is one of the most geographically concentrated supply chains globally, as China dominates raw material mining and refining and manufactures over 90% of critical inputs such as polysilicon, ingots and wafers. Key countries and regions with ambitious decarbonisation targets (including the United States, Europe and India) are therefore considering or already implementing policies to attract investment to localise manufacturing in multiple solar PV supply chain segments.
Diversification of the solar PV
Solar Vulnerabilities for Clean Energy Technologies by Supply Chain Resource Extraction Material Production Manufacturing Operation
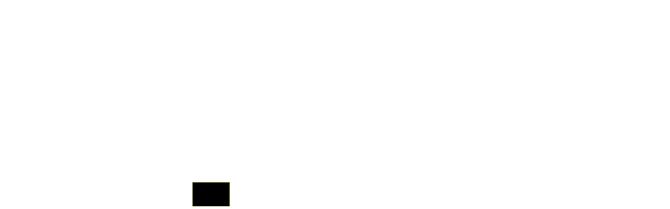
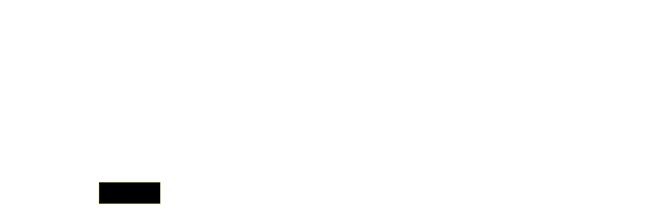
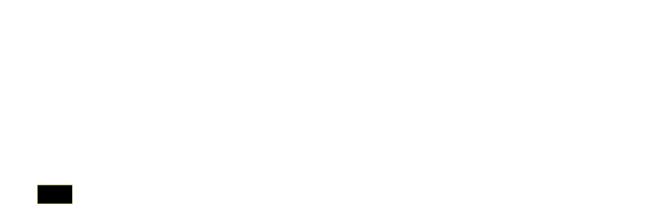
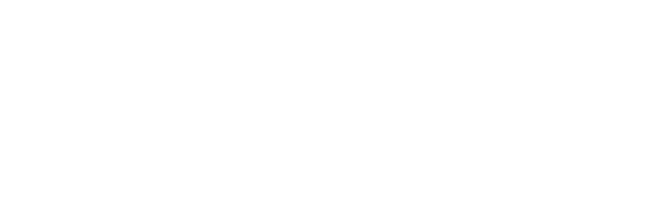
Batteries
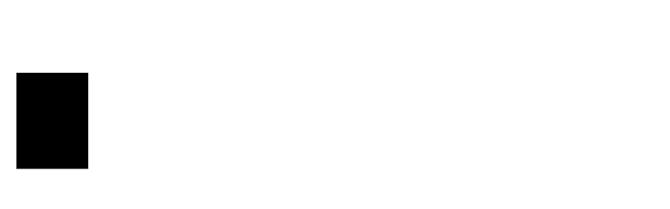
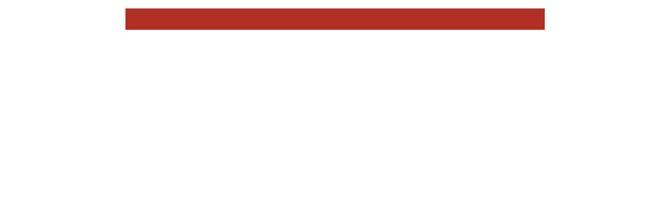
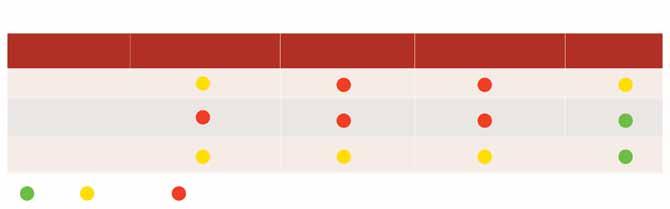
Hydrogen
Low Medium High
supply chain has both costs and economic benefits countries need to assess when designing and implementing policies. To assess these, countries should consider multiple factors such as job creation, investment requirements, electricity prices, CO2 emissions, manufacturing costs and, finally, recycling.
co2 EMission & ELEctricity pricEs:
A more geographically diversified solar PV supply chain could offer opportunities to reduce manufacturing emissions if new facilities are built in places with access to electricity that is less carbon-intensive than where current production is. At present, manufacturing modules generates far more emissions than transporting them to demand centres does. In fact, the single largest source of solar PV industry emissions is indirect emissions from electricity consumed in manufacturing. In 2021, the electricity used to produce solar panels was responsible for 89% of PV industry emissions globally, compared with just over 8% from direct consumption of fossil fuels and over 3% from transport. Thus, ambitious electricity decarbonisation goals in many countries will help reduce overall global solar PV manufacturing emissions.
However, domestic solar PV manufacturing is not always less carbon-intensive than importing from China. For example, at today’s power mixes, producing the entire supply chain in India or Australia would generate more manufacturing emissions than importing the finished modules from China. India’s solar PV ambitions for both demand and supply, supported by concrete policies, are critical for solar PV supply chain diversification and resiliency. In the short term, however, manufacturing the entire solar PV supply chain in India would be almost 15% more emissions-intensive than in China. Therefore, a compromise between total or partial self-sufficiency and lower emissions will need to be reached while high-emissionsintensity countries work towards decarbonising their domestic power generation.
Among all supply chain segments, the largest scope for reducing manufacturing emissions intensity through diversification is in polysilicon and wafers. However, maintaining competitiveness in these segments will also require that manufacturers have access to electricity at costs comparable with or lower than today’s global averages. For instance, the average price of industrial electricity is close to USD 90/MWh for polysilicon and wafer production. In India, new polysilicon or wafer production may be more economically challenging than in other countries in the region due to higher industrial electricity prices (USD 100/MWh). While industrial electricity prices in China are in the range of USD 60-80/MWh excluding subsidies, which enables cost-competitive manufacturing in many provinces.
inVEstMEnt cost:
High investment costs for polysilicon and wafer manufacturing challenge the business case for projects outside of China.
The amount of initial capital needed to establish a solar PV manufacturing facility varies significantly by country/region, type of equipment used, and costs associated with land, construction and financing. A manufacturing facility’s size has a direct impact on the economies of scale that can be realised, affecting investment per megawatt. According to recently commissioned plant and equipment price data, polysilicon plants and ingot and wafer factories are significantly more CAPEX-heavy than cell- and module-manufacturing facilities. In addition, because of the considerable infrastructure investments needed (USD 200-400 million), Greenfield polysilicon plants are not usually bankable for capacities of less than 10 000 Mt (around 3 GW).
For polysilicon, ingot and wafer manufacturing, benefitting from economies of scale is crucial to realise lower per-megawatt investment costs. Recent Greenfield polysilicon plants in China range in size from 40 000 Mt to 100 000 Mt, almost tripling historical averages.
Investment costs in the United States, the European Union and India are three to four times higher per megawatt than in China and ASEAN countries for polysilicon, ingot and wafer production. Longer construction and development timelines, considerable labour and material costs, the
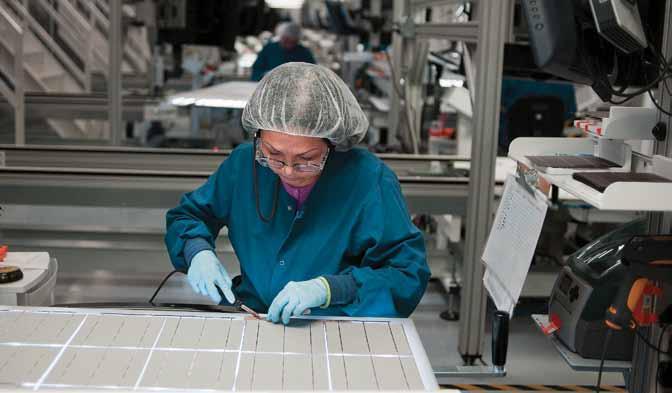
Quality Inspection of Solar Laminate // Image Courtesy: SolarWorld USA
higher cost of capital, a lack of economies of scale and a dearth of knowhow in developing megascale PV manufacturing facilities remain key reasons for higher costs. For instance, experience in developing large-scale ingot and wafer manufacturing facilities is very limited outside of China, as the country holds over 95% of the market share.
MAnufActurinG cost:
Manufacturing cost parity across regions and countries is critical for solar PV supply chain diversification. While cost differentials dictate whether a country’s solar PV products are cost-competitive, they are also critical for policymakers to design policies that effectively support the solar PV sector, including manufacturing plants. Solar PV production costs currently vary widely across both components and locations.
Based on modelled assumptions for each supply chain segment, the total cost of producing modules in key countries and regions varies from USD 0.24/W in China to USD 0.33/W in Europe, excluding profit margins, taxes and transport fees.
Relatively low energy and investment costs (which lead to lower depreciation costs) and inexpensive labour make China the most cost-competitive location to manufacture all components of the solar PV supply chain.
Large variations in energy, labour and depreciation inputs (due to relatively high investment costs) make PV manufacturing 9% costlier in India and around 20-35% more expensive in the United States, Europe and Korea.
Thus, diversifying solar PV manufacturing will depend on the ability of nascent and new markets to match the cost efficiencies evident in China. For instance, realising economies of scale and integrating plants and processes can reduce variable costs to increase competitivity.
JoB crEAtion:
Job creation is one of the main arguments for expanding domestic manufacturing of any product, as many governments consider manufacturing jobs to be sustainable. Thus, given solar PV’s critical role in the energy transition and its job creation potential, it is a key industry for the global expansion of manufacturing jobs.
For policymakers, the job intensity of various solar PV supply chain segments can be an important factor, especially when designing incentives to support the manufacturing sector. For instance, according to estimate that producing 1 GW of c-Si solar module capacity per year could create as many as 1 300 full-time manufacturing jobs, covering polysilicon, ingots, wafers, cells, modules and other materials such as glass, backsheet and EVA. The most job-intensive segments along the PV supply chain are module production (requiring 600900 jobs) and cell manufacturing (450-650 jobs).
PV manufacturing requires a diversity of workers, including production engineers, material handlers and assemblers. Due to the current geographical concentration of the solar PV supply chain, the majority of skilled personnel is based in China and Southeast Asia, so diversification will require
»
a concerted effort to train new employees. Thus, any strategy to increase PV manufacturing capacity must include a workforce training component. While governments and employers have already introduced training programmes for new employees, training must be co-ordinated and scaled up to provide the amount of labour needed to secure investment in local manufacturing facilities. There is not currently enough trained labour for PV manufacturing, especially in small or emerging manufacturing markets, given the low amount of job opportunities available.
rEcycLinG:
Solar PV modules currently have an estimated average service lifetime of 25-30 years, after which time their performance can deteriorate and they can be subject to failures. Considering historical capacity additions, we estimate that the global cumulative flow of decommissioned solar PV capacity will reach around 7 GW by 2030 and could increase to over 200 GW by 2040. This represents 400-600 kt of embodied materials cumulatively by 2030 and 11-15 Mt by 2040. As setting up effective policy frameworks and value chains can take time, it is crucial that governments, industries and other stakeholders prepare now to manage the future surge of solar PV waste from a systemic, circular-economy perspective.
Manag ing end-of-life (EoL) flows of solar PV equipment is an environmental challenge. In addition to contradicting circularity principles, putting PV panels in landfills can cause environmental pollution and health issues due to the presence of hazardous materials such as lead. In this context, the benefits of recycling are manifold: it provides not only an alternative to land filling, but also the pportunity to recover valuable elements and secure a reliable secondary source of raw materials for the PV industry and other sectors.
Furthermore, because it provides a domestic supply alternative, recycling can alleviate energy security concerns for countries heavily dependent on imports. It also helps avoid negative environmental, social and health impacts associated with raw-material mining, and can reduce the energy and environmental footprint of solar PV. Moreover, reconditioning and recycling can generate employment opportunities and support local economic activity.
Last but not least, in addition to recycling, circular approaches aimed at improving solar PV designs for reuse, enhancing product longevity and developing remanufacturing will be pivotal to diversify the solar PV supply chain and shrink its environmental footprint.
concLusion:
A country’s policy and macroeconomic environment is critical to attract investment in manufacturing facilities for any industry. For solar PV, governments worldwide have implemented multiple policies and incentive schemes, with varying success. In simple terms, solar PV manufacturing policies can provide direct support to man-

Cost of imported modules, including overseas shipping, vs domestic modules, 2022

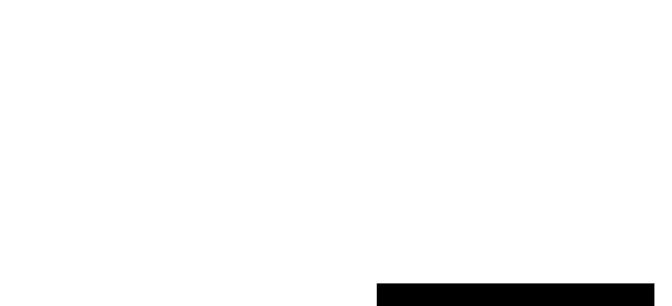
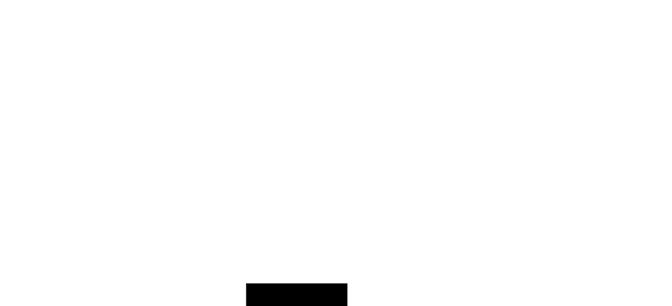
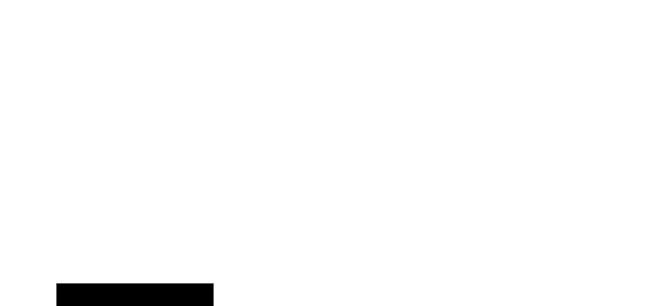
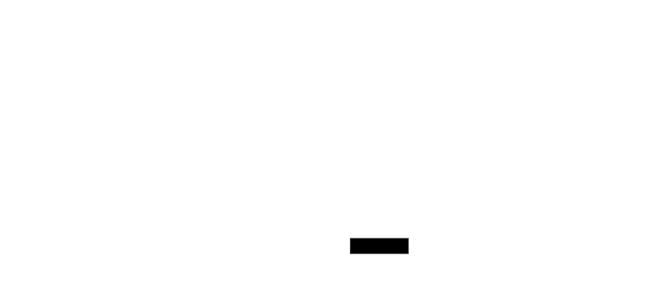
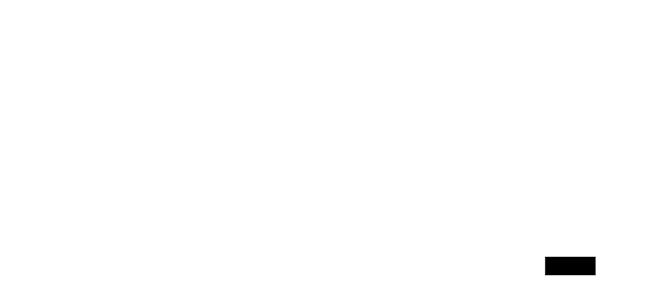
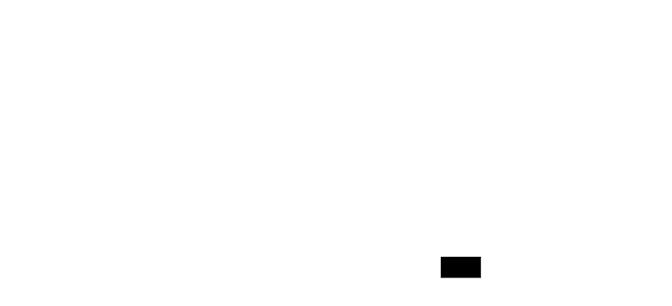
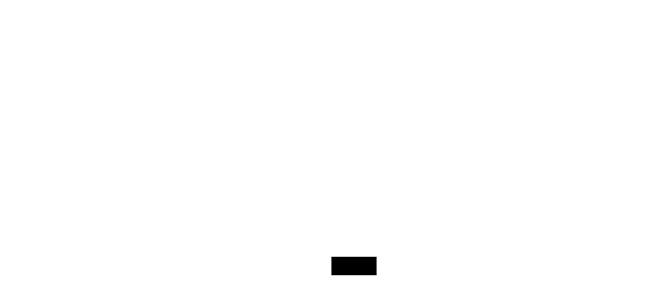
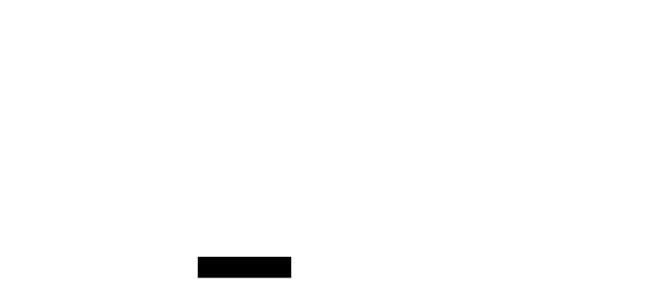

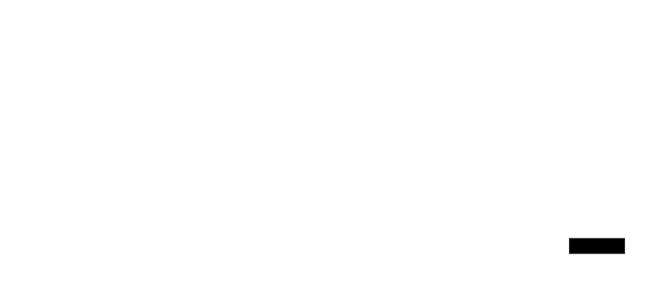
0.40 0.35 0.30 0.25 0.20 0.15 0 0.10 0.05 0.00

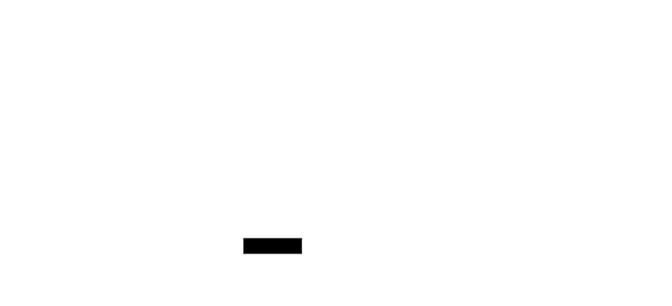
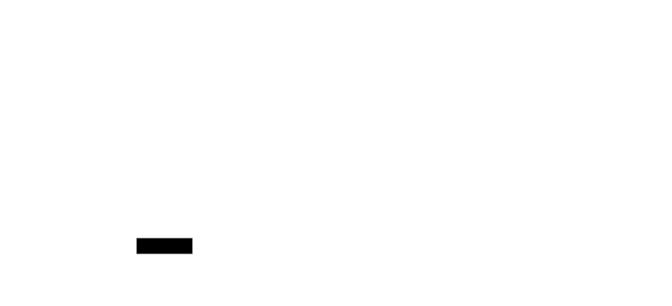
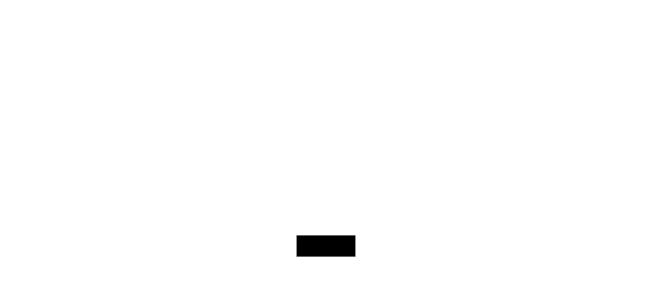
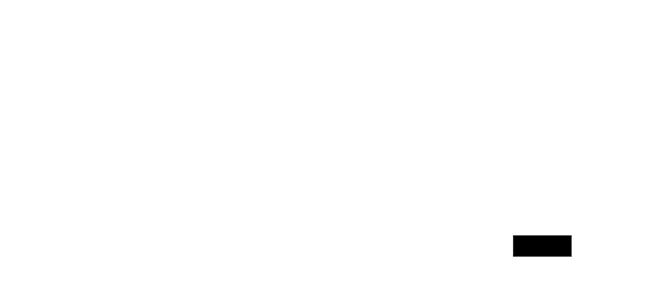
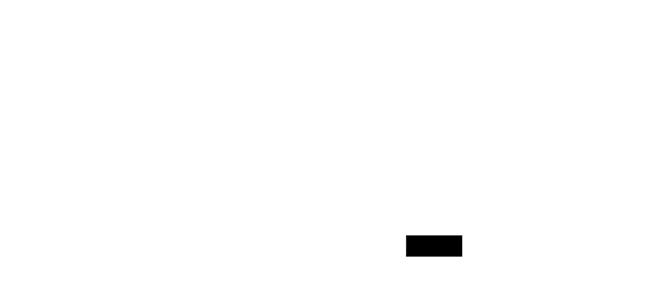
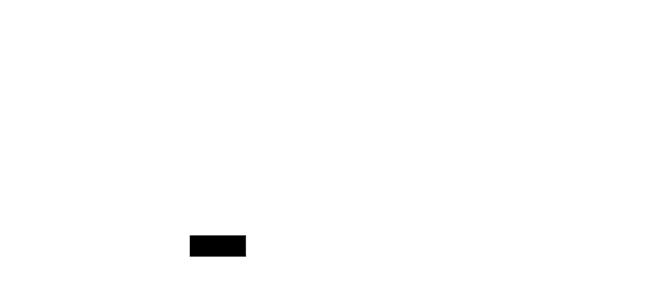
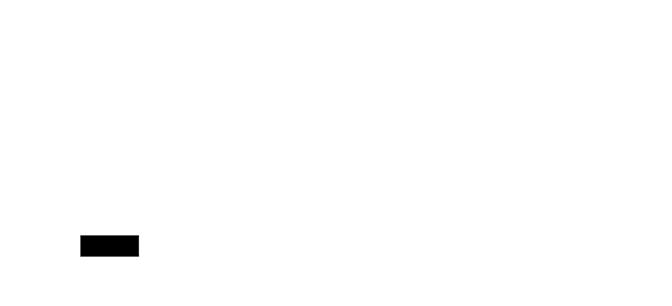
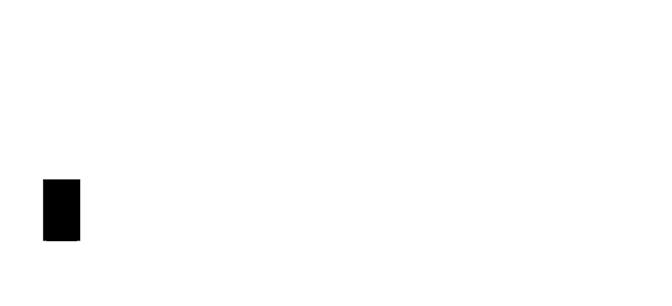
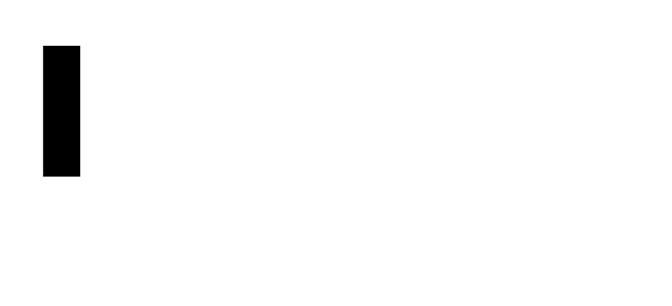
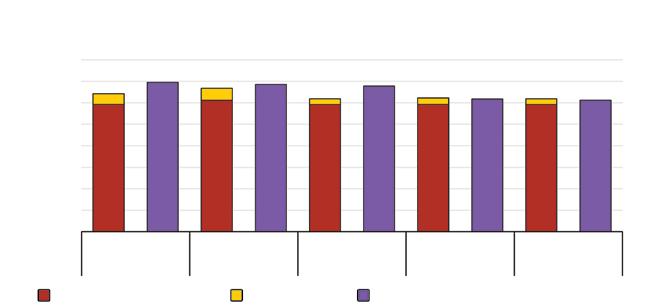
Imported Domestic Imported Domestic Imported Domestic
Imported Domestic Imported Domestic Europe United States Korea India ASEAN Imported module costs Shipping costs Domestically manufactured module costs Reference: IEA Special Report on PV Solar Global Supply Chain
ufacturing investors, or they can indirectly stimulate investments by creating an attractive investment environment. Support policies can be applied on the supply side (upstream) or the demand side (downstream), through four possible combinations described below.
dirEct:
i Manufacturing tax credits for one or multiple solar PV supply chain segment manufacturing facilities. i Grants for one or multiple solar PV supply chain segment manufacturing facilities, including to cover land and infrastructure costs. i Low-cost financing for greenfield solar PV manufacturing facilities, or for their expansion or operation. i Lower energy prices for energyintensive PV manufacturing facilities. i Lower income tax rates for solar PV manufacturing companies. i Lower import tariffs and VAT rates for imported manufacturing equipment. i Government funds to reduce labour costs through lower charges. i Incentives for to exported goods manufactured domestically. i Local-content requirements for domestically manufactured equipment attached to policies to stimulate solar PV demand. i Solar PV power plant auctions/ tenders linked to commissioning new manufacturing facilities.
indirEct:
i Import tariffs or trade duties to raise the cost of imported solar PV equipment and related products. i Import bans on solar PV products not meeting certain sustainability standards or regulations, to set standards for imported PV equipment. i Border CO2 tax adjustment for imported solar PV products. i Carbon footprint standard for modules in tenders. i R&D and innovation funds, or funds for academics and the private sector to develop solar PV technologies. i Tax incentives to employ highly skilled labour for R&D. i National or sub-national funds to educate skilled labour for solar PV manufacturing. i Government investment to upgrade infrastructure, including for logistics, waste management and power, including industrial clusters. i Policies to stimulate domestic solar PV demand (tax credits, FITs, auctions). i Local-content premiums for domestically manufactured equipment attached to policies to stimulate solar PV demand. i Low-cost financing for domestically manufactured equipment attached to policies to stimulate solar PV demand
PODCAST
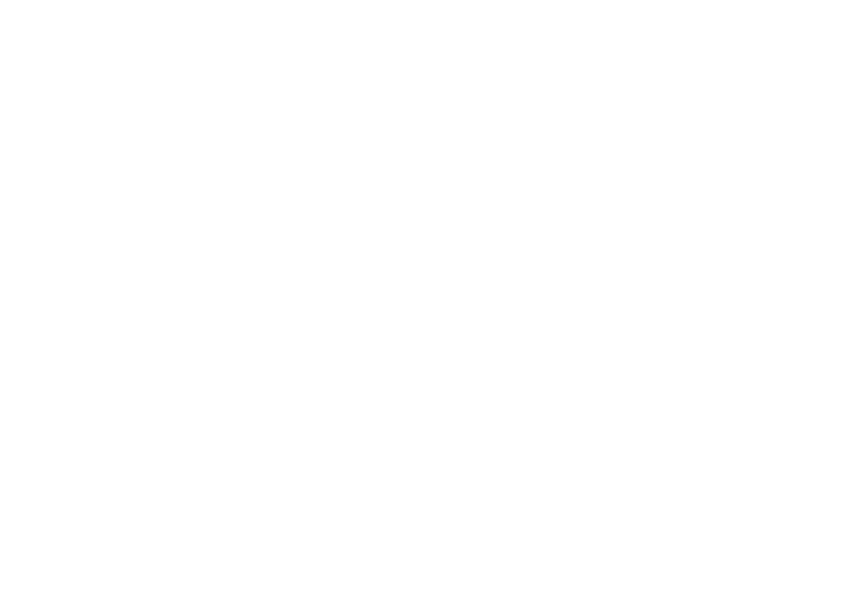
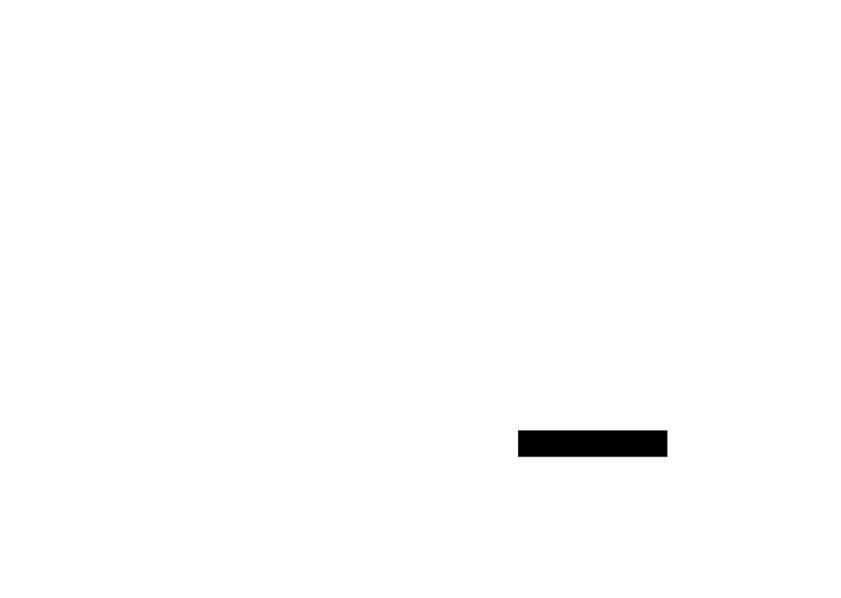
Atrendywayto getupdatesfrom thecleanenergy &e-mobility industry
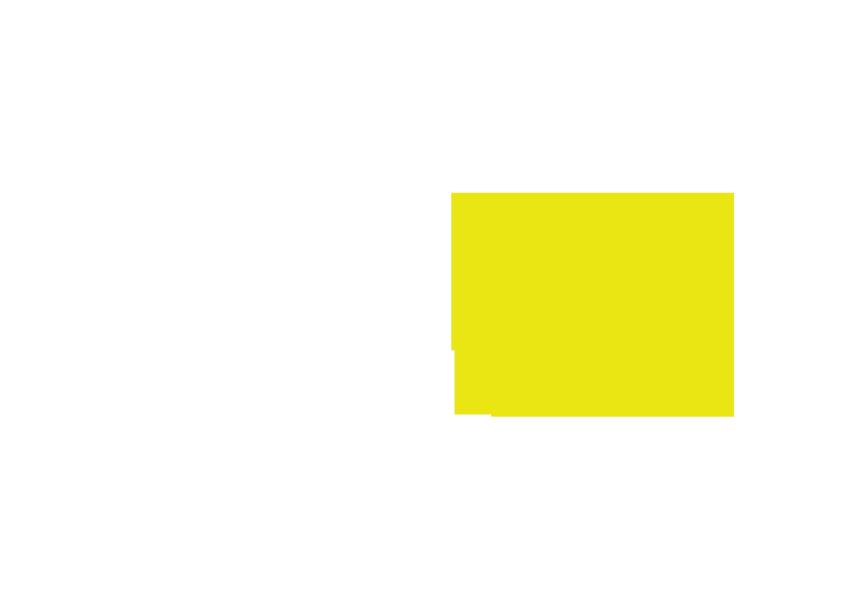
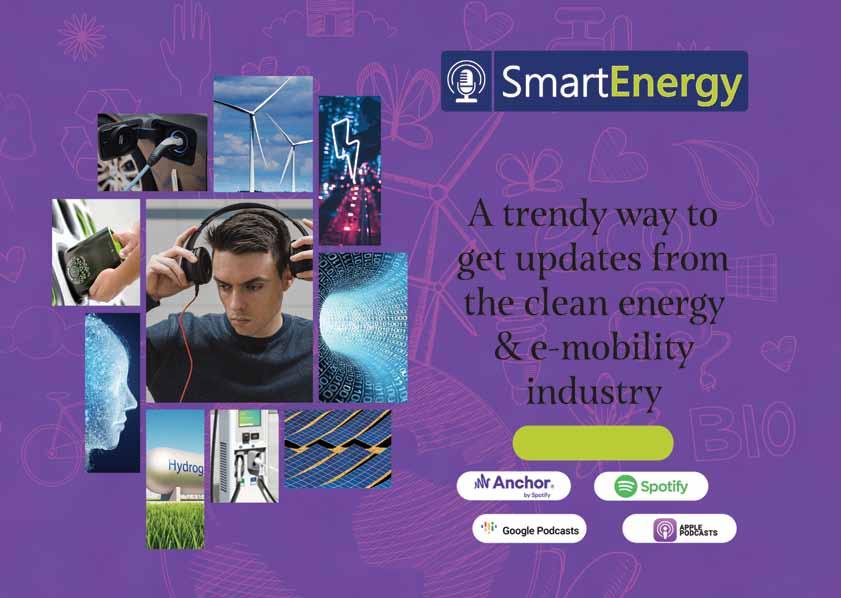
AVAILABLE ON
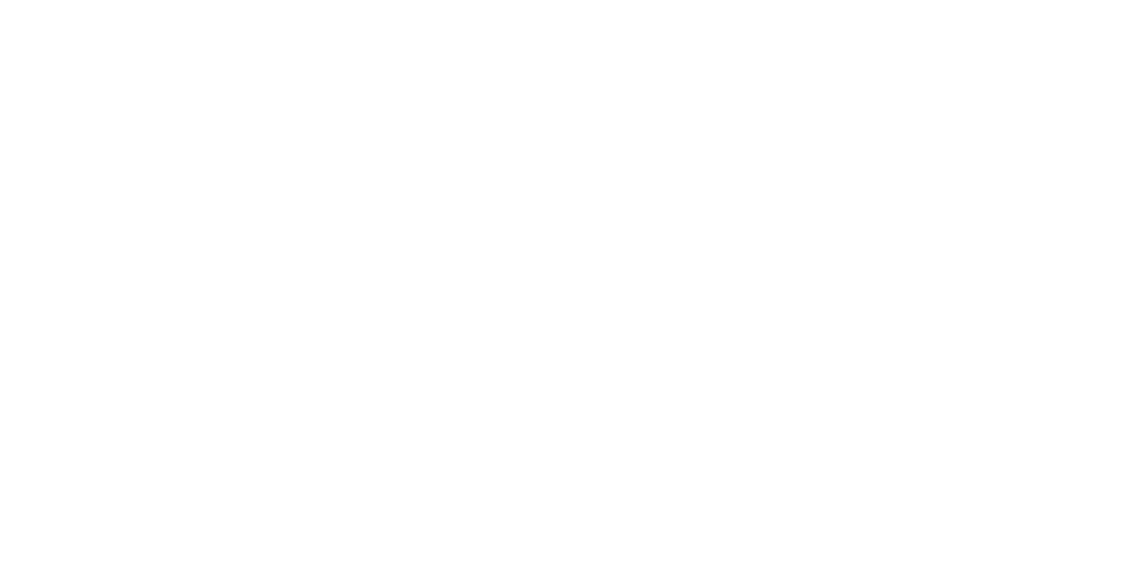

the Mighty Srav

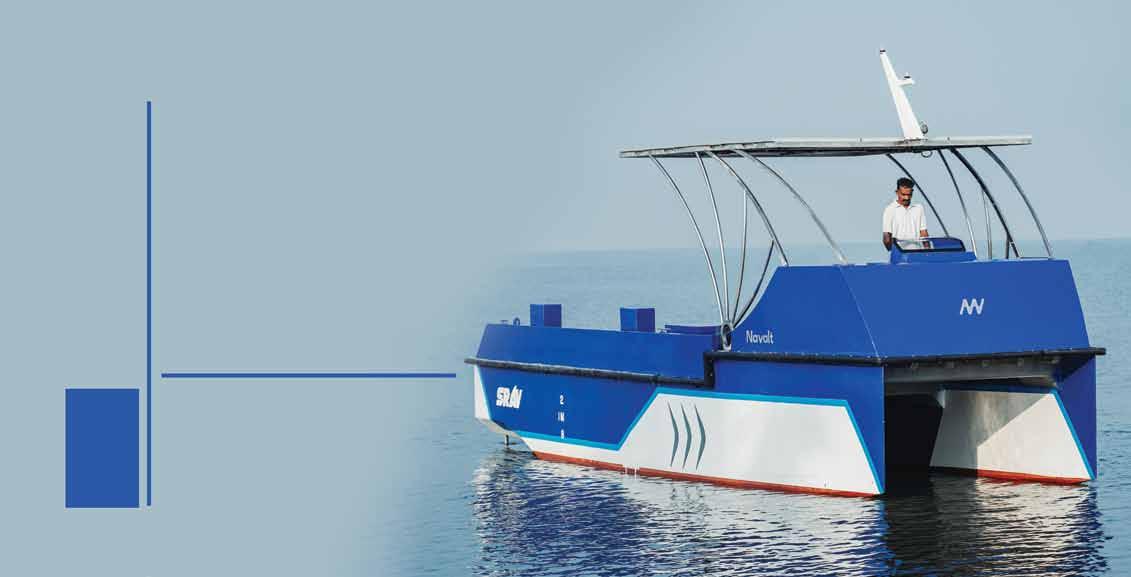
A vessel one step closer to the Dream Ocean
We live in a continually developing world. Technological advancements have brought everything to the tip of our fingers, our methods and routines have refined but life still remains the same for one community. The magnificent sea hullers, the rowing and constant tiding of those who bring the sea to life. The fishermen! All across the shores of India, fishermen live a life of constant turmoil. They are exposed to the raging heat and polluting gases emitted by the boats they use; they have to withstand the continuous pulsating and treacherous vibrations of the boat and are still at the mercy of the mighty seas, hoping it gives them back something to take home.
To put an end to this suffering and pen the story for a more sustainable future, last year Navalt came up with an innovation to gift them a boon that would change the course of their lives forever – The mighty Srav. A solar electric catamaran sea-going fishing vessel designed to revolutionize the fishing industry and to upgrade the life of those who are a part of the fishing community. Powered and mechanized by the sun, the Srav is the world’s first solar electric fishing vessel, the winner of the 2022 Gustave Trouve award in the best electric workboat category. Approximately 100 million marine animals die each year due to water pollution. The harmful gases, carbon dioxide, and spillages emitted from fishing boats pose a great threat to the sea and its living beings. If fishing vessels were their own country, they would be the ‘6th largest’ carbon dioxide contributing country in this world. Apart from creating a negative impact on wildlife, the boats also cause a lot of noise pollution, motor discharge, emittance of toxins, and navigational hazards. The animals that cruise through the sea borders are also highly affected by the pollution that is caused by motor boats. The excessive nutrients that are emitted into the water increases the growth of toxic algae and exotic plants, causing deep sea corals to die and sea turtles and mammals to develop an oily coating on their shells. Humans who consume the fishes can develop congenital disabilities resulting in slow development, immune suppression and reproductive problems. All of
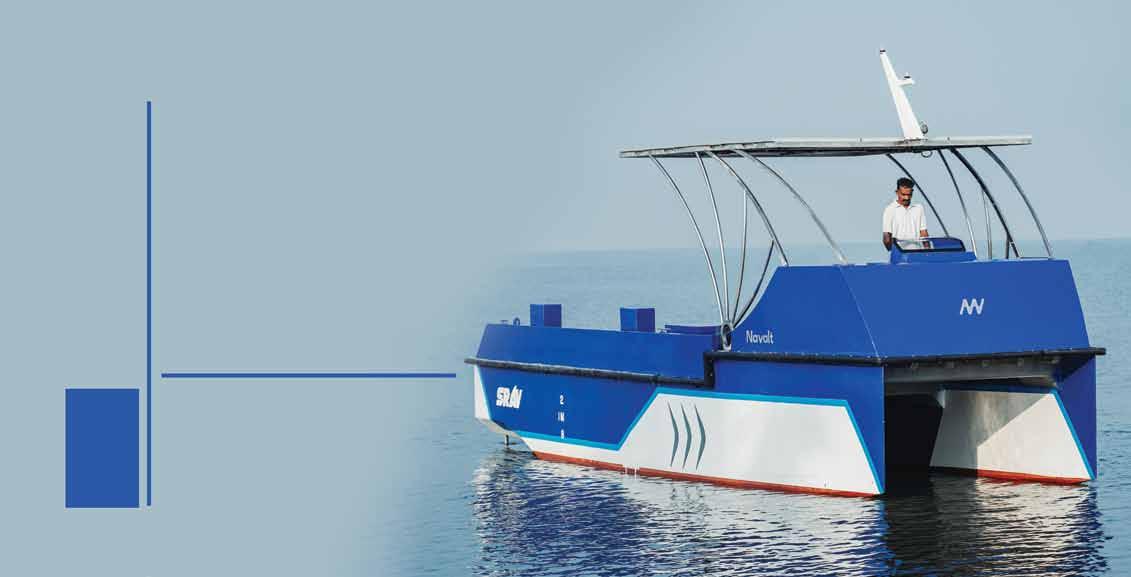
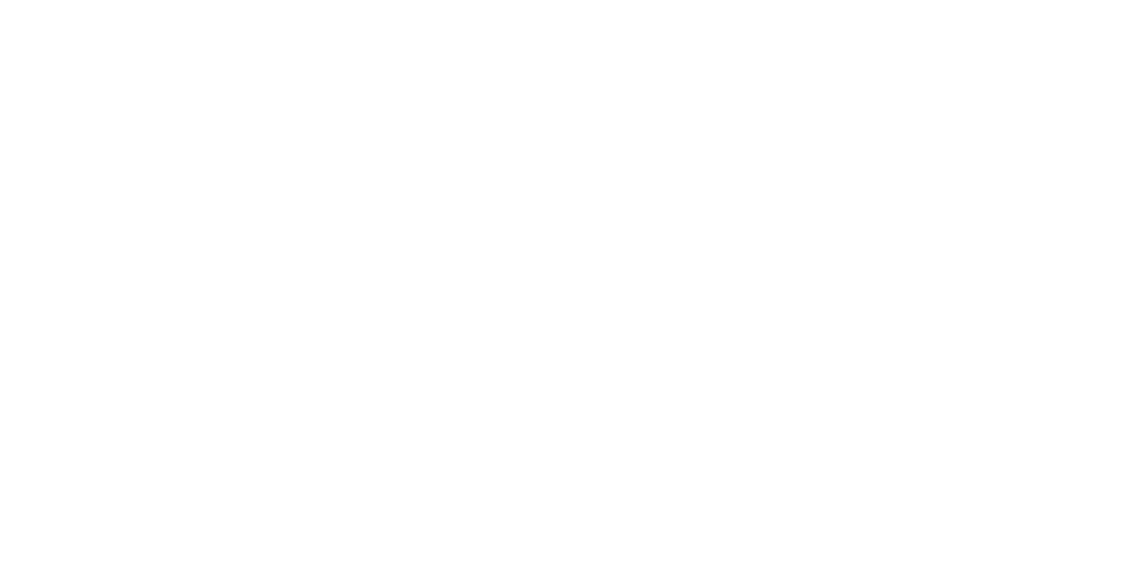


these are problems induced by the functioning of boats which emit diesel and other harmful fuels into the water.
To revolutionise the fishing industry and introduce a greener solution for the community, Navalt introduced the Srav in 2022. Srav aims to completely wipe out the emission of any fuels into the water, switching to an absolute greener solution. Powered by the sun, this solar electric fishing vessel requires no fuel to operate hence avoiding any carbon emissions into the atmosphere. The fishermen who are exposed to the constantly burning fuel complain about the foul odour that they have to tolerate on a daily basis, and when it comes to Srav there is no such thing as fuel odour as it runs solely on a solar powered battery. While a petrol or kerosene boat would emit close to 9 tonnes of CO2 every year the Srav wouldn’t be emitting any harmful gases into the atmosphere or causing any pollution. The yearly fuel import savings tend to have a great impact on the future. The decrease in amount of carbon dioxide is nearly close to that absorbed by 2 crore trees every year.
While fishes are categorized as hearing specialists and they use sound to communicate both actively and passively in the environment. The underwater noises caused by boats interfere with the basic motor functions of these marine mammals, impairing their sense of hearing, eliciting aggressive reactions or causing psychological stress. The aquatic life will always remain vulnerable to hearing loss when they are exposed to such intense vibration and they also require time to fully recover from this exposure. Srav is the ultimate solution to this problem as it’s silent motor and vibration free design yields an excellent noise free performance.
With a capacity to accommodate 3 crew members, a speed of 8 knots and 70 km range the Srav uses marine grade LFP batteries and solar panels to charge them. While the Srav definitely helps to fish in a more efficient and smooth manner, the biggest catch is the fact that the fuel expenses are completely nullified, with an even greater amount of decrease in the daily operational expenses. Instead of choosing to invest in a single petrol boat, opting for four Srav’s with the same investment would generate an even greater revenue in comparison. This catamaran designed for fishing is an architecture marvel as it embodies the literal translation of the Malayalam word Srav which means ‘Shark’. The boat, like the shark has a perfectly shaped gliding body, fins and teeth to help it transition through the water in a smooth manner. The sharks are known to be an ocean’s top predators, and the Srav embodying this marine animal is a more environment friendly option for all the fishermen communities in India.
In the impending future if the Indian government decides to completely switch to solar electric fishing vessels it will be able to save nearly 31,0000 crores on fuel imports. Replacing the present fuel boats are replaced with solar electric counterparts is also another option. While this will help reduce purchase of fuel altogether helping save a lot of money, it also paves the way to a greener and better tomorrow.
The mastermind behind this genius innovation, Navalt – is an eco-marine technology company that specializes in the manufacturing of solar electric vessels. At Navalt, we have always pushed the boundaries when it comes to designing extraordinary vessels. They have over 21 years of experience, and their boats have safely and successfully transported close to 2 million people. Keeping in mind the motto of creating ‘cleaner and quieter’ oceans, they have risen to become India’s only indigenous, electric propulsion system builder and constantly continue to push to become the world’s best solar electric vessel builders for private or public transport. Our Marine data science division named Oceanix, harnesses the best of fishing industry expertise and combines it with data analytics to provide, data driven decision – making opportunities for ship owners. As of today, this company with a greener and cleaner solution in mind has over 1500 shipping vessels in our platform for the largest shipping companies worldwide and is pushing the boundaries when it comes to electrifying the ocean!
This article is contributed by Navalt Solar & Electric Boats Pvt. Ltd., a Kochi based company specialising in manufacturing of solar electric vessels. Navalt’s flagship solar electric ferry, ‘Aditya’, is recognised as the world’s best.
Himanshu Jadhav
CEO & Director, Jendamark India Pvt. ltd.
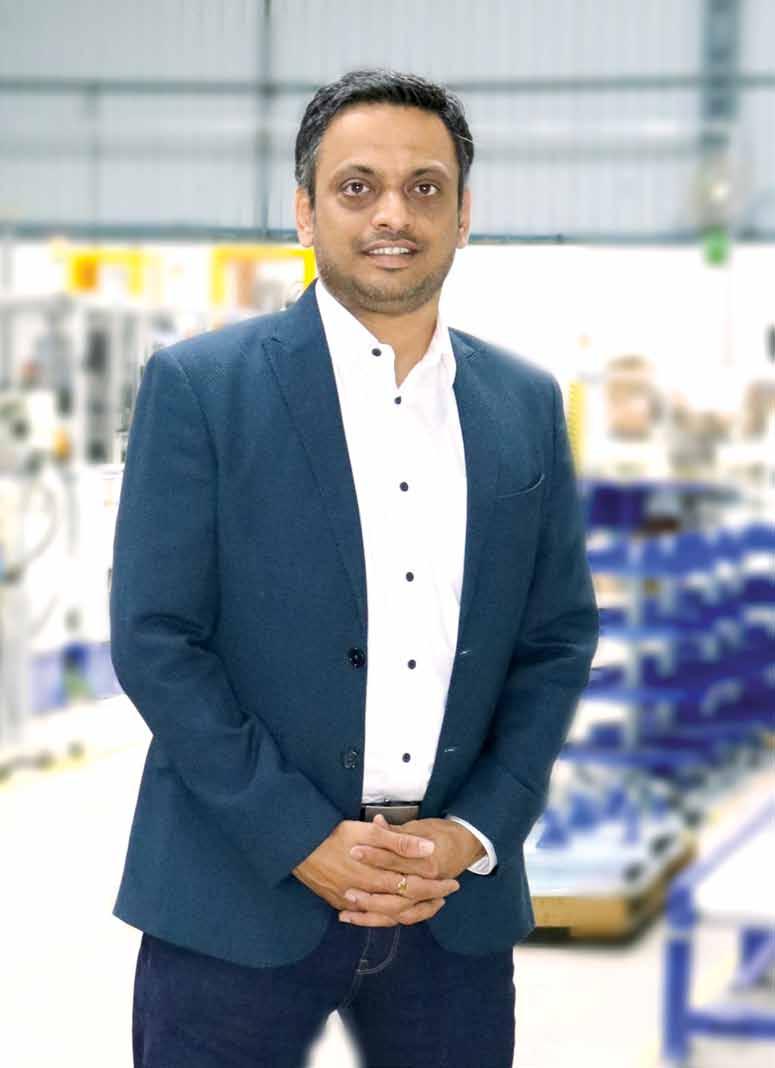
Q.to begin with, before we dive deep into the world of technology and digital transformation or industry 4.0, can you take our listeners though your earlier journey that is before you joined Jendamark?
My journey is of typical middleclass family origin whereas we all have experienced education is of prime importance. Obviously, in my family, as I grew up as well, a lot of emphases was laid on education, getting the right education competitively as well. So with that mindset, I excelled in my studies and followed it up with engineering in Mechanical, where I was lucky to get selected in one of the first batches of GETs (Graduate Engineering Trainees) which
got me recruited by Tata Motors from my college. After a stint of almost five years at Tata Motors, I joined Volkswagen. After 8 to 9 years at Volkswagen, I decided to join Jendamark in 2016. So, over the entire journey from my schooling till now I have been blessed to have good influencers and well-wishers who have supported me in this journey till date and I am quite thankful for all those individuals who have shaped where I am today.
Q.from leading and growing the company to creating a brand identity for an unknown company, how would you sum up your journey at Jendamark?
Jendamark was an unknown company in India but globally it was quite well know and established brand providing automation solutions worldwide from South Africa to Europe, US and rest of the world. It was only in India that it was a bit of unknown company. My discovery with Jendamark started when I visited South Africa in 2010, that's when i came across
this wonderful guys from Jendamark in South Africa who where very open, honest, transparent, hardworking, which resonant with my way of working and thinking as well was. That's how my association grew with Jendamark and for almost six years we were working together. But, I was part of volkswagen then. In terms of summing up my journey with Jendamark so far, it's been extremely exhilarating, hustling, purposeful and more importantly I think it has given me an opportunity to broaden my meaning and definition of life and what I would like to do in life in general. Of course, we all are tech companies provinding technical solutions but on a higher level we are getting a lot of purpose and I feel I have found a purpose in lot of things which I am doing with Jendamark. There were some lessons, there are always ups and downs but overall the purpose and the intent has been really amazing to work in Jendamark.
Q.Jendmark is recognised as a pioneer of industry 4.0 revolution in india, can you brief our listeners about the different products and solutions that you offer and the different industries you cater to?
We are known as the pioneer of the industry 4.0 revolution in India primarily because of our approach to industry 4.0 in general. We have what we proudly claim is a humancentric approach in Industry 4.0, which is what is a distinguishing factor between the solutions offered by Jendamark and by the other players in India. We are a country with an evergrowing population, and our dynamic and socioeconomic problems are all revolving around the human capital that we have. As much as we feel and we would like to have automation as a mainstay, we cannot and should not oversight the power of individual humans and what it brings to the table. That's why we have devel-
oped a suite of products under the brand name ODIN which are enabling, energizing and increasing the efficiency of humans involved in the manufacturing sector to start with. We are open to any industry. Primarily we are focusing on the automotive sector, but to be honest the manufacturing sector at large be it the pharmaceutical sector, white goods, bottling plants or anything which involves manufacturing, our product suite of ODIN is well received in all these industries.
Q.As i understand, Jendamark’s primary business comes from the automotive sector, how is Jendamark catering to the needs of the emerging sector like EV?
Innovation is the only way in which we can provide solutions for an emerging sector like EV and ESS. We have provided battery pack lines, motor lines, inverter lines, e transmission etc to many customers over the last 3 to 4 years. We have realised the challenges the emerging EV sector faces and that providing only automation solutions or equipment is not going to solve their challenges. There is a range of variables, some companies want a low-cost, lowvolume solution. While, Some companies want high-volume, highly complex solutions. What we have kept consistent across the entire range is our process security for making this product for our customers and this process security is one of the key factors and differentiators in our offerings. We also understand the financial challenges which come up with an emerging sector like EV. To address these challenges, we have come up with various financing models like software on license model, we also have the option of leasing the line and equipment. These kinds of licensing and leasing models allow a bootstrap company to have low costs in the initial phase. What we have realised is that these companies are innovative companies that have developed good products but the initial investment is a bit of an issue for them. These licensing and leasing models allow them to focus on their main stay which is R&D and product and not worry about financing. As the product grows, as the volume comes in automatically the sales will result in better finances. That is our contribution to these bootstrap companies. From our experience internationally and locally and our expertise in setting up factories, we are happy to consult any company in EV specifically on how to go about setting up an EV factory. So, it is not all about just providing assembly lines and machines. It’s solving the financial issue, and consulting them on setting up EV factories and that is what we are focusing on as a wholesome solutions provider to our customers. .
Q.We are seeing a lot of policy support, push and customer preference towards adoption of EVs, how do you see the EV sector in india and going forward what are the opportunities in the EV sector that you at Jendamark are getting ready for?
The EV sector is here to stay and grow. What we are experiencing is a big transition. In a span of 20 to 25 years, even fuel prices have gone up by six times which is an indicator that it is not going to slow down. Apart from that, the pollution factor which the IC vehicle brings in also needs to be
addressed. What we need to work on is creating renewable energy to power EVs. From Jendamark's perspective, we are a very vocal-for-local company. We are focusing on Innovation and R&D and we have a dedicated R&D department globally working on making innovative solutions which are otherwise imported from Europe, the US or China. We are working on making innovative local SPMs catering to the EV industry. Another topic that we are working on is lowering the lead time to delivery. Because time to market in EV is key to success. There is a lot of challenges involved in lowering the lead time due to the uncertain supply of electronic goods because of semiconductor and chip shortage issue. But, we are trying different solutions to enable us to cater to that challenge and solve it successfully for our customers.
Q.in addition to manufacturing of EVs, we see a lot of opportunities that are coming up in the stationary and EV battery business, what would you advise to the entrepreneurs that are looking to enter into or traditional led-acid battery manufacturers diversifying into lithium-ion battery manufacturing/ assembly business?
It is a good opportunity for sure, but be cautious about your product. I think engineering & R&D is a key ingredient which is going to be the only way forward and only those companies who have a focus on developing their own product will be sustainable in the market in the coming years. Companies who are looking for quick turnaround, importing and selling stuff in India already are seeing problems because the government has tightened a few measures. The new policies coming from the government to make EV safer with the AIS 156 and its amendments. All of this only means that the companies that have sustainable, strong products will remain and the rest will perish. From an assembly point of view, securing a good supply chain and more importantly having state of art assembly line solutions to assemble the product in the right way is essential. Many solutions are coming from other countries that are not sustainable. You have to look at a sustainable manufacturing assembly line solutions provider who can support you over the next decade or so.
Q.share your experience of working with hero yamaha corp where Jendamark has delivered high volume E-cycle assembly line for the company? What were the challenges in delivering this project and how did you overcome the challenges?
It was a very exciting six months project. It was a record even for us to deliver a high-volume e-motor line for the Hero Yamaha JV. The challenge was with parallel product development. The product was getting developed and at the same time, we were developing the line that too is delivered in the shortest time. The deadlines were strict and straight. We had to have the plant opening along with our line and the component being made on our line on 15th Dec 2022. We had a very clear directive of what we wanted to do. The team put together by Jendamark was fantastic team, we choose guys who loved and thrived in these challenges. That's what differentiates Jendamark from the people aspect as well. We also got fantastic support from Hero Motors and Hero Yamaha team working with us on our floor. They were more like our partners working with us, staying with us, sleeping on the floor with us and delivering together a very successful project for their company and us as well. Our partners and suppliers also stood up to the challenge to ensure that we get what we want in time. Overall it was a very good team effort from everyone to deliver a world-class soluton to Hero Yamaha Motor Corp.
Q.How would you define success for yourself and your company? Where do you see Jendamark in the next 5 to 10 year?
Six years back when I joined Jendamark if someone told me that this is where we would be in Dec 2022, I would have not believed him or her. We are an evolving company even now. We think like a startup and work like a startup. This comes from the DNA of the company which always hassles. We always hassle and thrive in situations that are challenging. We venture into the area where most people do not venture because the risk is too high. But, where there is a high risk that's where the opportunities lie as well. In terms of success, we are not here to just get bigger, but we want to get better and while getting better we also want to get bolder. Getting bigger, better and bolder is what success is for me and is a continuous process. As we grow bigger, we will get better, we will get bolder and that for me will be an ultimate definition of a successful journey in this process
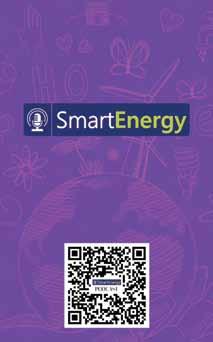
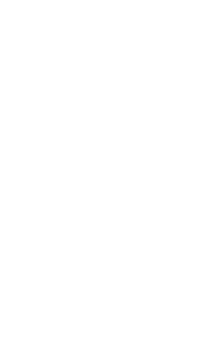