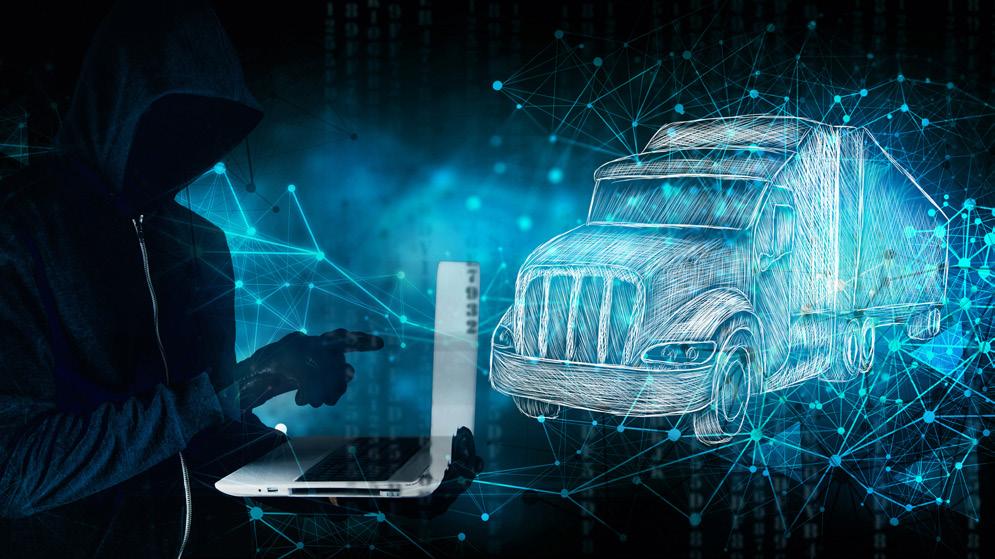
16 minute read
FOR STARTERS BY MARINA MAYER, EDITOR-IN-CHIEF MITIGATING CARGO THEFT IN FOOD DISTRIBUTION
Earlier this month, I presented at PLM TrustLink’s Food Distribution Summit in Naperville, Ill. Flanked by industry greats such as Amber Engebretson, supply chain Center of Excellence senior manager for Chipotle; Bridgette Blitch, a legal expert on food safety regulations; and Liz Sertl, senior director, community engagement at GS1, I used my 30-minute timeslot to talk about safety and security in food distribution…. namely, cargo theft.
For those of you who have not experienced cargo theft yet, consider yourselves lucky. That’s because cargo theft in the food distribution space is a really big deal.
In fact, according to TT Club, the food and beverage industry experienced the most cargo theft in 2022. Think about that. In relation to theft of semiconductors, pharmaceuticals and other forms of product theft, food and beverage topped that.
But, it’s not just the product itself being stolen.
Events that involved theft of at least one heavy commercial vehicle such as a semi-truck or semi-trailer increased by 17% year-over-year, according to a CargoNet study, and the average value of cargo stolen in an event was $214,104, equivalent to an estimated $223 million in cargo. To put that into perspective, 98 trucks and 119 trailers were reported stolen in one quarter.
Increased theft activity around major intermodal hubs was also a big thing in 2022, with California remaining the top state for reported events in 2022. Meanwhile, theft in Georgia increased by 34% year-over-year, due in part to organized crime groups that took advantage of increased traffic to the Port of Savannah.
And, think about those fake Facebook profiles that try to become friends with you. Fictitious pickups act in the same way. CargoNet recorded 96 more fictitious pickups in 2022 compared to the year prior, a 600% increase year-over-year.
According to TT Club, carrier fraud accounted for 84% of claims involving fraud or deception in 2022.
Even though many of today’s U.S. and global cold food chains continue to face the same threats they’ve been facing the past 2-3 years, understanding and overcoming such threats will help companies achieve some stability.
EDITORIAL
Editor-in-Chief Marina Mayer mmayer@ACBusinessMedia.com
Managing Editor Alexis Mizell-Pleasant amizell@ACBusinessMedia.com
Associate Editor Emry Lloyd elloyd@ACBusinessMedia.com
AUDIENCE
Audience Development Manager Angela Franks
PRODUCTION
Senior Production Manger Cindy Rusch crusch@ACBusinessMedia.com
Art Director .................................................................... Willard Kill
ADVERTISING/SALES
Brand Director Jason DeSarle jdesarle@ACBusinessMedia.com
Sales Associate Brian Hines bhines@ACBusinessMedia.com
Account Executive Jay Gagan jgagan@ACBusinessMedia.com
Account Executive Paul Petterson ppetterson@ACBusinessMedia.com
AC BUSINESS MEDIA
Chief Executive Officer Ron Spink
Chief Financial Officer JoAnn Breuchel
Chief Revenue Officer Amy Schwandt

Chief Digital Officer Kris Heineman
VP, Audience Development Ronda Hughes
VP, Operations & IT .................................................. Nick Raether
Content Director ..................................................... Marina Mayer
Director, Online & Marketing Services Bethany Chambers
Content Director, Marketing Services Jess Lombardo
Director, Demand Generation & Education Jim Bagan CIRCULATION & SUBSCRIPTIONS
P.O. Box 3605, Northbrook, IL 60065-3605 (877) 201-3915 | Fax: (847)-291-4816 circ.FoodLogistics@omeda.com
LIST RENTAL
Sr. Account Manager Bart Piccirillo | Data Axle (518) 339 4511 | bart.piccirillo@infogroup.com
REPRINT SERVICES
Brian Hines (647) 296-5014 | bhines@ACBusinessMedia.com
Published and copyrighted 2023 by AC Business Media. All rights reserved. No part of this publication may be reproduced or transmitted in any form or by any means, electronic or mechanical, including photocopy, recording or any information storage or retrieval system, without written permission from the publisher.
Food Logistics (USPS 015-667; ISSN 1094-7450 print; ISSN 19307527 online) is published 6 times per year in January/February, March/ April, May/June, July/August, September/October, and November/ December by AC Business Media, 201 N. Main Street, Fort Atkinson, WI 53538. Periodicals postage paid at Fort Atkinson, WI 53538 and additional mailing offices.
POSTMASTER: Send address changes to Food Logistics, P.O. Box 3605, Northbrook, IL 60065-3605. Subscriptions: U.S., one year, $45; two years, $85; Canada & Mexico, one year, $65; two years, $120; international, one year, $95; two years, $180. All subscriptions must be paid in U.S. funds, drawn from a U.S. bank. Printed in the USA. @FOOD-LOGISTICS-MAGAZINE @FOODLOGISTICS @FOODLOGISTICS
The Journey of Avocado Toast
The journey of avocado toast is far from simple and involves many characters working behind the scenes, especially logistics companies. From cross-border logistics to cold chain shipping, logistics companies work around the clock so that consumers can have the foods they want, when they want them, no questions asked.

Dani EtkinSpigelman, VP of business development at TA Services, explains that while consumers find avocados unrefrigerated in supermarkets—or smeared on toast—they require specialized refrigerated shipment. By keeping avocados cold throughout their supply chain journey, ripening slows and customers receive them at peak ripeness.
After preparation for shipment, the next major step in cold chain logistics for avocado consumption is crossing the U.S.Mexico border. To cross the border, the shipment will have to go through U.S. Customs and Border Patrol. Paperwork will need to be filed in advance, and to navigate the complexities of crossborder logistics, many companies turn to a third-party logistics (3PL) provider.
Cold chain logistics reveals its complexities as combining perishable foods is far less simple than one may assume. Remembering that avocados require precise temperatures, so too, do all perishable foods. In fact, each ingredient of this avocado toast—bread, tomatoes, arugula, and mozzarella cheese—all have unique shipping requirements.

Scan the QR code to learn more https://foodl.me/t0mrt4
Food Commodities Climb in Price
Food manufacturing produce price index (PPI) is up 10.4% yearover-year and 25.9% above pre-pandemic levels seen in February 2020, according to Consumer Brands Association (CBA).
“There are countless factors impacting production costs right now as ongoing supply chain disruptions are constantly at play,” says Tom Madrecki, VP of supply chain for CBA. “As CPG manufacturers adjust their inventory strategies, staffing and recruitment models and shipping decisions to account for the supply chain challenges, the federal government must take action to boost supply chain resiliency.”
Key commodities continue to show wholesale prices well above last year and significantly higher than pre-pandemic norms. Year-over-year, eggs spiked 158%, grains increased 29% and pasta is up 37%. While there was some decline in wholesale meat prices, turkeys are up 40% over last year. Diesel fuel has risen 62% year-over-year, making a significant impact on the CPG industry, which accounts for one-fifth of all freight transportation.
Scan the QR code to learn more https://foodl.me/u90w7d
Women Celebrated in Logistics
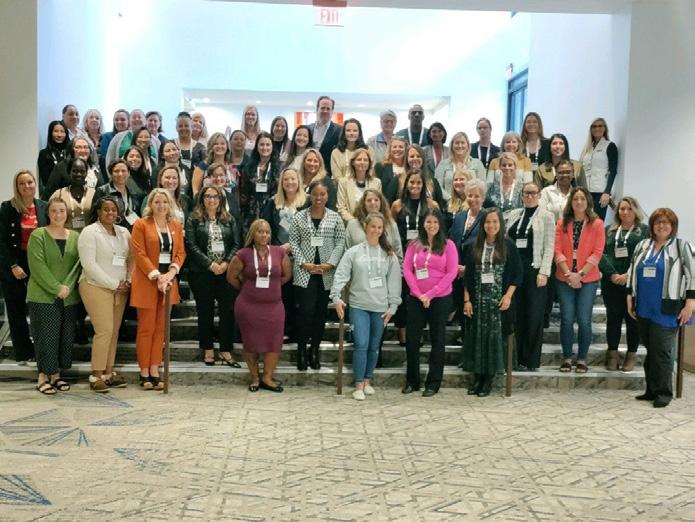
Professional growth often starts with a conversation and on open dialogue to understanding the strengths and weaknesses of yourself and the industry you work in. The 2022 Women in Supply Chain Forum sparked those conversations about women in the supply chain and offered a workshop on collaborative problem solving. The keynote speaker, Sarah Barnes-Humphrey, host of Let’s Talk Supply Chain podcast, kicked off the event with insight into how self-advocacy and diversity improves the supply chain and empowers men and women alike.
The Forum featured both panel discussions and fireside chats with applicable topics to professional and workforce development. The Forum also brought together women, and men, of all backgrounds—in life and business. Some of these women were Supply & Demand Chain Executive’s 2022 Women in Supply Chain award winners and this gave the event a chance to celebrate them in person. The networking opportunities were compounded by various receptions and conversation tables that allowed attendees to share stories, connect on socials and truly celebrate the diversity of women in the industry.
Scan the OR code to learn more https://foodl.me/02hn0m
Autonomous Sourcing During Food Inflation
Food inflation has been increasing at its fastest rate since 1979. Supply chain challenges like delays, transportation disruption, worker unrest and more amid a looming recession have led to higher prices and shortages of household favorites. As a result, the cost of groceries in the United States has soared 13% from 2021, with little signs of slowing down. In the UK, inflation has recently hit 10.1%. Working-class families are feeling the heat, and businesses are at a loss.
Thankfully, there is a secret weapon that procurement teams can use to their advantage, according to Dylan Alperin, head of professional services at Keevlar. With autonomous sourcing, businesses can reduce costs, drive operational efficiencies, decrease time to market and more—no matter the sudden situation at hand. The result: guaranteed continuity and supply chain resiliency, without robbing the working-class family at the grocery store.
Scan the QR code to learn more https://foodl.me/b2w97q
Online Grocery Shopping Today
Seventy percent of consumers in a Phononic survey say they will buy most of their groceries for holiday meals and/or holiday parties in-store, yet 84% of retailers still expect their online grocery delivery and curbside pickup operations to increase in the next year.
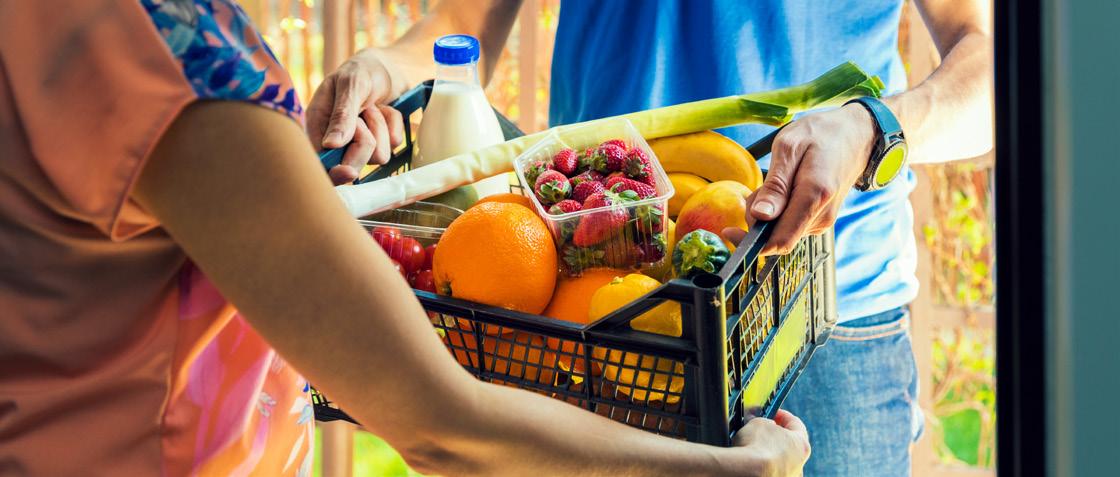
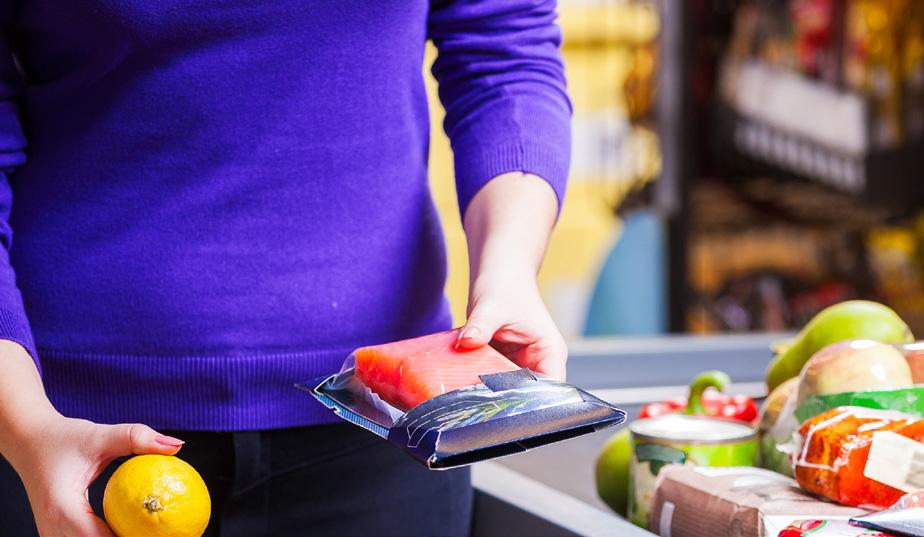
“Given the explosive adoption of curbside pickup and last mile delivery over the last few years, it’s clear that online grocery shopping is here to stay,” says Dana Krug, SVP and general manager at Phononic. “Yet there are challenges that our industry report highlights—notably, concerns around food safety, consumer trust and consideration in sustainability within the industry from both sides—that show there is an opportunity for retailers to strengthen business with their online delivery and curbside pick-up. With cold chain technology slated to be a multimillion-dollar investment for nearly a third of retailers over the coming year, identifying more sustainable technology such as solid-state cooling can offer game changing results for both retailers and customers. Solid state cooling also checks the sustainability box for retailers, providing a non-toxic, low carbon footprint option that doesn’t use harmful Global Warming Potential (GWP) refrigerants. Implementing changes such as this has the potential to revolutionize the industry.”
Scan the QR code to learn more https://foodl.me/efdei2
Causes of Food Waste Today
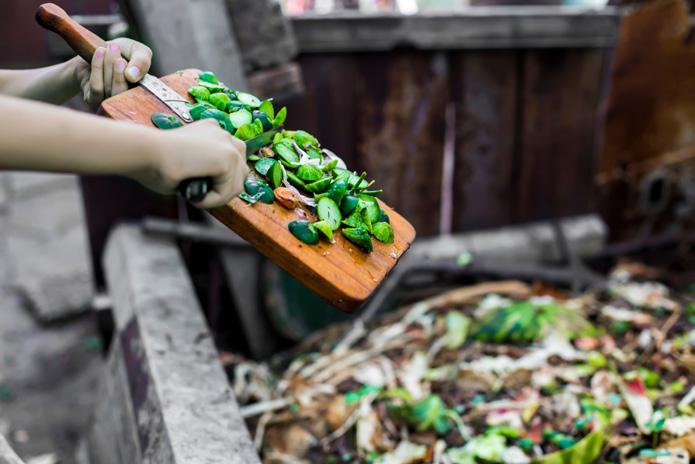
@Lomiso.stock.@adobe.com
Food insecurity and sustainability are two of the most talked about challenges today. But it’s important to realize they’re not mutually exclusive. In fact, they’re intertwined. Nearly 10% of the world’s emissions are caused by the manufacturing of food that will ultimately go to waste. Svante Göthe, head of sustainability at RELEX Solutions, outlines top causes of waste across the food supply chain, and how technology can help grocery stores meet customer needs while reducing the food they must throw out and ultimately cut their footprint:
Properly assessing demand requires grocery chains to understand both macro and micro trends across locations. For instance, ingredients for baked goods may climb in demand nationwide right before the holidays. But the popularity of fillings for these goods may differ from region to region.
Food merchandising is a tricky business, especially for the products customers would typically find around the supermarket’s outer ring, such as fresh produce, meat and dairy. Customers are unlikely to purchase bruised or over-ripened fruits and vegetables. Steaks, pork and chicken nearing their sell-by dates are also often rejected in favor of food that will stay good for another week or longer. For grocery stores, the last two years have been one of the most turbulent periods on record. COVID-19 led to supply shocks in every corner of the retail marketplace, and grocery stores felt the heat. Meat suppliers went offline because of outbreaks, and demand soared for products that don’t typically fly off the shelves, such as toilet paper.
Scan the QR code to learn more https://foodl.me/lwa08o
Changing Policies, Changing Agriculture
A well-functioning agricultural sector is a crucial component for any successful and sustainable economy, given its core role in the production of food and raw materials. Supply chains of many sectors rely on crops, fibers and fuels, linking them to agriculture and its impacts.
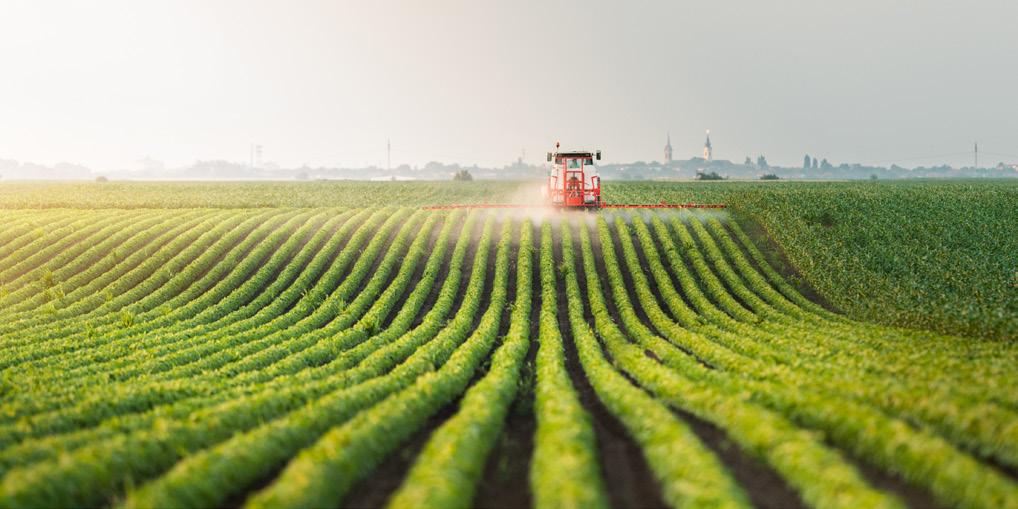
As new sustainability policies for crop and animal production continue to emerge, the corporate sector needs to be ready. Demonstrating sustainable agricultural production is becoming critical to preserve access to local and global markets, says Margarita Lysenkova, manager—sector program, Global Reporting Initiative (GRI).
GRI 13: Agriculture, Aquaculture and Fishing Sectors, released in June, is a dedicated standard for agriculture companies. It is an extension of the GRI Standards, the most widely used sustainability reporting standards across global regions, which incorporate general due diligence requirements as well as key sectoral topics. While GRI’s standards are voluntary, they build on emerging policies and adopt requirements in line with international law, often exceeding jurisdictional regulations. GRI 13 integrates sustainability expectations across 26 topics, including those highlighted above, making it allencompassing.
Scan the QR code to learn more https://foodl.me/vhzj5x
U.S. Port Improvements Strengthen Supply Chains
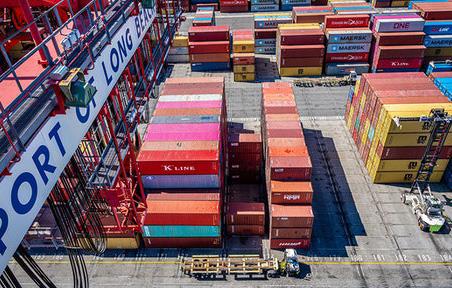
The United States Department of Transportation (USDOT) Maritime Administration (MARAD) announced $703 million in grants to fund 41 projects in 22 states through the Port Infrastructure Development Program (PIDP), the largest amount than any year in the program’s history.
More than 60% of the funds will benefit ports in disadvantaged communities and several of the projects will help reduce emissions at the ports through electrification. Additionally, more than $150 million in awards include a focus on electrification of port equipment to reduce emissions and improve air quality.
“This funding will continue to augment PIDP for the next several years, through federal fiscal year 2026 (FY2026). At a time when vital infrastructure at U.S. seaports has become the subject of national attention, this strong investment will enable projects aimed at improving and expanding port infrastructure to ensure critical cargo is transported efficiently and safely,” according to American Association of Port Authorities (AAPA).
Scan the QR code to learn more https://foodl.me/kf0zoh
Get Your Sustainable Packing Ready for 2023
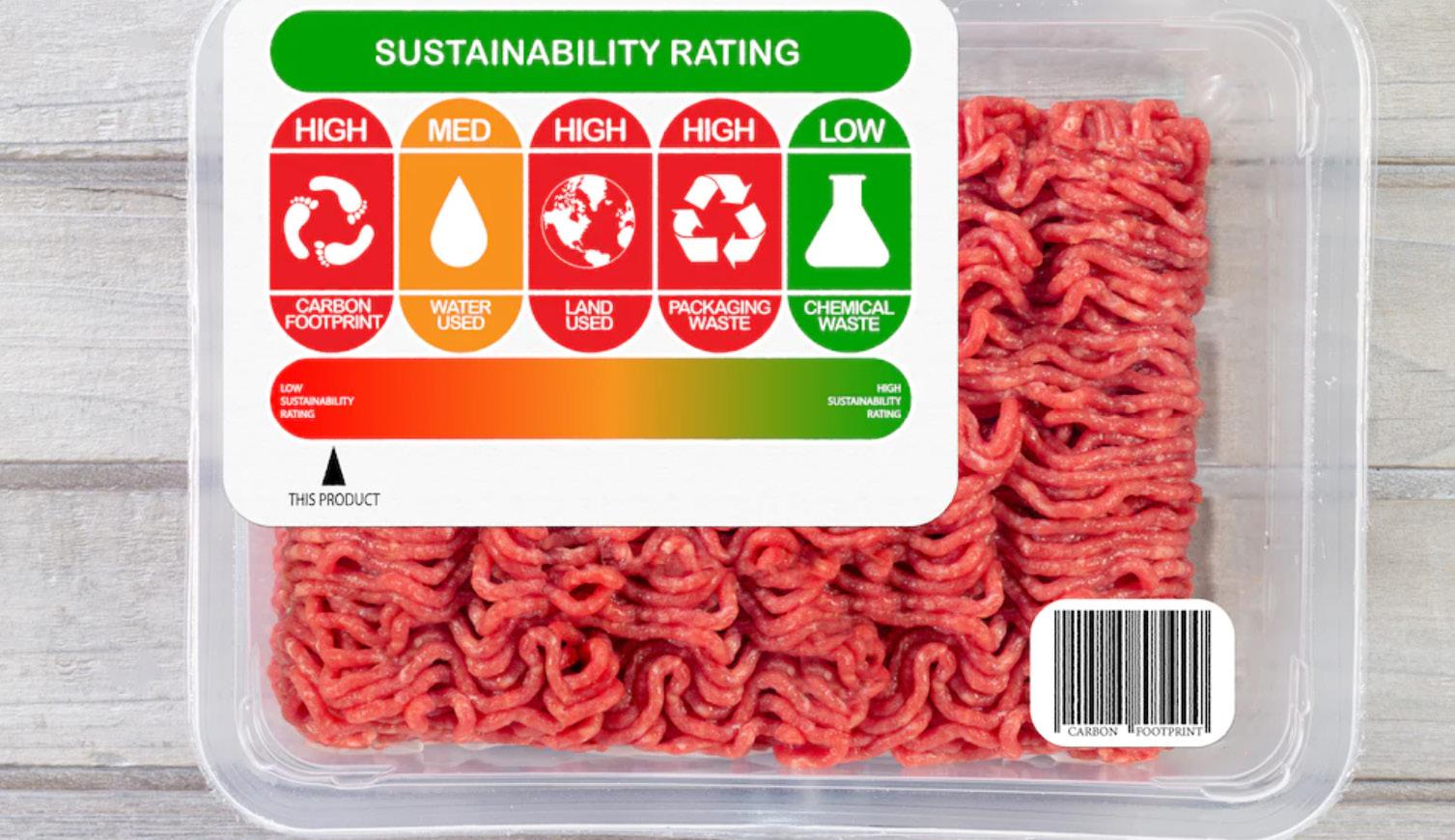
With the New Year comes new rules and regulations. California is still leading the way when it comes to sustainable packaging, but now other states are following in their footsteps. It is very likely that more states will continue to follow in their footsteps to show consumers that they are sustainability savvy. Carl Tiu, first VP of food and beverage financing at BHI, offers three ways to prepare for this: assess your needs for working capital, work with your banker on capital expenditures and plan for future growth.
Scan the QR code to learn more. https://foodl.me/wfxp97
Women Break Barriers in Trucking
Although women account for around half of the labor force in this country, fewer than 8% of truck drivers are women. There are several benefits in the trucking and transportation industries that would benefit working women if they were aware of the opportunities. Candace Davis, owner-operator of Davis & Davis Transportation LLC, gives insight and advice for women trying to break through the trucking industry.

• Learn the business: Trucking companies across the country are actually raising wages to attract new workers, especially females. It’s also an industry that doesn’t have a pay gap — drivers are paid by the mile or the load — and has clear paths for entrepreneurial advancement.
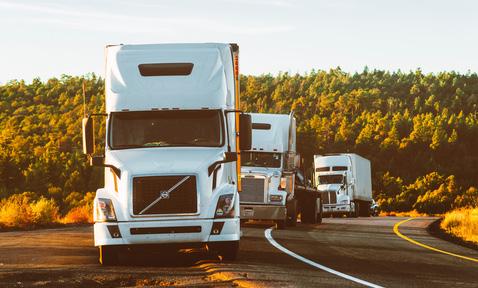
• Questions aren’t a form of weakness: Let your voice be heard and let your actions gain positive attention by making an impact from start to finish. By showing competency through actions, people will understand that women can do the job just as well as anybody else.
• Cultivate a collective mindset: The diversity of corporate culture is defined through a scope of equality, the right to professional development and career advancement opportunities for women in a competitive market.
The industry is growing, supply chains are becoming more complex and there are ample opportunities. The demand for drivers and the competitive pay that comes with the job make the trucking industry an untapped resource for women. Scan the QR code to learn more https://foodl.me/azol9y
A Winter Wonderland in Food Distribution
The practice of winterizing any food distribution fleet today has changed drastically from even just five or 10 years ago. Gone are the days of adjusting each truck based on historical perceptions or just going on experience. Brian Antonellis, SVP fleet operations at Fleet Advantage, explains that everything starts with preventative maintenance (PM) and the ability to calendarize the PM plan. Maintenance prepared for and performed in the spring and summer will have a different focus than that of winter, and distributor fleets must be able to identify the trends and areas that colder climates may affect more so than in warmer climates. Setting the appropriate annual plan will be vital to establishing the proper PM checklist at different times of the year. This can include paying close attention to fuel systems, staying vigilant on reoccurring tasks like changing tires and properly communicating cost breakdowns to the C-level.
Scan the QR code to learn more https://foodl.me/45b3ru
The Great Rate Wars in Container Shipping
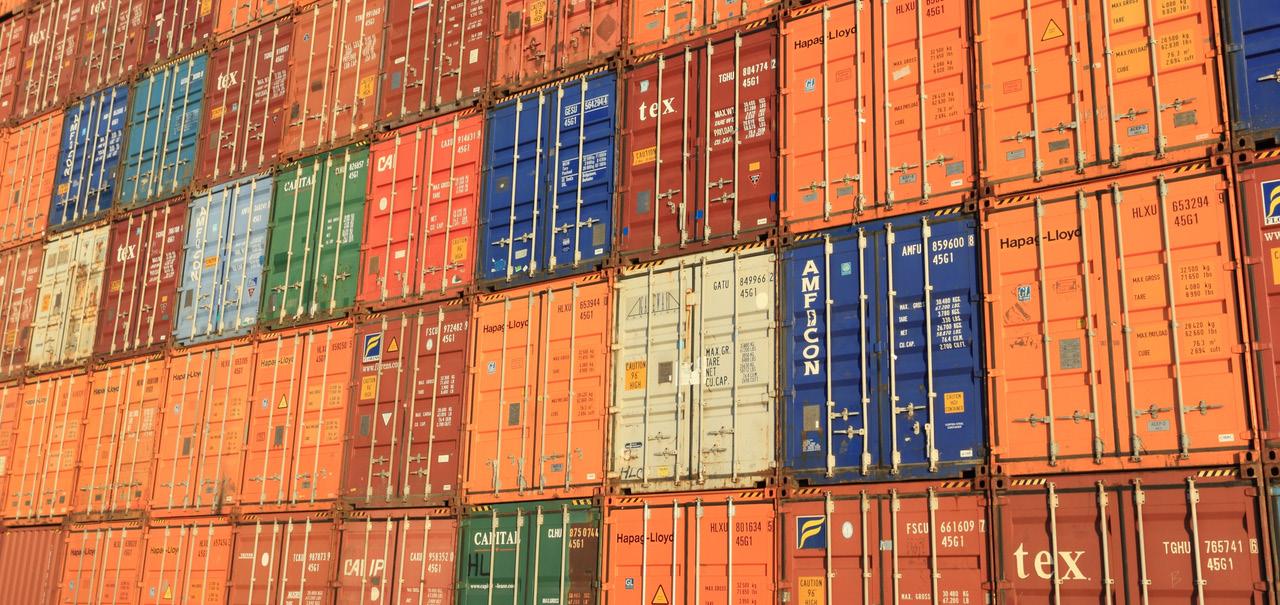
There is significant market volatility that continues to disrupt the container shipping industry. With a significant oversupply of containers and a further influx of more TEUs in 2023, shipping lines continue to reduce vessel capacity and suspend services by considerable blank sailings, according to the market forecaster by Container xChange. In fact, some shippers plan to continue making capacity adjustments on services from Asia to North America, Europe and the Mediterranean to better align with demand fluctuations.
“In 2023, there is a high possibility of an all-out price war. It doesn’t seem that the capacity restrictions that we have seen in the past two years are due to return, so we’ll just have ample capacity both on the vessel as well as on the container side. With the competitive dynamics in the container shipping and liner industry, I don’t expect especially the big players to hold back, and we do expect prices to come down to almost variable costs. We also foresee market consolidation,” says Christian Roeloffs, co-founder and CEO of Container xChange. Scan the QR code to learn more https://foodl.me/mztmnb
Capacity Optimization in the Last-Mile
Capacity Optimization takes electronic requests from shipping customers to autogenerate orders. A dispatch scheduling tool calculates variables from appointment windows and truck availability to truck floor space and maximum weight. Recently launched at Fleet Enable, CEO Krishna Vattipalli says, “There is a lot of complexity in determining what freight will fit onto a truck that ends up increasing the odds of a delivery failure. Capacity Optimization ensures we are creating the most profitable routes that can be scheduled, loaded, unloaded and delivered at the appropriate time.”
• Capacity Optimization replaces manual calculations that determine if deliveries fit on trucks and meet weight limits.
• Capacity Optimization takes electronic requests from shipping customers to auto-generate orders. A dispatch scheduling tool calculates variables from appointment windows and truck availability to truck floor space and maximum weight.
The tool auto-generates delivery routes that adhere to delivery constraints.
Capacity Optimization provides the warehouse with truck loading instructions to ensure proper shipment delivery.
Scan the QR code to learn more https://foodl.me/sism1k
EV Charging Stations Surge Spending
Historically, says Dallas Henderson, account manager at RizePoint, consumers wanted to dash into gas stations or convenience stores, gas up their cars, grab a quick snack and be back on the road in a few minutes. Moving forward, consumers will seek destinations when they need to charge their cars. This will no longer be a fast exchange, but a more leisurely experience. Since charging an EV can take an hour or more, these consumers will need something to do (eat, shop, work) while they wait.
The increasing EV demand means that restaurants will be competing with other businesses, including shopping centers, grocery stores and convenience stores to attract EV owners and convince them to come stay—and spend—with them. This comes in the form of considering these action steps:
1. Recognizing the benefits of adding EV charging stations.
2. Attracting the key EV users.
3. Elevating sustainability efforts as a whole.
4. Filling a need for the consumer.
5. Generating awareness and brand loyalty.
6. Attracting visitors as well as locals.
Americans Agree: Video Saves Drivers
Despite safety efforts deployed by many fleets, Americans feel greatly impacted by unsafe fleet driving behaviors, according to a study by Solera Holdings, LLC.
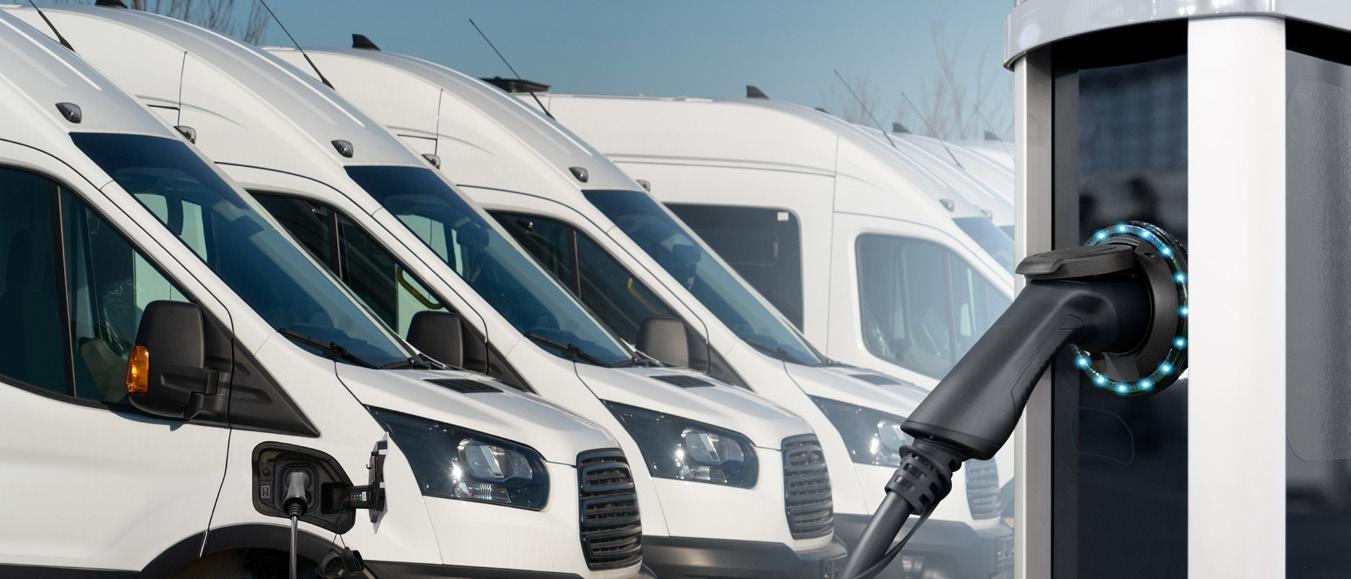
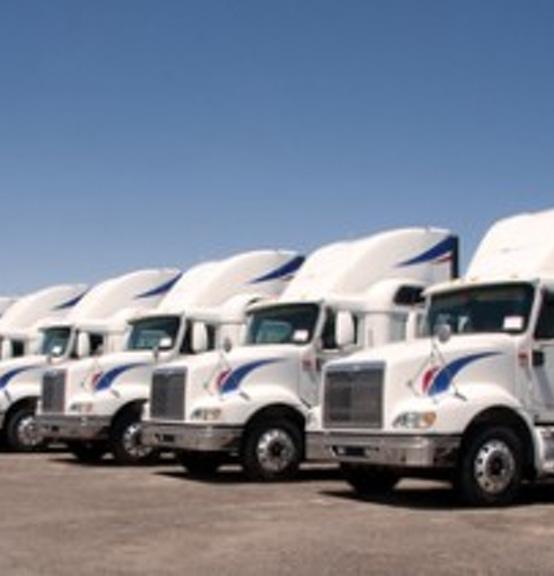
7. Prioritizing QA and safety.
8. Monitoring suppliers along the supply chain.
9. Pivoting from punitive to collaborative inspections. Scan the QR code to learn more https://foodl.me/f9h7an
“The industry has come a long way in improving driver safety standards, and it’s important that we continue on this journey collectively, especially as there are public perceptions to overcome,” says Michal Yariv, VP and GM of strategic initiatives at Solera. “First and foremost, driver safety needs to be a top priority for fleet managers to ensure drivers can do their job and get home safely at the end of the day, and video technology with built-in driver coaching is the key to achieving optimum safety.”
The vast majority of respondents (89%) believe commercial truck drivers could benefit from further safety training. In addition, two-thirds believe video-based safety systems would have a positive effect on commercial truck drivers’ ability to drive safely.
Scan the QR code to learn more https://foodl.me/0tcim3
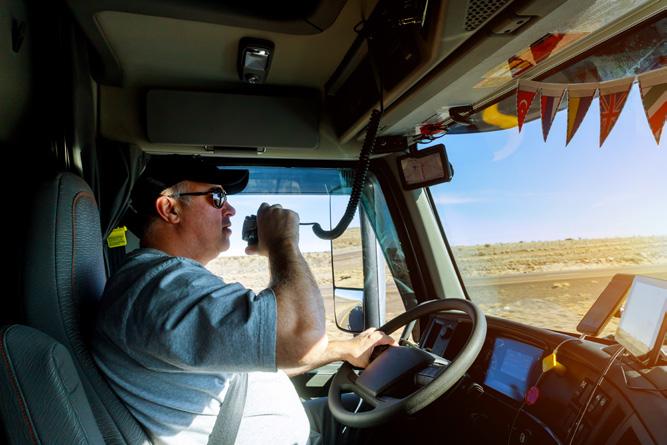
Sustainable Considerations in Transportation
Josh Boulk, president at Trax Technologies, says it’s no secret that supply chain processes directly impact the environment. As the demand for corporate social responsibility grows, supply chain leaders must make strategic course corrections and chart a path toward sustainable supply chain operations. These efforts must be defined and timely but also reasonable and scalable.
Adopting sustainable supply chain practices is a top priority for transportation and logistics leaders. But the question of how to achieve this isn’t one-size-fits-all. That’s why it’s essential to understand the fundamental steps before launching a full-fledged
Kiosk for Supply Chain Safety
IntelliTrans introduced Kiosk functionality within the IntelliTrans transportation management system to keep truck drivers in their cabs. Doing so improves safety, speeds up check-in process and reduces on-site time by 30 minutes or more.

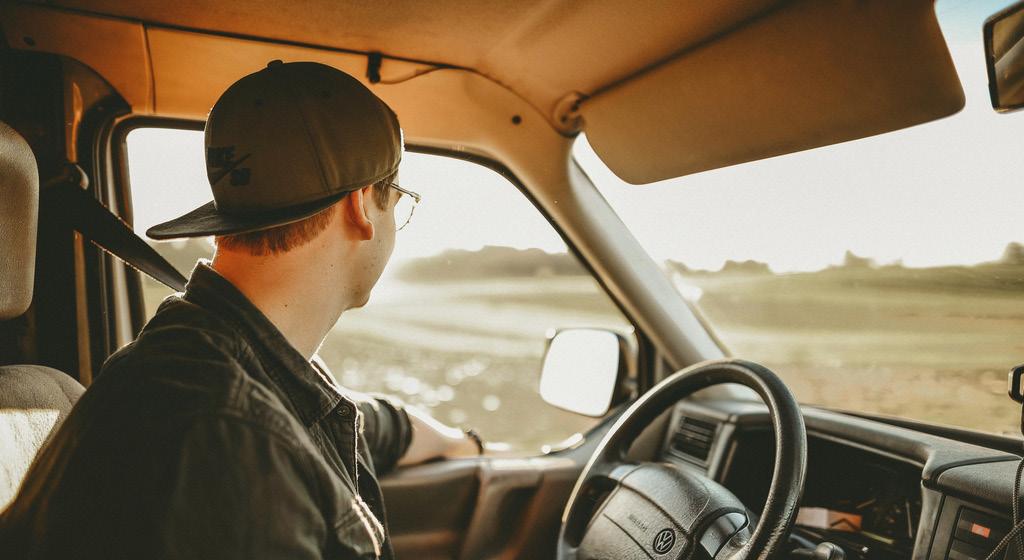
sustainability strategy that include scalable solutions, internal alignment, engagement with suppliers and established goals and overall tracking.

Business leaders are welltrained to establish performance indicators, set goals and track performance. However, you need sound data and data governance processes to do it. That’s where freight audit and payment come in, along with regular data cleansing and other operational best practices. A freight audit and payment program can capture the foundational transportation logistics data needed to build a sustainability program and measure KPIs over time.
Scan the QR code to learn more https://foodl.me/c3wdpp
Cargo Theft is Still Supply Chains #1 Concern
CargoNet recorded 1,778 supply chain risk events across the United States and Canada in 2022. In 2022, supply chains were more concerned with disruptions because of it’s effect on inflation. However, theft is still the top concern for supply chains to keep in mind. There were 96 more fictitious pickups in 2022 than there were in 2021. This was especially prominent in states such as California and has since spread to Washington, New Jersey, Pennsylvania, Illinois and Texas.
Scan the QR code to learn more.
https://foodl.me/q85n7n
“Previously, the guard in a guard shack had to look at his clipboard to validate whether a particular truck should be on the property,” says Brian Cupp, director of operations at IntelliTrans. “Guards needed to validate that the driver was with the right company with the correct load and that the driver could check-in. With Kiosk, the guard knows this information before the truck arrives, allowing him to wave the driver into the yard without the driver having to stop and get out of the truck. Even better, the warehouse personnel preparing shipments sees when a truck is approaching the facility prior to check-in, providing advanced confirmation of the required product staging. This new self-service experience has really helped employee and driver satisfaction, as well as reduced on-site time.”
Scan the QR code to learn more https://foodl.me/zjcbi5